J. Cent. South Univ. Technol. (2009) 16: 0535-0540
DOI: 10.1007/s11771-009-0089-0

Cyclic oxidation behavior of Fe-9Cr-1Mo steel in water vapor atmosphere
ZHANG Du-qing(张都清)1, 2, LIU Guang-ming(刘光明)3, ZHAO Guo-qun(赵国群)1, GUAN Yan-jin(管延锦)1
(1. Key Laboratory of Liquid Structure and Heredity of Materials, Ministry of Education,
Shandong University, Jinan 250061, China;
2. Boiler and Pressure Vessel Inspection Center, Shandong Electric Research Institute, Jinan 250002, China;
3. Key Laboratory of Nondestructive Testing of Ministry of Education, Nanchang Hangkong University,
Nanchang 330034, China)
Abstract: The cyclic oxidation behavior of Fe-9Cr-1Mo steel (9Cr-1Mo) in 10%H2O+90%Ar (volume fraction) atmosphere at 600, 650 and 700 ℃ for various time was studied. The oxidation mechanism of 9Cr-1Mo steel in 10%H2O+90%Ar atmosphere was discussed. The thermal stress was evaluated in two oxide layers to illustrate the spallation of the oxide layer. The experimental results indicate that there exists a duplex oxide scale with an outer layer of Fe2O3 and an inner layer of mixed (Fe, Cr)3O4 formed on 9Cr-1Mo steel during cyclic oxidation. Some cracks generated in both inner and outer oxide layers. Parts of oxide scales spalled from substrate during the cyclic oxidation. A higher tensile stress in the oxide layer is formed at the early oxidation stage than at the later oxidation stage during heating. This tensile stress results in the formation of cracks in the oxide layer.
Key words: Fe-9Cr-1Mo steel; water vapor; cyclic oxidation; crack
1 Introduction
Energy security and lower carbon dioxide emissions are increasingly regarded as key factors in protecting the global environment. Research and development of heat resistant steels and alloys for highly-efficient ultra-supercritical power plants at 650 ℃ and above are now being promoted [1-3]. Critical issues for the development of ferritic steels for ultra-supercritical boilers at 650 ℃ are to improve the oxidation resistance and long-term creep rupture strength [4]. In recent years, various Cr-Mo ferritic heat-resistant steels have been developed for use as main steam pipes or super-heater tubes in power generation boiler [5]. These materials have higher creep strength than conventional ferritic steels, so they can be used at higher operating temperature and pressure to increase the efficiency of steam power plants. 9Cr-1Mo steel, as a type of ferritic steel, is widely used as a thick steam pipe component in thermal power plants [6]. Although this alloy exhibits good mechanical and oxidation resistance at an operating temperature of 550 ℃, it still suffers corrosion after long time exposure to severe environment or higher temperature. Up to now, the oxidation or corrosion behavior of this alloy in various environments has been investigated [7-9].
It is well known that the adhesion of the oxide scales is a very important factor to determine the oxidation resistance of a material. However, few investigations have been focused on the cyclic oxidation of this alloy in water vapor environment [10]. Therefore, further research work about the mechanism of cracking and spallation of oxide layers is needed. In order to comprehensively probe the oxidation behavior of 9Cr-1Mo steel in water vapor environment, the cracking and spallation behavior of oxide layers on this material was studied at 600, 650 and 700 ℃ in 10%H2O+90%Ar atmosphere (volume fraction) by cyclic oxidation in this work.
2 Experimental
9Cr-1Mo steel (Fe-0.09C-0.08Si-0.20Mn-9.10Cr- 1.05Mo-0.06Nb-0.18V-0.03N) was received by Baoshan Iron & Steel Co., Ltd, China. Rectangular specimens with dimensions of 15.0 mm×10.0 mm×3.1 mm were cut by the electrical-discharge method. The surfaces were polished by 800 alumina paper. Then the specimens were cleaned sequentially with acetone, ethanol, and distilled water in an ultrasonic bath before tests.
