
Effect of TiO2 cathode performance on preparation of Ti by electro-deoxidation
DU Ji-hong(杜继红)1,XI Zheng-ping(奚正平)1,LI Qing-yu(李晴宇)1,
XU Qian(许茜)2,TANG Yong(唐勇)1, 2,LI Zheng-xian(李争显)1
1. Northwest Institute for Nonferrous Metal Research, Xi’an 710016, China;
2. School of Materials Science and Metallurgy, Northwestern University, Shenyang 110006, China
Received 15 July 2007; accepted 10 September 2007
Abstract: To resolve the problem of low current efficiency and low reaction rate when preparing metal by electro-deoxidization method, various contents of CaO and CaCO3 were added into the TiO2 powder, which were compacted into pellets and sintered, and then conducted as the cathode. The morphology and contents of the cathode and products were studied by scanning electron microscopy and X-ray diffractometry, the effect of the additives were studied. The results show that formation of calcium titanate and change of microstructure within the cathode enhance the velocity of the direct electrochemical reduction of solid TiO2 to Ti.
Key words: titanium; molten salt; electro-deoxidization; additive; electrolysis activity
1 Introduction
Titanium has been widely used in aerospace, chemical engineering and pharmacy because it has high strength, low density, excellent corrosive resistance. Now used preparation technologies, eg the Kroll process, have drawbacks of high cost, complicated process, high energy consumption, pollution of toxic chlorine gas,so we need develop new preparation technology of titanium which is low cost, short process flow and environmentally friendly.
Electro-deoxidization of titania in molten salt is a novel method to prepare metal titanium by electrochemistry. The process flow is short and friendly to environment. Both of domestic and abroad researcher do much research work about preparation of titanium metal by electro-deoxidization of titania in molten salt[1-9], the cathode of FFC method is titania powder pressed via cool isostatic pressing and then sintered to pellet, because the electrolytic process involves with solid phase mass transfer and phase transition, the reaction rate is slow, and efficiency of electrolytic reaction is low, so the current efficiency of preparation of metal titanium is low. Many researchers do much work to resolve these problems. In this paper, various contents of CaO and CaCO3 were doped into TiO2 powders and
the doped powders pressed to pellets respectively to enhance the activity of the electrochemistry reaction of the cathode pallets, improve the electrolysis efficiency, lower the energy consumption. Microstructure transformation of the doped TiO2 which were compacted and sintered, and the effect of the dopants to electro-deoxidization reaction of the TiO2 cathode were studied.
2 Theoretical consideration
The electro-deoxidization in CaCl2 melt of TiO2 is a much complex reaction process. The overall reaction involves not only with molten salt electrochemistry, chemical thermodynamics, mass transfer, but also with phase transformation dynamics, etc. Recently, SCHWANDT et al[2-3] proposed that during different stages of preparation of metal titanium by electro- deoxidization, the control step of the reaction is also different.
Integrate the theory with CHEN et al[4-5], YAN et al[6-7], XU[10-11], DU[8-9,12] proposed factors affecting molten electro-deoxidization reaction rate proposed as follows.
2.1 Electrochemistry reaction factor
Electron transfer process between ionic melt and TiO2 cathode accompanies the reduction process of the TiO2 cathode:
4TiO2 +Ca2++2e = Ti3O5+CaTiO3 (1)
3TiO2+Ca2++2e = Ti2O3+CaTiO3 (2)
2TiO2 +Ca2++2e = TiO+CaTiO3 (3)
2CaTiO3+2e = CaTi2O4+Ca2++2O2- (4)
CaTi2O4+2e = Ca2++2TiO+2O2- (5)
TiO+2(1-δ)e = TiOδ+(1-δ)O2- (6)
2.2 Chemical reaction factor
The chemical reaction is as follows:
CaTiO3+TiO=CaTi2O4 (7)
2.3 Mass transfer processes
During the electro-deoxidization process of TiO2 cathode, mass transfer process in solid phase includes diffuseness of oxygen ion and titanium ion, diffuseness of molten salt in porous cathode, oxygen ion diffuseness and transfer in molten salt.
