- Abstract:
- 1 Introduction▲
- 2 Experimental▲
- 3 Results and discussion▲
- 4 Conclusions▲
- References
- Figure
- Fig.1 Calcium conversion (η) vs sulfation time at SO2 volume fraction 0.2%: (a) In O2/CO2 atmosphere; (b) In air
- Fig.2 Effect of SO2 concentration on η at 900 ℃: (a) In O2/CO2 atmosphere; (b) In air
- Fig.3 Effect of SO2 concentration on η at 1 100 ℃: (a) In O2/CO2 atmosphere; (b) In air
- Fig.4 XRD patterns of sulfated products obtained in air at 900 ℃ for different reaction times: (a) 5 min; (b) 20 min; (c) 40 min
- Fig.5 BET specific surface area of sulfated product vs temperature in different atmospheres
J. Cent. South Univ. Technol. (2009) 16: 0845-0850
DOI: 10.1007/s11771-009-0140-1
Temperature dependence on reaction of CaCO3 and
SO2 in O2/CO2 coal combustion
WANG Hong(王 宏)1, 2, XU Hui-bi(徐辉碧)2, ZHENG Chu-guang(郑楚光)1, QIU Jian-rong(邱建荣)1
(1. National Laboratory of Coal Combustion, Huazhong University of Science and Technology,
Wuhan 430074, China;
2. School of Chemistry and Chemical Engineering, Huazhong University of Science and Technology,
Wuhan 430074, China)
Abstract:
The temperature dependence on the reaction of desulfurization reagent CaCO3 and SO2 in O2/CO2 coal combustion was investigated by thermogravimetric analysis, X-ray diffraction measurement and pore structure analysis. The results show that the conversion of the reaction of CaCO3 and SO2 in air is higher at 500-1 100 ℃ and lower at 1 200 ℃ compared with that in O2/CO2 atmosphere. The conversion can be increased by increasing the concentration of SO2, which causes the inhibition of CaSO4 decomposition and shifting of the reaction equilibrium toward the products. XRD analysis of the product shows that the reaction mechanism of CaCO3 and SO2 differs with temperature in O2/CO2 atmosphere, i.e. CaCO3 directly reacts with SO2 at 500 ℃ and CaO from CaCO3 decomposition reacts with SO2 at 1 000 ℃. The pore analysis of the products indicates that the maximum specific surface area of the products accounts for the highest conversion at 1 100 ℃ in O2/CO2 atmosphere. The results reveal that the effect of the atmosphere on the conversion is temperature dependence.
Key words:
CaCO3; SO2; O2/CO2 coal combustion; temperature dependence;
1 Introduction
Extensive research has been devoted recently to CO2-capture techniques because of growing concerns with respect to greenhouse gas emissions [1]. CO2 emission from fossil fuel combustion is a significant source of global warming and climate change. Clean coal combustion technologies have been developed toward easy CO2 recovery, low NOx emission and high desulfurization efficiency [2-6]. O2/CO2 coal combustion is one of these new technologies associated with reduced CO2 emission to the atmosphere [7-8].
Ca-based sorbent such as CaCO3 is used as sulfur absorbent in conventional combustion atmosphere [9-10]. The reaction of desulfurization reagent CaCO3 and SO2 has been a subject of increasing attention in O2/CO2 coal combustion [11-12]. LIU et al [13] reported sulfation behavior of limestone at high CO2 concentrations in O2/CO2 coal combustion. They found that sintering was much mitigated during direct sulfation of limestone. The rate of direct sulfation does not decrease as much as the CaO-SO2 sulfation. CHEN et al [14] investigated the calcination and sintering characteristics of limestone in O2/CO2 atmosphere. The results showed that the specific pore volume and specific surface area of CaO calcined in O2/CO2 atmosphere were less than those of CaO calcined in air at the same temperature. FUERTES et al [15] studied the direct sulfation behavior of dolomite at a high CO2 partial pressure and temperatures ranging from 650 to 875 ℃. The results suggested that solid diffusion was the control process in direct sulfation of dolomite. However, most of these investigations were carried out by using thermogravimetric analysis (TGA) at temperatures below 1 000 ℃ [16-17].
