DOI: 10.11817/j.ysxb.1004.0609.2021-35965
限制模压变形和超声喷丸复合工艺对AZ31镁合金表层组织及硬度的影响
黄庆国1,朱立华1,王宗申1,管延锦2,陈 浩1,于从潇1
(1. 山东理工大学 机械工程学院,淄博 255000;
2. 山东大学 材料科学与工程学院,济南 250061)
摘 要:以AZ31镁合金板材为实验材料,先对其进行限制模压变形,再利用超声喷丸技术进行表面处理,研究限制模压变形和超声喷丸复合工艺对材料表层组织和硬度的影响。结果表明:限制模压变形和超声喷丸具有叠加效果,该复合工艺相对于单一工艺能进一步减小AZ31镁合金的晶粒尺寸,增强表面硬度。经复合工艺处理后,AZ31镁合金的最小平均晶粒尺寸为7.52 μm,相比于原始试样细化43.16%;表面硬度最高达到236 HV,相比于原始试样提高306.90%。此外,与限制模压变形相比,超声喷丸对AZ31镁合金表层组织和硬度的影响更加明显。其中,随着喷丸时间的增加,晶粒逐渐细化,硬度不断升高,但当处理时间达到400 s时,晶粒尺寸不再有明显减小,硬度达到一定极限不再变化。
关键词:AZ31镁合金;限制模压变形;超声喷丸;晶粒细化;硬度提高
文章编号:1004-0609(2021)-03-0623-16 中图分类号:TG316 文献标志码:A
引文格式:黄庆国, 朱立华, 王宗申, 等. 限制模压变形和超声喷丸复合工艺对AZ31镁合金表层组织及硬度的影响[J]. 中国有色金属学报, 2021, 31(3): 623-638. DOI: 10.11817/j.ysxb.1004.0609.2021-35965
HUANG Qing-guo, ZHU Li-hua, WANG Zong-shen, et al. Effects of constrained groove pressing and ultrasonic shot peening on surface microstructure and hardness of AZ31 magnesium alloy[J]. The Chinese Journal of Nonferrous Metals, 2021, 31(3): 623-638. DOI: 10.11817/j.ysxb.1004.0609.2021-35965
镁合金是目前最轻质的金属结构材料,其密度仅为1.8 g/cm3,并且具有优异的散热性和减震性能,在航空、航天、交通运输和电子等行业都有广泛的应用,被誉为“21世纪的绿色工程材料”[1]。然而,镁合金仍存在室温塑性变形能力差、绝对强度偏低、耐腐蚀性差等问题,制约了镁合金的应用范围[2-3]。因此,研究镁合金性能强化技术,对于推动镁合金更广泛的工程应用具有重要意义。
限制模压变形(Constrained groove pressing, CGP)是由SHIN等[4]提出的、适用于制备超细晶金属板材的一种剧烈塑性变形技术,即在加工过程中使用对试样两端有限制作用的模具,对试样上下进行压弯、压直使其产生剧烈塑性变形,从而达到细化晶粒的目的。CGP工艺原理图如图1所示,齿宽(T)和倾斜角(θ)是所述模具结构的主要参数(见图1(a))。在整个变形过程中,样品周围总是受限于模具的侧壁。样品厚度与模具闭合间隙一致,使得试样受纯剪切变形,保证变形区域的均匀性。如图1(b)所示,此时,板材只有一半的区域受到了挤压,但由于压弯模具的齿廓不对称,当样品绕其法线旋转180°后,其未变形区域将经历相同的变形,因此,塑性变形就能够在整个试样中得到均匀积累。如图1(d)~(f)所示,将图1所示的四次压制的过程称为一个变形道次。如果经历多个道次变形,可在材料的内部累积大量塑性应变,使晶粒得到细化,在不改变试样的形状以及尺寸的情况下,获得均匀超细晶组织[5-6]。
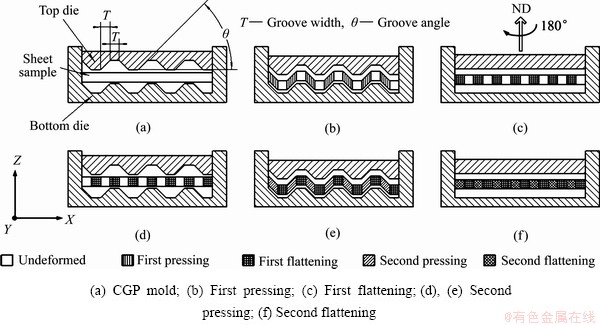
图1 CGP工艺原理图[7]
Fig. 1 Schematic illustration of CGP process[7]
CGP技术提出后,LEE等[8]研制出了限制模压轧制法,杨开怀等[9]探究了不同的限制模压方式下1060纯铝的模压效果,彭开萍等[10]研究了限制模压变形工艺对材料内部微观组织和力学性能的影响。SAJADI等[11]研究了模具倾角对纯铝CGP过程的影响规律、BORHANI等[12]用橡胶垫代替刚性上模,开发了橡胶垫限制模压变形(Rubber pad-constrained groove pressing, RP-CGP)。此外,范仁杰等[13]对AA6063铝合金进行CGP处理发现,随着变形道次的增加,在CGP第一道次中形成的细长晶粒会逐渐转变为等轴晶粒。尽管国内外有不少学者对其进行研究,但技术工艺还不太成熟,仍需进行进一步研究。
超声喷丸技术(Ultrasonic shot peening, USP)是将超声振动作为能量源,驱动钢球高速撞击金属材料表面,从而实现材料表面改性或变形的一种剧烈塑性变形技术[14]。其工作原理图如图2所示,工具头输出的超声振幅可达10~100 μm。以一定频率和振幅振动的工具头直接作用在喷丸室里的钢球上,驱动钢球以一定速度撞击上方的试样。撞击结束后,钢球会由于反弹和重力作用重新回落到工具头上,再次被工具头驱动撞击试样,经过多次反复的高速撞击[15],会形成排列不规则的微晶,而这一过程会伴随着纳米层的形成。在钢球反复高速冲击试样表面时,随着喷丸时间的增加,受喷表面会逐渐产生纳米层,在材料表面产生厚度可达几十微米的纳米层[16]。与传统喷丸相比,超声喷丸采用多向离散的低速冲击方式,喷丸的冲击能量更小,因而具有更加均匀的表面形貌和较低的表面粗糙度[17]。正是由于超声喷丸克服了传统喷丸导致的材料表面较粗糙缺陷,且操作方便,无污染,已广泛地应用于航空航天、汽车制造和国防工业领域,实现复杂工件的性能强化和喷丸校形。如空客公司采用超声喷丸对焊接机身壁板实现了喷丸校形[18]。
