- Abstract:
- 1 Introduction▲
- 2 Experimental▲
- 3 Results and discussion▲
- 4 Conclusions▲
- References
- Figure
- Fig.1 XRD diagram of waste fluorgypsum
- Fig.2 Preparation of acidic modified solution
- Fig.3 Modification process of waste fluorgypsum
- Fig.4 Schematic drawing of cement injection device
- Fig.5 SEM image of hydration products of waste fluorgypsum
- Fig.6 SEM image of hydration products of modified fluorgypsum
- Fig.7 Effect of modified fluorgypsum and
- Fig.8 Effect of modified fluorgypsum and fly ash co-dopped cement on cement hydration heat
J. Cent. South Univ. Technol. (2011) 18: 1402-1407
DOI: 10.1007/s11771-011-0853-9
Modification of waste fluorgypsum and its applications as a cement retarder
YAO Yan(姚艳), YANG Dao-wu(杨道武), TONG Hai-xia(童海霞), ZENG Ju-lan(曾巨澜), LIU Yi(刘义)
School of Chemistry and Biological Engineering, Changsha University of Science and Technology,Changsha 410114, China
? Central South University Press and Springer-Verlag Berlin Heidelberg 2011
Abstract:
The waste fluorgypsum was modified and applied as a cement retarder. The main chemical composition and mineral structure of the waste fluorgypsum were analyzed. Scanning electron microscopy (SEM) and eight-channel micro-calorimeter (TAM Air) were employed to analyze the changes in morphology and study the application performance of the modified fluorgypsum, respectively. Experimental results indicate that the flexural strength and compressive strength of the modified fluorgypsum are roughly equal to those of the natural gypsum. The morphology of the crystal of the fluorgypsum changes from block particle into trimetric short column. The fluorgypsum crystals stagger mutually and improve the strength of the hardened body. The modified fluorgypsum as cement retarder could delay the hydration, reduce the heat of the hydration and make the setting time, volume stability, and the SO3 content of the cement meet the national standards. The modified fluorgypsum is a good substitute for the natural gypsum.
Key words:
waste fluorgypsum; modified technology; hydration heat; cement retarder; application performance;
1 Introduction
Fluorgypsum, as an industrial chemical waste residue, is produced by the reaction of sulfuric acid and fluorite during the process for producing hydrofluoric. For 1 kg of hydrofluoric acid, there is approximately 4 kg of fluorgypsum produced and the present domestic output of fluorgypsum is more than one million tons. The waste fluorgypsum occupies considerable land and contaminates air and water sources if it is not utilized appropriately [1-3]. How to utilize the waste fluorgypsum is a very important and urgent issue.
Demand for cement in China exceeded 1.2 billion tons in 2010, which results in the increase of the demand for natural gypsum [4-6]. To exploit and use fluorgypsum as a substitute for natural gypsum reasonably and efficiently can not only save the resources of natural gypsum and lower the cost of gypsum mining, but also benefit the environment [7]. During the last decade, some researches that focused on applying the waste fluorgypsum directly as a cement retarder had been published, but that kind of cement appeared “false coagulated”. It is mainly because that the speed of hydration and dissolution of the waste fluorgypsum are very slow [8]. These disadvantageous factors restrict the application of the waste fluorgypsum in cement. So, the modification of fluorgypsum with addition of activator, water reducing agent, water retaining agent, admixture and aggregate were reported. The properties of fluorgypsum were improved, but the alkalinity which can affect the performance of cement was increased. Thus, the content of fluorgypsum in cement was only 3% [9-11]. Besides, the studies on the effect of fluorgypsum as a cement retarder to the heat of hydration of cement are less reported.
In the present work, a different approach was adopted and a kind of acidic modified solution was used to neutralize the excess alkalinity. The water-retaining agent, K2SO4 and semi-hydrated gypsum were added to stimulate its activation. Scanning electron microscopy was employed to investigate the changes of the morphology. The effects of the modified fluorgypsum on the hydration heat of cement were also investigated by the eight-channel micro-calorimeter (TAM Air).
