DOI: 10.11817/j.issn.1672-7207.2015.11.046
铝合金与镀锌钢板CMT焊接过程传热传质现象的数值模拟
饶政华1,李芸霄1,刘江维1,廖胜明1,王凤江2
(1. 中南大学 能源科学与工程学院,湖南 长沙,410083;
2. 江苏科技大学 先进焊接技术省级重点实验室,江苏 镇江,212003)
摘要:建立冷金属过渡(CMT)焊接的三维非稳态数学模型,研究铝合金和镀锌钢板CMT焊接过程的传热、传质现象,包括电弧等离子体的形成和变化、焊丝的送入与回抽、熔滴生长与过渡、熔池动态行为、镀锌层的蒸发及锌蒸气在电弧中的扩散。研究结果表明:在高温电弧的作用下钢板表面的镀锌层蒸发,锌蒸气由钢板表面向电弧区扩散,其分布受等离子体流动的影响。焊接过程中焊接电流、电弧长度不断变化,造成焊接工件表面附近的电弧压力持续变化。锌层蒸发增大了钢板表面附近的电弧压力,易造成熔滴过渡和焊接过程的不稳定。
关键词:冷金属过渡;电弧等离子体;传热传质;数值模拟
中图分类号:TG44 文献标志码:A 文章编号:1672-7207(2015)11-4325-09
Numerical simulation of heat and mass transfer during CMT welding of aluminum alloy and galvanized mild steel
RAO Zhenghua1, LI Yunxiao1, LIU Jiangwei1, LIAO Shengming1, WANG Fengjiang2
(1. School of Energy Science and Engineering, Central South University, Changsha 410083, China;
2. Provincial Key Lab of Advanced Welding Technology, Jiangsu University of Science and Technology,
Zhenjiang 212003, China)
Abstract: A 3D transient cold metal transfer (CMT) welding model was developed to study the heat and mass transfer during CMT welding of aluminum alloy and galvanized steel sheets, which includes arc generation and evolution, up-and-down movement of welding wire, droplet formation and dipping into the weld pool, weld pool dynamics, zinc evaporation and zinc vapor diffusion in the arc. The results show that the zinc layer at the steel surface evaporates and diffuses into the arc under the impact of high-temperature arc, and the zinc vapor