- Abstract:
- 1 Introduction▲
- 2 Experimental▲
- 3 Results▲
- 4 Discussion▲
- 5 Conclusions▲
- References
- Figure
- Fig.1 Schematic diagram of experimental set-up for water vapor oxidation test
- Fig.2 Mass gain curves of blank and CeO2-coated T91 steels oxidized in water vapor at 600 °C for up to 150 h
- Fig.3 Backscattered electron images and corresponding EPMA element line scanning images of blank and cerium-coated T91 steels oxidized in water vapor for 150 h: (a) Blank; (b) CeO2-coated
- Fig.4 SEM micrographs of fractured oxide scales of blank and cerium-coated T91 steels after oxidation in water vapor for 60 h: (a) Blank; (b) CeO2-coated
- Fig.5 Schematic diagrams of scale growth of T91 steels with and without CeO2 coating oxidized in water vapor at 600 °C: (a) Blank; (b) CeO2 coated
J. Cent. South Univ. Technol. (2011) 18: 1354-1358
DOI: 10.1007/s11771-011-0845-9
Effects of CeO2 coating on oxidation behavior of T91 steel in water vapor
YUE Zeng-wu(岳增武)1, 2, FU Min(傅敏)2, LI Xin-geng(李辛庚)2, TIAN Xue-lei(田学雷)1
1. Key Laboratory for Liquid-Solid Structural Evolution and Processing of Materials of Ministry of Education,
Shandong University, Jinan 250061, China;
2. Boiler and Pressure Vessel Inspection Center, Shandong Electric Power Research Institute, Jinan 250002, China
? Central South University Press and Springer-Verlag Berlin Heidelberg 2011
Abstract:
Oxidation behaviors of blank and CeO2 coated T91 steel were investigated at 600 °C in water vapor for up to 150 h. Gold marker was used to define the mass transport direction. The oxide scales were studied with X-ray diffractometry (XRD), scanning electron microscopy (SEM) and electron probe microanalyzer (EPMA). The oxidation resistance of the steel is improved by CeO2 coating, though the improvement is not remarkable. Ce-rich oxide band is located at the interface of the inner equiaxed layer and the outer columnar layer after oxidation, which is not consistent with the original surface. The results show that outward iron transport is blocked by the Ce-rich band. A new oxide nucleating and growing site (reaction front) is induced at the inner surface of the Ce rich band.
Key words:
high temperature oxidation; T91 steel; cerium; reactive element; diffusion;
1 Introduction
The beneficial effects of reactive element additions on the oxidation resistance of Fe-Cr alloys are well known [1-4]. Small amounts of reactive elements (such as rare earth elements) can improve the oxidation resistance of chromia-forming alloys, usually called reactive element effect (REE). The beneficial effects of rare earth elements on Fe-Cr alloy in wet atmosphere have also been clearly proved [5-7]. The reactive elements can be introduced as alloying elements and oxide coatings, or they can be implanted onto the alloy surface. The choice of coatings seems to be the most practical procedure to introduce reactive element without altering the mechanical properties of the metallic substrate, and electrodeposition is a practical technique for coating.
T91 steel was selected in the present experiments because it is widely used in advanced thermal power plants for its superior creep properties at elevated temperatures. It has been developed for use at higher temperatures than lower alloying steels and can offer attractive properties up to 650 °C. However, it is now widely acknowledged that the steam oxidation resistance of the 9% Cr (mass fraction) steels could be the factor that limits their maximum service temperature [8]. The oxide scale of T91 in steam is mainly constituted by three layers: (FeCr)3O4, Fe3O4, and Fe2O3 from the substrate to the oxide/gas interface respectively, or constituted by two layers (without outmost Fe2O3) in low oxygen content environment [9-11]. However, the nano-ceria coated T91 ferritic steel showed better oxidation resistance than uncoated steel in air and steam [7].