In O2/CO2 coal combustion, the concentrations of CO2 and SO2 in the flue gas may be enriched up owing to the gas recirculation. At high CO2 and SO2 concentrations, and high calcium conversion, the influence of high SO2 concentration on the calcium conversion and the reaction mechanism of desulfurization reagent CaCO3 and SO2 are not clear at temperatures ranging from 500 to 1 200 ℃. Therefore, it is necessary to study the calcium conversion and mechanism in O2/CO2 coal combustion at high CO2 concentration. However, few researches have been reported about the composition of sulfated products and the desulfurization mechanism in the O2/CO2 coal combustion with high concentration of CO2.In this work, the calcium conversions in O2/CO2 coal combustion at 500-1 200 ℃ were investigated and the effect of concentration of SO2 on calcium conversion was also studied. The reaction mechanism of desulfurization reagents CaCO3 and SO2 in O2/CO2 coal combustion was investigated by thermogravimetric analysis, X-ray diffraction measurement and pore structure analysis.
2 Experimental
2.1 Materials
O2, CO2, N2 and SO2, each with mass fraction of 99.9%, were purchased from Wuhan Gas Co. Ltd, Wuhan, China. 99.9% (mass fraction) CaCO3 was purchased from Sinopharm Chemical Reagent Co. Ltd, Beijing, China.
2.2 Experimental setup
Experiments were performed in a fixed-bed quartz reactor placed in a tubular oven. The reactor was 650 mm in length. A sintered quartz filter of 20 mm in diameter was placed at the middle of the reactor to support the sample powder. The temperature in the reactor was measured by a thermocouple placed immediately under the sample. Premixed gases were introduced into the reactor from an inlet above the reactor, and the gas flow rates were regulated by mass flow controllers. The concentration of SO2 in the premixed gases was measured by a SO2 sensor (Z-1300, ESC).
2.3 Experimental procedure
In the experiments, two kinds of reactive atmospheres were utilized: (1) 21.0% O2/79.0% CO2 with trace SO2 (designated as O2/CO2 atmosphere) and (2) 21.0% O2/79.0% N2 with trace SO2 (designated as air atmosphere). The experiments were carried out under reactant gas conditions. In all cases, isothermal conditions in the quartz reactor were first established and the desired reactant gas conditions were then achieved. For each run, 0.5 g of the CaCO3 powder was rapidly loaded from a sample feeder onto the sintered quartz filter in the reactor. After a specified time period was over, the sample from the fixed bed reactor was allowed to cool down under N2, and subsequently placed in a desiccator for characterization and analysis. The content of SO42- in the product was determined by the gravimetric method, and the calcium conversion (η) was calculated by the following equation:
×100% (1)
where m(CaSO4) is the mass of CaSO4 in the product, and m(CaCO3) is the initial mass of CaCO3.
2.4 Characterization of reaction product
Thermogravimetric analysis was performed with a TG/DSC analyzer (STA 449C, Netzsch). In the TG analysis, the temperature was ramped from room temperature to 1 200 ℃ at a rate of 20 ℃/min and then held at 1 200 ℃ for 10 min under a steady flow of mixed gases of 50 mL/min. The mixed gases were of 21.0% O2/ 79.0% CO2 or 21.0% O2/79.0% N2, which were similar to those described in section 2.3, but without SO2. The starting decomposition temperature was defined as the temperature when the thermogravimetric curve started to deviate from the baseline. The end decomposition temperature was defined as the temperature when the maximum mass loss occurred. The sulfated products were characterized by X-ray diffractometry (XRD, D/max-Ⅲ B, Rigaku) using an X-ray diffractometer with Cu Kα radiation (λ=0.154 06 nm) and a Ni ray filter. The tube current and the voltage were set at 30 mA and 30 kV, respectively. The peak positions of samples were compared with JCPDS files. BET surface areas of sulfated products were measured with N2 adsorption analysis by using a specific surface area analyzer (ASAP 2020, Micromeritics).