distribution is affected by the plasma flow. During the welding process, the welding current and arc length keep changing, leading to the continuous variation of arc pressure at the workpiece surface. The zinc evaporation increases the arc pressure near the steel surface, which always results in the instable metal transfer and welding process.
Key words: cold metal transfer; arc plasma; heat and mass transfer; numerical simulation
冷金属过渡技术(CMT)是Fronius公司发明的一种改进的GMAW(熔化极气体保护焊)焊接方式[1]。与传统的GMAW过程相比,CMT焊接将送丝运动和熔滴过渡过程进行数字化协调,能够实现熔滴的平稳过渡。焊丝在燃弧期间向工件表面移动,接触到熔池表面时向送丝机构反馈短路信号,送丝机构接到信号后迅速回抽焊丝,促使焊丝顶端的熔滴和焊丝分离,焊丝回到起始位置开始新一轮的焊接过程。由于CMT焊具有热输入量低、无飞溅、搭桥能力强、焊缝均匀一致、变形小等优点,在薄板焊接、铝-钢等异种金属连接等领域得到了日益广泛的应用[2]。近年来,国内外研究者从不同的角度对CMT焊接的技术与机理进行了分析。Pickin等[3]以1.2 mm AA 4043为焊丝利用CMT焊技术对3 mm厚AA 6111板进行了堆焊实验,发现焊接周期中短路过渡时间越短,熔深越大。Feng等[4]以1.2 mm AlSi5合金为焊丝,对1 mm纯铝板进行CMT堆焊实验,对CMT铝板焊接的波形特性及熔滴过渡特性进行分析,发现CMT焊接纯铝薄板的挠曲变形较小。Pires等[5]通过对比GMAW、脉冲GMAW和CMT焊接过程,发现CMT焊可减少对工件的热输入量。以上研究结果均是采用实验方法获得的。然而,由于金属材料的不透明性、高温高压的等离子体等因素的影响,一些参数难以准确测量,单纯依靠实验的方法难以完全理解CMT焊的物理现象和机理。而数值模拟为解决该问题提供了有效的方法。目前,许多研究者[6-10]建立了GMAW等电弧焊的数学模型,对焊接过程的物理现象开展了大量研究,但关于CMT焊接过程的数值研究则少有报道,而对铝合金和镀锌钢板CMT焊的数值研究则更少。基于连续介质理论[8]和VOF方法[11]建立三维非稳态的数学模型,本文作者研究铝合金AA6061和镀锌钢板CMT焊接过程的传热传质现象和机理;并通过比较有、无镀锌层的计算结果,分析锌层蒸发对CMT焊接过程的影响。
1 数学模型
图1(a)所示为CMT焊接系统[2]的三维示意图,该系统关于x-z和y-z平面对称;图1(b)所示为x(y)-z平面图(图中H1为工件高度;H2为喷嘴到工件表面高度;L为对称轴到工件侧壁宽度)。由图1可见:铝合金AA 6061板(板1)置于镀锌钢板(板2)的上方,在板1的中心位置设置一个小孔。焊丝为铝合金AA 6061,且垂直于工件。焊接电源连接系统顶端的导电嘴,提供焊接所需要的能量。喷嘴喷出保护气体,以防止熔化的金属被氧化。保护气体被电离后,在焊丝(阳极)和工件(阴极)之间形成高温电弧。连续送入的焊丝熔化后在其端头形成熔滴并不断长大;同时,焊丝匀速下移,接触到工件表面形成短路,焊丝回抽,将熔滴脱离并过渡到工件上形成熔池。熔滴在板1表面铺展至两板间的缝隙,凝固后形成焊缝。
