- Abstract:
- 1 Introduction▲
- 2 Experimental▲
- 3 Results▲
- 5 Conclusions▲
- References
- Figure
- Fig.1 Influence of transfer time on mechanical properties of alloy: (a) Strength; (b) Elongation
- Fig.2 Optical micrographs of alloys: (a) Zr-free; (b) 0.15%Zr
- Fig.3 TEM images of Zr-free alloy after aging for different transfer time: (a) 2 s; (b) 80 s
- Fig.4 TEM images of Zr-containing alloys aged for different transfer time: (a) 2 s; (b) Grain boundary, 80 s; (c) Inside grain, 80 s
- Fig.5 Influence of transfer time on fracture surface of samples: (a) Zr-free alloy, 2 s; (b) Zr-free alloy, 80 s; (c) Zr-containing alloy, 2 s; (d) Zr-containing alloy, 80 s
J. Cent. South Univ. Technol. (2008) 15: 153-158
DOI: 10.1007/s11771-008-0030-y
Influence of quench transfer time on microstructure and mechanical properties of 7055 aluminum alloy
YOU Jiang-hai(游江海)1, 2, LIU Sheng-dan(刘胜胆)1, 2,
ZHANG Xin-ming(张新明)1, 2, ZHANG Xiao-yan(张小艳)1, 2
(1. Educational Key Laboratory of Non-ferrous Metal Materials Science and Engineering,
Central South University, Changsha 410083, China;
2. School of Materials Science and Engineering, Central South University, Changsha 410083, China)
Abstract:
The influence of quench transfer time on the microstructure and mechanical properties of 7055 aluminum alloy with and without zirconium was investigated by tensile properties test, optical microscopy, scanning electron microscopy and transmission electron microscopy. For the Zr-free alloy, the strength increases to the highest value at 20 s with transfer time, and then decreases slightly. The elongation decreases slowly with transfer time within 20 s, and more rapidly after 20 s. For the Zr-containing alloy, prolonging transfer time within 20 s results in slight decrease in the strength and elongation, and rapid drop of which is observed after 20 s. For the Zr-free alloy, prolonging transfer time can increase the percentage of intergranular fracture, which is mainly caused by wide grain boundary precipitate free zone. The failure mode of the Zr-containing alloy is modified from the predominant transgranular void growth and intergranular fracture to transgranular shear and intergranular fracture with increase in the transfer time, which is attributed to the wider grain boundary precipitate free zone and coarse equilibrium η phases in the matrix.
Key words:
1 Introduction
In recent years, it is urgently desired for production of thick plates of AlZnMgCu alloys to reduce cost and enhance the reliability of the structures in the aerospace industry[1]. The quench sensitivity often results in drop in the mechanical properties of the alloys, so quench process, must be well controlled so as to avoid negative effect caused by slow quench. After solution-treatment, the alloys must be cooled rapidly to freeze all the solutes in the matrix to avoid heterogeneous precipitation primarily on dispersoids and grain boundaries[2-4], which reduces the solutes available for hardening precipitates during subsequent aging. But in practice, inadequate quench often occurs, for instance, the cooling rate in the middle of the thick plate or forgings is lower than that on the surface, which leads to inhomogeneity and drop in properties[5].
Improvements in aircraft structure, which demand a superior combination of high strength, fracture toughness and stress corrosion cracking resistance, have led to the development of 7055 aluminum alloy. 7055-T77 alloys provide higher strength about 10% than 7150-T6 and 30% than 7075-T76 with high fracture toughness and good resistance to corrosion and to the growth of fatigue cracks, and these attractive properties are attributed to the high Zn/Mg and Cu/Mg ratios[1]. As this alloy is age-hardenable, most investigations have focused on solution heat treatment and aging[6-8]. LIU et al[9] studied the quench sensitivity of this alloy by evaluating the TTP diagrams, and found that this alloy is more quench sensitive than some other alloys, which may be attributed to larger amount of alloying elements. The purpose of this work is to investigate the influence of quench transfer time on the microstructure and mechanical properties of 7055 alloy with and without zirconium.
