- Abstract:
- 1 Introduction▲
- 2 Extraction mechani...▲
- 3 Parameters determi...▲
- 4 Conclusions▲
- References
- Figure
- Fig. 1 Numerical simulation of flow field in vertical plane: (a) Seepage field without negative pressure; (b) Seepage field with negative pressure
- Fig. 2 Typical pictures for fluid flow in coal-mining plane of gob: (a) Goaf air leaking near working face flow into high drainage roadway; (b) Air leakage of deep goaf flow into gas tail roadway
- Fig. 3 Gas permeation model of drilling extraction in circle equipotential boundary
- Fig. 4 Curved face chart of gas concentration surface (Z=15 m)
- Fig. 5 Relation curves between borehole amount and extraction rate, equivalent radius of single drilling
- Fig. 6 Layout of long and great diameter suction holes
J. Cent. South Univ. (2012) 19: 2591-2597
DOI: 10.1007/s11771-012-1315-8
Mechanism and experiment of substituting high drainage roadway with directional long drilling group to extract pressure-relief gas
XIE Sheng-rong(谢生荣)1, ZHAO Yao-jiang(赵耀江)2, ZHANG Shou-bao(张守宝)1,
YANG Hong-zeng(杨洪增)1, XIAO Dian-cai(肖殿才)1, TIAN Chun-yang(田春阳)1
1. College of Resources & Safety Engineering, China University of Mining and Technology (Beijing), Beijing 100083, China;
2. College of Mining Engineering, Taiyuan University of Technology, Taiyuan 030024, China
? Central South University Press and Springer-Verlag Berlin Heidelberg 2012
Abstract:
By establishing the numerical model in the vertical plane and the similar model in the horizontal plane of gas flow in goaf, the influence of high drainage roadway or drilling on the gas seepage field was analyzed, and the extraction mechanism was clarified. On this basis, the academic thought of directional long drilling group instead of high drainage roadway was put forward. And then using complex function theory, the permeation mechanical model of drilling group with circle distribution in the mining-induced fracture zone was established to explore the coupling relationship between the drilling quantity, extraction volume and the equivalent extraction rate of single drilling. Finally, combined with the concrete geological production conditions, the main parameters of directional long drilling group were determined. The distance between the drilling group center and the air-return roadway is 24 m, the height is 18 m, and the three drillings are in an approximate equilateral triangle distribution with a space of 8 m. The equivalent extraction square is 4.15 m2. It is shown that the effect of directional long drilling group is evident. The gas content in the upper corner is controlled below 0.95%, the content in the tail roadway is kept below the alarm value, and the content is over 50% in the drill, realizing the secure and effective extraction of coal and gas.
Key words:
1 Introduction
Coal gas has always been the critical factor restricting the secure and effective extraction of coal mines, and gas management is the precondition and foundation to achieve the extraction of coal. After years of hard work of many scholars, theory of pressure relief gas extraction and a technical system of co-mining of coal and gas have been established [1]. Based on the release mining theory, gas seepage law is researched by means of laboratory experiment [2], coupling model [3] and numerical simulation [4-5]. This theory and technical system has been widely applied in coal mines under different coal seam deposit conditions [6-8], and a number of new gas control methods including surface goaf gas drainage [4, 9], drilling-slotting-extracting integration technology [10], extracting current seam gas by floor rock roadway [11] and combined gas control by extraction and pressure balancing ventilation [12] are proposed. But the gas control under complex conditions remains a problem, and still needs further research.