2.4 New phase formation and phase transfer processes
Because TiO2 in cathode reacts with Ca2+ in molten salt by electrochemistry mechanism, important intermediate products CaTiO3 and CaTi2O4 were created, which consists of perovskite and pseudo-pyromelane structure respectively; on the later period of electro-deoxidization reaction, the structure of the product is face-centered cubic TiO and close packed hexahedron Ti(O). The above process includes the process of nucleation and growth up of new phase. At the same time, because of partial Ti4+ are deoxidized, TiO2 are transformed from rutile to magneli phase, so small amount CaO or CaCO3 are doped into TiO2, the dopants would accur reaction as follows:
(8)
Rutile TiO2 will form cation impurity defect Ca″Ti, at the same time, on the basis of electroneutrality principle, the oxygen ion vacancy V″O will be formed in TiO2 crystal lattice, this will be propitious to diffuse of oxygen ion in solidoid during the electro-deoxidization process of cathode, along with the increase of defect of cathode, the amount of active site in solid cathode will be increased, which will promote the electrochemical reaction and chemical reaction. When CaO or CaCO3 are doped into TiO2, the cathode will probably form perovskite structure after sintering, which may act as crystal nucleus of intermediate product CaTiO3 of the electro-deoxidization reaction. This will improve the formation of CaTiO3 in cathode, and are likely to restrain over growth of CaTiO3 crystal.
Furthermore, decomposing and emitting of CO2 during sintering will affect pore distribution and pore size of TiO2 cathode doped CaCO3.
It is very important that the reaction of electro- deoxidization occurs in CaCl2 molten, both CaTiO3 and CaTi2O4 are just the intermediate product of electro- deoxidization, so comparing with pure TiO2 cathode, doped CaO or CaCO3 in cathode could not bring out impurity in final product.
3 Experimental
Various contents of CaO or CaCO3 were doped into TiO2 powder (AR grade), then it were compacted and sintered at different temperature to make into 2 g TiO2 pallets. Sintering temperature were 750, 900 and 1 200 ℃ separately. Using CaCl2 molten as electrolyte, sintered TiO2 as cathode, graphite rod as anode, the pallets were electrolyzed at 900 ℃ under 3.0 V for 6 h. Argon was admitted into the sealed reactor continuously when temperature was higher than 300 ℃. After electrolysis, the product was rinsed with distilled water, dried at low temperature of 100 ℃.
The microstructure and morphology of the cathode were studied by JSM-6400 scanning electron microscope (SEM). The contents of the product were analysed by INCA X-sight energy dispersive spectrum (EDS). Phase compositions of cathode were studied by D/max-2200PC X-ray diffraction (XRD).
4 Results sand discussion
The intensity of the TiO2 cathode is markedly increased after sintering, which prevents the cathode pulverization by molten salt during electrolysis, at the same time, the junction effect of powder particles of cathode is enhanced by high temperature sintering, which will improve constructing conduct net in TiO2 cathode.
Fig.1 shows the SEM images of TiO2 cathode which was compacted under 100 MPa, and sintered for 4 h at 750, 900 and 1 200 ℃ separately. It can be observed from the SEM images that the particle size of the cathode pallet sintered at 750 ℃ is much small, the particles are densely arranged, the particle size of the pallet sintered at 900 ℃ is larger, pore size between particles also grow larger, the particle size of the pallet sintered at 1 200 ℃ is about several 10 times larger than the pallet sintered at 750 ℃, pore size of the pallets is much larger. The densities of the three pallets sintered at different temperature are listed in Table 1. The sintering temperature greatly affects the volume density of the pallets, the volume density of the pallets sintered at 1 200 ℃ is the maximal. The density of the cathode pallets is controlled by the size of particle and array compactness of the pallets. Because the particles size increases and array compacts, the volume of the pallet is contracted after being sintered, and the density of the pallets increases. The cathode pallets sintered separately at 750, 900 and 1 200 ℃ were electrolyzed 6 h, microstructure and contents of the cross section were studied by SEM and EDS line scanning (Fig.2).
The results shows that the cathode pallets is layered after electrolysis, the main content of the outer layer is Ti, O content is very lower in out layer. But in inner layer, the oxygen content is higher, Ti content is relatively low, the thickness of metal layer of electrolyzed cathode pallets which were sintered at 750, 900 and 1 200 ℃ are 0.75, 0.70, 0.52 mm. Although the metal layer of the pallets sintered at 750 ℃ has the maximum thickness, but it’s intensity is so poor that it is incline to be pulverized by molten salt. So 900 ℃ is the optimal sintering temperature for the doped cathode pallets.
