J. Cent. South Univ. Technol. (2009) 16: 0354-0359
DOI: 10.1007/s11771-009-0060-0

Microstructural evolution during aging of
Ti-5Al-5Mo-5V-1Cr-1Fe alloy
ZHANG Shang-zhou(张尚洲)1, LIU Zi-quan(刘子全)1, WANG Guang-dong(王广东)1,
CHEN Li-qing(陈礼清)2, LIU Xiang-hua(刘相华)2, YANG Rui (杨 锐)3
(1. School of Environment and Materials Engineering, Yantai University, Yantai 264005, China;
2. State Key Laboratory of Rolling and Automation, Northeastern University, Shenyang 110004, China;
3. Institute of Metal Research, Chinese Academy of Sciences, Shenyang 110016, China)
Abstract: The evolution of microstructure on aging of an (α+β) titanium alloy (Ti-5Al-5Mo-5V-1Cr-1Fe) in the β and (α+β) solution-treated and quenched conditions was investigated. The presence of very fine ω phase was detected by electron diffraction for samples aged below 400 ℃. The fine α aggregates are uniformly formed within β grains by nucleating at the ω particles or β/ω interfaces. At higher temperature, the formation of ω phase is avoided and the α lamellae are precipitated at the preferred site of grain boundary and then within the matrix. The highest hardness values are found when the alloys are aged at 450 ℃ for β condition and 350 ℃ for (α+β) condition.
Key words: (α+β) titanium alloy; microstructure; precipitation; aging
1 Introduction
High-strength (α+β) titanium alloys are considered for a variety of aerospace structural applications. This type of alloy development is underway to optimize combinations of strength, toughness, fatigue and crack growth resistance [1]. These mechanical properties can be changed significantly through microstructural control by processing as well as heat treatment variations [2-3]. A problem often encountered in the aging treatment of the hardenable (α+β) alloys is microstructural inhomogeneity after solution treatment in the β or (α+β) phase field, which leads to potentially wide scatter of mechanical properties [4]. It has been established that α and ω phase precipitates appear depending on aging temperature and time in hardenable (α+β) or metastable β alloys [5-6]. The homogeneous nucleation and subsequent growth of finely dispersed α phase are accompanied by considerable improvement in mechanical properties. However, it is rather difficult to obtain a uniform and dispersed α phase distribution. Nevertheless, the precipitates of nanoscale ω phase particles are widely used to act as heterogeneous nucleation sites for α laths and a uniform distribution of α precipitates is obtained [7-8]. Thus, the changes during aging treatment must be evaluated in order to make accurate estimations of component life or to guide the alloy designer in improvement of alloy composition.
Ti-5Al-5Mo-5V-1Cr-1Fe alloy is a deeply hardenable (α+β) alloy, which is used below 400 ℃ for fan and compressor discs. The microstructural stability is one of the major concerns regarding its potential intermediate temperature application. In this alloy, the concentration of β stabilizing elements is sufficiently high that the metastable β phase can be fully retained at room temperature after rapid quenching. Two types of precipitates, namely ω and α phases, have been shown to form under specific aging treatment, thus causing drastic changes of mechanical properties [9]. It is essential to clarify the role of ω precipitates and fully understand detailed mechanism of ω→α transformation. The aim of this work is to optimize conditions for developing a required structure in Ti-5Al-5Mo-5V-1Cr-1Fe alloy after various heat treatments.
2 Experimental
The alloy was prepared by consumable electrode arc melting and had nominal chemical composition of Ti-5Al-5Mo-5V-1Cr-1Fe (mass fraction, %), with an (α+β)/β-transus temperature of about 870 ℃. The alloy was finish-forged in the (α+β) phase field to produce bars with 20 mm diameter. Samples of alloy were
heat-treated at 900 ℃ or 830 ℃, and followed by water quenching to produce equiaxed β grain and bimodal microstructure, respectively. The water quenched samples were then aged at various temperatures in the range of 300-650 ℃ for 8-48 h. All the heat treatments were carried out in air. The final heat treatment specimens were machined to remove the oxygen contaminated surface α case.