The cyclic oxidation was conducted in a sealed Al2O3 tube with an inlet and an outlet to pass Ar+H2O mixed gases. The cyclic oxidation samples were placed in the Al2O3 tube, which can be moved in/out a tubular electric furnace freely. The atmosphere (Ar and water
vapor) was obtained by passing pure Ar through distilled water in a glass bubbler, and the distilled water was heated by the recycling water in a water bath. For producing water vapor concentration of about 10%, the temperature of the water vapor was controlled by controlling the temperature of the water bath. The carrying gas (Ar)? flow rate was set to be 0.021 mm3/min. After the furnace reached the desired temperature and the gas flow was stabilized, the specimen was put in the Al2O3 tube, and then the Al2O3 tube was put in the electric furnace. The cyclic oxidation test was conducted at 600, 650 and 700 ℃, respectively, for 1 h and then cooled down for 15 min in the Al2O3 tube. The above processes were defined as one cycle. An analytical balance with a sensitivity of 1×10-5 g was used to measure the mass of the specimen at intervals during the test. Thus, the mass change of the specimen with cyclic times was determined. After cyclic oxidation tests the microstructures of corroded specimens were investigated by a scanning electron microscope (SEM) equipped with an energy dispersive spectroscope (EDS). The phase compositions of the corroded specimens were determined by X-ray diffractometry (XRD).
3 Results and discussion
3.1 Cyclic oxidation kinetics and corrosion products
Fig.1 shows the mass change per unit area of 9Cr-1Mo steel during cyclic oxidation in 10%H2O+ 90%Ar atmosphere at 600, 650, and 700 ℃. When 9Cr-1Mo steel is oxidized at 600 ℃, the oxidation behavior exhibits three-stage oxidation kinetics. At the first stage (t<150 h), the sample shows a very slow mass gain rate. After this stage, a significantly fast mass gain rate is observed (150 h<t<220 h), then followed by a slow mass gain rate again (t>220 h). It is noteworthy that a mass loss is observed at the third oxidation stage, which suggests that the oxide scale is spalled from the
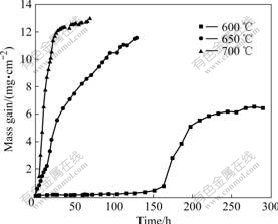
Fig.1 Mass change during cyclic oxidation in 10%H2O+90%Ar at mosphere at various temperatures
substrate. When 9Cr-1Mo steel is oxidized at 650 ℃, a continuous and fast mass gain rate is observed during the cyclic oxidation. Meanwhile, a mass loss is observed after 104 cycles. At 700 ℃ the oxidation rate increases obviously at the initial oxidation stage, and then slows down when mass loss occurs.
Fig.2 shows XRD patterns of the samples after cyclic oxidation at 600 ℃ for 290 cycles, 650 ℃ for 130 cycles and 700 ℃ for 69 cycles. XRD analysis reveals that the main crystalline phase formed on 9Cr-1Mo steel is Fe2O3.
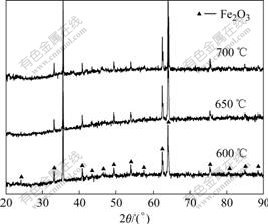
Fig.2 XRD patterns of 9Cr-1Mo steel after cyclic oxidation at various temperatures
Fig.3 shows the surface microstructures of 9Cr-1Mo steel after oxidation at 600 ℃ for 290 cycles, 650 ℃ for 130 cycles and 700 ℃ for 69 cycles. It is seen from Fig.3 that some micro-cracks form on the sample surface (marked as R), and the oxide scales are spalled locally (marked as S) on the sample surface.
Figs.4(a), (b) and (c) show the cross section morphologies of samples cyclically oxidized at 600, 650 and 700 ℃, respectively. In Fig.4 SEM observations reveal that the formed oxide scales have a duplex microstructure. In the outer layer the molar ratio of Fe to O is nearly 2:3. Combining the results of XRD and EDS analysis, we conclude that the outer layer is recognized as Fe2O3. The inner layer is recognized as (Fe, Cr)3O4 by EDS results. The thickness of the outer Fe2O3 layer is larger than 20 μm, which exceeds the detectable depth of XRD. Therefore, the oxide phases in the inner layer cannot be detected by XRD. At the oxide layer/substrate interface, a very thin inner oxidation layer is observed. It is noteworthy that in Fig.4 there exist some cracks in the oxide scales. These cracks penetrate the whole inner layer and outer layer and end at the inner oxide layer/substrate interface.