1.1 控制方程
如图1(a)所示,由于关于x-z和y-z平面对称分布,计算区域仅取模型的1/4。将计算区域分为电弧区和金属区,分别对其进行计算,两者通过电弧―金属界面上的特殊边界条件进行耦合[12-13]。其中,金属区包括焊丝阳极区、工件阴极区和熔滴3个部分。控制方程组[10]如下所示。
1) 连续性方程:
(1)
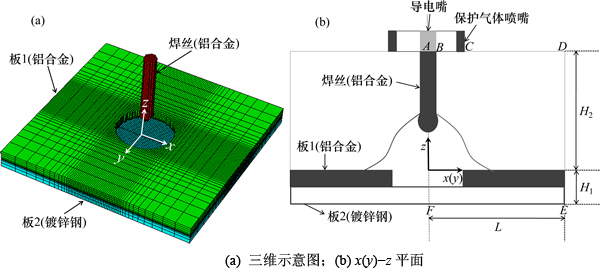
图1 CMT焊接过程示意图
Fig. 1 Schematic diagram of CMT welding process
2) 动量守恒方程:

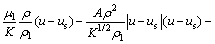
(2)

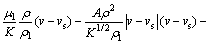
(3)
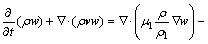

(4)
3) 能量守恒方程:


(5)
4) 组分守恒方程:
(6)
5) 电流连续性方程:
(7)
6) 欧姆定律:
,
(8)
7) 麦克斯韦方程:
(9)
上述方程组用于确定电弧区和金属区的基本物理参数,包括压力p,等离子体和熔融金属的速度
,焓h,温度T,电弧中锌蒸气质量分数CZn,电势
以及x,y,z方向电流密度Jx,Jy和Jz;等离子体和金属材料的性质包括密度ρ,比热容c,导热系数k,黏性系数μ,固液态质量分数f,电导率σe,渗透函数K,惯性系数A和锌蒸汽在氩中的扩散系数D;下标s和l分别表示固态和液态,下标0表示初始条件。方程(2)~(4)中,vr=vl–vs为固液共存的两相区内液相与固相的相对速度矢量;J为电流密度矢量;B为磁通矢量;g为重力加速度;
为热膨胀系数。方程(6)中的S为镀锌钢板表面锌蒸发引起的源项[14]。利用VOF算法跟踪自由运动表面[11]。
1.2 边界条件
根据边界的几何位置(见图1),边界条件如下所述。
1.2.1 上表面(z=H2)
1) 焊丝所在的上表面(AB平面)
u=0,v=0,w=vw,T=300 K,CZn=0,
(10)
式中:vw为送丝速度;I为电流强度;R为焊丝半径。
2) 喷嘴所在的上表面(BC平面)
u=0,v=0,w=vs,T=300 K,CZn=0,
(11)
式中:vs为保护气体流速。
3) 其他位置(CD平面)
u=0,v=0,
,
,
,
(12)
1.2.2 侧表面(DE平面)
x=L:
,
,w=0,
,
,
(13)
y=L:
,
,w=0,
,
,
(14)
1.2.3 底表面(z=-H1,EF平面)
u=0,v=0,w=0,T=300 K,CZn=0,
(15)
1.2.4 对称面(x=0或y=0,AF平面)
x=0:u=0,
,
,
,
,
(16)
y=0:
,v=0,
,
,
,
(17)
2 数值方法
用FORTRAN编程,对控制方程组及相关的附加条件和边界条件通过以下的迭代方案进行计算。
