
Synthesis and electrochemical behavior of LiCoO2 recycled from incisors bound of Li-ion batteries
LIU Yun-jian(刘云建), HU Qi-yang(胡启阳), LI Xin-hai(李新海),
GUO Hua-jun(郭华军), WANG Zhi-xing(王志兴)
School of Metallurgical Science and Engineering, Central South University, Changsha 410083, China
Received 15 July 2007; accepted 10 September 2007
Abstract: LiCoO2 was separated from Al foil with dimethyl acetamide(DMAC), and then polyvinylidene fluoride(PVDF) and carbon powders in active material were eliminated by high temperature calcining. The content of the elements in the recovered powders were analyzed. Then the Li2CO3 was added in recycled powders to adjust molar ratio of Li to Co to 1.00, 1.03 and 1.05, respectively. The new LiCoO2 was obtained by calcining the mixture at 850 ℃ for 12 h in air. Structure and morphology of the recycled powders and resulted sample were observed by XRD and SEM technique, respectively. The layered structure of the LiCoO2 is improved with the decrease of molar ratio of Li to Co. The charge/discharge performance, and cyclic voltammograms performance were studied. The recycle-synthesized LiCoO2 powders, whose molar ratio of Li to Co is 1.0, is found to have the best characteristics as cathode material in terms of charge—discharge capacity and cycling performance. And the cyclic voltammograms(CV) curve shows the lithium extraction/insertion characteristics of the LiCoO2 well.
Key words: LiCoO2; synthesis; electrochemical behavior; cyclic voltammograms
1 Introduction
Layered LiCoO2 is the most widely used positive electrode material in commercial lithium secondary batteries due to ease of preparation, high electronic conductivity, and excellent cycling performance, etc. The market for Li-ion battery(LIB) has expanded rapidly because of the increase in demand for mobile electronics. It is reported that the total world sales of the Li-ion cells have reached more than 10 billion dollars in 2006[1]. It demands for large amount of Co to meet the market. So in one hand, the LiMn2O4[2-3], LiFePO4[4-5] and Li[NiCoMn]O2[6-7] with low or no content of Co have attracted more and more attention because of their low price, abundant resources and safety;and in other hands, many researchers have paid attention to the recycle of LIB[8-12].
JINSIK et al[8] reported that cobalt ions, extracted from waste LiCoO2 by using a nitric acid leaching solution, were transformed into cobalt hydroxide on a titanium electrode and cobalt oxide was then obtained via a dehydration procedure. ZHANG et al[9] reported the recycle of the valued metal such as cobalt and lithium from the spent Li-ion secondary batteries. MICHEAL[10] recycled the valued metal from waste cell using a special processing technology. The above investigators just recycled the valuable metal from the waste batteries. But CHURL et al[11] and CESTAILE et al[12] not only recycled the valuable metal but also prepared new LiCoO2 just by using the recycled valuable metal.
In this work, a new LiCoO2 recycle and synthesis technology from the incisors bound of Li-ion battery is studied. Wherein the impurities of cathode such as polyvinylidene fluoride(PVDF) and carbon powders are eliminated by calcining at high temperature; after recycle the Li2CO3 is added in the recycled powders to adjust the molar ratio of Li to Co to 1.00, 1.03 and 1.05; the structure, morphology and electrochemical behaviors of the recycle-synthesized LiCoO2 are studied.
2 Experimental
At first, a certain incisors bound of Li-ion battery was immersed in dimethyl acetamide(DMAC), and the aluminum foil was picked out several hours later. The solution was filtrated after several-hour deposition. The cathode material without aluminum was gained after filtration. Then the cathode material was heated at 120 ℃ in air for 12 h. The dry powders were firstly heated at 450 ℃ in air for 2 h, then heated at 600 ℃for 5 h to gain the recycled powders. The structure and morphology of the recycled powders were characterized with XRD and SEM technique. The content of the Co was analyzed by titrating, and the content of the element Li was analyzed by atomic absorption spectrometry.
The Li2CO3 was added in the recycled powders to adjust the molar ratio of Li to Co to 1.00, 1.03 and 1.05, respectively. The final LiCoO2 was synthesized by calcaining at 850 ℃ for 12 h in air, and cooled to room temperature in a tube-furnace.
The powders X-ray diffraction(XRD, Rint-2000, Rigaku) measurement using Cu Kα radiation was employed to identify the crystalline phase of the synthesized materials. And the particle size and morphological character of the LiCoO2 powders were measured by scanning electron microscope (JEOL, JSM-5600LV) with an accelerating voltage of 20 kV.