The specimens for microscopy were sectioned, mounted, and polished by standard techniques and etched in a solution of HF-HNO3 (the volume ratio of HF to HNO3 to H2O was 1?2?50). Thin foils for transmission electron microscopy (TEM) were prepared by a twin-jet electropolishing technique using a solution of 21% perchloric acid, 50% methanol and 29% n-butyl alcohol at -30 ℃. Microstructural examinations were performed using an MEF4A optical microscope, a JSM-6301F SEM, and a JEOL2000FXII TEM. Microhardness tests were carried out on the β matrix using 2.94 N load. At least 10 points were analyzed for each sample.
3 Results and discussion
The microstructure of as-forged sample consisted of primary α phase (αP) in the β matrix. Some of the samples were heat-treated at 900 ℃ for 1 h and then water-quenched. The microstructure is shown in Fig.1. A fully recrystallized equiaxed β grain structure is obtained but grain growth is significant. The average grain size is about 180 mm. The heat treatment was then followed by aging at 300-650 ℃ for different time.
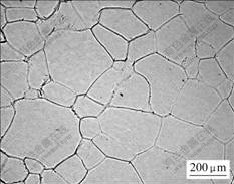
Fig.1 Optical micrograph of experimental alloy heat-treated at 900 ℃ for 1 h
As expected, the optical microscopy shows no microstructural difference when the sample is aged at 300 ℃. But the ω phase precipitations are clearly recognized in the specimens by TEM. Fig.2(a) shows the dark image using a
reflection and the selected area electron diffraction pattern in the specimen aged at 300 ℃ for 24 h. The dark field illumination indicates that large amount of small spherical ω particles are formed.
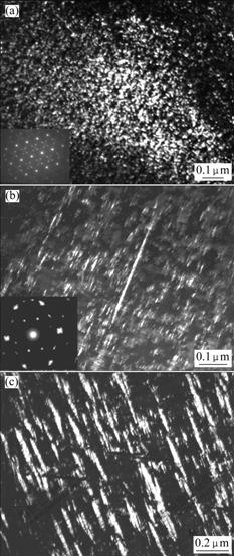
Fig.2 TEM micrographs of alloys after solution treatment at 900 ℃ for 1 h followed by aging at 300 ℃ (a), 350 ℃ (b), and 400 ℃ (c) for 24 h
This is consistent with the established orientation relationship between the ω and β phases, viz., {0001}w //{111}b , <11
0>w //<110>β . For the mechanism of ω phase formation, de FONTAINE et al [10] proposed a model that the (2/3)<111>β longitudinal displacement waves produced ω phase structure by yielding a local ordering of the displaced {111}β planes or the ω lattice can be obtained by collapsing one pair of (111) planes to the intermediate position, leaving the adjacent (111) planes unaltered.
For the alloy aged at 350 ℃ for a few minutes, the ω phase diffraction patterns could also be detected. But it was too weak to observe ω particles in the dark field. After long term exposure for 24 h, fine hexagonal α precipitates were only observed, as identified by TEM in Fig.2(b). Such a fine α phase is thought to nucleate at ω phase particles or the β/ω interfaces [11]. This suggests the possibility that ω phase particles can act as strong nucleation sites for hexagonal α phase and can be utilized for the microstructural control of α/β duplex phase structure to improve the mechanical properties. At the aging temperature of 400 ℃, fine α phase platelets are formed as the bands on specific crystallographic planes, as shown in Fig.2(c).
Fig.3 shows the micrographs taken from samples that were aged at 500, 600 and 650 ℃ for 24 h. Aging produces fine lathlike or platelike products aligning in specific orientations. With increasing aging temperature, the α precipitation in the β matrix significantly increases. As expected, the density of the precipitates increases with increasing aging time.
