J. Cent. South Univ. (2016) 23: 2536-2541
DOI: 10.1007/s11771-016-3314-7

Improvement of thickness deposition uniformity in nickel electroforming for micro mold inserts
JIANG Bing-yan(蒋炳炎)1, 2, WENG Can(翁灿)1, 2, ZHOU Ming-yong(周明勇)1, 2,LV Hui(吕辉)1, 2, DRUMMER Dietmar3
1. State Key Laboratory of High Performance Complex Manufacturing (Central South University), Changsha 410083, China;
2. School of Mechanical and Electrical Engineering, Central South University, Changsha 410083, China;
3. Institute of Polymer Technology (Friedrich-Alexander-
Erlangen-Nürnberg),Am weichselgarten 9, 91058 Erlangen, Tennenlohe, Germany
Central South University Press and Springer-Verlag Berlin Heidelberg 2016
Abstract: Thickness deposition is a crucial issue on the application of electroformed micro mold inserts. Edge concentration effect is the main source of the non-uniformity. The techniques of adopting a non-conducting shield, a secondary electrode and a movable cathode were explored to improve the thickness deposition uniformity during the nickel electroforming process. Regarding these techniques, a micro electroforming system with a movable cathode was particularly developed. The thickness variation of a 16 mm×16 mm electroformed sample decreased respectively from 150% to 35%, 12% and 18% by these three techniques. Combining these validated methods, anickelmold insert for microlens array was electroformed with satisfactory mechanical properties and high replication precision. It could be applied to the following injection molding process.
Key words: deposition uniformity; nickel electroforming; secondary electrode; non-conducting shield; movable cathode; micro mold insert
1 Introduction
Today’s machining processes are facing challenges from advanced difficult-to-machine materials, stringent design requirements (high precision, complex shape, and high quality), and machining costs. The LIGA (from the German Lithographie, Galvanoformung, Abformung) and associated processes become important techniques for the fabrication of micro-electro-mechanical system (MEMS) components [1-5]. Electroforming is to form a metallic part, even with a complex shape, by electrolytic deposition on a substrate. Electroformed parts or molds have high replication accuracy, high hardness, and good mechanical strength, with a short cycle time. These parts or molds have been widely used in various fields such as aerospace, electronics and automotive industry [6-7].
The deposition uniformity of electroformed layer is one of the important factors restricting the application of electroforming methods. The deposited metal layer is naturally concave due to the edge concentration effect [8-10]. A number of methods have been proposed in the literature to improve the deposition uniformity. Pulse power supply, suitable bath agitation, proper temperature and appropriate cathode–anode arrangement have been found to be useful for improving the uniformity of electroformed layer [11-13]. The use of a shield was shown to be an effective and simple way to improve the current distribution uniformity. The deviation of the current density distribution was decreased from 35% to less than about 10% with a shield [14]. The rotation of a disk electrode provided a new approach to control over the nickel electroforming process without affecting electrochemical parameters. Deposition uniformity and deposition rate could be enhanced by the adjustment of rotating speed [15]. A piece of nickel mold insert of 15 inches. micro-prism patterned light guide panel was fabricated by electroforming process and successfully applied to the injection molding process for PMMA material [16].
The poor deposition uniformity would directly affect the performance of fabricated items. Several useful and simple methods are combined in this work to improve the deposition uniformity in electroforming for micro mold inserts and the improvement of each method are quantitatively analyzed. Micro lens array is a key component wildly used in the micro-optical system because of its unique optical properties [17-19].Combining these methods in process, a mold insert for micro lens array is fabricated by a self-designed micro electroforming system.
2 Theoretical analyses
Non-uniform deposition layer is caused by the different layer growth rates on cathode, which is mainly determined by the distribution of electrical field and the mass transfer of liquid phase.
2.1 Electrical field distribution
According to Faraday’s law, the mass of metallic nickel on cathode is proportional to the amount of an electric current and the time for which it flows on cathode. It can be described as
(1)
where m is the mass of metal on cathode; K is the constant of proportionality; Q is the amount of an electric current; I is the electrical current; t is the time.
With the Maxwell equations, the current density distribution on cathode is derived as
(2)
where is
the gradient operator; J is the current density; E is the electrical field intensity; γ is the electrical conductivity of the electrolyte; φ is the electrical potential of the electrolyte.
2.2 Flow field distribution
The uniformity of deposition layer is affected by the concentration of metal ion in the electrolyte, which is controlled by the flow field distribution. The mass transport is the coupled effect of diffusion and convection actions. The diffusive flux can be determined during the mass transfer by
(3)
where Jd,i is the diffusive flux; Di is the diffusion coefficient of i ion; Cb is the reactive ion concentration.
