Effect of vacuum on solidification process and microstructure of LFC magnesium alloy
LIU Zi-li(刘子利)1, 2,LIU Xi-qin(刘希琴)1, XU Jiang(徐 江)1,GUO Hua-ming(郭华明)1,
PAN Qing-lin(潘青林)2, ZHOU Hai-tao(周海涛)2
1. College of Materials Science and Engineering , Nanjing University of Aeronautics and Astronautics, Nanjing 210016;
2. School of Materials Science and Engineering, Central South University, Changsha 410083, China
Received 28 July 2006; accepted 15 September 2006
Abstract: Lost foam casting (LFC) is regarded as a cost-effective, environment-friendly vital option to the conventional casting process for production of near-net shape castings with high quality. Effect of vacuum on the solidification process and microstructure of LFC magnesium alloy were explored. The results indicate that vacuum plays a very important role in the heat transfer during mould filling and solidification periods, it increases the cooling rate of the filling melt, but greatly decreases the cooling rate of the casting during solidification period, and the solidification time of the casting is greater than that without vacuum. The microstructure of LFC magnesium alloy is rather coarse. Compared with that without vacuum, the microstructure of the LFC magnesium alloy under vacuum is more refined and has less precipitated β-phase, which is formed at the grain boundry and around the Al-Mn compound particle.
Key words: magnesium alloy; lost foam casting; vacuum; solidification process; microstructure
1 Introduction
Magnesium alloys exhibit great potential in mass reduction for aerospace and automotive industries. Currently, casting is the main industrial forming method for magnesium alloys, the lag of research and development on casting technology has become a bottleneck for their further application[1-3]. Lost foam casting (LFC) has been regarded as a cost-effective, environment-friendly vital option to the conventional casting process for production of near-net shape castings[3-5]. As the great advantages over the traditional casting process and the bright application future, magnesium alloy LFC process has been paid increasing attentions in recent years[3, 6-11].
The great difference between LFC and conventional empty cavity casting is that there is foam pattern in the mold which will be gasified and removed out during the mold filling process. The endothermic degradation of the foam pattern produces a chilling effect in the liquid metal, and this will influence the solidification of the filling metal and microstructure of castings. Currently, the solidification characteristics in LFC process without vacuum have been investigated by many researchers, especially for aluminum alloys and cast iron[12-17], but little is known about effect of vacuum on the solidification and microstructure of LFC casting, though it has been reported that vacuum can increase the fluidity and metal fill velocity for aluminum and ferrous alloys, and lessen the carbon defects in ferrous alloy[4-5]. Previous works on mold filling suggested that vacuum plays a vital role in the magnesium alloy LFC process[3, 6, 7]. In the paper the effects of vacuum on the solidification process and microstructure of LFC magnesium alloy were investigated.
2 Experimental 2.1 Foam, molding, melting and pouring
30/15 mm(height)×30 mm(width) ×250 mm (length) patterns and a gate(30 mm×30 mm×200 mm) were hot-wire cut from EPS plates of nominal density 0.017 g/cm3, and assembled using commercially available glue. The ceramic coating was a low permeability coating providing by Ashland Chemical Company. The refractory slurry was brushed onto the patterns, and dried to a final thickness about 0.3 mm. The coated pattern was placed in the 40 cm×40 cm×40 cm flask with plenum chamber in its base, and filled with washed silica sand of 40/70 screen mesh until it was completely embedded in it. Then, a plastic sheet was covered onto the flask, and a pouring cup of baked clay sand was placed on the position of the sprue. When no vacuum was applied, the pouring cup was put directly on the top of the sprue.
Commercial AZ91 ingot was melted in an electric resistance furnace. During melting and pouring of the magnesium alloy, a protective atmosphere of 0.1%SF6+CO2 was used to prevent its oxidation and burning. The metal was poured under vacuum of 0 and 0.02 MPa, and with the pouring temperature of 750 ℃. If vacuum was applied, it was maintained throughout the whole pouring process and for another 5 min.
2.2 Data collection
Six thermocouples were positioned at 2, 6, 10, 14, 18, 22 cm from the sprue along the length of the foam pattern, and their tips lay at sectional center of the locations, and a thermocouple was also inserted into the top of the sprue to monitor the heat transfer and solidification behavior (Fig.1). Data from the thermocouples were collected and disposed by computerized data acquisition system. The process of the data collections was divided into 2 periods. For the first period, which was about 45 s from the beginning of pouring, the thermocouples were scanned every 0.02 s; afterwards, the thermocouples were scanned every 0.08 s for the second period to record the heat transfer characteristic and solidification behaviors after the mold filling finished.