In this work, the oxidation kinetics and the oxide scales of blank and CeO2 deposited T91 steel were studied. Oxidizing was performed at 600 °C in water vapor. The purpose of the present work is to study the effects of CeO2 coating on the diffusion profile of the oxide scale at elevated temperature in water vapor.
2 Experimental
The studied alloy was commercial T91 steel, and the composition was presented in Table 1. The specimens (15 mm × 8 mm × 2 mm) were cut from a boiler tube, polished up to 1 μm grade with diamond paste, then washed with alcohol in an ultrasonic bath and dried. Some of the specimens were deposited with gold marker. For CeO2 coated specimen, gold marker was deposited before CeO2 coating.
Cerium was deposited on the steel surface by electrodeposition in 0.05 mol/L alcohol solution of Ce(NO3)3·6H2O. The specimen was used as cathode, and two stainless steel plates (the same size with the sample) were used as anodes. The specimens were coated on the two main surfaces for 15 s with a voltage of 15 V/mm. Approximately 1-2 ?m thick Ce(OH)4 coating can be formed. Finally, a homogeneous CeO2 coating was produced by thermal decomposition at 300 °C for 30 min.
The specimens were oxidized at 600 °C for up to 150 h in a set-up, as illustrated in Fig.1 under atmospheric pressure. The water vapor was produced from deionized water treated by high purity argon. Evaporating rate was 0.4 L/h with oxygen less than 0.007 mg/L. Specimens were weighed using an electric balance with accuracy of 0.01 mg. The oxidation scales were examined using X-ray diffraction (XRD), electron-probe microanalyzer (EPMA) and scanning electron microscopy (SEM, coupled with energy dispersive X-ray spectrometry (EDX)).
Table 1 Composition of T91 steel (mass fraction, %)
Fig.1 Schematic diagram of experimental set-up for water vapor oxidation test
3 Results
3.1 Isothermal kinetics
Figure 2 exhibits the mass gain curves of blank and CeO2-coated T91 specimens after 150 h isothermal oxidation. The scale growth kinetics of the blank specimens follows a parabolic rate law during the whole oxidation test, whereas the kinetic curve of the cerium-coated specimen exhibits an initial transient stage during the first 5 h, followed by a parabolic regime. The mass gain curves show an improvement in the oxidation resistance for the CeO2-coated T91 steel, though the improvement is not remarkable.
Fig.2 Mass gain curves of blank and CeO2-coated T91 steels oxidized in water vapor at 600 °C for up to 150 h
3.2 Polished cross sectional morphology and composition
Figure 3 shows the backscattered electron images and EDX line scanning images of the scale cross section of the blank and CeO2-coated T91 steels oxidized at 600 °C for 150 h in water vapor. Both of the scales show double-layer structure according to the composition: the outer layer consists of predominantly iron oxide (magnetite as characterized by XRD); the inner layer is Cr and Fe rich oxide. The overall oxide thickness of the blank sample (about 28-32 μm) is larger than that of the coated one (about 23-26 μm).
The position of the original metal surface is represented by gold marker, as shown in Fig.3, revealing that the oxide scales of both blank and cerium-coated T91 steel mainly grow by outward iron diffusion and inward oxygen diffusion. The interface of the inner layer (Fe and Cr rich oxide) and outer layer (iron oxide) of the blank sample is consistent with the original surface (the interface is characterized by composition and designated as interface 1). For CeO2-coated sample, cerium- containing oxide band is located outside the original surface, as shown in Fig.3(b). Some of the CeO2 may attach to the gold marker, so another weaker Ce peak is shown in EPMA line scan in Fig.3(b).