1) 在t=0 s时刻,焊丝设置在初始位置,金属区设置为初始温度分布,求解电弧区的稳态方程得到初始的温度、速度、压力和电流分布。
2) 计算电弧压力、表面张力、Marangoni切应力、等离子体切应力和电磁力,更新其他与金属区相关的边界条件。
3) 迭代计算连续性方程、动量方程和能量方程得到金属区的温度、速度和压力分布。
4) 求解VOF方程,获得新的金属自由表面形状。更新计算区域内各计算单元的物性参数和边界条件。
5) 利用更新的参数在整个计算区域内求解电流连续性方程,得到电流密度和电磁力。
6) 迭代计算连续性方程、动量方程、组分方程,得到电弧区的速度分布、压力分布和锌蒸气质量分数分布。
7) 求解电弧区的能量方程,得到温度分布。更新等离子体电弧区的物性参数。此时,迭代过程返回到步骤5),重复计算直到收敛。
8) 进入到下一个时间步长,计算并更新焊丝的位置。返回至步骤2)重复上述过程,直至计算结束。
计算区域的长×宽×高(x×y×z)为20 mm×20 mm×8 mm,网格点为100×100×50,由于实际中仅计算原模型1/4的区域,网格点为50×50×50。采用了自适应的非均匀网格,使电弧中心附近具有更密的网格,经验证可获得网格独立的解。时间步长为5×10-6 s。
3 结果与讨论
3.1 计算条件
当钢板表面的镀锌层会蒸发进入电弧区时,电弧区为氩-锌混合等离子体,根据等离子体理论[15]计算得到其物性参数随温度的变化(如图2所示)。铝合金AA 6061和镀锌钢板的材料物性如表1和表2所示。
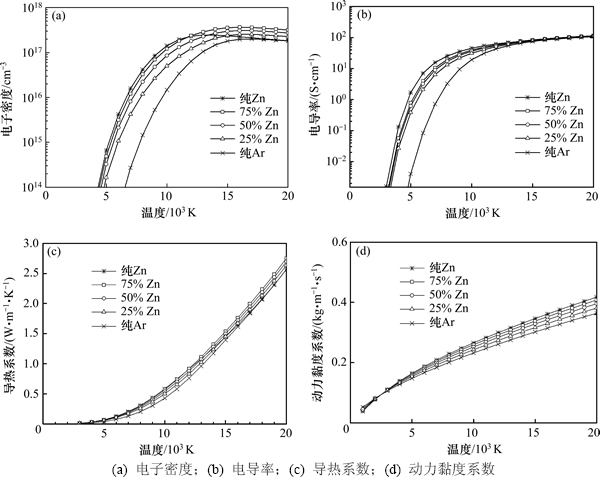
图2 氩-锌混合等离子体的物性参数
Fig. 2 Physical properties for mixture of zinc vapor and argon
图3所示为焊接电流和电压波形图,初始电流和电压分别为85 A和10.0 V,在燃弧后期电流和电压分别降为55 A和6.5 V。表3所示为其他焊接条件和参数。
3.2 CMT焊接过程的传递现象
图4~6所示分别为有镀锌层时,不同时刻等离子体电弧区的温度、速度和锌蒸气质量分数分布。由图4可见:电弧为一个典型的喇叭口形,电弧由上向下向外扩散,使得靠近工件处的电弧温度减小。熔滴与焊丝分离前,在焊丝顶端与工件上表面之间存在高温电弧柱。由图3可见:t=4 ms时电流和电压分别降为55 A和6.5 V。因此,用于电离保护气体和加热电弧的能量减少,导致t=4 ms时的电弧温度和尺寸与t=3 ms时相比明显减小。当焊丝继续向下移动时,由于短路过渡发生之前电流和电压保持不变,且输入的能量不变,而焊丝顶端与工件之间被加热和电离的保护气体越来越少,因此,电弧温度有所增大。当t=17 ms时,焊丝与工件2接触,发生短路,电弧温度明显降低至接近环境温度。熔滴随即与焊丝分离,焊丝回抽到初始位置,在焊丝顶端和脱落的熔滴上表面之间形成了新的电弧柱,熔滴在板2表面铺展(如t=20 ms)。与传统电弧焊接方式相比,焊丝向工件移动的过程中电流较小,短路过渡时电流为0 A,从而减小了焊接过程中的热输入,有效防止了熔滴冲击熔池所造成的飞溅。
表1 AA 6061的物性参数
Table 1 Material properties for aluminum AA 6061
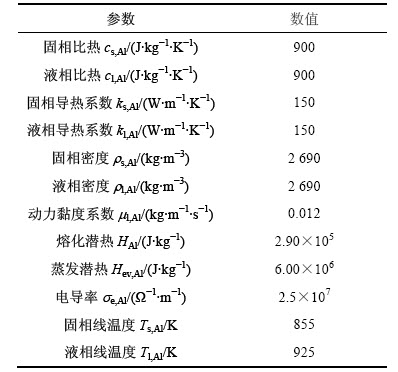
表2 镀锌钢板的物性参数