3 Results and discussion
3.1 Effect of reactive atmosphere on calcium conversion (η)
In conventional air combustion, the reaction of CaCO3 and SO2 occurs as follows:
CaCO3→CaO+CO2 (Decomposition) (2)
CaO+SO2+1/2O2→CaSO4 (Sulfation) (3)
The reaction of CaCO3 and SO2 is a solid-gas reaction. In general, the reaction rate and η are affected by temperature and atmosphere. Fig.1 shows calcium conversion vs sulfation time at varied temperatures in different atmospheres. Obviously, η increases with the increase of reaction time at a given temperature for both reactive atmospheres. The change of η between 500 and 900 ℃ is faster than that between 900 and 1 100 ℃. η, however, decreases when the temperature is higher than 1 100 ℃.
It is found from Fig.1 that the values of η in air are much higher than those in O2/CO2 atmosphere when the temperature is lower than 900 ℃. For instance, at 900 ℃ the values of η in air are 23.1% and 26.9% at reaction time of 30 and 40 min, respectively, after the reaction started; whereas the values of η at the same time are only 9.6% and 16.5% in O2/CO2 atmosphere, respectively. A possible explanation involves the competitive reaction of CO2 and CaO in O2/CO2 atmosphere. In addition, the
Fig.1 Calcium conversion (η) vs sulfation time at SO2 volume fraction 0.2%: (a) In O2/CO2 atmosphere; (b) In air
amount of CaO decomposed from CaCO3 in O2/CO2 atmosphere is less than that in air because of the inhibition of the decomposition of CaCO3 by higher concentrations of CO2. When the temperature is increased to 1 100 ℃, the effect of both atmospheres on η becomes weaker. For instance, the values of η are 25.8% and 32.4% in air and 23.3% and 29.1% in O2/CO2 atmosphere at reaction time of 30 and 40 min, respectively. More CaO from CaCO3 decomposition at this temperature is produced than that at 900 ℃. At 1 200 ℃, η in O2/CO2 atmosphere is higher than that in air, which may be related to less sintering of CaO in O2/CO2 atmosphere. This indicates that O2/CO2 atmosphere is beneficial to the removal of SO2 at high temperatures.
3.2 Effect of SO2 concentration on calcium conversion
In comparison with conventional air combustion, the O2/CO2 coal combustion features recycling of flue gas, resulting in high concentrations of SO2 and CO2 in the combustion atmosphere. Generally speaking, increasing SO2 concentration causes the equilibrium of sulfation reaction to shift toward the products, leading to a higher η. Figs.2 and 3 show the effect of SO2 concentration on η at 900 ℃ and 1 100 ℃, respectively.
Fig.2 Effect of SO2 concentration on η at 900 ℃: (a) In O2/CO2 atmosphere; (b) In air
As shown in Figs.2 and 3, η increases with increasing SO2 concentration at either 900 ℃ or 1 100 ℃. As mentioned above, high SO2 concentrations will be better for the equilibrium of sulfation reaction to shift toward the products. A comparison between Figs.3(a) and (b) shows that the increase of η in O2/CO2 atmosphere is faster than that in air during the reaction time period of 30-40 min. This can be attributed to the inhibition of the decomposition of CaSO4 [11]. This result further demonstrates that high temperatures are beneficial to the removal of SO2 in O2/CO2 atmosphere.
3.3 Decomposition processes of CaCO3 in both atmospheres
The decomposition of CaCO3 was strongly affected by the concentration of CO2 and temperature [14]. The decomposition process of CaCO3 in both atmospheres without SO2 was investigated by TGA in order to determine the effect of the reactive atmosphere on it. The results are listed in Table 1.
As shown in Table 1, the mass losses of the samples are rather close to each other in both atmospheres. However, the decomposition of CaCO3 starts at 884 ℃ in O2/CO2 atmosphere, whereas the decomposition takes
Fig.3 Effect of SO2 concentration on η at 1 100 ℃: (a) In O2/CO2 atmosphere; (b) In air
Table 1 Effects of atmosphere on decomposition of CaCO3
place at 758 ℃ in air. The starting and end temperatures of the decomposition in O2/CO2 atmosphere are 126 and 55 ℃ higher than those in air, respectively. This is likely due to the constraint or the inhibition of decomposition of CaCO3 at high concentration of CO2.