It is reported that even there exists a small amount of water vapor in the environment, the oxidation rate of metals or alloys would be accelerated significantly [11].
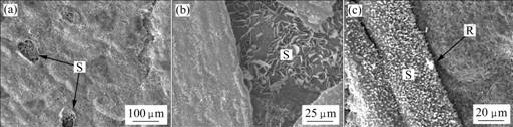
Fig.3 Surface morphologies of oxide scales formed on 9Cr-1Mo steel after cyclic oxidation in 10%H2O+90%Ar atmosphere at various temperatures: (a) 600 ℃ for 290 cycles; (b) 650 ℃ for 130 cycles; (c) 700 ℃ for 69 cycles
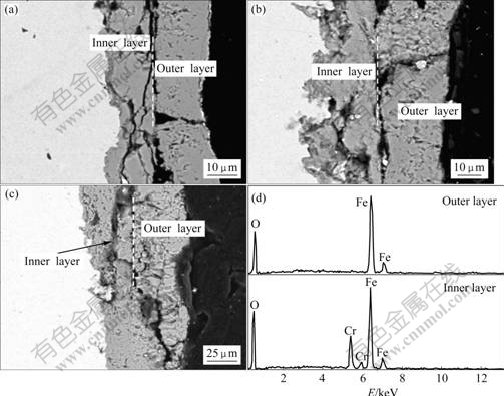
Fig.4 Cross section morphologies and EDS X-ray spectrum of 9Cr-1Mo steel after cyclic oxidation in 10%H2O+90%Ar atmosphere at various temperatures: (a) 600 ℃; (b) 650 ℃; (c) 700 ℃; (d) EDS
A number of studies demonstrated that hydrogen might dissolve in metal oxides at high temperatures and significantly affect their defect structures and defect-dependent properties. Some oxides may even become hydrogen ion conductors under proper conditions. At high temperatures, hydrogen dissolves in metal oxides as protons, and the dissolved protons are associated with an oxide ion, and thus convert an oxide ion to a hydroxide ion (having a positive effective charge) on a normal oxygen site. This dissolution may be expressed as follows when it takes place from ambient H2(g) [12]
(1)
where a defect is denoted by the major symbol and the site occupied is denoted by a subscript; a positive effective charge is indicated by a superior dot, and a negative effective charge by a superior prime; subscript “i” denotes an interstitial position.
In this experiment, water vapor exists in the environment. Under this condition, the following reaction equilibrium can be established:
(g) (2)
Combining reactions (1) and (2), the following reaction equilibrium can be obtained:
(3)
The reaction equilibrium constant can be obtained as follows:
(4)
where K is the reaction equilibrium constant, and p is the partial pressure of gases.
During the experiment, only water vapor and Ar were introduced, and the water vapor pressure was set as constant. According to Eqn.(4), oxygen pressure is lower; the concentration of protons becomes higher. Therefore, more hydrogen defects form at native point defect in the oxide layer, which makes ion diffusion accelerate in the oxide layer. Under this condition, the oxidation rate of the substrate steel is accelerated. Therefore, during the cyclic oxidation, 9Cr-1Mo steel exhibits a fast oxidation rate in water vapor environment.