Table 2 Material properties for galvanized steel
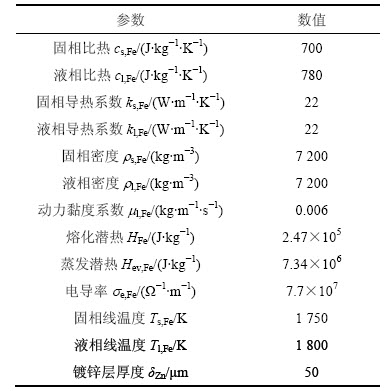
表3 计算所需的焊接条件和参数
Table 3 Welding condition and parameters used in calculation
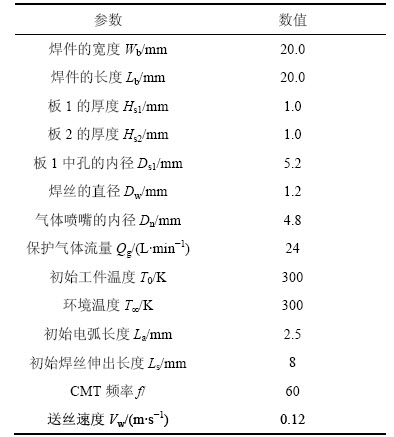
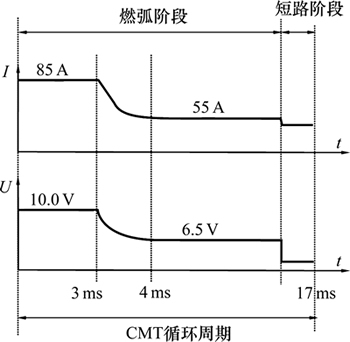
图3 CMT焊接过程中的电流(I)和电压(U)波形图
Fig. 3 Welding current (I) and voltage (U) waveforms used in CMT welding
由图5可见:保护气体初始速度约为5.9 m/s,由喷嘴射出后沿焊丝表面向下流动,在焊丝端部附近被电离,形成等离子体。在电磁力的作用下加速,等离子体速度在板2上表面附近达到最大值(约200 m/s)。板2上表面附近,等离子体动压转变为静压,同时等离子体向下速度开始减小,板2上表面中心处附近的高压推动等离子体向外流动。当t为4, 10和14 ms时,由于输入电流和电压较小,等离子体的速度比t=3 ms时低。当t=17 ms时,焊丝接触到板2的上表面,电压降为0 V和电流降为0 A,由于没有电磁力的加速作用,保护气体的速度急剧降低。熔滴从焊丝脱离后(t=20 ms时),电压和电流增加到初始值,等离子体的速度分布与t=3 ms时的情形相似。
由图6可见:在电弧和工件之间的对流和辐射传热的作用下,镀锌层从板2表面蒸发,锌蒸气由板2上表面向电弧区扩散。因此,与板2上表面邻近的电弧中锌蒸气浓度最高,锌蒸气在高压作用下向上扩散,并被向下流动的纯氩等离子体稀释,使锌蒸气的浓度沿z轴正方向不断降低。锌蒸气的浓度明显受到等离子体流动形态的影响,整体呈U形分布。由于等离子体向下向外流动(如图5所示),锌蒸气由板2中心处向外扩散,使焊丝下方的锌蒸气浓度很小。t=4 ms时,电流降至55 A,等离子体向下向外流动的速度降低,而镀锌钢板表面锌蒸气的速度基本不变,致使更多的锌蒸气扩散到电弧中心区域。当焊丝继续向下移动(如t=10 ms和t=14 ms),电弧长度继续减小,等离子体的温度和速度有所增加,更多的锌蒸气被推到孔的外面。当短路过渡(t=17 ms)时,等离子体电弧瞬间熄灭,电弧区内的锌蒸气质量分数降为0。当熔滴过渡到板2上之后(t>17 ms),熔融金属覆盖在板2表面上,锌蒸气无法向电弧区内扩散,此时电弧区内不存在锌蒸气。因此,t≥17 ms 时,锌蒸气质量分数为0(图中未给出)。
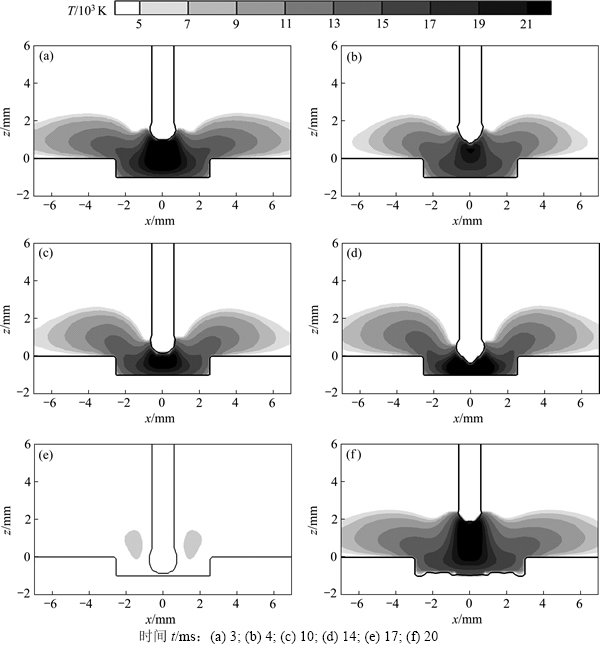
图4 有镀锌层时,不同时刻等离子体电弧区的温度分布
Fig. 4 Temperature distribution in plasma arcs at various instants with zinc layer
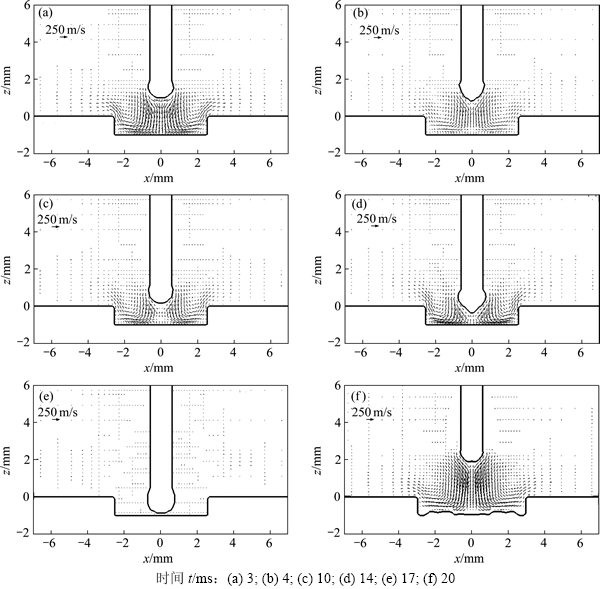
图5 有镀锌层时,不同时刻等离子体电弧区的速度分布
Fig. 5 Velocity distribution in plasma arcs at various instants with zinc layer