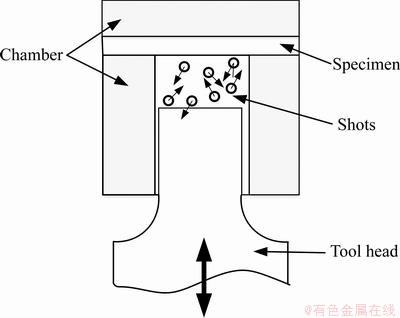
图2 超声喷丸工作原理图
Fig. 2 Working principle of USP
法国CHARDIN等[19]最先进行超声喷丸的实 验研究。随后,俄国ABRAMOV等[20]、法国COCHENNEC等[21]和PILE等[22]、中国科学院刘刚等[23]和冯淦等[24]都对USP技术进行了相关实验研究,提高了实验材料的性能,达到了预定实验目的。
CGP和USP都是对金属进行晶粒细化的方法。但是,依据现有的文献,大多数学者都只是单独研究CGP或USP对材料组织和性能的影响,尚未有研究CGP和USP复合工艺对金属组织性能的影响,而且过去CGP和USP的研究对象多为室温下塑性较好的体心立方或面心立方晶体结构金属,对于密排六方金属研究较少。因此,本文以AZ31镁合金板材为实验材料,先后采用CGP与USP对其进行处理,探究CGP和USP复合工艺对AZ31镁合金表层组织和硬度的影响规律。
1 实验
1.1 试样制备
试样材料为商用AZ31镁合金轧制板材,厚度为2 mm。模压前先将AZ31镁合金板材在300 ℃下进行1 h均匀化退火处理,并消除残余内应力。模压实验在YAW-5000F型微机控制电液伺服压力试验机上进行,模压速度为5 mm/min。将AZ31镁合金试样切割成大小均为25 mm×25 mm×2 mm的36块小板,任取其中12块,即为未模压变形试样,标记为A组;另取12块进行200 ℃模压变形1道次,标记为B组;取剩下的12块AZ31镁合金板进行200 ℃模压变形2道次,标记为C组。
对每组CGP处理后的试样都进行USP处理,所用超声喷丸实验装置如图3所示。该实验装置包括超声施振部分和超声处理两大部分。超声施振部分主要由超声发生器、换能器、变幅杆和工具头组成。喷丸处理部分主要包括工具头、喷丸室及喷丸室固定板、钢球、试样及试样固定装置[25]。喷丸工艺过程中,超声喷丸实验装置能产生20 kHz的振动频率,工作振幅有32 μm和40 μm两种,喷丸室的直径为21 mm,高度为40 mm。钢球为45~55 HRC的铸钢丸,喷丸处理时间可以从0调整到999 s。具体的超声喷丸实验参数见表1。
1.2 金相试样的制备与观察
为了研究超声喷丸处理引起的由表及里的微观组织变化,需要从横截面观察喷丸表面到心部的组织变化情况。对每组试样进行金相试样制备,截取试样的四分之一进行镶嵌,如图4(b)所示。采用浇注镶嵌法,将试样放入直径约为20 mm的圆形塑胶软模中,浇入环氧树脂混合液(90 g环氧树脂+10 g乙二胺),静置,待液体凝固至透明后取出,如图4(c)所示。再选取砂纸粒度由粗到细,依次为240#、400#、800#、1200#、2000#、3000#进行研磨。研磨完成后按1 mL硝酸、1 mL冰乙酸和150 mL水的比例混合配置腐蚀剂,将试样腐蚀5~10 s,立即取出并用酒精冲洗,吹干,在显微镜下观察从喷丸表面到心部的金相组织。
1.3 硬度测量
选用DHV-1000型数显显微表面硬度测量仪,实验力为4.9 N,保压时间为10 s,共计36种不同的试样。
考虑到超声喷丸产生的粗糙表面会使硬度测量产生较大的误差,因此对每一组试样的细晶层横截面进行了硬度测量,以A组6#试样为例,测量路径如下图5(a)所示。以超声喷丸表面为基线,垂直基线沿试样中心区域,每隔20 μm选取一个测量点,在与每个测量点距喷丸表面相同距离的位置进行三次测量,取其算术平均值作为此测量点的硬度值。得到硬度随距喷丸表面距离的变化如图5(b)所示,从图中可以清晰看出,硬度随距喷丸表面距离的增加而下降。因此,选用横截面上最贴近强化表面的测量结果作为本文中讨论的表面硬度值。
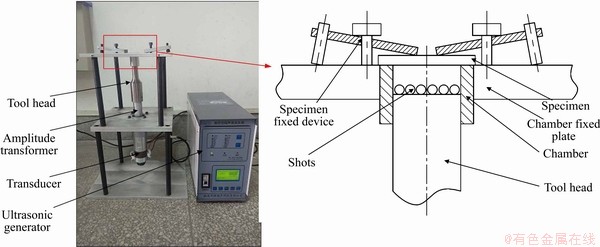
图3 超声喷丸实验装置[25]
Fig. 3 Experimental equipment of USP[25]
表1 超声喷丸实验参数
Table 1 Experimental parameters of USP
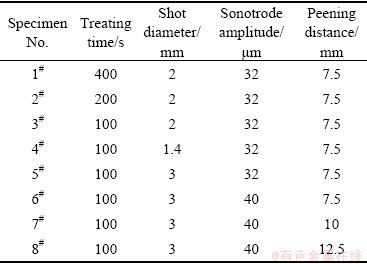
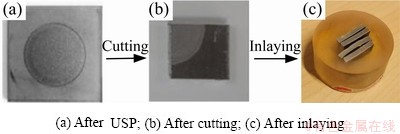
图4 金相试样的制备
Fig. 4 Preparation of metallographic specimen
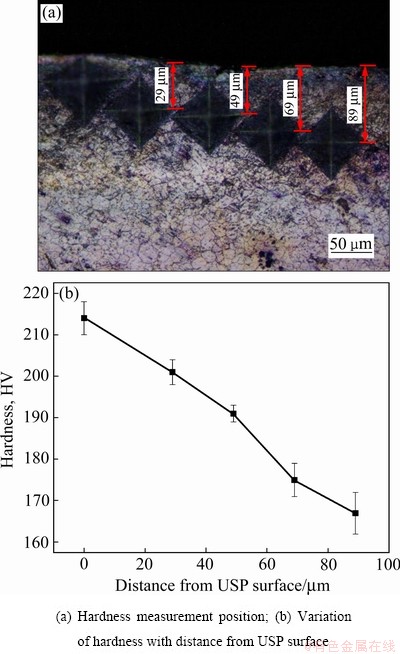
图5 A组6#试样的硬度测量位置和硬度随距喷丸表面的距离变化图
Fig. 5 Hardness measurement position of group A 6# samples and variation of hardness with distance from USP surface
2 结果与讨论
2.1 CGP对AZ31镁合金显微组织和硬度的影响
从A、B、C三组试样中每组各任取一块板材,三件试样均未经过喷丸处理,只在300 ℃退火状态下进行不同道次的CGP处理,从而可探究CGP对AZ31镁合金的影响。
观察每组试样的金相显微组织,如图6所示。由图6(a)、(b)和(c)可见,在不进行USP处理的情况下,用截线法估测,A组未经过CGP处理的试样平均晶粒尺寸约为13.23 μm,B组经过200 ℃ 1道次CGP处理的试样平均晶粒尺寸约为10.78 μm,C组经过200 ℃ 2道次CGP处理的试样平均晶粒尺寸约为10.23 μm,平均晶粒尺寸最大降低了22.68%。随着变形道次的增加,模具对试样产生的塑性应变量逐渐积累,导致材料塑性变形程度增大,试样平均晶粒尺寸减小。