As mentioned above, when 9Cr-1Mo steel is cyclically oxidized at 600 ℃, a three-stage oxidation kinetic curves are observed. Especially, the oxidation rate increases sharply during 151-219 cycles. This phenomenon is related to the diffusion rates of protective scale forming elements, such as Cr, in the steel at high temperature [10]. At the beginning oxidation stage, Cr favors to form (Fe, Cr)3O4, and the formation of Cr-rich spinel bands in the inner part of oxide scale probably suppresses outward diffusion of cations. Thus, the protective nature of the scale is improved, and a slight mass gain is observed at this oxidation stage. However, the content of Cr is not high enough to form a complete and compact Cr2O3 layer on the sample surface. Furthermore, during cyclic oxidation Cr depletes in the substrate near the oxide/substrate interface. Under this condition, Fe ions diffuse outwardly on a large scale and are oxidized. Therefore, the sample exhibits a fast oxidation rate. After the second oxidation stage, Fe ion diffusion and oxidation lead to Fe depletion, which forms Cr2O3-rich oxide layer and suppresses outward diffusion of cations. Therefore, the oxidation rate decreases at this stage again. Actually, similar phenomenon is observed on 9Cr-1Mo steel oxidized at high temperatures [13].
3.2 Cracks mechanism of oxide scale
In this test, the spallation of oxide scale is observed during cyclic oxidation of 9Cr-1Mo steel at 600, 650 and 700 ℃, which indicates that stress is generated in the oxide layer during cyclic oxidation. The stress may cause cracking and rupture of the scales, and this, in turn, leads to the loss of protective properties and fast degradation of substrate. A number of stress sources may arise in oxidation reactions depending upon the reaction mechanism. These may include effects of oxygen dissolution in metals, volume ratios of oxide to metal, epitaxial relationships, growth mechanisms of scales, and specimen geometry. During cyclic oxidation the growth and thermal stresses are of great importance considering the generation of cracks in the oxide scale or spallation of the scale from the sample surface. Generally, growth stress results from the growth of the oxide layer when the substrate is oxidized isothermally. Thermal stress generates from the mismatch of thermal expansion coefficients between the oxide layer and the substrate when the environment temperature changes [14]. The scales fail by cracking when the stress generated in the oxide scale is high enough. Some cracks may be developed in the scale or at the oxide/substrate interface. Further spreading of these cracks may lead to scale spallation. Because the cyclic oxidation is conducted between high temperature heating and cooling to room temperature, the thermal stress has an important effect on the oxide cracking. During the heating and cooling, the thermal stress generates rapidly, which may cause micro-crack formation in the oxide scale. Because a duplex oxide scale forms on the 9Cr-1Mo steel surface after cyclic oxidation, a quantitative equation is adopted to evaluate the stress in the oxide scale during heating stage [14].
(5)
(6)
(7)
where σ is the thermal stress, x represents the thickness of oxide layer and substrate, E is the elastic modulus, α is the linear expansion coefficient, Dt=t-t0 is the temperature difference (t0 is the room temperature, t is the oxidation temperature, and t>t0), m is Poisson ratio (μ≈0.3), and subscripts 1, 2 and 3 indicate outer oxide layer, inner oxide layer, and substrate, respectively.
The data of various parameters for Fe3O4, Cr2O3, Fe2O3 and Fe, which are needed for calculation, are listed in Table 1. Here we only discussed the cyclic oxidation at 600 ℃. Because the inner oxide layer consists of the
Table 1 Parameters of oxide layer and substrate for model
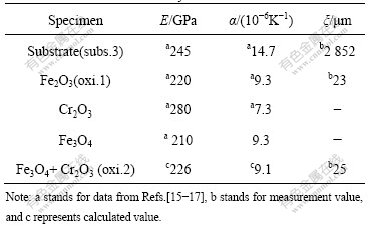
mixture of (Fe, Cr)3O4, in order to simplify the calculation, we assumed this layer as a composite. Therefore, the average values of α2 and E2 can be evaluated according to the following equations:
(8)
(9)
(10)
where Ki is the volume modulus of component i, Vi is the volume fraction of component i, and mi is the Poisson ratio of component i.
