- Abstract:
- 1 Introduction▲
- 2 Experimental▲
- 3 Results and discus...▲
- 4 Conclusions▲
- References
- Figure
- Figure 1 Influence of reaction temperature on depolymerization rate of PET, yield and purity of TPA
- Figure 2 Influence of reaction time on depolymerization rate of PET, yield and purity of TPA
- Figure 3 Influence of stirring rate on depolymerization rate of PET, yield and purity of TPA
- Figure 4 Influence of consumption of sodium bicarbonate on depolymerization rate of PET, yield and purity of TPA
- Figure 5 Influence of consumption of EG on depolymerization rate of PET, yield and purity of TPA
- Figure 6 Influence of consumption of water on depolymerization rate of PET, yield and purity of TPA
- Figure 7 Characterization results of product:
J. Cent. South Univ. (2018) 25: 543-549
DOI: https://doi.org/10.1007/s11771-018-3759-y
Recycling and depolymerization of waste polyethylene terephthalate bottles by alcohol alkali hydrolysis
SUN Cong-hao(孙琮皓), CHEN Xiang-ping(陈湘萍), ZHUO Qiang(卓强), ZHOU Tao(周涛)
Hunan Provincial Key Laboratory of Efficient and Clean Utilization of Manganese Resources
(School of Chemistry and Chemical Engineering), Central South University, Changsha 410083, China
Central South University Press and Springer-Verlag GmbH Germany, part of Springer Nature 2018
Abstract:
In this work, a novel alcohol alkali hydrolysis method was explored for the preparation of terephthalic acid (TPA) from waste polyethylene terephthalate (PET). First, a series of single factor experiments on the depolymerization rate of waste PET bottles and the yield of TPA were conducted to determine the optimized experimental conditions, in terms of reaction time, reaction temperature, dosage of ethylene glycol and sodium bicarbonate, amount of distilled water and stirring rate. Then IR spectra and elemental analysis were carried out for the characterization of obtained product. Under optimal experimental conditions, over 98% PET can be depolymerized into the target product (TPA) and the purity and yield of TPA are over 97% and 94%, respectively. Both the experimental and analytical results support a feasible process for the preparation of TPA from waste PET. It is expected that this alcohol alkali hydrolysis method can promise an effective way for the sustainable recycling of waste PET.
Key words:
waste polyethylene terephthalate; terephthalic acid; alcohol alkali hydrolysis; ethylene glycol;
Cite this article as:
SUN Cong-hao, CHEN Xiang-ping, ZHUO Qiang, ZHOU Tao. Recycling and depolymerization of waste polyethylene terephthalate bottles by alcohol alkali hydrolysis [J]. Journal of Central South University, 2018, 25(3): 543–549.
DOI:https://dx.doi.org/https://doi.org/10.1007/s11771-018-3759-y1 Introduction
Polyethylene terephthalate (PET) or polyester is typically considered as one of the most important engineering polymers due to its excellent tensile properties in terms of chemical corrosion resistance and thermal stability [1–4]. Its extensive consumption will be a consequence of requirement for the disposal or recovery valuable materials from waste PET [1, 4].
Recently, physical and chemical methods are the two main approaches for the recovery of TPA from waste PET [5–7]. As a widely used process in industrial production, granulitization is an essential method for the physical recovery [8]. For chemical recovery, it can be roughly divided into hydrolysis [9–11], alcoholysis [12], aminolysis [13, 14], alcohol alkali combination [15] and other depolymerization methods [16–18].
Low molecular weight material, like ethylene glycol and TPA, can be commonly obtained through the hydrolysis method (one of the chemical recovery strategies) which can be divided into three categories (neutral hydrolysis [19], acid hydrolysis [14] and alkaline hydrolysis [12]). Based on the current researches, alkali hydrolysis may be an appropriate option for its advantages on equipment investment, reaction condition, reagents consumption and secondary pollution compared with neutral hydrolysis and acid hydrolysis.