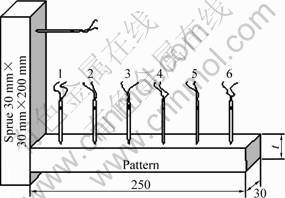
Fig.1 Schematic diagram of experimental setup: Six thermo- couples were located at intervals of 40 mm along the length of the foam pattern: 1—2 cm; 2—6 cm; 3—10 cm; 4—14 cm; 5—18 cm; 6—22 cm
3 Results 3.1 Solidification process of LFC magnesium alloy casting
Figs.2 and 3 show the cooling curves at different locations in the castings of the magnesium alloy LFC process without vacuum and under vacuum, respectively. From analysis of cooling curves, times and temperatures at the beginning and end of solidification for the LFC magnesium alloy castings are listed in Table 1.
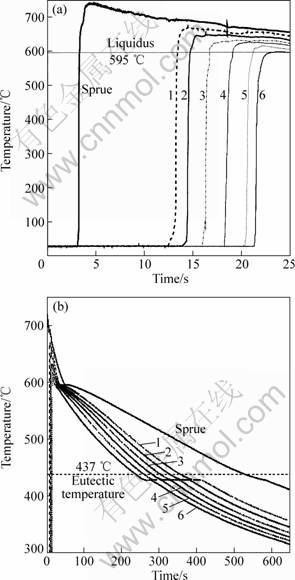
Fig.2 Cooling curves at each location in casting during magnesium alloy LFC process without vacuum(30 mm high pattern and 750 ℃ pouring temperature were used): (a) Mold filling period; (b) Whole casting period; 1—2 cm; 2—6 cm; 3—10 cm; 4—14 cm; 5—18 cm; 6—22 cm
Without vacuum, a positive temperature gradient was established from gating to the end of casting immediately after mold filling finished, and the temperature in the casting was near the liquids temperature (Fig.2). As the melt cooled down, solidification began at nearly the same temperature of 594 ℃ from the end of the casting to sprue (Table 1).
Under vacuum, the temperature of the liquid metal decreases sharply when it enters into sprue, most of the liquid metal is in the state of supercooling after mold filling (Fig.3), and solidified in a greater supercooling than that without vacuum (Table 1). A positive temperature gradient is also formed along the sprue to the end of casting in the late of casting solidification process (Fig.3), and solidification times in the casting increase inversely with the distance from the sprue. Compared with the cases without vacuum, solidification times in the casting are much longer, and the eutectic temperature is much lower (Table 1), so, the cooling rate of the casting under vacuum is definitely smaller during solidification period. From the analysis above, it can be indicated that applying vacuum increases the cooling rate of the mold filling melt, but greatly decreases the cooling rate of casting during solidification period.
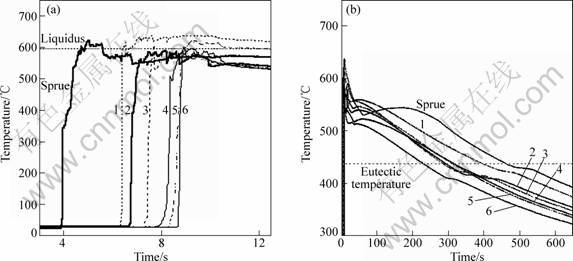
Fig.3 Cooling curves at each position in casting during magnesium alloy LFC process under vacuum(30 mm high pattern, 750 ℃ pouring temperature and 0.02 MPa vacuum were used): (a) Mold filling period; (b) Whole casting period; 1—2 cm; 2—6 cm; 3—10 cm; 4—14 cm; 5—18 cm; 6—22 cm
Table 1 Time and temperature at beginning and end of solidification, and cooling rates during solidification processes for LFC magnesium alloy castings (30 mm thick patterns)
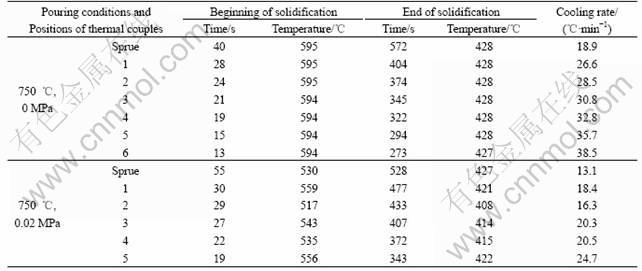
3.2 Microstructures of LFC magnesium alloy castings
As shown in Fig.4, the microstructure of LFC AZ91 magnesium alloy is much coarse, disconnected netted β(Mg17Al12) phase distributes along grain boundary of α-Mg matrix. There are two types of β phase in the microstructure: the white one is the divorced eutectic β phase, while the dark one in the lamellar structure is the precipitated β phase. From the analysis of EDX (Fig. 5), the dark pellet scatters in α-Mg matrix is Al-Mn intermetallic compound containing small amount of Fe. Besides grain boundary, the precipitated β phase also forms around the Al-Mn compounds (Fig. 6).
