J. Cent. South Univ. Technol. (2010) 17: 24-27
DOI: 10.1007/s11771-010-0005-7 
Effect of heat treatment on microstructures and mechanical properties of Al-6Zn-2Mg-1.5Cu-0.4Er alloy
LIU Ying-ying(刘莹颖), XIA Chang-qing(夏长清), PENG Xiao-min(彭小敏)
School of Materials Science and Engineering, Central South University, Changsha 410083, China
? Central South University Press and Springer-Verlag Berlin Heidelberg 2010
Abstract: The microstructures and mechanical properties of A1-6Zn-2Mg-1.5Cu-0.4Er alloy under different treatment conditions were investigated by transmission electron microscopy (TEM) observation, and tensile properties and hardness test, respectively. The relationship between mechanical properties and microstructures of the alloys was discussed. With trace Er addition to A1-Zn-Mg-Cu alloy, Er and Al interact to form Al3Er phase, which is coherent with α(Al) matrix. The results show that A1-Zn-Mg-Cu alloy after retrogression and re-ageing (RRA) heat treatment exhibits higher tensile strength, ductility and conductivity.
Key words: Al-Zn-Mg-Cu alloy; Er; heat treatment; microstructures; mechanical properties; conductivity
1 Introduction
Al-Zn-Mg-Cu alloys have been widely used as aircraft structure material because of their high strength- to-density ratio. However, these alloys generally have poor ductility and low fracture strength in the as-cast condition. So extensive processes, including a combination of heat treatment and hot working, are required to improve the mechanical properties [1]. Al-Zn-Mg-Cu alloys are typical ageing precipitate strengthening alloys and the ageing treatment is a key process to achieve the required microstructures and properties. T6 temper can obtain the peak hardness and tensile strength, with high stress corrosion cracking (SCC) susceptivity, which has a positive relationship with the variation of electrical conductivity [2]. T76 temper increases the stress corrosion resistance of Al-Zn-Mg-Cu alloys by modifying microstructures, although there exists certain sacrifice in tensile properties compared with T6 temper [3-4]. Retrogression and re-ageing (RRA) heat treatment can enhance the SCC resistance, while retaining the T6 strength of 7075 alloy [5-6], which is a popular heat treatment for Al-Zn-Mg- Cu alloys.
Also, many researches show that with reasonable rare earth additions the properties of Al and its alloys can be remarkably improved. Recently, Er has been considered as the most popular minor alloying element to take place of Sc for Al-Mg and Al-Zn-Mg alloys [7-8]. YANG et al [9] found that with a small amount of Er addition to high pure Al or its alloys, Er can directly react with Al to form primary Al3Er particles. With the similar crystal lattice type (L12), parameter of Al3Er particles to Al matrix (FCC, crystal parameter a=0.404 9 nm) and rather small mismatch (about 4.1%), Al3Er particles that are coherent or semi-coherent with the matrix, have positive and resemble effects. ZHAO et al [10] found that in Al-Zn-Mg-Cu-Er alloys Er is mainly in the form of Al3Er, and small Al3Er phase can be used as the core of heterogeneous nucleation and then improve the mechanical properties of aging state alloy.
The purpose of the present work is to investigate the ageing behavior of Al-Zn-Mg-Cu-0.4Er alloy and to understand the ageing strengthening mechanism in different ageing conditions, as well as the effect of Er addition on the mechanical properties of Al-Zn-Mg-Cu alloys.
2 Experimental
The experimental alloys with the compositions (shown in Table 1) were melted in the resistance furnace and poured into cast iron mold. The obtained alloys were d50 mm ingots. Then, the ingots were homogenized at 460 ℃ for 24 h, and cooled in air. After that, the homogenized ingots were rolled into 2.0 mm-thick sheets at 430 ℃. Then, obtained samples from the above mentioned sheets were treated at 470 ℃ for 120 min, and then water quenched. After that, the samples were aged at 120 ℃ for 36 h. Finally, the samples were heat-treated with T6, T73 and RRA. The detailed conditions of the heat treatments are listed in Table 2.