Some preliminary work in alkaline hydrolysis had been conducted by previous researchers. For instance, 18% sodium hydroxide solution was employed to depolymerize PET at 110 °C [12]. According to Ref. [4], waste PET after pretreatment at 20%–25% (mass fraction) NaOH solution can be effectively depolymerized under the optimized conditions of reaction time of 2–3 h and reaction temperature of 92 °C. However, considering the waste liquid discharged in ordinary alkaline hydrolysis during the deploymerization process, new technologies which are eco-friendly have been further developed. At this point, bio-based recovery process was developed [20] and microwave depolymerization of PET was further investigated [9].
Though novel and eco-friendly technologies spring up concerning the recycling of waste PET, it has never been exploited by alcohol alkali hydrolysis method (alcohol & alkali & water) for the depolymerization. In this work, a novel method was explored to obtain TPA from waste PET under alcohol alkali hydrolysis. Ethylene glycol and alkali were used as reaction media to depolymerize the waste PET under atmospheric pressure, and waste PET bottles were employed as raw materials. Different effects on the depolymerization of waste PET bottles were optimized to achieve the optimal experimental condition. It is expected that this alcohol alkali hydrolysis strategy can provide an effective process for the preparation of TPA from waste PET bottles.
2 Experimental
2.1 Materials and reagents
The materials and reagents employed in this work include waste PET received from the used mineral water bottles (1.55 L, Huarun C'estbon Food and Drink Co.Ltd., Changsha), sodium bicarbonate (AR, Tianjin City Damao Chemical Reagent Factory), ethylene glycol (AR, Tianjin City Bodi Chemical Limited Company) and hydrochloric acid (AR, Zhuzhou Research Institute of Chemical Industry, Hunan Province). Different solutions at specified concentrations were prepared or diluted by deionized water.
2.2 Depolymerization experiment
In order to avoid introducing other organics during the depolymerization reaction, ethylene glycol was chosen as an alcohol solvent demanded. Sodium bicarbonate was chosen as an alkali during the alcohol alkali hydrolysis process to minimize the cost and enhance the solubility of terephthalic acid salts. And the sodium bicarbonate can be dissociated into sodium carbonate and sodium hydroxide under thermal conditions. As a cheap and weak alkali, sodium bicarbonate can not only reduce corrosion to the equipment, but also can reduce the cost.
All depolymerization reactions were conducted in a magnetic stirring batch reactor (WHF, 250 mL, Weihai Automatically-controlled Reaction Kettle Ltd. Co.) under the manipulated experimental conditions. The slurry was then cooled, filtered and dried, and the depolymerization rate of PET can be calculated according to the masses of the filter cake and initial raw material. Then the filtrate (generally yellow or deep yellow) was sequentially treated with activated carbon to decolor the filtrate and separate the product (TPA), respectively. And the targeted product (TPA) can be obtained after cooling, filtering and drying at 105 °C.
2.3 Analytical method
Vario EL Ⅲ element analyzer (Germany EMENTAR company) was employed to analyze the element content of waste PET bottles at the decomposition temperature of 950–1200 °C using 99.995% helium as working gas. The analytical results reveal that the mass fractions of C, H and O in PET bottles are 62.14%, 4.61% and 33.25%, which was close to the mass fractions of the PET (C: H: O= 62.50: 4.17: 33.33).
The depolymerization rate of PET and yield of TPA can be calculated according to Eqs. (1) and (2), respectively.
(1)
(2)
where PTPA is the purity of TPA; m0 is the initial mass of waste PET bottles, g; m is the mass of unreacted solid, g; mE is the mass of dried TPA filter cake, g; mT is the mass of TPA obtained theoretically, g; PTPA is the purity of TPA.
