
Effect of Y content on microstructure and mechanical properties of
2519 aluminum alloy
LI Hui-zhong(李慧中), LIANG Xiao-peng(梁霄鹏), LI Fang-fang(李芳芳),
GUO Fei-fei(郭菲菲), LI Zhou(李 洲), ZHANG Xin-ming(张新明)
School of Materials Science and Engineering, Central South University, Changsha 410083, China
Received 15 July 2007; accepted 10 September 2007
Abstract: The effects of yttrium(Y) content on precipitation hardening, elevated temperature mechanical properties and morphologies of 2519 aluminum alloy were investigated by means of microhardness test, tensile test, optical microscopy(OM), transmission electron microscopy(TEM) and scanning electron microscopy(SEM). The results show that the tensile strength increases from 485 MPa to 490 MPa by increasing Y content from 0 to 0.10%(mass fraction) at room temperature, and from 155 MPa to 205 MPa by increasing Y content from 0 to 0.20% at 300 ℃. The high strength of 2519 aluminum alloy is attributed to the high density of fine θ′ precipitates and intermetallic compound AlCuY with high thermal stability. Addition of Y above 0.20% in 2519 aluminum alloy may induce the decrease in the tensile strength both at room temperature (20 ℃) and 300 ℃.
Key words: 2519 aluminum alloy; yttrium; microstructure; mechanical properties
1 Introduction
Aluminum alloys have been the primary materials for structural components of military aircrafts, helicopters, amphibians, etc for several decades. This may attribute to the low density of aluminum in mass- critical application[1]. 2519 aluminum alloys that is used as armor plates have good weldability, acceptable ballistic resistance and mechanical properties as well as resistance to stress corrosion cracking[1-3].
It is well known that trace or microalloying additions to Al alloys can strongly influence the precipitation process and are of great practice importance. These additions can modify the dispersion and/or the habit plane, morphology and crystal structure of the resulting precipitations[4-6]. Rare earth elements in conventional casting aluminum alloys have shown beneficial effects on melting and solidification. These elements reduce the contents of gases and some impurities and spacing between secondary dendrite arms. The use of rare earth as micro-alloying element in Al has been studied for several years. It was reported that Ce affected the grain size of a binary Al-Li alloy and the mechanical properties of Al-Li-Mg casting alloys containing impurity Fe. The number of grains per unit area in the binary alloy linearly increases with raising the Ce content up to 1.1% (mass fraction), and the mechanical properties of the Al-Li-Mg casting alloys were improved[7]. The addition of Ce was also reported to affect the ductility and fracture, and the negative effect of impurity Fe was controlled by Ce addition. The Ce addition can toughen 8090 alloy sheets rich in impurities of Fe, Si and alkali metals[7]. The velocity of crack initiation of Al-4.5%Cu alloy without Ce addition is obviously greater than that of alloy with Ce addition[8]. The addition of Ce into Al-Cu-Mg-Mn-Ag alloy decreases the size of Ω phase, and improves the density and thermal stability of Ω phase between 200 ℃ and 300 ℃[9]. A previous study indicated that rare earth element Y can improve the strength of Al-Zn-Mg-Cu alloy at elevated temperature. This is attributed to the fact that Y decreases the as-cast grain size, increases the nucleation ratio, and decreases the growth speed of the precipitates during artificial aging[10-12]. Trace Y has little effect on the casting microstructure of 2618 alloy and shape of Al9FeNi phase. Meanwhile, Y can decrease strength and plasticity of 2618 alloy at room temperature [13]. But there is little information available for the effect of rare earth Y addition on precipitation hardening and strengthening in 2519 aluminum alloy. The present work was thus to examine such effect with a view of establishing the potential for enhancing the mechanical properties of these alloys.
2 Experimental
Table 1 lists the chemical compositions of the present alloys with Y additions of 0, 0.10%, 0.20% and 0.30% (mass fraction). Al-Cu, Al-Mn, Al-Y, Al-Ti-B, Al-Zr, Al-V intermediate alloy and pure Mg, industrial pure Al were used to prepare the alloy in induction furnace under argon atmosphere, and then cast into iron moulds to produce billets of 100 mm×100 mm×25 mm. The billets were homogenized at 520℃ for 18 h followed by air cooling to room temperature, and then hot rolled to 3 mm-thick plate at 440 ℃. Subsequently, the plate was solution-treated for 2 h at 530 ℃ and then water quenched. At last, the plate was rolled by 15% before artificial aging at 165 ℃ for various time period (up to 27 h).
