- Abstract:
- 1 Introduction▲
- 2 Experimental▲
- 3 Results and discus...▲
- 4 Conclusions▲
- References
- Figure
- Figure 1 SEM of images of group A samples with different porogens:
- Figure 2 Molecular structure of methylcellulose
- Figure 3 DSC-TDG of methylcellulose
- Figure 4 Pore size distribution of sample A1 (a) and sample A2(b)
- Figure 5 SEM of images of group B samples with different copper powders:
- Figure 6 Pore size distribution of sample B1 (a) and sample B2(b)
J. Cent. South Univ. (2018) 25: 2143-2149
DOI: https://doi.org/10.1007/s11771-018-3903-8
Influence of porogen type and copper powder morphology on property of sintering copper porous materials
LIU Ru-tie(刘如铁), CHEN Jie(陈洁), XIONG Xiang(熊翔)
State Key Laboratory of Powder Metallurgy, Central South University, Changsha 410083, China
Central South University Press and Springer-Verlag GmbH Germany, part of Springer Nature 2018
Abstract:
Copper porous materials have been manufactured by the method of powder metallurgy. Electrolytic copper powders and atomized copper powders are used as matrix material. Methylcellulose and paraffin are used as porogen. The influence of porogen type and copper powder morphology on the property of copper porous materials is investigated as well. The results show that copper porous materials with paraffin as porogen have lower porosity and permeability compared with materials using methylcellulose as porogen, due to the different pore-forming mechanisms. The pore forming mechanism of methylcellulose is thermal decomposition, while the pore forming mechanism of paraffin is melting–evaporation. The morphology of copper powders affects the contact state between adjacent powders, which further influence the sintering shrinkage. The porous materials using arborescent copper powders as matrix have lower porosity, smaller pore size and lower permeability, compared with materials with atomized copper powders as matrix.
Key words:
copper porous materials; sintered neck; porosity; permeability;
Cite this article as:
LIU Ru-tie, CHEN Jie, XIONG Xiang. Influence of porogen type and copper powder morphology on property of sintering copper porous materials [J]. Journal of Central South University, 2018, 25(9): 2143–2149.
DOI:https://dx.doi.org/https://doi.org/10.1007/s11771-018-3903-81 Introduction
The metal porous materials exhibit special properties different from the metal compacts by the presence of internal pores. It has been a new kind of multifunctional composites rapidly developed in these years [1–2]. The sintered metal porous materials are widely used in the field of aerospace, automotive, new energy, environmental protection and electrochemical industries, due to the low density, high strength, large surface area, energy absorption, well heat dissipation, infiltration and good damping characteristics [3–5].
Nowadays, many new type porous metals with different geometries and microstructures are being explored to meet the needs of different applications. WEI et al [6] introduced a novel porous metal fiber sintered sheet (PMFSS) with high porosity fabricated by the solid-state sintering method of copper fibers. Sintered copper-based porous materials have high thermal conductivity, well flexibility and low cost [7–9]. So copper porous materials are ideal heat dissipation materials widely applied in field of aerospace, such as porous wick for loop heat pipe. Due to the structure characteristics and harmless to human body, copper porous materials also become a good medicine filter material, such as hemodialysis materials [10]. ZHAO [11] provided the comprehensive state-of-the-art knowledge and research results of thermal transport in open celled cellular porous materials. Therefore it is particularly important to analyze the mass and heat transfer of copper-based porous materials, with the rapid development of modern industry. As known, porosity, pore structure and pore size distribution are the guarantee of excellent heat transfer and permeability for porous materials. The microstructure of materials is mainly influenced by the preparations.
There are many methods to prepare metal porous materials, such as foaming, bulk sintering, and adding porogen. By contrast, the method of powder metallurgy adding porogen is more flexible and controllable, so it is more conducive to the development of high-performance porous metal material [12–13]. In this study, copper porous materials have been manufactured by the method of adding porogen, in which methylcellulose and paraffin are used as porogen, electrolytic copper powders and atomized copper powders are used as matrix powders. The pore formation mechanisms of the two porogen are analyzed. The influence of porogen type and copper powder morphology on the property of copper porous materials is investigated as well.
