J. Cent. South Univ. Technol. (2010) 17: 1207-1210
DOI: 10.1007/s11771-010-0620-3
Effects of carbon sources on electrochemical performance of Li4Ti5O12/C composite anode materials
LIU Ping(刘萍), ZHANG Zhi-an(张治安), LI Jie(李劼), LAI Yan-qing(赖延清)
School of Metallurgical Science and Engineering, Central South University, Changsha 410083, China
? Central South University Press and Springer-Verlag Berlin Heidelberg 2010
Abstract: Li4Ti5O12/C composite materials were synthesized by two-step solid state reaction method with glucose, sucrose, and starch as carbon sources, respectively. The effects of carbon sources on the structure, morphology, and electrochemical performance of Li4Ti5O12/C composite materials were investigated by SEM, XRD and electrochemical tests. The results indicate that carbon sources have almost no effect on the structure of Li4Ti5O12/C composite materials. The initial discharge capacities of the Li4Ti5O12/C composite materials are slightly lower than those of as-synthesized Li4Ti5O12. However, Li4Ti5O12/C composite materials show better electrochemical rate performance than the as-synthesized Li4Ti5O12. The capacity retention (79%) of the Li4Ti5O12/C composite materials with starch as carbon source, is higher than that of Li4Ti5O12/C composite materials with glucose and sucrose as carbon source at current rate of 2.0C.
Key words: lithium-ion battery; anode material; Li4Ti5O12; carbon; electrochemical performance
1 Introduction
Over the past few years, a surging demand for portable electronics and hybrid electric vehicles has increased the production of lithium-ion batteries and supercapacitors [1-2]. Spinel lithium titanate (Li4Ti5O12) is demonstrated as the most potential candidate for the anode materials in high power lithium-ion batteries as well as hybrid supercapacitors. The active material has a great lithium-ion intercalation and deintercalation reversibility and exhibits several advantages as follows: (1) high columbic efficiency (>95% at 1.0C) close to the theoretical capacity of 175 mA?h/g; (2) the discharge plateau at 1.55 V vs Li/Li+; (3) zero-strain insertion that provides little volume change during charge-discharge; (4) little electrolyte decomposition (little solid electrolyte interface and little gas evolution); and (5) inexpensive raw materials [3-8].
However, the conventional Li4Ti5O12 has a defect of poor electrochemical rate performance due to inherent poor Li+ diffusion coefficient (<10-6 cm2/s) and low electronic conductivity (<10-13 S/cm). So far, two typical approaches have been developed to overcome this problem. One is to improve the intrinsic electronic conductivity by cation doping (V5+, Mn4+, Fe3+, and Ni2+) [9-11]. The other is to synthesize Li4Ti5O12 with small particle size by adding conductive additives such as carbon and metal powders [12-14].
To improve the rate performance of Li4Ti5O12 materials for lithium-ion batteries in the large-scale application for hybrid electric vehicles, carbon is considered a good electric conductor, which is widely used in lithium-ion batteries. Moreover, carbon can take part in the control of active material particle growth, thus enhancing its conductivity [15-16]. It is important to optimize carbon sources that can lead to excellent electrochemical properties of Li4Ti5O12/C composite materials.
In this work, a simple solid-state reaction method was developed to synthesize the Li4Ti5O12/C composite materials using three different cheap carbon sources, i.e., glucose, sucrose, and starch. The effects of carbon sources on the Li4Ti5O12/C anode electrochemical performances were investigated by charge-discharge, and EIS electrochemical tests.
2 Experimental
The pristine Li4Ti5O12 was prepared by solid-state reaction. Li2CO3 and TiO2 powders with purities of 99.0% and 99.5% respectively, were used as the raw materials to synthesize Li4Ti5O12. Li2CO3 and TiO2 powders (the molar ratio of Li to Ti is 4.12:5.00) were mixed sufficiently in a rotary mill. After that, the mixtures were dried at 120 ℃ for 12 h in the vacuum oven. The powders were then pre-calcined at 650 ℃ for 8 h and continued to be treated at 800 ℃ for 6 h to form the crystalline structure of Li4Ti5O12 powders. The as-synthesized powder was denoted as LTO-P.
The Li4Ti5O12/C composite materials were prepared as follows: LTO-P and 2% (mass fraction) carbon sources (glucose, sucrose, and starch) were mixed in ethanol solvent and ground in a rotary mill for 2 h. Then, the mixture was dried at 120 ℃ for 8 h. The obtained powders were placed in a tubular furnace and sintered at 800 ℃ for 6 h in N2 atmosphere, and then cooled to the room temperature. The glucose-coated Li4Ti5O12/C, sucrose-coated Li4Ti5O12/C, and starch-coated Li4Ti5O12/ C composite powders were denoted as 4G2, 4S2 and 4F2, respectively.
