
Mechanical and friction properties of aluminum and titanium reinforced Ni-based self-lubricating composite
LI Jian-liang(李建亮), XIONG Dang-sheng(熊党生)
Department of Materials Science and Engineering,Nanjing University of Science and Technology,
Nanjing 210094, China
Received 15 July 2007; accepted 10 September 2007
Abstract: Ni-20Cr powders mixed with tungsten, aluminum, titanium, and different contents of molybdenum disulfides were hot-pressed in graphite mould by powder metallurgy method. Their tribological properties from room temperature to 600 ℃ and mechanical properties at atmosphere were tested. The results show that the hardness and anti-bending strength of composites increase by more than 20% when containing 6%(mass fraction) MoS2. But when molybdenum disulfide content exceeds 6%, the hardness and anti-bending strength will decrease gradually. The addition of MoS2 is favored to the reduction of friction coefficient of composite. The friction coefficient of composite decreases with the increase of molybdenum disulfide until the percentage of lubricant reaches 12%. In excess of this value, the friction coefficient value starts to ascend. The wear rates of composite with molybdenum disulfide are one order of magnitude lower than the alloy without lubricant. When the addition amount of MoS2 is in the range of 6% and 12%, the wear rates keep at the resemble level.
Key words: Ni-20Cr; MoS2; solid lubrication; self-lubricating composite; high-temperature; friction
1 Introduction
Solid lubricating materials that are effective over an extreme range of operating temperatures are necessary for the development of new generation high-performance gas turbine engines[1]. Molybdenum disulfide is a widely used solid lubricant and performs best under dry conditions[2]. Its lubricating properties are largely attributed to its lamellar structure and inert basal planes existing in the individual crystallites where very easy shear occurs. However, molybdenum disulfide is instable at high temperature and will decompose in the process of hot pressing when it is used as additive in the metal-based composite, which induces its lubricating function lost partly[3-6]. LIU et al[3] found that the chromium sulfide formed by reaction was also excellent solid lubricant. WU et al[4] prepared Ni/MoS2 self-lubricating composite by powder metallurgy method and found that mechanical properties of the composites decrease with the increase of MoS2 amount. LI et al[5] added Ni coated MoS2 in the metal matrix and found that nickel coating can prevent the decomposition of MoS2 during hot pressing, resulting in good mechanical but a little higher friction coefficient at 600 ℃. XIONG et al[6] discussed the synthesis action of oxide film and molybdenum disulfide at high temperature.
In this work, nickel-based composites containing molybdenum disulfide were prepared by powder metallurgy (P/M) method. Their mechanical and tribological properties were investigated.
2 Experimental
2.1 Materials preparation
Ni-20Cr alloy powder(about 60 μm), tungsten (20 μm), aluminum, titanium powder, and 0-20%(mass fraction) MoS2 (20 μm) were mixed together and pressed as disks (diameter of 45 mm and thickness of 8 mm) in a steel mould. The temperature was elevated to 1 240 ℃ at 20 ℃/min. The furnace was draw vacuum to 10-5 Pa and protected by nitrogen gas. After holding for 20 min, they were hot pressed under 16 MPa in vacuum.
2.2 Properties testing
Friction and wear tests were carried out on a MG-2000 high-temperature pin-on-disk tribometer (Beilun Corp.). The upper samples of flat-ended composite pins (d5 mm×12 mm) were kept still, while counterface disks were rotated. The mating materials were alumina ceramic disk (d52 mm×8 mm, hardness HRC70, roughness 1.5 μm). The load was 50 N, the sliding velocity was 0.8 m/s, the environment temperature was room temperature, 200, 400, 600 ℃. The sliding distance was 600 m. The average wear track was 31 mm. The frictional moment was recorded by a computer consistently. The samples were cleaned by ethanol after each test. The wear mass losses of pins were weighed by an analytical balance with accuracy of 0.1 mg. The microstructure and transferring glaze layer were analyzed by SEM and XRD, and the worn surface profiles were observed by optical microscope.
3 Results and discussion
3.1 Phase and microstructure
It is shown in Figs.1(a) and (b) that sulfide and tungsten are dispersed in the matrix. XRD results indicate that there are Cr3S4 and TiS formed in the alloy besides nickel-based solution (Fig.1(c)). Although molybdenum disulfide reacts with matrix and reduces its lubrication function to some degree, but new phases such as Cr3S4 and Cr5S6 formed through reaction are also excellent solid lubricants[7].