对A、B和C三组试样进行硬度测试,测得结果如图7所示,A组变形道次为0时,即未进行CGP处理,此时试样硬度为58 HV;当进行200 ℃ 2道次CGP处理时,试样硬度上升为64 HV;C组经过200 ℃ 2道次CGP处理的试样硬度最高,为70 HV,与喷丸前的硬度相比提高了20.69%。
根据霍尔-佩奇(Hall-Petch)公式
(1)
式中:
代表材料的屈服极限;
表示位错在滑移面上滑移时的摩擦应力;k为应力集中系数,与材料种类性质以及晶粒尺寸有关;d为平均晶粒尺寸[26]。由此可知,当材料的平均晶粒尺寸越小时,材料的屈服极限越大,从而硬度也越高。CGP变形道次的增加,使试样的晶粒尺寸逐渐减小,因而硬度不断提高。
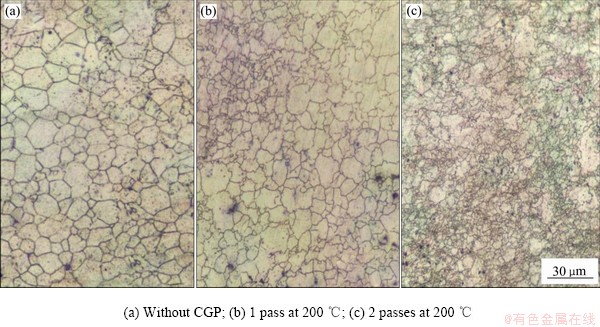
图6 A、B和C组未喷丸试样的显微组织
Fig. 6 Microstructures of A, B and C samples without USP
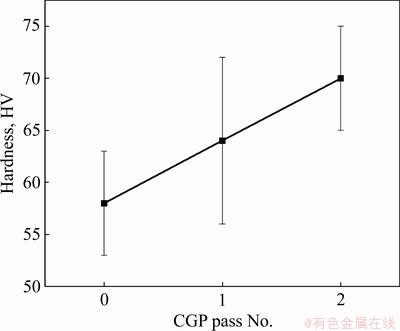
图7 CGP对AZ31镁合金硬度的影响
Fig. 7 Effect of CGP on hardness of AZ31 magnesium alloy
2.2 USP对AZ31镁合金显微组织和硬度的影响
2.2.1 处理时间对AZ31镁合金显微组织和硬度的影响
从A组剩余11件试样中任选三件,进行不同处理时间的USP处理。实验参数如表1中序号3#、2#和1#,其他喷丸参数均相同,只有处理时间不同,分别为100、200和400 s。
如图8(a)所示,经过100 s喷丸处理的试样晶粒相对粗大,截线法测得平均晶粒尺寸约为9.86 μm;如图8(b)所示,当200 s喷丸处理后,试样平均晶粒尺寸约为8.90 μm;从图8(c)中可见,喷丸处理400 s后的试样晶粒最为细小且相对均匀,平均晶粒尺寸减小至8.44 μm,与A组喷丸前的晶粒尺寸相比,晶粒最大细化了36.2%。试样经过不同喷丸时间处理后,晶粒组织出现了一定程度的不均匀性,但随着喷丸处理时间越长,钢球撞击试样的次数越多,钢球撞击试样表面各区域的概率相差不大,因此这种晶粒不均匀性越来越不明显。另外,钢球经过更长时间的撞击,在试样表面积累的动能越多,使试样表面产生更大程度的塑性变形,从而实现晶粒逐渐细化,但随着处理时间的增加,晶粒细化的速度会逐渐减慢。
如图9所示,测得经过USP处理100、200和400 s后的试样硬度分别为163 HV、169 HV和170 HV,喷丸之前的试样硬度为58 HV,USP处理后试样硬度最大提高了181.03%。从喷丸处理0 s到100 s,晶粒组织出现了较大的不均匀性,但正是这种组织的不均匀性,使得晶粒组织出现了局部细化,硬度提高比较明显。当喷丸时间进一步增加时,晶粒组织越发趋于均匀,这种晶粒的不均匀性表现得越不明显,晶粒尺寸变化不大,故试样硬度提升速度下降,硬度变化相对平缓。
2.2.2 钢球直径对AZ31镁合金显微组织和硬度的影响
从A组剩余8件试样中任选三件,进行不同钢球直径的USP处理。实验参数如表1中序号4#、3#和5#,其他喷丸参数均相同,只有钢球直径不同,分别为1.4、2和3 mm。
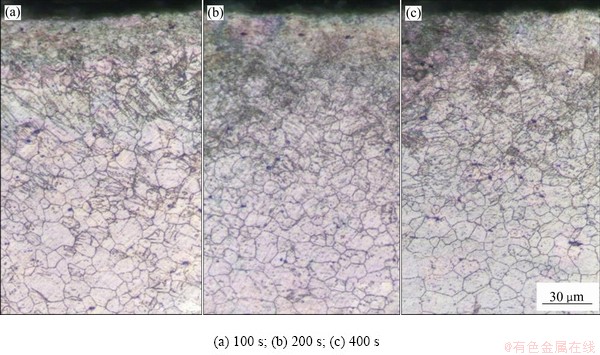
图8 USP处理时间对AZ31镁合金显微组织的影响
Fig. 8 Effect of USP treating time on microstructure of AZ31 magnesium alloy
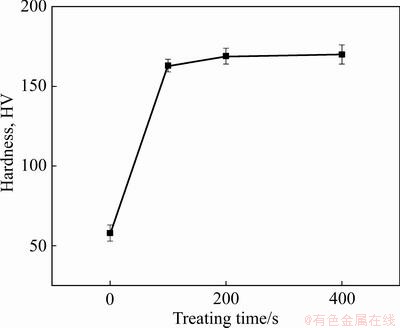
图9 USP处理时间对AZ31镁合金硬度的影响
Fig. 9 Effect of USP treating time on hardness of AZ31 magnesium alloy
如图10所示,随着钢球直径的提升,AZ31镁合金出现了明显的晶粒细化,在钢球直径为2 mm时,出现了孪晶组织。与用直径为1.4 mm和2 mm的钢球喷丸处理的试样相比,钢球直径为3 mm喷丸的试样表面晶粒细化最为明显,组织也更加均匀,平均晶粒尺寸达到8.16 μm,与喷丸前的晶粒尺寸相比,晶粒细化了38.32%。
试样硬度随钢球直径变化的曲线如图11所示,大致呈线性关系,使用直径为1.4 mm的钢球喷丸后,硬度迅速提高到148 HV;换成直径为2 mm的钢球喷丸后,试样硬度上升至163 HV;继续增加钢球直径至3 mm,喷丸处理后,试样硬度达到198 HV,与未喷丸的试样硬度相比提高241.38%。由于钢球质量与工具头相比非常小,因此钢球直径的增加对钢球撞击速度影响不大,但是钢球直径越大,钢球的质量也越大,因此其携带的动能也就越大,最终产生塑性变形越剧烈,故晶粒细化程度也会越大,表面硬度会进一步提高。
2.2.3 工作振幅对AZ31镁合金显微组织和硬度的影响
从A组剩余5件试样中任选两件,进行不同工作振幅的USP处理。实验参数如表1中序号5#和6#,其他喷丸参数均相同,只有工作振幅不同,分别为32 μm和40 μm。
不同的工作振幅,对试样的晶粒细化程度不同,图12给出了工作振幅分别为32 μm和40 μm的USP处理下的试样金相显微组织图。从图12(b)可观察到喷丸处理的表层晶粒出现了孪晶组织,晶粒细小,而心部中心组织晶粒相对粗大,晶粒由表层向心部晶粒尺寸逐渐变大。试样在振幅为32 μm的喷丸处理下,晶粒平均尺寸约为8.16 μm,而当工作振幅调至40 μm时,晶粒平均尺寸更小,减小至8.00 μm,比喷丸前的晶粒平均尺寸减小了39.53%。当工作振幅增大时,工具头的振动平均速度增大,钢球跟随工具头以更大的速度来回振动,钢球的动能随之增大,撞击试样表面产生更大的塑性变形,进而使受钢球撞击的晶粒影响层和表面晶粒细化层变厚,实现表层晶粒逐渐细化,而试样心部组织受喷丸影响较小,晶粒较之表层更加粗大。
