J. Cent. South Univ. Technol. (2007)04-0447-05
DOI: 10.1007/s11771-007-0087-z
Effects of warm compaction on mechanical properties of sintered P/M steels
YI Jian-hong(易健宏)1,YE Tu-ming (叶途明)1,2, PENG Yuan-dong(彭元东)1,
XIA Qing-lin(夏庆林)1, WANG Hong-zhong(王红忠)1
(1. State Key Laboratory of Powder Metallurgy, Central South University, Changsha 410083, China;
2. No.1 Steelmaking Plant, Wuhan Iron and Steel Corporation, Wuhan 430083, China)
_________________________________________________________
Abstract:
The green and sintered densities, and tensile strength of sintered P/M steels produced by cold compaction, warm compaction, warm compaction combined with die wall lubrication (DWL) were measured under various compaction pressures using polytetrafluoroethylene (PTFE) emulsion as the die wall lubricant. The effects of warm compaction on the mechanical properties were studied. The tensile fracture behaviors of cold compaction and warm compaction were studied using scanning electron microscope (SEM). The results show that the density of sintered P/M steel prepared by warm compaction or warm compaction with DWL is higher than that by cold compaction under all compaction pressures. Meanwhile, the highest tensile strength is obtained by combination of warm compaction and die wall lubrication under all compaction pressures. The SEM results show that the fracture modes of the sintered samples prepared by cold compaction and warm compaction at 700 MPa are the mixed mode of ductile fracture and brittle fracture, and obvious dimples can be found in some regions. The fracture of sample prepared by cold compaction is uneven and has irregular and big pores, but that by warm compaction is relatively even and the pores are round mostly, and the samples have many obvious dimples on the whole fracture surface.
Key words:
warm compaction; die wall lubrication; powder metallurgy; mechanical properties;
_________________________________________________________
1 Introduction
It is important to increase the sintered strength of powder metallurgy (P/M) parts for high performance applications, and increasing the density is the best method to improve the sintered strength. The fatigue strength and toughness of iron-based P/M parts increase remarkably with a density larger than 7.2 g/cm3[1]. However, conventional P/M processing can only produce iron-based P/M parts with a density less than 7.1 g/cm3 (a relative density of approximately 90%), so their mechanical properties are substantially worse than those of full density counterparts. To expend the applied field, there are many processes that can produce iron-based P/M parts with high density such as high temperature sintering, Cu infiltration, double press/double sintering (DP/DS), powder forging and warm compaction[2-3].
Warm compaction was introduced to the market in PM2TEC-1994 and had rapidly won ground as a cost effective method to produce high density P/M parts used in various applications. Warm compaction is an interesting avenue to achieve high green densities at a lower cost compared to DP/DS and powder forging[4-6]. Warm compaction is the process during which mixed iron/steel powders are compacted in a heated condition, at approximately 130 ℃, to reduce the iron/steel powder’s yield strength[7-8]. However, a good understanding of the mechanisms that involved during the warm compaction and sintering stages can help people to optimize the sintered density and hence the mechanical properties of the P/M parts. Indeed, the green density is not only closely related to the compressibility of the based powder but also to the type and concentration of the admixed lubricant. There are two issues in this process. One is that the attainable density has limitation due to the presence of lubricant. The theoretical density is defined as the density of green part without porosity. The green density can be improved by reducing the amount of admixed lubricant. The other is the difficulty of removing lubricant from green compact. No lubricant can burn off completely during sintering and leaving ashes inside the compact, thereby, hindering the diffusion process during sintering[9-12]. Therefore, several researchers have studied die wall lubrication (DWL) as an alternative to admixed lubricant in metal powders. Due to friction reduction between powder particles and die wall by combining warm compaction with die wall lubrication, high density parts may be produced with reduced internal lubricant[13-15]. The aim of present work is to study the effects of warm compaction and warm compaction combined with die wall lubrication on the mechanical properties of sintered P/M steels, in hope of reducing the concentration level of admixed lubricant.
