Article ID: 1003-6326(2005)02-0217-04
Effect of particle size on thermo-physical properties of SiCp/Cu composites fabricated by squeeze casting
WU Gao-hui(武高辉), CHEN Guo-qin(陈国钦), ZHU De-zhi(朱德志),
ZHANG Qiang(张 强), JIANG Long-tao(姜龙涛)
(School of Materials Science and Engineering, Harbin Institute of Technology, Harbin 150001, China)
Abstract: For the electronic packaging applications, copper matrix composites reinforced with different sized SiC particles (10μm, 20μm and 63μm) were fabricated by squeeze casting technology. And the effect of particle size on their thermo-physical properties was discussed. The composites are free of porosity and the SiC particles are distributed uniformly in the composites. It is found that the mean linear thermal expansion coefficients(20-100℃) of SiCp/Cu composites are in the range of (8.4-9.2)×10-6/℃, and smaller expansion coefficient can be obtained for the composites with finer SiC particles because of the larger restriction in expansion through interfaces. Their thermal conductivities are reduced with the decrease of SiC sizes. This is attributed to the fact that the negative effect of interfacial thermal resistance becomes increasingly dominant as the particles becomes smaller.
Key words: particle size; copper matrix composites; thermal expansion; thermal conductivity CLC number: TB133
Document code: A
1 INTRODUCTION
SiC particle reinforced aluminum matrix composites have received much recognition in electronic packaging and thermal management (such as power module base plates, printed wiring board cores, microprocessor lids, and electric enclosures), because of their flexible fabrication techniques, designable thermo-physical properties and excellent specific strength and rigidity[1-4]. Compared with aluminum, copper has higher electronic and thermal conductivities, lower thermal expansion coefficients(CTE) and higher melting point. These characteristics make copper more attractive in electronic packaging applications.
The previous work showed that copper matrix composites reinforced with bare or coated SiC particulates exhibited a higher thermal conductivity and a lower CTE because of the high thermal conductivity of copper and the low CTE of silicon carbide[5, 6]. However, most SiCp/Cu composites are produced by powder metallurgy[7, 8]. Limitations of this technique include relatively higher cost, complicated process, longer production cycles and lower density. Contrarily, squeeze-casting method is believed to be an effective technique because of such advantages as higher production rates, elimination of expensive equipments, feasibility of mass production and near-net shape products.
In the present work, copper matrix composites reinforced with different sized SiC particles (10μm, 20μm and 63μm) are produced by squeeze casting technology, and the effects of particle size on their thermo-physical properties are investigated.
2 EXPERIMENTAL
2.1 Materials preparation
The reinforcements used in this work were angular-shaped silicon carbide particles(SiCp) with nominal diameters of 10, 20 and 63μm, and the volume fraction of the reinforcements was 55%. The SiC particles are available in hexagonal crystal structures from inexpensive raw material sources. The copper matrix was commercially available pure copper(≥99.7%). This pure copper was chosen for the purpose of high thermal conductivity and low cost. Table 1 lists the typical properties of SiC particles and Cu[9]. The SiCp/Cu composites were fabricated by squeeze casting technology. Then the composites were annealed in vacuum at 700℃ for 1.5h and furnace cooled in order to release residual stress within the composites.
2.2 Testing
An OLYMPUS PMG3 optical microscope was used to examine the microstructure of as-fabricated SiCp/Cu composites. The CTE was measured on a DIL 402C (NETZSCH Corp) with a heating rate of 5℃/min. And a helium atmosphere with a flowing rate of 50mL/min was used to keep the chamber temperature consistent. Based on the measured curves of relative length changes versus temperature, the CTE was calculated between 20℃ and 100℃. To diminish systematic errors, the dilatometer was calibrated by measuring an alumina sample under identical condition. The thermal conductivity measurement was performed on TCT 416 (NETZSCH Corp) at 50℃.
3 RESULTS AND DISCUSSION
3.1 Microstructure analysis
Fig.1 shows the optical micrographs of the polished SiCp/Cu composites produced by the squeeze casting technology. It is found that three SiCp/Cu composites with different particle sizes are all dense and macroscopically homogeneous, and particle clusters are seldomly observed. A dense microstructure is beneficial to electronic packaging applications because of the improvement in strength and thermal conductivity.
3.2 Thermal expansion analysis
Fig.2 shows variation of relative length change with temperature for SiCp/Cu composites. The measured linear expansion coefficient of SiCp/Cu composites are 8.4 ×10-6/℃, 8.7 ×10-6/℃ and 9.2 ×10-6/℃ for the composites with 10μm, 20μm and 63μm in size, respectively. It can be observed that the CTE values of the composites decrease with decreasing particle size of SiC. In a SiCp/Cu composite, the thermal expansion behavior is influenced by the thermal expansion of copper matrix and the tightened restriction of SiC particles.