The electrochemical characterizations were carried out using a CR2025 coin type cell. For cathode fabrication, the prepared powders were mixed with 10% (mass fraction) of carbon black and 10% (mass fraction) of polyvinylidene fluoride in N-methyl pyrrolidinone until slurry was obtained. The blended slurries were pasted onto an aluminum current collector, and the electrode was dried at 100 ℃ for 12 h in vacuum. The test cell consisted of the cathode and lithium foil anode coated by a porous polypropylene film, cellgard 2300 as the separator and 1 mol/L LiPF6 in EC?EMC?DMC (C3H4O3?C4H8O3?C3H6O3, 1?1?1 in volume) as the electrolyte. The assembly of the cells was carried out in a dry Ar-filled glove box. Capacity measurements and cycling tests of the coin-type cells were carried out between 3.0 V and 4.2 V at current density of 0.2 C and temperature of 25℃.
The cyclic voltammetry(CV) measurements were performed on LiCoO2 electrode at a sweep rate of 0.1 mV/s over a volt of 3.0-4.4 V.
3 Results and discussion
The surface morphology of the recycled LiCoO2 powders is shown in Fig.1. Some small particles, with diameter of 1 μm are observed in Fig.1. Some particles were smashed during the recycle process of high temperature calcining and washing.
XRD patterns of recycled LiCoO2 powders are shown in Fig.2. The diffraction peaks of Co3O4 at 31.3?, 36.8? are observed in Fig.2. To analysis the reaction and validate the reaction results, the recycled powders were
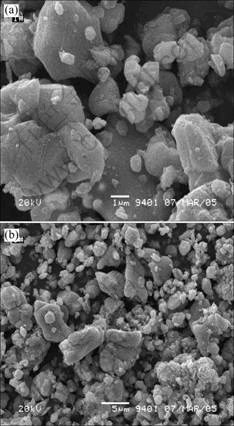
Fig.1 SEM micrograph of recycled powders
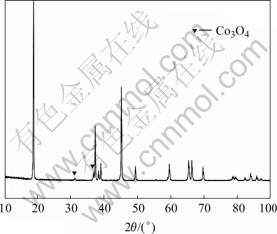
Fig.2 XRD patterns of recycled LiCoO2 powders
washed by hot water, and then filtrated. White deposition appeared after adding CaCl2 solution into the hot filtrate. The white deposition should be CaF2. We just think that PVDF gives out HF when it is heated. And the HF reacts with LiCoO2 to produce Co3O4 and LiF.
The content of the elements in the recycled powders were analyzed. The results are listed in Table 1. From Table 1, it can be known that the content of the C and F are little, and the molar ratio of Li to Co is 0.914, which is not consistent with that of the normal LiCoO2.
Table 1 Content of elements in recycled LiCoO2 (mass fraction, %)

SEM micrographs of the LiCoO2 synthesized at different molar ratios of Li to Co are shown in Fig.3. Compared with Fig.1 the small particles disappeared and the particle size raised with the increase of the molar ratio of Li to Co. The average particle size is over 5 μm. This is because that the small particle reunites when the residual Li2CO3 melts at high temperature.
The final LiCoO2 was obtained by adding a certain amount of Li2CO3 in the recycled LiCoO2 and calcining at 850 ℃ for 12 h. Fig.4 shows the XRD of the LiCoO2 synthesized at different molar ratios of Li to Co. A pure phase of LiCoO2 could be identified. The high intensity of the (003) peak and the clear splitting between the (006)/(012) and (018)/(110) peaks can be observed in Fig.4. The spinel phase of Co3O4 has disappeared indicating that Co3O4 reacts with Li2CO3 at high temperature, and well-crystallized single phase LiCoO2 could be obtained after calcining for 12 h at 850 ℃.
The ratio of I(003)/I(104) of LiCoO2 synthesized at different molar ratios of Li to Co is listed in Table 2. It shows that the ratio of I(003)/I(104) of LiCoO2 is increased with the decrease of molar ratio of Li to Co. The intensity ratio of (003) to (104) is known to be closely related to the degree of cation disordering in the doped LiCoO2 crystals[13]. We think that the degree of cation disordering is increased by redundant Li inasmuch as higher I(003)/I(104) ratio corresponds to lower degree of cation mixing and lower R-factor. According to Ref.[14], the lower the R-factor, the better the hexagonal ordering and hence the electrochemical performance.