2 Experimental
2.1 Materials
The waste fluorgypsum was obtained from Hunan Nonferrous Fluorine Chemistry Co., Ltd., and its density and specific surface area are 2.91 g/cm3 and 656 m2/kg, respectively. The water content is about 0.02%. Because of some unreacted lime, the pH value of the waste fluorgypsum with mass fraction of 10% is about 8.89, and the major composition is presented in Table 1 and the X-ray diffraction (XRD) pattern is shown in Fig.1. From Fig.1, peaks of CaSO4, CaSO4?0.5H2O and CaF2 can be seen. And the content of anhydrite is 95% from the chemical analysis.
Table 1 Compositions of waste fluorgypsum (mass fraction, %)
Fig.1 XRD diagram of waste fluorgypsum
The fly ash complying with Chinese National Standard GB 1596—91 was from Hunan Xiangtan Power Generation Co., Ltd. It was dried at 353.15 K for 24 h, and then sifted by 74 μm sieve. Its loss on ignition is 3.5%, and the specific surface area is 5 400 cm2/kg. 425# cement was purchased from Hunan Xiangxiang Cement Manufacturing Co., Ltd. It was dried for 24 h at 353.15 K, and then sifted by 74 μm sieve before used. The acid waste residue from the fluoride salt factory was washed with warm water at 318.15 K, and then the wash solution was recycled, cooled, filted and heated at 318.15 K for 1 h to obtain the acidic modified solution. The preparation process is shown in Fig.2.
2.2 Modification of waste fluorgypsum
The modified fluorgypsum can be obtained through the following steps: 1) The excess alkalinity of the waste fluorgypsum was neutralized by adding the self-prepared acidic solution. After vigorous stirring for 5 min, the fluorgypsum was dried at 378.15 K for 2 h and then cooled in air; 2) The fluorgypsum and water-retaining agent in 100:0.3 mass ratio were mixed for 1-2 min under vigorous stirring. And then, the mixed solid and water in 100:(15-25) mass ratio were mixed and stirred for 3-5 min. At last the mixture was laid aside for 4-6 d and dried at 423.15 K for 3 h; 3) After dried, the modified products were added with grinding aid (0.5% K2SO4 solution). The fineness was controlled through a 66 μm sieve and no less than 97% passes through a ball mill grinding; 4) The fluorgypsum and hemihydrate gypsum in 100:0.3 mass ratio were mixed. Then, the modified fluorgypsum was obtained. The modified process is shown in Fig.3.
2.3 Methods used for investigation
2.3.1 Basic properties tests
The pastes of the hardened fluorogypsum were mixed by machine for 3 min, and then cast into moulds (40 mm × 40 mm × 40 mm) for the strength tests after 3, 7 and 28 d in accordance with the GB 9776—88. Some of the fragmented pieces were ground using a mortar and then dried in a vacuum oven at 313.15 K for 24 h. The water-to-solid ratio was kept at 0.5 for all pastes in order to provide the same amount of water while having workable pastes.
The normal consistency and setting time were measured in the Key Laboratory of Road and Traffic Engineering of the Ministry of Education according to GB/T1346—2001 and GB 9776—88, respectively.
Fluorgypsum, gypsum, fly ash and cement were blended according to the proportion listed in Table 4. The mixture was ground in a ball mill to fineness similar to Portland cement. The water-to-binder ratio of the pastes is 0.26. The pastes were mixed by machine for 3 min, and then cast into moulds (40 mm × 40 mm × 160 mm) for the strength tests after vibrated for 2 min. The samples were kept in air at (293.15±2) K for 24 h. After demoulded, part of the samples was cured in air at (293.15±2) K, and the rest was cured in water at (293.15±2) K until the day of test. The restrained samples were cured only in air. The corresponding pastes were prepared and cured in the same conditions.
Fig.2 Preparation of acidic modified solution
Fig.3 Modification process of waste fluorgypsum
2.3.2 SEM analysis
The strength of the hardened fluorgypsum was determined at the scheduled ages. Crushed pastes were washed with alcohol and dried at 353.15 K for 5 h to stop hydration at the same age. Then, the middle of the original section of the hardened specimens was tested after gold plating. Scanning electron microscope (Japan JSM-5600LV) was used to investigate the morphology of the specimens.