2 ExperimentalThe chemical compositions of the samples were 93.4%Fe, 4%Ni, 1.5%Cu, 0.5%Mo and 0.6% graphite (mass fraction). The powder was prepared by mixing a highly compressible water atomized Atomet 1001 iron powder, which was produced by Quebec Metal Powders Limited, Canada, with particle size of ≤147.0 μm. Carbonyl nickel with an average size of 1.5 μm and electrolytic copper powder with a size of ≤38.0 μm were used. A special lubricant developed for warm compaction was added to the powder with concentrations ranged from 0.2% to 0.6%. The characteristics of raw powders and lubricant are shown in Table 1. Elemental powders and lubricant were mixed for 60 min in a planetary ball mill. Die wall lubrication was selected in part of experiments. Polytetrafluoroethylene (PTFE) emulsion was brushed onto the die wall as the die wall lubricant.
Table 1 Characteristics of raw powders and lubricant
All samples were compacted into standard tensile specimens (ISO 2740-1973) by an Instron testing machine with different pressures from 550 to 700 MPa in a steel mold. Samples were processed according to three different routes, as shown in Table 2. Materials A1 and A2 were compacted using the conventional method (Cold compaction) and warm compaction method with 0.6% of lubricant, respectively. Incorporation of warm compaction and die wall lubrication methods, material B was compacted with 0.2% of lubricant. And all samples were sintered in hydrogen atmosphere at 1 120 ℃ for 30 min in a pusher type furnace, then cooled to room temperature.
Table 2 Processing conditions for different materials
The green density, sintered density and tensile strength of samples were measured. Densities were measured by Archimedes drainage method. Tensile tests were observed on an LJ-3000A tensile testing machine. Results reported in this study are the average of four samples. Porosity characteristics of the sintered specimens were observed on MeF3A metallographic microscope. Fractographic features of the tensile samples were evaluated using JSM-6700F scanning electron microscope (SEM).
3 Results and discussion
3.1 Effects of warm compaction on green density and sintered density
The green density and sintered density of the studied materials are given in Figs.1 and 2, respectively. The results indicate that the green and sintered densities of materials increase with the increase of the compaction pressure. However, the green and sintered densities of material A2 and material B are greater than that of material A1 under different compaction pressures. The increase of sintered density of materials is directly associated with the decreasing porosity, in terms of pore size and number, as illustrated in Fig.3. Material B has slightly higher or approximately the same green densities than that of warm compacted material A2 under all pressures except 550 MPa. For sintered density, all sintered samples of material B have higher values than those of warm compacted material A2 under different compaction pressures.
Fig.1 Green density of studied materials under different compaction pressures
Fig.2 Sintered density of studied materials under different compaction pressures
Fig.3 Porosity comparison for different sintered materials compacted at 700 MPa
(a) Material A1; (b) Material A2; (c) Material B
3.2 Effects of warm compaction on mechanical properties
Ultimate tensile strength of the sintered samples as a function of compaction pressure is shown in Fig.4. The results show that the tensile strengths increase with the increase of the compaction pressure. Under different compaction pressures, cold compacted material A1 has the lowest tensile strength, and material B has the highest tensile strength.
Fig.4 Ultimate tensile strength of materials vs compaction pressure
3.3 Fractographs
Fig.5 shows the tensile fracture surfaces for cold compacted and warm compacted materials compacted at 700 MPa. It can be seen from Fig.5 that dimples appear and the fracture mode is the mixed mode of ductile fracture and brittle fracture. Whereas, compared with material A2, the microstructure of material A1 is more uneven, and has irregular and big pores. On the contrary, the distribution of pores in warm compacted material A2 is relatively even, and pores are mostly round. For material B, it has fewer and smaller pores than warm compacted material A2, and it has many dimples. These characteristics show that a great degree of plastic deformation take place during fracture of material B.