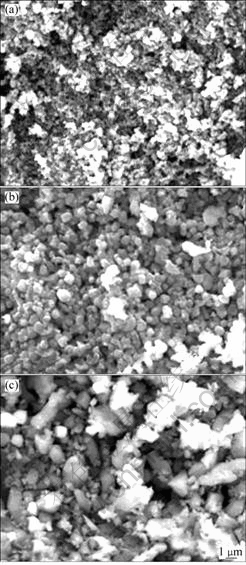
Fig.1 SEM images of TiO2 pellets after sintering at various temperatures for 4 h: (a) 750 ℃; (b) 900 ℃; (c) 1 200 ℃
Table 1 Densities of cathode under various sintering temperatures for 4 h

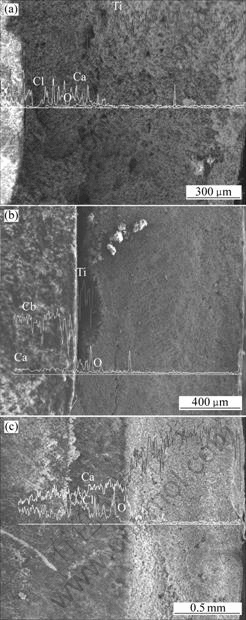
Fig.2 SEM images of TiO2 pellets electrolyzed for 6 h at 900 ℃ after sintering at various temperatures for 4 h: (a) 750 ℃; (b) 900 ℃; (c) 1 200 ℃
Fig.3 shows the SEM images of the sintered cathode pallets which doped with different concentration of CaO (mass fraction, %), macroscopically, volume of the pallets contract obviously after being sintered, and it’s intensity is enhanced too. It can be observed from Fig.3 that the particle size of the sintered cathode is smaller when the content of CaO is 1% and 5%, the particle size of the sintered cathode is obviously larger when content of CaO is 10% and 15%.
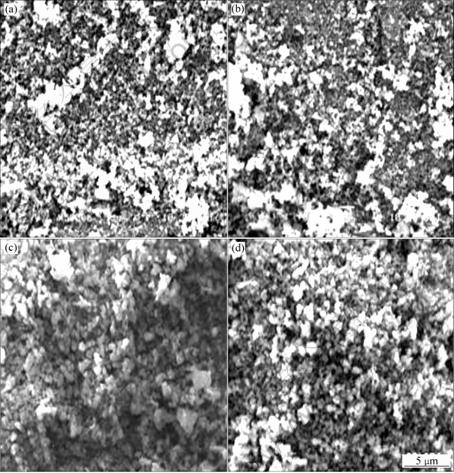
Fig.3 SEM images of TiO2 pellets with various contents of CaO after sintering at 900 ℃ for 6 h: (a) 1%; (b) 5%; (c) 10%; (d) 15%
Fig.4 shows the XRD pattern of the sintered TiO2 cathode pallets doped 10% CaO. There is diffraction peak of CaTiO3 in the XRD spectrum, indicating that TiO2 doped CaO would form new phase CaTiO3 after being sintered. Formation of CaTiO3 may be an important factor of growth of cathode pallets which doped 10% or 15%CaO after being sintered.
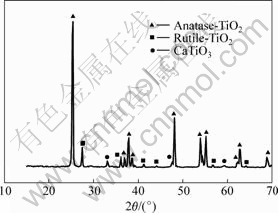
Fig.4 X-ray diffraction pattern of TiO2 pellets with 10% CaO after sintering at 900 ℃ for 6 h
From Fig.4 we found that there is two kinds of diffraction peaks of TiO2 for the cathode pallets after being sintered, rutile-TiO2 and Anatase-TiO2, no CaO peak is found, this may be explained as majority CaO reacted with TiO2 to produce CaTiO3. If all CaO (10%) dopes into TiO2 and forms CaTiO3, mass fraction of CaTiO3 in cathode is 24.29%.
