- Abstract:
- 1 Introduction▲
- 2 Experimental▲
- 3 Results and discussion▲
- 4 Conclusions▲
- References
- Figure
- Fig.1 Mass gain per unit area vs oxidation time: (a) Materials A and B; (b) Materials C and D
- Fig.2 X-ray diffraction patterns of materials B (a) and D (b)
- Fig.3 Surface morphologies of materials B and D oxidized for 480 h: (a) Material B, lower magnification; (b) Material D, lower magnification; (c) Material B, higher magnification; (d) Material D, higher magnification
- Fig.4 Cross-section morphologies of oxide scale: (a) Material B; (b) Material D
J. Cent. South Univ. Technol. (2008) 15: 301-304
DOI: 10.1007/s11771-008-0056-1
Effect of relative density on cyclic oxidation resistance properties of MoSi2
YAN Jian-hui(颜建辉)1, 2, LI Yi-min(李益民)1, ZHANG Hou-an(张厚安)2
(1. State Key Laboratory of Powder Metallurgy, Central South University, Changsha 410083, China;
2. College of Electromechanical Engineering, Hunan University of Science and Technology,
Xiangtan 411201, China)
Abstract:
MoSi2 powders were fabricated respectively by mechanical alloying technique and sintering at different temperatures to prepare materials with different relative densities. The relative oxidation behavior of all MoSi2 materials at 1 473 K was investigated by TGA, SEM and XRD. The results show that the “pesting” is not found in all materials after being oxidized for 480 h. The density has no essential relation to the “pesting”. The oxidation curve of specimens with lower density shows two-step oxidation kinetics. Both the first stage (0-1 h) and the second stage (1-480 h) nearly obey linear kinetics, but the oxidation rates are obviously different. The oxidation kinetics of MoSi2 with higher relative density nearly follows parabolic law. The mass gains of MoSi2 with the lowest relative density (78.6%) and the highest relative density (94.8%) are increased by 10.390 and 0.135 mg/cm2, respectively. The oxide scale of materials with lower densities is non-protective and makes the oxygen diffusion easy. A dense scale in the material with higher density is formed, which acts as a diffusion barrier to the oxygen atoms to penetrate into the matrix, showing much better high temperature oxidation resistance. The phases distribution of oxidation scale from the outside to the inside is SiO2→Mo5Si3→MoSi2.
Key words:
MoSi2; relative density; diffusion; oxidation resistance;
1 Introduction
MoSi2 is known to be a promising material for ultra-high temperature material application in oxidizing atmospheres[1]. Much work has been done on the oxidation behavior of MoSi2 and MoSi2-based composites to improve the “pesting” at about 773 K[2-6]. Accelerated oxidation of MoSi2 is influenced by material factors (composition and density) and environmental factors (oxidation temperature and atmosphere)[7-10]. ZHANG et al[11] and CHOU and NEIH[12] compared the resistance of as-cast, spark plasma sintered polycrystalline MoSi2 and single-crystalline MoSi2 at 773 K. Specimens (either poly- or single-crystalline) containing cracks are liable to pest disintegration. Oxidation resistance of single-crystalline MoSi2 is much better than that of dense poly-crystalline counterparts. The oxidation kinetics changes from a linear law in poly-crystalline MoSi2 to a parabolic law in the single-crystalline MoSi2. LIU et al[13] predicted a change in oxidation kinetics from linear law at a low temperature to parabolic law at a high temperature based on the differences of bulk and grain boundary diffusivity in MoSi2. Most of the reported oxidation kinetics of MoSi2 follows this model. KUROKAWA et al[7] compared low temperature oxidation of fully dense and porous MoSi2 and found accelerated oxidation and “pesting” in porous material only. They attributed “pesting” oxidation to extrinsic effects such as cracks.
In this work, the oxidation properties of MoSi2 with different relative density at 1 473 K were investigated. The objective was to clarify the relationship between oxidation resistance and relative density.
