
Isothermal corrosion (γ′+γ) Ni3Al alloy in liquid zinc
WANG Wen-jun(王文俊), LIN Jun-pin(林均品), WANG Yan-li(王艳丽), CHEN Guo-liang(陈国良)
State Key Laboratory for Advanced Metals and Materials,
University of Science and Technology Beijing, Beijing 100083, China
Received 20 April 2006; accepted 30 June 2006
Abstract: The isothermal corrosion testing and microscopic examination of Ni3Al alloy in liquid zinc containing small amounts of aluminum (mass fraction less than 0.2%) at 450 ℃ were carried out. The results show that the controlling mechanism of the dissolution reaction is diffusion through a boundary layer into liquid zinc. For two-phase alloy, Ni3Al alloy (γ′+γ), the interface between dissolving solid and liquid remains remarkably planar and the difference in dissolution of the two adjacent phases (γ′+γ) can not be experimentally observed. The boundaries between γ′ phase and γ phase play no perceptible role in the dissolution of Ni3Al alloy in liquid zinc. The X-ray diffraction spectra of the diffusion layer confirm the presence of Ni5Zn21. The corrosion rate of the Ni3Al alloy in molten zinc was calculated to be approximately 2.6×10-3 g/(cm2?h), therefore the liquid zinc corrosion resistance of Ni3Al alloy is very weak.
Key words: Ni3Al alloy; liquid zinc corrosion; hot-dip galvanizing; intermetallics
1 Introduction
The considerable volume of research on corrosion of metals by liquid zinc can be ascribed to the historical interest in the galvanizing industry [1]. In continuous hot-dip coating lines, the immersed bath hardware (e.g. bearings, sink, stabilizer, corrector rolls, support roll arms and snout tip) is subject to corrosive attack by the molten bath material [2]. Current materials used in the bearing application of continuous hot-dip coating lines include 316 stainless steel, specialized ceramics, stellite alloys and multiple other materials. Though many materials have been examined in the search for corrosion resistance bath hardware, none of these has emerged as an obvious leader in this field. An improvement in the material used for bearings in the hot-dip coating process would mean a decrease in the frequency of line shutdowns and substantial cost and energy savings. The continuous hot-dip coating lines could run for longer periods and produce higher quality products [3-5].
In the present study, two-phase solid metals were selected for investigation because such a structure is common in construction materials used in liquid metal engineering systems. The high performance directionally solidified Ni3Al base alloy IC6, has been developed for aero-engine turbine vanes operating in the temperature range of 950-1 100 ℃. The alloy was used for the second stage gas turbine vanes [6, 7]. An experimental program was designed to investigate the role of a second phase on dissolution kinetics, and examine the potential of using Ni3Al alloy in the bath hardware application of the continuous hot-dipping process.
2 Experimental
2.1 Experimental methods
The nominal composition of the Ni3Al alloy is Ni-(7.5-8.5)Al-(10-14)Mo-(0.02-0.15)B (mass fraction, %). The main phases of matrix alloy are as follows: about 80%(volume fraction) γ′-Ni3(Al, Mo), about 20%(volume fraction) γ-Ni(Mo) supersaturated solid solution and <2%(volume fraction) boride. The dimensions of the test specimens are 50 mm×20 mm×1.7 mm. Before the corrosion test, the specimens were polished.
The bath material liquid zinc containing small amounts of aluminum (mass fraction less than 0.2%) was melted, brought to the desired testing temperature (450 ℃), and stabilized. The specimens’ thickness was measured before being introduced to the molten bath. Four specimens of Ni3Al were immersed in the baths for 1, 2, 4 and 8 d, respectively. One by one, the specimens were removed from the bath after their specified immersion times had expired. The specimens’ thickness was measured again.
2.2 Method of calculating corrosion rate
The thickness of every tested specimen was measured at multiple locations across the cross-section of the specimen. The thickness measurement was made at 2 mm intervals across the cross-sections. The measurement was not taken fully to the end of the specimen, but only taken 8 mm to either side of the specimen center. This was done in order to eliminate erroneous data that might result from the tapering of the specimen on the ends due to accelerated corrosion in these areas.
From the thickness measurement taken along the cross-section of each corrosion specimen, the average thickness loss was found. The average thickness loss was used to calculate corrosion rate. The formula used to calculate the corrosion rate of the tested alloy is given by
(1)
where dw/dt is the corrosion rate, g/(cm2·h); r is the density of base material, g/cm3; dy/dt is the average thickness loss per unit time, cm/h; the factor of 1/2 in the equation reflects the fact that the average thickness change of the specimen is caused by the corrosion of both faces of the specimen [8].