3.3 Fractured cross sectional morphology
Figure 4 shows the fractured scale cross section of blank and cerium-coated T91 oxidized in water vapor for 60 h (these two samples were not deposited with gold marker). Both samples show double-layer structure: the inner layer is fine equiaxed structure; the outer layer is coarse columnar structure. There are obvious differences between the blank and cerium-coated specimens: 1) the outer columnar layer of the blank specimen is porous, especially near the interface of the outer and inner layers, while the outer columnar layer of the CeO2 coated specimen is much more compact. 2) by EDX analysis, the interface of the outer columnar layer and inner equiaxed layer (here the interface is characterized by morphology and designated as interface 2) of the blank specimen is consistent with interface 1 in the polished cross section, corresponding to the original surface as shown in Fig.3(a), while the interface 2 of the CeO2- coated specimen corresponds to the Ce-rich band, as indicated by the white curve line in Fig.3(b).
Fig.3 Backscattered electron images and corresponding EPMA element line scanning images of blank and cerium-coated T91 steels oxidized in water vapor for 150 h: (a) Blank; (b) CeO2-coated
Fig.4 SEM micrographs of fractured oxide scales of blank and cerium-coated T91 steels after oxidation in water vapor for 60 h: (a) Blank; (b) CeO2-coated
4 Discussion
The REE is well known to improve the high temperature oxidation resistance of Fe-Cr alloys, which includes reducing the oxide growth rate and preventing the oxide scale exfoliation. Though no clear conclusions have been drawn for the REE, the improvement of oxidation property has been ascribed partly to: 1) producing more nucleation sites so as to reduce the oxide grain size and improve the plasticity of the oxide layer; 2) resulting in an inversion of transport processes from predominant outward cation transport to inward anion transport [2-3, 12-14].
The effects of reactive elements may depend on the nature of the elements and also on the oxidation environment. CHEVALIER et al [4] studied the oxidation of Nd2O3 coated F17Ti steel in air and located the rare-earth element in the external part of the oxide scale. SUNDARARAJAN et al [7] studied ceria coated 9Cr-1Mo ferritic steel in air and steam and found that Ce was rich at the surface when oxidized in air but was rich at the interface between the outer and inner layer when oxidized in steam.
The present results show that the gold marker, which represents the original surface, acts as a division of inner Fe-Cr oxide (usually (FeCr)3O4) and outer Fe3O4 oxide after oxidation for both blank and Ce-coated specimens, indicating that both the inward and outward diffusion process still exist. It is worth mentioning that for the blank specimen, the original surface is also the interface of the inner equiaxed oxides and outer columnar oxides. But it is not the case for cerium-coated specimen. The composition and morphology profile of the oxidized specimen can be depicted in Fig.5. For uncoated T91 specimen, the outer layer grows mainly by the outward iron diffusion, to form a columnar iron oxide layer, while the inner layer grows mainly by inward oxygen diffusion, to form a fine equiaxed oxide layer. For CeO2 coated specimen, since reactive element oxides are dominated with oxygen defects, it is therefore conceivable that oxygen transport through the Ce-rich band is easier [15]. Figure 5(b) shows that outward diffusion of iron is blocked/delayed by Ce-rich band, and the inner surface of Ce-rich band becomes a new nucleating and growing site (reaction front) for oxide, so a fine equiaxed iron oxide region is formed between the original surface and the Ce-rich band. The effect of CeO2 coating on the diffusion of oxygen ion is little.
Fig.5 Schematic diagrams of scale growth of T91 steels with and without CeO2 coating oxidized in water vapor at 600 °C: (a) Blank; (b) CeO2 coated
5 Conclusions
1) CeO2 coating can improve the oxidation resistance of T91 steel in water vapor at 600 °C and the improvement is not remarkable under the testing condition.
2) For CeO2 coated specimen, outward iron transport is blocked by Ce-rich band. A new nucleating and growing site for oxides is induced. A fine equiaxed iron oxide region is formed between the original surface and the Ce-rich band.
3) Cerium-rich oxide band is located between the outer coarse columnar oxides and inner fine equiaxed oxides and it is outside the original surface.
References
[1] ECER G M, SINGH R B, MEIER G H. The influence of superficially applied oxide powders on the high-temperature oxidation behavior of Cr2O3-forming alloys [J]. Oxidation of Metals, 1982, 18(1/2): 55-81.