Fig.5 shows SEM images of electrolyzed cathode pallets which doped different concentration of CaO. From Fig.5 we can know that after 6 h electrolysis, particle array of the cathode pallets doped 1% and 5% CaO is still compactly, the pore size of intergranular is relatively smaller. After 6 h electrolysis, intergranular pore size of the cathode pallets doped 10% CaO is obviously larger, and it’s microstructure is spongy, and the intergranular pore size of the cathode pallets doped 15% CaO is much larger.
Table 2 lists the comparison of oxygen content of pure TiO2 cathode pallets and TiO2 cathode doped different concentration CaO after electrolysis for 6 h, oxygen content of different cathodes reduced in different degrees, deoxidation affection of the cathode doped 15%CaO is the best, residual oxygen in product is 0.39%. In consideration that all doped CaO reacts with TiO2 to form CaTiO3, if concentration of 15% doped CaO is conversed to concentration of CaTiO3, its value is 36.43%, the research of GEORGE et al show that using CaTiO3 as raw material to prepare Ti by molten electro-deoxidation has higher electrolytic efficiency.
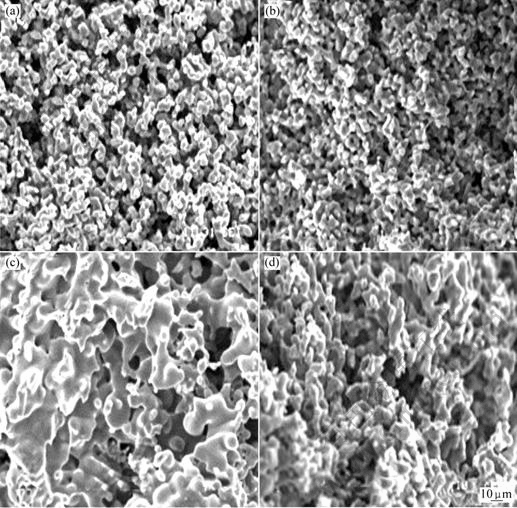
Fig.5 SEM images of TiO2 pellets with various contents of CaO after electrolysis at 900 ℃ for 6 h: (a) 1%; (b) %; (c) 10%; (d) 15%
Table 2 Oxygen contents of reduced TiO2 pellets with various contents of CaO after electrolysis at 900 ℃ for 6 h

Fig.6 shows XRD patterns of electrolyzed TiO2 cathode pallets doped with different concentration of CaO. From Fig.6 we know that when the doping amount is 1% and 5%, diffraction peaks of the product have some Ti protoxide and intermediate product CaTiO3. Beside Ti and very small quantity of impurity, when doped concentration is 15%, diffraction peak of the product only has Ti. In addition, appearance of many kinds of protoxide of Ti in XRD pattern illustrates that the electro-deoxidation reaction of TiO2 is a progressive process. Fig.7 shows SEM images of the TiO2 pellets doped various contents of CaCO3 after sintering at 900 ℃ for 6 h. From Fig.6 we know when the concentration of CaCO3 are 1% and 5%,the particle size of the sintered cathode is almost the same, when the content of CaO is 10% and 15%,the particle size of the sintered cathode grows larger. This is because the dopant CaCO3 decomposes to CaO and CO2 when it is sintered a 900 ℃, the more CaCO3 is doped, the more CaO is decomposed, the more new phase CaTiO3 is formed. Formation of CaTiO3 is verified by XRD patter (Fig.8) of sintered sample. The main phases of sintered cathode pallets are rutile-TiO2, anatase-TiO2, undecomposed CaCO3 and new phase CaTiO3.
