- Abstract:
- References
- Figure
- Fig.1 Stress—strain curves of ZK60 magnesium alloy with neodymium at various strain rate: (a) =0.002 s-1; (b) = 0.01 s-1; (c) = 0.1 s-1
- Fig.2 Apparent activation energy(Q) of ZK60 magnesium alloy with neodymium at different temperatures
- Fig.3 Microstructures of ZK60 magnesium alloy with neodymium during hot compression: (a) Grains before deformation; (b) Beginning of DRX; (c) DRX grains during deformation (ε=0.2); (d) DRX grains during deformation (ε=0.6)
- Fig.4 TEM images of experimental alloy: (a) DRX grain of matrix; (b) Dislocations and Mg12Nd phase
J. Cent. South Univ. Technol. (2008) 15: 434-437
DOI: 10.1007/s11771-008-0081-0
Plastic deformation behavior of ZK60 magnesium alloy with
addition of neodymium
YU Kun(余 琨), WANG Xiao-yan(王晓艳), RUI Shou-tai(芮守泰), WANG Ri-chu(王日初)
(School of Materials Science and Engineering, Central South University, Changsha 410083, China)
Abstract:
The hot deformation simulation of a ZK60 magnesium alloy at different temperatures from 373 to 673 K and different strain rates of 0.1, 0.01 and 0.002 s-1 was studied by using the Gleebe-1500 simulator. The plastic deformation behavior was measured and the deformation activation energy was calculated. The microstructures of ZK60 magnesium alloy with an addition of neodymium during the deformation process were observed by using Polyvar-MET optical microscope and Tecnai G2 20 TEM. The results show that the working hardening, the dynamic recovery and the dynamic recrystallization occur during the plastic deformation process at different temperatures and strain rates. The dynamic recrystallization starts when the temperature is over 473 K and the DRX grain size after hot deformation is only 5-10 μm. So the refined grains improve both the tensile strength and the elongation of alloys at room temperature. Neodymium is added into the alloy and a precipitate phase Mg12Nd that impedes the movement of dislocations is formed, which benefits to increasing mechanical properties of ZK60 magnesium alloy.
Key words:
ZK60 magnesium alloy; rare earth; plastic deformation behavior; dynamic recrystallization;
Introduction
Magnesium alloys are attractive for engineering applications due to their low density, high specific strength and stiffness[1-3]. The wrought magnesium alloys have higher strength, better ductility and more alternative properties than the ordinary cast magnesium alloys to meet the application demands. But the plastic deformation of magnesium alloys at room temperature is difficult due to the deformation of magnesium occurs mainly by slip on the basal planes in the directions <> and by twinning on the pyramidal planes {
}[4-5]. Insufficient knowledge of the process parameters of plastic deformation has limited the production and widespread use of wrought magnesium alloys. Since the rare earth elements have many good influences on the properties of magnesium alloys, neodymium has been added to improve mechanical properties of the experimental alloy[6-9]. In order to obtain more information about the plastic deformation behavior of magnesium alloy at different temperatures, a compressive deformation simulation of a typical wrought ZK60 magnesium alloy was performed in this work. And the plastic deformation behavior and the microstructures of ZK60 magnesium alloy were presented and the effects of neodymium on the experimental alloy were also discussed.
The experimental alloy was ZK60 magnesium alloy, and 1.0%Nd was added in the alloy though a Mg-20%Nd master alloy. The chemical composition was Mg- 5.62%Zn-0.68%Zr-0.93%Nd. The alloy was melted with a special flux to reduce the burning of magnesium and the wastage of rare earth. The hot compressive deformation simulation was performed on a Gleebe-1500 simulator in the deformation temperature range from 373 to 673 K. Three strain rates of 0.002, 0.01 and 0.1 s-1 were chosen[10]. The microstructures of the alloy were observed by using Polyvar-MET optical microscope with a VSM2000 quantitative analysis system and Tecnai G2 20 TEM. Tensile test was performed on a CSS-44100 testing system with computerized data acquisition.
3 Results and discussionThe stress—strain curves of the experimental alloy at various strain rates and different deformation temperatures are shown in Fig.1. It is shown that the temperature and the strain rate have obvious influences on the stress—strain behavior. There are three typical plastic deformation behaviors.
At the low temperature about 373 K, the flow stress increases with increasing strain and the alloy specimens break quickly. When =0.002 s-1 at 373 K, the maximum value of stress is 316.0 MPa and the specimen breaks at a strain of 0.41; when
=0.01 s-1, the maximum value of stress is 347.4 MPa with a maximum strain of 0.32. At such a low temperature, the stress maintains increasing during all the deformation process and the alloy specimens break at the peak stress point. Such phenomena illuminate that the work hardening plays a main role in the plastic deformation of alloy.
