
Preparation of AZ91D magnesium alloy semi-solid billet by
new strain induced melt activated method
JIANG Ju-fu(姜巨福)1, 2, LUO Shou-jing(罗守靖)1, ZOU Jing-xiang(邹经湘)2
1. School of Materials Science and Engineering, Harbin Institute of Technology, Harbin 150001, China;
2. Postdoctoral Mobile Station of Mechanics, Harbin Institute of Technology, Harbin 150001, China
Received 14 December 2005; accepted 6 April 2006
Abstract:New strain induced melt activated (new SIMA) method for preparing AZ91D magnesium alloy semi-solid billet is introduced by applying equal channel angular extrusion into strain induced step in SIMA method, by which semi-solid billet with fine spheroidal grains and average grain size of 18 μm can be prepared. Furthermore, average grain size of semi-solid billet is reduced with increasing extrusion pass of AZ91D magnesium alloy obtained in ECAE process. By using semi-solid billet prepared by new SIMA, thixoforged magazine plates component with high mechanical properties such as yield strength of 201.4 MPa, ultimate tensile strength of 321.8 MPa and elongation of 15.3%, can be obtained.
Key words: equal channel angular extrusion; semi-solid billet; strain induced melt activated method; mechanical properties
1 Introduction
AZ91D magnesium alloy has received more attention due to its high specific strength, specific rigidity and good dimensional stability and so on[1]. Thixoforming is one of the best methods with regard to forming AZ91D magnesium alloy components because of its low resistance of deformation compared with solid metal forging, and high mechanical properties compared with liquid metal die casting[2-5]. Thixoforming is one branch of semi-solid processing of alloy, which forms alloys in the semi-solid state to near net shaped products. It relies on the thixotropic behavior of alloys which have a spheroidal rather than a dendritic microstructure in the semi-solid state[6-9].
For thixoforming of magnesium alloy, the most important step is to prepare semi-solid billets, that is, to obtain alloy with non-dendritic, or spheroidal micro- structure. SIMA, strain induced and melt activated method, is a good technology with regard to preparing magnesium alloy semi-solid billets with high solid fraction[10-12]. In general, there are two important steps in SIMA, strain induced step and melt activated step. However, for magnesium alloy, coarse and non-globular gains often exist in the microstructure of semi-solid billets prepared by common SIMA method, i.e., semi-solid isothermal treatment(SSIT) of upsetted magnesium cast materials. This is due to difficulties of magnesium alloy in obtaining severe deformation in strain induced step in SIMA because of the limited slip system in a close-packed hexagonal crystal structure. Therefore, a new strain induced procedure for SIMA is needed to obtain severe deformation, in which two advantages such as obtaining large deformation and refining grains of material should be included. Equal channel angular extrusion(ECAE) is a promising technique for obtaining ultra-fine grained bulk materials with increased strength and ductility through severe plastic deformation. During ECAE, a billet is extruded through a die that consists of two channels with equal cross-section, intersecting at an angle φ[13-18]. Studies on commercial and engineered application of ECAE are rarely reported, compared with microstructure, mechanical properties and texture of material processed by ECAE[19].
In the present study, a new method called new SIMA is introduced firstly by the application of ECAE into strain induced procedure in SIMA, which will promote the commercial and engineering application of ECAE and accelerate the application of thixoforming into forming magnesium alloys components.
2 Experimental
The alloy used in the present study was a commercial AZ91D magnesium alloy. Three materials processed by casting, conventional upsetting and ECAE were used. The material by casting was produced using continuous casting technique, donated as cast material. The upsetted material was cast material upsetted by 30% deformation degree at 573 K[20]. The material by ECAE was processed ranging from 1 pass to 4 passes at 573 K by an equal channel die that consists of two channels with equal cross-section, intersecting at an angle of 90?. During ECAE, the billet was rotated by 90? in the same direction between each pass. Fig.1 shows the die for ECAE. The diameter of equal cross-section channel is 58 mm. Three AZ91D magnesium alloys processed by casting, conventional upsetting and ECAE, were machined into samples with the height of 10 mm and diameter of 10 mm, which were isothermally treated in semi-solid state.