2.3.3 Hydration heat tests
The values of hydration heat of the pure and modified cement were recorded by an eight-channel micro-calorimeter (3114/3236 TAM Air, Swiss). The calorimeter was electrically calibrated at 293.15 K and 303.15 K before experiment. 6.0 g of freshly mixed cement paste was added into a glass vial of internal diameter 22.5 mm.
The ingredients added to each bottle are listed in Table 2. The ampoule bottles were sealed. Afterward, as shown in Fig.4, the ampoule bottle was connected to a liquid storage tank which was then connected to an injector. Grade II desalted water was stored in the liquid storage tank. Then, these ampoule bottles were put into the experimental side of the micro-calorimeter, while the ampoule bottles which were filled with equivalent amount of completely hydrated pure cement were put into the reference side. The calorimeter was stabilized at constant temperature (293.15 K or 303.15 K) for 8 h. When the baseline reached stable, the desalted water in the liquid storage tank was poured into the ampoule bottles by twitching the injector for five times. The ratio of water to cement was 0.5. Due to the sufficient water, the water and the solid can be mixed well. The hydration was started and the thermal spectra were recorded. During the experiment, the measuring cells within the calorimeter were kept at constant temperature with accuracy of ±0.02 K.
Table 2 Ingredient of samples at 303.15 K
Fig.4 Schematic drawing of cement injection device
3 Results and discussion
3.1 Comparison of basic properties of modified fluorgypsum and waste fluorgypsum
The basic parameters of waste fluorgypsum and modified fluorgypsum are listed in Table 3. As can be seen from Table 3, the setting time of the waste fluorgypsum is very long and its 28 d compression strength is only 1.2 MPa. So, the waste fluorgypsum is not favorable to the stability of the late stage and cannot meet the needs of the project. The initial setting time and final setting time after modification are shortened to 40 min and 90 min, respectively. And the flexural strength and compressive strength of the modified fluorgypsum are roughly equal to those of natural gypsum.
The solubility of fluorgypsum is higher in an acidic environment than in alkaline environment. And the acidic environment benefits to the crystallization, the hydration and hardening of the fluorgypsum. So, it can be seen from Fig.3 that the excess alkalinity of the waste fluorgypsum is neutralized by the self-prepared acidic modified solution and the pH value for 10% fluorgypsum is maintained at 6.0-6.5. The water-retaining agent can increase the water retention of fluorgypsum. The hydration of fluorgypsum is from the outside to the inside. The hydration rate is low because of the dense granular texture and great hardness. The grain refinement and the large surface area, which can improve the dissolution rate of fluorgypsum and stimulate the hydration activity of fluorgypsum, can be achieved by grinding. The semi-hydrated gypsum plays a role as developing the seed due to the secondary nucleation. These factors can improve the hydration activity of the waste performance.
Table 3 Comparison of basic performance of waste and modified fluorgypsum
3.2 Morphology of waste fluorgypsum before and after modification
The SEM images of the waste fluorgypsum before and after modification are shown in Fig.5 and Fig.6, respectively. It can be seen from the Fig.5 and Fig.6 that the modification makes the crystal morphology of the fluorgypsum change from block or granular into trimetric and short column shape. The modified fluorgypsum crystal becomes more perfect and more slender. It takes to connect more airtight solid. The porosity of the hardened body decreases significantly, making an exaltation of the hardened body strength [12].
Fig.5 SEM image of hydration products of waste fluorgypsum
Fig.6 SEM image of hydration products of modified fluorgypsum
3.3 Application of modified fluorgypsum in cement
3.3.1 Effect of modified fluorgypsum as retarder on cement hydration
The hydration of cement is an exothermic reaction and can result in serious problem for concrete. The interior of the concrete could reach very high temperature during the hydration process. As a result, great temperature difference would exist between the interior and the outer of the concrete, which can cause serious thermal stress [13-17]. Thus, the concrete would be destroyed by the cracks resulted from the thermal stress. The heat released by the cement hydration and the hydration rate can be regulated by adding fluorgypsum as cement retarder [18-21]. The results are shown in Figs.7 and 8. The total heat of hydration equals the area under the curves, and the change trend of hydration heat is similar to that of the voltage.