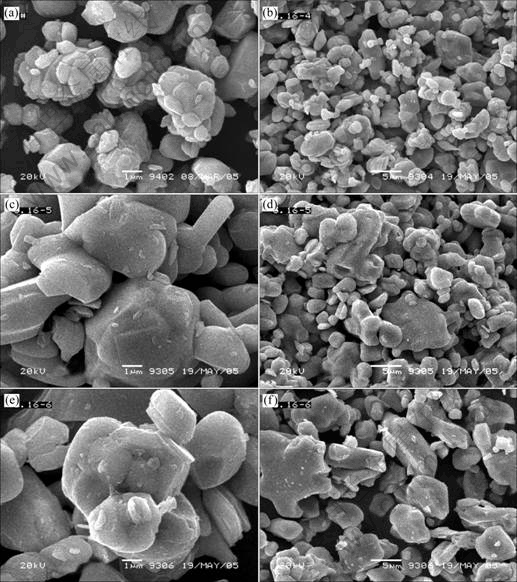
Fig.3 SEM micrographs of LiCoO2 synthesized at different molar ratios of Li to Co: (a)-(b) 1.0; (c)-(d) 1.03; (e)-(f) 1.05
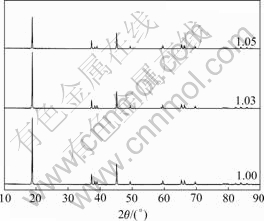
Fig.4 XRD patterns of LiCoO2 synthesized at different molar ratios of Li to Co of 1.0, 1.03, 1.05 respectively
Table 2 Ratio of I(003)/I(104) of LiCoO2 synthesized at different molar ratios of Li to Co

The electrochemical performances of LiCoO2 synthesized at different Li/Co ratios were tested with coin cell. The samples were cycled between 3.0-4.2 V at a constant current density 0.2 C rate. The first discharge curves of the samples are given in Fig.5. The initial discharge capacity of LiCoO2 decreases with the increase of the molar ratio of Li to Co. The discharge capacities of samples with molar ratio of Li to Co of 1.0, 1.03 and 1.05 are 150, 147 and 142 mA?h/g, respectively. This is because that the overdosed Li decreases the hexagonal ordering, and results in lower discharge capacity.
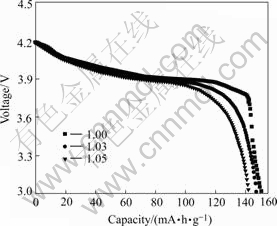
Fig.5 Discharge curve of LiCoO2 synthesized at different molar ratios of Li to Co of 1.0, 1.03, 1.05 respectively
The discharge plateau of the three samples is same, just situating between 3.9-4.0 V. These are the same as those for conventional HT-LiCoO2.
Fig.6 shows the cycling data of cells made of LiCoO2 synthesized at different Li/Co molar ratios. The test cells were cycled at 0.2 C rate between 3.0 and 4.2 V at room temperature. The LiCoO2 whose Li/Co ratio is 1.0 shows the best cycling performance. After 30 cycles, the capacity retention is 93.5%, while those of the other two samples are 93.0% and 91.5%. These results indicate that existence of overdose Li decreases the capacity of LiCoO2 during charge-discharge cycling. As mentioned before, the channel for Li+ diffusion is jammed by overdose Li and affects the hexagonal order. So the cycling behavior was affected.
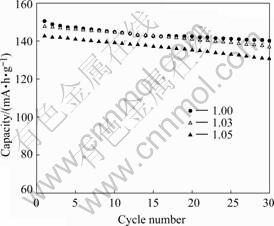
Fig.6 Cycling performance of LiCoO2 synthesized at different molar ratios of Li to Co of 1.0, 1.03, 1.05 respectively
Cycle voltammograms technology was used to compare the difference between the recycle-synthesized LiCoO2 and the normal LiCoO2. Fig.7 shows the CV curves of the recycle-synthesized and normal LiCoO2. There are no obvious difference between the two curves. This indicates that the structure of the recycle- synthesized LiCoO2 is similar with that of the normal LiCoO2. There are two obvious and one unconspicuous peaks in the oxidation process, and corresponding three peaks in reductive process. The curve is the same as what in GEORGE’s report[14]. The three cathodic and anodic peaks correspond to as many LiCoO2 structure changes. The first peak at 4.045 V is related to the existence of a two-phase domain for LixCoO2(0.75<x<0.94) and the third peak at 4.19 V corresponded to the presence of a monoclinic distortion for x=0.5 due to an interslab Li/vacancy ordering. The second peak at 4.09 V is unidentified[15].
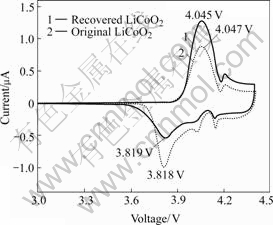
Fig.7 CV curves of LiCoO2
4 Conclusions
1) Cathodic powders are separated from the Al foil with dimethyl acetamide(DMAC) easily, and then the impurity, polyvinylidene fluoride(PVDF) and carbon powders, in the active material are eliminated by high temperature calcining, and there are some Co3O4 in the obtained powders.