The structures of the products were determined by an X-ray diffractometer (XRD, D/max-r A type Cu Kα1, 40 kV, 300 mA, 10?-85?, Japan). The morphologies of the products were observed by a scanning electron microscope (SEM, JEOL JSM-6360LV).
The anode was prepared by mixing 80% (mass fraction) active material, 10% carbon black and 10% polyvinylidene fluoride (PVDF). The mixture was made into slurry by milling using N-methyl-2 pyrrolidene (NMP) as the solvent. The electrodes were formed by coating the slurry onto Cu foils. After drying at overnight 393 K in a vacuum oven, the 2025 coin-type cells were assembled with the as-prepared anode, lithium metal and Celgard 2400 film in an ultrapure argon-filled glove box. The electrolyte was 1 mol/L LiPF6 dissolved in ethylene carbonate (EC)/dimethyl carbonate (DMC)/ethyl methyl carbonate (EMC) (1:1:1, in mass ratio). The electro- chemical measurements were performed by LAND CT2001A test system between 2.5 and 0.8 V at room temperature. And the EIS measurement at a constant potential of 1.55 V against Li metal electrode, was performed by an electrochemical workstation M273 with the amplitude of an alternating current signal of 5 mV and the frequencies ranging from 100 kHz to 10 mHz.
3 Results and discussion
3.1 XRD analysis
Fig.1 shows the XRD patterns of the Li4Ti5O12 and Li4Ti5O12/C composite materials. The XRD results are in good agreement with JCPDS file (card No.49-0207), confirming that pure Li4Ti5O12 was formed. The diffraction peaks can be indexed on the spinel structure Li4Ti5O12 with the space group Fd3m and without any impurity phase peaks. No diffraction response of carbon in the XRD patterns is observed since it is in low content and amorphous state [12]. The carbon sources have no effect on the spinel structure of Li4Ti5O12 during the sintering reaction. The results indicate that carbon is in amorphous form, which is not incorporated in the Li4Ti5O12 crystal lattice.
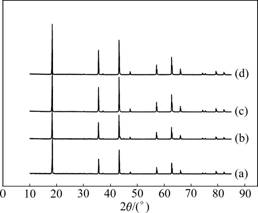
Fig.1 XRD patterns of different samples: (a) LTO-P; (b) 4G2; (c) 4S2; (d) 4F2
3.2 Morphology
The as-synthesized LTO-P has a very white color without any different color dots, while the Li4Ti5O12/C composite powders are deep gray or black in visual inspection. Scanning electronic micrographs (SEM) of the prepared products are shown in Fig.2. The surface of the as-synthesized LTO-P composite powders is inclined to be smooth, since they agglomerate from independent sphere-like micro particles. However, the surface of Li4Ti5O12/C composite powders is coarse and the particles of the Li4Ti5O12/C composite materials appear to be finer because of the existence of carbon. The carbon can exist in the place among the Li4Ti5O12 particles and the surface of Li4Ti5O12 particles. Such a carbon network can lead to electrical interparticle connection, which results in improving the electronic conductivity. However, it can be seen that the SEM images of Li4Ti5O12/C composite materials from glucose, sucrose, and starch have no distinct difference. Further investigation will be performed by TEM analysis.
3.3 Electrochemical performance
The electrochemical performance in terms of initial charge-discharge of Li4Ti5O12 and Li4Ti5O12/C composite materials are shown in Fig.3. It can be seen that the charge-discharge plateau is quite flat. The discharge plateau potential and charge potential are about 1.53 and 1.57 V, respectively. Moreover, it can be seen that the coulomb efficiency of all the products are close to 100%, which suggests that the products have good reversibilty. In addition, the initial discharge capacity of Li4Ti5O12 is 168.7 mA?h/g, slightly higher than that of Li4Ti5O12/C composite materials. The initial discharge capacities of 4G2, 4S2, and 4F2 are 154.3, 158.6, and 159.0 mA?h/g, respectively.