2 Experimental
The starting powders used in this work were 99.9% Mo powder (2-4 μm), 99.5% Si powder (<43 μm). Mo and Si powders were mixed at the desired composition and fabricated by mechanical alloying(MA) technique. Then, the powder mixtures were prepared by pressureless sintering at different temperatures in vacuum for 1 h to acquire different relative densities. Table 1 shows the relative density at different sintering temperature.
Cycle oxidation experiments were carried out at 1 473 K in flowing air, with small specimens of 10 mm×10 mm×2 mm dimensions, whose surfaces were mechanically polished with 1 μm diamond particles, and then cleaned ultrasonically. For the oxidation tests, the specimens were placed into an alumina crucible in the box type furnace. The mass of samples was measured every certain hour by an analytical balance with a sensi-tivity of 0.1 mg. The total oxidation time was 480 h. All the mass gain data in this work were provided by the specific mass gain, the mass gain was normalized by the specimen surface area.
Phase identification was carried out by a D8-Advance X-ray diffractometer with monochromated Cu Kα radiation. Using a KYKY-2800 scanning electron microscope equipped with energy dispersive spectroscopy(EDS), the microstructures of samples were analyzed.
Table 1 Relative densities of MoSi2 at different sintering temperatures
3 Results and discussion
3.1 Cyclic oxidation behavior
The oxidation kinetics curves of four materials at 1 473 K are shown in Fig.1. “Pesting” did not occur in all materials. The mass gain increases in the oxidation
Fig.1 Mass gain per unit area vs oxidation time: (a) Materials A and B; (b) Materials C and D
time range from 0 to 480 h. With the increase of relative density, the mass gains greatly decrease. The mass gains of materials A and D reach 10.390 and 0.135 mg/cm2, and the average oxidation rates are 2.16×10-2 and 2.80×10-4 mg/(cm2·h), respectively. The oxidation curves of lower density materials (A and B) show two-step oxidation kinetics. Both the first step (0-1 h) and the second stage (1-480 h) nearly obey the linear law (Fig.1(a)). However, the oxidation kinetics of higher density materials (C and D) nearly follows parabolic law (Fig.1(b)). The oxidation resistance of MoSi2 with the highest density is improved by 98% compared with that of MoSi2 with the lowest relative density. So, the oxidation resistance of MoSi2 can be improved by increasing the density of materials.
3.2 Phase analysis of oxide scale
Fig.2 shows XRD patterns of the oxides formed on the surface of materials B with relative density of 85.0% and D with relative density of 94.8% at 1 473 K for 480 h. According to the profiles, the oxides of material D are identified to be mainly MoSi2, SiO2(monoclinic cristobalite, JCPDS card No.27-0605), and a small amount of Mo5Si3 and Fe2O3 (Fe oxidized from MA process). However, the oxide of material B mainly consists of MoSi2, Mo5Si3 and SiO2 (cristobalite and tridymite, JCPDS cards No.27-0605 and 181170) and a small amount of Fe2O3. The Mo5Si3 diffraction intensity of material B is much higher than that of material D when they are oxidized for 480 h, which shows that the oxidation rate of material B is much quicker than that of material D. The result is also consistent with oxidation kinetics.
Fig.2 X-ray diffraction patterns of materials B (a) and D (b)
According to the X-ray diffraction analysis, two oxidation reactions are possible for MoSi2:
5MoSi2(s)+7O2(g)→Mo5Si3(s)+7SiO2(s) (1)
2Mo5Si3(s)+21O2(g)→10MoO3(g)+6SiO2(s) (2)
Reactions (1) and (2) are thermodynamically favored at 1 473 K because Gibbs free energy is about -836.8 and -1 464.4 kJ/mol, respectively. Reaction (1) causes a net mass-gain because of no formation of volatile matter. However, reaction (2) causes a net mass-reduction because of MoO3 evaporating. In this experiment, mass increasing exceeds mass reducing, resulting in the increase of all samples.
3.3 Morphology analysis of oxide scale
Surface morphologies of the oxides formed on materials B and D are shown in Fig.3. The oxide scale on the material is full of small granule. The granule on the surface of material B is larger than that on the surface of material D. The microcrack is found on the surface of material B (Fig.3(c)), which is formed because of the mismatch between the oxide scale and the MoSi2 matrix.