The Shaqu Colliery faces the gas control problem from the start mining of coal seam No. 4 with complex condition of close distance and high gas content. Since it went into production in 2004, the problems of gas over limit remain unsolved though many kinds of conventional gas extraction methods were tried. So, the directional drilling machine DDR-1200 was introduced from Germany to improve the related gas management technology. Extracting the press relief gas by directional long drill is one of the major development directions for underground gas extraction. Some field researches on extracting relief gas with this long drill have been done [8, 13-14]. The common way is to arrange the drills in the fracture zone and gas gathering area, and the determination of drill amount is simply expressed by the efficiency because of increase or decrease in drill quantity, without consideration of the extraction effect and mutual interference in the drilling group. In some Chinese mining groups such as Huainan, Yangquan, and Pingmei, high drainage roadway is applied, but there are some disadvantages for this method: large work quantities, difficult mining and development replacement, and high risk. So, the academic thought of directional long drilling group instead of high drainage roadway was put forward. The permeation mechanical model of drilling group with circle distribution in the mining-induced fracture zone was established to explore the mutual interference problem in the drilling group. Finally, the technology of directional long drilling group and optimal design method were proposed, applying theoretical basis for the drilling arrangement and parameter determination. The drilling group not only extracted the high concentration gas efficiently, but also controlled the goaf gas seepage field, solving the problem of gas over limit and promoting the technology development of simultaneous extraction of coal and gas.
2 Extraction mechanism of drilling or high drainage roadway
2.1 Mechanism of extracting pressure-relief gas by high drainage roadway or drilling
Both theory and practice have shown that to extract gas efficiently, the roadway or drilling should be located in the area of high gas desorption rate, high permeability and high concentration. After the coal is mined out, there will be an annular fracture zone formed in the overlying strata above the goaf, which is the so-called high position fracture ring for effective gas drainage. This ring is the main channel for gas accumulation and migration, and it is also the optimum position for the drainage roadway or drilling [15-17]. Under the action of negative pressure and concentration gradient, pressure-relief gas in goaf flows into the extraction drilling along the fissure in form of diffusion and seepage. So it is wise to put the drainage roadway or drilling group in the exhaust side of high position fracture ring. It can not only extract the high concentration gas for long term steadily, but also disturb the gas seepage field in goaf. In order to research the influence of drainage roadway or drilling on the goaf seepage field, the numerical model in the vertical plane and the similar simulation model in the horizontal plane of gas flow in goaf under conditions of extraction and no-extraction are built individually, providing guidance for location of large diameter drilling in the goaf roof.
To simplify the question, the uniform flow was adopted to show the relationship between extraction and seepage field. The inlet wind velocity was 1 m/s, and thirty measure points were set on the inlet boundary. By monitoring streamline of these points, a comparative analysis of seepage field with and without extraction roadway was done. The results are shown in Fig. 1. Known from Fig. 1(a), the face streamline was in uniform and symmetrical distribution before the extraction generally. Practice has proved that the leaking wind from the airflow inlet side of working face always flows into the goaf. By action of negative pressure, the pressure-relief gas moves along with the main airflow or leaking air. With the advance of face streamline, the released gas from the fracture zone of high gas coal seam No. 2 and 3 flowed in. So, the gas concentration along the streamline direction increased gradually, and the gas concentration of middle-upper part of goaf increased faster. If the high concentration gas was not exhausted in time, it would flow into the working face and the problem of gas over limit would occur in the upper corner. From Fig. 1(b), if the drainage roadway or drilling group was arranged at the exhaust side of high position fracture ring, high concentration gas around middle-upper goaf and drilling would flow in directly, while the gas in the lower zone flowed into the working face by action of negative pressure. As a result, it was favorable to control the air flow of goaf and reduce the gas migration into the face and upper corner if the drainage roadway or drilling was in lower area.
Fig. 1 Numerical simulation of flow field in vertical plane: (a) Seepage field without negative pressure; (b) Seepage field with negative pressure
Figure 2 shows the smoke flow in goaf after the drainage roadway was added to the “U+L” ventilation system. It could be known that the trajectory of smoke from the intake airflow roadway was approximate to a flow field composed of an intake airflow roadway and a high drainage roadway. The streamline gathered in the entrance of high roadway obviously. Only in the last stage, the deeper goaf smoke flowed back to the air-return and gas tailing roadway. So the barrier formed by flow field of the high drainage roadway prevented the movement and gather of most gas brought back by the leaking wind.