2 Experimental
7055 aluminum alloys were prepared with the nominal chemical compositions of Al-8.0Zn-2.0Mg- 2.3Cu and Al-8.0Zn- 2.0Mg-2.3Cu-0.15Zr (mass fraction, %). The content of Fe+Si was kept below 0.15%. The ingots of 20 mm× 150 mm in cross section and 200 mm in length were prepared by an induction furnace. The ingots were homogenized at 465 ℃ with heating rate of 0.8 ℃/min and holding for 24 h, and then cooled in air. After preheating at 420 ℃ for 2 h, the homogenized ingots were rolled to samples with thickness of 2.5 mm
through 10 passes.
After solution-treatment at 470℃ for 60 min, the samples were first cooled in the air for 2, 5, 10, 20, 40 and 80 s, which is defined as transfer time, respectively, and then quenched into room temperature water. The artificial aging at 121 ℃ for 24 h was carried out immediately after quench. The ambient tensile properties of the aged samples were tested with a CSS-44100 machine at a tensile velocity of 2 mm/min. The microstructures were observed by optical microscope (OM) and TecnaiG2 20 transmission electron microscope (TEM). The samples of 3 mm in diameter, 0.08 mm in thickness for transmission electron microscope observation were electropolished using 30% HNO3+ 70% CH3OH solution below -20 ℃. The fracture surfaces of the tensile samples were observed by KYKY-2800 scanning electron microscope(SEM).
3 Results
3.1 Mechanical properties
The influence of transfer time on mechanical properties of the aged alloy is shown in Fig.1. It can be seen that with the transfer time from 2 to 80 s the strength
Fig.1 Influence of transfer time on mechanical properties of alloy: (a) Strength; (b) Elongation
of the aged Zr-free alloy increases, reaches a maximum at 20 s and then decreases, while the elongation decreases slowly first, then sharply after 20 s. Within 20 s, slight decrease in the strength of the Zr-containing alloy with transfer time can be observed. Further increase in the transfer time results in sharp drop in the strength. The elongation decreases slowly with increase in transfer time. The Zr-containing alloy has higher strength than the Zr-free alloy within 40 s, but lower strength after 40 s. The elongation of Zr-containing alloy is always higher than that of Zr-free alloy, especially after 20 s, which receives no effect from transfer time. According to these results, the transfer time must be controlled within 20 s to avoid sharp drop in the mechanical properties of the alloy.
3.2 Microstructures
Typical grain structures of the aged alloys are given in Fig.2. The grain structure of the alloys was mainly modified by solution-treatment, while subsequent low temperature aging exerted little effect. From Fig.2(a), it is clear that complete recrystallization occurs in the Zr- free alloy after solution-treatment and the recrystallized grains are quite large. Partial recrystallization occurs in the Zr-containing alloy after solution-treatment, as shown in Fig.2(b). After etching by Graff Sargent’s reagent, the recrystallized grains are identified to be
Fig.2 Optical micrographs of alloys: (a) Zr-free; (b) 0.15%Zr
white, and the unrecystallized regions are dark, which contain many subgrains[10]. This is obviously attributed to the recrystallization inhibiting and grain refining effect of zirconium[10-11].
Fig.3 and Fig.4 show typical TEM images of the Zr-free and Zr-containing alloys after aging, respectively. For the Zr-free alloy with transfer time of 2 s, fine dispersed GP zones with high density and η′ precipitates can be observed in the matrix (Fig.3(a)), while precipitates with uniform size distribute along the grain boundaries with narrow precipitate free zone. When the transfer time is prolonged to 80 s, the width of grain boundary precipitate free zone is significantly increased with non-uniform and more spaced precipitates at the grain boundary (Fig3.(b)). The shorter the distance to the grain boundary, the lower the density of the hardening precipitates in the matrix. No significant effect of transfer time on the hardening precipitates in the matrix far from the grain boundary is observed.