3 Results and discussion
3.1 Optimization experiments
3.1.1 Effect of reaction temperature
Figure 1 shows the influence of reaction temperature on the depolymerization rate of PET, the yield and purity of targeted product (TPA). It can be observed that the depolymerization rate of PET increases rapidly from 23% to 96% as the reaction temperature increases from 150 °C to 170 °C so as the yield of TPA presents the same trend. The yield of TPA which attains the maximum value of 94% at the reaction temperature of 180 °C shows a descending trend with the further increase of reaction temperatures. Meanwhile, the purity of TPA almost keeps invariant (98%) with the change of reaction temperature from 150 °C to 200 °C.
Figure 1 Influence of reaction temperature on depolymerization rate of PET, yield and purity of TPA
The increasing depolymerization rate of PET with the increasing temperature may be attributed to the following two reasons. First, the depolymerization of PET will be facilitated by the increased reaction temperature which can significantly enhance cohesive energy and contact area of the depolymerization reaction. On the other hand, the depolymerization reaction of PET is an endothermic process and rising temperature can promote the decomposition of PET. However, the heterogeneous reaction of liquid–solid will be discouraged by excessively high temperature (over the boiling point of liquid phase including ethylene glycol), which may result in remarkable decline of the content of ethylene glycol. Furthermore, the high temperature would cause some side reaction and (e.g., thermal oxidative degradation of PET, and intermolecular dehydration of ethylene glycol), which may not be beneficial for subsequent purification operation. Therefore, the suitable reaction temperature of PET depolymerization is 170 °C or 180 °C.
3.1.2 Effect of reaction time
Figure 2 shows the effect of reaction time on depolymerization rate of PET, the yield and purity of TPA, respectively. It can be concluded from Figure 2 that depolymerization rate of PET witnesses a gradual increase with the increase of reaction time at 170 °C. At 180 °C, the growth of depolymerization rate of PET is un-conspicuous with the reaction time from 15 to 60 min and it keeps almost stable from 60 to 105 min. This phenomenon means that higher reaction temperature is favorable for the decomposition of PET. When depolymerization reaction attains its equilibrium, further increase of reaction time cannot improve depolymerization rate any more.
Figure 2 Influence of reaction time on depolymerization rate of PET, yield and purity of TPA
Although increasing reaction time can improve the depolymerization rate of PET, it may also cause some side reactions. The influence of reaction time on the yield of TPA at different temperatures is also presented in Figure 2. It can be seen that the yield of TPA almost levels off from 60 to 105 min at 170 or 180 °C (about 95%). It also shows that the purity of TPA maintains at a high level (97.6%– 98.6%) during the whole reaction. Therefore, the optimized reaction time should be around 60–75 min.
3.1.3 Effect of stirring rate
Figure 3 illustrates the effect of stirring rate on the depolymerization rate of PET, the yield and purity of TPA at 180 °C. It can be seen that the stirring speed presents no significant effects on the depolymerization rate of PET and the yield of TPA at 180 °C. In general, the purpose of stirring is to ensure the uniform distribution of reaction temperature and sufficient mixture of the reactants, which can further promote the reaction forwards. At 180 °C (exceed critical temperature of PET depolymerization), the enhancement of stirring speed can only reduce reaction time of complete depolymerization of waste PET without affecting the depolymerization rate of PET and the yield of TPA.
Figure 3 Influence of stirring rate on depolymerization rate of PET, yield and purity of TPA
3.1.4 Effect of sodium bicarbonate dosage
Figure 4 shows the effect of sodium bicarbonate (NaHCO3) dosage (mass ratio of NaHCO3 and PET, mNaHCO3:mPET) on the depolymerization rate of PET, the yield and purity of TPA at 180 °C. It can be observed that the purity of TPA keeps at 97.4%–98.5%. The decomposition rate of PET and yield of TPA increases in a certain range when the mass ratio of NaHCO3 to PET (mNaHCO3/mPET) increases from 0.8 to 1.1. Both the decomposition rate of PET and yield of TPA reach their peaks (99.1% and 90.9%, respectively) at the mass ratio of 1.1. However, the depolymerization rate of PET tends to keep invariant with the further addition of sodium bicarbonate while the yield of TPA presents a descending trend. This phenomenon may be ascribed to that the PET decomposition will be beneficial to the sufficient amount of NaHCO3 and the enhanced pH caused by excessive sodium bicarbonate will neutralize the targeted product (TPA) during the PET alkaline hydrolysis process (forming terephthalic acid sodium). Therefore, the optimal mass ratio of sodium bicarbonate to PET should be 1:1.1 to achieve a relatively high depolymerization rate of PET and avoid the side reactions and by-products.