The analysis of the diffusion layer formed during the corrosion testing was conducted with the aid of a scanning electron microscope (SEM) using backscattered electron imaging (BSE) and the energy dispersion spectroscopy (EDS) capability of the microscope. Phase analysis was performed by X-ray diffractometry (XRD) technique. The measurements were carried out at room temperature on a Philips APD-10 diffractometer, using Cu Kα radiation for an angle (2θ) range of 20?-90?. An electron probe micro-analyzer (EPMA) was used to inspect the elemental distribution in the diffusion layer.
3 Results
3.1 Calculation of corrosion rate
The specimens of Ni3Al alloy embedded in resin from liquid zinc for different immersion periods are shown in Fig.1. The specimens were tested for periods of 1, 2, 4 and 8 d from left to right. The darker section in the middle of the black resin is the part of original Ni3Al alloy from liquid zinc. The lighter section on both sides of the Ni3Al alloy is zinc. The thickness loss of the Ni3Al specimens can be observed to increase with testing time.
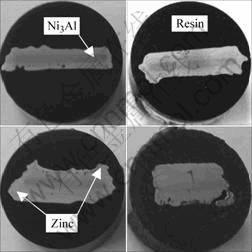
Fig.1 Cross-sections of Ni3Al specimens embedded in resin from liquid zinc (Specimens were tested for periods of 1, 2, 4 and 8 d from left to right)
Fig.2 shows a plot of specimen thickness loss measured at specified locations on the cross-section of a test specimen. The data in Fig.2 were measured from the designation of the respective test specimens, which shows greater thickness loses occurring at the end of the specimens, compared to the specimen center.
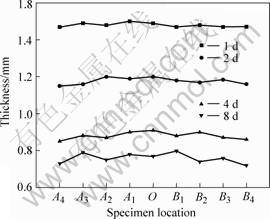
Fig.2 Specimen thickness measurement from liquid zinc at 450 ℃
From the thickness loss data in Fig.2, the average thickness loss was calculated and the value was plotted vs time.
Fig.3 shows the result of the corrosion testing of the Ni3Al alloy in liquid zinc, indicating that the second-degree parabolic nature of the thickness reduction rate is evident.
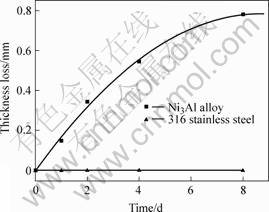
Fig.3 Thickness loss of specimens from liquid zinc at 450 ℃
The average thickness loss dy/dt of the specimens in the static immersion test was calculated to be 7.0×10-4 cm/h.
From the average thickness loss and according to Eqn.(1), the corrosion rate of the Ni3Al alloy in liquid zinc was calculated to be approximately 2.6×10-3 g/(cm2·h), which is two orders of magnitude faster than that of 316 stainless steel in the same environment (typical material used for galvanizing operations is type 316 stainless steel for bath hardware rolls).
3.2 Corrosion characteristics
Fig.4 shows the back scattered-electron micro- graphs of Ni3Al from liquid zinc for 8 d. It is found that there is a straight boundary between Ni3Al alloy and liquid zinc. It can be concluded that the liquid zinc corrosion on Ni3Al alloy is general corrosion. Fig.4(b) shows the high magnification image of boxed zone in Fig.4(a). From Fig.4(b) it can also be found obviously that Ni3Al alloy dissolves in liquid zinc.
Fig.5(a) shows the back scattered-electron micrograph of Ni3Al alloy. The γ′ phase contains a relatively high amount of aluminum and low amount of molybdenum, compared to the amounts of those in the γ phase [9]. The relatively heavy elements in the base material appear as a lighter area when using the back-scattered imaging capability of the SEM. The lighter areas are γ phase and the darker areas are γ′ phase. Fig.5(b) shows the back scattered-electron micrograph of Ni3Al alloy from liquid zinc for 8 d that has a bigger magnification times than Fig.4(b). From Fig.5(b) it can be more obviously found that the Ni3Al alloy is corroded by liquid zinc after immersion. The γ′ phase drifts into liquid zinc because liquid zinc attacks γ phase quickly, which is around γ′ phase. There are a lot of grains of γ′ phase that are still not dissolved completely in liquid zinc. However γ phase is almost dissolved completely by
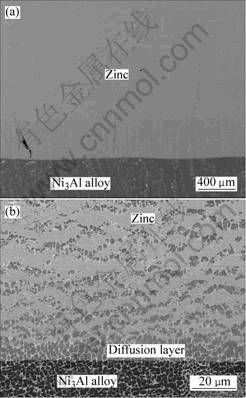
Fig.4 Back scattered-electron micrographs of Ni3Al alloy from liquid zinc for 8 d: (a) Low magnification; (b) High magni- fication
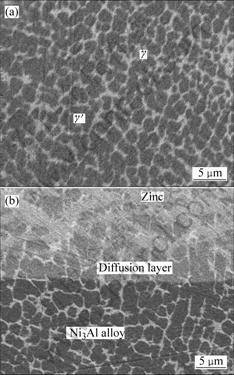
Fig.5 Back scattered-electron micrograph of Ni3Al alloy(a) and Ni3Al alloy from liquid zinc for 8 d(b)
liquid zinc. Diffusion through a boundary layer in the liquid zinc controls the dissolution reaction. The thickness of the boundary layer is certainly less than 10 μm and most likely less than 5μm.
