J. Cent. South Univ. Technol. (2010) 17: 102-109
DOI: 10.1007/s11771-010-0017-3 
Sintering technology for micro heat pipe with sintered wick
LI Xi-bing(李西兵)1, 2, 3, TANG Yong(汤勇)3, LI Yong(李勇)3, ZHOU Shu-zhang(周述璋)3, ZENG Zhi-xin(曾志新)3
1. Department of Mechanical and Power Engineering, Harbin University of Science and Technology,
Harbin 150080, China;
2. School of Mechanical Engineering, Qiqihar University, Qiqihar 161006, China;
3. School of Mechanical and Automotive Engineering, South China University of Technology,
Guangzhou 510640, China
? Central South University Press and Springer-Verlag Berlin Heidelberg 2010
Abstract: In order to study reasonable sintering technological parameters and appropriate copper powder size range of micro heat pipe (MHP) with the sintered wick, the forming principle of copper powders in wicks and MHP’s heat transfer capabilities were first analyzed, then copper powders with different cell sizes and dispersions were sintered in RXL-12-11 resistance furnace under the protection of the hydrogen at different sintering temperatures for different durations of sintering time, and finally the sintered wicks’ scanning electron microscope (SEM) images and their heat transfer capabilities were analyzed. The results indicate that the wick sintered with copper powders of larger cell size or smaller size range has better sintering properties and larger heat transfer capabilities; and that the increase of either sintering temperatures or sintering time also helps to improve the wick’s sintering properties and heat transfer capabilities, and the former affects more obviously than the latter. Considering both its manufacturing cost and performance requirements, it is recommended that copper powders with the size range of 140-170 μm are sintered at 900-950℃ for 30-60 min in practical manufacturing. In addition, two approaches to improve wick’s porosity are also proposed through theoretical analysis, which suggests that the larger the wick’s porosity, the better the heat transfer capabilities of the MHP.
Key words: micro heat pipe; copper powders; wick; forming principle
1 Introduction
In the past several decades, powder metallurgy technique has developed rapidly. Greater capillary pumping force and larger porosity can be obtained by sintering powders [1-2]. At present, powder metallurgy is the most economical, feasible and promising approach [3-6]. It is especially appropriate when larger porosity is needed. LEONG and LIU [7] sintered the mixture of Emultex D64 and copper powders with mean cell size of 63 μm at 800 and 1 000 ℃, respectively, to make the wicks of heat pipes and study their performances. ZHAO et al [8-9] illustrated that when K2CO3 is added into the copper powders with the particle size range of 53- 1 500 μm, the porosity of 50%-85% can be obtained in the sintered wick. The porosity of the Ti parts was improved by adding volatile substances of ammonium bicarbonate and carbamide powders into Ti powders to be sintered. AHMED et al [4] studied the relationships between the porosity and some technological parameters, such as sintering temperature, sintering time, pressure and the amount of naphthalene, and then deduced some empirical formulas. All the above studies are about sintering under high pressures and only suitable for the case of demanding smaller porosity, but not for the case of larger porosity in a thin layer of sintered copper powders in inner wall of slender copper tube.
With the development of microelectronic technique, power consumption and heat dissipation have become the bottleneck that hinders microelectronic technique from further development [10-11]. Micro heat pipes (MHPs) have many good characteristics, such as high heat conductivity, good isothermal temperature, variability of heat flux, reversibility of heat flow direction, thermodiode, heat switch performance, temperature steadiness and adaptability to environment [12-15], and greater heat transfer efficiency that is several hundredfold or even thousandfold of that of copper rod. As MHP’s heat transfer capability, to a large extent, depends on the capillary structure of its wick, manufacturing of MHPs’ sintered wicks has rigorous demands for quality, purity and cell size of a single copper powder, sintering temperature and sintering uniformity. In this work, the forming principle of copper powders in wicks and the influences of sintering technological parameters, such as copper powders’ size range, sintering temperature and sintering time, upon wick’s performances were analyzed. The future developments of sintered wicks were predicted through theoretical analysis. Thus, appropriate sintering technological parameters were determined, which could help to solve the technical problem of sintering a thin layer of copper powders in inner wall of slender copper tube with a larger porosity, so as to provide some technical data for manufacturing MHPs with sintered wicks.
