J. Cent. South Univ. Technol. (2008) 15(s1): 088-092
DOI: 10.1007/s11771-008-321-3
Rheological characteristics of drug-loaded microemulsions and their printability in three dimensional printing systems
YU Deng-guang(余灯广)1, YAN Wei-xia(闫伟霞)1, ZHU Si-jun(朱思君)1, LI Xue-lian(李雪莲)1,
Branford-white Chris2, ZHU Li-min(朱利民)1
(1. College of Chemistry, Chemical Engineering and Biotechnology, Donghua University, Shanghai 201620, China;
2. Institute for Health Research and Policy, London Metropolitan University, London N7 8DB, UK)
Abstract:
Rheological properties of microemulsions (MEs) and their printability in three dimensional printing (3DP) systems were investigated. A series of MEs with different contents of oil phase were prepared using sonication method with ibuprofen as model drug and soybean lecithin as emulfier. Stationary and transient rheological properties of MEs were investigated by ARES-SRF using concentric cylinders measuring systems. 3DP systems with piezoelectric drop-on-demand print heads were employed to test the printability of the MEs. Results demonstrate that the apparent viscosity and dynamic linear viscoelastic regions of the MEs are the most important parameters for continuous and stable printing of MEs by 3DP. The incorporation of drug in the MEs has little influence on the MEs’ stationary rheological behaviors and dynamic viscoelasticity, but the concentration of oil phase has a strong influence on them. The rheological property of binder liquids has a close relationship with their printability in 3DP system.
Key words:
three-dimensional printing; rheological property; microemulsions; printability; apparent viscosity;
1 Introduction
Three-dimensional printing(3DP), a rapid prototyping technology, was firstly developed at the Massachusetts Institute of Technology in 1992[1-2]. It employs powder processing and a liquid binder material in the construction of parts in a layer-wise manner and is one of the most vital modern advanced technologies due to its outstanding manufacturing capabilities, easy process, excellent flexibility, fast phototyping rate and low cost.
3DP has developed its applications in many fields once it was developed. In pharmaceutics field, implantable drug delivery systems fabricated using 3DP technology was initially demonstrated by WU et al[3] with dye solutions as binding liquid. Later, KATSTRA et al[4-5] successfully prepared oral drug delivery systems (DDS) bearing controlled release profiles with drug solutions and polymer solutions as printed binder liquids. However there are still some basic problems for further and more extensive applications of 3DP in fabricating DDS, including printability of binder liquid, laminating and prototyping properties of the mixed powders, binding mechanism of DDS and its relationship with the DDS’s characteristics, among them the printability of binder liquids is the most important one. It is only by precisely controlling the jetting direction and shape of the binder liquids’ droplets that accurate printing amounts of binder liquid and high printing precision could be achieved. Among all kinds of binder liquids’ properties, the rheological behaviors are concernful. Only with suitable viscosity and surface tension, stable flow and continuous jetting of binder liquids are possible. On the other hand, although the application of 3DP is ever increasing, comparatively little information has been published on how inkjet printability of materials correlates with their rheological properties.
3DP machine is mainly consists of a powder delivery and dispensing system, a working platform, and a printing system driven by the stepping motor. Generally speaking the 3DP is an up runner of the ink-jet printing technology originally developed some 30 years ago. Print head is considered to be a key element in 3DP machine, and piezoelectric drop-on-demand (DoD) print head is more popular than continuous jet print heads and thermal DoD print head[6-7]. The jet mechanism is that droplets of binder liquid are forced out of the nozzles by piezoelectric crystals in the print heads that expand and “jet” the binder liquids. Based on a 3DP machine equipped with piezoelectric DoD print heads and oil-in-water (O/W) drug-loaded microemulsions (MEs) as binder liquids, the influence of the binder liquids’ rheological property on their printability was investigated.
2 Experimental
2.1 Materials
Soybean lecithin was purchased from Shanghai Taiwei Pharmaceutical Co., Ltd.; Ibuprofen was purchased from Hubei Hongjing Chemical Co., ltd; 1,2-Propanediol and borneol was purchased from Shanghai Chemicals Reagent Co.,Ltd.; Fluorescein sodium was purchased from Shanghai Yope Biotech Inc. All other chemicals used were of analytical grade, and water was twice-distilled just before use.