Fig.7 Effect of modified fluorgypsum and natural gypsum on cement hydration heat
Fig.8 Effect of modified fluorgypsum and fly ash co-dopped cement on cement hydration heat
Figure 7 shows that the modified fluorgypsum could also reduce the hydration heat of cement as same as the natural gypsum, mainly because the hydration heat of the modified fluorgypsum is lower than that of the cement. When the cement is replaced by the commensurably modified fluorgypsum, the hydration heat is reduced.
Figure 8 shows that the modified fluorgypsum or natural gypsum as the blended cement retarder could both reduce the heat of hydration of cement and delay the cement hydration reaction. It is easy to conclude that the modified fluorgypsum is a good substitute for natural gypsum.
3.3.2 Comparison of application performance of modified fluorgypsum and natural gypsum
To determine whether the modified fluorgypsum could completely replace the natural gypsum as cement retarder, some physical indicators of the modified fluorgypsum application in cement were detected according to the national standards. The testing results of the modified fluorgypsum and natural gypsum in cement are listed in Table 4.
It can be seen from Table 4 that when the modified fluorgypsum is used as cement retarder, the setting time, stability and the SO3 content etc. can also meet the national standards. The higher content of sulfur trioxide leads to a relatively high compressive strength within a certain range. If the content of SO3 exceeds a certain limit, it will continue to hydrate and swell after cement hardening so that it causes the destruction of the hardened cement and reduces the strength. The flexural strength and compressive strength of the cements with modified fluorgypsum and natural gypsum after 3 d and 28 d are roughly equal. This is because that the modified fluorgypsum and fly ash can fill the gaps of each other and make concrete stronger. This phenomena is consistent with the hydration heat. The hydration rate of the co-doped cement is accelerated and the development of early strength of cement is promoted by CaF2 of the fluorgypsum. Besides, the cement can be used as an alkali-activator for the early activation of fly ash, then the dissolution and hydration of fluorgypsum are accelerated due to the Si-Al active components of fly ash, and the modified fluorgypsum can in turn be used as sulfate activator for fly ash. Hence, the synergy effect of cement, modified fluorgypsum and fly ash is exhibited and the strength of co-doped cement is further enhanced.
Table 4 Comparison of application performance of modified fluorgypsum and natural gypsum
4 Conclusions
1) The basic parameters of the modified performance are improved greatly. The flexural strength and compressive strength of the modified fluorgypsum are roughly equal to those of the natural gypsum.
2) The crystal morphology of fluorgypsum changes from block or granular into trimetric or short column shape. The modified fluorgypsum crystal becomes more perfect and more slender.
3) Fluorgypsum single-dopped cement or fluorgypsum and fly ash co-dopped cement as cement retarder can delay the reaction of cement hydration and reduce the heat of hydration of cement.
4) Using the modified fluorgypsum as cement retarder, the setting time, stability and SO3 content can also meet the national standards.
References
[1] FENG Qi-biao, WANG Jun-hui, ZHANG Xin, WANG Liang-liang, CHEN Yong-liang. Study on comprehensive utilization of fluorgypsum [J]. Non-Metallic Mines, 2010, 33(3): 36-38. (in Chinese)
[2] JIANG Xiao-hu. The application status and analysis of fluorine gypsum [J]. Shanxi Architecture, 2008, 34(20): 161-162. (in Chinese)
[3] LI Ru-yi. Exploration and practice of comprehensive utilization of fluorgypsum residue [J]. Safety and Environmental Engineering, 2006, 13(1): 55-58, 65. (in Chinese)
[4] LI Ru-yi, YU Ran-gang, CHEN Jin-ping, CHEN Xiao-guang. The comprehensive utilization of fluorgypsum residue in building material [J]. Inorganic Chemicals Industry, 2005, 37(12): 43-46. (in Chinese)
[5] XU Qing. Comprehensive utilization discussion on fluorine gypsum of fluorid salt factory [J]. Light Metal, 2000(10): 12-15. (in Chinese)
[6] ZHU Xiao-li, YANG Xiao-wen. Experiment on using fluorine gypsum as retarder instead of natural gypsum [J]. Journal of Tangshan Polytechnic College, 1999(4): 29-31. (in Chinese)
[7] TIAN Jing-cheng. Study on comprehensive utilization of fluorgypsum [J]. Journal of Xuzhou Engineering College, 2005, 20(1): 104-107. (in Chinese)
[8] YANG Miao, GUO Zhao-hui, WEI Xiao-ying, XIAO Xi-yuan. Modification and comprehensive utilization of fluorgypsum [J]. Organo-Fluorine Industry, 2010(1): 9-41, 21. (in Chinese)
[9] YAN Pei-yu, YANG Wen-yan. The cementitious binder derived with fluorogypsum and low quality of fly ash[J]. Cem Concr Res, 2000, 30(2): 275-280.