Fig.5 Fractographs of materials compacted at 700 MPa
(a) Material A1; (b) Material A2; (c) Material B
3.4 Discussion
Compared to the green and sintered densities of cold compacted material A1, warm compacted materials A2 and B exhibit larger increase. It can be explained as follows: in warm compaction, the plastic deformation capability of iron powder is enhanced by heating, and the decrease in force needs to flatten asperities by means of the mutual action of the facing sliding particles. Another reason may be that the lubricant undergoes a phase transformation during the warm compaction (from elastomeric state to viscous flow state), as a result, friction coefficient of the lubricant decreases and thus the effective load is increased during the compaction[16-17]. The results of tensile strength shown in Fig.4 demonstrate the benefit of warm compaction.
The results obtained from material B illustrate that the green and sintered densities, and tensile strength of samples prepared by warm compaction with die wall lubrication have higher values than that by warm compaction without die wall lubrication, except the green density for samples compacted at 550 MPa. It can be explained that, since PTFE has a very low friction coefficient and, as pointed out by many researchers[18-19], the most important role of lubricant is to overcome die wall friction rather than inter-particle friction, PTFE on the die wall reduces a great portion of the friction during compaction and thus increases the effective pressure on the powder. On the other hand, inter-particle friction can be reduced by admixed lubricant and therefore is beneficial to the densification of the powder compacts and provides compacts with better quality. However, the presence of admixed lubricant occupies the spaces in the compact, which results in the decrease of the final density. And lubricant cannot be burned off completely during sintering, thereby, the diffusion process during sintering is hindered. From Figs.1 and 2, it can be seen that the difference of sintered density is bigger than that of green density between warm compacted material A2 and material B due to the less admixed lubricant in material B.
As shown in Fig.4, the sintered samples B has the highest tensile strength. It is mainly due to the high density of the sintered samples B. Reducing the amount of admixed lubricant in material B minimizes the negative effect associated with lubricant burn-off in sintering furnace. It can also be seen from Fig.5 that there are many irregular and big pores in cold compacted samples, which result in stress concentration in some regions, so the material ruptures more easily. Nevertheless, the distribution of pores in warm compacted samples is relatively even, and pores are round mostly, and samples have many obvious dimples in the whole fracture face. Therefore, the stress distribution in entire section is relatively even, and the tensile strength of material increases.
4 Conclusions
1) Under different compaction pressures, the samples with warm compaction have higher green and sintered densities, and also tensile strength.
2) All the green and sintered densities, and tensile strength obtained by warm compaction with die wall lubrication have slightly higher or approximately the same values when compared with those obtained by warm compaction without die wall lubrication, except the green density for samples compacted at 550 MPa.
3) The sample prepared by warm compaction and die wall lubrication has the highest tensile strength under different compaction pressures.
4) The fracture mode of sintered samples compacted at 700 MPa is the mixed mode of ductile fracture and brittle fracture, and obvious dimples can be found. The microstructure of samples prepared by cold compaction is uneven and has irregular and big pores, but samples prepared by warm compaction are relatively even and pores are round mostly, and samples have many dimples in the whole fracture surface.
References[1] HUANG Pei-yun. The Principle of Powder Metallurgy[M]. 2nd. Beijing: Metallurgical Industry Press, 2004: 377-396. (in Chinese)
[2] YE Tu-ming, YI Jian-hong, PENG Yuan-dong, et al. New technique of increasing the compact density of powder metallurgy parts[J]. Powder Metallurgy Industry, 2003, 13(6): 32-36. (in Chinese)
[3] GUO Shi-ju. Technical progress in warm compaction in powder metallurgy[J]. Powder Metallurgy Industry, 2003, 13(2): 4-8. (in Chinese)
[4] CAPUS J, PICKERING S, WEAVER A. Hoeganaes offers higher density at lower cost[J]. Metal Powder Report, 1994, 49(7/8): 22-24.
[5] RUTZ H G, HANEJKO F G. High density processing of high performance ferrous materials[J]. International of Powder Metallurgy, 1995, 31(1): 9-17.