Figure 4 Influence of consumption of sodium bicarbonate on depolymerization rate of PET, yield and purity of TPA
3.1.5 Effect of EG dosage
Figure 5 illustrates the effect of ethylene glycol (EG) dosage (VEG/mPET, mL/g) on depolymerization rate of PET, the yield and purity of TPA under the following optimized conditions of 180 °C, 70 min and mNaHCO3/mPET=1:1.1. The purity of TPA maintains at 98.0%–98.5%. It can be obtained from Figure 5 that both the depolymerization rate of PET and the yield of TPA increase with the increase of EG dosage from 0/3 to 10/3, while both two targets almost keep stable (99.4% and 90%, respectively) when VET/mPET exceeds over 10/3. It can, therefore, be concluded that the increase of EG dosage can accelerate the alcoholysis reaction of PET depolymerization and excessive EG presents no benefit for the depolymerization reaction of PET.
Figure 5 Influence of consumption of EG on depolymerization rate of PET, yield and purity of TPA
3.1.6 Effect of water dosage
Figure 6 shows the influence of water dosage on the depolymerization rate of PET, the yield and the purity of TPA at 180 °C under conditions of 80 °C, 70 min and mNaHCO3/mPET=1:1.1 and VET/mPET of 10/3. It can be obtained that both the depolymerization rate of PET and the yield of TPA experience a gradual increase from 20/3 to 50/3 and then a slight decline from 50/3 to 60/3. The addition of water can effectively enhance the reaction contact area which is beneficial for the depolymerization of waste PET. However, excessive water may lead to an obvious decline of pH of the reaction system, which may prevent the formation of alkaline hydrolysis products (TPA). The suitable water dosage should, therefore, be controlled at 40/3, under which the maximum values of the depolymerization rate of PET and yield of TPA are 99.7% and 94.1%, respectively.
Figure 6 Influence of consumption of water on depolymerization rate of PET, yield and purity of TPA
There are three advantages by adding water to the reaction system. First, the addition of water can increase the reaction contact area and accelerate the depolymerization reaction during the liquid–solid heterogeneous reaction. In addition, the subsequent purification and acidification operations may benefit from the addition of water due to the soluble alkaline hydrolysis products in water. Finally, the large specific heat capacity of water will facilitate the controlling of reaction temperature in a laboratory scale.
3.2 Characterization of product
In this work, NICOLET380 Fourier transform infrared spectroscopy (NICOLET company, US) was employed to analyze functional groups of target product (see Figure 7(a)) and the pure TPA sample (see Figure 7(b)). It can be discovered that correlation peak of substituted phenyl group appears around 3060, 1570 and 1510 cm–1. And the peak around 1570 cm–1 is skeleton vibration peak of benzene, which can identify the presence of phencyclidine. Absorption peak moves to low frequency, which can judge the substituents and phencyclidine in conjugated effect. The first strong peak around 1690 cm–1 in characteristic area can be thought as the carboxyl groups (C=O) peak. All the above analytical results can attribute to the characteristics of pure TPA and the target product is relatively pure TPA.
At the same time, Vario EL III element analyzer was employed to analyze the elements of the separated solid samples after acidification. Analytical results show that the value of C: H: O in the samples is 58.02: 4.00: 37.98, which is close to the value of (57.83: 3.61: 38.55) in pure TPA. The solid samples obtained can be identified to be the terephthalic acid based on the infrared and elemental analytical results.