Fig. 2 Typical pictures for fluid flow in coal-mining plane of gob: (a) Goaf air leaking near working face flow into high drainage roadway; (b) Air leakage of deep goaf flow into gas tail roadway
2.2 Permeation model of drilling group extracting gas in mining fracture zone
Under the condition of directional long drilling group extraction, the gas flow in the mining fracture zone above the goaf roof was affected by many factors. Known from the permeability dynamics, under the same condition, the smaller the space between the drilling was, the worse the interaction and the lower the extraction efficiency of each drilling. So, it was wise to layout the drilling group in a circle. To simplify the question and determine the relationship between the main factors, the following basic assumptions were made for the model of steady gas flow under condition of directional long drilling group extraction in the fracture zone:
1) There was little temperature change in the gas flow field, and the gas flow in the fracture zone was isothermal;
2) Gas was considered to be ideal fluid and its flow obeyed the Darcy Law and mass conservation law;
3) It was homogeneous in the fracture zone, that was to say, Kx=Ky=Kz=K;
4) In the vertical plane of fracture zone, the gas was approximately considered as incompressible fluid and its flow caused by single drilling extraction was steady in the radial direction;
5) The gas extraction volume by drilling was fixed and the negative pressure of each drilling was equal;
6) Ventilation negative pressure had little effect on the gas above fracture zone. The field measurement showed that the differential pressure between intake and return air was only about 260 Pa, which was far lower than the extraction negative pressure (18.66-23.99 kPa), so the effect of the ventilation negative pressure can be neglected;
7) The directional drilling group was to substitute the high drainage roadway, so the permeation mechanical model of high drainage roadway was just to research the influence of group radius and equivalent single extraction radius on extraction effect;
8) There was little influence of circle or line boundary for extraction drilling on the extraction effect.
So, to simplify the calculation, the plane permeation mechanical model of drilling group can be equivalently substituted as the gas flow under condition of drilling group in circle arrangement in a circle area.
Based on above assumption, the gas permeation model of drilling extraction in the circle equipotential boundary was built, as shown in Fig. 3. The gas permeation area was a circle with the radius of R, and the boundary was equipotential; the drilling was in circle arrangement and the radius was R1 with the same centre of equipotential boundary; the position of the extraction drilling center was z0(z0=x0+iy0), the drilling radius was rw, the extraction strength was q, and the opposite sign mirror lied outside the circle with a direction of .
Fig. 3 Gas permeation model of drilling extraction in circle equipotential boundary
As for the two-dimensional steady seepage, the complex function theory can simplify the question. According to the complex potential theory and mirror image theory, the complex potential function of single drilling in the circle area could be derived:
(1)
Assume that the X axis passed the junction, then (d was the distance between the junction and origin), and the potential function was
(2)
where r1 was the distance between junction and field point; r2 was the distance between the mirror point R2/d and field point.
By the triangular geometry relationship, it was easy to prove that the mathematical relation r1/r2=d/R was right for any point in the equipotential boundary circle. And then by locating the field point in the drilling wall and the equipotential boundary, following function could be got:
(3)
where and
were the potential functions of the field point in the equipotential boundary and drilling wall, respectively; 2a was the distance between the junction in the circle and its mirror point outside the circle.
By the gas flow theory, following complex potential function was introduced:
(4)
where λ was the permeability coefficient of the rock stratum, m2/(MPa2·d); P was square of gas pressure, and P=p2, MPa2; p was the gas pressure of position z, MPa.
Assume that the effective extraction length was M, Φ=kP/μ, then the extraction volume of single drilling on the equipotential boundary was
(5)
where Pe and Pw were the square of gas pressure at the equipotential boundary and drilling wall, respectively.
If there were n drillings equally distributed on the circle with the radius of R1, the extraction volume of each drilling was Qj, and the negative pressure and extraction volume of each drilling were equal. According to the superposition principle, the pressure formula could be derived by Eq. (2):
(6)
(7)
where ∑ stands for that there was no items of i=j; rij stands for the distance between the i-th drilling and the j-th one.
Let ΔP=Pe-Pw, the volume of each drilling was equal, and the total extraction volume was
(8)
The equivalent circle of each drilling was
(9)
Seen from Eq. (8), such conclusion could be got that with the increase of drilling amount, the interaction would increase, and the extraction volume of each drilling decreased. But when drilling amounted to a certain number, the increased extraction volume could not cover additional cost.
