- Abstract:
- 1 Introduction▲
- 2 Confirmation of constit...▲
- 3 Static response of IPMC...▲
- 4 Conclusions▲
- References
- Figure
- Fig.1 Collected speckles data under load in experiment
- Fig.2 Stress—displacement curve in stretching orientation
- Fig.3 2D pixels distribution diagrams at different states of U field strain contour
- Fig.4 Strain fields in x orientation and y orientation
- Fig.5 Strain—stress curve in stretching orientation
- Fig.6 Relationship between lengthways strain and transverse strain
- Fig.7 Sketch map of cantilever setup
- Fig.8 Relationship curve of tip displacement and voltage
- Fig.9 Relationship curve between tip displacement and frequency
J. Cent. South Univ. Technol. (2008) 15: 387-391
DOI: 10.1007/s11771-008-0073-0
Constitutive relationship of ionic polymer-metal composite and static response character of its cantilever setup to voltage
TANG Hua-ping(唐华平)1, NIE Tuo(聂 拓)1, TANG Yun-jun(唐运军)1,
YIN Chen-feng(殷陈峰)1, TANG Chun-xi(唐春喜)1, WANG Qiao-yi(王桥医)2
(1. School of Mechanical and Electrical Engineering, Central South University, Changsha 410083, China;
2. School of Mechanical Engineering, Hunan University of Technology, Zhuzhou 412008, China)
Abstract:
As a new ionic polymer-metal composite(IPMC) for artificial muscle,the mechanical performance parameters and the relationship between the deformation and the electrical parameters of the IPMC were studied. With the digital speckle correlation method, the constitutive relationship of the IPMC was confirmed. With non-contact photography measurement, a cantilever setup was designed to confirm the relationship between the deformation of the IPMC film and the applied voltage. The relationship curve of tip displacement of the IPMC cantilever setup vs the voltage was achieved. The results indicate that the IPMC is isotropic, its elastic modulus is 232 MPa and Poisson ratio is 0.163. The curve achieved from the test of the tip displacement of the IPMC cantilever setup shows that the tip displacement reaches the maximum when the stimulated voltage is 5 V. And the tip displacement descends largely when the frequency of the applied voltage is between 30 mHz and 100 mHz.
Key words:
constitutive relationship; ionic polymer-metal composite(IPMC); cantilever setup; static response;
1 Introduction
As a new discovered material for artificial muscle, the ionic polymer-metal composite(IPMC) has been used to biomimetic robot, flexible and low damping machine arm and so on.
Since SHAHINPOOR discovered that the IPMC has a large displacement at low voltage in 1992, many scholars have made a lot study on it. SHAHINPOOR[1-7] made a series of studies and got the base voltage and frequency response character of the cantilever setup of the IPMC. KWANG and SHAHINPOOR[5] studied the open loop response character of the cantilever equipment. YAMAKITA et al[8] made a linear actuator with the IPMC and studied its displacement and movement character at different voltages, currents and frequencies. JUNG et al[9] studied the actuation character of the IPMC. OTERO and CORTES[10] brought forward one movement control algorithm for the artificial muscle actuator of IPMC. CURT and DONALD [11] studied the bandwidth character of frequency response of the IPMC artificial muscle actuator. Other scholars[12-15] also did the similar work.
When the new kind of biomimetic robot, actuator and other kinds of setups are developed, the kinetic parameters of the setup must be confirmed and the mechanical parameters of the IPMC must be analyzed. It is very difficult to obtain the mechanical characteristic parameter by using traditional mechanical experiment because it is difficult to fix sensor on IPMC. In this work, the kinetic parameters of the setup were obtained by collecting digital speckles of displacement, and the problem of the traditional mechanical experiment was successfully solved; the constitutive relationship and the isotropy of the IPMC were confirmed, and its elastic modulus and Poisson ratio were obtained.
2 Confirmation of constitutive relationship of IPMC
2.1 Constitutive relationship of elastic medium
The IPMC is a kind of super elastic material with strain energy. Adopting Green method, the constitutive relationship of elastic material can be described as follows:
(1)
(2)
where S, E, and
are Kirchhoff stress vector, the Green strain vector, the secant elastic constant vector and the tangent elastic constant vector, respectively.
For the material with an isotropy, there exists
(3)
where E0 is the elastic modulus and ν0 is the Poisson ratio; E0 and ν0 are the elastic constant. Under the condition of small deformation, there are E=E0 and ν=ν0.