2 Forming principle of sintering
Sintering is a process in which powders or powder- pressed green compacts are heated at appropriate temperatures and in appropriate atmospheres, with the results that powders are conglutinated and adhesive strength of sintered body is improved. According to thermodynamic principles, powders tend to conglomerate spontaneously, and superfine powders can gradually conglomerate after a long period of time even at room temperatures, but this conglomeration process is more obvious at high temperatures [16]. In the whole process of sintering, as the amplitude of atom vibration increases at high temperatures, the atoms begin to diffuse, which makes more atoms at the interface enter the scope of interatomic forces. Such increasing attractions among atoms make adhesive interfaces gradually take shape. With the extension of adhesive interfaces, the strength of sintered body increases. Single-component system sintering or homogeneous sintering, is defined as the sintering process of pure metal (or compound with a definite chemical composition, or uniform sosoloid powders) in the solid state, in which neither new compound nor new phase is generated, and nor does coacervation change. In single-component system sintering, there exists neither solution among elements nor formation of new compounds, except adhesion, compaction and the structural changes of pure metal. Since the principal mechanisms are diffusion and flow, the performances acquired are mainly determined by sintering temperature and sintering time.
As for MHPs with sintered wicks, the process of sintering copper powders in the inner wall of copper tube belongs to single-component system sintering. The pressure of protective gas remains relatively low in the entire forming process to enlarge the wick’s porosity. In the following experiments, copper powders were sintered in the inner wall of a copper tube under the protection of 99.999% H2, and other technological parameters were as follows: the pressure employed 0.03-0.05 MPa, the inner diameter of copper tube 5.2 mm, and the effective sintered length 235 mm. The forming principle of MHP’s sintered wicks is illustrated in Fig.1. The copper tube was firstly sealed by a big choke plug at one end, then a stainless mandrel was placed into this tube, and after that copper powders were primed into the tube from the other end, which was then sealed by a small choke plug. The whole apparatus formed was then placed on the steadier and sintered at some certain sintering temperatures in RXL-12-11 resistance furnace for some durations of time. After sintering, the mandrel and the two choke plugs were taken out by special tools, thus a sintered wick with certain porosity was made. The sintering process of copper powders in the container is illustrated in Fig.2. When the MHP is in operation, the sintered wick serves as the passage for fluid back flow, and the hole formed by the mandrel serves as the passage for vapor flow. Heat is transferred by the reciprocating motions of the working fluid from the hot end to the cold end under the capillary pumping force in the wick.

Fig.1 Forming principle for sintered wicks of MHP: 1—Small choke plug; 2—Copper container; 3—Copper powders; 4— Stainless mandrel; 5—Big choke plug
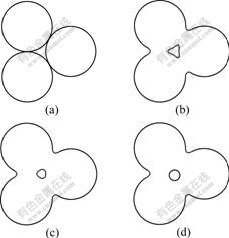
Fig.2 Models for sintering process of spherical powders: (a) Initial contact before sintering; (b) Neck growth in early stage of sintering; (c) Pore spheroidization at intermediate stage of sintering; (d) Pore spheroidization at late stage of sintering
3 Requirements of MHP’s heat transfer capabilities on its sintered wick
Wick’s performances directly determine MHP’s heat transfer capability. As the operating temperature of microelectronic chip is generally controlled to be around 60 ℃ to ensure its steady operation, nowadays, MHPs with an outer diameter of 6 mm are commonly used for chip heat dissipation. The main limits affecting MHP’s heat transfer capabilities are capillary limit and entrainment limit. And capillary limit refers to the heat quantity transferred by circulation of the working fluid in MHP. Since the circulation is driven by the capillary head between capillary structures in the wick and working fluid, MHP’s heat transfer capability is mainly determined by its wick’s performance. According to Chi’s assumption that heat load is homogeneously distributed in the evaporation and condensation sections, the capillary limit is deduced for the vapor flow that is incompressible and in the state of laminar flow as follows:
(1)
where Fv is the coefficient which is related to both Rev (the Reynolds’ number of vapor) and Mv (the Mach’s number of vapor)
(2)
(3)
When Rev≤2 300 and Mv≤0.2,
(4)
When Rev≤2 300 and Mv>0.2,
(5)
When Rev>2 300 and Mv≤0.2,
(6)
When Rev>2 300 and Mv>0.2,
(7)
In Eqs.(1)-(7), Q is the smaller value of capillary limit and entrainment limit; σ is the surface tension of working fluid; g is the acceleration of gravity; leff is the MHP’s effective length; ρ1 is the density of working fluid; dv is the diameter of wick’s chamber;
is the included angle between MHP and level plane; l is the MHP’s length; ε is the wick’s porosity; rs is the cell size of copper powders; μl is the viscosity of working fluid; δ is the thickness of sintered wick; hfg is the working fluid’s latent heat of vaporization; μv is the viscosity of working fluid vapor; ρv is the density of working fluid vapor; γv is the vapor’s specific heat capacity of ratio; R0 is the universal gas constant; Tv is the MHP’s operating temperature; and M is the relative molecular mass of working fluid.