2 Experimental
2.1 Preparation of samples
The electrolytic copper powders (purity of 99%) and atomized copper powders (purity of 99%) both with mean size of 38–45 μm were used as matrix material. Methylcellulose (C29H54O16) and paraffin both with the mean size of 40–50 μm were used as porogen. As for group A samples, the matrix powders are electrolytic copper powders and porogen is methylcellulose and paraffin respectively. The content of porogen is 10%. As for group B samples, the matrix powders are electrolytic copper powders and atomized copper powders respectively, and porogen is methylcellulose. The content of porogen is 10%.
Copper powders and porogen powders were mixed in the V-type mixer for 1 h. Next the powder mixture was pressed under 60 MPa for group A samples and 100 MPa for group B samples in a stainless steel mould. Finally, the compacts were sintered at 880 °C in a hydrogen furnace, with hydrogen as the protection atmosphere. The sintering time was 60 min. For samples with methylcellulose as porogen, the heating rate was 2 °C/min below 310 °C and stay at 310 °C for 60 min. After 310 °C, the heating rate was raised to 10 °C/min until sintering temperature. For samples with paraffin as porogen, the heating rate was 10 °C/min before sintering temperature.
2.2 Characterization
Archimedes method is used to get the porosity (ε) of porous media as shown in Eq. (1), which is easily manipulative and low-cost. Therefore, it is used in the current work:
(1)
where m1 is the beaker mass with distilled water; m2 is the total beaker mass when the wick sample is suspended in water and completely saturated; m3 is the beaker mass when the saturated wick is removed from water and there is no water-drop dripping outside the beaker; q is the density of distilled water. All the above mass quantities are measured within the accuracy of ±0.1 mg.
The morphology and microstructure of the porous materials were examined by scanning electron microscopy.
The pore size distribution and the permeability were examined by PSDA-20 pore-size distribution analyzer. The principle and measuring method is bubble-point method. The pore channel is firstly filled with liquid, which is wetting well with the surface of the pores. The pore channel is then purged with compressed gas to push out the liquid. The pore channels will be reopened until the gas pressure is high enough to overcome the capillary force at the pore-throat. With increasing the gas pressure, more and more pore channels will reopen, accompanying with the increasing gas flux. Once the change of flux is detected, the equivalent- pore-size distribution can be calculated based on the established relation of gas flux versus pressure.
3 Results and discussion
3.1 Influence of porogen type on property of copper porous materials
Figure 1 shows the SEM images of group A samples with different porogen under the same preparation conditions. It can be seen from Figures 1(a) and (c) that the porosity of sample A2 is slightly lower than that of sample A1. By measuring, the open porosity of sample A1 is 56.8% and that of sample A2 is 50.1%. Further observation from images of high magnification indicates that the combination microstructure between copper particles in two samples was different, as shown in Figures 1(b) and (d). In sample A1, the surface of copper powders is rough. The sintering neck between particles is obvious with small size. As for sample A2, the surface of copper powders is relatively smooth and the sintering neck is not so obvious with big size, which is similar to liquid sintering. The difference of microstructure between two samples under the same preparing conditions lies to the difference of the pore forming mechanism between two porogens.
Figure 1 SEM of images of group A samples with different porogens:
Methylcellulose is a kind of substituted cellulose with long chain. The molecular structure is shown in Figure 2. According to pyrolysis experiments, methylcellulose has slow mass loss between 200 to 300 °C and intense mass loss at 310 °C, as shown in Figure 3 [14]. It can be seen that the intense mass loss begins when the temperature is over 310 °C and the mass loss reaches 88.14%. During sintering process, methylcellulose begins thermal decomposition when the sintering temperature reaches 200 °C and severe decomposition occurs at 310 °C. Therefore, the heating rate should be slow (2 °C/min) below 310 °C and stay at 310 °C for 60 min for the full decomposition of methylcellulose during the process of sintering. Rapid heating rate would cause incomplete decomposition of methylcellulose. The volatile pyrolysis products exhaust from copper matrix and then the positions they occupied become pores in the matrix [15].