2.2 Test experiment
The electrical testing machine AGS-10KNG (Japanese Shimadzu) and CCD digital speckle strain gauge were adopted in this test. The standard distance between samples was 40 mm and the stretching velocity was 3 mm/min. The dimensions of IPMC sample were 120 mm (length)×50 mm (width)×0.18 mm (thickness). In the test, the photography system was composed of a CCD, a photography card and a computer. The type of CCD was LCL-902 K and its ratio of signal to noise was larger than 50 dB; photography card (OK-M10) was bitmap photography card (768×576 pixel).
The software for dealing with the digital speckles was programmed with Visual C++6.0. The illuminative system was a fiber optic light of 100 W.
The collected speckles are shown in Fig.1. The displacement can be calculated from the pixel of the speckles picture. Deformation field can be obtained from the relative displacement in this orientation on the basis of the relative positional change between the two pictures[16]. Fig.2 shows the stress—displacement curve in the stretching orientation. Fig.3 shows the U field contour obtained by comparison with the collected picture when the load is zero. The abscissa in Fig.3 is the relative displacement under different pixel in x orientation (landscape orientation), and the ordinate is the relative displacement under different pixel in y orientation (lengthways). The curve in Fig.3 is the displacement of each point, from which the strain can be calculated. The strain fields in x orientation and y orientation are shown in Fig.4. Using the method of linear regression statistics, the elastic modulus and the Poisson ratio can be achieved. The strain—stress curve in stretching orientation is shown in Fig.5, from which it can be obtained that the elastic modulus is 0.232 GPa. Fig.6 shows the relationship between the lengthways and transverse strain, from which it is can be obtained that Poisson ratio is 0.163.
Fig.1 Collected speckles data under load in experiment
Fig.2 Stress—displacement curve in stretching orientation
Fig.3 2D pixels distribution diagrams at different states of U field strain contour
Fig.4 Strain fields in x orientation and y orientation
Fig.5 Strain—stress curve in stretching orientation
Fig.6 Relationship between lengthways strain and transverse strain
3 Static response of IPMC stimulated by voltage
3.1 Cantilever setup
The cantilever setup is shown in Fig.7. The tip displacement (S) is a function of the sample’s thickness (d), the cantilever length (d1), the grip length (d2), the amplitude (V) and the frequency (υ) of the input voltage. There is a relationship:
Fig.7 Sketch map of cantilever setup
S=f(V, υ, d, d1, d2) (4)
3.2 Relationship between tip displacement and amplitude of stimulating voltage
At the fixed setup and certain frequency, the tip displacement is just a function of the amplitude of stimulating voltage:
S=f(V) (5)
The data of the tip displacement and the amplitude of voltage obtained in the experiment are listed in Table 1.
Table 1 Tip displacement and amplitude of voltage (limitless periods)
To deal with the data, the polynomial least square fit method was adopted. From the results of linear least square fit to 10 times, it can be found the cubic polynomial least square fit method is the best. So we adopted the cubic polynomial least square fit method to fit the data. The fit curve is shown in Fig.8. The fit cubic polynomial is
S=0.016 2 V3-0.412 4V2+2.836 8V+2.419 3 (6)
From Fig.8, it can be seen that the tip displacement is the largest when the applied voltage is about 5 V.
3.3 Relationship between tip displacement and frequency of stimulating voltage
At the fixed setup and certain voltage, the tip
Fig.8 Relationship curve of tip displacement and voltage
displacement is just the function of the frequency of the stimulating voltage:
S=f(υ) (7)
The data of the tip displacement and the frequency of the applied voltage at 5 V obtained in the experiments are listed in Table 2.
Table 2 Tip displacement and voltage frequency at 5 V
To deal with the data, we adopted the cubic polynomial least square fit method again. The fitted curve is shown in Fig.9. The fitted cubic polynomial is
S=-2.946-6υ3+1.252-3υ2-0.178 3 υ+14.027 2 (8)
Fig.9 and Table 2 show that the tip displacement descends largely when the frequency of the applied voltage is between 30 mHz and 100 mHz, and the change of the displacement is small between 100 mHz and 200 mHz, which shows that the IPMC has a low pass chara-
Fig.9 Relationship curve between tip displacement and frequency
cter to the frequency of the driving voltage.
4 Conclusions
1) The mechanical characteristic parameter by fixing sensor on IPMC cannot be obtained by traditional mechanics experiment is solved, but can be obtained by collecting digital speckles of displacement with the digital speckle method.
2) According to the theory of constitutive relation- ship of elastic medium, the constitutive relationship of the material IPMC is confirmed by experiments. The IPMC has an isotropy, and its elastic modulus is about 232 MPa, and the Poisson ratio is 0.163.