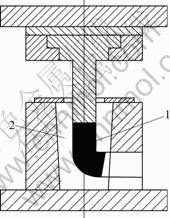
Fig.1 Schematic diagram of ECAE: 1 AZ91D magnesium alloy cast ingots; 2 Half die of ECAE
Based on differential scanning calorimetry (DSC) experimental result, isothermal treatment temperature was varied from 788 K to 853 K, corresponding to fraction solid from 0.85 to 0.28. Holding time varies from 10 min to 20 min. After the samples were isothermally treated, they were quenched quickly in water to keep the microstructure. Average gain size and shape factor were determined by image analysis equipment. When the shape factor value approaches to 1, it suggests that the real grain shape reaches spheroidal one. In order to demonstrate advantages of new SIMA in preparing AZ91D magnesium alloy semi-solid billets, thixoforging test for AZ91D magnesium alloy magazine plate component was employed to compare the difference in mechanical properties of thixoforged components using semi-solid billets prepared by three methods. During thixoforging, the technological parameters involved: holding the billet for 20 min at 818 K, die preheating temperature of 723 K and pressure of 2 000 kN.
3 Results and discussion
3.1 Microstructures of AZ91D magnesium alloy in three states
Fig.2 shows the microstructures of AZ91D magnesium alloys in three states before semi-solid isothermal treatment. As shown in Fig.2, microstructures are composed of α phase (Mg matrix) and β phase (Mg17Al12). However, the evident difference in grain size occurs in microstructures of AZ91D magnesium alloys in three states. As to cast material, coarse grains of above 250 μm occur in microstructure. Compared with cast material, upsetted material consists of relatively small grains ranging from 100 μm to 200 μm due to some plastic deformation. After the cast AZ91D magnesium alloys are extruded for 4 passes by ECAE, fine grains with the average size of 10 μm occur in microstructure because of severe plastic deformation. The micro- structure with fine grains will build foundations for obtaining finer globular grains in semi-solid billets during the following semi-solid isothermal treatment.
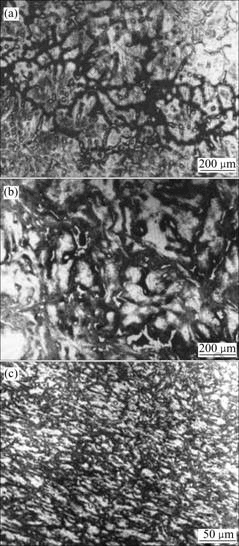
Fig.2 Microstructures of AZ91D magnesium alloy in three states before SSIT: (a) Cast; (b) Upsetted; (c) ECAE for 4 passes
3.2 Microstructures of semi-solid billets of AZ91D magnesium alloy prepared by three methods
Here, based on microstructure evolution of materials in three states, three methods for preparing semi-solid of AZ91D magnesium alloy are entitled: semi-solid isothermal treatment(SSIT) of cast material, common SIMA, that is, SSIT of upsetted material, and new SIMA method involving SSIT of processed material by ECAE.
Fig.3 shows the microstructures of semi-solid billets of AZ91D magnesium alloy prepared by three methods at 833 K. Fig.3(a) presents microstructure of semi-solid billet prepared by SSIT of cast material. It can be noted that coarse and non-globular grains occur in the microstructure. An important conclusion can be drawn that SSIT of cast AZ91D magnesium alloy is very difficult to prepare desirable semi-solid billet with fine globular grains. Microstructure of semi-solid billet prepared by common SIMA is shown in Fig.3(b). Compared with SSIT sample of cast material, semi-solid billet prepared by common SIMA consists of relatively small globular grains. However, the microstructure is inhomogenous due to limited plastic deformation during upsetting. Fig.3(c) shows microstructure of semi-solid billet prepared by new SIMA. It is very evident that the microstructure of semi-solid prepared by new SIMA is composed of finer globular grains. There exist two important characteristics in the microstructure. Firstly, the microstructure is very homogeneous. Secondly, the gain is very fine and shape of grain is close to globular.