3.4 XRD analysis of sulfated products
Possible sulfated products include CaCO3, CaO and CaSO4 according to reactions (2) and (3). An XRD technique was used to characterize their phase compositions to clarify the reaction mechanism of CaCO3 and SO2 in O2/CO2 atmosphere and in air. Proportions of phase composition were estimated from relative peak intensities. Fig.4 shows the XRD patterns of sulfated products at 900 ℃ for different reaction times in air.
Fig.4 XRD patterns of sulfated products obtained in air at 900 ℃ for different reaction times: (a) 5 min; (b) 20 min; (c) 40 min
According to the JCPDS files, the major diffraction peaks of sulfated products CaCO3, CaO and CaSO4 appear at 2θ of 29.4?, 37.4? and 25.5?, respectively. Obviously, the sulfated products contain a significant amount of CaCO3 and small amount of CaO and CaSO4 after 5 min of reaction time. When the reaction time is increased to 20 min, the intensity of the major peak of CaCO3 is smaller than that of either major peak of CaSO4 or CaO. When the reaction time is increased to 40 min, the intensity of the major peak of CaCO3 is very low and the intensities of the major peaks of CaSO4 and CaO become very high. The phase compositions of sulfated products in different atmospheres for varied reaction times are given in Table 2.
Table 2 shows that the phase compositions of sulfated products in two kinds of atmospheres are CaCO3 and CaSO3 at 500 ℃. At this temperature, the decomposition of CaCO3 does not occur. This is in concord with the TGA result. CaSO3 is the direct sulfation product of CaCO3 and SO2, as shown in Eq.(4), and this compound is too stable to oxidize to CaSO4 at low temperatures.
CaCO3+SO2→CaSO3+CO2 (4)
In air, the phase composition of sulfation products at 700 ℃ is dependent on the reaction time. The phases are CaCO3, CaSO3 and CaSO4 after 5 min of reaction. As the reaction time increases, CaSO3 phase disappears due to the oxidation to CaSO4. CaO is a absent most likely
Table 2 Phase compositions of sulfated products determined by XRD
because CaCO3 does not decompose at 700 ℃. This result is also in accordance with that of TGA.
In O2/CO2 atmosphere, CaCO3 and CaSO3 phases are found at 700 ℃ after 5 min of reaction. This result is quite different from that in air. When the reaction time is increased to 20 min, CaSO4 phase is produced. The phase composition is the same as that in air after 40 min of reaction. The results indicate that the effect of atmosphere on the phase composition of sulfation products is reaction time dependent. The sulfation in both atmospheres can be described as follows:
CaSO3+1/2O2→CaSO4 (5)
According to Table 1, the decomposition of CaCO3 starts at 758 ℃ in air. Therefore, CaO described in Eq.(2) is found in all samples at 900 ℃. After 40 min of reaction, only CaSO4 and CaO are found and the proportion of CaO is more than that of CaSO4, suggesting indirect sulfation of CaCO3, as shown in Eq.(3).
Likewise, the decomposition of CaCO3 starts at 884 ℃ in O2/CO2 atmosphere, as shown in Table 1. When the reaction time is increased from 5 to 40 min, the phase compositions of the sulfation products are CaSO4, CaO and CaCO3 at 900 ℃. In a high CO2 concentration atmosphere, CaO can be consumed in two ways: (1) sulfation reaction of CaO and SO2, which forms CaSO4; and (2) recarbonation reaction of CaO and CO2, which forms CaCO3. If the decomposition rate of CaCO3 to produce CaO is equal to the consumption rate of CaO, sintering of CaO can be avoided. This can lead to an optimum η. ANTHONY and GRANATSTEIN [18] reported that the recarbonation reaction is faster than sulfation, causing excessive CaCO3 in the sulfation product. Therefore, indirect and direct sulfation reactions are simultaneously performed to form CaSO4. The sulfation mechanism can be described by the combination of Eqs.(2)-(5).