Entrainment limit refers to the maximum heat quantity transferred when the vapor speed in MHP is high enough for shear stress existing at the vapor-liquid interface to tear apart the liquid on wick’s surface and then bring it into the vapor flow. In this case Weber’s number is 1. This phenomenon decreases the refluxing of working fluid and restricts heat transfer capability. The entrainment limit is deduced as follows when Weber’s number is 1:
(8)
It is indicated through analyzing Eqs.(1)-(8) that the factors influencing MHP’s heat transfer capability are such physical dimensions as thickness of sintered wick, cell size of copper powders and porosity of sintered wick, as well as some related parameters of working fluid and MHP’s working conditions. Furthermore, strength of sintered wick and some other performances influence MHP’s thermal resistance and operational life span. In order to improve MHP’s heat transfer capability, copper powders should be of larger cell size and size range as small as possible, while the porosity of sintered wick should be as large as possible. Thereinto, increasing the wick’s porosity is the most difficult and costly approach. Therefore, this investigation explored optimal sintering technological parameters, appropriate cell size and size range of copper powders, and the approaches to increasing wick’s porosity.
4 Influences of sintering technological parameters
4.1 Sintering temperature
Sintering temperature refers to the highest temperature when sintering, i.e., the holding temperature. Since the slenderness ratio of the sintered wick is very great (for example, a d6 mm MHP can amount to 200 mm in length or even longer) and the stainless steel mandrel must be drawn out after sintering, if the strength of sintered wick is not great enough, large numbers of copper powders will fall off when the mandrel is drawn out, which leads to the great increase of drawing force and even to the failure of drawing the mandrel out. In addition, the operational life span of MHP, the back flow resistance of working fluid and the thermal resistance of the wick also demand the sintering temperature to be set above a given value. With all these factors considered, sintering temperature should be set to be around 850 ℃, which was verified to be appropriate by experiments.
With the sintering thickness of 1.6 mm, copper powders of 140-170 μm size range were sintered in the inner wall of copper tube at 850, 900, 950 and 1 000 ℃ for 60 min, respectively. The sintered wicks’ SEM images of cross-sections magnified by 200 times are illustrated in Fig.3, and their corresponding values of porosity, maximum tension, strength limit, maximum torque and shear stress limit are shown in Table 1. The heat pipes with and without sintered wicks, which were from the same copper pipe and simultaneously sintered in the sintering furnace, were tested for their tensions and torques on a tensile machine and a machine for testing torsion respectively. Then the pullup curve and the torque curve of the two heat pipes were compared, and the maximum differences were the maximum tension and the maximum torque.