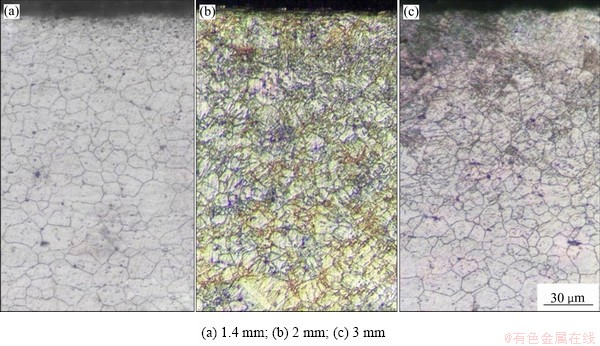
图10 USP钢球直径对AZ31镁合金显微组织的影响
Fig. 10 Effect of USP shot diameter on microstructure of AZ31 magnesium alloy
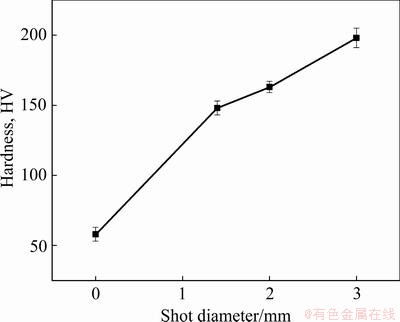
图11 USP钢球直径对AZ31镁合金硬度的影响
Fig. 11 Effect of USP shot diameter on hardness of AZ31 magnesium alloy
图13反映了试样硬度随工作振幅变化的关系,工作振幅为0时即为未喷丸试样的硬度。在工作振幅为32 μm下,硬度提高到198 HV,继续将工作振幅增大到40 μm,试样硬度增加了16 HV,相对于喷丸前试样的硬度提高了268.97%。
2.2.4 工作距离对AZ31镁合金显微组织和硬度的影响
将A组最后三块试样进行不同工作距离的USP处理。实验参数如表1中序号6#、7#和8#,其他喷丸参数均相同,只有工作距离不同,分别为7.5、10和12.5 mm。
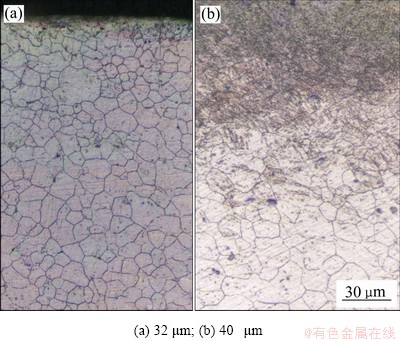
图12 USP工作振幅对AZ31镁合金显微组织的影响
Fig. 12 Effect of USP sonotrode amplitude on microstructure of AZ31 magnesium alloy
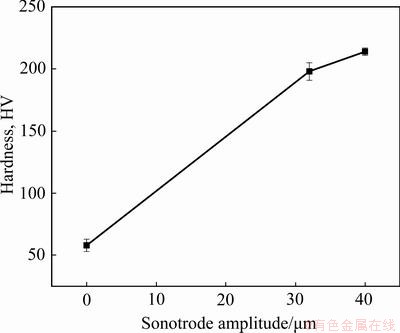
图13 USP工作振幅对AZ31镁合金硬度的影响
Fig. 13 Effect of USP sonotrode amplitude on hardness of AZ31 magnesium alloy
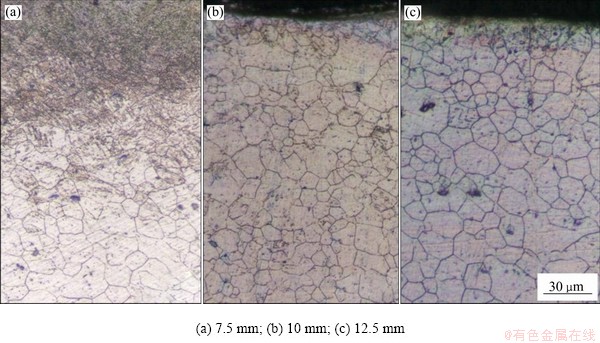
图14 USP工作距离对AZ31镁合金显微组织的影响
Fig. 14 Effect of USP peening distance on microstructure of AZ31 magnesium alloy
如图14所示,图14(a)中的晶粒相比于图14(b)、(c)中的晶粒更加细小;图14(a)中试样的平均晶粒尺寸约为8.00 μm,晶粒减小了39.53%,而图14(c)中晶粒更加粗大,约为10.78 μm,只减小18.52%。由此可见,随着工作距离的增加,晶粒细化的程度会越来越小。这是因为,一方面,整个喷丸撞击试样的过程,重力对喷丸做负功,阻碍喷丸的上升运动,随着工作距离的增加,喷丸钢球到达工件表面时,动能越来越小。另一方面,喷丸距离增加使钢球运动的方向有了更多的可能性,与钢球之间以及钢球与喷丸室之间的碰撞会增加,导致钢球动能损耗增加。故随着工作距离的增加,其显微组织的晶粒细化越来越不明显。
如图15所示,在工作距离为7.5 mm时,硬度提高至214 HV,比未喷丸的试样硬度提高了268.97%;在工作距离为10 mm时,硬度为179 HV;而当工作距离为12.5 mm时,硬度为167 HV,仅提高187.93%。随着工作距离的增加,喷丸对试样表面的冲击力不断减小,晶粒尺寸不断增大,故硬度降低。
2.3 CGP和USP的复合工艺对AZ31镁合金显微组织和硬度的影响
2.3.1 USP处理时间对已CGP处理的AZ31镁合金显微组织和硬度的影响
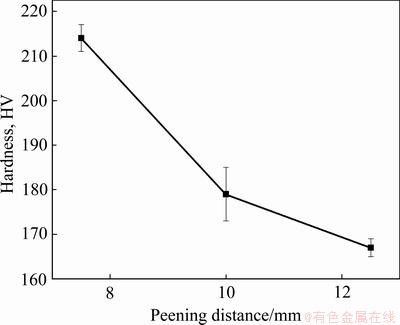
图15 USP工作距离对AZ31镁合金硬度的影响
Fig. 15 Effect of USP peening distance on hardness of AZ31 magnesium alloy
分别从B、C组剩余试样中各任选三件试样,进行不同喷丸处理时间的USP处理。具体实验参数如表1中序号3#、2#和1#,其他喷丸参数均相同,只有处理时间不同,分别为100、200和400 s。由于B、C组的试样都已进行了不同道次的CGP处理,故可研究USP处理时间对已CGP处理的AZ31镁合金的影响。
如图8、16、17所示,A、B、C三组试样经过100 s喷丸处理,晶粒均出现细化,但是晶粒当中仍还存在较大的晶粒,表现出一定的不均匀性;但经过200 s喷丸处理后,大的晶粒得到进一步细化,晶粒明显更加均匀,此时总体上呈现出细晶与少部分较大晶粒共存的状态;经过400 s喷丸处理后,A组和B组晶粒变化不大,而C组晶粒变得更加细小均匀,晶粒大小几乎一致,表现出均匀性,平均晶粒尺寸达到8.16 μm,与A组未喷丸的试样相比晶粒细化了38.32%。将经过相同喷丸时间处理的A、B、C三组试样的显微组织进行纵向对比,可看出A组的晶粒比B、C组的粗大,且B、C组的晶粒明显比A组的均匀,说明试样先经过CGP再进行USP处理,比试样直接进行USP处理,得到的晶粒尺寸更加细小,分布情况更加均匀。
A、B、C三组试样未喷丸前的硬度分别为58 HV、64 HV、70 HV。如图18所示,喷丸处理时间经过100 s后,三种材料表面硬度迅速提高,而当处理时间增加至200 s时,试样硬度进一步提高,但变化相对平缓。这是因为超声喷丸中镁合金表面会受到钢球多次高频高速的撞击,每一次钢球的撞击都会使镁合金表面产生局部的剧烈塑性变形,这些剧烈塑性变形不断叠加,使镁合金表层晶粒进一步细化。其中,影响晶粒细化程度最关键的因素是钢球的撞击速度和撞击次数。一方面喷丸时间的增加对喷丸速度的影响不大,但是喷丸时间的增加会大幅度地增加钢球的撞击次数,从而使变形量不断增加,提高晶粒细化程度。另一方面,随着晶粒细化程度的增加,硬度不断提高,使进一步的塑性变形越来越难以发生。因此,超声喷丸前100 s的细化晶粒效率和表面硬化效率是最高的。当喷丸时间为100 s时,A、B、C三组试样的表面晶粒尺寸已经分别达到了9.86 μm、8.39 μm、8.22 μm,此时硬度也已经达到163 HV、172 HV、183 HV;再增加同样的100 s喷丸处理,所获得的晶粒细化效果和表面硬化效果不再像前100 s那样明显。