For the Zr-containing alloy with transfer time of 2 s, fine dispersed GP zones with high density and η′ precipitates can be observed in the matrix (see Fig.4(a)).
Fig.3 TEM images of Zr-free alloy after aging for different transfer time: (a) 2 s; (b) 80 s
The precipitates with uniform size distribute continuously along the grain boundary with quite narrow precipitate free zone. When the transfer time is prolonged to 80 s, hardening precipitates with slightly larger size and lower density are observed in the matrix, (see Fig.4(b)). The precipitates at the grain boundaries become larger and are more spaced with wider precipitate
Fig.4 TEM images of Zr-containing alloys aged for different transfer time: (a) 2 s; (b) Grain boundary, 80 s; (c) Inside grain, 80 s
free zone. Moreover, many coarse equilibrium η particles in the shape of platelet or laths can be seen in the matrix (see Fig.4(c)). These particles are induced by slow air quench as the transfer time increases, which are nucleated primarily on Al3Zr dispersoids[3].
3.3 Fractography
On macroscopic level, for the Zr-free alloy a 45? inclination angle of the fracture surface to the tensile direction was observed when the transfer time was shorter than 20 s. But longer transfer time resulted in an inclination angle of about 90?. For the 0.15%Zr containing alloy, the inclination angle of the fracture surface to the tensile direction was 45?, which was not influenced by transfer time. The fracture surfaces were further observed by SEM, with typical images presented in Fig.5. On the microscopic level, the fracture mode of the Zr-free alloy with transfer time of 2 s is mainly transgranular microvoid coalescence and intergranular crack (see Fig.5(a)). While for the Zr-free alloy with transfer time of 80 s, the failure mode is almost complete intergranular fracture, as many intergranular cracks and relatively flat grain boundary surfaces can be seen on the fracture surface (see Fig.5(b)). For the Zr-containing alloy with transfer time of 2 s, a lot of large dimples, most of which contain large intermetallics, and some intergranular cracks can be observed on the fracture surface (Fig.5(c)), which indicates that the failure mode of this alloy is predominant transgranular void growth fracture with some intergranular fracture. When the transfer time was 80 s, the failure mode of the alloy is dominated by transgranular shear and intergranular fracture (see Fig.5(d)).
4 Discussion
7055 aluminum alloy is quench sensitive, so the quench transfer time exerts effect on the mechanical properties of the alloys. In general, the quench sensitivity of 7XXX aluminum alloy is mainly attributed to two reasons[3-4,12]. One is that slow quench results in coarse equilibrium phases in the matrix, which reduces the super-saturation of the solid solution, therefore decreases the aging hardening effect. These coarse equilibrium phases are primarily nucleated on dispersoids and grain boundaries. The other is that during slow quench vacancies diffuse and annihilate at (sub)grain boundaries, thus lower vacancy concentration in the matrix after quench is obtained, which is unfavorable for formation of fine dispersed precipitates with high density. So it is believed that quench sensitivity is closely associated with the amount of dispersoids or (sub)grain boundaries are available for heterogeneous precipitation. The effect of transfer time on the microstructure and mechanical pro-
Fig.5 Influence of transfer time on fracture surface of samples: (a) Zr-free alloy, 2 s; (b) Zr-free alloy, 80 s; (c) Zr-containing alloy, 2 s; (d) Zr-containing alloy, 80 s
perties of the alloy is also influenced by content of Zr.