Table 1 Compositions of experimental alloys (mass fraction, %)
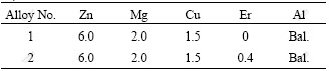
Table 2 Detailed conditions of heat treatments for alloys
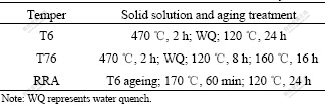
Microstructures of the samples were observed by transmission electron microscopy (TEM). The thin foils were prepared by double-jet and observed on a Tecnai Gz 20 microscope at 200 kV. The mechanical testing was performed on a universal tensile testing machine of CSS-44100 type at room temperature. Vickers micro- hardness measurements were performed by using a load of 50 g Vickers hardness. The SCC trend of different heat-treated alloys was identified by conductivity testing.
3 Results and discussion
3.1 Aging curve
Fig.1 shows the ageing response of the alloys at 120 ℃. In Fig.1, the age-hardening curves show the basic states of under-aged, peak-aged and over-aged. First, the hardness increases gradually with the increase of aging time. The peak hardness of alloy 2 is HRB179 at 120 ℃, which is increased by HRB30 compared with that of alloy 1. The ageing time to achieve peak hardness of alloy 2 is 24 h, which is 4 h less than that of alloy 1.
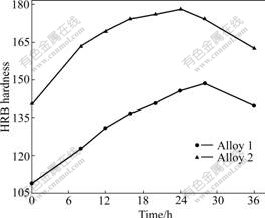
Fig.1 Aging curves of alloys at 120 ℃
The microstructures of alloy 2 after ageing at 120 ℃ for 24 h (T6 temper) are shown in Fig.2. It can be seen that very fine precipitates distribute homogeneously in the matrix (Fig.2(a)). Fig.2(a) indicates that the strengthening mechanism of the peak-aged alloy is the η′ phase strengthening.
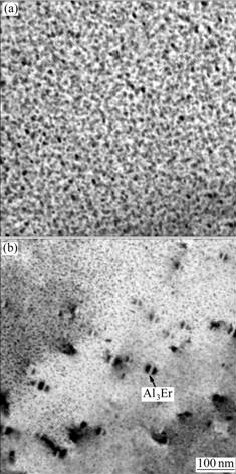
Fig.2 TEM images of Al-6Zn-2Mg-1.5Cu-0.4Er alloy aged at 120 ℃ for 24 h (T6 temper): (a) η′ precipitates; (b) Al3Er precipitates
The fine Al3Er precipitates are found to be on the nanometer scale after solid solution and T6 (Fig.2(b)). In the course of subsequent homogenization of the ingot, the supersaturated solid solution decomposes under thermal activation, and forms secondary precipitates of the dispersed intermetallic Al3Er. These particles strongly pin sub-grain boundaries and dislocations, hinder the movement of the dislocation and sub-grain boundary migration, and increase the tensile strength of the alloy [10]. The strengthening mechanism of Al-6Zn- 2Mg-1.5Cu-0.4Er is considered as fine grain strengthening and dispersion strengthening by Al3Er.
3.2 Mechanical properties and electrical conductivity
The mechanical properties and electrical conductivities of Al-6Zn-2Mg-1.5Cu-0.4Er alloy under different conditions are listed in Table 3. The tensile strength (σb) after T6 temper is 577.12 MPa, and the elongation (δ) is 11.8%. It is found that the electrical conductivity (γ) of the samples has a remarkable increase after T76 treatment (23.0 MS/m) compared with that after T6 treatment (18.4 MS/m). According to Ref.[11], electrical conductivity serves as an indicator of corrosion resistance, that is, higher electrical conductivity means that the material has better SCC performance. It suggests that the SCC resistance of the alloy obtained by the T76 temper is higher than that obtained by the peak-aged (T6 temper). After RRA treatment, the tensile strength of the alloy slightly decreases compared with that after T6 temper, and electrical conductivity of the alloy is almost the same as that after T76 temper. Considering the factors of mechanical property and corrosion resistance property, the alloy after RRA treatment is regarded as the one with the most excellent property.