Figure 2 Molecular structure of methylcellulose
Figure 3 DSC-TDG of methylcellulose
Paraffin is a polymer mixture with melting point of 50–70 °C and boiling point of 300–550 °C [16]. During sintering process, paraffin firstly melts into liquid phase when temperature reaches its melting point and then evaporates away from copper matrix leaving pores in the matrix. The liquid phase of paraffin in the copper matrix wets the particle surface. It is beneficial to the movement and rearrangement of particles during sintering and then promotes the formation of sintered necks [17, 18]. Therefore the particle surface of sample A2 is smooth and the sintering neck forms better, compared with sample A1. It is the presence of liquid phase that promotes the activation of sintering densification. So a certain degree of pore shrinkage would happen in sample A2, which results in that the pore size of sample A2 is smaller than that of sample A1, although the size of porogen in two samples is similar. The pore size distribution of two samples is shown in Figure 4. The pore size of sample A1 is mainly concentrated at 10–40 μm. However, the pore size of sample A2 is mainly concentrated at 5–30 μm. Therefore, the porosity of sample B is lower than that of sample A. The permeability is an important performance index of porous materials. It indicates the transport capacity of fluid flow through the porous body, which is determined by porosity and pore structure [19, 20]. High porosity and well connectivity between pores is the guarantee of excellent permeability. The test shows that the permeability of sample A1 is 1.5842×10–12 m2 and that of sample A2 is 1.4786×10–12 m2. According to the above analysis, the pore structures of two samples are similar, so the porosity is the main factor. The permeability of sample A1 is higher than that of sample A2, due to the higher porosity.
Figure 4 Pore size distribution of sample A1 (a) and sample A2(b)
3.2 Influence of copper powder morphology on property of copper porous materials
Figure 5 shows the SEM of images of group B samples with different copper powders as matrix under the same preparation conditions. As known, the electrolytic copper powder is arborescent and the atomized copper powder is spherical. The porogen in the two samples is methylcellulose with the same size and the same content. Therefore, the microstructure of copper porous materials made from them is different. It can be seen from Figure 5 that there are two types of pores in the samples: the macro-pores obtained by porogen and the micro- pores obtained by sintering of copper powders. The morphology of sample B1 is flocculent with irregular shaped pores, as shown in Figure 5(a). For sample B2, obvious spherical particles can be seen in the microstructure with regular shaped pores, as shown in Figure 5(b). In addition, the porosity of sample B1 is 36%, lower than that of sample B2 of 37.8%.
Figure 5 SEM of images of group B samples with different copper powders:
The pore size distributions of the two samples are shown in Figure 6. It can be seen from Figure 6 that the micro-pore size of sample B1 distributes mainly between 2 and 10 μm and the micro-pore size of sample B2 distributes mainly between 8 and 30 μm, except for macro-pores with the size of 30–50 μm. According to the preparation method, the macro-pores with size of 30–50 μm are caused by porogen and the micro-pores are caused by the sintering gap between copper powders. That is to say, the gap between arborescent copper is obviously smaller than the gap between spherical copper powders under the same cold compress and sintering condition. It is the morphology of copper powders that causes the different pore size distribution between two samples. During compress, the stacking of arborescent copper powders leaves micro-pores with irregular shape. And the contact area between arborescent copper powders is larger than that of spherical powders, so the green density of sample B1 using arborescent copper powders is higher than that of sample B2. Namely, the porosity of green compact of sample B1 is lower than that of sample B2 with the same amount of porogen under the same compress condition. In the following sintering process, the large contact area between particles is beneficial to atom migrations at the bonding surface of adjacent particles, which further promotes the well formation of sintered necks and the densification of copper matrix. So the micro-pores caused by matrix powders of sample B1 are relatively small, mainly between 2 and 10 μm. As for sample B2, it is the point contact between spherical particles with regular shaped micro-pores during compress. The contact area of adjacent particles is obviously small than that of arborescent particles. So the densification of sample B2 is lower than that of sample B1 during sintering and the micro-pores caused by matrix powders is relatively larger with the size between 8 and 30 μm. The pore size distribution further affects the permeability of the porous materials [16]. Through test, the permeability of sample B1 is 1.072×10–12 m2 and that of sample B2 is 1.557×10–12 m2. On one hand, sample B1 has lower porosity, smaller micro-pore size compared with sample B2. On the other hand, the connectivity of the irregular shaped micro-pores in sample B1 is not good as that of regular shaped micro-pores in sample B2, due to the different morphology of copper powders. Undoubtedly the permeability of porous materials with arborescent copper powders as matrix is lower than that of materials with atomized copper powders as matrix.