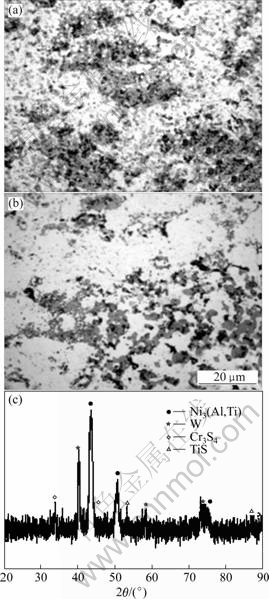
Fig.1 Optical morphologies of nickel-based composite with 12% MoS2(a) and 20% MoS2(b) and X-ray diffraction pattern(c) of composites(12% MoS2)
3.2 Mechanical properties
It is shown in Table 1 that with the increase of the adding amount of MoS2, the density of composite decreases linearly, corresponding to its theoretical value, which indicates that the composites are compact. With the increase of MoS2, the hardness of composite increases a little, but decreases slightly when the content of MoS2 exceeds 12%. The anti-bending strength of composite is improved by adding MoS2, but is reduced when the content of MoS2 exceeds its critical value (12%). The hardness and anti-bending strength of composite are kept at a relatively high value due to the solid solution strength of molybdenum.
Fig.2 shows the fracture surface of composite without MoS2 and 12%MoS2, respectively. The surface of composite without MoS2 shows the brittle fracture feather and the cracks appears, while the surface of composite with 12%MoS2 forms cavities in which the MoS2 exist. Theoretically, molybdenum disulfide as relatively soft phase will ruin mechanical properties of composite when adding into the composite (see Fig.2(b)).
Table 1 Mechanical properties of Ni-based composite
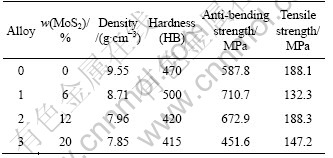
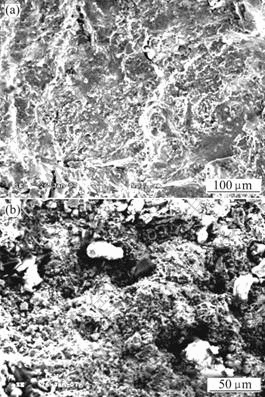
Fig.2 Fracture morphologies without MoS2(a) and with 12% MoS2(b)
However, when molybdenum disulfide discomposes and reacts with metal matrix, the interface between lubricant phase and matrix is not evidence, which is positive to the mechanical properties[8]. Furthermore, molybdenum dissolves into nickel-based alloy and reinforces nickel matrix, which is also responsible for the excellent mechanical properties.
3.3 Effect of adding amounts of MoS2 on friction properties of composites
It is shown in Fig.3(a) that the friction coefficient decreases with the increase of temperature at elevated temperature. When the adding amount of MoS2 is below 6%,the friction coefficient is relatively high. Low friction coefficient appears until the adding amount of MoS2 exceeds 12%. At 600℃, the friction coefficient is less influenced by the amount of MoS2 due to the assistant lubrication of oxide[9]. In this study, the composite containing 12%MoS2 shows the lowest friction coefficients from room temperature to 600 ℃.
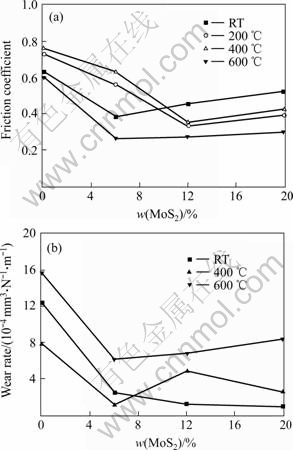
Fig.3 Friction coefficient(a) and wear rate(b) vs MoS2(50 N, 0.8 m/s, Al2O3)
As shown in Fig.3(b), the wear rate of composite containing MoS2 is much less than those of pristine alloys from room temperature to 600 ℃. The wear rate of Ni-Cr-W-Al-Ti alloy is in the magnitude of 10-4 mm3/(N?m) while those of composites containing MoS2 are in the range of 10-6-10-5 mm3/(N?m). The composite with 6%-12% MoS2 has low wear rate at 400 ℃ and 600 ℃. When the adding amount of MoS2 reaches 20%, the wear rate rises again. In summary, too high and too low contents of MoS2 are not beneficial to the tribological properties of nickel-based self- lubricating composite[10-11]. In this study, the optimum amount of MoS2 addition is 12%.
Fig.4 shows the worn surface morphologies of composites after rubbing with Al2O3 at room temperature and 600 ℃. The worn surface at room temperature presents integrant sulfide lubricating film (Fig.4(a)). The worn surface morphology of composite containing MoS2 at elevated temperatures is covered with melted sulfide (Fig.4(b)), while that of pristine alloy consists of only oxide films(Fig.4(c)). The abrasive wear character appears visibly on the worn surfaces at 600 ℃ due to low-melt-point sulfide partly melted and soft at high temperature[12-13]. Fig.4(d) shows the morphologies of glaze layers on the worn surface of Ni-Cr-W-Al-Ti-MoS2 pins, which is formed through the agglomerate and compact of chromium oxides and other oxides[14-15].