Table 3 Tensile properties and electrical conductivity of Al-6Zn-2Mg-1.5Cu-0.4Er alloy
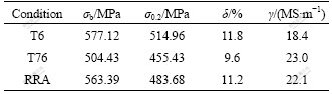
The complete ageing sequence in a wide range of ternary compositions during the ageing heat treatment is as follows: supersaturated solid solution—GP (Zn, Mg) zones—η′ (hexagonal)—η (MgZn2, hexagonal) [12]. These series of alloys provide high strength in the T6 condition. Multi-stage heat treatments provide a means for modifying the size, composition, species, morphology and distribution of precipitate particles in aged aluminum alloys. These changes result in the improvement of mechanical properties [13]. TEM images of samples under different ageing tempers are shown in Fig.3. Fig.3 demonstrates the presence of the η′ phase, which is the main strengthening phase under the ageing condition. Fig.3(a) shows the image of Al-Zn-Mg-Cu-0.4Er alloy after ageing at 120 ℃ for 24 h (peak-aged T6 condition), and reveals that fine precipitations homogeneously distribute in the matrix. The precipitates at grain boundary mainly belong to η phase with continuous distribution. Fig.3(b) shows the image of the alloy after solid solution and T76 treatment. It can be seen from Fig.3(b) that the precipitates in the matrix increase remarkably and the precipitation density is very low. Then, it is not surprising that the alloy possesses low tensile strength under this ageing temper. Furthermore, the grain boundary precipitates, recognized as η phase [14], grow up to be coarser and are more sparsely distributed, and the precipitate free zone (PFZ) with about 50 nm in width can also be observed. Fig.3(c) shows the TEM image of the alloy after RRA treatment.
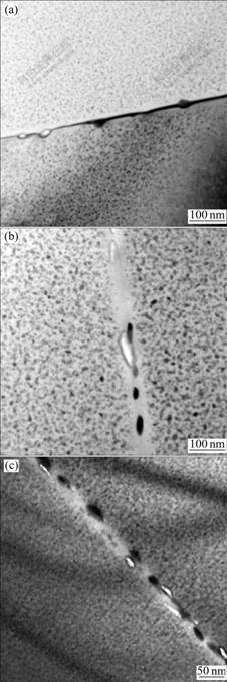
Fig.3 TEM images of Al-Zn-Mg-Cu-0.4Er alloy after different treatments: (a) At 120 ℃ for 24 h; (b) At 120 ℃ for 36 h;(c) RRA
It can be found that the precipitates in the matrix are very similar to those treated by the T6 temper, which are very fine and distributed homogeneously. Therefore, the tensile strength of the alloy after RRA temper is very close to that obtained by the T6 temper. The grain boundary characteristics are similar to those obtained by the T76 temper (Fig.3(b)) and the precipitates are coarse and discontinuously distributed. According to Ref.[15], the coarser and more discrete grain boundary precipitates are suggested to improve the SCC resistance. Thus, it may be inferred that the RRA treatment is favorable for the SCC resistance of the alloy. Furthermore, apparent PFZ with 40-50 nm in width along the grain boundary can be observed.
4 Conclusions
(1) The optimum single-step aging treatment for Al-6Zn-2Mg-1.5Cu-0.4Er alloy is at 120 ℃ for 24 h (T6).
(2) The rare earth element Er mainly exists in the form of Al3Er phase in Al-6Zn-2Mg-1.5Cu-0.4Er alloy. The secondary Al3Er precipitates from supersaturated solid solution that are coherent with the α(Al) matrix can strongly pin sub-grain boundaries and dislocations, hinder the movement of the dislocation and migration of sub-grain boundary and then increase the strength of the alloy.
(3) The tensile strength, ductility and conductivity of Al-6Zn-2Mg-1.5Cu-0.4Er alloy after RRA treatment are 563.39 MPa, 11.2% and 22.1 MS/m, respectively.
References
[1] DAVIS J R. Aluminum and aluminum alloys, ASM specialty handbook [M]. Ohio: ASM International, 1993: 41-43.
[2] WALLANDE W, BEDDOES J C, MALHERBE M C. A new approach to the problem of stress corrosion cracking in 7075-T6 aluminum [J]. Canadian Aeronautics and Space Journal, 1981, 27(3): 222-232.