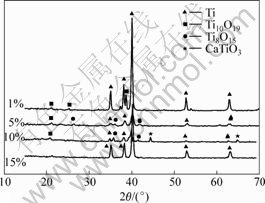
Fig.6 X-ray diffraction patterns of TiO2 pellets with various contents of CaO after electrolysis for 6 h
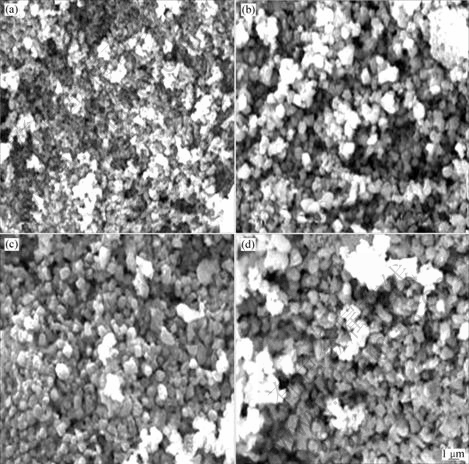
Fig.7 SEM images of TiO2 pellets with various contents of CaCO3 after sintering at 900 ℃ for 6 h: (a) 1%; (b) 5%; (c) 10%; (d) 15%
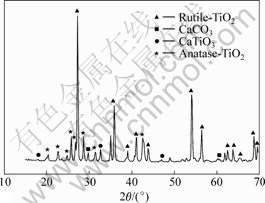
Fig.8 X-ray diffraction pattern of TiO2 pellets with 10% CaCO3 after sintering at 900 ℃ for 6 h
Fig.9 shows SEM images of the TiO2 pellets with various concentration of CaCO3 electrolysis at 900 ℃ for 6 h. Fig.9 shows that after 6 h electrolysis there is little intergranular pore in the cathode pallets doped 1% and 5% CaCO3; after 6 h electrolysis, pore size of intergranular of the cathode pallets doped 10% CaCO3 and 5% CaCO3 is obviously larger, and it’s microstructure is spongy.
Table 3 shows the comparison of oxygen content of TiO2 cathode doped with different participation CaCO3 after 6 h electrolysis, oxygen content of different cathode reduces in different degrees, deoxidation affection of the cathode doped 15%CaCO3 is the best, residual oxygen in product is not detected by EDS. If concentration of 15% doped CaCO3 is conversed to concentration of CaTiO3, it’s value is 21.48%, relative to same doping amount of CaO, deoxidation of 15% CaCO3 additive is better. One of the prime reasons is that CaCO3 is decomposed to liberating CO2 gases, this makes intergranular pore size much larger, moreover, pylome is probably formed in cathode which is favorable to ‘entry’ of molten salt, the new formed phase CaO is much activated which is more prone to form CaTiO3 with TiO2.
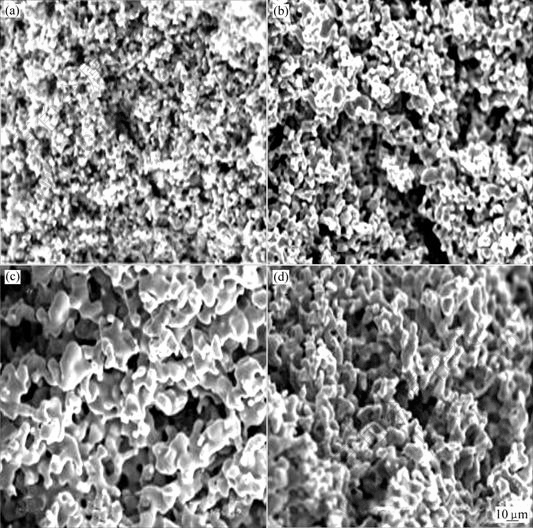
Fig.9 SEM images of TiO2 pellets with various contents of CaCO3 electrolysis at 900 ℃ for 6 h: (a) 1%; (b) 5%; (c) 10%; (d) 15%
Fig.10 shows the X-ray diffraction patterns of TiO2 pellets with various content of CaCO3 after electrolysis for 6 h. When doping amount of CaCO3 is 1% and 5%, there are much impurity peak in product XRD patters, when doping amount of CaCO3 is 10%. Electrolysis product are mainly Ti and some CaTiO3, the latter content is very low, the XRD peak of CaTiO3 is very weak. And when doping amount of CaCO3 is 15%, electrolysis product is almost entirely Ti and there is very little impurity peak. Some kinds of sub-oxide peak in XRD pattern confirms that the reduction of TiO2 is progressive.
Table 3 Oxygen contents of reduced TiO2 pellets with various contents of CaCO3 after electrolysis at 900 ℃ for 6 h

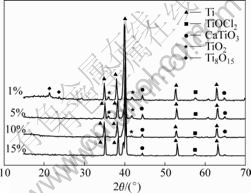
Fig.10 X-ray diffraction patterns of TiO2 pellets with various content of CaCO3 after electrolysis for 6 h
5 Conclusions
1) Volume density of TiO2 cathode varies with increment of sintering temperature. TiO2 cathode has optimal intensity and electrochemical reaction activity when it is compacted under 100 MPa and sintered for 6 h at 900 ℃, its volume density is 2.0 g/cm3, the pore size of TiO2 cathode is about 0.5 ?m.