Fig.4 shows the cycling performance of Li4Ti5O12 and Li4Ti5O12/C composite materials at various charge- discharge current rates of 0.1, 0.2, 0.5, 1.0 and 2.0C. This result shows high discharge rate capability and good cycling stability of the Li4Ti5O12/C composite material. It is related to the high electrical conductivity of Li4Ti5O12/C composite materials [12, 15]. When the charge-discharge current rate is 0.1C, the discharge capacity of Li4Ti5O12/C composite materials is lower than that of Li4Ti5O12. With the increase of the discharge current rate, when the current rate exceeds 0.2C, the discharge capacity of Li4Ti5O12/C composites is superior to that of Li4Ti5O12. Among the Li4Ti5O12/C composite materials, it can be seen that the capacity retentions of 4G2, 4S2, and 4F2 are almost equal. However, when the discharge current rate is 2C, 4F2 shows the highest capacity retention of 79%. The capacity retentions of 4G2 and 4S2 are 68% and 72%, respectively.
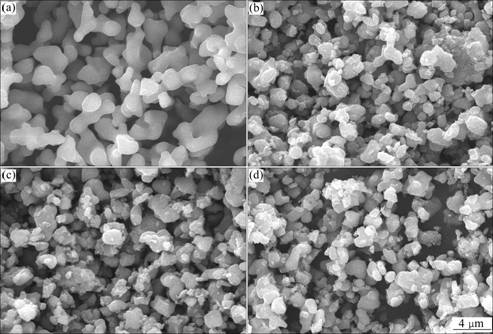
Fig.2 SEM images of different samples: (a) LTO-P; (b) 4G2; (c) 4S2; (d) 4F2
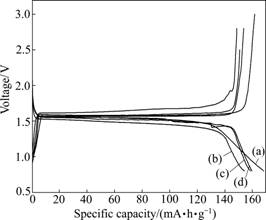
Fig.3 Charge-discharge profiles of Li4Ti5O12 and Li4Ti5O12/C composite materials: (a) LTO-P; (b) 4G2; (c) 4S2; (d) 4F2
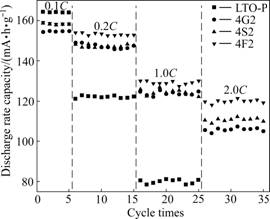
Fig.4 Cycling behaviors of Li4Ti5O12 and Li4Ti5O12/C composite materials at different discharge current rates: (a) LTO-P; (b) 4G2; (c) 4S2; (d) 4F2
To further investigate the difference of electrochemical performances of the three Li4Ti5O12/C composite materials and understand the carbon coating effect in more detail, EIS measurements were carried out in order to compare the conductivity of the three Li4Ti5O12/C composite materials. The Nyquist plots of 4G2, 4S2, and 4F2 are depicted in Fig.5. An intercept in Re Z axis in high frequency corresponds to the ohmic resistance (RΩ), which represents the resistance of the electrolyte. The depressed semicircle in the high frequency range is related to the Li-ion migration resistance (Rct-C) through carbon layer formed on the anode surface. The second semicircle in the middle frequency range indicates the charge transfer resistance (Rct). The inclined line in the lower frequency represents the Warburg impedance, which is associated with Li-ion
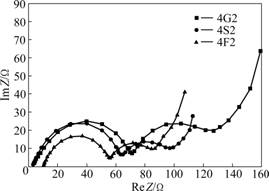
Fig.5 Nyquist plots for different samples (Z is impedance of sample): (a) 4G2; (b) 4S2; (c) 4F2
diffusion in the Li4Ti5O12 particles. It is found that the migration resistance (Rct-C) through carbon layer and charge transfer resistance of 4F2 are smaller than those of the 4S2 and 4G2.
This indicates that the coating layer obtained from the starch enhances the electrical contacts between Li4Ti5O12 particles better than glucose and sucrose. Considering the resistance, the Li4Ti5O12/C composite materials from starch show the lowest resistance, suggesting that the carbon greatly improves the performance of the active materials.
Therefore, the Li4Ti5O12/C composite materials from starch show high initial capacity, good rate capability indicating the promising anode material for lithium-ion battery.
4 Conclusions
(1) Using glucose, sucrose, and starch as carbon sources, Li4Ti5O12/C composite materials are obtained by heating the mixture of carbon sources and the spinel Li4Ti5O12 firstly synthesized by a solid-state reaction method with two-step calcination.
(2) The XRD results show that Li4Ti5O12/C composite materials show the spinel structure and carbon have almost no effect on the structure of Li4Ti5O12/C composite materials.
(3) The initial discharge capacity of the Li4Ti5O12/C composite materials is slightly lower than that of the as-synthesized Li4Ti5O12. The initial discharge capacities of 4G2, 4S2, 4F2 are 154.3, 158.6, and 159.0 mA?h/g, respectively.
(4) Li4Ti5O12/C composite materials show better electrochemical rate performance than as-synthesized Li4Ti5O12. The capacity retention (79%) of the Li4Ti5O12/C composite materials using the starch is higher than that of glucose and sucrose under 2.0C rate, indicating the promising anode material for lithium-ion battery.