3 Parameters determination of large diameter drilling group and its application
3.1 Engineering situation
Shaqu Colliery lies in the Liuli mine area of middle of Hedong coal field in west of Shanxi Province. It is a mine with high coal and gas outburst danger, and the coal seam presents characteristics of high gas content, short distance, multilayer coal and instability. The fully mechanized face No. 14205 extracts coal seam No. 4 with an average thickness of 2.45 m and dip of 2°-7°. The adjacent coal seam is No. 2, 3 and 5 from top to bottom, and the coal space is less than 10 m. These coal seams are all with high gas content and the original gas content of No. 4 coal is 30.73-41.25 m3/t, and it is more than 20 m3/t for the adjacent coal (No. 3 and 5). Field data show that the gas content by ventilation and extraction amounts to over 100 m3/min. Despite many kinds of extraction ways, the gas in upper corner and return air is always over the limit which severely affects normal production and safety.
3.2 Parameters determination of directional long drilling group
The parameters of directional long drilling group mainly include drilling location, quantity and space. The determination method was used to determine the reasonable position of high drainage roadway within the return air side of high fracture ring and high gas area. Centered on the center of the high drainage roadway and based on the permeation mechanical model of drilling group in a circle arrangement, the drilling quantity and distribution radius were researched and determined.
3.2.1 Optimization of high drainage position
1) Position determination of high drainage in horizontal direction
It was concluded by numerical simulation that the thickness of caving zone was about 10 m, and the fracture zone was about 30 m high, so the high drainage roadway or the drilling should be located in the fracture zone of 10-25 m above the coal roof and 10-35 m away from the return air side. According to the geology production condition of fully mechanized face of No. 14205 and the fundamental parameters of fracture distribution, the CFD model of goaf gas seepage goaf was established. Figure 4 shows the gas concentration surface (Z=15 m) in the model. In the range of 10-35 m away from the return air side and 20 m away from the working face, the gas content was 9.5%-18.2%; it was 17.7%-38.4% within 20-38 m from the face, 63.8% deeper in goaf, and went on increasing further in goaf. The concentration within 20-28 m was higher than that within 5-20 m and 28-35 m. As a result, the high drainage roadway or drilling group should be located in the range of 20-28 m from the return air side. Based on the above research, level center of the drainage roadway was 24 m from the return air side, which can meet requirements of extracting high concentration gas as long as the extraction height was over 15 m.
Fig. 4 Curved face chart of gas concentration surface (Z=15 m)
2) Position determination of high drainage in vertical direction
Added to high drainage roadway in the model which was 24 m from the return air side, the simulation was done according to the different roadway heights (Z) of 15, 18, 21 and 24 m. The high drainage roadway was rectangular with 2.0 m high and 2.0 m wide. As shown by the numerical simulation results, the gas content in upper corner was 6.92%, 6.65%, 7.86% and 11.43% corresponding to the roadway heights of 15, 18, 21 and 24 m. Combined with the seepage analysis on the gas extraction in the vertical direction of goaf, it could be included that when the drainage roadway height changed from 15 to 18 m, the control of roadway over the gas flow field weakened in the lower goaf, and strengthened in the upper goaf, so the gas content in the upper corner reduced from 6.92% to 6.65%. With the increase of roadway height, the control over the gas flow field in the lower goaf went on weakening. The gas in this area flowed into the return air roadway directly, resulting in the content increasing in the upper corner. When the height was 24 m, the content was 11.43%, and it went on increasing. By the analysis above, the best position for the gas control in goaf was 18 m.
3.2.2 Parameters determination of directional long drilling group
The large diameter drilling of 200 mm was applied in the fully mechanized face No.14205 of Shaqu Colliery. When the distribution radius was 4.5 m, the relationship between the group quantity and extraction rate of single drilling, equivalent single extraction radius could be derived according to Eqs. (8) and (9), as shown in Fig. 5.