Fig.3 Microstructures of semi-solid billet by three methods: (a) SSIT of cast material; (b) Common SIMA; (c) New SIMA
Table 1 lists the average grain size and shape factor of microstructures of semi-solid billets prepared by three methods. Average grain sizes of semi-solid billets prepared by three methods correspond respectively to 246 μm, 189 μm and 18 μm. It shows that compared with previous two methods, average grain size of AZ91D magnesium alloy semi-solid billet prepared by new SIMA decreases obviously, which will be beneficial to the following thixoforging process of components. The shape factors of microstructures of semi-solid billets also decrease obviously, corresponding to 3.4, 1.8 and 1.1, respectively, which implies spheroidization effect of grain becomes better and better. The results show that new SIMA method is a good method for preparing semi-solid billet of AZ91D magnesium alloy. By this method, semi-solid billet with fine globular grains and the gain size of 18 μm can be obtained.
Table 1 Average grain size and shape factor of semi-solid billets of AZ91D magnesium alloys prepared by three methods
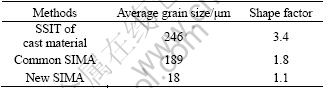
The reason for the difference in grain size and globurizing effect of semi-solid billets prepared by three methods lies in microstructures with different grain sizes before SSIT. The microstructure of cast material consists of coarse dendrites with average grain size of above 250 μm, which are difficult to become globular grains in the following SSIT. Though some globular grains occur in the microstructure, grain size is still very large, which leads to increased viscosity of semi-solid slurries. When cast material is upsetted by 30% deformation degree, grain size becomes relatively small because of limited plastic deformation, which leads to some relatively fine globular grains during the following semi-solid isothermal treatment. However, it is difficult to obtain finer globular grains in the microstructure during SSIT due to limited deformation ability of cast AZ91D magnesium alloy in upsetting process. When cast material is extruded for 4 passes by ECAE, fine-grain alloy with a grain size of 10 μm is created due to severe plastic deformation, which will accelerate formation of finer globular grains during SSIT.
3.3 Influence of extrusion pass in ECAE on microstructure evolution
In this paper, equal channel angular extrusion (ECAE) technology is used as strain induced operation in new SIMA method. Therefore, extrusion pass during ECAE has an influence on microstructure evolution of semi-solid billet during SSIT. Fig.4 shows microstructure evolution of semi-solid billet during SSIT with different extrusion passes of AZ91D magnesium alloy in ECAE. The observed samples are held for 10 min at 843K. As indicated in Fig.4, with increasing extrusion pass in ECAE, grain size of semi-solid billet becomes smaller and smaller, and more and more globular grains are created. Increasing extrusion pass corresponds to increasing deformation degree of processed material by ECAE. It fully demonstrates that severe plastic deformation created by ECAE is beneficial to formation of fine globular grains in the following SSIT. It implies that new SIMA method, that is, SSIT of processed material by ECAE, is a very good method for preparing AZ91D magnesium alloy semi-solid billet.

Fig.4 Microstructure evolution of semi-solid billet under different extrusion passes of AZ91D magnesium alloy in ECAE (held for 10 min at 853 K): (a) 1 pass; (b) 2 passes; (c) 3 passes; (d) 4 passes
3.4 Thixoforging of AZ91D magnesium alloy magazine plate component
Fig.5 shows the AZ91D magnesium alloy magazine plate components by thixoforging the semi-solid billets prepared by three methods, including SSIT of cast AZ91D magnesium alloy, common SIMA and new SIMA. In Fig.5, components (a) and (d) are thixoforged ones using AZ91D magnesium alloy semi-solid billet prepared by SSIT of cast AZ91D magnesium alloy, components (b) and (e) are thixoforged ones using AZ91D magnesium alloy semi-solid billet prepared by common SIMA, and components (c) and (f) are thixoforged ones using AZ91D magnesium alloy semi-solid billet by new SIMA. The difference among them is not obvious in macroscopic view. However, as indicated in Fig.6, the difference among them is very obvious in microstructure. In Fig.6, observed samples are obtained from the location A in Fig.5.