[3] QU Bin-lung, YANG Ji-gang. Effect of step quench and aging on mechanical properties and resistance to stress corrosion cracking of 7050 aluminum alloy [J]. Materials Transactions, JIM, 2000, 41(7): 783-789.
[4] WERENSKIOLD J C, DESCHAMPS A, BRECHET Y. Characterization and modeling of precipitation kinetics in an Al-Zn-Mg alloy [J]. Materials Science and Engineering A, 2000, 293(1/2): 267-274.
[5] OLIVEIRA A F J, DE BARROS M C, CARDOSO K R, TRAVESSA D N. The effect of RRA on the strength and SCC resistance on AA7050 and AA7150 aluminium alloys [J]. Materials Science and Engineering A, 2004, 379(1/2): 321-326.
[6] WARREN P J, GROVENOR C R M, CROMPTON J S. Field-ion microscope/atom-probe analysis of the effect of RRA heat treatment on the matrix strengthening precipitates in alloy Al-7150 [J]. Surface Science, 1992, 266(15): 342-349.
[7] MAO Jian-wei, JIN Tou-nan, XU Guo-fu, NIE Zuo-ren. As-cast microstructure of Al-Zn-Mg and Al-Zn-Mg-Cu alloys added erbium [J]. Transactions of Nonferrous Metals Society of China, 2005, 15(6): 1341-1345.
[8] XU Guo-fu, NIE Zuo-ren, JIN Tou-nan, YANG Jun-jun, FU Jian-bo, YIN Zhi-min. Effect of trace Er on the as-cast structure of LF3 aluminum alloy [J]. Journal of Rare Earths, 2002, 20(2): 143-150. (in Chinese)
[9] YANG Jun-jun, NIE Zuo-ren, JIN Tou-nan, XU Guo-fu, FU Jing-bo, RUAN Hai-qiong, ZUO Tie-yong. Effect of trace rare earth element Er on high pure Al [J]. Transactions of Nonferrous Metals Society of China, 2003, 13(5): 1035-1039.
[10] ZHAO Zhong-kui, ZHOU Tie-tao, LIU Pei-ying, CHEN Chang-qi. TEM investigation of precipitations with Er in aging Al-Zn-Mg-Cu- Li-Er alloy [J]. Rare Metal Materials and Engineering, 2004, 33(10): 1108-1111. (in Chinese)
[11] LI Zhi-hui, XIONG Bai-qing, ZHANG Yong-an, ZHU Bao-hong, WANG Feng, LIU Hong-wei. Ageing behavior of an Al-Zn-Mg-Cu alloy pre-stretched thick plate [J]. Journal of University of Science and Technology Beijing, 2007, 14(3): 246-250.
[12] FRIDLYANDER I N, DOBROMYSLOV A V, TKACHENKO E A, SENATOROVA O G. Advanced high-strength aluminum-base materials [J]. Metal Science and Heat Treatment, 2005, 47(7/8): 269-275.
[13] MILLER M P, HARLEY E J, TURNER T J, BEAUDOIN A J, CASSADA W A. Mechanical behavior of thin sheets machined from AA7050-T7451 plate [J]. Materials Science Forum, 2000, 331/337(3): 1243-1248.
[14] LI Yun-tao, LIU Zhi-yi, MA Fei-yue, XIA Qing-kun. Phase constitution and growth manner at grain boundary in Al-Cu-Mg- Ag-Er alloy [J]. Rare Metal Materials and Engineering, 2008, 37(6): 1019-1022. (in Chinese)
[15] PUIGGALI M, ZIELINSKI A, OLIVE J M, RENAULD E, DESJARDINS D, CID M. Effect of microstructure on stress corrosion cracking of an Al-Zn-Mg-Cu alloy [J]. Corrosion Science, 1998, 40(4/5): 805-819.
Foundation item: Project(2005CB623706) supported by the National Basic Research Program of China
Received date: 2009-03-09; Accepted date: 2009-09-07
Corresponding author: XIA Chang-qing, Professor; Tel: +86-731-88830267; E-mail: xia_gro@mail.csu.ed.cn
(Edited by CHEN Wei-ping)