2.2 Sample preparation
The ibuprofen-loaded microemulsions were prepared according to Ref.[8]. Concretely, ibuprofen and soybean lecithin were dissolved in the 1,2-propanediol containing 0.5% borneol and 0.1% (mass fraction) fluorescein sodium according mass ratio of 1?1?3 under ultrasonic wave (15 min, 500 W, SB2200 ultrasonic generator, Branson Ultrasonics Shanghai Company, Ltd.) for oil phase, then the oil phase was dropped into 0.1mol/L pH 7.4 phosphate-buffered saline under ultrasonic wave (20 min) according to mass ratios of 1?1, 1?2 and 1?5 to prepare drug-loaded MEs with different contents of oil phase.
The same processes were repeated to prepare the control MEs without ibuprofen in the oil phase and with an oil-to-water mass ratio of 1?2.
2.3 Rheological measurement
Stationary and transient rheological properties of MEs were investigated by Advanced Rheometric Expansion System Rheometrics Fluids Spectrometer (TA Instruments, USA) using concentric cylinders measuring systems. All experiments were performed at 25 ℃.
Stationary rheological behaviors of MEs were measured by Steady rate sweep test, and transient rheological behaviors of MEs were measured by Dynamic strain sweep test and Dynamic frequency sweep test. The storage modulus (G′), the loss modulus (G″) and the loss factor (tan δ) were calculated.
2.4 Print tests in 3DP systems
The desktop 3DP machine was assembled at Shanghai Folichif Co. Ltd., which had two piezoelectric DoD print-heads.
The printability of MEs in 3DP system was evaluated both quantificationally and qualitatively. The qualitative evaluations included obversing the jetting of binder liquids, the clogging of nozzles in the print head, continuity and stability of printing processes. Based on qualitative observations, the print amount of binder liquids in unit time and the print precision of line-to-line distance were measured. The former was conducted by an electronic balance, which was connected with the powder bed of 3DP system. The later was finished according to Ref.[9]. Concretely, the MEs were printed onto a mixed powders composed of lactose, HPMC E50, PVP K30 and colloidal silicon dioxide according to mass ratio of 40?30?29?1. The phototyped layer were observed using a Phillips reflex fluorescence microscope equipped with a high pressure Hg excitation lamp and an Olympus IX 70 digital camera (Olympus, Japan). The excitation wavelength was 492 nm and the emission was filtered through 400 nm dichroic cube. The objective magnification was 40×20 and the exposure time was 1 s.
3 Results and discussion
3.1 Stationary rheological behaviors
Fig.1 shows the effect of shear rate on shear stress for four MEs. All the MEs show non-Newtonian flow behaviors, except drug-loaded MEs with an oil-to-water mass ratio of 1?5 that show Newtonian flow behaviors.
Fig.1 Effect of shear rate on shear stress of MEs
Different with ordinary emulsions, MEs are clear, stable, isotropic liquid mixtures of oil, water and surfactant.Two immiscible phases (water and ‘oil’) are present with a surfactant, the surfactant molecules form a monolayer at the interface between the oil and water, with the hydrophobic tails of the surfactant molecules dissolved in the oil phase and the hydrophilic head groups in the aqueous phase. The oil particles were highly dispersible in the aqueous phase. Resistance for free flow of microemulsions to be overcome is often very small, thus very nice linear relationships between the shear rate and the shear stress are illustrated in Fig.1 for the MEs.
It can be seen from Fig.2 that the apparent viscosities of MEs gradually decrease with the decrease of oil-to-water ratios.
Fig.2 Effect of shear rate on apparent viscosity
For MEs except the one with an oil-to-water ratio of 1?5, apparent viscosity ha decreases with shear rate and Mes are shear-thinning fluids in the shear rate range of 0.1-4.0 s-1. However, when the shear rate is bigger than 4.0 s-1, the MEs turn from non-Newtonian pseudo- plastic fluids to Newtonian fluids. The drug-loaded MEs and the control MEs have slightly different apparent viscosity values only when the shear rates are very small, demonstrating that the drug has little influence on the MEs’ stationary rheological behaviors. The main factor that exerts influence on the MEs’ stationary rheological properties is the content of oil phase.