Fig. 5 Relation curves between borehole amount and extraction rate, equivalent radius of single drilling
As can be seen from Fig. 5, in circumstances of certain drilling radius and distribution radius, when the drilling quantity increased from 2 to 5, the single extraction rate reduced from 85.22% to 52.10%, and the decline rate gradually decreased. If the drilling quantity went on increasing, the growth rate of equivalent extraction radius for single drilling decreased dramatically. So, taking the engineering quantity and duration into consideration, two or three drilling groups were chosen to substitute for the high drainage roadway, and the equivalent extraction radius of two and three drilling groups were 1.34 and 4.15 m2, respectively. Considering the extraction effect, the drilling group was three. It could be included from Eqs. (8) and (9) that on the basis of certain drilling radius and quantity, with the increase of the extraction distribution radius, the extraction rate and equivalent extraction radius for single drilling increased, while the increasing rate became smaller gradually. So centered on the center of the drilling group, it was wise to use larger distribution radius. In order to make sure that the drill was in the rock seam instead of coal seam No. 3, the minimum distance between the group and the No. 3 coal seam was 2 m.
Based on the above research results and the convenience for construction, the drilling quantity of the drilling group was 3, and drilling No. 1 and 3 were located at 13 m away from the roof of coal No. 4, drilling No. 2 was at 20 m. The negative pressure of the drillings was 18.66-23.99 kPa. According to the distribution style of the drilling group in the roof fracture zone, the extraction technology of directional long drilling groups for Shaqu Colliery was proposed, as shown in Fig. 6.
Fig. 6 Layout of long and great diameter suction holes
3.3 Analysis of extraction effect
After the technology of directional large drilling group was applied in the fully mechanized face No. 14205, the gas content of upper corner was 0.63%-0.95%, preventing the gas over limit. The content range in the tail roadway was 1.33%-2.34% that was less than the alarm value of 2.5%, and the gas content of the extraction drilling was 55%-72%. The field practice showed that this technology solved the gas control problem effectively and the extracted gas in the drill was in high content, achieving the safe and efficient extraction for coal and gas.
4 Conclusions
1) The air return side of high fracture ring is the main thoroughfare for gas aggregation and migration, and also the best distribution area for extraction roadway or drilling group. The height of Z=18 m in high drainage roadway is the best equilibrium position controlling the gas flow field.
2) The permeation mechanical model for drilling group with circle distribution in the fracture zone is established, and based on the numerical simulation results and site actual condition, it is finally determined that three drillings in approximate equilateral triangle distribution is appropriate. The space is 8 m and the equivalent extraction area is 4.15 m2.
3) It is effective and safe by applying the technology of directional large drilling group substituting for the high drainage roadway to treat the problem of gas over limit, and the extraction content amounts to 50%, promoting the technology advance of gas treatment and enriching the technology system of efficient extraction for coal gas.
References
[1] YUAN Liang. Theory of pressure-relieved gas extraction and technique system of integrated coal production and gas extraction [J]. Journal of China Coal Society, 2009, 34(1): 1-8. (in Chinese)
[2] LI Shu-gang, XIAO Peng, PAN Hong-yu, LIN Hai-fei, CHENG Lian-hua. Experimental investigation on the seepage law of pressure-relieved gas under the influence of mining [J]. Safety Science, 2012, 50(4): 614-617.
[3] YANG T H, XU T, LIU H Y, TANG C A, SHI B M, YU Q X. Stress-damage-flow coupling model and its application to pressure relief coal bed methane in deep coal seam [J]. International Journal of Coal Geology, 2011, 86(4): 357-366.
[4] KARACAN C ?, DIAMOND W P, SCHATZEL S J. Numerical analysis of the influence of in-seam horizontal methane drainage boreholes on longwall face emission rates [J]. International Journal of Coal Geology, 2007, 72: 15-32.
[5] ZHANG Yong-jun, MA Nian-jie, ZHANG Zi-min, JIA Tian-rang. Numerical simulation of gas distribution and mined seepage passage with the pressure relief of short distance protective coal stratum [J]. Applied Mechanics and Materials, 2012, 105/106/107: 1517-1520.
[6] CHENG Yuan-ping, FU Jian-hua, YU Qi-xiang. Development of gas extraction technology in coal mines of China [J]. Journal of Mining & Safety Engineering, 2009, 26(2): 127-139. (in Chinese)
[7] SANG Shu-xun, XU Hong-jie, FANG Liang-cai, LI Guo-jun, HUANG Hua-zhou. Stress relief coal-bed methane drainage by surface vertical wells in China [J]. International Journal of Coal Geology, 2010, 82: 196-203.