The phase compositions of the sulfation product are CaSO4 and CaO in both atmospheres at temperatures ranging from 1 100 to 1 200 ℃. The major phase is CaO, suggesting a typical indirect sulfation process. The sulfation mechanism can be described by the combination of Eqs.(2) and (3) in this temperature range.
3.5 Pore structure analysis of sulfated products
It is known that the pore structure of sulfated products plays an important role in the desulfurization reaction. The pore structure is greatly affected by the reaction temperature and atmosphere. The specific surface areas of sulfated products were measured by the N2 adsorption method. Fig.5 shows the plots of BET specific surface area of sulfated products vs reaction temperature in both atmospheres after 20 min of reaction. A maximum BET specific surface area is found at 900 ℃ in air, whereas the surface area is almost independent of temperature in O2/ CO2 atmosphere.
As seen from Fig.5, the BET specific surface areas of sulfated products in both atmospheres are almost the same in the temperature range from 500 to 700 ℃. This can be attributed to the fact that the decomposition of CaCO3 does not occur at these temperatures. When the temperature is increased to 900 ℃, a distinct difference is found between the atmospheres employed. According to the result of TGA (shown in Table 1), the decomposition of CaCO3 is almost completed at 900 ℃ in air, but not in O2/CO2 atmosphere. In this case, the decomposed CaCO3 is a dominant contributor to the BET specific surface area of sulfated products. As the temperature is increased to 1 100 ℃ and above, the BET specific surface area of sulfated products in air decreases to the same level as that in O2/CO2 atmosphere. This result can be attributed to considerable sintering of CaO and the pore plugging of sulfated products. This suggests that the decrease of surface area of reactant accounts for the lower calcium conversion at high temperatures in air. By contrast, the BET specific surface area of sulfated products is less affected by reaction temperature in O2/CO2 atmosphere, and this further confirms that high temperature is beneficial to the capture of SO2 in O2/CO2 atmosphere.
Fig.5 BET specific surface area of sulfated product vs temperature in different atmospheres
4 Conclusions
(1) Temperature has a great influence on the calcium conversion in air and in O2/CO2 atmosphere. The calcium conversion in air is higher than that in O2/CO2 atmosphere at temperatures ranging from 500 to 1 100 ℃, and it is higher in O2/CO2 atmosphere at 1 200 ℃. The results show that high temperature is beneficial to the removal of SO2 in O2/ CO2 atmosphere.
(2) The calcium conversion increases with the increase of concentration of SO2 due to shifting of the reaction equilibrium and the inhibition of the decomposition of CaSO4.
(3) The reaction mechanism of desulfurization reagents CaCO3 and SO2 in O2/CO2 coal combustion dependents on the temperature in O2/CO2 atmosphere. It involves both direct and indirect sulfation reactions.
(4) The BET specific surface area of sulfated products is less affected by reaction temperature in O2/CO2 atmosphere, which is responsible for the high desulfurization efficiency in O2/CO2 coal combustion at high temperature.
References
[1] YANG H Q, XU Z H, FAN M H, GUPTA R, SLIMANE R B, BLAND A E, WRIGHT I. Progress in carbon dioxide separation and capture: A review [J]. Journal of Environmental Sciences, 2008, 20: 14-27.
[2] NAKAYAMA S, NOGUCHI Y, KIGA T, MIYAMAE S, MAEDA U, KAWAI M, TANAKA T. Pulverized coal combustion in O2/CO2 mixtures on a power plant for CO2 recovery [J]. Energy Conversion and Management, 1992, 33(5/8): 379-386.
[3] KIMURA N, OMATA K, KIGA T, TAKANO S, SHIKISIMA S. The characteristics of pulverized coal combustion in O2/CO2 mixtures for CO2 recovery [J]. Energy Conversion and Management, 1995, 36(6/9): 805-808.
