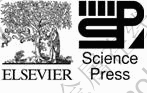
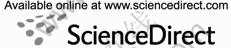

Trans. Nonferrous Met. Soc. China 22(2012) 853-857
Decarburization and improvement of
ultra fine straight WC-8Co sintered via microwave sintering
BAO Rui1, YI Jian-hong1,2, PENG Yuan-dong1, ZHANG Hao-ze1, LI Ai-kun1
1. State Key Laboratory of Powder Metallurgy, Central South University, Changsha 410083, China;
2. School of Materials Science and Engineering, Kunming University of Science and Technology,Kunming 650093, China
Received 22 April 2011; accepted 24 July 2011
Abstract: Cemented tungsten carbide with ultra fine grains was prepared via microwave sintering. η phase (W3Co3C) was formed on the surface of the samples during the preparation process. Extra carbon black was premixed and the influence of carbon content on mechanical properties was studied. The results show that the maximum value of hardness and transverse rupture strength are HRA 93.2 and 3396 MPa respectively when the carbon black content is 0.45%. The microstructure investigated by SEM show that the WC grains growth mainly occurs during the early stage of microwave sintering by the coalescence of grains.
Key words: cemented carbide; microwave sintering; carbon content; mechanical properties
1 Introduction
Cemented carbide with high quality and great performance is demanded with the rapid development of industry. Traditional cemented tungsten carbide is not able to fulfill the requirement of super-high hardness and strength at the same time. Ultra fine carbide alloy has been naturally attracted more and more attention in the last few decades because of its excellent hardness, toughness, wear resistance, thermal conductivity and other advantages [1,2]. However, rapid growth of ultra fine WC grains always happens during heating even the liquid phase is not formed [3]. A variety of new technologies, including spark plasma sintering [4-6], pulse plasma sintering [7] and ultrahigh pressure rapid hot consolidation [8] are employed to resolve this contradiction between grain growth and densification.
Microwave sintering (MS) [9] has also been employed to control the WC grain growth during the sintering process of cemented tungsten carbide. MS offers rapid and uniform heating, and makes it possible to achieve densification in reduced cycle time [10,11]. It is expected that the WC-Co sintered via microwave irradiation would be improved with better properties [12]. Over the last two decades, initial exploration of MS of WC-Co has been made [13]. BREVAL et al [12] compared the microstructures of the WC-Co sintered by conventional and microwave methods. They reported that the microwave sintered sample barely exhibited any growth of WC grains, and its mechanical properties were improved. Besides, they believed that with respect to the potential of saving energy consumption and protecting the environment, MS had a broad and promising prospect for the development and application [14].
Though some of the studies have been done on the MS of WC-Co powders, to the best of our knowledge, no report has been published on the relationship between the mechanical properties and carbon content of cemented tungsten carbide sintered via microwave irradiation so far. It is well known that total carbon content has a significant effect on the performance of carbide alloys [15], especially for ultrafine WC and Co powders. In this work, the influence of carbon content on ultrafine straight WC-8Co alloy was studied.
2 Experimental
Samples with a composition of WC-8Co (mass fraction, %) were prepared from WC (purity >99.9% and average size 0.4 μm, Golden Egret Special Alloy Co. Ltd., China) and Co (purity >99.9% and average size of 0.8 μm, Golden Egret Special Alloy Co. Ltd., China) powders. The additions of carbon black in the samples were 0, 0.30%, 0.35%, 0.40%, 0.45% and 0.50% (mass fraction), respectively. Mold paraffin (2.0%, mass fraction) was mixed to ensure the forming property. In order to show the characteristics and advantages of MS, no grain growth inhibitors were premixed in the WC-Co powder. The compacts were shaped into cylindrical and rectangular, and sintered in a microwave furnace with frequency of 2.45 GHz and maximum power of 5.5 kW after removing the molding paraffin in a conventional furnace. Temperature was measured using an infrared pyrometer (RaytekMM2MH, US) with an emissivity of 0.75. The compacts were placed in the center of alumina-?ber insulations with SiC served as a susceptor. The SiC susceptor was used and mounted encircling the compact to inhibit the heat loss [11]. The stage supporting the insulations turned clockwise at a speed of 5 r/min. The heating was adjusted by changing the input power of magnetron at a constant rate of 30 °C/min. The whole sintering process was carried out in pure N2 atmosphere [16].