According to the optical microstructures, complete recrystallization occurred in the Zr-free alloy after solution heat treatment and the grains were quite large. It is supposed that only high angle grain boundaries can act as heterogeneous precipitation sites or vacancy sink during slow quench. Thus, when the transfer time was prolonged, coarse particles precipitated at the high angle grain boundaries and the vacancy concentrations adjacent to grain boundaries were lower, which resulted in wide precipitate free zone[13]. But the solute and vacancy concentration in the matrix far from the grain boundaries received no significant effect. There is still high density of fine dispersed precipitates in the matrix after aging. As shown in Fig.1, an increase in transfer time to 20 s even slightly enhanced the strength, namely intermediate quench rate resulted in higher strength, which was also found in previous investigation[12]. This may be attributed to the enhanced segregation of solutes in this case. So there is little quench sensitivity relative to strength for the Zr-free alloy. While the quench sensitivity relative to elongation is quite large, as the elongation of the alloy is decreased sharply after 20 s and the failure mode is primarily intergranular fracture (Fig5(b)), which is mainly attributed to wider grain boundary precipitate free zone (Fig.3). Most investigations show that wide grain boundary precipitate free zone has negative effect on the properties of the alloy[2,14-15]. The precipitate free zone is softer than the matrix and dislocations are easy to pile up in the zone during plastic deformation, which causes stress concentration, aids crack initiation and propagation along grain boundaries and accelerates failure of the alloy.
The addition of zirconium results in a number of fine Al3Zr dispersoids, which inhibits recrystallization by pinning migration of grain boundaries. Generally, in the sheet of the alloy, the occurrence of recrystallization is unavoidable due to the existence of coarse intermetallics along initial grain boundaries, which leads to particle stimulated nucleation(PSN) of new grains[10]. As a result, partial recrystallization with plenty of sub-grains in the unrecrystallized zone is obtained after solution heat treatment. Recrystallization increases the amount of random high angle grain boundaries and often makes coherent Al3Zr dispersoids lose coherency with the matrix[14]. Consequently, a lot of equilibrium particles precipitate preferentially on these incoherent dispersoids with increase in transfer time, which results in loss of solutes in the matrix and less volume fraction of hardening precipitates after aging. While in the unrecrystallized zone, lower vacancy concentration is attained due to a large number of subgrain boundaries, which results in hardening precipitates with lower density and slight larger size. As a result, the aging hardening effect is greatly reduced as shown in Fig.1(a). The elongation of this alloy decreases slowly with increase in transfer time, which is quite different from that of Zr-free alloy (Fig.1(b)). This is supposed to be attributed to the recrystallization inhibiting and grain refining effect of zirconium. In general, the precipitates at subgrain boundaries are smaller than those at high angle grain boundaries due to their smaller free volumes and lower solute diffusivity, which result in a slower precipitates growth rate. Meanwhile, the width of precipitate free zones adjacent to subgrain boundaries is smaller, too. Moreover, the nature of the grain boundary leads to higher cohesive strength of subgrain boundaries. Thus, the work for crack to nucleate and propagate along these boundaries will be higher than that along high angle grain boundaries[15], which reduces intergranular fracture. In addition, the formation of coarse equilibrium phase in the recrystallized grains can also reduce intergranular fracture, therefore, enhance the elongation[12].
5 Conclusions
1) As transfer time increases from 2 to 80 s the strength of the aged Zr-free alloy increases, goes through a maximum at 20 s and then decreases, while the elongation decreases slowly first and then sharply after 20 s, the failure mode is modified from transgranular void growth and intergranular fracture to complete intergranular fracture, which is primarily attributed to increase in the width of grain boundary precipitate free zone.
2) For the 0.15%Zr-containing alloy, the transfer time must be shorter than 20 s, otherwise its mechanical properties will decrease sharply, which is primarily attributed to lower solutes and vacancy concentration in the matrix after quench. The failure mode is modified from transgranular void growth and intergranular fracture to transgranular shear and intergranular fracture, which is closely associated with coarse equilibrium η phases in the matrix and wider grain boundary precipitate free zone.
References
[1] WILLIAMS J C, STARKE E A Jr. Progress in structural materials for aerospace systems[J]. Acta Materialia, 2003, 51(19): 5775-5799.