3.3 EDS and XRD analysis
The positions of EDS of the six points (A, B, C, D, E and F) are shown in Fig.6. Table 1 lists the chemical compositions of the six points in Fig.6 analyzed by EDS. From Table 1 it is found that point B contains 4.0%(mole fraction) of molybdenum, which is higher than that of point A 1.7%, therefore it is confirmed that γ phase is lighter than γ′ phase. Point D contains 50.8% of zinc, which is slightly higher than point C 40.7%. The reason for this difference is that point D is slightly far from Ni3Al alloy matrix than point C, but note that liquid zinc preferentially attacks γ phase which is around γ′. Points E and F have almost the same amount of zinc and nickel. The XRD patterns of the diffusion layer is shown in Fig.7. The mainly phase in the diffusion layer is determined to be Ni5Zn21. Investigation of other phases’ crystal structure is underway.
The position of the EPMA line is shown in Fig.8. The intensity distribution curve of zinc, aluminum, molybdenum and nickel vs distance along the EPMA line in Fig.8 is shown in Fig.9. The higher the intensity somewhere, the higher the relative content of the element there. The important point considered here is that zinc exhibits linearly increasing and nickel exhibits linearly
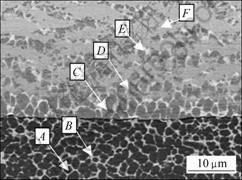
Fig.6 Location of EDS analysis of Ni3Al alloy from liquid zinc for 8 d
Table 1 Chemical compositions of six points (A, B, C, D, E and F) shown in Fig.6 (mole fraction, %)
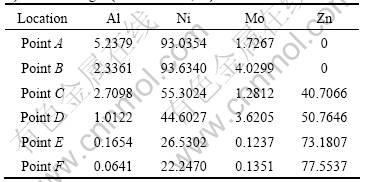
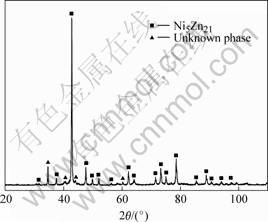
Fig. 7 X-ray diffraction pattern of diffusion layer
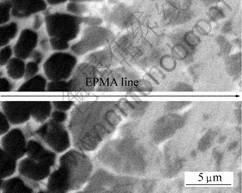
Fig.8 Positions of EPMA line
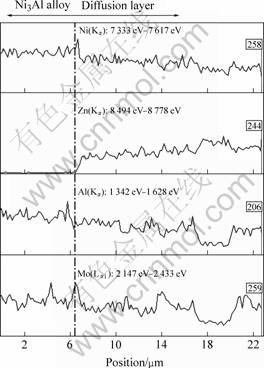
Fig.9 Intensity of elements distribution along EPMA line in Fig.8
decreasing along the EPMA line in Fig.8. The EPMA line is across both γ phase and γ′ phase, therefore it is confirmed that the controlling mechanism of dissolution reaction is diffusion. That is to say, the dissolution velocity of γ phase into liquid zinc is the same as that of γ′ phase.
4 Discussion
The main research on dissolution reactions was performed for the reaction between a solid and a liquid metal. From the kinetics, one could decided an interface controlled or a diffusion controlled reaction. In general, diffusion controlled processes result in uniform attack while interface controlled reactions are marked by preferential etching or grain boundary attack [10].
It is shown that, in the experimental conditions employed, the controlling mechanism of the dissolution reaction is diffusion of metal through a boundary layer into the liquid zinc. For Ni3Al alloy, the interface between the dissolving solid and liquid remains remarkably planar and the difference in dissolution of the two adjacent phases (γ′+γ) could not be experimentally observed.
