J. Cent. South Univ. Technol. (2009) 16: 0530-0534
DOI: 10.1007/s11771-009-0088-1

Deformation behavior and microstructural evolution of Al-Zn-Cu-Mg-Sc-Zr alloy during high temperature compression
LI Wen-bin(李文斌)1, 2, PAN Qing-lin(潘清林)1, LIU Jun-sheng(刘俊生)1,
LIANG Wen-jie(梁文杰)1, HE Yun-bin(何运斌)1, LIU Xiao-yan(刘晓艳)1
(1. School of Materials Science and Engineering, Central South University, Changsha 410083, China;
2. Department of Civil Engineering, Hunan City University, Yiyang 413000, China)
Abstract: The deformation behavior of a new Al-Zn-Cu-Mg-Sc-Zr alloy was investigated with compression tests in temperature range of 380-470 ℃ and strain rate range of 0.001-10 s-1 using Gleeble 1500 system, and the associated microstructural evolutions were studied by metallographic microscopy and transmission electron microscopy. The results show that true stress—strain curves exhibit a peak stress, followed by a dynamic flow softening at low strains (ε<0.05). The stress decreases with increasing deformation temperature and decreasing strain rate, which can be represented by a Zener-Hollomon exponential equation with the activation energy for deformation of 157.9 kJ/mol. The substructure in the deformed specimens consists of few fine precipitates with equaixed polygonized subgrains in the elongated grains and developed serrations at the grain boundaries. The dynamic flow softening is attributed mainly to dynamic recovery and dynamic recrystallization.
Key words: Al-Zn-Cu-Mg-Sc-Zr alloy; hot deformation; flow softening; microstructural evolution; activation energy
1 Introduction
Ultra high strength aluminum alloys that combine high strength-to-density ratio with excellent mechanical properties are widely used for aeronautical applications and other fields [1-4]. A desirable formability during conventional forging and extrusion at an elevated temperature is very important for extensive application of such aluminum alloys. The Al-Zn-Cu-Mg-Zr alloy containing Sc is one of the ultra high strength aluminum alloys developed from demands of aeronautical industry [5-6]. Increased strength of the Al-Zn-Cu-Mg-Sc-Zr alloy was anticipated by increasing the quantity of Zn, Cu, Mg and adding transitive elements of Zr and Sc which greatly improve the strength of the alloy [7]. The formability of the Al-Zn-Cu-Mg-Zr alloy containing Sc at high temperature is actually related with its compositions and complicated microstructure evolution. To approach the mechanisms of microstructural control during hot deformation requires knowledge of how these mechanisms respond to dynamic control parameters, including deformation temperature, strain and strain rate. Many reports have revealed in general that the flow stress during hot deformation diminishes with the increase of deformation temperature and the decrease of strain rate, and the flow curves are marked by a peak softening, which decline as deformation temperature rises [8-10]. Dynamic recovery and dynamic recrystallization often occur in aluminum alloy during high temperature deformation [11-13]. In each report, the hot temperature deformation behavior and dynamic softening mechanism are discussed. The present researches have shown that in aluminum alloys the softening mechanism and microstructure evolution during hot temperature deformation are determined by thermomechanical parameters, such as deformation temperature, strain rate and strain degree. However, differences of microstructural evolution in those reported aluminum alloys appear obviously and vary from their compositions [14].
In this work, a new Al-Zn-Cu-Mg-Sc-Zr alloy was developed by adding minor Sc on the basis of Al-Zn-Cu-Mg-Zr alloy. The hot deformation features, including flow stress and associated microstructural evolution, were studied. The constitutive analyses of the alloy and the effects of Sc addition on hot deformation process and microstructural evolution were also investigated.
2 Experimental
The experimental material is a new kind of Al-8.1% Zn-2.3%Cu-2.05%Mg-0.12%Zr(mass fraction) based
alloy with 0.21%Sc addition. The alloy was prepared with pure Al, Mg, Zn and Al-Cu, Al-Sc, Al-Zr master alloys by ingot metallurgy in a crucible furnace and then poured into a copper book-shape mould (260 mm×150 mm×30 mm). The ingot was homogenized at 460 ℃ for 24 h in a furnace and then machined to cylindrical samples with a diameter of 10 mm and a height of 15 mm. The flat ends of the specimen were recessed to a depth of 0.2 mm to entrap the lubricant of graphite mixed with machine oil so that the friction along the interface of specimen and die could be minimized during hot deformation. Hot compression tests were carried out in strain rate range of 0.001-10 s-1 and a deformation temperature range of 380-470 ℃ using computer servo-controlled Gleeble 1500 system. The specimens were electrically heated by its own resistance to deformation temperature at a heating rate of 1 ℃/s by thermocoupled feedback-controlled alternating current and homogenized for 300 s before its total deformation of 0.7 true strain was initiated. As soon as the compression deformation ended, the compressed specimens were quenched into water and then sectioned parallel to the compression axis and prepared by conventional methods for microstructural observations on metallographic microscope (OM) and Tecnai G220 transmission electron microscope (TEM).