2) The new LiCoO2 is obtained after calcine for 12 h in air at 850 ℃ by adding a certain amount of Li2CO3. The well-crystallized single phase LiCoO2 without Co3O4 phase is obtained. The layered structure of the LiCoO2 is improved when the Li/Co molar ratio is lower.
3) The recycle-synthesized LiCoO2 powders, whose Li/Co molar ratio is 1.0, is found to have the best discharge capacity and cycling behavior. The first discharge capacity is 150 mAh/g, and the capacity retention is 93.5% after 30 cycles.
4) The cyclic voltammograms curve shows that there is no structure difference in the synthesized LiCoO2 and normal LiCoO2. And it also shows the lithium extraction/ insertion performances of the LiCoO2 well.
References
[1] KIM J, BYOUG S K, LEE J G, CHO J, BYUNG PP W. Differential voltage analyses of high-power, lithium-ion cells (I): Technique and Application [J]. J Power Sources, 2005, 139(1/2): 289-294.
[2] TU Jian, ZHAO Xin-bing, CAO Gao-shao, TU Jiang-ping, ZHU Tie-jun. Improved performance of LiMn2O4 cathode materials for lithium ion batteries by gold coating [J]. Mater Lett, 2006, 60(5): 3251-3254.
[3] LI Yang, MICHIO T, WANG Bao-feng. A study on capacity fading of lithium-ion battery with manganese spinel positive electrode during cycling [J]. Electrochemical Acta, 2006, 51(9): 3228-3234.
[4] CHOI D, KUMTA P N. Surfactant based sol-gel approach to nanostructured LiFePO4 for high rate Li-ion batteries [J]. J Power Sources, 2007, 163(2): 1064-1069.
[5] WANG Yang-qiang, WANG Jiu-lin, YANG Jun, NULI A Y. High-rate LiFePO4 electrode material synthesis by a novel route from FePO4?4H2O [J]. Advanced Functional Materials, 2006, 16: 2135-2140.
[6] ZHANG Shi-chao, QIU Xin-ping, HE Zhi-qi, WENG Dang-sheng, ZHU Wen-tao. Nanoparticle Li(Ni1/3Co1/3Mn1/3)O2 as cathode material for high-rate lithium-ion batteries [J]. J Power Sources, 2006, 153(1): 350-353.
[7] CHO T H, SHIOSAKI Y, NOGUCHI H. Preparation and characterization of layered LiMn1/3Ni1/3Co1/3O2 as a cathode material by an oxalate co-precipitation method [J]. J Power Sources, 2006, 159(4): 1322-1327.
[8] JINSIK M, JUNG Y W, LEE J Y, TAK Y S. Cobalt oxide preparation from waste LiCoO2 by electrochemical-hydrothermal method [J]. J Power Sources, 2002, 112(2): 639-642.
[9] ZHANG Ping-wei, YOKOYAMA T, ITABASHI O, SUZUKI T M, INOUE K. Hydrometallurgical process for recovery of metal values from spent lithium-ion secondary batteries [J]. Hydrometallurgy, 1998, 47(2/3): 259-271.
[10] MICHIAEL J L. Recycling of lithium ion cells and batteries [J]. J Power Sources, 2001, 97/98(1): 736-738.
[11] CHURL K L, KANG-IN R. Preparation of LiCoO2 from spent lithium-ion batteries [J]. J Power Sources, 2002, 109(1): 17-21.
[12] CESTAILE M, PANERO S, SCROSATI B. A laboratory-scale lithium-ion battery recycling process [J]. J Power Source, 2001, 92(1/2): 65-69.
[13] FANG T, DUH J, SHEEN S. LiCoO2 cathode material coated with nano-crystallized ZnO for Li-ion batteres [J]. Thin Solid Films, 2004,469/470(1): 361-365.
[14] FEY G T, LIN Y Y, KUNAR T P. Enhanced cyclability and thermal stability of LiCoO2 coated with cobalt oxides [J]. Surface & Coatings Technology, 2005, 191(1): 68-75.
[15] ANTOLINI E. LiCoO2: Formation, structure, lithium and oxygen nonstoichiometry, electrochemical behaviour and transport properties [J]. Solid State Ionics, 2004, 170(1): 159-171.
(Edited by LAI Hai-hui)
Foundation item: Project(2007CB613607) supported by the National Basic Research Program of China
Corresponding author: HU Qi-yang; Tel: +86-731-8836633; E-mail: hqyangbox@163.com