Table 1 Chemical compositions of alloys (mass fraction, %)
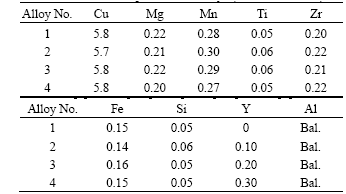
Vickers hardness measurement was carried out on all aged samples. The samples that show the highest hardness were selected for tensile testing at room temperature and 300 ℃. Tensile tests were performed at 20 ℃ at the stretching speed of 2 mm/min on the CSS-44100 electronic stretching machine, and the test at 300 ℃ was performed at the speed of 2 mm/min on Gleeble-1500 hot simulation machine. The rate of elevating temperature was about 10 ℃/s and the sample was held at 300 ℃ for about 3 min.
OM, SEM and TEM were applied to characterize the microstructure of the alloys with different Ce additions. TEM samples were electo-polished in a 70% ethanol and 30% nitric acid solution at -35 ℃, using a twin-jet equipment operated at 30 V.
3 Results
3.1 Age-hardening behavior
Fig.1 shows the Vickers hardness(Hv) curves of the

Fig.1 Age-hardening curves of alloys at 165 ℃
four alloys. All the alloys show the same trend of variation with aging time. That is, the micro-hardness increases when the aging time increases and decreases after the hardness reaches the peak value. It should be noted that different behavior is observed as for the effect of Y addition on the aging response when being compared with alloy without Y. For the aging alloy at 165 ℃, age hardening speed and the Vickers hardness are increased with 0.10% Y addition. The highest hardness increases from HV155 for the alloy without Y to HV161 for that containing 0.10%Y. However, the highest hardness is reduced to HV145 when the Y content is further increased to 0.30%. Meanwhile, the peak-ageing time for 0%Y, 0.20%Y, 0.30%Y alloys is 15 h, but that for 0.10%Y contained alloy is 12 h.
3.2 Tensile properties
Tensile properties of different Y contained alloys at different temperatures after peak aging are listed in Table 2. Compared with Alloy 1, the tensile strength is increased from 485 MPa to 490 MPa and yield strength is increased from 445 MPa to 455 MPa at room tempera-
Table 2 Mechanical properties of alloys at different tempera- tures
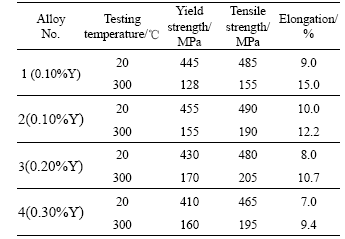
ture when the Y content is increased up to 0.10%. But, it is decreased gradually when the Y content is increased from 0.10% to 0.20%. At 300 ℃, the tensile strength is increased from 155 MPa to 205 MPa when the Y content is increased up to 0.20%. However, it is decreased slightly when the Y content is increased from 0.20% to 0.30%.
With increasing Y content in the alloys, the elongation is changed. At room temperature, the elongation is increased only slightly from 9.0% to 10.0% when the Y content is increased up to 0.10%. It is decreased gradually from10.0% to 7.0% when the Y content is increased from 0.10% to 0.30%. At 300 ℃, the elongation is decreased from 15% to 9.4% when the Y content is increased up to 0.30%. It could be concluded that increasing Y content increases the elevated temperature strength but decreases the elongation of 2519 aluminum alloy.
3.3 Microstructure observation
Fig.2 shows the TEM morphologies of the four alloys after aging to peak-aged stage. It can be seen that θ′ phase is uniformly distributed in all the four alloys, which is the main phase in 2519 aluminum alloy. The density of θ′ phase in alloy 2 is higher than that in other alloys. However, the θ′ phase is coarsened when the content of Y is increased from 0.10% to 0.30%. Meanwhile, the density of θ′ phase is decreased. TEM was used to analyze the microstructure of alloy 3 after tensile tests at 300 ℃ and the results are shown in Fig.3(a). Coarsened secondary phases on grain boundary pin the grain boundary, and the interaction between precipitates and dislocations is observed. Using energy spectrum analysis, the coarsened secondary phases are identified to be the intermediate compound of Al, Cu and Y, as observed in Fig.3(b). This indicates that the intermediate compounds could hinder grain boundary movement at high temperature, then increasing heat-resistance property.