It is indicated from Fig.3 and Table 1 that with the increase of temperatures, the shape of pore space tends to become rounder, the exteriority of copper powders becomes smoother and the binding strength among copper powders becomes greater; while the wick’s porosity remains almost constant in this entire process. The reasons why the shape of pore space becomes rounder and the exteriority of copper powders becomes smoother are that both the diffusion and the flow of copper atoms accelerate with the rise of the temperatures when the sintering temperature is above the recrystallization temperature for copper powders. Incomplete-contact surface area of copper powders, the amount of gas and oxide-film on the exteriority of copper powders, and the gas products precipitated by volatile substances decrease with the rise of sintering temperatures, while the amount of the fused copper powders increases. Therefore, the binding strength of the sintered wick becomes larger. The reason why the wick’s porosity almost remains constant is that the porosity is related to the initial state rather than to the sintering process. In this experiment, as the copper powders of larger cell size were sintered in horizontally placed heat pipes with a smaller diameter under the protective gas of a relatively low pressure, the space occupied by the copper powders did not change at all. Therefore, porosity can be calculated by the amount of copper powders filled in unit volume. It is proved that the higher the sintering temperature, the greater the binding strength, the greater heat conductivity, the less the thermal resistance, the longer the MHP’s operational life span and the greater the heat rate transferred by MHP.
Table 1 Related performances of wicks sintered at different sintering temperatures for 60 min

4.2 Sintering time
Sintering time refers to the time duration holding for sintering at the highest sintering temperature, i.e., the holding time. With the thickness of 1.6 mm, copper powders of 140-170 μm size range were sintered in the inner wall of the copper tube at 950 ℃ for different durations of sintering time, i.e., 30, 60 and 90 min, respectively. The wicks’ SEM images of cross-sections magnified by 200 times are illustrated in Fig.3(c) and Fig.4, while the values of porosity, maximum tension, strength limit, maximum torque and shear stress limit are shown in Table 2.
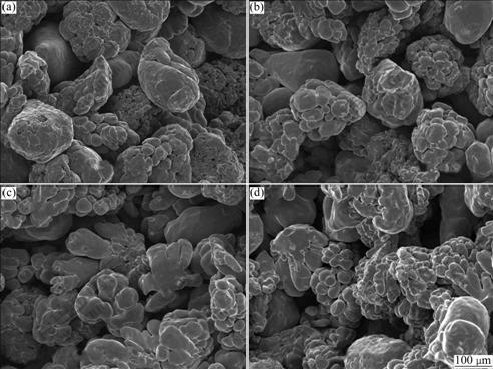
Fig.3 SEM images of wicks sintered at different sintering temperatures for 60 min: (a) 850 ℃; (b) 900 ℃; (c) 950 ℃; (d) 1 000 ℃
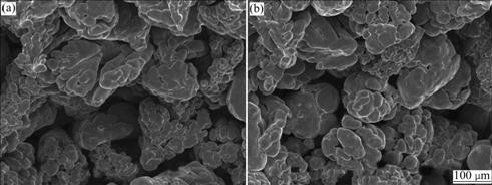
Fig.4 SEM images of wicks sintered at 950 ℃ for different durations of sintering time: (a) 30 min; (b) 90 min
Table 2 Related performances of wicks sintered at 950 ℃ for different durations of sintering time

It is indicated from Fig.3(c), Fig.4 and Table 2 that when the sintering temperature is fixed, the longer the sintering time, the better the performance of the sintered body. Sintering time influences the performance of the sintered body in the same way as sintering temperature, but the influences of sintering time are less obvious than those of sintering temperatures. The reason is the same as that in the case of increasing sintering temperature. Similarly, the wick’s porosity remains almost constant in the sintering process. Therefore, the flow resistance of working fluid in the wick decreases with the increase of the sintering duration, so does MHP’s radial thermal resistance. Thus, MHP’s operational life span can be extended and its heat transfer capabilities can be greatly improved. So it is concluded that the longer the duration of sintering time, the greater the binding strength, the less the radial thermal resistance, the longer the operational span and the greater the heat rate transferred by MHP.
With the influences of such related factors as sintering temperature and sintering time on MHP’s operational life span, manufacturing cost and heat transfer rate being considered, copper powders should be sintered at 900-950 ℃ for 30-60 min in practical manufacturing process.