The densities of the sintered specimen were determined by weighting in air and water using the Archimedes’ method. The hardness of the samples was measured on polished surfaces under a Rockwell hardness tester. The measurement was done at least five times for each sample, and the average value and the standard deviation was presented. The transverse rupture strength was measured using a material testing machine Instron 3369 at a speed of 1.0 mm/min, span of 30.00 mm. Each test examined three specimens, and the average value was used. The X-ray diffraction (XRD) was exploited for the characterization of morphology. The microstructures of the samples were observed under a scanning electron microscope (SEM, SIRION200) and optical microscopy after chemical etching in a Murakami solution (10 g K3Fe(CN)6+10 g NaOH+100 g H2O).
3 Results and discussion
3.1 Formation of eta phase
The compacts of sample A without the addition of C were sintered via microwave irradiation. The XRD analysis is shown in Fig. 1. There is an obvious difference between the surface and central region of the samples. By analyzing the morphology of the surface and central region, a great deal of eta phases (W3Co3C) are found in the surface region (see Fig. 1), but not in the central region.
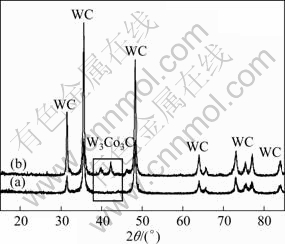
Fig. 1 XRD patterns of central (a) and surface (b) region of cylinder sample
In order to prove the results analyzed by XRD, the surface microstructure of sample was observed under optical microscopy (see Fig. 2). The eta phase is also found.

Fig. 2 Microstructure of WC-Co alloy sintered by microwave irradiation
There are two possible explanations account for this special phenomenon. The first possibility is microwave effect [17]. The migration rate of the nonmetal atoms increases drastically when the samples are exposed in the microwave irradiation field. This effect may make the carbon atoms unstable and very reactive with oxygen atoms which are absorbed during the green-compact processing and the micro amount of oxygen atoms in the protective atmosphere. The second reason is the opposite temperature distribution of microwave heating compared with traditional heating methods. The temperature in the central part of the sample is higher than that on the surface area. During the cooling stage, the solidification of binder phase is different from the center to the surface area, which results in the unbalance of liquid phase. It is easy for binder phase to migrate with carbon atoms and lead to the formation of eta phase [15].
A small amount of carbon black was premixed to look forward to resolving the problem of decarburization and exploring the relationship between the carbon black content and mechanical properties.
3.2 Influence of carbon black content
3.2.1 Density
Table 1 lists the effect of carbon black content on the density of the alloy sintered at 1350 °C for 5 min. MS has advantages such as high speed of heating rate, low temperature of sintering and short time of soaking. All of these advantages are quite useful to slow down the growth rate of grain. The influence of carbon black content on density is very small when the mass fraction is lower than 0.45%. The density of carbide alloy starts to decrease when the mass fraction is 0.50%, which is a result of disappearing of eta phase and formation of graphite phase. When the carbon content is lower, there is always a certain amount of eta phase in the samples. Eta phase is a kind of compacted phase. There is no obvious influence on the alloy density. However, the graphite phase is always supposed to be pores when the density of cemented tungsten carbide is studied. High added carbon content results in the formation of graphite phase and causes a dramatic drop of density. It is found that the formation of eta phase no longer occurred when the added carbon content is 0.45%.
Table 1 Effect of carbon black content on density of alloy
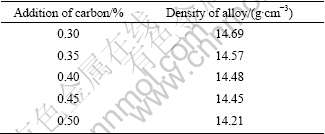
3.2.2 Hardness and transverse rupture strength
The effects of added carbon black content on the hardness and transverse rupture strength are shown in Fig. 3. It can be seen from Fig. 3 that the hardness reaches the highest value of HRA 93.2 at carbon black content of 0.45%. It seems that there is no significant change of hardness with increased added carbon black content until the addition reaches 0.50%. It may stem from the measurement method of hardness or the content of eta phase. The measurement of hardness is made on the polished surface of sintered samples. Besides, there is a certain amount of eta phase on the surface as discussed above. As a result, the measured value of hardness is higher than the actual value. The hardness of samples has a tiny difference when the added carbon black content is below 0.45% and shows a low value with 0.50% carbon black addition. This is because the graphite phase is formed when the total carbon content is beyond the range of WC-γ phase. Excessive amounts of carbon black exist in the form of graphite phase in the samples, which results in decreased hardness.