[6] ST-LAURENT S, CHAGNON F. Key parameters for warm compaction of high density materials[C]// Advances in Powder Metallurgy & Particulate Materials. Princeton: MPIF, 1996, 2: 125-138.
[7] ENSTR?M U, JOHANSSON B. Experience with warm compaction of densmix powders in the production of complex parts[C]// KOSUGE K, NAGAI H. Proceedings of 2000 Powder Metallurgy World Congress. Kyoto: Japan Society of Powder and Powder Metallurgy, 2000: 536-539.
[8] SAWAYAMA T, SATO M, SEKI Y, et al. High performance P/M materials by high density process[C]// KOSUGE K, NAGAI H. Proceedings of 2000 Powder Metallurgy World Congress. Kyoto: Japan Society of Powder and Powder Metallurgy, 2000: 540-542.
[9] CHAGNON F, ST-LAURENT S. Optimizing powder mix formulation and processing conditions for warm compaction[C]// KOSUGE K, NAGAI H. Proceedings of 2000 Powder Metallurgy World Congress. Kyoto: Japan Society of Powder and Powder Metallurgy, 2000: 543-546.
[10] LI Yuan-yuan, NGAI T L, ZHANG Da-tong, et al. Effect of die wall lubrication on warm compaction powder metallurgy[J]. Journal of Materials Processing Technology, 2002, 129(1/3): 354-358.
[11] CHAGNON F, G?LINAS C, TRUDEL Y. Development of high density materials for P/M applications[C]// Advances in Powder Metallurgy & Particulate Materials. Princeton: MPIF, 1994, 3: 199-206.
[12] NGAI T L, CHEN Wei-ping, XIAO Zhi-yu, et al. Die wall lubricated warm compaction of iron-based powder metallurgy material[J]. Trans Nonferrous Met Soc China, 2002, 12(6): 1095-1098.
[13] YE Tu-ming, YI Jian-hong, CHEN Shi-jin, et al. Die wall lubricated warm compaction behavior of non-lubricant admixed iron powders[J]. J Cent South Univ Technol, 2005, 12(6): 653-656.
[14] LEMIEUX P, THOMAS Y, MONGENON P E, et al. Benefits of die wall lubrication for powder compaction[C]// Advances in Powder Metallurgy & Particulate Materials. Princeton: MPIF, 2003, 3: 16-25.
[15] CAPUS J M. Die wall lubrication aids higher density[J]. Metal Powder Report, 1998, 53(9): 28.
[16] KATSUHIKO U, TERUFUMI M, MAKOTO I, et al. Effects of powder lubricants and compacting temperature on the higher density of iron-based green compacts[J]. Hitachi Powdered Metals Technical Report, 2002(1): 29-38.
[17] BOCCHINI G F. Warm compaction of metal powders: Why it works, why it requires a sophisticated engineering approach[J]. Powder Metallurgy, 1999, 42(2): 171-180.
[18] SAJDAK R J, MCNALLY R P, NASTA M D, et al. Two methods for characterizing the compaction and ejection behavior of metal powders in a die[J]. Int J Powder Metall, 1970, 6(2): 13-23.
[19] YARNTON D, DAVIES T J. Effect of lubrication on the compaction and sintering of iron powder compacts[J]. Int J Powder Metall, 1972, 8(2): 51-57.
____________________________
Foundation item: Project (MKPT-2004-09ZD) supported by the National Key Technological Research and Development Program of China; Project (040117) supported by the Innovative Engineering Program of Central South University
Received date: 2006-09-25; Accepted date: 2007-03-10
Corresponding author: YI Jian-hong, PhD, Professor; Tel: +86-731-8876420; E-mail: yijianhong2004@yahoo.com.cn
- Effects of warm compaction on mechanical properties of sintered P/M steels
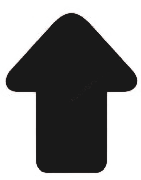