On the condition of convection, the ion concentration variation on cathode is determined as
(4)
where JC,i is the convective flux; υx is the vertical fluid velocity on cathode.
3 Materials and methods
3.1 Micro electroforming system
Micro electroforming equipment was self-designed with a movable cathode, which is able to fulfill the movements of rotating vertically and reciprocating horizontally. The motion parameters could be adjusted by a control unit. Specialized cathode fixture with a non- conducting shield or a secondary electrode was developed to improve the deposition uniformity. To avoid the impurities, an electrolyte circulating filtration system was designed. The anode was an electrolytic nickel plate with the dimensions of 65 mm×55 mm×4 mm and the initial distance between the anode and the cathode was 100 mm.
3.2 Nickel electroforming
Rectangular pulse power was used in this work. The ingredients of electrolyte and the working condition are listed in Table 1.
Adjusting the size of non-conducting shield, adding the secondary electrode and adjusting the motion parameters of the cathode were tried in this study to improve the deposition uniformity of samples respectively. The substrate was a 16 mm×16 mm rectangle with 1 mm in thick ness. Before deposition, the cathode carrying microstructures and the anode were vertically placed in the electrolyte face to face (shown in Fig. 1(a)). The values of the deposit layer thickness were measured in the cross-section by an electronic micrometer at every 0.8 mm interval along the vertical direction. The measured points of electroformed samples are demonstrated in Fig. 1(b).
4 Results and discussion
4.1 Effect of non-conducting shield
A non-conducting shield designed in the electroforming process was to decrease the impact of mentioned edge concentration effect. A shield made of polyvinyl chloride (PVC) was placed 10 mm away from the cathode with a square hole, as shown in Fig. 2. The square hole and the shield were all centered with a horizontal axis of the cathode regardless of their side length.
Table 1 Electrolyte composition and working condition

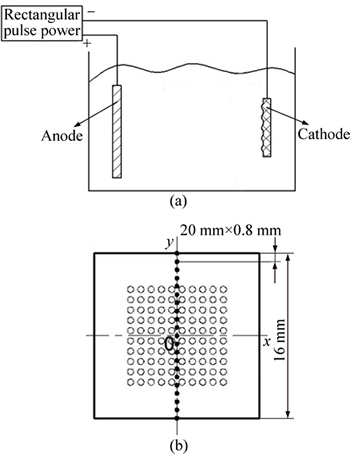
Fig. 1 Schematic diagram of electroforming system (a) and thickness measured points (b)
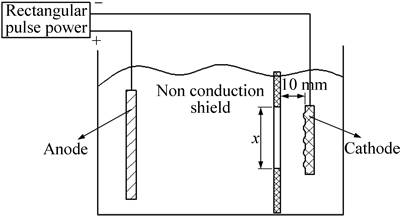
Fig. 2 Schematic diagram of electroforming system with a non-conducting shield
Figure 3 presents the experimental results of deposit layer thickness with different side length of the square hole and the result with no shield. These samples were fabricated after 20 h non-stop electroforming. The deposition uniformity, characterized by the thickness variation, is interpreted as
(5)
where Hvariation is the thickness variation; Hmax, Hmin and Have are the maximum value, the minimum value and the average value of deposit layer thickness, separately.
Figure 4 shows the effect of the square hole side length in the non-conducting shield on the deposit layer thickness variation. With no shield, the thickness variation reached up to 150%. The use of a non-conducting shield could effectively reduce the impact of edge concentration effect on the deposition uniformity. The thickness variation decreased with the increase of the square hole side length from 12 mm to 16 mm, then increased from 16 mm to 24 mm. The thickness variation reached its minimum as 35% when the side length of the square hole was 16 mm. This side length was exactly equal to the size of the substrate.