Fig. 3 Effect of carbon content on transverse rupture strength and hardness
The transverse rupture strength value increases with the increase of added carbon black content, and then decreases. The maximum value of 3396 MPa appears when the added carbon black content is 0.45%. It also can be explained by the formation of eta phase and graphite phase, both of which have a detrimental impact on the transverse rupture strength value due to stress concentration.
3.2.3 Microstructure
The microstructure of microwave sintered sample with carbon black content of 0.45% is shown in Fig. 4. It can be seen that the WC grains are all transformed to well-defined angular shaped platelets even the specimen is heated at a high heating rate and for short soaking time by MS. Some residual pores appear at the original grain boundaries or at the center of the perfect shaped grains, as marked by the square in Fig. 4(b) [18]. It means that the growth of WC grains is mainly related to the coalescence of grain-to-grain contacts. So, the heating rate at the early stage of sintering process can be increased to inhibit the grain growth. The surface and center area of the samples have the same microstructure when the carbon addition is 0.45%.
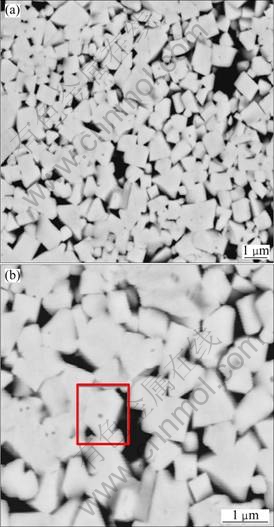
Fig. 4 SEM images of alloy with carbon black content of 0.45%: (a) Surface; (b) Center
4 Conclusions
1) Eta phase is formed easily on the surface of the alloys when they are exposed in the microwave irradiation field.
2) The method of premixing carbon black could avoid the formation of eta phase. The maximum values of hardness and transverse rupture strength can reach HRA 93.2 and 3396 MPa, respectively.
3) The same microstructures of the surface and central area are obtained when the carbon content is 0.45%.
4) Fast heating rate is beneficial to inhibit the growth of WC grains, which is related to the coalescence of grain-to-grain contacts in the early stage of MS.
References
[1] FANG Z Z, WANG X, RYU T, HWANG K S, SOHN H Y. Synthesis, sintering and mechanical properities of nanocrystailline cemented tungste carbide—A review [J]. International Journal of Refractory Metals & Hard Materials, 2009, 27: 288-299.
[2] XIONG Z, SHAO G, SHI X, DUAN X, YAN L. Ultra?ne hardmetals prepared by WC–10 wt.%Co composite powder [J]. International Journal of Refractory Metals & Hard Materials, 2008, 26: 242-250.
[3] WANG X, FANG Z Z, SOHN H Y. Grain growth during the early stage of sintering of nanosized WC-Co powder [J]. International Journal of Refractory Metals & Hard Materials, 2008, 26: 232-241.
[4] SHI X L, SHAO G Q, DUAN X L, YUAN R Z, LIN H H. Mechanical properties, phases and microstructure of ultra?ne hardmetals prepared by WC-6.29Co nanocrystalline composite powder [J]. Materials Science and Engineering A, 2005, 392: 335-339.
[5] SUN L, JIA C C, TANG H. Research on two sintered techniques of nanometer WC-Co powder [J]. Material Science Forum, 2007, 534-536: 593-596.
[6] SIVAPRAHASAM D, CHANDRASEKAR S B, SUNDARESAN R. Microstructure and mechanical properties of nanocrystalline WC–12Co consolidated by spark plasma sintering [J]. International Journal of Refractory Metals & Hard Materials, 2007, 25: 144-152.
