
Fabrication and microstructure of nanostructured Mg-3Ni-2MnO2 by ball milling in hydrogen atmosphere
FANG Wen-bin(房文斌), FANG Wa(房 娃), SUN Hong-fei(孙宏飞), YU Zhen-xing(于振兴)
School of Materials Science and Engineering, Harbin Institute of Technology, Harbin 150001, China
Received 10 June 2009; accepted 15 August 2009
Abstract: Nanostructured Mg-3Ni-2MnO2 was synthesized by ball milling elemental powders of Mg, Ni and MnO2 in hydrogen atmosphere. The microstructures of the powder prepared at different milling time were analyzed by X-ray diffractometry(XRD), scanning electron microscopy(SEM) and high resolution electron microscopy(HREM). The milling time is the most key parameter impacting on the grain size and the microstructure of material. With prolonging the milling time, particle size becomes smaller and smaller. But after the ball milling time reaches about 20 h, reduction of grain size becomes slowly. When the milling time is more than 50 h, nanocrystalline fully forms. When the milling time is more than 80 h, there are more amorphous phases in materials. The average particle diameter of material is about 1 μm and the grain size is 10-30 nm.
Key words: nanocrystalline; ball milling; grain size; amorphous phase
1 Introduction
Magnesium alloys possess interesting characteristics, such as small density and high specific strength, which could reduce hardware mass and bring cost benefits when being used in aerospace, electrical and traffic fields[1]. Poor handling characteristics and easy corrosion of common magnesium alloys limit their applications[2-3]. But if grain size can be reduced to large extent, its characteristics will be changed. In recent years, many efforts have been devoted to grain refinement. These methods include hot and warm rolling, hot extrusion at high reduction ratio, and several plastic deformation processes such as equal channel angular pressing(ECAP) [4-5]. Powder metallurgy(PM) is quite a potential way to prepare nanocrystalline or ultrafine grained bulk alloys. By this route, nanocrystalline alloy powders have to be used. For most Mg alloys, however, it is difficult to produce nanocrystalline alloy powders by means of rapid solidification due to their thermal/ physical properties and limitations in thermodynamic aspects. Therefore, searching the ways of producing nanocrystalline Mg alloy powders is of great significance [6-10]. Hence, in this work, the possibility of developing nanocrystalline microstructure in Mg alloy powder by balling milling and the effect of milling time on the particle size and microstructure of Mg-3Ni-2MnO2 powders were studied.
2 Experimental
The nanostructured Mg alloy was prepared by mixing three kinds of powder: Mg, Ni and MnO2. Magnesium(Mg) powder (>99%), nickel(Ni) powder (>99.5%) and manganese dioxide(MnO2) (>99.5%) were provided by Shanghai Chemical Reagent Company, China. The average size of the powder was 20 μm as reported by the manufacturer. Three kinds of powder were mixed in stainless vial in mass ratio of 95:3:2. The milling was carried out with a QM21SP4 planetary ball milling machine in hydrogen atmosphere (about 0.5 MPa) made in Nanjing University, China, with a ball-to-powder mass ratio of 10:1. The diameters of the ball of 20 mm and 10 mm were used, respectively. Because the samples absorb hydrogen in the ball milling process, hydrogen pressure cannot keep constant. The hydrogen of the vials must be recharged to 0.5 MPa at intervals. Small amount of powder was taken for analysis. All handling was conducted in a glove box in argon. X-ray diffraction was performed on a Rigaku apparatus [11-15] with Cu Kα radiation. The SEM and HREM images were obtained on a Hitachi S2570 and JEM- 2010 type apparatus, respectively.
3 Results and discussion
3.1 XRD analysis of Mg-3Ni-2MnO2 powder
X-ray diffraction patterns as a function of milling time for the Mg-3Ni-2MnO2 samples are shown in Fig.1. It can be clearly seen that the intensity of the diffraction peaks of magnesium decreases rapidly as well as the width of the peaks increases with increasing milling time. At the same time, the intensity and the width of the peaks of MgH2 increase rapidly. The reason is that upon milling, repeated ball-powder collisions induce mechanical deformations, and introduce strain into the powder, as a result, the crystallites fracture into smaller pieces down to the nanometer range. From Fig.1, it is also observed that, after 82 h of milling, no characteristic diffraction peaks of Mg is found, which confirms that the powder is fully hydrogenated. The diffraction peaks of MgH2 become very broad, which proves that the crystalline size of MgH2 is reduced into the nanocrystalline range. From the increase of width of MgH2 peaks, it is considered that the crystalline of MgH2 partly becomes amorphous. Calculation using the Scherrer equation based on the XRD patterns reveals that the average crystallite sizes of Mg-3Ni-2MnO2 obtained by 25, 57 and 82 h milling are about 30, 20-30 and 10 nm, respectively[16-18].
