
Effect of Y and Y2O3 on oxidation of AZ91D Mg alloys between 400 ℃ and 500 ℃
Sang-Hwan BAK, Dong-Bok LEE
School of Advanced Materials Science and Engineering, Sungkyunkwan University, Suwon, 440-746, Korea
Received 18 June 2008; accepted 10 March 2009
Abstract: AZ91D, AZ91D+1%Y, and AZ91D+3%Y2O3 (mass fraction) alloys were cast, and oxidized between 400 and 500 ℃ in air. The oxidation resistance increased in the order of AZ91D, AZ91D+3%Y2O3, and AZ91D+1%Y, indicating that Y was more effective than Y2O3 in increasing the oxidation resistance of the Mg alloys. However, all the alloys tested experienced ignition because the major oxide was MgO.
Key words: magnesium; yttrium; yttria; oxidation
1 Introduction
The application of magnesium alloys as light-weight structural materials is increasing due to their excellent merits such as high specific strength, rigidity, and the lowest density among metallic materials in practical use[1]. However, most Mg alloys possess poor strength and low resistance to corrosion and creep at elevated temperatures[2-3]. Hence, various alloying elements were attempted to increase the oxidation resistance of Mg alloys during casting for commercial usage.
The ignition temperature for the AZ91 alloy (Mg-8.2Al-0.7Zn, in mass fraction, %) is 580-590 ℃ in air[3]. However, WE43 alloy (Mg-4Y-0.6Zr-3RE with Nd, in mass fraction, %) has not burned up to 750 ℃, because an Y-rich oxide quickly formed in the cracked region of the oxide layer[1]. The rare earth element, Y, increased the oxidation resistance of the pure Mg metal and, much effectively, the AZ 91D alloy because of the compact Y2O3 film formed on the surface[4]. When Mg-Y-Ce alloys were oxidized at 600 ℃ for 0.5 h, dense, compact oxide films having Y2O3 formed[5]. When yttrium was added to Mg-Ca alloys, the oxide layer had a double-layered structure of MgO/CaO and Y2O3, playing a role of very effective barriers to improve the high-temperature oxidation resistance[6]. During the early oxidation of Mg-Y alloys (w(Y)=0.82%, 1.09%, 4.32%, 25%) at high temperatures, the increase of Y led to the decrease of the oxidation rate[7]. On the other hand, it is well established that small additions of Y2O3 dispersoids or Y2O3-coating on the alumina-[8] and chromia-forming alloys[9] improve scale adhesion and reduce the scale-growth rate. However, it is not yet adequately confirmed whether such a beneficial effect of Y2O3 is operative in the Mg alloys or not. Mg alloys form the non-protective MgO scale. In this study, AZ91 alloys, AZ91 alloyed with 1%Y, and AZ91 alloys containing 3%Y2O3 particles were cast, and oxidized between 400 ℃ and 500 ℃ in order to find the effect of the reactive element of Y and its oxide, Y2O3, on the high temperature oxidation of AZ91D alloys.
2 Experimental
Commercially available AZ91D alloys were melted at 680 ℃ in steel crucible under a CO2+1% SF6 protective atmosphere using an electric resistance furnace. While the alloy melt was rotated with a speed of 800 r/min for uniform mixing using a stirrer positioned at top of the crucible, either Y (98.5% purity, <350 μm) or Y2O3 particles (99.9% purity, 6 μm) were added with a feed rate of 7 g/min[10]. Mg alloys cast were AZ91D, AZ91D+1%Y, and AZ91D+3%Y2O3.
The Mg alloy samples were cut into coupons of 5 mm×10 mm×10 mm in size, ground to a 1 000 grit finish, degreased, and oxidized in an electrical furnace between 400 ℃ and 500 ℃ in atmospheric air. The oxidized specimens were inspected by a scanning electron microscope (SEM), an X-ray diffractometer (XRD), and an electron probe microanalyzer (EPMA).
3 Results and discussion
When Mg alloys were exposed to hot air, they suffered from severe oxidation or even burning after certain time. This resulted in the complete disintegrating into oxide powders. The time when local burning began to occur in the specimen was defined as the oxidation limit, and the values for AZ91D, AZ91D+1%Y and AZ91D+3%Y2O3 alloys are listed in Table 1. As expected, the oxidation rate increased rapidly with an increase in the oxidation temperature. It is seen that the addition of Y is more effective than that of Y2O3 in increasing the oxidation resistance. The oxide scales formed initially was thin and protective. But, they were eventually destroyed sooner or later during oxidation testing.