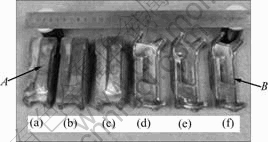
Fig.5 Thixoforged magazine plate components using semi-solid billets prepared by three methods: (a) and (d) SSIT of cast material; (b) and (e) Common SIMA; (c) and (f) New SIMA
As shown in Fig.6, grains of thixoforged magazine plate using semi-solid billet prepared by SSIT of cast material are very coarse and their average grain size is above 200 μm. At the same time, shape of grain is not close to globular one and microstructure is inhomo- geneous. Average grain size of thixoforged magazine plate component using semi-solid billet prepared by common SIMA is about 100 μm and some globular grains occur in the microstructure. However, its microstructure is inhomogenous and there is an obvious segregation in its microstructure. Compared with previous two methods, there are fine globular grains with grain size of about 20 μm in the microstructure of thixoforged magazine plate component using semi-solid billet by new SIMA.
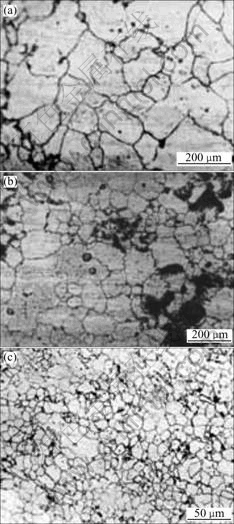
Fig.6 Microstructures of thixoforged magazine plates using semi-solid prepared by three methods: (a) SSIT of cast material; (b) Common SIMA; (c) New SIMA
Table 2 presents the mechanical properties of thixoforged magazine plate components using semi-solid billets prepared by three methods. It can be seen that the mechanical properties of thixoforged magazine plate components using semi-solid billets prepared by new SIMA are enhanced greatly. By using semi-solid billet prepared by new SIMA, mechanical properties of thixoforged magazine plate components such as yield strength(σs) of 201.4 MPa, ultimate tensile strength(σb) of 321.8 MPa and elongation of 15.3% can be obtained. It is fully demonstrated that new SIMA is a desirable method for preparing AZ91D magnesium alloy semi-solid billet. Furthermore, it is found that applying ECAE to strain induced step in SIMA is a good engineering application to semi-solid processing of magnesium alloy.
Table 2 Mechanical properties of thixoforged components using semi-solid billets prepared by three methods
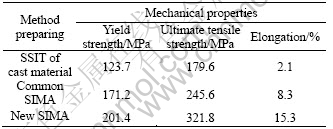
4 Conclusions
1) New strain induced melt activated (new SIMA) method for preparing AZ91D magnesium alloy semi-solid billet is introduced by applying equal channel angular extrusion into strain induced step in SIMA method.
2) Semi-solid billet with fine spheroidal grains with grain size of 18 μm can be prepared by new SIMA. Furthermore, average grain size of semi-solid is reduced with increasing extrusion pass of AZ91D magnesium alloy obtained in ECAE process.
3) By using semi-solid billet prepared by new SIMA, high mechanical properties of thixoforged magazine plate component, such as yield strength of 201.4 MPa, ultimate tensile strength of 321.8 MPa and elongation of 15.3%, can be obtained.
References
[1] MORDIKE B L, ELBERT T. Magnesium: properties-applications- potential [J]. Mater Sci Eng A, 2001, A302: 37-45.
[2] CHO W G, KANG C G. Mechanical properties and their micro- structure evaluation in the thixoforming process of semi-solid aluminum alloys [J]. J Mater Process Tech, 2000, 105: 269-277.