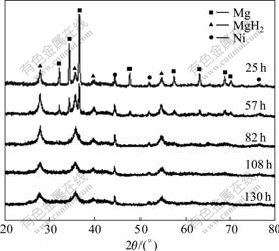
Fig.1 X-ray diffraction patterns of Mg-3Ni-2MnO2 mixture after ball milling for different time
3.2 SEM analysis of Mg-3Ni-2MnO2 powder
Fig.2 shows the microstructures of the sample milled for various time. It is observed that when the ball milling time is 25 h (Fig.2(a)), the difference of diameter of powders is significant; but this difference decreases with milling time increasing. When the milling time is over 57 h, the average powder size is about 1.0 μm. Even the milling time reaches 130 h, the average diameter almost doesn’t change. The powder size is one of key factors for kinetics in hydrogenation, disproportionation,
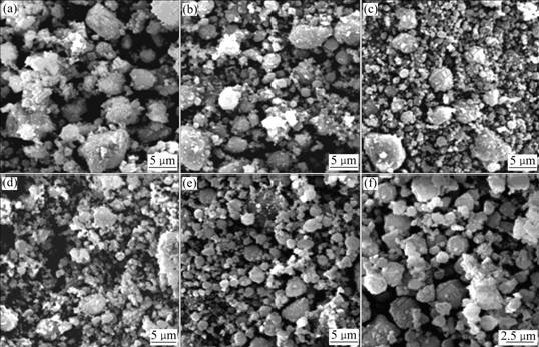
Fig.2 SEM micrographs of Mg-3Ni-2MnO2 mixture after ball milling for different time: (a) 25 h; (b) 57 h; (c) 82 h; (d) 108 h; (e) and (f) 130 h
desorption and recombination (HDDR) process. In general, small powders possess larger specific surface and more active sites for hydrogen decomposition and recombination, less distance of hydrogen diffusion and higher surface energy that is helpful to hydrogen absorption and desorption.
From Fig.3, it can be clearly seen that with prolonging the milling time, particle size becomes smaller and smaller. When milling time is 20 h, the average particle size is about 4 μm. But when the ball milling time is beyond 20 h, the particle size is decreased slowly. When the milling time reaches about 80 h, with the milling time increasing, the particle size becomes unchanged. The reason may be that when the milling time exceeds 80 h, particles are in the range of ultra-fine range, so further milling hardly has effect on the particle size.
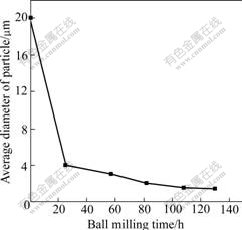
Fig.3 Average diameter of Mg-3Ni-2MnO2 particles as function of ball milling time
3.3 HREM analysis of Mg-3Ni-2MnO2 powder
Figs.4(a) and (b) show the HREM images of samples milled for 25 h and 108 h. It can be seen clearly that more regular atomic arrangement of perfect crystal can be observed for short milling time. After the milling time reaches 108 h, the grain size is about 10 nm, and grain boundary and amorphous phases are dominated.
4 Conclusions
Milling process has an important impact on the microstructure of Mg-3Ni-2MnO2. It can be seen that with prolonging the milling time, particle size becomes smaller and smaller. After the ball milling time reaches about 20 h, reduction of grain size becomes slowly. When milling time is more than 50 h, nanocrystalline fully forms. When milling time is more than 80 h, more amorphous phases appear in materials. The average particle diameter of material is about 1 μm and the grain size is about 10-30 nm.
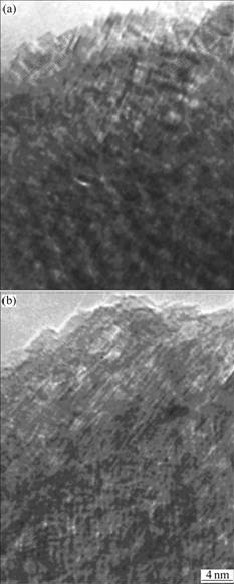
Fig.4 HREM images of Mg-3Ni-2MnO2 samples as function of milling time: (a) 25 h; (b) 108 h
References
[1] LUO A, RENAUD J, NAKATSUGAWA I, PLOURDE J. Magnesium castings for automotive applications [J]. J Organomet Chem, 1995, 47(7): 28-31.