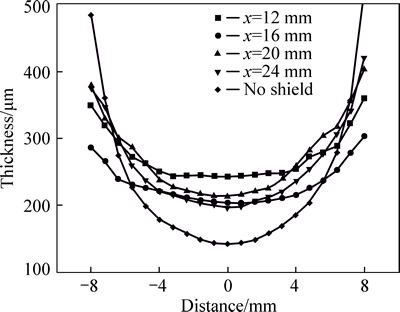
Fig. 3 Thickness profiles of electroformed nickel layers with a non-conducting shield and without shield (x is side length of square hole in non-conducting shield)
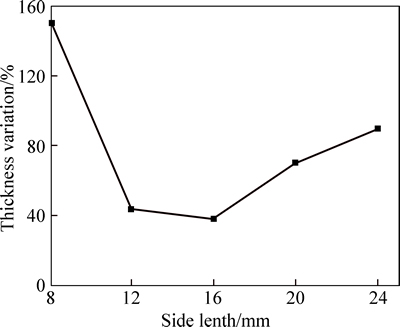
Fig. 4 Effect of side length of square hole in non-conducting shield on deposit layer thickness variation
4.2 Effect of secondary cathode
Secondary cathodes made of titanium were applied instead of the no-conducting shield, as shown in Fig. 5(a), to improve the deposition uniformity. These cathodes were square frames with the side length of 16 mm, 20 mm, 24 mm and 28 mm, respectively. During the electroforming process, the secondary cathode was placed 5 mm away from the primary cathode. There were two power supplies in this system. One was for the primary cathode; the other was for the secondary cathode. The current densities for double cathodes were set at the same level.
Figure 6 shows the deposit layer thicknesses of measured points with different side lengths of the secondary electrode. The thickness profile displayed a W shape with the double cathodes, while presented a U shape with one cathode.
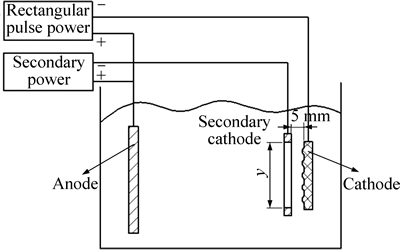
Fig. 5 Schematic diagram of electroforming system with a secondary cathode
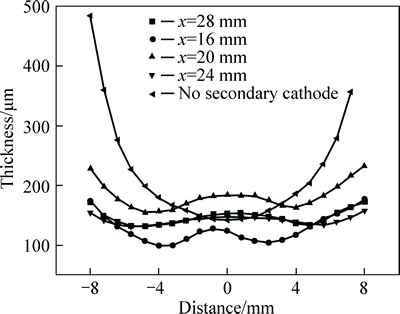
Fig. 6 Thickness profiles of electroformed nickel layers with double cathodes and with one cathode (x is the side length of the secondary cathode)
The effect of the secondary cathode side length on the thickness variation is shown in Fig. 7. With the help of a secondary cathode, there was a significant reduction in the thickness variation of the deposited layer. The thickness variation sharply decreased with the increase of the secondary cathode side length from 16 mm to 24 mm, and then increased from 24 mm to 28 mm. When the side length was 24 mm, it was the lowest thickness variation of around 12%. This side length was 1.5 times that of the primary cathode. Although the deposit rate was reduced due to the current consumption by the secondary cathode, this approach could significantly reduce the thickness variation of the deposit layer.
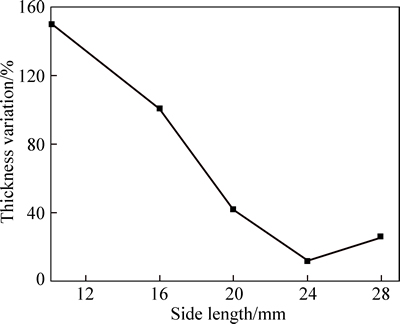
Fig. 7 Effect of secondary cathode side length on deposited layer thickness
4.3 Effect of cathode movement
The schematic diagram of the electroforming system with a moveable cathode is shown in Fig. 8. This moveable cathode could rotate around its vertical axis and move to-and-fro along its horizontal axis. The parameters of these two movements are listed in Table 2.
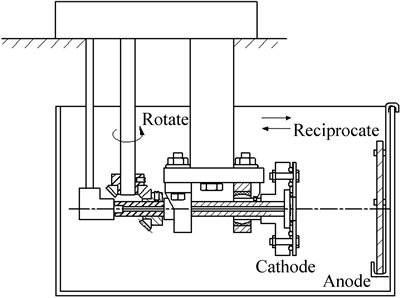
Fig. 8 Schematic diagram of electroforming system with a moveable cathode
Table 2 Parameters of two movements for moveable cathode
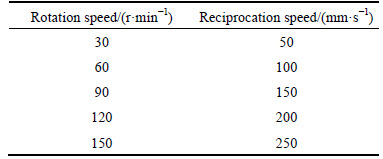
Figure 9 shows the effect of the two movement parameters on the thickness of electroformed deposition. The larger the cathode rotating speed was, the better the uniformity would become. The thickness variation was decreased from 67% to 18% when the rotational speed increased from 30 to 150 r/min. The reciprocation of the cathode also could improve the uniformity of the deposit layer. With the cathode reciprocation speed of 50 mm/s, the thickness variation was 74.19%. It was reduced to 20.76% when the speed was 250 mm/s.