Finally, thermogravimetric analysis (TGA) was conducted to identify the target product obtained (see Figure 7(c)). Obvious weight loss (about 97%) can be observed according to the TG-DTG curve of the target product from 300 °C to 400 °C, which agrees with the property of pure TPA (easy sublimation over 300 °C).
4 Conclusions
In this work, waste PET bottles are depolymerized by the alcohol alkali hydrolysis method and effects of different experimental conditions are optimized on the depolymerization of waste PET bottles. The results of optimization experiments indicate that the optimal conditions are reaction temperature of 170–180 °C; reaction time of 60–75 min; mass ratio of sodium bicarbonate to PET of 1:1.1; volume ratio of EG to PET mass of 10/3 mL/g; volume ratio of water to PET mass of 40/3–50/3 mL/g. It can be concluded from analytical results that the obtained products is relatively pure TPA. It is expected that this alcohol alkali hydrolysis method combined with alcoholysis and hydrolysis can promise an effective route for sustainable recycling of waste PET bottles for the preparation of TPA under a mild experimental conditions.
Figure 7 Characterization results of product:
References
[1] VOUYIOUKA S N, KARAKATSANI E K, PAPASPYRIDES C D. Solid state polymerization [J]. Progress in Polymer Science, 2005, 30: 10–37.
[2] AWAJA F, PAVEL D. Recycling of PET [J]. European Polymer Journal, 2005, 41: 1453–1477.
[3] DUH B. Effects of the carboxyl concentration on the solidstate polymerization of poly (ethylene terephthalate) [J]. Journal of Applied Polymer Science, 2002, 83: 1288–1304.
[4] WELLE F. Twenty years of PET bottle to bottle recycling—An overview [J]. Resources Conservation and Recycling, 2011, 55: 865–875.
[5] LIU Y, WANG M, PAN Z. Catalytic depolymerization of polyethylene terephthalate in hot compressed water [J]. The Journal of Supercritical Fluids, 2012, 62: 226–231.
[6] PALIWAL N R, MUNGRAY A K. Ultrasound assisted alkaline hydrolysis of poly (ethylene terephthalate) in presence of phase transfer catalyst [J]. Polymer Degradation and Stability, 2013, 98(10): 2094–2101.
[7] GENTA M, IWAYA T, SASAKI M, GOTO M. Supercritical methanol for polyethylene terephthalate depolymerization: Observation using simulator [J]. Waste Management, 2007, 27(9): 1167–1177.
[8] AL-SABAGH A M, YEHIA F Z, ESHAQ G, RABIE A M, ELMETWALLY A E. Greener routes for recycling of polyethylene terephthalate [J]. Egyptian Journal of Petroleum, 2016, 25(1): 53–64.
[9] KHALAF H I, HASAN O A. Effect of quaternary ammonium salt as a phase transfer catalyst for the microwave depolymerization of polyethylene terephthalate waste bottles [J]. Chemical Engineering Journal, 2012, 19: 245–248.
[10] MO H B, CHEN X P, LIAO X Y, ZHOU T. Sustainable synthesis of 5-hydroxymethylfurfural from waste cotton stalk catalyzed by solid superacid-SO42–/ZrO2 [J]. Journal of Central South University, 2017, 24(8): 1745–1753.
[11] GEYER B, LORENZ G, KANDELBAUER A. Recycling of poly (ethylene terephthalate)–A review focusing on chemical methods [J]. Express Polymer Letters, 2016, 10(7): 559–586.
[12] SINHA V, PATEL M R, PATEL J V. Pet waste management by chemical recycling: A review [J]. Journal of Polymers and the Environment, 2010, 18(1): 8–25.
[13] KUROKAWA H, OHSHIMA M A, SUGIYAMA K, MIURA H. Methanolysis of polyethylene terephthalate (PET) in the presence of aluminium triisopropoxide catalyst to form dimethyl terephthalate and ethylene glycol [J]. Polymer Degradation and Stability, 2003, 79(3): 529–533.