The effects of vacuum on microstructures of LFC AZ91 alloy is shown in Fig.7. Compared with that without vacuum, the microstructure of LFC magnesium under vacuum is refined and has less precipitated β phase. This indicates that the greater cooling rate of the mold filling melt under vacuum refines the grain and the lower eutectic temperature suppresses the formation of the precipitated β-phase, though the cooling rate of casting during solidification period is greatly reduced.
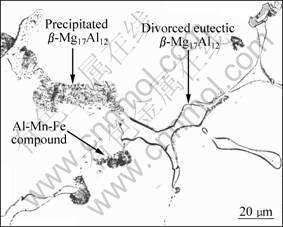
Fig.4 Microstructure of LFC AZ91magnesium alloy
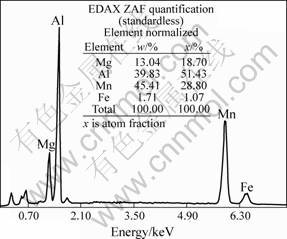
Fig.5 EDAX analysis of spherical phase in LFC AZ91 magnesium alloy
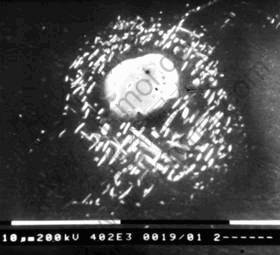
Fig.6 β phase precipitated at interface of Al-Mn compound and α-Mg compound
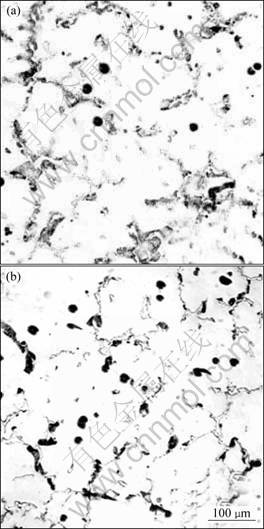
Fig.7 Effects of vacuum on microstructures of LFC AZ91 alloys(15 mm high patterns were used): (a) Without vacuum; (b) 0.02 MPa
4 Discussion
During the mold filling process of LFC, the existence of the foam makes the heat transfer behaviors of the metal liquid more intricate than that of conventional casting process. On one side, the foam endothermic decomposition is a complex Stefan heat transfer process, at which the heat transfer medium is the liquid and gaseous thermal decomposed products between the moving mental-foam interface. The type and amount of foam thermal decomposed products determine the size of mental-foam interface, thus the effect of Stefan heat transfer (even if the mental-foam interface is less than 0.05 cm, it can still prevent heat transfer from the mental liquid to the foam greatly[13]), and the removing process of the foam decomposition products also carry some heat away from the liquid metal by heat convection. On the other hand, the removing liquid products between the mental-foam interface will be gasified during the mold filling process and LFC employed the dry sand, the heat transfer of the liquid metal to the surrounding sand through coating layers will be quite different from the traditional casting process. The rate of pattern degradation and the expelling rate of the degradation products determine the contact time of liquid metal with the foam pattern and the mold, thus the heat transfer effects of the liquid metal.
Without vacuum, the heat loss of the filling metal is mainly due to the mode of Stefan radiation to liquefy the foam and the mode of heat conduction to the surrounding coating and sand, while heat loss by the removing gaseous products in the mode of heat convection is very small[13]. Just as that in the conventional sand casting process, when α-Mg forms the consecutive solid skeleton in the casting, the solidification shrinkage of the casting will produce a gap at the metal-coating interface, which will become the major heat resistance in the metal solidification, thus, the casting cooling rate is greatly reduced, and the microstructure of LFC magnesium alloy is rather coarse. The divorced eutectic reaction of the remained small liquid at the end of solidification, leads β phase distribute along the grain boundary, afterwards, the precipitated β phase will be formed in α-Mg solution mainly at grain boundary. Furthermore, the precipitated β phase is easy to nucleate and grow up near Al-Mn compound particle.