Fig.1 Stress—strain curves of ZK60 magnesium alloy with neodymium at various strain rate: (a) =0.002 s-1; (b)
= 0.01 s-1; (c)
= 0.1 s-1
At the intermediate temperature from 423 to 473 K, and at relative low strain rates of 0.002 s-1 and 0.01 s-1, the flow stress does not increase with increasing strain but keep a steady value during the deformation process. Such phenomena appear at 473 K and a higher strain rate of 0.1 s-1. All these show that both the work hardening and the dynamic recovery influence the deformation behavior of alloy. The effects of such two mechanisms may keep balance so that the flow stress curves keep steady during the whole compressive process.
At the high temperatures above 473 K, the flow stress increases to a maximum value at the three strain rates, then decreases with increasing strain and attains a steady state finally. Such a flow behavior is characteristic for hot working accompanied by dynamic recrystallization(DRX)[11-12]. At the point of the maximum stress value (peak-stress), the work hardening and DRX softening become balance, then the DRX softening is more pronounced than the hardening, so the stress decreases, the higher the deformation temperature is, the faster the DRX starts.
In the constitutive analysis, the effects of temperature and the strain rate on the flow stress are adequately expressed by the following equation[4]:
(1)
where A, α and n are all constants; is the strain rate and Z is Zener-Hollomon parameter combining the two control variables through Arrhenius equation with activation energy Q. Then Q can be expressed as
(2)
In order to calculate Q, is plotted vs
and
vs 1/T. The relationship of Q with the temperature and strain rate is therefore found, as shown in Fig.2. The apparent activation energy Q rises from low temperature to high temperature and the strain rate has an obvious effect on Q. Compared with the value of Q of ZK60 magnesium alloy in Ref.[9], Q is higher in the experimental ZK60 magnesium alloy with neodymium. This is because the neodymium has a solid solution strength effect in the α(Mg) matrix, and the precipitate phase Mg12Nd can also impede the movement of dislocation. So the required energy for dynamic recovery is higher in this alloy and therefore provides advantages for the dynamic recrystallization.
The variation of microstructure of experimental alloy during the hot compression is shown in Fig.3. The average grain size of cast alloy after homogenization is 100-140 μm (Fig.3(a)). With the compressive process begins, the grains are drawn long along the deformation direction. On the boundaries of the deformed grains, there are some very refined grains (Fig.3(b)). The refined grains are the DRX grains due to the effects of thermal and deformation force. With the deformation process continuing, the DRX grains become more and more (Fig.3(c)). Only a few unrecrystallized grains, with white color, are drawn very long with a serious deformation. The morphology of the alloy after hot compressive simulation is almost very small DRX grains with an average size 5-10 μm (Fig.3(d)). It is shown that the grain size can refine about 10 times at a suitable deformation rate and temperature. Obviously, the refined grains can provide good mechanical properties for the experimental alloy.
Fig.2 Apparent activation energy(Q) of ZK60 magnesium alloy with neodymium at different temperatures
Based on the above analysis, it can be concluded that the compressive deformation of this alloy should be performed at least above 473 K and a high strain rate. So the experimental alloy is extruded at 623 K and a high strain rate successfully. The yield tensile strength of the extruded alloy bars at room temperature is 284.6 MPa, and the ultimate tensile strength is 376.9 MPa. The elongation is 10.3%. Good mechanical properties of the experimental alloy are due to two different strengthening mechanisms. First, the grain is refined through the DRX with the hot deformation[13]. The grain size of alloy operated by means of a Hall-Petch relationship has been identified as a major factor determining the strength of wrought magnesium alloys[14]. The refined grains also provide a good ductility to the alloy so that the elongation increases greatly and similarly with increasing strength.
Second, the hard Mg12Nd phases that have a higher hardness and better heat resistance than the phases Mg2Zn in ZK60 magnesium alloy, can hinder the dislocation motion on both ambient and elevated temperatures[15]. The Mg12Nd phases that can precipitate dispersedly after aging provide precipitation strengthening in the matrix. Fig.4 shows the precipitate Mg12Nd phase of the alloy after aging. It can be seen that the matrix is recrystallized (Fig.4(a)) and the Mg12Nd Mg12Nd precipitates pin the dislocations (Fig.4(b)).