[3] WANG J G, LU P, WANG H Y. Semisolid microstructure evolution of the predeformed AZ91D alloy during heat treatment [J]. J Alloy Compd, 2005, 395: 108-113.
[4] CHAYONG S, ATKINSON H V, KAPRANOS P. Thixoforming 7075 aluminium alloys [J]. Mater Sci Eng A, 2005, A390: 3-12.
[5] LIU D, ATKINSON H V, KAPRANOS P, JIRATTITICHAROEAN W, JONES H. Microstructural evolution and tensile mechanical properties of thixoformed high performance aluminium alloys [J]. Mater Sci Eng A, 2003, A361: 213-224.
[6] PAES M, ZOQUI E J. Semi-solid behavior of new Al-Si-Mg alloys for thixoforming [J]. Mater Sci Eng A, 2005, A406: 63-73.
[7] TZIMAS E, ZAVALIANGOS A. Evolution of near-equiaxed microstructure in the semisolid state [J]. Mater Sci Eng A, 2000, A289: 228-240.
[8] CHINO Y, KOBATA M, IWASAKI H, MABUCHI M. An investigation of compressive deformation behaviour for AZ91 Mg alloy containing a small volume of liquid [J]. Acta Mater, 2003, 51: 3309-3318.
[9] HAGA T, KAPRANOS P. Thixoforming of laminate made from semisolid cast strips [J]. J Mater Process Tech, 2004, 157-158: 508-512.
[10] JAE C C, HYUNG J P. Microstructural characteristics of aluminum 2024 by cold working in the SIMA process [J]. J Mater Process Tech, 1998, 82: 107-116.
[11] SAKLAKOGLU N, IETEM S I, TANOGLU M, OZTAS O, CUBUKCUOGLU O. Mechanical properties and microstructural evaluation of AA5013 aluminum alloy treated in the semi-solid state by SIMA process [J]. J Mater Process Tech, 2004, 148: 103-107.
[12] JIANG Ju-fu, LUO Shou-jing. Reheating microstructure of refined AZ91D magnesium alloy in semi-solid state [J]. Trans Nonferrous Met Soc China, 2004, 14(6): 1074-1081.
[13] SEGAL V M. Severe plastic deformation: simple shear versus pure shear [J]. Mater Sci Eng A, 2002, A338: 331-344.
[14] ROSACHOWSKI A, OLEJNIK L. Numerical and physical modelling of plastic deformation in 2-turn equal channel angular extrusion [J]. J Mater Process Tech, 2002, 125-126: 309-316.
[15] HUANG W H, CHANG L, KAO P W. Effect of die angle on the deformation texture of copper processed by equal channel angular extrusion [J]. Mater Sci Eng, 2001, A307: 113-118.
[16] CHEN Y C, HUANG YY, CHANG C P. The effect of extrusion temperature on the development of deformation microstructures in 5052 aluminium alloy processed by equal channel angular extrusion [J]. Acta Mater, 2003, 51: 2005-2015.
[17] KIM I, KIM J, LEE D H, HWANG S K. Effects of equal channel angular pressing temperature on deformation structures of pure Ti [J]. Mater Sci Eng A, 2003, A342: 302-310.
[18] MABUCHI M, IWASAKI H, YANASE K. Low temperature superplasticity in an AZ91 magnesium alloy processed by ecae [J]. Scriptia Mater, 1996, 36: 681-686.
[19] SEGALl V M. Engineering and commercialization of equal channel angular extrusion (ECAE) [J]. Mater Sci Eng A, 2004, A386: 269-276.
[20] JIANG Ju-fu. Research on Preparing AZ91D Semi-Solid Billets by New SIMA and its Thixoforging [D]. Harbin: Harbin Institute of Technology, 2005. 28-40. (in Chinese)
Foundation item: Project(50475029, 50605015) supported by the National Natural Science Foundation of China
Corresponding author: JIANG Ju-fu; Tel: +86-451-86415464; E-mail: jiangjufu@hit.edu.cn
(Edited by YANG Bing)