A highly significant feature of this research is the retention of an almost planar interface in dissolution. We say almost planar because any difference in dissolution between the phases is not resolvable. This apparent smoothness of the interface is independent of grain boundaries or changes in chemical composition of the dissolving phases.
One point should be addressed here that as long as the controlling factor is diffusion across an interface, dissolution is dependent only on the chemistry and hydrodynamics of the liquid boundary layer. This means that an intermetallic compound may show comparable solubility rates in a molten metal with those of pure metals.
It seems that γ phase is corroded more quickly than γ′ phase by liquid zinc after immersion (see Fig.4(b)). Maybe someone thinks incorrectly that liquid zinc preferentially attacks γ phase which is around γ′ phase. This may be considered in the following way. Since the controlling factor is the diffusion of solute atoms across the diffusion boundary layer, only a given number of nickel atoms per unit area can leave the solid in unit time and move into the liquid. Thus, the phase that is richer in nickel should retreat at a slower rate than the phase with less nickel. The γ phase contains almost the same amount of nickel as γ′ phase, but the amount of γ phase is much less than γ′ phase in Ni3Al alloy. Therefore, γ phase is corroded more quickly than γ′ phase by liquid zinc.
It might also be pointed out that no galvanic effects are noted, which would be demonstrated in aqueous solution. Hence, a solvent which is an electron carrier does not behave like a solvent that is predominantly an ion carrier. Furthermore, there is no intergranular penetration by liquid zinc, which may also be directly related to the fact of diffusion control for this reaction.
One may then summarize the observed planarity of interface that the dissolution of two phases proceeds with no enhanced effects due to one of them, and the grain boundaries play no part in the dissolution.
5 Conclusions
1) The interface between the solid Ni3Al alloy and reacting liquid zinc remains almost smooth and is independent of microstructure. The boundaries between solid phases (γ and γ′) play no perceptible role in the dissolution of Ni3Al alloy.
2) Diffusion through a boundary layer in the liquid zinc controls the dissolution reaction. The thickness of the boundary layer is 5-10 μm. The mainly phase in the diffusion layer is determined to be Ni5Zn21. Electrochemical effects do not significantly enter into the reaction.
3) The corrosion rate of the Ni3Al alloy in liquid zinc was calculated to be approximately 2.6×10-3 g/(cm2·h). The liquid zinc corrosion resistance of Ni3Al alloy is very weak.
References
[1] LEE H H, HIAM D. Corrosion resistance of galvannealed steel [J]. Corrosion, 1989, 45(10): 852-856.
[2] TOWNSEND H E. Corrosion of stainless steel conductor rolls in a continuous sheet electrogalvanizing line [J]. Corrosion, 1990, 46: 418-423.
[3] BRUNNOCK M S, JONES R D. Interactions between liquid zinc and bath hardware materials in continuous galvanizing lines [J]. Ironmaking Steelmaking, 1996, 23: 171-176.
[4] VERMA A R B. High temperature batch hot-dip galvanizing: Part 2. Comparison of coatings formed in the temperature range 520-555 ℃ [J]. Surface and Coatings Technology, 1997, 89: 143-150.
[5] SHIH H C, HSU J W. The lifetime assessment of hot-dip 5%Al-Zn coatings in chloride environments [J]. Surface and Coatings Technology, 2002, 150: 70-75.
[6] MA Shu-wei, ZHENG Yun-rong, YU Xi-hong. Microstructural characterization of Ni7Hf2/Ni3Al eutectic alloy [J]. Trans Nonferrous Met Soc China, 1996, 6(4): 158-162.
[7] LIN Yi-min, XU Tao, ZHANG Hong-tao. Surface modification of Ni3Al alloy by intense pulsed ion beams irradiation [J]. Trans Nonferrous Met Soc China, 2003, 13(1): 205-210.
[8] BURRIS M L. Material Evaluation of Liquid Metal Corrosion in Zn-Al Hot-Dip Coating Baths [D]. West Virginia: College of Engineering and Mineral Resources at West Virginia University Morgantown, 2000.
[9] SONG J X, HAN Y F. Repair of NiCrAlYSi overlay coating on Ni3Al base alloy IC6 [J]. Intermetallics, 2005, 13: 351-355.
[10] LAMPE V, ROOS H, SWENSON M. Attack of molten zinc on steels [J]. Werkstoffe and Korrosion, 1977, 28(4): 226-232.
(Edited by CHEN Wei-ping)
Foundation item: Project (50274005) supported by the National Natural Science Foundation of China
Corresponding author: LIN Jun-pin; Tel: +86-10-62332192; E-mail: linjunpin@skl.ustb.edu.cn