During the mold filling process with vacuum, the heat convection effect of the sucked fresh air at the pouring cup makes the temperature of the filling melt reduce greatly. As lower heat content of liquid magnesium alloy, the liquid metal in the mold cavity after mold filling is in the state of great supercooling. For the nuclear rate at the start of solidification determines the grain size, the microstructure of LFC magnesium alloy under vacuum is refined than that without vacuum. Applying vacuum makes the air in the casting-coating interface gap much rarer than that without vacuum[17], the cooling rate of the casting during solidification is smaller. As the actual eutectic temperature under vacuum is far below equilibrium eutectic temperature (Fig.3), eutectic reaction will be more divorced, and precipitation of β phase after solidification will be suppressed.
5 Conclusions
1) The applied vacuum plays a very important role for the LFC magnesium alloy during the mold filling and solidification process. It increases the cooling rate of the filling melt, but greatly decreases the cooling rate of the casting during solidification period, and the solidification time of the casting is greater than that without vacuum.
2) For the microstructure of LFC AZ91 magnesium alloy, disconnected netted β (Mg17Al12) phase distributes along grain boundary, and the precipitated β phase forms at the grain boundary and around Al-Mn compound particle. Compared with that without vacuum, the microstructure of LFC magnesium alloy under vacuum is refined and has less precipitated β-phase, which is formed at the grain boundary and around Al-Mn compound particle.
References
[1] NICHOLAS J. High-performance magnesium[J]. Advanced Materials and Processes, 2005, 193(9): 65-67.
[2] LUO A A. Recent magnesium alloy development for automotive powertrain applications[J]. Materials Science Forum, 2003, 419/422: 57-65.
[3] LIU Zi-li, HU Jing-yu, DING Wen-jiang, et al. Evaluation of the effect of vacuum on mold filling in the magnesium EPC process[J]. Journal of Materials Processing Technology, 2002, 120: 94-100.
[4] HAND B. High-alloy and stainless steel applications of the EPC process[J]. AFS Transactions, 1993, 101: 323-326.
[5] PAN En-ning, LIAO Kao-yu. Analysis of the flow and solidification patterns of the lost foam (EPC) A356 Al cast alloy[J]. Journal of the Chinese Society of Mechanical Engineers, 2000, 21(3): 283-92.
[6] LIU Zi-li, WU Guo-hua, DING Wen-jiang, et al. Study on molding filling velocity in AZ91 magnesium alloy LFC process with vacuum[J]. Journal of Aeronautical Materials, 2002, 22(2), 12-16. (in Chinese)
[7] LIU Zi-li, PAN Qing-lin, CHEN Zhao-feng, et al. Investigation of foam-metal interface behaviors during mold filling of magnesium alloy LFC proces[J]. Transactions of Nanjing University of Aeronautics & Astronau, 2006, 23(1), 72-80.
[8] Anon. Genesis of a new process: Magnesium lost foam casting[J]. Modern Casting, 2003, (4): 26-28.
[9] BICHLE L, RAVINDRAN C, MACHIN A. Challenges in lost foam casting of AZ91 alloy[J]. Materials Science Forum, 2003, 426-432: 533-538.
[10] CHO G S, LEE K W, KIM S K, et al. Expendable pattern casting of AZ91D magnesium alloy[J]. Materials Science Forum, 2003, 426-432: 623-628.
[11] TIAN Xue-feng, FAN Zi-tian, HUANG Nai-yu, et al. Microstructure and mechanical properties of magnesium alloy prepared by lost foam casting[J]. Trans Nonferrous Met Soc China, 2005, 15(1): 7-13.
[12] SHIVKUMAR S. Casting characteristics of aluminum alloys in the EPC process[J]. AFS Transactions, 1993, 101: 513-518.
[13] SHIVKUMAR S. Modelling of temperature losses in liquid metal during casting formation in expendable pattern casting process[J]. Materials Science and Technology, 1994, 10 (11): 986-992.
[14] BENNETT S, RAMSAY C W, ASKELAND D R. Temperature gradients during fill and solidification of Al LFCs[J]. AFS Transactions, 1998, 106: 357-363.
[15] SHIVKUMAR S, WANG L, APELIAN D. The lost-foam casting of aluminum alloy components[J]. JOM, 1990, 42(11): 38-44.
[16] YAO X, SHIVKUMAR S. Mold filling and solidification in the lost foam process[J]. AFS Transactions, 1995, 103: 761-765.
[17] VENKATARAMANI R, RAVINDRAN C. Effects of coating thickness and pouring temperature on thermal response in lost foam casting[J]. AFS Transactions, 1996, 104: 281-290.
(Edited by CHEN Can-hua)
Foundation item: Project (2005037697) supported by China Postdoctoral Science Foundation; project (Y04850-61) supported by Creative Program of Nanjing University of Aeronautics and Astronautics
Corresponding author: LIU Zi-li; Tel: +86-25-52112626; E-mail: zililiu@sohu.com