[10] YANG Xin-ya, MU Shan-bin, WANG Jin-hua. Modification of fluor-gypsum and its application as a cement retarder [J]. China Cement, 2006, 50(6): 52-54. (in Chinese)
[11] KOVLER K. Strength and water absorption for gypsum cement–silica fume blends of improved performance [J]. Adv Cem Res, 1998, 10(2): 81-92.
[12] YU De-gao, YANG Xin-ya, YANG Shu-zhen, ZHANG Li-ying. A research on the properties and microstructure of hemihydrate gypsum [J]. Journal of WuHan University of Technology, 2006,28(5): 27-29. (in Chinese)
[13] RAHHAL V, CABRERA O, TALERO R, DELGADO A, PEDRAJAS C. C4AF ettringite and calorific synergic effect contribution [J]. J Therm Anal Calorim, 2010, 100(1): 57-63.
[14] KJELLSEN K O, DETWILLER R J, GJORV O E. Development of microstructures in plain cement pastes hydrated at different temperatures [J]. Cem Conc Res, 1991, 21(1): 179-189.
[15] TAN Guan-zheng, WU Jian-hua, FAN Bi-shuang, JIANG Bin. Effect of CaCO3 on hydration characteristics of C3A [J]. J Cent South Univ Technol, 2010, 17(5): 1028-1035.
[16] Kjellsen K O, Detwiter R J. Reaction kinetics of Portland cement mortars hydrated at different temperatures[J]. Cem Concr Res, 1992, 22(1): 112–120.
[17] SEMSI Y, G?ZDE INAN S. The effect of cylindrical specimen size on the compressive strength of concrete [J]. Build Environ, 2007, 42(6): 2417-2420.
[18] AL-NOAIMI K KH, EL-HOSINY F I, ABO-EL-ENEIN S A. Thermal and pore structural characteristics of polymer-impregnated and superplasticized cement pastes [J]. J Therm Anal Calorim, 2000, 61(1): 173-180.
[19] PACEWSKA B, BLONKOWSKI G, WILI?SKA I. Investigations of the influence of different fly ashes on cement hydration [J]. J Therm Anal Calorim, 2006, 86(1): 179-186.
[20] YAN Pei-yu, YANG Wen-yan, QIN Xiao, YOU Yi. Microstructure and properties of the binder of fly ash-fluorogypsum-Portland cement [J]. Cem Concr Res, 1999, 29(3): 349-354.
[21] YAN Pei-yu, YOU Yi. Hydraulic properties of the binder consisting of fluorgypsum and fly ash under different curing conditions [J]. Journal of the Chinese Ceramic Society, 1998, 26(6): 689-694.
(Edited by HE Yun-bin)
Foundation item: Project(21003014) supported by the National Natural Science Foundation of China; Project(2010FJ3167) supported by the Hunan Provincial Science and Technology Program, China; Project(K1104029-11) supported by the Changsha IT Project
Received date: 2011-02-28; Accepted date: 2011-05-23
Corresponding author: YANG Dao-wu, Professor; Tel: +86-731-85258733; E-mail: daowuy@163.com
- Modification of waste fluorgypsum and its applications as a cement retarder
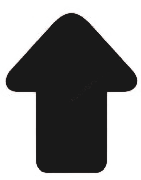