Figure 6 Pore size distribution of sample B1 (a) and sample B2(b)
4 Conclusions
Copper porous materials have been manufactured by the method of adding porogen. The electrolytic copper powders and atomized copper powders are used as matrix material. Methylcellulose and paraffin are used as porogen. The pore forming mechanism of methylcellulose is pyrolysis. The pore forming mechanism of paraffin is melting and then boiling. The copper porous materials with paraffin as porogen have lower porosity and permeability than materials with methylcellulose as porogen, because the melting paraffin promotes the activation of sintering densification. The morphology of copper powders also influences the microstructure of porous materials. Electrolytic copper powder is arborescent and atomized copper powder is spherical. The contact state between adjacent particles is different for the two kinds of powders. The gap between arborescent coppers after pressing is obviously smaller than the gap between spherical copper powders, which is beneficial for the sintering shrinkage. So the porous materials with arborescent copper powders as matrix has lower porosity, smaller pore size, irregular pore shape and lower permeability, compared with materials using atomized copper powders as matrix.
References
[1] TANG Hui-ping, TAN Ping, XI Zheng-ping. Research progress of sintered porous metal [J]. Rare Metal Materials and Engineering, 2006, 35(2): 429–431. (in Chinese)
[2] CHEN Wen-gen, ZHANG Qiang. Characteristics application fabrication and development of porous metals [J]. Powder Metallurgy Industry, 2005, 15(2): 37–40. (in Chinese)
[3] HUANG Cai-min. Application research and development prospects of porous materials [J]. Equipment Manufacturing Technology, 2014(2): 230–232. (in Chinese)
[4] CHEN Wei, QU Man. Analysis of the heat transfer and airflow in solar chimney drying system with porous absorber [J]. Renew Energy, 2014, 63: 511–518. (in Chinese)
[5] MINKO D, BELYAVIN K. A porous materials production with an electric discharge sintering [J]. Int Journal of Refractory Metals and Hard Materials. 2016, 59: 67–77.
[6] WEI Zhou, WANG Qing-hui. Characterization of three- and four-point bending properties of porous metal fiber sintered sheet [J]. Int J Heat and Mass Transfer, 2012, 55: 3618–3632.
[7] BOVAND M, RASHIDI S, ESFAHANI J. Heat transfer enhancement and pressure droppenalty in porous solar heaters: Numerical simulations [J]. Sol Energy, 2016, 123: 145–159.
[8] MONTES J M, RODRIGUEZ J A, HERRERA E J. Thermal and electric conductivities of sintered powder compacts [J]. Powder Metallurgy, 2003, 46(3): 251–256
[9] LI Chuan-fu, LI Yan-fang. Research progress on mechanical properties of metallic porous materials [J]. Equipment Manufacturing Technology, 2015, 8: 244–245. (in Chinese)
[10] MEDHAT A E, SALEH K. Mechanical and physical characterization of copper foam [J]. Int J Mech Mater Des, 2008, 4(3): 63–69.
[11] ZHAO C Y. Review on thermal transport in high porosity cellular metal foams with open cells [J]. Materials and Design, 2014, 56(4): 522–527.
[12] REN Xiao-jun, ZHANG Peng, WANG Xiao-jun, PAN Yan-pin. Permeability, thermal conductivity and the pore characters of sintered porous metal materials [J]. Journal of Shanghai Jiao Tong University, 2013, 47(3): 352–357. (in Chinese)
[13] BHATTACHARY A, CALMIDI V V, MAHAJAN R L. Thermophysical properties of high porosity metal foams [J]. International Journal of Heat and Mass Transfer, 2002, 45: 1017–1031.