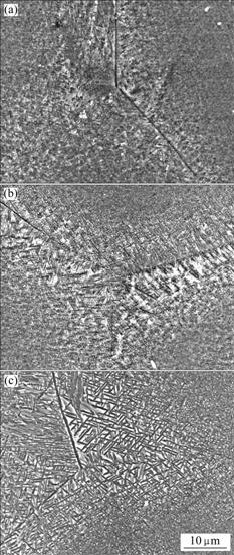
Fig.3 SEM micrographs of alloys after solution treatment at 900 ℃ for 1 h followed by aging at 500 ℃ (a), 600 ℃ (b) and 650 ℃ (c) for 24 h
α precipitates with high densities occur extensively on grain boundaries or within grains. However, uniform α precipitates are not observed. Fig.4 shows SEM and
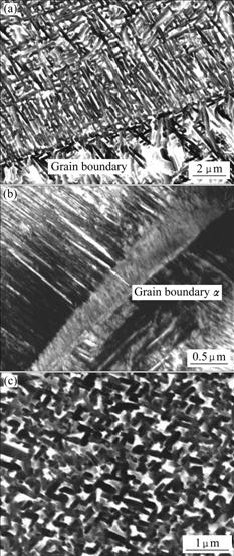
Fig.4 SEM and TEM micrographs of alloys after solution treatment at 900 ℃ for 1 h followed by aging at 600 ℃ for 16 h, showing α precipitates from grain boundary to interior of grain (a), on grain boundary (b), and within interior of grain (c)
TEM micrographs taken from sample that was exposed at 600 ℃ for 16 h. The α precipitates are coarser on β grain boundaries than those within grain, as shown in Fig.4(a), indicating that the α precipitations first take place on the preferred site of boundaries, followed by a matrix nucleation. It can also be seen from Fig.4(b) that at some sites of boundaries the precipitates appear columnar-like. This further suggests that they nucleate and grow from the boundaries. Fig.4(c) shows the high magnified SEM morphology of Fig.4(a) in the interior of β grain. The α precipitates are very fine.
It is proposed that grain boundary precipitate has a near rational orientation relationship with respect to one of the adjacent matrix grains but an irrational relationship with respect to the second grain [12]. The interphase boundary of the precipitate with the rationally oriented matrix is at least partly coherent and the other is incoherent. This strongly implies that the grain boundary precipitate nucleates coherently as much as possible with the rational matrix grains. Therefore, in the recrystallized matrix, a high-angle grain boundary plane plays a major role in variant selection for grain boundary nucleation [13]. In this work, the alloy was solution-treated in the β field phase. The matrix was fully recrystallized, forming a large β grain size. At precipitation aging temperature, grain boundary acts as preferential nucleation site, as shown in Fig.4. The α phase required a very small critical radius for nucleation in the matrix. Consequently the density of nuclei is high and nucleation takes place homogeneously throughout the matrix over a large span of aging temperatures.
Solution treatment in the (α+β) phase field leads to a bimodal microstructure consisting of globular primary α in the β matrix, with grain boundary α in discontinuous form, as shown in Fig.5.
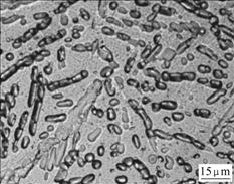
Fig.5 Optical micrograph of alloy heat-treated at 830 ℃ for 1 h
Fig.6 shows the TEM micrographs of the water-quenched specimens aged at 300 ℃ for 24 h. It is confirmed that both ω and α phase particles precipitate in the β matrix. It should be noted in Fig.6(b) that very fine α laths of the same orientation variant are imaged on these ω phase groups. In this case, the shape of the ω phase particles is distorted significantly by the formation of α laths, suggesting that nucleation of α occurs at the ω phase or β/ω interfaces, followed by the growth of the ω phase into the α precipitate, resulting in the very fine α plates.
A transformation mechanism from ω phase to α phase occurred by a mixed displacive and diffusive mechanism [14-16]. The three phases β, ω and α have the classical Bürgers orientation relations [16]:
β→ω with
and
,
ω→α with
and
.
Owing to the minimum misfit low index plane between ω and α phases, the activation energy for the nucleation of an α lath can be largely reduced. The nucleation of α platelets mainly occurs by displacive transformation in the core of ω particles, as shown in Fig.6(b). This leads to a perfect planar interface between the two phases and α is able to grow from the ω phase, which plays the role of precursor for its formation.
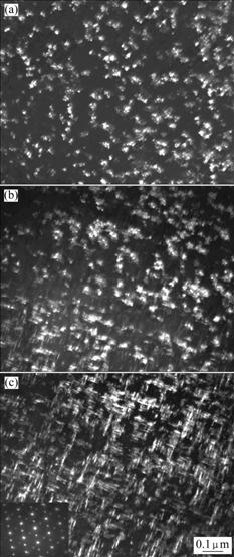
Fig.6 TEM micrographs of alloys aged at 300 ℃ for 24 h showing ω precipitates (a), distorting of ω particles (b), and α phase (c)
After nucleation from ω phase by displacive transformation, the α phase growth, however, is proceeded by either penetrating into ω particles or into the β matrix with consuming ω phase particles, leading to the plate-like morphology. As the ω phase completely disappears, the α phase growth is governed by the interface mobility between α and β phases.