[7] ARIA A K, MALIK H K. Numerical studies on wake?eld excited by Gaussian-like microwave pulse in a plasma ?lled waveguide [J]. Optics Communications, 2009, 28: 423-426.
[8] SHON I J, KIMA B R, DOHC J M, YOONC J K. Properties and rapid consolidation of ultra-hard tungsten carbide [J]. Journal of Alloys and Compounds, 2010, 489: L4-L8.
[9] SUNIL B R, SIVAPRAHASAM D, SUBASRI R. Microwave sintering of nanocrystalline WC–12Co: Challenges and perspectives [J]. International Journal of Refractory Metals & Hard Materials, 2010, 28: 180-186.
[10] AGRAWAL D, CHENG J, SEEGOPAUL P, GAO L. Grain growth control in microwave sintering of ultrafine WC-Co composite powder compacts [J]. Powder Metallurgy, 2000, 43: 15-16.
[11] GUO Ying-li, YI Jian-hong, LUO Shu-dong, ZHOU Cheng-shang, CHEN Li-fang, PENG Yuan-dong. Fabrication of W-Cu composition by microwave infiltration [J]. Journal of Alloys and Compounds, 2010, 492: L75-L78.
[12] BREVAL E, CHENG J P, AGRAWAL D K, GIGL P, DENNIS M, ROY R, PAPWORTH A J. Comparison between microwave and conventional sintering of WC/Co composites [J]. Materials Science and Engineering A, 2005, 391: 285-295.
[13] CHEN L M, DENNIS T, GIGL P, HAMPSHIRE B. Microwave sintering of submicron cemented carbides [J]. International Journal of Powder Metallurgy, 2007, 43: 49-57.
[14] OGHBAEI M, MIRZAEE O. Microwave versus conventional sintering: A review of fundamentals, advantages and applications [J]. Journal of Alloys and Compands, 2010, 494(1-2): 175-189.
[15] GUO J, FAN P, WANG X, FANG Z Z. Formation of Co-capping during sintering of straight WC–10 wt% Co [J]. International Journal of Refractory Metals & Hard Materials, 2010, 28: 317-323.
[16] ZHOU Cheng-shang, YI Jian-hong, LUO Shu-dong, PENG Yuan-dong, LI Li-ya, CHEN Gang. Effect of heating rate on the microwave sintered W-Ni-Fe heavy alloys [J]. Journal of Alloys and Compounds, 2009, 482: 6-8.
[17] DEMIRSKYI D, AGRAWAL D, RAGULY A. Densi?cation kinetics of powdered copper under single-mode and multimode microwave sintering [J]. Materials Letters, 2010, 64: 1433-1436.
[18] FANG Z, MAHESHWARI P, WANG X, SOHN H Y, GRIFFO A, RILEY R. An experimental study of the sintering of nanocrystalline WC–Co powders [J]. International Journal of Refractory Metals & Hard Materials, 2005, 23: 249-257.
微波烧结超细WC-8Co硬质合金中的脱碳及其改进
鲍 瑞1,易健宏1, 2,彭元东1,张浩泽1,李爱坤1
1. 中南大学 粉末冶金国家重点实验室,长沙 410083;
2. 昆明理工大学 材料科学与工程学院,昆明 650093
摘 要:通过微波烧结技术制备超细WC-Co硬质合金。烧结过程中在试样的表层形成脱碳相W3Co3C。在混料过程中添加炭黑,研究碳含量与合金力学性能之间的关系。结果表明:当碳含量为0.45%时,合金的硬度和断裂强度达到最大值,分别为HRA 93.2和3396 MPa。SEM观察发现在微波烧结超细硬质合金过程中,WC晶粒的长大主要为初期的合并长大。
关键词:硬质合金;微波烧结;碳含量;力学性能
(Edited by FANG Jing-hua)
Foundation item: Project (2008890) supported by the Scientific Research Foundation for the Returned Overseas Chinese Scholars, China
Corresponding author: YI Jian-hong; Tel: +86-731-88877328; Fax: +86-731-88710855; E-mail: yijianhong2007@sohu.com
DOI: 10.1016/S1003-6326(11)61256-9