The pores on the surface of material B become a preferential path for oxygen inward diffusion. Therefore, the oxidation reaction occurs easily for material with lower density and the mass gain increases much quicker at initial oxidation stage(Fig.1). For the sample with lower density, the oxidation rates are different at the pore between the grains. This leads to a non-uniform growth and expansion within the oxide scale where cracks and defects are formed. Thus the scale is non-protective and a linear law of kinetics is followed. According to the research of BARTLETT[14], the loose oxidation scale made the oxygen diffusion easy, which caused the oxygen pressure of boundary between SiO2 and MoSi2 much higher, and reaction (2) occurred easily. The result is also consistent with X-ray diffraction patterns (Fig.2). The evaporating MoO3 prevents the protective scale from forming. So, it is thought that loose oxidation scale acts as a path for simultaneous oxidation of Mo and Si.
It can be seen that the oxidation scale of the surface of material D was made of small SiO2 granular (Figs.3(b) and (d)). The edge angle of SiO2 granule surface is sharp. The crystal structure develops completely and shows balancing crystal structure[15]. The fluidity of SiO2 granular is very good and SiO2 granule flows easily to fill up the crack. So, the microcrack is not found on the surface. A dense scale will be almost completely formed when material D is oxidized for 480 h. According to Ref.[12], the dense scale acts as a diffusion barrier to the oxygen atoms to penetrate into the matrix. The oxidation is limited by the diffusion of oxygen and a parabolic kinetics is followed. This makes the oxygen pressure of boundary between SiO2 and MoSi2 very low and reaction (2) hardly occurs. However, the oxygen pressure can cause reaction (1) to take place. To some extent, the dense and continuous scale prevents further oxidation of MoSi2, showing excellent resistance to oxidation at high temperature. It is thought that dense oxidation scale only acted as a path for optional oxidation of Mo and Si.
Cross-section morphologies of the oxide scale formed on materials B and D are presented in Fig.4. The oxide scale on the surface of material B is about 5 μm in
Fig.3 Surface morphologies of materials B and D oxidized for 480 h: (a) Material B, lower magnification; (b) Material D, lower magnification; (c) Material B, higher magnification; (d) Material D, higher magnification
Fig.4 Cross-section morphologies of oxide scale: (a) Material B; (b) Material D
thickness and contains a lot of defects and cracks (Fig.4(a)). The oxide scale on the surface of material D is much thinner, which is about 1.5 μm (Fig.4(b)), which shows that the oxidation rate of material B is much faster than that of material D. The most noteworthy feature in morphologies is that the scale of material D is quite uniform and dense, showing no defects and cracks. The EDS results of oxide scale on material B are shown in Table 2. The phases distribution of oxidation scale is SiO2→Mo5Si3→MoSi2 from the outside to the inside.
Table 2 EDS results of different points of oxide scale on material B (molar fraction, %)
4 Conclusions
1) “Pesting” is not found in MoSi2 materials, with different relative densities, oxidized at 1 473 K for 480 h. The relative density of MoSi2 has no essential relation to the “pesting”.
2) The oxidation kinetics of higher density MoSi2 nearly follows parabolic law. However, the oxidation curve of lower density sample shows two-step oxidation kinetics. Both the first stage (0-1 h) and the second stage (1-480 h) nearly obey linear kinetics law. The oxidation kinetics of MoSi2 with higher density nearly follows parabolic law. The mass gains of the materials with the lowest relative density (78.6%) and the highest relative density (94.8%) reach 10.390 and 0.135 mg/cm2, respectively. And the average oxidation rates are 2.16×10-2 and 2.80×10-4 mg/(cm2·h), respectively.
3) A dense oxide scale is formed on the surface of material with higher relative density, which hinders the diffusion of oxygen, exhibiting much better oxidation resistance. The oxidation resistance can be improved by increasing the density of the materials.