The aging response of bimodal microstructure is somewhat different from fully lamellar microstructures because of the alloying element partitioning effect taking place during recrystallization treatment that leads to an enrichment of α-stabilizer (for example Al) in the primary α- and β-stabilizer (Mo, V, Cr, Fe) in β matrix. This alloy element partitioning effect has the consequence that the ω particles precipitate at lower aging temperature which are promoting the nucleation by formation of α phase in bimodal as compared with lamellar microstructure.
Oriented α precipitates within the β matrix appear and ω phase is no longer detected after aging above 350 ℃. But there is no remarkable indication of heterogeneous α precipitation on the grain boundary. The precipitation of α platelets is relatively uniform distribution throughout the matrix. An example in the case of aging at 600 ℃ for 24 h is shown in Fig.7.
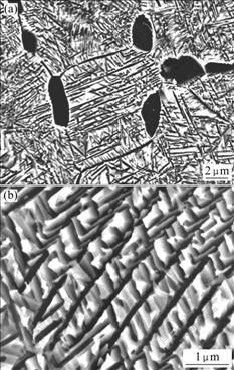
Fig.7 SEM micrographs of alloys after solution treatment at 830 ℃ for 1 h followed by aging at 600 ℃ for 24 h (a) and high magnified morphology in center of grain (b)
The matrix is completely recrystallized during solution treatment in the (α+β) phase field. Nucleation of the α precipitation also takes place first on grain boundary during aging treatment. But it is known that the main microstructural characteristic of bimodal microstructure is the small β grain size (about 8 mm). Owing to the large area of grain boundary, nucleation on grain boundary is considerably high. However, the small β grain size limits the length of grain boundary precipitates. Thus the α precipitates appear to be homogeneously distributed throughout the matrix.
Variations of microhardness of the water-quenched specimens in aging conditions are shown in Fig.8. The first point of the curves corresponded to the unaged material. It can be seen that the curves show a common feature: the microhardness increases with the increase of aging temperature, passes through maxima, and then decreases. However, it should be noted that for β solution-treated condition the microhardness reaches its maximum value at the aging temperature of 450 ℃ while in (α+β) condition at 350 ℃. The alloys that are heat-treated in β field and aged always present higher values than that in (α+β) condition. Since no alloy element partitioning effect is present for lamellar microstructure, the degree of aging-hardening is usually higher than that of bimodal microstructure. In all aging conditions, the maximum the microhardness occurs after about 8 h exposure. Later, there are only slight changes in microhardness with aging time.
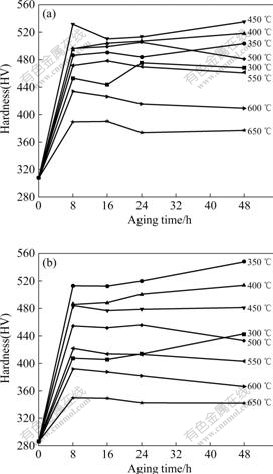
Fig.8 Plots of Vickers-microhardness vs aging time for alloys solution-treated at 900 ℃(a) and 830 ℃(b) for 1 h followed by aging at 300-650 ℃ for 8-48 h
The influence of aging at 300-650 ℃ on the microhardness can be understood on the basis of the observations of the nature of precipitation. The hardness increases when the sample is aged below 450 ℃ in the β water-quenched condition or below 350 ℃ in the (α+β) condition, which is considered to be related to the w precipitation in the β matrix. The formation of α phase contributes hardness to the β phase. The maximum in hardness is due to ω particles for the nucleation of α precipitations, leading to very fine α precipitations in the structure. Higher temperature aging treatment leads to the removal of nucleation sites for α precipitate within grains and thus to an increased tendency for grain boundary precipitation. The resultant extensive grain boundary precipitation leads to greatly reduced strength. Aging at higher temperature also leads to larger α precipitates that would be expected to be detrimental to strength.
4 Conclusions
(1) The microstructural features of Ti-5Al-5Mo-5V- 1Cr-1Fe alloy are studied after aging over a temperature range of 300-650 ℃ followed by solution treatment in the β and (α+β) phase field.
(2) Transmission electron microscopy studies reveal that aging below 400 ℃ produces uniform ω precipitations in the matrix and the ω particles are shown to behave as nucleation sites for extremely fine α lathes.