Based on the EDS analysis of cross section for the oxidized specimen, the volume fractions of Cr2O3 and Fe3O4 in the inner oxide layer are estimated to be 15% and 85%, respectively. According to Eqns.(8)-(10) and data in Table 1, α2 and E2 can be calculated. The calculated results are also listed in Table 1, as shown as the data marked with superscript “c”. The thickness of duplex oxide layer and substrate are measured through cross section of the specimen. Substituting the values concerned into Eqns.(5)-(7), the thermal stresses in duplex oxide layers and substrate are obtained when the temperature increases from room temperature to 600 ℃ (Dt=575 ℃): σ1=184 MPa, σ2 = 498 MPa, σ3 =-12 MPa. If σ<0, the stress is compressive; if σ>0, the stress is tensile. Therefore, the tensile thermal stress exists in two oxide sub-layers, and the compressive stress exists in the substrate during heating stage if we assume that the oxide scale is integrity and there is no crack during cyclic oxidation. It can also be seen that the inner layer endures higher tensile stress than the outer layer. According to data in Ref.[18], the tensile strength of Fe2O3 and Fe3O4 is less than 50 MPa. Therefore, it is reasonable to deduce that the thermal stress is high enough to cause the duplex oxide layer to crack when the temperature increases from room temperature to 600 ℃. With the increase of oxidation temperature, the tensile stress also increases during the heating stage. Therefore, many cracks are observed in the oxide layer after cyclic oxidation at 650 and 700 ℃. According to Eqns.(5)-(7), the thermal stress is only related to the thickness of duplex oxide layers and substrate if oxidation temperature is constant. In order to understand the dependence of the thermal stress on the oxide thickness, Eqns.(5)-(7) can be rewritten as follows:
(11)
(12)
(13)
For Eqns.(11)-(13), the stresses in duplex oxide layer are only related to x1/x3 and x2/x3. When the samples are oxidized at 600, 650 and 700 ℃, x1/x3 equals 1.10/1.00 1.08/1.00 and 1.11/1.00 respectively, which indicates that the thickness ratio of the outer oxide layer to the inner oxide layer approximately equals a constant. If we assume that x1/x2 is constant, it can be known from Eqns.(11) and (12) that, the stresses in duplex oxide layer and substrate only vary with x1/x3 or x2/x3 because Ei, σi and Dt are constant. According to Eqns.(11)-(13), the stress in the oxide layer and substrate can be calculated with different ratios of x1 to x3. Fig.5 shows the relationship between the calculated thermal stress at room temperature with x1/x3. In Fig.5, with increasing cycle times, the thickness of the duplex oxide layer increases, and the thermal stress decreases. Therefore, if the oxide is integrity and no cracks are formed, the tensile stress is larger at the initial oxidation stage than that at the later oxidation stage. Under this condition, cracks form in the oxide layer during the heating stage even at the early oxidation stage.
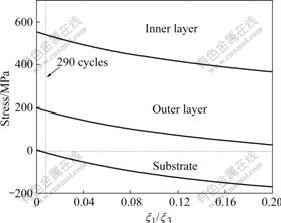
Fig.5 Relationship between thermal stress in duplex at room temperature and relative thickness of outer oxide layer (x1/x3)
4 Conclusions
(1) A three-stage oxidation kinetics is observed when 9Cr-1Mo steel is cyclically oxidized in 10%H2O+90%Ar atmosphere at 600 ℃ for 290 h. At the initial oxidation stage, the oxidation rate is very slow, and then the breakaway oxidation occurs, which is related to the low Cr content in the substrate. However, during cyclic oxidation at 650 and 700 ℃, even at the initial oxidation stage, the samples show a fast oxidation rate.
(2) A duplex oxide layer with an outer layer of Fe2O3 and an inner layer of Fe3O4 and Cr2O3 is formed and some cracks penetrate the duplex layer.
(3) The calculated results show that the tensile stress exists in the duplex oxide during the cyclic oxidation. During the cyclic oxidation the tensile stress exceeds the tensile strength of oxide scale, and cracks are generated in the oxide layer. The tensile stress in the oxide layer is higher at the early oxidation stage than that at the later oxidation during the heating stage.
Acknowledgement
The authors express their gratitude to Dr. LI Mei-shuan from Institute of Metal Research, Chinese Academy of Sciences, for his suggestions during the experiment.
References
[1] BLUM R, VANSTONE R W. Materials development for boilers and steam turbines operating at 700 ℃ [C]// Proceedings of the sixth International Charles Parsons Turbine Conference. Dublin, 2003: 489-510.