Table 1 Oxidation limit of prepared Mg alloys
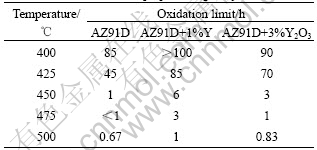
Fig.1 shows the XRD patterns of AZ91D+1%Y before and after oxidation in air. AZ91D+1%Y consisted primarily of α-Mg and a small amount of Al12Mg17 (Fig. 1(a)), being analogous to the AZ91D alloy. This is consistent with the fact that the Mg-9%Al melt solidifies into α-Mg and Al12Mg17(s) by the eutectic reaction upon cooling, according to the Mg-Al binary phase diagram. Yttrium was not detectible in Fig.1. However, Y is believed to exist as Al2Y, owing to its strong binding energy with Y[11]. The oxide scale formed before ignition was too thin to detect using XRD, as shown in Fig.1(b). Generally, initially formed, thin oxide scales became thick, and loosely-adherent as oxidation progressed. The ignition of the alloy led to the formation of MgO-rich oxide scales, as shown in Fig.1(c). Since the amount of Mg was the largest, predominantly the MgO scale formed, regardless of the oxidation temperature and time.
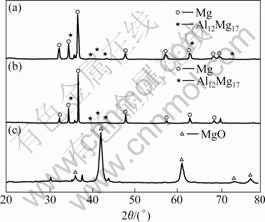
Fig.1 XRD patterns of AZ91D+1%Y: (a) As-cast; (b) Oxidized at 400 ℃ for 100 h; (c) Oxidized at 450 ℃ for 20 h
Fig.2 shows XRD patterns of AZ91D+3%Y2O3 before and after oxidation in air. As did AZ91D+1%Y, AZ91D+3%Y2O3 also consisted primarily of α-Mg and a small amount of Al12Mg17 (Fig.2(a)). Here, a faint indication of Y2O3 particles added is seen. In Fig.2(b), a strong MgO pattern is seen, resulting from the ignition of the alloy. The ignition resulted in the formation of thick, porous oxide scales. In this study, Y and Y2O3 added have not improved the oxidation resistance significantly. This must be originated from the inherently highly poor oxidation resistance of Mg alloys.
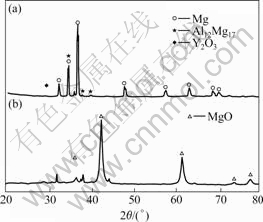
Fig.2 XRD patterns of AZ91D+3%Y2O3: (a) As-cast; (b) Oxidized at 450 ℃ for 25 h
Fig.3 shows the SEM top view and cross-sectional image of the oxide scale formed on AZ91D+1%Y. The scale formed initially was generally thin and uniform. Oxide nodules formed locally (Fig.3(a)). A thin, compact scale formed on the alloy, consisting of the α-Mg grains and the eutectic Mg/Al12 Mg17 mixture (Fig.3(b)). As the oxidation progressed, a porous, non-adherent, thick, and fragile scale or nodules having a cauliflower morphology formed. Oxide nodules formed by local ignition, and spread over the whole surface as oxidation progressed.
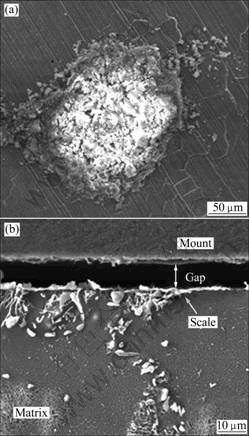
Fig.3 SEM images of scale formed on AZ91D+1%Y after oxidation at 400 ℃ for 100 h in air: (a) Top view; (b) Cross- sectional image
Fig.4 shows the SEM top view of the oxide scale formed on AZ91D+3%Y2O3. Usually thin scales fromed before ignition (Fig.4(a)). However, such scales were destroyed after ignition, forming porous, non-adherent, thick scales. The loosely adherent oxide layer shown in Fig.4(b) progressively became non-adherent, thick oxide powders.
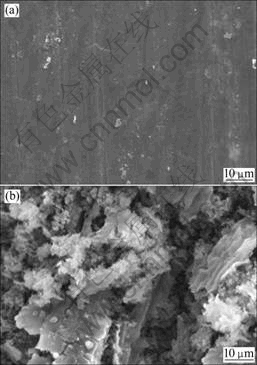
Fig.4 SEM top view of scale formed on AZ91D+3%Y2O3 after oxidation: (a) 425 ℃ for 10 h; (b) 475 ℃ for 1 h
Fig.5 shows the cross-sectional image and the corresponding EPMA line profiles of the AZ91D+ 3%Y2O3 after oxidation at 500 ℃ for 40 min. In Fig.5(a), the thin oxide layer is partially embedded in the mounting epoxy, because it is loosely adherent. In Fig.5(b), it is seen that the MgO-rich oxide layer was incorporated with a large amount of Al, and a small amount Zn and Y. Since the oxide layer was neither dense nor impervious, oxygen transported into the matrix rather easily along the phase boundaries of the Y2O3. Internally formed oxides consisted primarily of Mg, Al, Zn, and Y2O3. Further oxidation resulted in the sudden ignition, completely destroying the alloy.