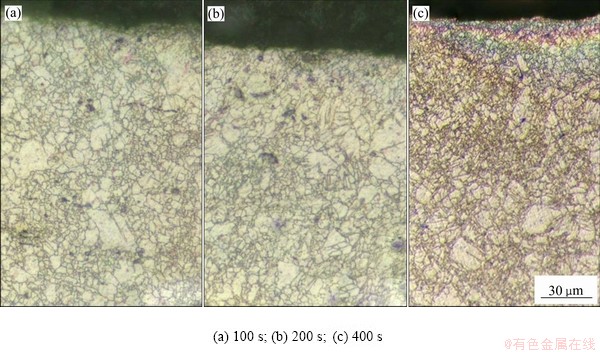
图16 B组不同USP处理时间处理的AZ31镁合金显微组织
Fig. 16 Microstructures of AZ31 magnesium alloys treated with different USP treating time in group B
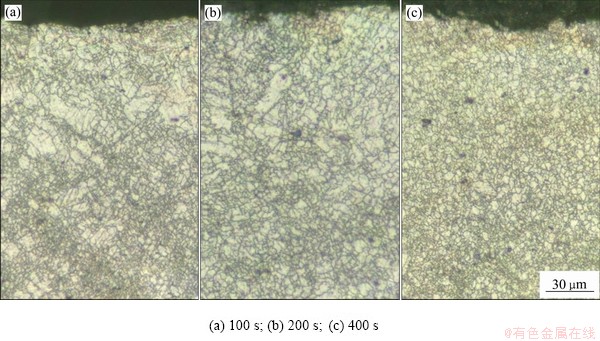
图17 C组不同USP处理时间处理的AZ31镁合金显微组织
Fig. 17 Microstructures of AZ31 magnesium alloys treated with different USP treating time in group C
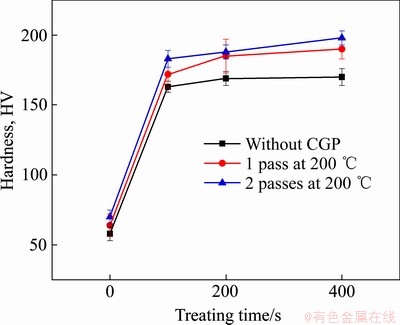
图18 不同USP处理时间处理的AZ31镁合金的硬度
Fig. 18 Hardness of AZ31 magnesium alloys treated with different USP treating time
当喷丸时间继续增加至400 s时,各组硬度均达到最高,A组未模压变形试样的硬度为170 HV,提高了193.10%;B组200 ℃1道次试样硬度为190 HV,提高了227.58%;而C组200 ℃ 2道次硬度达到198 HV,硬度提高最大,提高了241.38%。结合图像和数据分析可知,经过CGP处理试样的曲线所在位置,在未经CGP处理试样曲线的上方,且随着变形道次的增加,所处的位置越高;但随着变形道次的增加,硬度提高的程度有所减小。经过第1次CGP处理的表面硬度增量明显比经过第2次CGP处理的表面硬度增量大,即CGP工艺对于材料的硬度大幅度提高只在变形初期较为显著,这与SHIEDEDL等[27-28]的研究结果相吻合。其机理可用位错理论来解释。位错的增殖与应变速率之间的关系可用Orowan公式描述:
(2)
式中:
为位错增殖速率;
为分应变速率;b为柏氏矢量;L为位错自由程[7]。又因为晶粒尺寸与
成正比,再结合式(2)可知,塑性变形能够持续地细化材料晶粒组织。材料变形工程中的微观组织演化以位错的积累与湮灭过程之间的动态平衡为主要特征,随着变形道次的增加,变形量逐渐积累,材料的位错密度逐渐提高,使得位错的动态回复过程加剧,并占主导地位;位错湮灭速度提高,阻碍了位错的增殖过程,晶粒细化效率逐渐降低并趋于饱和,从而使硬度提高程度有所减小。
2.3.2 USP钢球直径对已CGP处理的AZ31镁合金显微组织和硬度的影响
分别从B、C组剩余8件试样中各任选三件试样,进行不同钢球直径的USP处理。具体试验参数如表1中序号4#、3#和5#,其他喷丸参数均相同,只有钢球直径不同,分别为1.4、2和3 mm。由于B、C组的试样都先进行了不同道次的CGP处理,故可研究USP钢球直径对已CGP处理的AZ31镁合金的影响。
如图10、19和20所示,随着钢球直径的提升,AZ31镁合金出现了明显的晶粒细化。与用直径为1.4 mm和2 mm的钢球喷丸处理的试样相比,钢球直径为3 mm喷丸的试样,表面晶粒细化最为明显,组织也更加均匀,C组试样用直径为3 mm的钢球喷完后,平均晶粒尺寸达到7.97 μm,晶粒细化了39.76%。
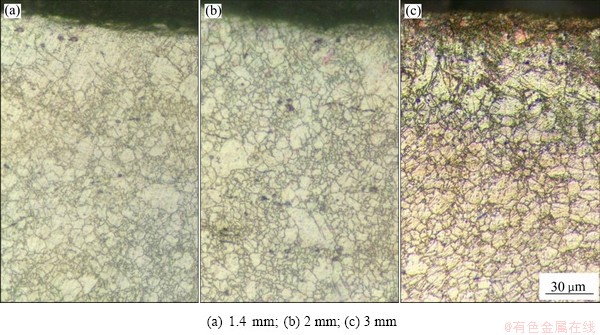
图19 B组不同USP钢球直径处理的AZ31镁合金显微组织
Fig. 19 Microstructures of AZ31 magnesium alloys treated with different USP shot diameters in group B
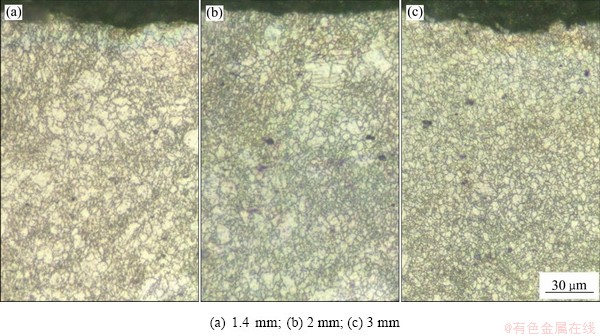
图20 C组不同USP钢球直径处理的AZ31镁合金显微组织
Fig. 20 Microstructures of AZ31 magnesium alloys treated with different USP shot diameters in group C
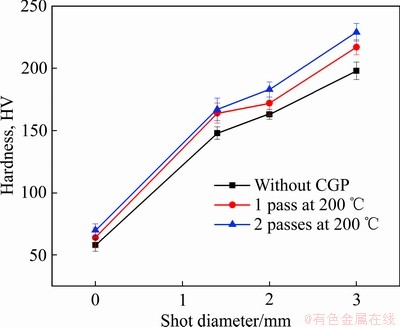
图21 不同USP钢球直径处理的AZ31镁合金的硬度
Fig. 21 Hardness of AZ31 magnesium alloys treated with different USP shot diameters
图21所示为钢球直径的大小对进行不同道次CGP处理的AZ31镁合金硬度的影响规律,随着钢球直径的增加,试样表面硬度也增加,两者之间基本上呈线性关系。喷丸处理后,三种材料表面硬度迅速提高。用直径为1.4 mm的钢球喷丸后,A、B和C三组试样硬度分别上升至148 HV、164 HV和167 HV,换更大的钢球进行喷丸实验,试样的硬度继续提高。当喷丸钢球直径为3 mm时,C组试样硬度最大,达到了229 HV,硬度提高了294.83%。钢球的体积和质量都远低于工具头,因此钢球直径的改变对钢球的撞击速度影响很小。然而,对于不同直径的钢球,本文所采用的钢球数都以铺满一层喷丸室为标准,也就意味着当用小直径的钢球进行处理时,喷丸室中的钢球数量更多。在喷丸实验中,由于小直径钢球的直径小、质量轻,在撞击试样表面的过程中,运动路线极不稳定,增加了钢球与钢球之间、钢球与喷丸室之间碰撞的可能性,造成钢球动能的损失,降低钢球撞击试样的速度;而当使用较大直径的钢球时,钢球直径的增加会直接导致钢球质量的增加,钢球以更大的动能去撞击试样表面,使试样产生更加剧烈的塑性变形,实现表面晶粒的细化。