4 Discussion
The present study shows that the addition of Y affects the microstructure and property of 2519 aluminum alloy. With the addition of Y, the size and density of the predominant hardening phase of θ′ phase are changed after peak-ageing at 165℃. For example, both the microhardness and tensile strength are increased with the addition of 0.10%Y. It is obvious that the density of θ′ phase in the experimental alloy increases. These fine phases hinder dislocation movement, then increasing tensile strength of the experimental alloy. However, excessive addition of Y could decrease strength because excessive Y would form intermediate
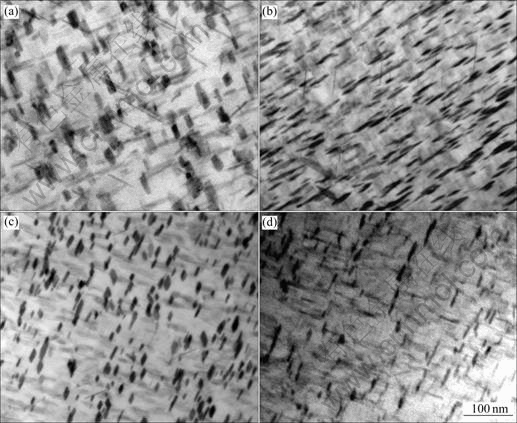
Fig.2 TEM micrographs of alloys after peak-aging at 165 ℃: (a) Alloy 1; (b) Alloy 2; (c) Alloy 3; (d) Alloy 4
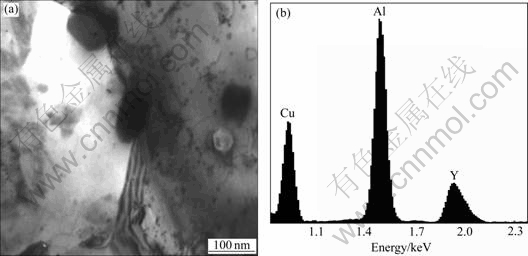
Fig.3 Morphology of second phases at grain boundary (a) and its EDS analysis (b) of alloy 3 at 300 ℃
compound of AlCuY together with Al and Cu, decreasing solid solubility of Cu in Al, and then decreasing θ′ phases precipitation. Therefore, the tensile strength of the present alloy decreases when the content of Y increases. The effect of Y on solid solubility of Cu and Mg in Al has been studied[14]. The results showed that addition of 0.20% Y caused the maximum solid solubility of Cu in Al at 430 ℃ to decrease from 2.2% to 0.50%. In the meantime, the maximum solid solubility of Mg decreases from 13% to 8%. There exists coarsened secondary phase, which forms during billet crystallizations in the alloy with 0.30% Y. In the casting structure of the experimental alloy, Y mainly distributes at the grain boundary but not in the grain. The diameter of Y atom is larger than that of Al, so when it enters the matrix, it will certainly cause great lattices distortion and increase system energy. However, the atoms on the boundary distribute loosely, so the distortion energy caused by rare earth compound aggregation on the boundary is much less than that caused by precipitation. In order to keep low free energy, Y atoms have to aggregate to the boundary unequally, so the intermediate compound AlCuY mainly precipitates along the grain boundary or dendritic crystal boundary. The intermediate compound of high melting point, which possesses high thermal stability, and distributes along the grain boundary in the shape of discontinuous net, enhances grain boundary to resist slipping and creeping at high temperature and increase the elevated temperature strength of experimental alloy. It is believed that trace addition of Y could reduce Cu atoms distribution, and then restrain precipitation coarsening, which is benefit for precipitation heat stability and heat resistance property of the alloy[15]. When the content of Y is above 0.30%, the elevated temperature strength of experimental alloy decreases obviously, because the intermediate compound containing Y aggregates and grows, and then cuts up the matrix, decreases mechanical properties and weakens the obstruction to the boundary movement.