[14] HAN Fei, CHEN Yu-hong, MA Jian-jun. Effects of CMC different content on the preparation of porous silicon carbide ceramic [J]. Guangzhou Chemistry, 2011, 39(5): 72–74. (in Chinese)
[15] WANG Yong-hong, ZHANG Yang, LIU Xing-qin. Microstructure control of ceramic membrane support from corundum-rutile powder mixture [J]. Powder Technology, 2006, 168: 125–133. (in Chinese)
[16] GUO Lai-yang, ZHANG Jing-wei, ZHAO Jing, WANG Jian-xn, WEN Jie, ZHANG Cong. Preparation and characterization of porous scaffolds with favorable interpore [J]. Journal of Inorganic Materials, 2011, 26(1): 17–21. (in Chinese)
[17] LI Bo-qing, LI Zhi-qiang, LU Xing. Effect of sintering processing on property of porous Ti using space holder technique [J]. Trans Nonferrous Met Soc China, 2015, 25: 2965–2973.
[18] PARHAMI F, MCMEEKING R M, COCKS A C F, SUO Z. A model for the sintering and coarsening of rows of spherical particles [J]. Mechanics of Materials, 1999, 31: 43-61.
[19] MEYERS J J, NAHAR S, LUDLOW D K, LIAPIS A I. Determination of the pore connectivity and pore size distribution and pore spatial distribution of porous chromatographic particles from nitrogen sorption measurements and pore network modeling theory [J]. Journal of Chromatography A, 2001, 907: 57–71.
[20] LI Bin-qiang, YAN Fen, LU Xuan. Effect of microstructure on the tensile property of porous Ti produced by powder metallurgy technique [J]. Materials Science and Engineering A, 2012, 534: 43-52.
(Edited by FANG Jing-hua)
中文导读
造孔剂种类和铜粉形貌对烧结铜多孔材料性能的影响
摘要:分别以电解铜粉和雾化铜粉作为原材料,采用粉末冶金的方法制备了烧结铜多孔材料,其中造孔剂选用了甲基纤维素和石蜡两种。研究了造孔剂种类和铜粉形貌对烧结铜多孔材料性能的影响。结果表明,由于造孔机理的不同,选用不同造孔剂所得多孔材料的性能有差异。与以甲基纤维素为造孔剂制得的样品相比,以石蜡为造孔剂所制得的样品有孔隙率和渗透率更小。甲基纤维素的成孔机理是热分解,而石蜡的成孔机理是熔融蒸发。铜粉形貌影响铜颗粒之间的相互接触形式,进而影响烧结过程中烧结颈的形成。与以雾化铜粉为基体的材料相比,使用电解铜粉作为基质的多孔材料具有较低的孔隙率,较小的孔径和较渗透率。
关键词:烧结铜多孔材料;烧结颈;孔隙率;渗透率
Foundation item: Project(2015DFR50580) supported by International S&T Cooperation Program of China; Project(51505503) supported by the National Natural Science Foundation of China
Received date: 2017-04-14; Accepted date: 2018-01-09
Corresponding author: CHEN Jie, PhD, Associate Professor; Tel: +86–731–88876566; Fax: +86–731–88876566l; E-mail: chenjiecsu@163.com; ORCID: 0000-0003-2083-0725
Abstract: Copper porous materials have been manufactured by the method of powder metallurgy. Electrolytic copper powders and atomized copper powders are used as matrix material. Methylcellulose and paraffin are used as porogen. The influence of porogen type and copper powder morphology on the property of copper porous materials is investigated as well. The results show that copper porous materials with paraffin as porogen have lower porosity and permeability compared with materials using methylcellulose as porogen, due to the different pore-forming mechanisms. The pore forming mechanism of methylcellulose is thermal decomposition, while the pore forming mechanism of paraffin is melting–evaporation. The morphology of copper powders affects the contact state between adjacent powders, which further influence the sintering shrinkage. The porous materials using arborescent copper powders as matrix have lower porosity, smaller pore size and lower permeability, compared with materials with atomized copper powders as matrix.
- Influence of porogen type and copper powder morphology on property of sintering copper porous materials
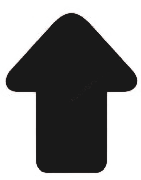