2.3.3 USP工作振幅对已CGP处理的AZ31镁合金显微组织和硬度的影响
分别从B、C两组剩余5件试样各中任选两件,进行不同工作振幅的USP处理。实验参数如表1中序号5#和6#,其他喷丸参数均相同,只有工作振幅不同,分别为32 μm和40 μm。由于B、C组的试样都先进行了不同道次的CGP处理,故可研究USP工作振幅对已CGP处理的AZ31镁合金的影响。
如图12、22和23所示,A、B、C三组试样的显微组织中C组的晶粒尺寸最为细小,分布最为均匀。当喷丸工作振幅为40 μm时,用截线法测得C组的平均晶粒尺寸约为7.52 μm,与A组喷丸前的试样相比细化了43.16%。
如图24所示,工作振幅为0时,即为各组未进行喷丸处理时的试样硬度。A、B和C三组试样在工作振幅为32 μm下进行USP处理,试样硬度分别提升至198 HV、217 HV和229 HV,与A组未喷丸的试样硬度相比,分别提高了241.38%、274.14%和294.83%。在工作振幅为40 μm下进行USP处理,C组200 ℃ 2道次CGP处理的试样硬度最高,达到了236 HV,硬度提高306.90%。工具头的平均速度与工作振幅在一定程度上呈线性关系,工具头输出的工作振幅越大,说明工具头振动的频率越大,产生的平均速度越大,而钢球运动所需的动能全部来自工具头的输出。因此,提高工作振幅,可以使钢球获得更大的动能和撞击速度,进而产生更加剧烈的塑性变形,使晶粒变形程度增大,晶粒不断细化,硬度显著提高。
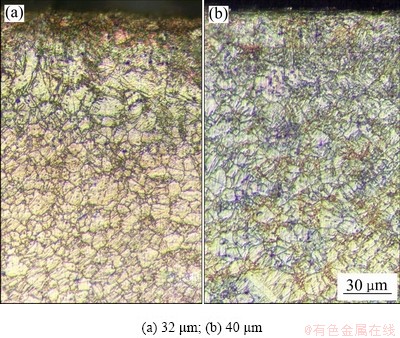
图22 B组不同USP工作振幅处理的AZ31镁合金显微组织
Fig. 22 Microstructures of AZ31 magnesium alloys treated with different USP sonotrode amplitudes in group B
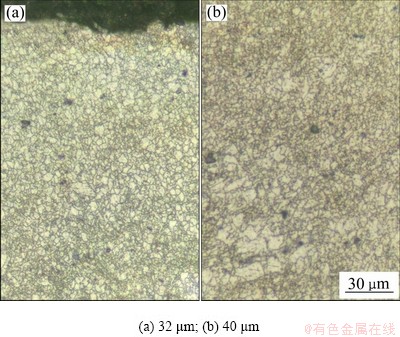
图23 C组不同USP工作振幅处理的AZ31镁合金显微组织
Fig. 23 Microstructures of AZ31 magnesium alloys treated with different USP sonotrode amplitudes in group C
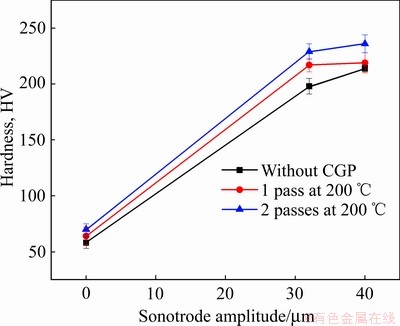
图24 不同USP工作振幅处理的AZ31镁合金的硬度
Fig. 24 Hardness of AZ31 magnesium alloys treated with different USP sonotrode amplitudes
2.3.4 USP工作距离对已CGP处理的AZ31镁合金显微组织和硬度的影响
对B、C两组剩余的最后三件试样进行不同工作距离的USP处理。具体实验参数如表1中序号6#、7#和8#,其他喷丸参数均相同,只有工作距离不同,分别为7.5、10和12.5 mm。由于B、C组的试样都先进行了不同道次的CGP处理,故可研究USP工作距离对已CGP处理的AZ31镁合金的影响。
如图14、25和26所示,USP在工作距离为7.5 mm处理试样时,每组试样晶粒细小且分布均匀,晶粒细化效果最好,此时A、B、C三组试样的平均晶粒尺寸分别约为8.00、7.89和7.52 μm,与A组未喷丸的试样平均晶粒相比分别细化了39.53%、40.36%和43.16%。而随着工作距离的增加,试样的表层晶粒逐渐增大,晶粒细化效果越来越不明显。
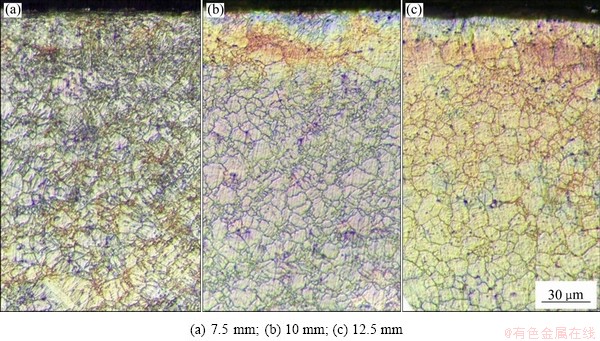
图25 B组不同USP工作距离处理的AZ31镁合金显微组织
Fig. 25 Microstructures of AZ31 magnesium alloys treated with different USP peening distances in group B
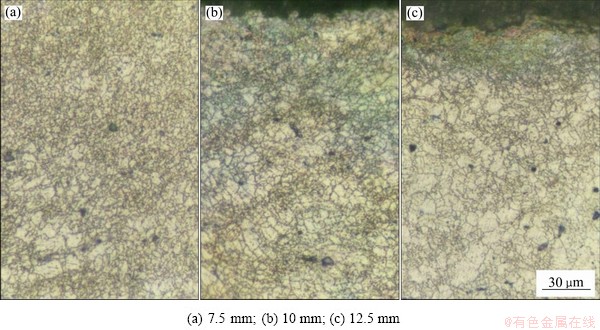
图26 C组不同USP工作距离处理的AZ31镁合金显微组织
Fig. 26 Microstructures of AZ31 magnesium alloys treated with different USP peening distances in group C
如图27所示,试样的硬度随工作距离的增大而减小,当工作距离为7.5 mm时,试样晶粒尺寸最小,硬度最大。A组试样在工作距离为7.5 mm下进行USP处理,硬度为214 HV,比A组喷丸前的试样硬度提高了268.97%。B和C两组试样在工作距离为7.5 mm时的硬度比A组高,分别为219 HV和236 HV,相对于A组喷丸前的试样硬度,分别提高了277.59%和306.90%。一方面,工作距离的增加,意味着钢球需要运动更长的距离到达试样表面,需要消耗更多的动能去克服重力做功,这样到达试样表面的动能就减小了,甚至可能导致有些钢球在还未到达试样表面之前,就已经下落,进而也减少了钢球到达表面的数量;另一方面,随着工作距离的增加,钢球的运动方向有了更多的可能性,同样增加了钢球与钢球、钢球与喷丸室之间碰撞的可能性,减弱了钢球的撞击速度,从而减小了晶粒细化程度,硬度提高效率下降。
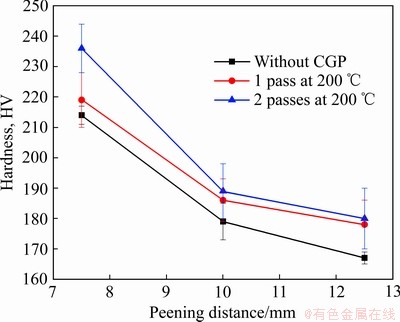
图27 不同USP工作距离处理的AZ31镁合金的硬度
Fig. 27 Hardness of AZ31 magnesium alloys treated with different USP peening distances
3 结论