2) Doping CaO or CaCO3 into TiO2 would affect the microstructure of cathode, formation of new CaTiO3 phase improves the electrochemical reaction activity, accelerates the reaction of electro-deoxidization.
3) When 1%-15% CaO is doped into TiO2, the electrochemical reaction activity of the cathode is improved with the increase of the concentration of the doped CaO, the product for the cathode doped 15% CaO after electro-deoxidization for 6 h has 99.3% metal titanium.
4) Doping 1%-15% CaCO3 into TiO2, the electrochemical reaction activity of the cathode is also improved with the increase of the concentration of doped CaO, the enhancement effect is preferable to that same doped concentration of CaO, the product for the cathode doped 15% CaCO3 after electro-deoxidization for 6 h does not detect oxygen by EDS, principal product is titanium.
References
[1] CHEN G Z, FRAY D J, FARTHING T W. Direct electrochemical reduction of titanium dioxide to titanium in molten calcium chloride[J]. Nature, 2000, 407: 361-364.
[2] SCHWANDT C, FRAY D J. Determination of the kinetic pathway in the electrochemical reduction of titanium dioxide in molten calcium chloride[J]. Electrochimica Acta, 2005, 51: 66-76.
[3] ALEXANDER D T L, SCHWANDT C, FRAY D J. Microstructural kinetics of phase transformations during electrochemical reduction of titanium dioxide in molten calcium chloride[J]. Acta Materialia, 2006, 54: 2933-2944.
[4] CHEN G Z, GORDO E, FRAY D J. Direct electrolytic production of chromium powder[J]. Metal Mater Trans B, 2004, 35B: 223-233.
[5] MA Meng, WANG Di-hua, WANG Wen-guang, HU Xiao-hong, JIN Xiao-bo, CHEN G Z. Extraction of titanium from different titania precursors by the FFC Cambridge process[J]. Journal of Alloys and Compounds, 2006, 420: 37-45.
[6] YAN X Y, FRAY D J. Production of niobium powder by direct electrochemical reduction of solid Nb2O5 in a eutectic CaCl2-NaCl melt[J]. Metall Mater Trans B, 2002, 33(B): 685-692.
[7] YAN X Y, FRAY D J. Electrochemical studies on reduction of solid Nb2O5 in molten CaCl2-NaCl eutectic(1)[J]. Journal of the Electrochemical Society, 2005, 152(1): D12-D21.
[8] DU Ji-hong, XI Zheng-ping, LI Qing-yu, LI Zhen-xian, TANG Yong. Activity of cathode for impact in TiO2 electrodeoxidation[J]. Journal of Rare Metals, 2007, 31(3): 336-340. (in Chinese)
[9] DU Ji-hong, XI Zheng-ping, LI Qing-yu, LI Zhen-xian, TANG Yong. Impact of CaCO3 doping on TiO2 performances[J]. Rare Metal Materials and Engineering, 2007, 36(1): 96-99. (in Chinese)
[10] DENG Li-qin, XU Qian, ZHAI Yu-chun, HUANG Zhen-qi. Preparation of niobium by direct electrochemical reduction of solid Nb2O5[J]. The Chinese Journal of Nonferrous Metals, 2005, 15(4): 541-545. (in Chinese)
[11] HU Xiao-feng, XU Qian. Preparation of tantalum by electro-deoxidization in a CaCl2-NaCl melt[J]. Acta Metallurgica Sinica, 2006, 42(3): 285-289. (in Chinese)
[12] DU Ji-hong, XI Zheng-ping, LI Qing-yu, LI Zhen-xian, TANG Yong. Process of reduction of TiO2 using electrodeoxidation[J]. Rare Metal Materials and Engineering, 2006, 35(7): 1045-1049. (in Chinese)
Foundation item: Project(50434030) supported by the National Natural Science Foundation of China; Project(2007CB613801) supported by the State Basic Research Program of China (973 Program)
Corresponding author: DU Ji-hong; Tel: +86-29-86231077; E-mail: Dujh@c-nin.com
(Edited by YANG Hua)