3.3 锌蒸气对CMT焊电弧的影响
图7所示为有、无镀锌层时,不同时刻小孔内电弧的温度和压力分布。由图7(a)可见:电弧温度分布接近于高斯分布,电弧温度在t=3 ms时最高,这是由于此时电流和电压较大。当电流由85 A(t=3 ms)降为55 A(t=4 ms),电弧温度明显降低。t=10 ms时,由于电弧长度较t=4 ms时变短,而电压和电流不变,使得相同的能量释放在更小的区域内,造成电弧温度较t= 4 ms时的高。对比有、无镀锌层的情况发现,远离中心处有镀锌层的温度较高,而靠近中心处无镀锌层的温度较高。这是由于锌蒸气扩散到纯氩等离子体中,改变了电弧的物性,尤其是电导率变大(见图2)。因此,当锌蒸气向电弧中扩散时,在远离中心处锌蒸气浓度较大(见图6),电弧电导率明显增大,在电流作用下气体更容易被电离,并使得此处的电弧温度升高。同时,由于能量平衡,靠近中心处的电弧温度有所降低。因此,锌蒸气的扩散导致电弧高温区域(T>1.2×104 K)增大。由图7(b)可见:电弧压力也呈高斯分布,其随时间变化的规律和温度变化规律相同。在同一时刻相同位置处,有锌情况下的电弧压力比无锌时的大。这是由于在有镀锌层的情况下,板2表面锌层蒸发产生向上的动压,与向下流动的等离子体相遇后,使得小孔内的电弧压力明显增加。电弧压力的增加将增大熔滴底部所受的阻力,影响熔滴向工件表面的过渡,易造成熔滴过渡和焊接过程的不稳定。
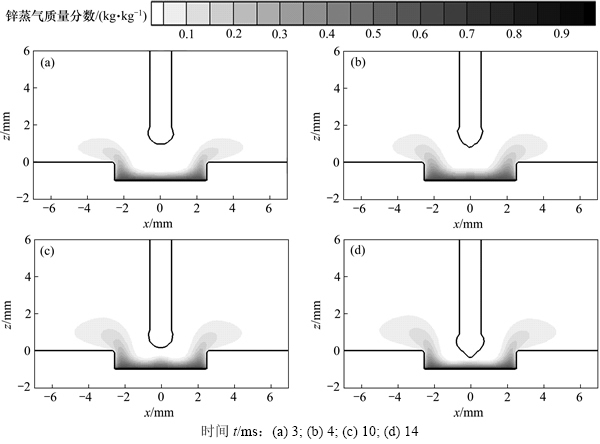
图6 有镀锌层时,不同时刻等离子体电弧区的锌蒸气质量分数分布
Fig. 6 Distribution of zinc vapor mass fraction in plasma arcs at various instants with zinc layer
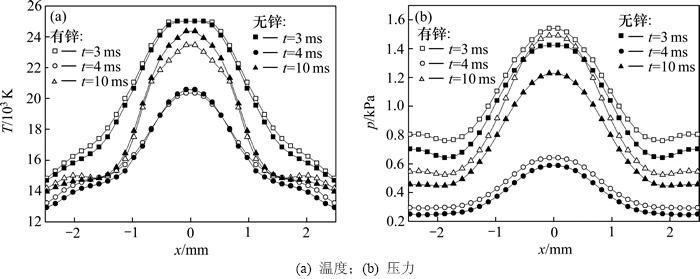
图7 有、无镀锌层情形下,不同时刻小孔内(z =-0.5 mm)电弧的温度和压力分布
Fig. 7 Comparison of arc pressure and arc temperature distribution between cases with and without zinc
4 结论
1) 电弧为一个典型的喇叭口形,电弧由上向下向外扩散,在焊丝顶端与工件上表面之间存在高温电弧柱,电弧温度沿电弧柱向外逐渐降低。等离子体在电磁力的作用下向下加速运动,在钢板上表面附近速度达到最大(约为200 m/s),到达钢板上表面后在压力的作用向外运动。
2) 锌层从工件表面蒸发,锌蒸气由工件表面扩散到等离子体电弧中。锌蒸气的浓度受等离子体流动形态的影响,焊丝下方电弧中心处的锌蒸气浓度很小。当电流较低或电弧长度较长时,等离子体速度减小,焊丝下方的锌蒸气浓度增大。
3) CMT焊接的过程中,由于焊接电流、电弧长度和锌蒸气的影响,电弧压力持续变化。锌蒸气的扩散导致电弧的电导率增大,使得电弧高温区扩大。锌层蒸发导致钢板上表面附近的电弧压力增大,尤其是在电弧长度变短时,电弧压力过大易造成熔滴过渡和焊接过程的不稳定。
参考文献:
[1] Schierl A. The CMT process: A revolution in welding technology[J]. Welding World, 2005, 49(9): 38.