1) CGP和USP复合工艺相对于单一工艺能进一步减小AZ31镁合金晶粒尺寸,增强表面硬度。镁合金经过复合工艺处理后的表面晶粒尺寸比仅经过单一USP或CGP处理后的表面晶粒尺寸更细小,硬度也有明显的提高,而且随着变形道次的增加,这种叠加效果更加明显。以本次实验为例,未经过CGP和USP处理的AZ31镁合金平均晶粒尺寸约为13.23 μm,表面硬度为58 HV,而经过CGP和USP复合处理的AZ31镁合金最小平均晶粒尺寸仅为7.52 μm,最大表面硬度达到236 HV,晶粒最大细化了43.16%,硬度最大提高了306.90%。
2) 在CGP和USP对AZ31镁合金的复合工艺实验中,USP工艺对表层组织和硬度的影响更加明显。一方面,A、B、C三组试样经过不同道次的CGP处理而不进行USP处理时,平均晶粒尺寸约为13.23、10.78和10.23 μm,相比于原始试样,晶粒最大细化了22.68%。而当A组不进行CGP处理,只经过USP处理后的最大和最小表层平均晶粒尺寸分别为10.78 μm和8.00 μm,晶粒最小细化了18.52%,最大细化了39.53%。另一方面,A、B、C三组试样经过不同道次的CGP处理而不进行USP处理时,试样硬度值分别为58 HV、64 HV和70 HV,最大只提高20.69%,可见CGP工艺对试样表面硬度提高较小。而A组中不进行CGP处理,只经过USP处理后的试样硬度值最低为148 HV,最小都提高了155.17%,远大于只经过CGP处理的试样硬度。因此,相比于CGP工艺,USP处理对于AZ31镁合金的表层组织和硬度影响更加显著,占主要地位。
3) 在试样经CGP处理后再进行USP的实验中,当喷丸处理时间较短时,晶粒组织在细化的同时,也不可避免地呈现出一定的不均匀性。而随着喷丸时间的增加,晶粒继续细化,硬度不断升高,这种不均匀性程度逐渐下降,晶粒组织越来越趋于均匀。当处理时间达到400 s时,显微组织最为细小均匀,硬度达到一定极限不再变化。当钢球直径或工作振幅增加时,晶粒逐渐细化,硬度越来越高;而当工作距离不断增加时,晶粒细化程度下降。
REFERENCES
[1] 李绍龙. AZ31镁合金板材的限制性模压工艺研究[D]. 济南: 山东大学, 2015.
LI Shao-long. Study on constrained groove pressing of AZ31 magnesium alloy sheet[D]. Jinan: Shandong University, 2015.
[2] 杨东峰, 董国疆, 赵长财, 等. AZ31B镁合金薄板热拉伸显微组织试验研究[J]. 塑性工程学报, 2011, 18(2): 76-80.
YANG Dong-feng, DONG Guo-jiang, ZHAO Chang-cai, et al. Experimental research on microstructure of AZ31B magnesium alloy thin sheet under thermal tension[J]. Journal of Plasticity Engineering, 2011, 18(2): 76-80.
[3] 徐振丽. 镁合金复合镀层结构和耐腐蚀性能研究[J]. 农机使用与维修, 2020(1): 30-32.
XU Zhen-li. Study on the structure and corrosion resistance of magnesium alloy composite coating[J]. Agricultural Mechanization Using and Maintenance, 2020(1): 30-32.
[4] SHIN D H, PARK J, KIM Y, et al. Constrained groove pressing and its application to grain refinement of aluminum[J]. Materials Science and Engineering A, 2002, 328(1): 98-103.
[5] 梁 萍. 纯铝/纯铜板材的限制性模压工艺研究[D]. 济南: 山东大学, 2013.
LIANG Ping. Research on constrained groove pressing of pure Al/Cu sheet[D]. Jinan: Shandong University, 2013.
[6] 王宗申, 管延锦, 魏修亭, 等. 模压变形工艺及其研究进展[J]. 河北科技大学学报, 2017, 38(3): 218-228.
WANG Zong-shen, GUAN Yan-jin, WEI Xiu-ting, et al. Groove pressing and its research progress[J]. Journal of Hebei University of Science and Technology, 2017, 38(3): 218-228.
[7] 王宗申. 金属板材限制模压变形工艺的实验与数值模拟研究[D]. 济南: 山东大学, 2014.
WANG Zong-shen. Experimental and numerical study on constrained groove pressing of sheet metals[D]. Jinan: Shandong University, 2014.
[8] LEE J W, PARK J J. Numerical and experimental investigations of constrained groove pressing and rolling for grain refinement[J]. Journal of Materials Processing Tech, 2002, 130/131: 208-213.