[2] VISWANATHAN R, HENRY J F, TANZOSH J, STANKO G, SHINGLEDECKER J, VITALIS B. US program on materials technology for USC power plants [C]// Proceedings of the fourth International Conference on Advances in Materials Technology for Fossil Power Plants. Hilton Head Island, South Carolina, 2004: 3-19.
[3] ABE F, OKADA H, WANIKAWA S, TABUCHI M, ITAGAKI T, KIMURA K. Guiding principles for development of advanced ferritic steels for 650 ℃ USC boilers [C]// Proceedings of the Seventh Liege Conference on Materials for Advanced Power Engineering 2002. Liege, Belgium, 2002: 1397-1406.
[4] ZHANG Ping, XU Jian-guang, LI Ning. Fatigue properties analysis of cracked rock based on fracture evolution process [J]. Journal of Central South University of Technology, 2008, 15(1): 95-99.
[5] ZHU Yuan-zhi, YIN Zhi-min, ZENG Yu, HUANG Ji-wu, LI Xue-qian. Effects of heat treatment on microstructure and mechanical properties of Fe-Co-Ni-Cr-Mo-C alloy [J]. Journal of Central South University of Technology, 2004, 11(3): 229-236.
[6] SUNDARARAJAN T, KURODA S, KAWAKITA J, SEAL S. High temperature corrosion of nanoceria coated 9Cr-1Mo ferritic steel in air and steam [J]. Surface and Coatings Technology, 2006, 201: 2124-2130.
[7] CHEN Y, SRIDHARAN K, ALLEN T. Corrosion behavior of ferritic-martensitic steel 9Cr-1Mo in supercritical water [J]. Corrosion Science, 2006, 48: 2843-2854.
[8] YI Y S, LEE B, KIM S, JIANG J S. Corrosion and corrosion fatigue behaviors of 9Cr steel in a supercritical water condition [J]. Materials Science and Engineering A, 2006, A429: 161-168.
[9] ENNIS P J, QUADAKKERS W J. Implications of steam oxidation for the service life of high-strength martensitic steel components in high-temperature plant [J]. International Journal of Pressure Vessels and Piping, 2007, 84: 82-87.
[10] ENNIS P J, QUADAKKERS W J. Mechanisms of steam oxidation in high strength martensitic steels [J]. International Journal of Pressure Vessels and Piping, 2007, 84: 75-81.
[11] SHEN Jia-nian, ZHOU Long-jian, LI Tie-fan, High temperature oxidation of Fe-Cr alloys in wet oxygen [J]. Oxidation of Metals, 1997, 48: 347-356.
[12] LI Tie-fan. High temperature oxidation and hot corrosion of metals [M]. Beijing: Chemical Industry Press, 2003. (in Chinese)
[13] KHANNA A S, RODRIGUEZ P, GNANAMOORTHY J B. Oxidation kinetics, breakaway oxidation, and inversion phenomenon in 9Cr-1Mo steels [J]. Oxidation of Metals, 1989, 26(3/4): 171-200.
[14] SUN Z, ZHOU Y, LI M. Cyclic oxidation behavior of Ti3SiC2-base material at 1 100 ℃ [J]. Oxidation of Metals, 2002, 57(5/6): 379-394.
[15] LI Mei-shuan. High temperature corrosion of metals [M]. Beijing: Metallurgical Industry Press, 2001. (in Chinese)
[16] SAMSONOV G V. The oxide handbook [M]. New York: IFI/Plenum Data Company. 1982.
[17] KOFSTAD P. High temperature corrosion [M]. New York: Elsevier Applied Science, 1988.
[18] HIDAKA Y, ANRAKU T, OTSUKA N. Deformation of iron oxides upon tensile tests at 600-1 250 ℃ [J]. Oxidation of Metals, 2003, 59(1/2): 469-485.
(Edited by CHEN Wei-ping)
Foundation item: Project(2006-8) supported by the Huadian International Corporation Limited
Received date: 2008-09-20; Accepted date: 2008-11-10
Corresponding author: ZHAO Guo-qun, Professor, PhD; Tel: +86-531-88393238; E-mail: zhaogq@sdu.edu.cn