There are many theoretical models to predict CTE of particle reinforced composites[10-12]. For a given composite, these models can predict quite different CTE values. Among these models, the rule of mixtures (ROM) is the simplest one. According to ROM , the following equation is obtained:
αc=αm·Vm+αp·Vp(1)
where α is the CTE value, V is the volume fraction, and the subscripts c, m, p denote the composite, matrix and particle, respectively.
Fig.3 shows the comparison between ROM predictions and experimental data. As can be seen in Fig.3, the CTEs of SiCp/Cu composites are smaller than the ROM values because of the influence of ceramic particle size on the thermal expansion of a composite.
The results by XU et al[13] indicated the CTE values of TiC/Al composites reduced with decreasing particle size. It was attributed to the lattice distortion at the interfacial zone that would affect the CTE values of the composites. The interfacial zone will be constrained to expand or contract with the particle, and thus, CTE of this zone will be closer to that of the particle than that of the metal matrix. The more constraint in the 10μm particle reinforced composite than in the 20μm and 63μm particle reinforced composites, as revealed by Fig.3, may be attributed to the interfacial zone where a lattice distortion layer exists because of particle. It can be shown that the area of a spherical particle/matrix interface per unit volume is given by the specific interfacial area (Ic):

where Vp is the particle volume fraction and d is the particle diameter. Fig.4 illustrates the effect of particle size on the specific interfacial area for the given 55%SiCp/Cu composite.
Table 1 Typical properties of SiCp and Cu[9]

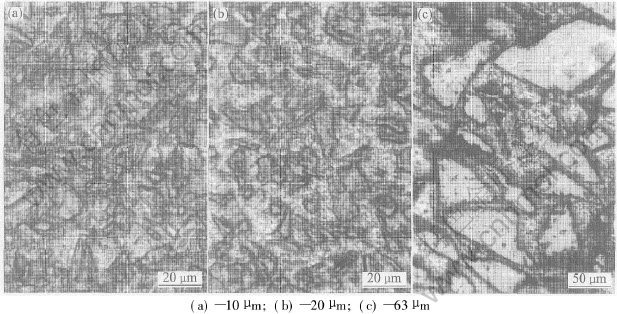
Fig.1 Microstructures of SiCp/Cu composites with different particle sizes
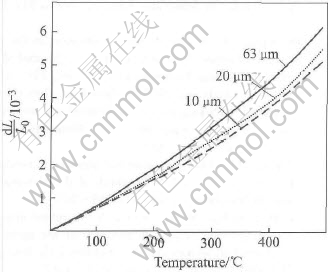
Fig.2 Variation of relative length change with temperature for SiCp/Cu composites
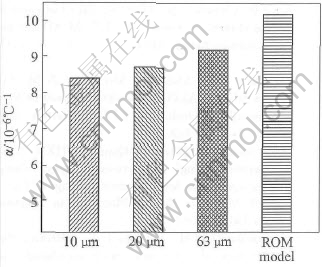
Fig.3 Comparison between ROM predictions and experimental data for SiCp/Cu composites
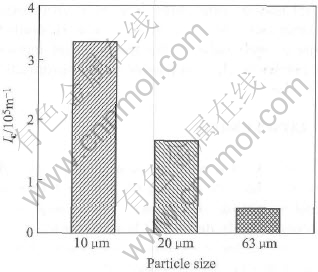
Fig.4 Change of specific interfacial area in SiCp/Cu composites as function of particle size
Since the specific interfacial area is dependent on the particle size, the effect of particle size on the CTE of composite is related to the specific interfacial area. For a given particle volume fraction, the smaller particle size will result in the greater specific interfacial area and higher restriction on thermal expansion. And then smaller CTEs are obtained for the composite with finer particles.
3.3 Thermal conductivity
The measured thermal conductivities of SiCp/Cu composites are 55, 64 and 78W/(m·℃) for the particle sizes of 10, 20 and 63μm, respectively. They are reduced with the decrease of SiC sizes. In general, the thermal conductivity of a composite varies with the thermal conduction properties, type, content, and distribution of different constituent components[14].
However, an interfacial resistance will be generated as a result of a poor mechanical or chemical bond and a thermal expansion mismatch among components. Wu et al[15] and Hasselman et al[16] have derived an effective medium approximation (EMA) to solve this problem. For spherical dispersions, the effective thermal conductivity of a composite is given by
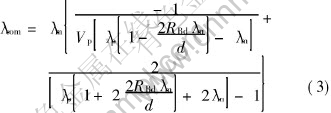
where λ is thermal conductivity, RBdis interfacial resistance, V is volume fraction, d is the diameter of the reinforcement, and subscripts com, p and m are composite, reinforcement particle and matrix, respectively.