5 Conclusions
1) Addition of 0.10% Y can speed up the ageing hardening speed of 2519 aluminum alloy. The tensile strength is increased by 5 MPa at peak ageing at room temperature. Addition of 0.20% Y makes the tensile strength of the alloy at 300 ℃ reach 205 MPa, which is 30% higher than that of the alloy without Y added.
2) Y mainly distributes in intermediate compound AlCuY, which effectively restrains base metal deformation and crystal boundary migration, and then obviously increases mechanical properties at high temperature.
References
[1] DYMEK S, DOLLAR M. TEM investigation of age-hardenable Al 2519 alloy subjected to stress corrosion cracking tests [J]. Materials Chemistry and Physics, 2003, 81(2/3): 286-288.
[2] KRAMER L S, BLAIR T P, BLOUGH S D. Stress-corrosion cracking susceptibility of various product forms of aluminum alloy 2519 [J]. Journal of Materials Engineering and Performance, 2002, 11(6): 645-650.
[3] FISHER J, JAMES J. Aluminum alloy 2519 in military vehicles [J]. Advance Materials and Processes, 2002, 160(9): 43-46.
[4] SOFYAN B T, RAVIPRASAD K, RINGER S P. Effects of microalloying with Cd and Ag on the precipitation process of Al-4Cu-0.3Mg(wt%) alloy at 200℃[J]. Micron, 2001, 32: 851-856.
[5] RINGER S P, HONO K, POLMEAR I J, SAKURAI T. Nucleation of precipitation in aged Al-Cu-Mg-(Ag) alloys with high Cu:Mg ratios [J]. Acta Mater, 1996, 44(5): 1883-1898.
[6] BARLAT F, LIU J. Precipitate-induced anisotropy in binary Al-Cu alloys [J]. Materials Science and Engineering, 1998, 257(A): 47-61.
[7] XIAO D H, WANG J N, DING D Y, YANG H L. Effect of rare earth Ce addition on the microstructure and mechanical properties of an Al-Cu-Mg-Ag alloy [J]. Journal of Alloys and Compounds, 2003, 352: 84-88.
[8] SI N C, GUO Y, LI G Q. Effect of RE cerium on thermal fatigue property of Al-4.5%Cu alloy [J]. The Chinese Journal of Nonferrous Metals, 2006, 16(4): 606-611. (in Chinese)
[9] XIAO D H, CHEN K H, SONG M. Effect of cerium addition on precipitation and microstructure of Al-Cu-Mg-Mn-Ag alloys [J]. The Chinese Journal of Nonferrous Metals, 2007, 17(5): 669-675. (in Chinese)
[10] SONG M, CHEN K H, HUANG L P. Effect of Ce and Ti on the microstructures and mechanical properties of an Al-Cu-Mg -Ag alloy [J]. Rare Metals, 2007, 26(1): 28-32.
[11] JIN S Z, RAN X, CHEN H. Effect of yttrium on the phase constituents in Zn and Mg containing aluminum alloys [J]. Journal of Inner Mongolia Polytechnic University, 1999, 20(2): 1-4.
[12] WANG Q L, WANG D Q. Effects of yttrium on microstructure and mechanical properties of AlZnMgCu alloy [J]. Journal of China University of Mining and Technology, 1999, 28(4): 382-385.
[13] WANG J H. Study on microstructure and mechanical properties of heat resistance aluminum alloy 2618 [D]. Changsha: Central South University, 2002. (in Chinese)
[14] ZENG L M, ZHENG J X. Effect of yttrium on α phase region of the Al-Cu-Mg system and properties of dural [J]. Journal of The Chinese Rare Earth Society, 1989, 7(4): 77-78.
[15] WANG J H, YI D Q, LU B. Effect of yttrium on microstructure and properties of 2618 aluminum alloy [J]. Journal of The Chinese Rare Earth Society, 2002, 20(2): 150-153.
(Edited by YANG Bing)
Foundation item: Project(2005CB623706) supported by the National Basic Research Program of China
Corresponding author: LI Hui-zhong; Tel: +86-731-8877949; E-mail: lhz606@mail.csu.edu.cn