[2] STRINGER J. The reactive element effect in high-temperature corrosion [J]. Materials Science and Engineering A, 1989, 120(1): 129-137.
[3] HOU P Y, STRINGER J. The influence of ion-implanted yttrium on the selective oxidation of chromium in Co-25wt.% Cr [J]. Oxidation of Metals, 1988, 29(1/2): 45-73.
[4] CHEVALIER S, BONNET G, DUFOUR P, LARPIN J P. The REE—A way to improve the high-temperature behavior of stainless steels [J]. Surface and Coatings Technology, 1998, 100/101: 208-213.
[5] ALMAN D E, JABLONSKI P D, KUNG S C. Surface modification of alloys for improved oxidation resistance in SOFC Applications [C]// BANSAL N P, WERESZCZAK A, LARA-CURZIO E. Advances in Solid Oxide Fuel Cells II: Ceramic Engineering and Science Proceedings. Cocoa Beach, Florida: The American Ceramic Society, 2007, 27(4): 253-262.
[6] WRIGHT I G, TORTORELLI P F. Program on technology innovation: Oxide growth and exfoliation on alloys exposed to steam [R]. Palo Alto, CA: Electric Power Institute, 2007.
[7] SUNDARARAJAN T, KURODA S, KAWAKITA J, SEAL S. High temperature corrosion of nanoceria coated 9Cr-1Mo ferritic steel in air and steam [J]. Surface and Coatings Technology, 2006, 201(6): 2124-2130.
[8] ENNIS P J, QUADAKKERS W J. Mechanisms of steam oxidation in high strength martensitic steels [J]. International Journal of Pressure Vessels and Piping, 2007, 84(1/2): 75-81.
[9] LAVERDE D, G?MEZ-ACEBO T, CASTRO F. Continuous and cyclic oxidation of T91 ferritic steel under steam [J]. Corrosion Science, 2004, 46(3): 613-631.
[10] Pantip Ampornrat, Gary S W. Oxidation of ferritic-martensitic alloys T91, HCM12A and HT-9 in supercritical water [J]. Journal of Nuclear Materials, 2007, 371(1/2/3): 1-17.
[11] ZHANG Du-qing, LIU Guang-ming, Zhao Guo-qun, GUAN Yan-jin. Cyclic oxidation behavior of Fe-9Cr-1Mo steel in water vapor atmosphere [J]. Journal of Central South University of Technology, 2009, 16(4): 535-540.
[12] POLMAN E A, FRANSEN T, GELLINGS P J. High-temperature corrosion and mechanical properties of protective scales on Incoloy 800H: The influence of preoxidation and ion implantation [J]. Oxidation of Metals, 1990, 33(1/2): 135-155.
[13] CHEVALIER S, LARPIN J P. Influence of reactive element oxide coatings on the high temperature cyclic oxidation of chromia- forming steels [J]. Materials Science and Engineering A, 2003, 363(1/2): 116-125.
[14] QI Hui-bin, LEES D G, HE Ye-dong. Effect of surface applied rare earth containing thin oxide films on high-temperature oxidation of Fe25Cr [J]. Corrosion Science and Protection Technology, 1999, 11(4): 193-201. (in Chinese)
[15] HOU P Y, SHUI Z R, CHUANG G Y, STRINGER J. Effect of reactive element oxide coatings on the high temperature oxidation behavior of a FeCrAl alloy [J]. Journal of The Electrochemical Society, 1992, 139(4): 1119-1126.
(Edited by HE Yun-bin)
Foundation item: Project(2007A-47) supported by Shandong Electric Power Corporation, China
Received date: 2010-09-13; Accepted date: 2010-10-22
Corresponding author: TIAN Xue-lei, Professor, PhD; Tel: +86-531-88392727; E-mail: tianxuelei@sdu.edu.cn
- Effects of CeO2 coating on oxidation behavior of T91 steel in water vapor
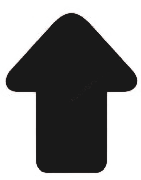