3) The static response character of the IPMC is obtained by stimulating voltage on the cantilever setup. The tip displacement is the largest when the applied voltage is about 5 V, and the tip displacement will descend largely when the frequency of the applied voltage is between 30 mHz and 100 mHz. The relation- ship between the deformation of the IPMC film and the applied voltage indicates the IPMC is a kind of material with larger strain.
References
[1] SHAHINPOOR M. Microelectro-mechanics of ionic polymeric gels as artificial muscles for robotic applications [C]// Proceedings—IEEE International Conference on Robotics and Automation. Atlanta: IEEE, 1993: 380-385.
[2] SHAHINPOOR M. Continuum electro-mechanics of ionic polymeric gels as artificial muscles for robotic applications [J]. Smart Materials and Structures, 1994, 3(3): 367-372.
[3] SHAHINPOOR M, BAR-COHEN Y, XUE T, SIMPSON J O, SMITH J. Some experimental results on ion-exchange polymer-metal composites as bio-mimetic sensor and actuators [C]// Proceedings of SPIE—The International Society for Optical Engineering. Bellingham: The International Society for Optical Engineering, 1998: 251-267.
[4] SALEHPOOR K, SHAHINPOOR M, RAZANI A. Role of ion transport in actuation of ionic polymeric-platinum composite (IPMC) artificial muscles[C]// Proceedings of SPIE—The International Society for Optical Engineering. Bellingham: The International Society for Optical Engineering, 1998: 50-58.
[5] KWANG J K, SHAHINPOOR M. A novel method of manufacturing three-dimensional ionic polymer-metal composites (IPMCs) biomimetic sensors, actuators and artificial muscles [J]. Polymer, 2002, 43(3): 797-802.
[6] SHAHINPOOR M, KWANG J K. Novel ionic polymer-metal composites equipped with physically loaded particulate electrodes as biomimetic, sensors, actuators and artificial muscles [J]. Sensors and Actuators A: Physical, 2002, 96(2/3): 125-132.
[7] SHAHINPOOR M,KWANG J K. Ionic polymer-metal composites (I): Fundamentals [J]. Smart Materials and Structures, 2001, 10(4): 819-833.
[8] YAMAKITA M, ASAKA K, KANEDA Y, KAMAMICHI N, LUO Z W. Development of artificial muscle actuator using ionic polymer with its application to biped walking robots [C]// Proceedings of SPIE—The International Society for Optical Engineering. Bellingham: The International Society for Optical Engineering, 2003: 301-308.
[9] JUNG K, NAM J, CHOI H. Investigations on actuation characteristics of IPMC artifical muscle actuator [J]. Sensors and Actuators A: Physical, 2003, 107(2): 183-192.
[10] OTERO T F, CORTES M T. Artificial muscle: Movement and position control [C]// Chemical Communication. Cambridge: Royal Soc Chemistry, 2004: 284-285.
[11] CURT S K, DONALD J L. Bandwidth characterization in the micropositioning of ionic polymer actuators [J]. Journal of Intelligent Material Systems and Structures, 2005, 16(1): 3-13.
[12] AKEL B J, DONALD J L, HICKNER M, MCGRATH J E. Electroactive polymers based on novel ionometers [C]// American Society of Mechanical Engineers: Aerospace Division (Publication). New York: American Society of Mechanical Engineers, 2003: 445-452.
[13] BENNETT M, LEO D. Manufacture and characterization of ionic polymer transducers employing non-precious metal electrodes [J]. Smart Materials and Structures, 2003, 12(3): 424-436.
[14] NEMAT-NASSER S. Micromechanics of actuation of ionic polymer-metal composites [J]. Journal of Applied Physics, 2002, 92(2): 2899-2915.
[15] NEWBURY K, LEO D. Electromechanical modeling and characterization of ionic polymer benders [J]. Journal of Intelligent Material System and Structures, 2002, 13(1): 51-60.
[16] MENG Li-bo, JIN Guan-chang, YAO Xue-feng, LUO Min. The digital speckle correlation method and the application in deformation measurement of carbon fiber composite pressure vessel [J]. Optical Technique, 2006, 32(2): 163-168. (in Chinese)
(Edited by YANG Hua)
Foundation item: Project(50575228) supported by the National Natural Science Foundation of China; Project(07JJ3089) supported by the Hunan Provincial Natural Science Foundation of China
Received date: 2007-10-25; Accepted date: 2007-12-29
Corresponding author: TANG Hua-ping, Professor, PhD; Tel: +86-731-8879351; E-mail: Huapingt@mail.csu.edu.cn
- Constitutive relationship of ionic polymer-metal composite and static response character of its cantilever setup to voltage
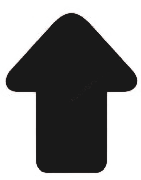