3 Results and discussion
3.1 Flow stress behavior
Typical true stress—strain curves obtained during hot compression are shown in Fig.1. It can be seen that all the curves exhibit a peak stress, followed by dynamic softening at low strain (εp<0.05). The peak stress increases with increasing strain rate and decreasing deformation temperature. Flow softening is a common characteristic of the true stress—true strain curves for many alloys deformed at elevated temperatures. The softening can be caused by deformation heating and also by microstructural instabilities inside the material, such as dynamic recrystallization, texture formation, dynamic precipitation and dissolution. In the present case, the flow softening appears more pronounced at low strain rates, which indicate that microstructural instability plays an important role in the process of softening. In the simulation of hot deformation, several constitutive
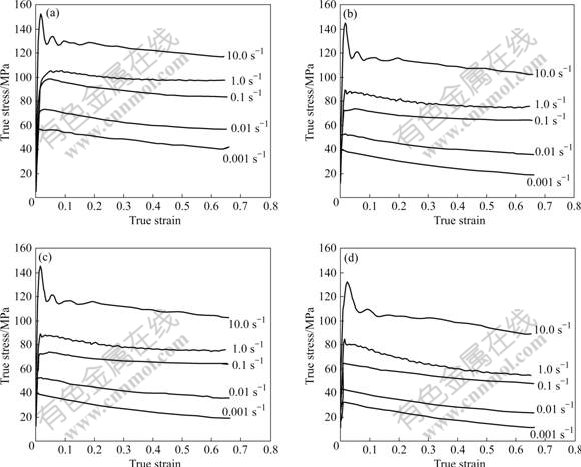
Fig.1 True stress—strain curves of studied alloy during hot compression deformation at different temperatures: (a) 380 ℃; (b) 410 ℃; (c) 440 ℃; (d) 470 ℃
equations have commonly been applied [8–9]:
(1)
(2)
(3)
(4)
where A, A1, A2, n1, n, α and β (=αn) are constants, Q is the activation energy for deformation, R is the gas constant, and Z is the Zener-Hollomon parameter. Eqn.(1) is often used at a low stress, and the exponential Eqn.(2) is usually adopted at a high stress. The hyperbolic sine Eqn.(3) is a more general form suitable for stresses over a wide range.
As shown in Fig.2, these peak stresses obtained from the above true stress—strain curves can be approximated by a group of parallel and straight lines in hot deformation conditions, demonstrating that the peak stress of the studied alloy can be represented by a Zener- Hollomon parameter in an exponent-type equation. The hot deformation activation energy derived from Fig.2(b) is 157.9 kJ/mol for the studied alloy, which is lower than that of solution-treated 7050 aluminum alloy (200- 230 kJ/mol), but is close to that of the precipitated and over aged 7012 aluminum alloy (141-162 kJ/mol) [15].