[4] KIGA T, TAKANO S, KIMURA N, OMATA K, OKAWA M, MORI T, KATO M. Characteristic of pulverized coal combustion in the system of oxygen/recycled flue gas combustion [J]. Energy Conversion and Management, 1997, 38(S): 129-134.
[5] CROISET E, THAMBIMUTHU K V. NOx and SO2 emissions from O2/CO2 recycle combustion [J]. Fuel, 2001, 80: 2117-2121.
[6] LIU H, ZAUKANI R, GIBBS B M. Pulverized coal combustion in air and in O2/CO2 mixtures with NOx recycles [J]. Fuel, 2005, 84: 2109-2115
[7] ZHENG L, FURIMSKY E. Assessment of coal combustion in O2+CO2 by equilibrium calculations [J]. Fuel Processing Technology, 2003, 81: 23-34.
[8] LIU H, OKAZAKI K. Simultaneous easy recovery and drastic reduction of SOx and NOx in O2/CO2 coal combustion with heat recirculation [J]. Fuel, 2003, 82: 1427-1436.
[9] CHENG Jun, ZHOU Jun-hu, LIU Jian-hong, ZHOU Zhi-jun, HUANG Zhen-yu, CAO Xin-yu, ZHAO Xiang, CEN Ke-fa. Sulfur removal at high temperature during coal combustion in furnaces: A review [J]. Progress in Energy and Combustion Science, 2003, 29: 381-405.
[10] TARELHO L A C, MATOS M A A, PEREIRA F J M A. The influence of operational parameters on SO2 removal by limestone during fluidized bed coal combustion [J]. Fuel Processing Technology, 2005, 86: 1385-1401.
[11] FUERTES A B, FERMANDEZ M J. The effect of metallic salt additives on direct sulfation of calcium carbonate and on decomposition of sulfated samples [J]. Thermochimica Acta, 1996, 276(25): 257-269.
[12] MAO Yu-ru, FANG Meng-xiang, LUO Zhong-yang, WU Xue-cheng, CEN Ke-fa. Calcination and desulfurization of limestone under O2/CO2 atmosphere [J]. Journal of Fuel Chemistry and Technology, 2004, 32: 323-328. (in Chinese)
[13] LIU H, KATAGIRI S, KANEKO U, OKAZAKI K. Sulfation behavior of limestone under high CO2 concentration in O2/CO2 coal combustion [J]. Fuel, 2000, 79: 945-953.
[14] CHEN Chuan-min, ZHAO Chang-sui, LIANG Cai, PANG Ke-liang. Calcination and sintering characteristics of limestone under O2/CO2 combustion atmosphere [J]. Fuel Processing Technology, 2007, 88: 171-178.
[15] FUERTES A B, VELASCO G, FERNANDEZ M J, ALVAREZ T. Analysis of the direct sulfation of calcium carbonate [J]. Thermochimica Acta, 1994, 242(15): 161-172.
[16] QIU K R, LINDQVIST O. Direct sulfation of limestone at elevated pressures [J]. Chemical Engineering Science, 2000, 55(16): 3091-3100.
[17] ALVAREZ E, GONZALEZ J F. High pressure thermogravimetric analysis of the direct sulfation of Spanish calcium-based sorbents [J]. Fuel,1999, 78: 341-348.
[18] ANTHONY E J, GRANATSTEIN D L. Sulphation phenomena in fluidized bed combustion systems [J]. Progress in Energy and Combustion Science, 2001, 27: 215-236.
(Edited by CHEN Wei-ping)
Foundation item: Project(50525619) supported by the National Natural Science Foundation of China; Project(306012) supported by the Key Foundation of Ministry of Education of China
Received date: 2008-11-29; Accepted date: 2009-03-20
Corresponding author: WANG Hong, PhD; Tel: +86-27-61287832; E-mail: hongwzy@mail.hust.edu.cn
- Temperature dependence on reaction of CaCO3 andSO2 in O2/CO2 coal combustion
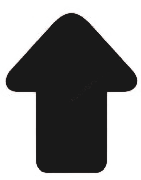