4.4 Mold insert electroforming
There were three procedures for the electroforming process of mold inserts. They were the pre-treatment of the substrate, the electro-deposition and the separation. By combining validated three improving methods, a mold insert for the micro-lens array was arranged to be electro formed. A 10×10 lens array (100 lenses) with lens diameter of 300 μm, and lens sag height of 45 μm was selected. The side length of the square hole in the non- conducting shield was 16 mm. The side length of the secondary electrode was 24 mm. The rotating speed of the movable cathode was 150 r/min and the reciprocating speed was 250 mm/min. The sectional morphologies of the electroformed mold inserts with and without the help of these methods were compared in Fig. 10. Adopting the three validated methods, the thickness uniformity was improved significantly and this was beneficial to the assembly and the application of micro mold inserts.
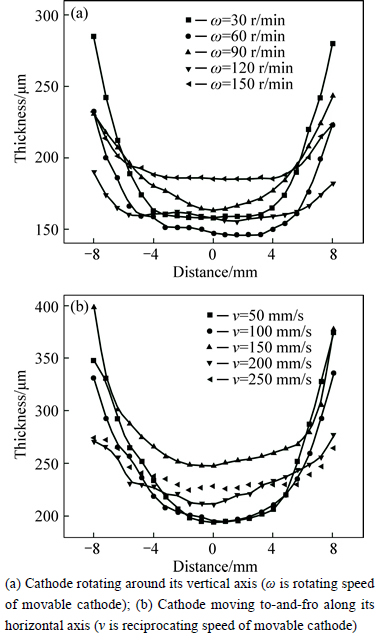
Fig. 9 Thickness profiles with different motion parameters:
After 200 h electroforming, a nickel mold insert for micro lens array with 4 mm thickness was fabricated as shown in Fig. 11(a). The electroformed nickel mold insert was measured by the Carl-Zeiss LSM 700 Confocal microscope. And the average diameter of the electroformed micro lens was 300.5 μm and the average sag height was 45.3 μm, as shown in Fig. 11(b). The nickel mold insert with the satisfactory mechanical properties, high replication precision could be successfully applied to the following injection molding process.

Fig. 10 Comparison of electroformed mold inserts without help of three validated methods (a) and with help of three validated methods (b)
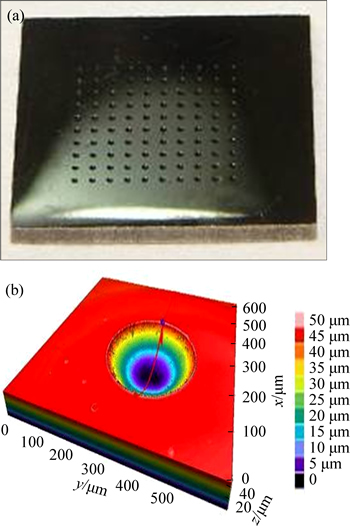
Fig. 11 4 mm thick nickel micro lens array mold insert (a) and 3D contour of a single lens (b)
5 Conclusions
1) It is observed that the non-uniform deposition layer in the electroforming process is mainly determined by the distribution of electrical field and the mass transfer of liquid phase. To improve the non-uniformity of nickel electroforming process, the techniques of adopting anon-conducting shield, a secondary electrode and a movable cathode are explored.
2) Experiments are carried out to investigate the effects of the size of non-conducting shields, secondary electrodes and the movement parameters of the movable cathode on the thickness deposition uniformity. With the help of these techniques, the minimum thickness variations of electroformed inserts decrease to 35%, 12% and 18%, respectively. The improvement of the deposition uniformity by each method in nickel electroforming process is validated by the experimental results.
3) A 4 mm-thick mold insert for the micro lens array with these validated methods is fabricated after 200 h electroforming with a satisfactory replication precision, which can be successfully applied in the following injection molding process.
References
[1] TANG Jun, WANG Hong, GUO Xin-qiu, DAI Xu-han, DING Gui-fu, YANG Chun-shen. An investigation of microstructure and mechanical properties of UV-LIGA nickel thin films electroplated in different electrolytes [J]. Journal of Micromechanics and Microengineering, 2010, 20(2): 025033.
[2] KERDLAPEE P, WISITSORAAT A, PHOKARATKUL D, LEKSAKUL K, PHATTHANAKUN R, TUANTRANONT A. Fabrication of electrostatic MEMS microactuatorbased on X-ray lithography with Pb-based X-ray mask and dry-film-transfer-to-PCB process [J]. Microsystem Technologies, 2014, 20(1): 127-135.