4) The phases distribution of oxidation scale from the outside to the inside is SiO2→Mo5Si3→MoSi2.
References
[1] VASUDEVAN A K, PETROVIC J J. A comparative overview of molybdenum disilicide composites [J]. Materials Science and Engineering A, 1992, A155: 1-17.
[2] KUCHINO J, KUROKAWA K, SHIBAYAMA T. Effect of microstructure on oxidation resistance of MoSi2 fabricated by spark plasma sintering [J]. Vacuum, 2004, 73: 623-628.
[3] MITRA R, RAMA R V V. Effect of minor alloying with Al on oxidation behaviour of MoSi2 at 1 200 ℃ [J]. Materials Science and Engineering A, 1999, A260: 146-160.
[4] MARUYAMA T, YANAGIHARA K. High temperature oxidation and pesting of Mo(Si,A1)2 [J]. Materials Science and Engineering A, 1997, A239/240: 828-841.
[5] LOHFELD S, SCHTZE M. Oxidation behavior of particle reinforced MoSi2 composites at temperature up to 1 700 ℃(part I): Literature review [J]. Materials and Corrosion, 2005, 56(2): 93-97.
[6] YAN Jian-hui, LI Yi-min, ZHANG Hou-an, TANG Si-wen. Mechanical properties and high temperature oxidation behavior of La2O3-Mo5Si3/MoSi2 [J]. The Chinese Journal of Nonferrous Metals, 2006, 16(10): 1730-1735. (in Chinese)
[7] KUROKAWA K, HOUZUMI H, SAEKI I. Low temperature oxidation of full dense and porous MoSi2 [J]. Materials Science and Engineering A, 1999, A261: 292-299.
[8] NATESAN K, DEDVI S C. Oxidation behavior of molybdenum silicides and their composites [J]. Intermetallics, 2000, 8: 1147-1158.
[9] BERZTISS D A, CERCHIARA R R, GULBRANSEN E A, PETTIT F S. Oxidation of MoSi2 and comparison with other silicide materials [J]. Materials Science and Engineering A, 1992, A155: 165-181.
[10] YAN Jian-hui, ZHANG Hou-an, LI Yi-min. Oxidation behaviors of MoSi2 with different density at high temperature of 700-1 200 ℃ [J]. Chinese Journal of Rare Metals, 2007, 31(1): 18-21.(in Chinese)
[11] ZHANG Fang, ZHANG Lan-ting, SHAN Ai-dang, WU Jian-sheng. Oxidation of stoichiometric poly- and single-crystalline MoSi2 at 773 K [J]. Intermetallics, 2006, 14: 406-411.
[12] CHOU T C, NEIH T G. Mechanism of MoSi2 pest during low temperature oxidation [J]. Journal of Materials Research, 1993, 8(1): 214-226.
[13] LIU Y Q, SHAO G, TSAKIROPOLOS P. On the oxidation behaviour of MoSi2 [J]. Intermetallics, 2001, 9: 125-136.
[14] BARTLETT R W, MARSUOKA, TAKAHASHI H. High temperature oxidation of molybdenum disilicide [J]. Journal of the American Ceramic Society, 1965, 48(11): 551-552.
[15] CHANG Chun, LI Mu-sheng, CHEN Chuan-zhong, TIAN Lei-yan. Microstructure of high-temperature oxidation layer of molybdenum disilicide [J]. Acta Metallurgica Sinica, 2003, 39(2): 126-130. (in Chinese)
(Edited by CHEN Wei-ping)
Foundation item: Project(50405041) supported by the National Natural Science Foundation of China; Project(06C316) supported by the Scientific Research Fund of Hunan Provincial Education Deparment, China
Received date: 2007-07-26; Accepted date: 2007-10-08
Corresponding author: YAN Jian-hui, PhD; Tel: +86-732-8290544; E-mail: yanjianhui88@163.com
- Effect of relative density on cyclic oxidation resistance properties of MoSi2
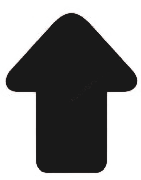