Fig.3 Microstructures of ZK60 magnesium alloy with neodymium during hot compression: (a) Grains before deformation; (b) Beginning of DRX; (c) DRX grains during deformation (ε=0.2); (d) DRX grains during deformation (ε=0.6)
Fig.4 TEM images of experimental alloy: (a) DRX grain of matrix; (b) Dislocations and Mg12Nd phase
4 Conclusions1) Flow stress curves of ZK60 magnesium alloy with neodymium at different temperatures and different strain rates can be divided into three groups. At a low temperature of 373 K and a high strain rate, work hardening mechanism plays a main role on the behavior of plastic deformation. At the intermediate temperature of 423 K, the mechanism includes both work hardening and dynamic recovery. At high temperatures above 473 K, flow behavior is characteristic for hot working accompanied by dynamic recrystallization.
2) The DRX grain size after hot deformation is only 5-10 μm in ZK60 alloy with neodymium. So the refined grains improve both the tensile strength and the elongation of alloys at room temperature.
3) The solid solution of neodymium in the α(Mg) matrix and the precipitate phase Mg12Nd impede the movement of dislocations, which benefits the mechanical properties and grain refining of magnesium alloy.
References[1] ASM International. Magnesium and magnesium alloy [M]. Ohio: Metal Park, 1999: 1-130.
[2] LI Wen-xian. Magnesium and magnesium alloy [M]. Changsha: Central South University Press, 2005: 338-380. (in Chinese)
[3] CAHN R W. Microstructures and properties of nonferrous alloys [M]. Beijing: Science Press, 1999: 460-485. (in Chinese)
[4] BUSSIBA A, ARTZY B A, SHTECHMAN A. Grain refinement of AZ31 and ZK60 Mg alloys—Towards superplasticity studies [J]. Mater Sci Eng A, 2001, A302: 56-62.
[5] YU Kun, LI Wen-xian, WANG Ri-chu. Research, development and application of wrought magnesium alloys [J]. The Chinese Journal of Nonferrous Metals, 2003, 13(2): 277-282. (in Chinese)
[6] LUO Z P, SONG D Y, ZHANG S Q. Strengthening effects of rare-earths on wrought Mg-Zn-Zr-RE alloys [J]. Journal of Alloys and Compounds, 1995, 230(2): 109-114.
[7] WEI L Y, DUNLOP G L, WESTENGEN H. Age hardening and precipitation in a cast magnesium rare-earth alloy [J]. Journal of Materials Science, 1996, 31(2): 387-397.
[8] NIE J F, MUDDLE B C. Characterization of strengthening precipitate phases in a Mg-Y-Nd alloy [J]. Acta Materialia, 2000, 48(8): 1691-1703.
[9] NIE J F. Effects of precipitate shape and orientation on dispersion strengthening in magnesium alloys [J]. Scripta Materialia, 2003, 48(8): 1009-1015.
[10] YU Kun, LI Wen-xian, WANG Ri-chu. Mechanical properties and microstructure of as-cast and extruded Mg-(Ce,Nd)-Zn-Zr alloys [J]. Journal of Central South University of Technology, 2005, 12(5): 499-502.
[11] KOJIMA Y. Progressive steps in the platform science and technology for advanced magnesium alloys [J]. Mater Sci Forum, 2003, 419/422: 3-20.
[12] PARK W J, PARK H, KIM D H. Structure and decomposition behavior of rapid solidified Mg-Nd-X alloys [J]. Mater Sci Eng A, 1994, A179/180: 637-640.
[13] JI Ze-sheng. Research process and new technology of magnesium alloy in Japan [J]. The Chinese Journal of Nonferrous Metals, 2004, 14(12): 1977-1984. (in Chinese)
[14] KHOSRHOSHAHI R A, PILKINGTON R, LORIMER G W. The microstructure and creep of as-cast and extruded WE54 alloy [C]// Proceeding of the Third International Magnesium Conference. Manchester, 1996: 261-256.
[15] LUO A. Magnesium castings for automotive applications [J]. JOM, 1995, 47(1): 28-31.
Foundation item: Project(2006BAE04B02-3) supported by the National Key Program of 11th Five-Year Plan of China
Received date: 2007-12-28; Accepted date: 2008-03-09
Corresponding author: YU Kun, PhD, Associate professor; Tel: +86-731-8879341; E-mail: kunyugroup@163.com
- Plastic deformation behavior of ZK60 magnesium alloy with addition of neodymium
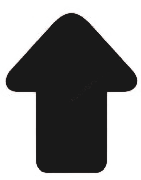