References
[1] Scrosati B, Garche J. Lithium batteries: Status, prospects and future [J]. Journal of Power Sources, 2010, 195: 2419-2430.
[2] K?TZ R, CARLEN M. Principles and applications of electrochemical capacitors [J]. Electrochimica Acta, 2000, 45(15/16): 2483-2498.
[3] MAJIMA M, UJIIE S, YAGASAKI E, KOYAMA K, INAZAWA S. Development of long life lithium ion battery for power storage [J]. Journal of Power Sources, 2001, 101: 53-59.
[4] CHRISTENSEN J, SRINIVASAN V, NEWMAN J. Optimization of lithium titanate electrodes for high-power cells [J]. Journal of The Electrochemical Society, 2006, 153(3): A560-A565.
[5] LU W, BELHAROUAK I, LIU J, AMINE K. Thermal properties of Li4/3Ti5/3O4/LiMn2O4 cell [J]. Journal of Power Sources, 2007, 174: 673-677.
[6] JIANG C, ICHIHARA M, HONMA I, ZHOU H. Effect of particel dispersion on high rate performance of nano-sized Li4Ti5O12 anode [J]. Electrochimica Acta, 2007, 52: 6470-6475.
[7] STEWART S, ALBERTUS P, SRINIVASAN V, PLITZ I, PEREIRA N, AMATUCCI G, NEWMAN, J. Optimizing the performance of lithium titanate spinel paired with activated carbon or iron phosphate [J]. Journal of The Electrochemical Society, 2008, 155(3): A253- A261.
[8] WU H M, BELHAROUAK I, DENG H, AOUIMRANE A, SUN Y K, AMINE K. Development of LiNi0.5Mn1.5O4/Li4Ti5O12 system with long cycle life [J]. Journal of The Electrochemical Society, 2009, 156(12): A1047-A1050.
[9] KUBIAK P, GARCIA A, WOMES M, ALDON L, OLIVIER- FOURCADE J, LIPPENS P, JUMAS J. Phase transition in the spinel Li4Ti5O12 induced by lithium insertion: Influence of the substitutions Ti/V, Ti/Mn, Ti/Fe [J]. Journal of Power Sources, 2003, 119/121: 626-630.
[10] MUKAI K, ARIYOSHI K, OHZUKU T. Comparative study of Li[CrTi]O4, Li[Li1/3Ti5/3]O4 and Li1/2Fe1/2[Li1/2Fe1/2Ti]O4 in non-aqueous lithium cells [J]. Journal of Power Sources, 2005, 146: 213-216.
[11] CHEN C H, VAUGHEY J T, JANSEN A N, DEES D W, KAHAIAN A J, GOACHER T, THACKERAY M M. Studies of Mg-substituted Li4-xMgxTi5O12 spinel electrodes (0≤x≤1) for lithium batteries [J]. Journal of The Electrochemical Society, 2001, 148(1): A102-A104.
[12] GAO J, YING J R, JIANG C Y, WAN C R. High-density spherical Li4Ti5O12/C anode material with good rate capability for lithium ion batteries [J]. Journal of Power Sources, 2007, 166: 255-259.
[13] WANG G J, GAO J, FU L J, ZHAO N H, WU Y P, TAKAMURA T. Preparation and characteristic of carbon-coated Li4Ti5O12 anode material [J]. Journal of Power Sources, 2007, 174: 1109-1112.
[14] KANAMURA K, UMEGAKI T, NAITO H, TAKEHARA Z, YAO T. Structural and electrochemical characteristics of Li4/3Ti5/3O4 as an anode material for rechargeable lithium batteries [J]. Journal of Applied Electrochemistry, 2001, 31: 73-78.
[15] DOMINKO R, GABERSCEK M, BELE M, MIHAILOVIC D, JAMNIK J. Carbon nanocoatings on active materials for Li-ion batteries [J]. Journal of the European Ceramic Society, 2007, 27: 909-913.
[16] KIM K, JEONG J H, KIM I J, KIM H S. Carbon coatings with olive oil, soybean oil and butter on nano-LiFePO4 [J]. Journal of Power Sources, 2007, 167: 524-528.
(Edited by CHEN Wei-ping)
Foundation item: Project(2007BAE12B01) supported by the National Key Technology Research and Development Program of China
Received date: 2010-5-12; Accepted date: 2010-10-14
Corresponding author: LI Jie, PhD, Professor; Tel: +86-731-88830649; E-mail: csulightmetals@126.com