(3) At higher aging temperature the α precipitates are preferred on grain boundaries and have a near-Bürgers orientation relationship with respect to at least one of the adjacent β grains.
(4) The microhardness of the β solution-treated and aged condition is higher than those in (α+β) condition, and both conditions reach maximal values after about 8 h exposure.
References
[1] SEMIATIN S L, BIELER T R. The effect of alpha platelet thickness on plastic flow during hot working of Ti-6Al-4V with a transformed microstructure [J]. Acta Mater, 2001, 49(17): 3565-3573.
[2] LIU Yong, WEI Wei-feng, ZHOU Ke-chao. Microstructures and mechanical behavior of PM Ti-Mo alloy [J]. J Cent South Univ Technol, 2003, 10(2): 81-86.
[3] BRUSCHI S, POGGIO S, QUADRINI F. Workability of Ti-6Al-4V alloy at high temperatures and strain rates [J]. Mater Lett, 2004, 58(27/28): 3622-3629.
[4] LEI Li-ming, HUANG Xu. Effect of size and distribution of titanium carbide on microstructure and mechanical properties of Ti-25V-15Cr-2Al-0.2C-0.2Si alloy [J]. Trans Nonferrous Met Soc China, 2005, 15(4): 722-725.
[5] IVASISHIN O M, MARKOVSKY P E. Aging response of coarse- and fine-grained β titanium alloys [J]. Mater Sci Eng A, 2005, A405(1/2): 296-305.
[6] TEIXEIRA J D C, APPOLAIRE B. Modeling of the effect of the β phase deformation on the α phase precipitation in near-β titanium alloys [J]. Acta Mater, 2006, 54(16): 4261-4271.
[7] OHMORI Y, OGO T, NAKAI K. Effects of ω-phase precipitation on β→α, α″ transformations in a metastable β titanium alloy [J]. Mater Sci Eng A, 2001, A312(1/2): 182-188.
[8] SUKEDAI E, YAGI H, YOSHIMITSU D. Electron microscopy study on a new phase in β-titanium alloys aged at a high temperature [J]. Ultramicroscopy, 2004, 98(2/4): 209-218.
[9] YAKOVLEVA T Y. Dislocation structure of VT22 titanium alloy in cyclic loading with various loading frequencies [J]. Strength of Materials, 2000, 32(4): 331-338.
[10] de FONTAINE D, PATON N E, WILLIAMS J C. The omega phase transformation in titanium alloys as an example of displacement controlled reactions [J]. Acta Metall,1971, 19(11): 1153-1162.
[11] FERRANDINI P L, CARDOSO F F, SOUZA S A. Aging response of the Ti-35Nb-7Zr-5Ta and Ti-35Nb-7Ta alloys [J]. J Alloys Comp, 2007, 433(16): 207-210.
[12] FURUHARA T, MAKI T. Variant selection in heterogeneous nucleation on defects in diffusional phase transformation and precipitation [J]. Mater Sci Eng A, 2001, A312(1/2): 145-154.
[13] NIE J F, MUDDLE B C. Toward the overthrow of half of a major paradigm for interfacial structure deduction, with special attention to the massive transformation in Ti-46.5 A/O Al alloy [J]. Scripta Mater, 1998, 39(4/5): 637-645.
[14] WEISS I. Thermomechanical processing of beta titanium alloys—An overview [J]. Mater Sci Eng A, 1998, A243(1/2): 46-65.
[15] TAKEMOTO Y, HIDA M. Solute enrichment in the omega phase in Ti-14Mo [J]. Scripta Metall Mater, 1991, 25(2): 299-302.
[16] PRIMA F, VERMAUT P, TEXIER G, ANSEL D, GLORIAN T T. Evidence of α-nanophase heterogeneous nucleation from ω particles in a β-metastable Ti-based alloy by high-resolution electron microscopy [J]. Scripta Mater, 2006, 54(4): 645-648.
(Edited by YANG You-ping)
Foundation item: Project (50634030) supported by the National Natural Science Foundation of China; Project (2007DS04014) supported by the Program of Science and Technology of Shandong Province, China; Project supported by the Open Research Fund from the State Key Laboratory of Rolling and Automation, Northeastern University, China
Received date: 2008-09-26; Accepted date: 2008-12-08
Corresponding author: ZHANG Shang-zhou, Associate professor, PhD; Tel: +86-535-6706731; E-mail: szzhangyt@163.com