5 Influences of copper powders’ geometric parameters
5.1 Copper powders with identical cell size range
The contact areas of copper powders with the same size range are different in a given volume, so is the performance acquired after being sintered. With the sintering thickness of 1.6 mm, copper powders with different cell sizes, i.e., 80-110, 110-140 and 140- 170 μm respectively (with the same cell size range of 30 μm), were sintered in the inner wall of the copper tube at 950 ℃ for 60 min. The sintered wicks’ SEM images of cross-sections magnified by 200 times are illustrated in Fig.3(c) and Fig.5, and the values of porosity, maximum tension, strength limit, maximum torque and shear stress limit are listed in Table 3.
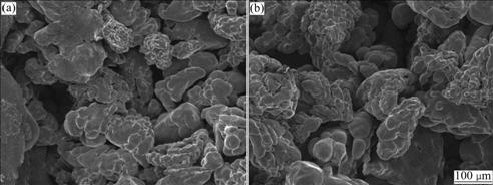
Fig.5 SEM images of wicks sintered by copper powders with different sizes at 950 ℃ for 60 min: (a) 80-110 μm; (b) 110-140 μm
Table 3 Related performances of wicks sintered by copper powders of with different cell size ranges

It is indicated from Fig.3(c), Fig.5 and Table 3 that when sintering temperature and sintering time are fixed, the larger the cell sizes of copper powders, the better the performances of the sintered body. But this improvement is not very great. The main reasons are that gas, oxide-film and gas products precipitated from volatile substances on the exteriority of copper powders are easy to be led out owing to the larger pore spaces between large particles, and that the contact areas of large copper powders are slightly larger than those of small powders. In addition, the porosity also remains almost constant because the arranging rule is uniform for the same cell size range. As illustrated in Fig.2, the larger the cell size of the copper powders, the larger the fusion splicing region, the greater the binding strength of the sintered wicks, the less the thermal resistance, the greater the heat rate transferred and the longer MHP’s operational life span. Besides, it can also be concluded through the theoretical analysis in section 2 that the larger the cell size of the copper powders, the larger the heat transfer rate. Therefore, the total heat rate transferred by MHP increases greatly.
5.2 Copper powders with different cell size range
Besides different contact areas, in a given volume the porosities of copper powders of different cell size ranges are different, so is the performance of the sintered wicks. With the sintered thickness of 1.6 mm, copper powders of different cell size ranges, i.e., <80, 80-110, 110-140 and 140-170, 80-140, 110-170 and 80- 170 μm, respectively, were sintered in the inner wall of copper tube at 950 ℃ for 60 min. The sintered wicks’ SEM images of cross-sections magnified by 200 times are illustrated in Fig.3(c), Fig.5 and Fig.6, and the values of porosity, maximum tension, strength limit, maximum torque and shear stress limit are shown in Table 3 and Table 4.
Table 4 Related performances of wicks sintered by copper powders of different cell size ranges at 950 ℃ for 60 min

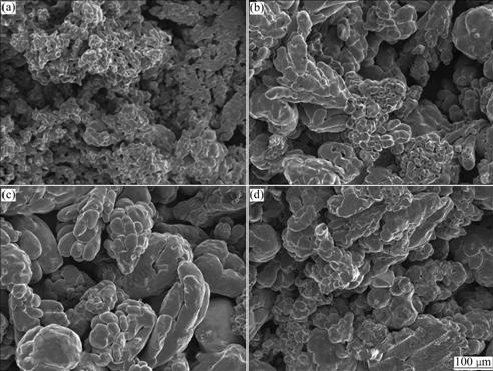
Fig.6 SEM images of wicks sintered by copper powders with different cell size ranges at 950 ℃ for 60 min: (a) <80 μm; (b) 80- 140 μm; (c) 110-170 μm; (d) 80-170 μm
It is indicated from Fig.3(c), Fig.5, Fig.6, Table 3 and Table 4 that when the sintering temperature and sintering time are fixed, the performances of sintered wicks will be weakened if copper powders with smaller cell size are added into copper powders of some cell size ranges, while the sintering properties will be improved if copper powders of larger cell size are added. Porosity changes slightly when the cell sizes are larger than 80 μm, while porosity varies a lot when the cell sizes are smaller than 80 μm. The main reason is that porosity is theoretically constant when copper powders of identical cell size are homogeneously arranged, and porosity decreases when powders of smaller cell size are mixed. But this law is applicable to globular powders. Practically, due to the irregular shapes of copper powders formed during the process of atomization—deoxidation—frag- mentation, when the powders of extensive cell size ranges are mixed, the looseness of copper powders increases contrarily. When copper powders are sintered with no extra external pressure, the porosity of sintered wicks is very