[9] 杨开怀, 彭开萍, 陈文哲. 限制模压变形1060纯铝的组织演化与晶粒细化[J]. 中国有色金属学报, 2011, 21(12): 3026-3032.
YANG Kai-huai, PENG Kai-ping, CHEN Wen-zhe. Microstructural evolution and grain refinement of 1060 pure Al processed by constrained groove pressing[J]. The Chinese Journal of Nonferrous Metals, 2011, 21(12): 3026-3032.
[10] PENG K, SU L, SHAW L L, QIAN K. Grain refinement and crack prevention in constrained groove pressing of two-phase Cu-Zn alloys[J]. Scripta Materialia, 2007, 56(11): 987-990.
[11] SAJADI A, EBRAHIMI M, DJAVANROODI F. Experimental and numerical investigation of Al properties fabricated by CGP process[J]. Materials Science and Engineering A, 2012, 552: 97-103.
[12] BORHANI M, DJAVANROODI F. Rubber pad-constrained groove pressing process: Experimental and finite element investigation[J]. Materials Science and Engineering A, 2012, 546: 1-7.
[13] FAN R, ATTARILAR S, SHAMSBORHAN M, et al. Enhancing mechanical properties and corrosion performance of AA6063 aluminum alloys through constrained groove pressing technique[J]. Transactions of Nonferrous Metals Society of China, 2020, 30(7): 1790-1802.
[14] TAO N R, SUI M L, LU J, et al. Surface nanocrystallization of iron induced by ultrasonic shot peening[J]. Nanostructured Materials, 1999, 11(4): 433-440.
[15] 王妍洁. 7075铝合金超声喷丸表面改性研究[D]. 济南: 山东大学, 2017.
WANG Yan-jie. Study on surface modification of 7075 aluminum alloy by ultrasonic shot peening[D]. Jinan: Shandong University, 2017.
[16] 闫林林. 超声喷丸技术的理论与实验研究[D]. 南京: 南京航空航天大学, 2010.
YAN Lin-lin. Theory and experiment research on ultrasonic shot peening[D]. Nanjing: Nanjing University of Aeronautics and Astronautics, 2010.
[17] 杨天南, 林 爽, 蔡 晋. 超声喷丸激励振动幅值对TC4钛合金表面状态影响的仿真研究[J]. 航空精密制造技术, 2020, 56(4): 14-18.
YANG Tian-nan, LIN Shuang, CAI Jin. Simulation study of effect of excited vibration on ultrasonic shot peening surface state of TC4 titanium alloy[J]. Aviation Precision Manufacturing Technology, 2020, 56(4): 14-18.
[18] 侯红亮, 王耀奇, 李晓华, 等. 先进钣金成形技术在航空航天领域的应用(上)[J]. 金属加工(热加工), 2008(13): 22-24.
HOU Hong-liang, WANG Yao-qi, LI Xiao-hua, et al. Application of advanced sheet metal forming technology in aerospace field[J]. MW Metal Forming, 2008(13): 22-24.
[19] CHARDIN H, NGUYEN F, GRILLON F, et al. Random approach to peening coverage in ultrasonic shot-peening[J]. Materials and Manufacturing Processes, 1995, 10(5): 1101-1106.
[20] ABRAMOV V O, ABRAMOV O V, SOMMER F, et al. Surface hardening of metals by ultrasonically accelerated small metal balls[J]. Ultrasonics, 1998, 36(10): 1013-1019.
[21] COCHENNEC F, ROUHAUD E, RETRAINT D, et al. Analysis of the impact of a shot at low velocity using the finite element method. Application to the ultrasonic shot-peening process[J]. Materials Science Forum, 2006, 44: 337-342.
[22] PILE C, FRANCOIS M, RETRAINT D, et al. Modelling of the ultrasonic shot peening process[J]. Materials Science Forum, 2005, 490/491: 67-72.
[23] LIU G, LU J, LU K. Surface nanocrystallization of 316L stainless steel induced by ultrasonic shot peening[J]. Materials Science and Engineering A, 2000, 286(1): 91-95.
[24] 冯 淦, 石连捷, 吕 坚, 等. 低碳钢超声喷丸表面纳米化的研究[J]. 金属学报, 2000, 36(3): 300-303.
FENG Gan, SHI Lian-jie, Lü Jian, et al. Investigation of surface nanocrystallization of a low carbon steel induced by ultrasonic shot peening[J]. Acta Metallurgica Sinica, 2000, 36(3): 300-303.
[25] 朱立华. 纯钛板材超声喷丸表面处理实验与建模研究[D]. 济南: 山东大学, 2019.
ZHU Li-hua. Experimental and modeling study of surface treatment on pure Titanium plate by ultrasonic shot peening[D]. Jinan: Shandong University, 2019.
[26] 余辉辉. 镁合金中界面特征与细晶强化的关系研究[D]. 重庆: 重庆大学, 2018.
YU Hui-hui. Research on the relationship between boundary character and strengthening in Mg alloys[D]. Chongqing: Chongqing University, 2018.
[27] SHIEDEL A, KHAJEH A, MPSHKSAR M M. Experimental and finite element investigation of semi-constrained groove pressing process[J]. Materials Science and Engineering A, 2010, 31(2): 946-950.
[28] SATHEESH KUMAR S S, RAGHU T. Structural and mechanical behaviour of severe plastically deformed high purity aluminium sheets processed by constrained groove pressing technique[J]. Materials and Design, 2014, 57: 114-120.
Effects of constrained groove pressing and ultrasonic shot peening on surface microstructure and hardness of AZ31 magnesium alloy
HUANG Qing-guo1, ZHU Li-hua1, WANG Zong-shen1, GUAN Yan-jin2, CHEN Hao1, YU Cong-xiao1
(1. School of Mechanical Engineering, Shandong University of Technology, Zibo 255000, China;
2. School of Materials Science and Engineering, Shandong University, Jinan 250061, China)
Abstract: The effects of a composite process of constrained groove pressing (CGP) and ultrasonic shot peening (USP) on the surface microstructures and hardness of AZ31 magnesium alloy were studied. The results show that the superposition effect of CGP and USP can further reduce the grain size of AZ31 magnesium alloy and enhance the surface hardness compared with the single process. After the composite processing, the minimum average grain size of AZ31 magnesium alloy is 7.52 μm, which is 43.16% finer than that of the original sample, and the surface hardness is up to 236 HV, which is 306.90% higher than that of the original sample. In addition, the effect of USP on the surface microstructure and hardness of AZ31 magnesium alloy is more obvious than that of CGP. With the increase of USP treating time, the grains become finer and the hardness becomes higher continuously. However, when the treating time reaches 400 s, the grain size is no longer significantly reduced and the hardness reaches a certain limit.
Key words: AZ31 magnesium alloy; constrained groove pressing; ultrasonic shot peening; grain refinement; hardness increase
Foundation item: Project(51605266) supported by the Youth Program of National Natural Science Foundation of China; Project(S201910433226) supported by the Innovation and Entrepreneurship Training Program for College Students in Shandong Province, China
Received date: 2020-04-27; Accepted date: 2020-10-26
Corresponding author: ZHU Li-hua; Tel: +86-18954441725; E-mail: zhulihua@sdut.edu.cn
(编辑 王 超)
基金项目:国家自然基金青年项目(51605266);山东省大学生创新创业训练项目(S201910433226)
收稿日期:2020-04-27;修订日期:2020-10-26
通信作者:朱立华,讲师,博士;电话:18954441725;E-mail: zhulihua@sdut.edu.cn