[3] MEYER P, CLAVERLEY J D, LEACH R K. Quality control for deep X-ray lithography (LIGA): A preliminary metrology study [J]. Microsystem Technologies, 2012, 18(4): 415-421.
[4] SHANA W L, YANG Y, HILLIE K T, JORDAAN W A, SOBOYEJO W O. Role of oxide thickening in fatigue crack initiation in LIGA nickel MEMS thin films [J]. Materials Science & Engineering A, 2013, 561(3): 434-440.
[5] JAIN A, GOPAL R. 2-DOF vibratory gyroscope fabricated by SU-8 based UV-LIGA process [J]. Microsystem Technologies, 2014, 20(7): 1291-1297.
[6] SHOUTE L C T, WU Y, MCCREERY R L. Direct spectroscopic monitoring of conductance switching in polythiophenememory devices [J]. Electrochimica Acta, 2013, 110(6): 437-445.
[7] YUTA O, KENJI Y, YOSHITAKA S, DAIJI N. Fabrication of UV range light guide plate [J]. Microsystem Technologies, 2010, 16(8): 1625-1631.
[8] YANG Jian-ming, KIM D H, ZHU Di, WANG Kun. Improvement of deposition uniformity in alloy electroforming for revolving parts [J]. International Journal of Machine Tools & Manufacture, 2008, 48(3/4): 329-337.
[9] MASLIY A I, PODDUBNY N P, VAIS A A. Effect of the variable profile of substrate conductivity on the dynamics of metal deposition on resistive tape [J]. Journal of Electroanalytical Chemistry, 2014, 727(11): 47-52.
[10] LIM T, KIM M J, PARK K J, KIM K H, CHOE S, LEE Y S, KIM J J. The effect of inducing uniform Cu growth on formation of electroless Cu seed layer [J]. Thin Solid Films, 2014, 564: 299-305.
[11] SHIH C J, LIN W C, LIN C S, OU S F, PAN Y N. Fabrication of diamond conditioners by using a micro patterning and electroforming approach [J]. Microelectronic Engineering, 2013, 103: 92-98.
[12] MUHAMMAD R, CHO S H, LEE J H, PARK J G. Fluorocarbon film-assisted fabrication of a CoNi mold with high aspect ratio for nanoimprint lithography [J]. Microelectronic Engineering, 2013, 104: 58-63.
[13] LEE J M, JOHN T H, JAMES J K, ALAN C W. Improvement of current distribution uniformity on substrates for microelectromechanical systems [J]. Journal of Micro/ Nanolithography, MEMS, and MOEMS, 2004, 3(1): 146-151.
[14] CHOI Y. Ultrasonic agitation-floating classification of nano-sized Ba–Mg ferrites particles formed by using self-propagating high temperature synthesis and fabrication of nickel-ferrites thin sheet by pulse-electroforming [J]. Journal of Nanoscience and Nanotechnology, 2013, 13(1): 607-610.
[15] QIAO Feng, SUN Xiao-xuan, WEST A C. A shielded rotating disk setup with improved current distribution [J]. Journal of Applied Electrochemistry, 2014, 44(8): 945-952.
[16] INGON K, PAT F M. Electroformed nickel stamper for light guide panel in LCD back light unit [J]. Electrochimica Acta, 2006, 52(4): 1805-1809.
[17] XIE Hong-bin, ZHAO Xing, YANG Yong, BU Jing, FANG Zhi-liang, YUANG Xiao-cong. Cross-lenticular lens array for full parallax 3-D display with crosstalk reduction [J]. Science China, 2012, 55(3): 735-742. (in Chinese)
[18] WENG Can, LEE W B, TO S. A study of the relevant effects on the maximum residual stress in the precision injection moulding of microlensarrays [J]. Journal of Micromechanics and Microengineering, 2010, 20(3): 035033.
[19] CHEN Lei, KIRCHBERG S, JIANG Bing-yan, XIE Lei, JIA Yun-long, SUN Lei-lei. Fabrication of long-focal-length plano- convex microlens array by combining the micro-milling and injection molding processes [J]. Applied Optics, 2014, 53(31): 7369-7380.
(Edited by YANG Hua)
Foundation item: Projects(51305465, 91123012) supported by the National Natural Science Foundation of China
Received date: 2016-01-11; Accepted date: 2016-05-17
Corresponding author: WENG Can, Associate Professor; Tel: +86-18711166127; E-mail: canweng@csu.edu.cn