large. And when copper powders are sintered with extra external pressure, the porosity of sintered wicks decreases with the increase of external pressure, and the porosity usually decreases faster than that of larger cell size powders. Moreover, copper powders’ self-weight also makes porosity decrease when the copper powders are sintered at high temperatures. Copper powders with cell size less than 80 μm were sintered at 950 ℃ for 60 min. The SEM image of pure spaces of sintered wick magnified by 15 times is illustrated in Fig.7. It is indicated by the figure that the self-weights of copper powders and the weight of mandrel make the looseness decrease and the gap between the wick and the inner wall surface of copper tube at the top left corner forms. This decreases the actual porosity and leads to nonuniform porosity distribu- tion with small porosity at the bottom and large porosity at the top. It can be concluded that the larger the cell size, the smaller the cell size range of copper powders, the greater the binding strength of the sintered wick, the less the thermal resistance, the longer MHP’s operational life span and the larger the heat rate transferred by MHP. Thus, the total heat rate transferred by MHP greatly increases.
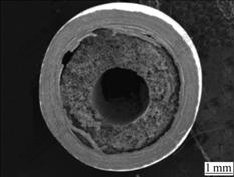
Fig.7 SEM image of pore spaces of sintering copper powders with cell size less than 80 μm at high temperature
Considering the influences of such related factors as cell size and cell size range of copper powders on the operational life span, manufacturing cost, thickness of sintered wick and MHP’s heat transfer rate, the copper powders with cell size range of 140-170 μm should be sintered in practical manufacturing.
6 Approaches to increasing porosity of sintered wick
With intensive concentration of microelectronic chips, more and more heat is accumulated within unit area, which poses stricter requirements on MHP’s heat transfer capability. When MHP sintered with common methods cannot satisfy the demands of microelectronic chips for heat dissipation, the technological problem of increasing wick’s porosity becomes urgent to be tackled. As for an excellent chip, the cost of its heat dissipating system accounts for 20%-40% of the chip’s total cost. Therefore, in order to meet the heat dissipation requirements of the electronic chips, the main consideration should be MHP’s heat transfer capability rather than its manufacturing cost.
It can be concluded through the theoretical analysis in section 2 that increasing porosity of the sintered wicks can transfer more heat. Therefore, to meet the increasing requirements on heat dissipation of microelectronic chips, two approaches seem to be rather promising to improve the wick’s porosity. One is to add volatile substances into the copper powders, such as ammonium bicarbonate powders, carbamide powders, K2CO3, organic glass powders and naphthalene powders, with stainless steel mandrel being employed to form MHP’s vapor chamber. When the temperature arrives at some values (lower than the sintering temperature) in the sintering process, these volatile substances begin to volatilize or to be decomposed to increase the wick’s porosity. As the force for drawing out the mandrel after sintering is usually very great, the wick’s structure may be destroyed in the process of drawing out the mandrel if too many volatile substances are added. Therefore, volatile substances cannot be added excessively when a mandrel is employed, and the wick’s porosity can only be increased by 5%-10% with this method. The other approach is to employ the mandrel made of volatile substances as well as to add volatile substances into the copper powders to be sintered. Thus, the vapor chamber is formed by the mandrel’s volatilization in the sintering process, and the wick’s porosity can be increased by 25%-30%. As the sintered wick cannot contain impurities, stricter requirements are posed on the purity of the additives in this case.
7 Conclusions
(1) As for the sintering technological parameters of copper powders in wicks, the sintering temperature should be set in the range of 900-950 ℃ and sintering time should be chosen in the range of 30-60 min. The wicks sintered under such sintering technological conditions have greater binding strength, less radial thermal resistance and higher cost performance.