3.2 Dynamic viscoelastic behaviors
The MEs had linear viscoelastic regions (LVR) and non-linear viscoelastic regions. In the linear viscoelastic regions, the shear stress was positively related to the strains, but the dynamic module had little relationship with the strains. To ensure that the “Dynamic frequency sweep tests” were conducted in the LVR, the correlation between the strain and the dynamic stress were investigated. Results show that the dynamic modulus of the MEs keep almost the same values in a broad range (0.1%-10%), illustrating the MEs have a large LVR. Correspondingly, the strain scope is kept as 1.0% during the dynamic frequency sweep tests.
Fig.3 shows the change of dynamic modulus (G′, G″) of the MEs with the angular frequency ω. MEs exhibit small dynamic module because of its high dispersibility. Under the same angular frequency, G′ and G″ increase with the increase of oil phase content in the MEs, illustrating that the concentration of oil particles has influence on the MEs’ viscoelasticity. The reason may be that there are negative charges on the surface of the oil particles, and net space structure may be formed among the oil particles due to the static force and other molecular interactions. MEs with an oil-to-water mass ratio of 1?5 have very small values of G′ and G″, which are not shown in Fig.3. G′ and G″ of drug-loaded MEs are almost the same with those of the control MEs, demonstrating that the incorporation of drug in the MEs has little influence on the dymanic viscoelasticity.
Fig.3 Effect of frequency on dynamic modulus (G′, G″)
The change of tan δ with the dynamic frequency is shown in Fig.4. The tan δ values of all the four MEs gradually decrease with the increase of frequency. In general, the bigger of tan δ is, the more of the energy lost by the MEs is, and the larger of friction force and the inner depletion are. Among the four MEs, tan δ gradually decreases along with the decrease of the contents of oil phase in the MEs. Comparison of tan δ of drug-loaded MEs and the control MEs, the former is a little bigger than the later. The reason should be that the absorbance and studdeding of drug micro-crystal on the surface of the MEs particles have influence on the particles’ shape, dimensions and surface charges, and thus increase the energy expenditure for the movement of the MEs particles.
Fig.4 Effect of frequency on loss factor (tan δ)
3.3 Printability in 3DP systems
All the MEs can be printed continuously and steadily through the piezoelectric DoD print heads and there is no puzzle-clogged phenomenon during the printing process. The MEs have a large dynamic linear viscoelastic region, the exerting shear stress is not able to reduce the MEs’ stability, and thus there are no aggregations of oil particles to clog the puzzles of the print heads. On the other hand, the dynamic viscoelastic behaviors have no direct relationship with the printability of MEs in 3DP system.
The printing mass in 5 min and precision for the four MEs are shown in Table 1. The fluorescence tracing image by printing drug-loaded MEs with an oil-to-water mass ratio of 1?2 onto the mixed powders is shown in Fig.5. The true printing precision should be better than the measured one because the binder liquid might migrate among the particles and along the capillaries in the particles. Except MEs with an oil-to-water ratio of 1?5, the other three have almost the same printing effects. MEs with an oil-to-water ratio of 1?5 have poorer printing precision but bigger average error due to their too small viscosity, which influence the form of droplets and make the capillary-migration phenomenon more severe.
Table 1 Printing mass of MEs and printing precision
Fig.5 Printing precision from fluorescence tracing images
ROWE et al[10] fabricated DDS by printing drug- loaded suspensions using continuous jet print heads. The increase of viscosity of binder liquids favored the printing precision by reducing solvent migrations stemmed from the capillaries. However, higher viscosity of binder liquids might let the printing failure, or the occurring of comet-tail on the printing droplets to depress the printing precision. It is often deemed that the suitable viscosity of binder liquid should be kept between 0.3-20 mPa·s. This research proves that for better printing effect of MES, their viscosity should be bigger than 5 mPa·s.