As indicated earlier, the composites with finer SiC particles will have a larger specific interfacial area. According to EMA theory, it is clear that the thermal conductivity of the composite will decrease with decreasing particulate size because of the presence of interfacial resistance. Therefore decrease of thermal conductivity for the present SiCp/Cu composites is attributed to the negative effect of interfacial resistance, which can be dominant increasingly as the particle size becomes smaller.
However, the previous work showed that the strength and ductility of discontinuouly reinforced metal matrix composites decreased with larger reinforcement size[17, 18]. So further work needs to be done to well balance the thermal and mechanical properties of the composites with appropriate particle size.
4 CONCLUSIONS
1) SiCp/Cu composites with three particle sizes of 10μm, 20μm and 63μm are fabricated by squeeze casting technology. The composites are macroscopically dense and homogeneous.
2) The linear expansion coefficient of SiCp/Cu composites is in the range of (8.4-9.2)×10-6/℃, and smaller expansion coefficient can be obtained for the composites with finer SiC size because of the larger restriction in expansion through interfaces.
3) As a result of the negative effect of interfacial thermal resistance, the thermal conductivity of SiCp/Cu composites decreases with the decrease of SiC size.
REFERENCES
[1]Johnston C, Young R. Advanced thermal management materials [J]. International Newsletter on Microsystems and MEMs, 2000, 2(1): 14-15.
[2]Zweben C. High performance thermal management materials [J]. Electronic Cooling Magazine, 1999, 5(3): 36-42.
[3]Saraswati R, Polese F J. Aluminum matrix composite heat sinks for microchips and microcircuits [A]. Proceedings of 1998 International Symposium on Microelectronics [C]. USA: California, 1998. 681-686.
[4]Zweben C. Advances in composite materials for thermal management in electronic packaging [J]. JOM, 1998, 50(6): 47-51.
[5]Lee Y F, Lee S L, Chuang C L. Effects of SiCp reinforcement by electroless copper plating on properties of Cu/SiCp composites [J]. Powder Metallurgy, 1999, 42(2): 147-152.
[6]Shu K M, Tu G C. The microstructure and the thermal expansion characteristics of Cu/SiCp composites [J]. Materials Science and Engineering, 2003, A349: 236-247.
[7]Yih P, Chung D D L. Brass-matrix silicon carbide whisker composites prepared by powder metallurgy [J]. Journal of Materials Science, 1999, 34: 359-364.
[8]Heringhaus F, Raube D. Recent advances in the manufacture of copper base composites [J]. Journal of Materials Processing Technology, 1996, 59: 367-372.
[9]ZHAN Yong-zhong, ZHANG Guo-ding. The effect of interfacial modifying on the mechanical and wear properties of SiCp/Cu composites [J]. Materials Letters, 2003, 57(29): 4583-4591.
[10]Turner P S. Thermal expansion stresses in reinforced plastics [J]. Journal of Research of the National Bureau of Standards, 1946, 37: 239-243.
[11]Park C S, Kim M H, Lee C. A theoretical approach for the thermal expansion behavior of the particulate reinforced aluminum matrix composite [J]. Journal of Materials Science, 2001, 36: 3579-3587.
[12]Kowbel W, Patel K, Champion W. Low cost, high thermal conductivity composites for power electronics [A]. International SAMPE Symposium and Exhibition (Proceedings) [C]. USA: CAs Long Beach, 2000, 45(Ⅰ): 527-533.
[13]Xu Z R, Chawla K K, Mitra R. Effect of particle size on the thermal expansion of TiC/Al XD composites [J]. Scripta Metall Mater, 1994, 31(11): 1525-1530.
[14]Moustafa S F, Abdel Z, Abd-Elhay A M. Copper matrix SiC and Al2O3 particulate composites by powder metallurgy technique [J]. Materials Letters, 2002, 53: 244-249.
[15]WU Gao-hui, ZHANG Qiang, CHEN Guo-qin. Properties of high-reinforcement-content aluminum matrix composite for electronic packages [J]. Journal of Materials Science-Materials in Electronics, 2003, 14(1): 9-12.
[16]Hasselman D P H, Johnson L F. Effective thermal conductivity of composites with interfacial thermal barrier resistance [J]. Journal of Composite Materials, 1987, 21(6): 508-515.
[17]Lee T W, Lee C H. Statistical analysis for strength and spatial distribution of reinforcement in SiC particulate reinforced aluminum alloy composites fabricated by die-casting [J]. Journal of Materials Science, 2000, 35(17): 4261-4269.
[18]Verhelle J P, Descamps P, Poorteman M. A comparative study of the fracture behaviour of alumina matrix composites reinforced with silicon carbide particles either of micro or nanosize [J]. Key Engineering Materials, 2001, 32(13): 43668-43675.
Received date:2004 -11-29; Accepted date: 2005-01-18
Correspondence: CHEN Guo-qin, PhD Candidate; Tel: +86-451-86402372; E-mail: chenguoqin@hit.edu.cn
(Edited by YANG Bing)