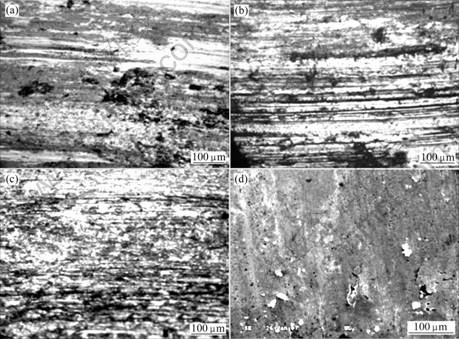
Fig.4 Worn morphologies of Ni-based composite: (a) 12% MoS2, room temperature; (b) 12% MoS2, 600 ℃; (c) Without MoS2, 600 ℃; (d) Glaze layer of 12% MoS2, 600 ℃
4 Conclusions
1) Nickel-based self-lubricating composites containing sulfur were prepared by powder metallurgy (P/M). The composites mainly consist of nickel-based solution, chromium sulfide, tungsten.
2) When the adding amount of MoS2 is suitable, the mechanical properties and tribological properties of composite are improved significantly, especially the friction properties at higher temperature, and the optimum amount of MoS2 in this study is 12%.
3) The lowest friction coefficient of 0.20-0.50 is obtained when using alumina ceramic as counter material from room temperature to 600 ℃.
References
[1] XUE Qun-ji, LV Jin-jun. Research status and developing trend of solid lubrication at high temperatures[J]. Tribology, 1999, 19(1): 91-96. (in Chinese).
[2] DONNET C, ERDEMIR A. Historical developments and new trends in tribological and solid lubricant coatings[J]. Surface and Coatings Technology, 2004, 180/181: 76-84
[3] LIU Ru-tie, LI Xi-bin, XIONG Dang-sheng, GHENG Shi-he. Study on the tribological characteristics of a high-temperature self-lubricating nickel-base material[J]. Journal of Central South University of Technology: Natural Science, 2000, 31(3): 260-263. (in Chinese)
[4] Wu Yun-xin, Wang Fu-xing, Chen Yin-qian, CHEN Nan-ping. A Study of the optimization mechanism of solid lubricant concentration in Ni/MoS2 self-lubricating composite[J]. Wear, 1997, 205: 64-70.
[5] LI xi-bin, LIU Ru-tie, GONG Xue-bing. Study of Ni-Cr high temperature solid self-lubricating materials added with Ni coated MoS2 powders[J]. Rare Metal Material and Engineering, 2003, 32(10): 783-786. (in Chinese).
[6] Xiong Dang-sheng, Peng Chao-qun, Huang Qi-zhong. Development of MoS2-containing Ni-Cr based alloys and their high-temperature tribological properties[J]. Trans Nonferrous Met Soc China, 1998, 8(2): 226-229.
[7] WANG Ying, WANG Jing-bo, WANG Jun-an, ZHAO Jia-zheng, OUYANG Jin-lin. Study on the nickel alloy containing sulfide and its tribological properties at high temperature[J]. Tribology, 1996, 16(4): 289-297. (in Chinese).
[8] KAN Cun-yi, LIU Jin-zhu, ZHANG Guo-wei, OUYANG Jin-lin. Preparation and tribological performance of a Ni-Cr-S alloy[J]. Tribology, 1994, 14(3): 193-204. (in Chinese).
[9] Xiong Dang-sheng. Lubrication behavior of Ni-Cr based alloys containing MoS2 at high temperature[J]. Wear, 2001, 250/251: 1094-1099.
[10] LIU Zuo-min. Elevated temperature diffusion self-lubricating mechanisms of a novel cermet sinter with orderly micro-pores[J]. Wear, 2007, 262(5/6): 600-606.
[11] XIONG Dang-sheng, WAN Yi, LIN Jian-ming, ZHU He-guo. Tribological property and high temperature oxidation of Ni-based alloy[J]. Trans Nonferrous Met Soc China, 2005, 15(3): 162-166.
[12] LI Jian-liang, XIONG Dang-sheng, WAN Yi. Effect of counterface material on friction and wear behavior of Ni-Cr-W-Al-Ti-MoS2 composites[J]. Chinese Journal of Aeronautics, 2006, 19: S74-S77.
[13] XUE Mao-quan, HUANG Zhi-de, XIONG Dang-sheng. High-temperature wear mechanism of Ni-based alloy containing MoS2[J]. Transactions of Materials and Heat Treatment, 2007, 28(1): 26-29. (in Chinese)
[14] FONTALVO G A, MITTERER C. The effect of oxide-forming alloying elements on the high temperature wear of a hot work steel[J]. Wear, 2005, 258(10): 1491-1499
[15] KATO H, KOMAI K. Tribofilm formation and mild wear by tribo-sintering of nanometer-sized oxide particles on rubbing steel surfaces[J]. Wear, 2007, 262(1/2): 36-41.
Foundation item: Project(BG2007046) supported by the High Technology Research of Jiangsu Province; Project(06-A-044) supported by the “Six Kinds of Excellent Peak” of Personnel Office of Jiangsu Province; Project(JHB06-04) supported by the College Scientific Research Production Translation of Jiangsu Educational Office
Corresponding author: XIONG Dang-sheng; Tel: +86-25-84315325; E-mail: xiongds@163.com
(Edited by ZHAO Jun)