[8] GUO Hua, RAO BALUSU, DEEPAK ADHIKARY. Coal mine gas drainage and recent development in Australia [C]// Chinese International Conference on Coal Mine Gas Control and Utilization. Huainan: 2008: 159-183.
[9] BALUSU R, TUFFS N, WHITE D, HARVEY T. Surface goaf gas drainage strategies for highly gassy longwall mines [J]. Journal of the Mine Ventilation Society of South Africa, 2006, 59(3): 78-84.
[10] LIN Bai-quan, MENG Fan-wei, ZHANG Hai-bin. Regional gas control based on drilling-slotting-extracting integration technology [J]. Journal of China Coal Society, 2011, 36(1): 75-79. (in Chinese)
[11] LIU lin, CHENG Yuan-ping, WANG Hai-feng, WANG Liang, MA Xian-qin. Principle and engineering application of pressure relief gas drainage in low permeability outburst coal seam [J]. Mining Science and Technology, 2009, 19(3): 342-345.
[12] WANG Fang-tian, Ren T X, Hungerford F, TU Shi-hao, AZIZ N. Advanced directional drilling technology for gas drainage and exploration in Australia coal mines [J]. Procedia Engineering, 2011, 26: 25-36.
[13] YUAN Liang. Theory and technology of gas drainage and capture in soft multiple coal seam of low permeability [M]. Beijing: China Coal Industry Publishing House, 2004: 116-138. (in Chinese)
[14] CAI Feng. Big diameter and long drilling-holes technology and its application in drainage gas in Dingji coal mine [J]. Advanced Materials Research, 2012, 354/355: 104-108.
[15] ZHANG Mei-hong, WU Shi-yue, WANG Yong-wen. Research and application of drainage parameters for gas accumulation zone in overlying strata of goaf area [J]. Safety Science, 2012, 50(4): 778-782.
[16] WANG Liang, CHENG Yuan-ping, LI Feng-rong, WANG Hai-feng, LIU Hai-bo. Fracture evolution and pressure relief gas drainage from distant protected coal seams under an extremely thick key stratum [J]. Journal of China University of Mining and Technology, 2008, 18(2): 182-186.
[17] LIU Hong-yong, CHENG Yuan-ping, ZHOU Hong-xing, WANG Feng, CHEN Hai-dong. Fissure evolution and evaluation of pressure-relief gas drainage in the exploitation of super-remote protected seams [J]. Mining Science and Technology, 2010, 20(2): 178-182.
(Edited by YANG Bing)
Foundation item: Project(50834005) supported by the National Natural Science Foundation of China; Project(2010QZ06) supported by the Fundamental Research Funds for the Central Universities of China
Received date: 2011-11-07; Accepted date: 2012-03-29
Corresponding author: XIE Sheng-rong, PhD; Tel: +86-13810521426; E-mail: xsrxcq@163.com
Abstract: By establishing the numerical model in the vertical plane and the similar model in the horizontal plane of gas flow in goaf, the influence of high drainage roadway or drilling on the gas seepage field was analyzed, and the extraction mechanism was clarified. On this basis, the academic thought of directional long drilling group instead of high drainage roadway was put forward. And then using complex function theory, the permeation mechanical model of drilling group with circle distribution in the mining-induced fracture zone was established to explore the coupling relationship between the drilling quantity, extraction volume and the equivalent extraction rate of single drilling. Finally, combined with the concrete geological production conditions, the main parameters of directional long drilling group were determined. The distance between the drilling group center and the air-return roadway is 24 m, the height is 18 m, and the three drillings are in an approximate equilateral triangle distribution with a space of 8 m. The equivalent extraction square is 4.15 m2. It is shown that the effect of directional long drilling group is evident. The gas content in the upper corner is controlled below 0.95%, the content in the tail roadway is kept below the alarm value, and the content is over 50% in the drill, realizing the secure and effective extraction of coal and gas.
- Mechanism and experiment of substituting high drainage roadway with directional long drilling group to extract pressure-relief gas
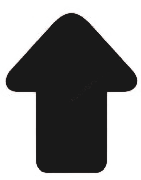