(2) Copper powders with 140-170 μm cell size range should be sintered. The wicks sintered by such copper powders have greater binding strength, better uniformity, greater capillary pumping force and less back flow resistance.
(3) As for the microelectronic chips that have stricter requirements on MHP’s heat dissipation, volatile substances should be added into copper powders to increase the wick’s porosity, which consequently increases MHP’s heat transfer rate.
References
[1] ASHBY M F, EVANS A, FIECK N A, GIBSON L J, HUTCHINSON J W, WADLEY H N. Metal foams [M]. New York: Butterworth- Heinemann Ltd, 2000: 175-197.
[2] HYUN S K, NAKAJIMA H. Anisotropic compressive properties of porous copper produced by unidirectional solidification [J]. Materials Science and Engineering A, 2003, 340: 258-264.
[3] BANHART B J. Manufacture characterization and application of cellular metals and metal foams [J]. Progress in Materials Science, 2001, 46(6): 559-632.
[4] AHMED Y M Z, RIAD M I, SAYED A S, AHLAM M K, SHALABI M E H. Correlation between factors controlling preparation of porous copper via sintering technique using experimental design [J]. Powder Technology, 2007, 175(1): 48-54.
[5] GIBSON L J. Mechanical behavior of metallic foams [J]. Annual Review of Materials Science, 2000, 30: 191-227.
[6] MARKAKI A E, GERGELY V, COCKBURN A, CLYNE T W. Production of a highly porous material by liquid phase sintering of short ferritic stainless steel fibers and a preliminary study of its mechanical behavior composites [J]. Journal of Science and Technology, 2003, 63: 2345-2351.
[7] LEONG K C, LIU C Y. Characterization of sintered copper wicks used in heat pipes [J]. Journal of Porous Materials, 1997, 4(4): 303- 308.
[8] ZHAO Y Y, HANA F, FUNG T. Optimization of compaction and liquid-state sintering in sintering and dissolution process for manufacturing Al foams [J]. Materials Science and Engineering A, 2004, 364: 117-125.
[9] ZHAO Yu-yuan, FUNG Tung. Lost carbonate sintering process for manufacturing metal foams [J]. Journal of Scripta Materialia, 2005, 52(4): 295-298.
[10] CHEN Deng-ke. New technologies of electronics cooling [J]. Chinese Journal of Low Temperature Physics, 2005, 27(8): 255-262. (in Chinese)
[11] VASILIEV L L. Micro and miniature heat pipes: Electronic component coolers [J]. Applied Thermal Engineering, 2006, 28(4): 266-273.
[12] ZHUANG Jun, ZHANG Hong. Technology and application of heat pipe [M]. Beijing: Chemical Industry Press, 2000: 25-78. (in Chinese)
[13] TAN B K, WONG T N, OOI K T. Analytical effective length study of a flat plate heat pipe using point source approach [J]. Applied Thermal Engineering, 2005, 25(14/15): 2272-2284.
[14] TANG Yong, CHI Yong, CHEN Jing-chuang. Experimental study of oil-filled high-speed spin forming micro-groove fin-inside tubes [J]. International Journal of Machine Tools and Manufacture, 2007, 47(7/8): 1059-1068.
[15] ZHANG Guang-liang, ZHANG Shi-hong, LI Bing, ZHANG Hai-qu. Analysis on folding defects of inner grooved copper tubes during ball spin forming [J]. Journal of Materials Processing Technology, 2007, 184(1/3): 393-400.
[16] HUANG Pei-yun. Principles of powder metallurgy [M]. Beijing: Metallurgical Industry Press, 2004: 265-337. (in Chinese)
Foundation item: Key Project(50436010, U0834002) supported by the National Natural Science Foundation of China; Projects(50675070, 50705031) supported by the National Natural Science Foundation of China; Project(8151064101000058) supported by the Natural Science Foundation of Guangdong Province, China; Project(E200909) supported by the Natural Science Foundation of Heilongjiang Province, China
Received date: 2009-02-05; Accepted date: 2009-05-22
Corresponding author: LI Xi-bing, PhD; Tel: +86-13836240750; E-mail: lxbwjj@163.com
(Edited by CHEN Wei-ping)