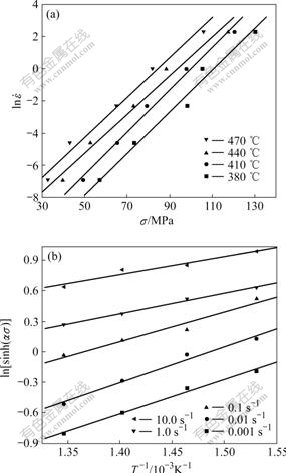
Fig.2 Relationship between peak stress and strain rate (a), and hyperbolic sine of peak stress and deformation temperature (b)
3.2 Microstructural evolution
Optical microstructures of the deformed specimens under different conditions are shown in Fig.3. Elongated grains and subgrains can be observed (Figs.3(a)-(c)), indicating that even at high deformation temperature the dynamic recovery occurs and prevails at a lower strain rate (Fig.1,
<1 s-1). The dynamic recovery is the main mechanism of flow softening at a strain rate less than 1 s-1. The grain size is dependent sensitively on deformation temperature and/or strain rate, also on the value of the Zener-Hollomon parameter Z. The size of the grains decreases with the increase of strain rate and the decrease of hot deformation temperature. The serrations at some elongated boundaries and the waves of flow stress in true stress—true strain curves can be distinguished at higher strain rate (
≥1 s-1), which indicates that the dynamic recrystallization occurs during hot compression deformation. The high strain rate results in high stored strain energy that is enough to induce dynamic recrystallization. Transmission electron micrographs (Figs.4(b)-(d)) show that the substructures with high density dislocations and dislocation walls interact with Al3(Sc, Zr) particles and grain boundaries, which constitute the main mechanisms of flow softening. The mechanism of dynamic recrystallization nucleation is related with some subgrains that swell through merging other adjacent subgrains and then become the recrystallized grains (Fig.3(d) and Fig.4(c)). Such microstructures indicate that the main type of dynamic recrystallization is continuous dynamic recrystallization. On the other hand, the geometric dynamic recrystallization also occurs during hot temperature deformation, which results in some serrations at grain boundaries. The solutes and a uniform dispersion of fine particles interacting with dislocations reduce dynamic recovery, which increase the stored strain energy and accelerate the process of dynamic recrystallization during hot deformation. Such dynamic recrystallization process leads to grain refinement [16-17].
The TEM observations show that very small amount of dynamic precipitate and Al3(Sc, Zr) particles appear in the grain and at the subgrain boundaries. The strong interaction between dislocations and small Al3(Sc, Zr) particles the main characteristic of the microstructure (Figs.4(a), (b) and (d)). The hot deformation activation energy Q plays a great role in the above interaction, which means that a careful consideration and selection of technological parameters is very important to hot working of the studied alloy.
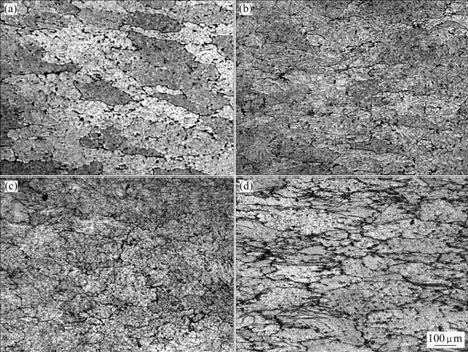
Fig.3 Optical microstructures of studied alloy under different conditions: (a) t=410 ℃,
=0.001 s-1; (b) t=410 ℃,
=10 s-1; (c) t= 410 ℃,
=1 s-1; (d) t=440 ℃,
=10 s-1
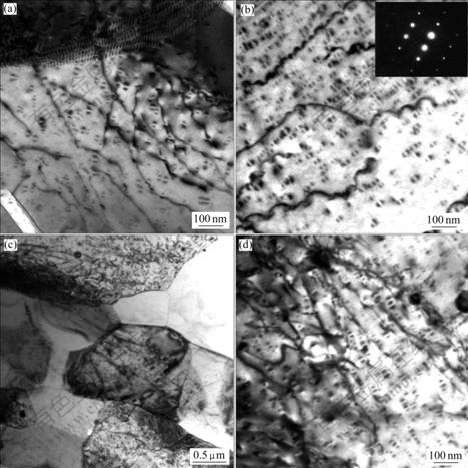
Fig.4 TEM images of studied alloy under different conditions: (a) 410 ℃, 0.1 s-1, dislocations and dislocation walls; (b) 470 ℃, 0.1 s-1, interaction of dislocations and Al3(Sc, Zr) particles, superlattice spots of Al3(Sc, Zr); (c) 410 ℃, 10 s-1, recrystallized grain and subgrain; (d) 410 ℃, 10 s-1, interaction of dislocations and Al3(Sc, Zr) particles
4 Conclusions
(1) The true stress—strain curves exhibit a peak stress at low strain (ε<0.05), after which the flow stresses decrease monotonically until high strains, showing a dynamic flow softening. The stress decreases with increasing deformation temperature and decreasing strain rate, which can be represented by an exponential equation with a Zener-Hollomon parameter and a activation energy for deformation of 157.9 kJ/mol.
(2) When the strain rates are low (
<1 s-1), the dynamic recovery is the main mechanism of flow softening even at high deformation temperature. At high strain rate (
≥1 s-1), the dynamic recrystallization is the main mechanism of flow softening even at lower deformation temperature.