[2] 李永兵, 林忠钦, 雷海洋, 等. 轻金属与镀层钢板的异种金属点焊系统及其焊接方法: 中国, CN 201010613175.1[P]. 2011-05-11.
LI Yongbing, LIN Zhongqin, LEI Haiyang, et al. Dissimilar metal spot welding system of light metal and coated steel and welding method: China, CN 201010613175.1[P]. 2011-05-11.
[3] Pickin C G, Young K. Evaluation of cold metal transfer (CMT) process for welding aluminium alloy [J]. Science and Technology of Welding & Joining, 2006, 11(5): 583-85.
[4] FENG Jicai, ZHANG Hongtao, HE Peng, et al. The CMT short-circuiting metal transfer process and its use in thin aluminium sheets welding[J]. Materials & Design, 2009, 30(5): 1850-1852.
[5] Pires I, Quintino L, Amaral V, et al. Reduction of fume and gas emissions using innovative gas metal arc welding variants[J]. The International Journal of Advanced Manufacturing Technology, 2010, 50 (5): 557-567.
[6] Haidar J. Predictions of metal droplet formation in gas metal arc welding. Ⅱ[J]. Journal of Applied Physics, 1998, 84(7): 3530-3540.
[7] 高如超, 饶政华, 李芸霄, 等. 脉冲GTAW熔池行为和焊缝成形的三维数值模拟[J]. 中南大学学报(自然科学版), 2013, 44(11): 4712-4719.
GAO Ruchao, RAO Zhonghua, LI Yunxiao, et al. Three dimensional modeling of weld pool dynamics and weld bead formation during pulsed GTAW[J]. Journal of Central South University (Science and Technology), 2013, 44(11): 4712-4719.
[8] Diao Q Z, Tsai H L. Modeling of solute redistribution in the mushy zone during solidification of aluminum-copper alloys [J]. Metallurgical Transactions A, 1993, 24(4): 963-973.
[9] Hu J, Tsai H L. Heat and mass transfer in gas metal arc welding. Part Ⅰ: The arc[J]. International Journal of Heat and Mass Transfer, 2007, 50(5): 833-846.
[10] Rao Z H, Hu J, Liao S M, et al. Modeling of the transport phenomena in GMAW using argon–helium mixtures. Part Ⅰ: The arc[J]. International Journal of Heat and Mass Transfer, 2010, 53(25): 5707-5721.
[11] Torrey M D, Mjolsness R C, Stein L R. NASA-VOF3D: A three–dimensional computer program for incompressible flows with free surfaces[R]. Los Alamos: Los Alamos National Laboratory, 1987: 4-5.
[12] Lowke J J, Morrow R, Haidar J. A simplified unified theory of arcs and their electrodes[J]. Journal of Physics D: Applied Physics, 1997, 30(14): 2033-2042.
[13] Lowke J J, Kovitya P, Schmidt H P. Theory of free-burning arc columns including the influence of the cathode[J]. Journal of Physics D: Applied Physics, 1992, 25(11): 1600-1606.
[14] Wu P C S, O’keefe T J, Kisslinger F. The inert gas effect on the rate of evaporation of zinc and cadmium[J]. Metallurgical and Materials Transactions A, 1980, 11(1): 123-126.
[15] Aubreton J, Elchinger M F, Rat V, et al. Two-temperature transport coefficients in argon-helium thermal plasmas[J]. Journal of Physics D: Applied Physics, 2004, 37(1): 34-41.
(编辑 杨幼平)
收稿日期:2014-12-06;修回日期:2015-03-09
基金项目(Foundation item):中央高校基本科研业务费专项资金资助项目(2013ZZTS206);江苏科技大学先进焊接技术省级重点实验室开放研究基金资助项目(JSAWT-13-03) (Project(2013ZZTS206) supported by the Fundamental Research Funds for the Central Universities; Project (JSAWT-13-03) supported by the Foundation of Provincial Key Lab of Advanced Welding Technology of Jiangsu University of Science and Technology)
通信作者:饶政华,博士,副教授,从事材料加工过程传热、传质分析研究;E-mail: raoz@csu.edu.cn