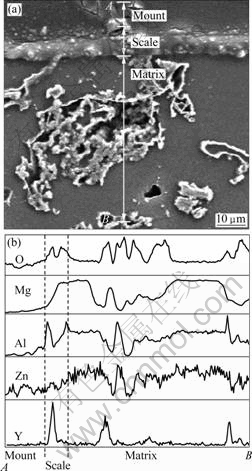
Fig.5 EPMA analytical results of AZ91D+3%Y2O3 after oxidation at 500 ℃ for 40 min: (a) Cross-sectional image (etched); (b) Line profile along A-B of (a)
4 Conclusions
The principal oxidation mode of AZ91D, AZ91D+1%Y, and AZ91D+3%Y2O3 alloys was similar. Before ignition, thin, uniform oxide scales formed on the surface. Oxide nodules continuously developed, as oxidation progressed. Finally, ignition occurred, forming non-protective oxides. Y2O3 and, moreover, Y were beneficial to increasing the oxidation resistance of Mg alloys to a certain extent. Apparently, Y2O3 scattered in the alloy provided short-diffusion paths such as phase boundaries. This favored the dissolution and transport of oxygen beyond the oxide scale. This may be one of the reasons for the less effectiveness of Y2O3 compared with Y in improving the oxidation resistance of Mg alloys.
Acknowledgment
This work is the outcome of a Manpower Development Program for Energy & Resources supported by the Ministry of Knowledge and Economy (MKE), Korea.
References
[1] RAVI KUMER N V, BLANDIN J J, SUERY M, GROSJEAN E. Effect of alloying elements on the ignition resistance of magnesium alloys [J]. Scripta Mater, 2003, 49: 225-230.
[2] CZERWINSKI F. The oxidation behavior of an AZ91D magnesium alloy at high temperatures [J]. Acta Mater, 2002, 50: 2639-2654.
[3] CZERWINSKI F. The early stage oxidation and evaporation of Mg- 9%Al-1%Zn alloy [J]. Corro Sci, 2004, 46: 377-386.
[4] FAN J F, YANG GC, CHEN SL, XIE H, WANG M, ZHOU YH. Effect of rare earths (Y, Ce) additions on the ignition points of magnesium alloys [J]. J Mater Sci, 2004, 39: 6375-6377.
[5] FAN J F, YANG GC, CHENG SL, XIE H, HAO W X, WANG M, ZHOU YH. Surface oxidation behavior of Mg-Y-Ce alloys at high temperature [J]. Metall Mater Trans, 2005, 36A: 235-239.
[6] YOU B S, KIM M H, PARK W W, CHUNG I S. Effects of Al and Y additions on the oxidation behavior of Mg-Ca base molten alloys [J]. Mater Sci Forum, 2003, 419/422: 581-586.
[7] WANG X M, ZENG X Q, ZHOU Y, WU G S, YAO S S, LAI Y J. Early oxidation behaviors of Mg-Y alloys at high temperatures [J]. J Alloy Compd, 2008, 460: 368-374.
[8] PINT B A, HOBBS L W. The oxidation behavior of Y2O3-dispersed γ-NiAl [J]. Oxid Met, 2004, 61: 273-292.
[9] CHEVALIER S, BONNET G, BORCHARDT G, COLSON J C, LARPIN J P. Mechanisms involved by reactive elements upon high temperature chromia scale growth [J]. Mater Sci Forum, 2001, 369: 327-336.
[10] KIM S K, KIM Y J. Rheological behaviour and fluidity of SiCP+ AZ91HP magnesium composites [J]. Mater Sci Technol, 2000, 16: 1-5.
[11] PARK W J, KIM N J. Identification of the dispersoid in a Mg-Al-Y alloy [J]. Scripta Metall Mater, 1995, 32: 1747-1752.
Foundation item: National 863 High Tech Project (2006AA03Z219); NUAA Foundation (S0417061); PCSIRT(IRT0534)
Corresponding author: Dong-Bok LEE; Tel: +82-31-290-7355; E-mail: dlee@skku.ac.kr
DOI: 10.1016/S1003-6326(08)60367-2
(Edited by YANG Bing)