(3) The substructure in the deformed specimens consists of few fine precipitates. Equaixed polygonized subgrains in the elongated grains and serrations can be easily observed at the grain boundaries.
References
[1] DESCHAMPS A, BRECHET Y. Influence of quench and heating rates on the ageing response of an Al-Zn-Mg-(Zr) alloy [J]. Materials Science and Engineering A, 1998, 251(1): 200-207.
[2] STILLER K, WARREN P J, HANSEN V, ANGENETE J, GJONNES J. Investigation of precipitation in an Al-Zn-Mg alloy after two-step ageing treatment at 100 ℃ and 150 ℃ [J]. Materials Science and Engineering A, 1999, 270(1): 55-63.
[3] JAMES C, WILLIAMS J C, STARKE E A. Progress in structural materials for aerospace systems [J]. Acta Materiala, 2003, 51(19): 5775-5799.
[4] SHA G, CEREZO A. Characterisation of precipitates in an aged 7××× series alloy [J]. Surface and Interface Analysis, 2004, 36(5/6): 564-568.
[5] ZHANG Zhuo, CHEN Kang-hua, FANG Hua-chan, QI Xiong-wei, LIU Gang. Effect of Yb addition on strength and fracture toughness of Al-Zn-Mg-Cu-Zr aluminum alloy [J]. Transactions of Nonferrous Metals Society of China, 2008, 18(5): 1037-1042.
[6] KAIBYSHEW R, SITDIKOV O, GOLOBORODKO A, SAKAI T. Grain refinement in as-cast 7475 aluminum alloy under hot deformation [J]. Materials Science and Engineering A, 2003, 344(1/2): 348-356.
[7] HE Yong-dong, ZHANG Xin-ming, YOU Jiang-hai. Effect of minor Sc and Zr on microstructure and mechanical properties of Al-Zn-Mg-Cu alloy [J]. Transactions of Nonferrous Metals Society of China, 2006, 16(5): 1228-1235.
[8] SPIGARELLI S, EVANGELISTA E, MCQUEEN H J. Study of hot workability of a heat treated AA6082 aluminum alloy [J]. Scripta Materialia, 2003, 49(2): 179-183.
[9] ZHANG H, LI L X, YUAN D. Hot deformation behavior of the new Al-Mg-Si-Cu aluminum alloy during compression at elevated temperatures [J]. Materials Characterization, 2007, 58(2): 168-173.
[10] Van der LANGKRUIS J, KOOL W H, Van der ZWAAG S. Assessment of constitutive equation in modeling the hot deformability of some overaged Al-Mg-Si alloys with varying solute contents [J]. Materials Science and Engineering A, 1999, 266(1): 135-145.
[11] GEERTRUYDEN W V, MISIOLEK W Z, WANG P T. Grain structure evolution in a 6061 aluminum alloy during hot torsion [J]. Materials Science and Engineering A, 2006, 419(1/2): 105-114.
[12] SU J Q, NELSON T W, STERLING C J. Microstructure evolution during FSW/FSP of high strength aluminum alloys [J]. Materials Science and Engineering A, 2005, 405(1/2): 277-286.
[13] GOURDET S, MONTHEILLET F. An experimental study of the recrystallization mechanism during hot deformation of aluminum [J]. Materials Science and Engineering A, 2000, 283(1/2): 274-288.
[14] REN B, MORRIS J G. Microstructure and texture evolution of Al during hot and cold rolling [J]. Metallurgical and Materials Transactions, 1995, 26(1): 31-40.
[15] HU H E, ZHEN L, YANG L, SHAO W Z, ZHANG B Y. Deformation behavior and microstructure evolution of 7050 aluminum alloy during high temperature deformation [J]. Materials Science and Engineering A, 2008, 488(1/2): 64-71.
[16] IHARA K, MIURA Y. Dynamic recrystallization in Al-Mg-Sc alloys [J]. Materials Science and Engineering A, 2004, 387/389: 647-650.
[17] CHA J R, BAE W B, HWANG W J, HARTLEY P. A study on the hot-deformation behavior and dynamic recrystallization of Al-5wt.% Mg alloy [J]. Journal of Materials Processing Technology, 2001, 118(1/3): 356-361.
(Edited by YANG You-ping)
Foundation item: Project(2006AA03Z523) supported by the National High-Tech Research and Development Program of China
Received date: 2008-08-27; Accepted date: 2008-12-30
Corresponding author: PAN Qing-lin, Professor, PhD; Tel: +86-731-88830933; E-mail: pql@mail.csu.edu.cn