4 Conclusions
1) MEs are non-Newtonian pseudoplastic fluids, except when the oil phase was very low. The drug has little influence on the MEs’ stationary rheological behaviors. The MEs have a large linear viscoelastic region. Under the same angular frequency, G′ and G″ increase with the increase of oil phase content in the MEs. The incorporation of drug in the MEs has little influence on the dynamic viscoelasticity, but the concentration of oil particles has a strong influence on it. tan δ of the MEs gradually decreases with the increase of dynamic frequency.
2) All the MEs can be printed continuously and steadily through the piezoelectric DoD print heads and there is no puzzle-clogged phenomenon during the printing process. Among the rheological parameters, the apparent viscosity and dynamic linear viscoelastic regions are the most important parameters. For continuously and steadily printing, suitable rheological characteristics of the MEs are vital.
3) Studies on how printability of binder liquids correlates with their other properties may open new avenues for the application of 3DP in pharmaceutics and other fields. For the first time, the correlation between the rheological parameters of binder liquids and their printability in 3DP systems was investigated in this research.
References
[1] SACHS E M, CIMA M J, WILLIAMS P, BRANCAZIO D and CORNIE J. Three-Dimensional PrintingTM: rapid tooling and prototypes directly from a CAD model [J]. J Eng Ind, 1992, 114(4): 481-488.
[2] YU Deng-guang, ZHU Li-min, BRANDFORD-WHITE Chris, YANG Xiang-liang. Three-dimensional printing in pharmaceutics- promises and problems [J]. J Pharm Sci, DOI: 10.1002/jps.21284.
[3] WU B M, BORLAND S W, GIORDANO R A, CIMA L G, SACHS E M,CIMA M J. Solid free-form fabrication of drug delivery devices [J]. J Control Release, 1996, 40(1): 77-87.
[4] KATSTRA W E, PALAZZOLO R D, ROWE C W, GIRITLIOGLU B, TEUNG P, CIMA M J. Oral dosage forms fabricated by three dimensional printing [J]. J Control Release, 2000, 66(1/2): 1-9.
[5] ROWE C W, KATSTRA W E, PALAZZOLO R R D, GIRITLIOGLU B, TEUNG P, CIMA M J. Multimechanism oral dosage forms fabricated by three dimensional printing [J]. J Control Release, 2000, 66(1/2): 11-17.
[6] DIMITROV D, SCHREVE K, DE BEER N. Advances in three dimensional printing–state of the art and future perspectives [J]. Rapid Prototyping J, 2006, 12(3): 136-147.
[7] DE GANS B J, DUINEVEL P C, SCHUBERT U S. Inkjet printing of polymers: State of the art and future developments [J]. Adv Mat, 2004, 16(3): 203-213.
[8] XU Hui-bi, HUANG Kai-xun, ZHU Yu-san, GAO Qiu-hua, WU Qin-zhi, TIAN Wei-chun, SHENG Xi-qun, CHEN Ze-xuan, GAO Zhong-hong. Hypoglycaemic effect of a novel insulin buccal formulation on rabbits [J]. Pharmcol Res, 2002, 46(5): 459-467.
[9] YU Deng-guang,YANG Xiang-liang, HUANG Wei-dong, LIU Jie, WANG Yun-gan, XU Hui-bi. Material gradient tablets fabricated by three-dimensional printing [J]. J Pharm Sci, 2007, 96(9): 2446-2456.
[10] ROWE C W, PRYCE LEWIS W E, CIMA M J, BORNANCINI R N, SHERWOOD J K, WANG C C, GAYLO C M, FAIRWEATHER J A. Printing of dispensing a suspension such as three-dimensional printing of dosage forms US, 0099708[P]. 2003-05-29.
Foundation item: Project(B07024) supported by Biomedical Textile Materials “111 Project” from Ministry of Education of China; Project(50773009) supported by the National Natural Science Foundation of China and Project(Grant IRT0526) supported by Program for Changjiang Scholars and Innovative Research Team in University
Received date: 2008-06-25; Accepted date: 2008-08-05
Corresponding author: ZHU Li-min, Professor; Tel: +86-21-67792655; E-mail: lzhu@dhu.edu.cn
- Rheological characteristics of drug-loaded microemulsions and their printability in three dimensional printing systems
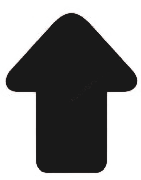