[14] YANG Y, LU Y, XIANG H, XU Y, LI Y. Study on methanolytic depolymerization of PET with supercritical methanol for chemical recycling [J]. Polymer Degradation and Stability, 2002, 75(1): 185–191.
[15] LIU J W, HU H P, WANG M, CHEN X P, CHEN Q Y, DING Z Y. Synthesis of modified polyacrylamide with high content of hydroxamate groups and settling performance of red mud [J]. Journal of Central South University, 2015, 22: 2073-2080.
[16] TROEV K, GRANCHAROV G, TSEVI R, GITSOV I. A novel catalyst for the glycolysis of poly (ethylene terephthalate) [J]. Journal of Applied Polymer Science, 2003, 90(4): l148–1152.
[17] WANG H, LIU Y Q, LI Z X, ZHANG X P, ZHANG S J, ZHANG Y Q. Glycolysis of poly (ethylene terephthalate) catalyzed by ionic liquids [J]. European Polymer Journal, 2009, 45(5): 1535–1544.
[18] BACCOUCH Z, MBAREK S, JAZIRI M. Experimental investigation of the effects of a compatibilizing agent on the properties of a recycled poly (ethylene terephthalate)/ polypropylene blend [J]. Polymer Bulletin, 2017, 74: 839–856.
[19] SHARMA V, SHRIVASTAVA P, AGARWAL D D. Degradation of PET-bottles to monohydroxyethyl terephthalate (MHT) using ethylene glycol and hydrotalcite [J]. Journal of PolymerResearch, 2015, 22(12): 1–10.
[20] ZIA K M, NOREEN A, ZUBER M, TABASUM S, MUJAHID M. Recent developments and future prospects on bio-based polyesters derived from renewable resources: A review [J]. International Journal Biological Macromolecules, 2016, 82: 1028–1040.
(Edited by FANG Jing-hua)
中文导读
醇碱水解作用下废旧聚酯瓶的解聚回收利用
摘要:本文采用醇碱水解法,结合醇解和碱性水解的特点,在相对低温低压的条件下,实现废旧聚酯瓶的快速分解,获得苯二甲酸和乙二醇。研究中主要考察反应温度、反应时间、搅拌速率、物料配比等对废旧聚酯瓶解聚效果的影响,获得最佳反应条件,并通过红外分析和热分析表征目标产物。结果表明:在优化条件下,通过醇碱水解法能够快速有效分解废旧聚酯并获得较高纯度的目标产物。
关键词:废旧聚酯;苯二甲酸;醇碱水解;快速分解
Foundation item: Project(2016TP1007) supported by the Hunan Provincial Science and Technology Plan, China
Received date: 2016-06-24; Accepted date: 2016-08-25
Corresponding author: ZHOU Tao, PhD, Professor; Tel: +86–731–88876605; E-mail: zhoutao@csu.edu.cn; ORCID: 0000-0002-2363- 2938
Abstract: In this work, a novel alcohol alkali hydrolysis method was explored for the preparation of terephthalic acid (TPA) from waste polyethylene terephthalate (PET). First, a series of single factor experiments on the depolymerization rate of waste PET bottles and the yield of TPA were conducted to determine the optimized experimental conditions, in terms of reaction time, reaction temperature, dosage of ethylene glycol and sodium bicarbonate, amount of distilled water and stirring rate. Then IR spectra and elemental analysis were carried out for the characterization of obtained product. Under optimal experimental conditions, over 98% PET can be depolymerized into the target product (TPA) and the purity and yield of TPA are over 97% and 94%, respectively. Both the experimental and analytical results support a feasible process for the preparation of TPA from waste PET. It is expected that this alcohol alkali hydrolysis method can promise an effective way for the sustainable recycling of waste PET.
- Recycling and depolymerization of waste polyethylene terephthalate bottles by alcohol alkali hydrolysis
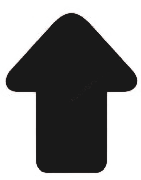