[2] PEREZ-PRADO M T, DEL VALLE J A, RUANO O A. Grain refinement of Mg-Al-Zn alloys via accumulative roll bonding [J]. Scripta Mater, 2004, 51(11): 1093-1097.
[3] WATANABE H, MUKAI T, ISHIKAW K, HIGASHI K. Low temperature superplasticity of a fine-grained ZK60 magnesium alloy processed by equal-channel-angular extrusion [J]. Scripta Mater, 2002, 46(12): 851-856.
[4] CHEN Y J, WANG Q D, ZHANG L J, LIN J B, ZHAI C Q. Network-shaped fine-grained microstructure and high ductility of magnesium alloy fabricated by cyclic extrusion compression [J]. Scripta Mater, 2008, 58(4): 331-334.
[5] VALIEVR Z, LANGDONT G P. Principles of equal-channel angular pressing as a processing tool for grain refinement [J]. Pro Mater Sci, 2006, 51(7): 881-981.
[6] HU Lian-xi, WU Yang, YUAN Yuan, WANG Heng. Microstructure nanocrystallization of a Mg-3%Al-1%Zn alloy by mechanically assisted hydriding-dehydriding [J]. Mater Lett, 2008, 62(17/18): 2984-2987.
[7] MAZAHERI M, ZAHEDI A M, HEJAZI M M. Processing of nanocrystalline 8mol% yttria-stabilized zirconia by conventional, microwave-assisted and two-step sintering [J]. Mater Sci Eng A, 2008, 492(1/2): 261-267.
[8] RAWERS J C, HARLOW D G. Understanding the strength of hot-pressed nanostructured powder compacts [J]. Mater Eng Perform, 1999, 8: 35-45.
[9] ZHOU F, WIT-KIN D, NUTT S R. Formation of nanostructure in Al produced by a low-energy ball milling at cryogenic temperature [J]. Mater Sci Eng A, 2004, 375/377: 917-921.
[10] CHOI J H, MOON K I, KIM J K. Consolidation behavior of nanocrystalline Al-5at.%Ti alloys synthesized by cryogenic milling [J]. J Alloy Compd, 2001, 315(1/2): 178-186.
[11] LU L, SUI M L, LU K. Cold rolling of bulk nanocrystalline copper [J]. Acta Mater, 2001, 49(19): 4127-4134.
[12] SUN X, REGLERO R, SUN X. Microhardness of bulk and higher density nanocrystalline copper obtained by hot compaction [J]. Mater Chem Phys, 2000, 63(1): 82-87.
[13] ZHANG X, WANG H, KASSEM M. Preparation of bulk ultrafine-grained and nanostructured Zn, Al and their alloys by in situ consolidation of powders during mechanical attrition [J]. Scripta Mater, 2002, 46(9): 661-665.
[14] PENG Qiu-ming, HOU Xiu-li, WANG Li-dong. Microstructure and mechanical properties of high performance Mg-Gd based alloys [J]. Mater Design, 2009, 30(2): 292-296.
[15] ZHO H T, ZHONG J W, ZHOU X. Microstructure and properties of Cu-1.0Cr-0.2Zr-0.03Fe alloy [J]. Mater Sci Eng A, 2008, 498: 225-230.
[16] YANG Jie, XIAO Wen-long. Influences of Gd on the microstructure and strength of Mg-4.5Zn alloy [J]. Mater Charac, 2008, 59(11): 1667-1674.
[17] TIAN X, WANG L M, WANG J L. The microstructure and mechanical properties of Mg-3Al-3RE alloys [J]. J Alloys Comp, 2008, 465(1/2): 412-416.
[18] WANG Er-de, YU Zhen-xing, LIU Zu-yan. Hydrogen storage properties of nanocomposite Mg-Ni-MnO2 made by mechanical milling [J]. Trans Nonferrous Met Soc China, 2002, 12(2): 227-232.
(Edited by YANG Bing)
Foundation item: Project(DCQQ24404018) supported by Scientific and Technological Program of Heilongjiang Province, China
Corresponding author: FANG Wa; Tel: +86-451-86403365; E-mail: fangwa1@sina.com