[2] DUMONT D, DESCHAMPS A. Characterization of precipitation microstructures in aluminium alloys 7040 and 7050 and their relationship to mechanical behavior[J]. Materials Science and Technology, 2004, 20(5): 567-576.
[3] DESCHAMPS A, BR?CHET C. Nature and distribution of quench-induced precipitation in an Al-Zn-Mg-Cu alloy[J]. Scripta Materialia, 1998, 39(11): 1517-1522.
[4] LIM S T, YUN S J, NAM S W. Improved quench sensitivity in modified aluminum alloy 7175 for thick forging applications[J]. Materials Science and Engineering A, 2004, 371(1/2): 82-90.
[5] JEREMY S R, CUDD R L, TANNER D A, DOLAN G P. Quench sensitivity and tensile property inhomogeneity in 7010 forgings[J]. Journal of Materials Processing Technology, 2001, 119(1/3): 261-267.
[6] LIU Sheng-dan, ZHANG Xin-ming, HUANG Zhen-bao, DU Yu-xuan. Effects of solution heat treatment on microstructure in a high-purity 7055 aluminum alloy[J]. Trans Mater Heat Treat, 2006, 27(3): 54-59. (in Chinese)
[7] CHEN K H, LIU H W, ZHANG Z, LI S, TOOD R I. The improvement of constituent dissolution and mechanical properties of 7055aluminum alloy by stepped heat treatments[J]. Journal of Materials Processing Technology, 2003, 142(1): 190-196.
[8] LI Hai, ZHENG Zhi-qiao. Retrogression and reaging of Ag-containing 7055 Al alloy[J]. Rare Metal Materials and Engineering, 2004, 33(7): 718-722. (in Chinese)
[9] LIU Sheng-dan, ZHANG Xin-ming, HUANG Zhen-bao, LIU Wen-hui. Quench sensitivity of 7055 aluminum alloy[J]. Journal of Central South University: Science and Technology, 2006, 37(5): 846-849. (in Chinese)
[10] ROBSON J D, PRANGNELL P B. Predicting the recrystallized volume fraction in AA7050 hot rolled plate[J]. Materials Science and Technology, 2002, 18(6): 607-619.
[11] ENGLER O, SACHOT E, EHRSTR?M J C. Recrystallization and texture in hot deformed aluminium alloy 7010 thick plates[J]. Materials Science and Technology, 1996, 12(9): 717-729.
[12] THOMPSON D S, SUBRAMANYA B S, LEVY S A. Quench rate effects in Al-Zn-Mg-Cu alloys[J]. Metallurgical Transactions, 1971, 2(4): 1149-1160.
[13] HIROSAWA S, OGURI Y, SATO T. Formation mechanism of precipitate free zones in age-hardenable Al alloys[J]. Materials Forum, 2004, 28: 666-671.
[14] DORWARD R C, BEERNTSEN D J. Grain structure and quench-rate effects on strength and toughness of AA7050 Al-Zn-Mg-Cu-Zr alloy plate[J]. Metallurgical and Materials Transactions A, 1995, A26(9): 2481-2484.
[15] de HAAS M, DE HOSSON J T M. On the effects of thermo- mechanical processing on failure mode in precipitation-hardened aluminium alloys[J]. Journal of Materials Science, 2002, 37(23): 5065-5073.
(Edited by YANG Hua)
Foundation item: Project(2005CB623706) supported by the Major State Basic Research Development Program of China; Project(50230310) supported by the National Natural Science Foundation of China
Received date: 2007-10-25; Accepted date: 2007-12-29
Corresponding author: ZHANG Xin-ming, Professor; Tel: +86-731-8830265; E-mail: xmzhang@mail.csu.edu.cn
- Influence of quench transfer time on microstructure and mechanical properties of 7055 aluminum alloy
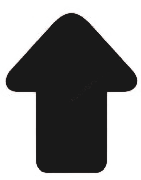