- Abstract:
- 1 Introduction▲
- 2 Experimental and princi...▲
- 3 Effect of hydrogen inhi...▲
- 4 Effect of hydrogen inhi...▲
- 5 Determination of chemic...▲
- 6 Conclusions▲
- References
- Figure
- Fig.1 Equivalent circuit(a) and AC impedance(b) diagrams of adsorption of hydrogen inhibitor
- Fig.2 Effect of hydrogen inhibitor on partial current density of Zn, Fe in Zn-Fe alloy codeposition
- Fig.3 Effect of hydrogen inhibitor on differential capacitance of double layer of electrode/electrolyte interface
- Fig.4 Effect of concentration of hydrogen inhibitor on
- Fig.5 AC impedance diagram of chemical adsorption of hydrogen inhibitor
J. Cent. South Univ. Technol. (2007)03-0336-04
DOI: 10.1007/s11771-007-0066-4
Mechanism of current efficiency improvement of Zn-Fe alloy electroplating by hydrogen inhibitor
WANG Yun-yan(王云燕), CHAI Li-yuan(柴立元)
(School of Metallurgical Science and Engineering, Central South University, Changsha 410083, China)
Abstract:The effect of hydrogen inhibitor on partial current densities of Zn, Fe and differential capacitance of electrode/electrolyte interface, and adsorbing type of hydrogen inhibitor were studied by the methods of electrochemistry. The mechanism of current efficiency improvement were explained from the point of valence electron theory. The results indicate that the partial current density of Fe increases in addition of hydrogen inhibitor, which reaches the maximum of 0.14 A/dm2 when current density is 0.2 A/dm2. Differential capacitance of electrode/electrolyte interface decreases obviously from 20.3 μF/cm2 to 7 μF/cm2 rapidly with the concentration varying from 0 to 20 mL/L, because hydrogen inhibitor chemically adsorbs on active points of Fe electrode surface selectively. Element S in hydrogen inhibitor with negative electricity and strong capacity of offering electron shares isolated electrons with Fe. The adsorption of H atom is inhibited when adsorbing on active points of Fe electrode surface firstly, and then current efficiency of Zn-Fe alloy electroplating is improved accordingly.
Key words:Zn-Fe alloy electroplating; current efficiency; hydrogen inhibitor; mechanism
1 Introduction
The electrochemistry of metal deposition and dissolution, in the past, was mostly an applied science, and only in resent years some fundamental knowledge has been accumulated in this field[1-6]. Binary alloys formed with zinc and iron have been investigated and applied widely. Among electroplating systems, zinc alloy coatings electroplated in alkaline zincate solution have many beneficial properties, such as excellent corrosion resistance, good ductibility, good painting characteristics, low hydrogen embrittlement, and small internal stress. And alkaline zincate system with the advantages of simple component, good spreading and covering power, being propitious to complicated electroplate accessory, less corrosion to equipment, lower cost, and so on, attracts more attention throughout the world. However, lower current efficiency (50%-80%,commonly about 65%) has become the main reason that restricts the development and application of alkaline zincate solution[7-9]. Fe element was introduced and Zn-Fe alloy coating was formed in order to improve the corrosion resistance. However, current efficiency of Zn-Fe alloy electroplating is lower than that of Zn deposition, and current efficiency decreases gradually with Fe content of coating increasing[10]. The reason is that on one hand negative deposition potential of complex Zn(OH)42- results in hydrogen separation inevitably in alkaline zincate solution; on the other hand, smaller overpotential of hydrogen on Fe than that on Zn promotes hydrogen evolution[11-13].
Based on the previous results[14], the hydrogen inhibitor belonging to sulfur family compound can distinctly improve current efficiency of Zn-Fe alloy electroplating from 63.28% up to 83.54%, and the optimum concentration is 20 mL/L. In this study, mechanism and essence of improvement of current efficiency of Zn-Fe alloy electroplating by hydrogen inhibitor were explored.
2 Experimental and principle
2.1 Electrochemical test
Electrochemical measurements were conducted by CHI660A electrochemical workstation monitored by computer. The cell was maintained in a thermostated water bath to keep a constant temperature of 25 ℃. The electrolyte was made of 180 g/L NaOH dissolved in redistilled water. Cathodic current efficiency was measured by copper coulometer[15]. Partial current density curves were studied by chronopotentiometry, and the thickness of Zn-Fe alloy coating was controlled to be larger than 5 μm to assure the veracity of measurement. The content of Fe in Zn-Fe alloy coating was measured by spectrophotometer after dissolved in 1:1 HCl solution[16].
2.2 Determination principle of differential capacitance of electrode/electrolyte interface
There are many methods to measure differential capacitance of electrode/electrolyte interface double layer, such as chronopotentiometry, and chrono- amperometry. In this study, chronoamperometry was adopted. The condition should be controlled under electrochemical polarization (Δφ<10 mV). The relationship between current and time can be expressed as[17]:
(1)
where R1 is the resistance of solution; Rr is the resistance of electrochemical reaction; Cd is the differential capacitance of double layer. In order to determine Cd, there should be no electrochemical reaction in the potential range chosen, then Rr→∞. When R1 is neglected, Eqn.(1) can be written as
(2)
When taking Δφ<10 mV and constant potential into account,integral of Eqn.(2) is
(3)
Differential capacitance of double layer Cd can be calculated according to the integral of current vs time curve measured in experiment.
2.3 Determination principle of adsorption type of hydrogen inhibitor
Based on AC impedance theory of electrode surface process[18], supposing that hydrogen inhibitor adsorbs on electrode surface, non-Faraday adsorption impedance can be expressed as follows:
(4)
where w is the angular frequency.
The corresponding equivalent circuit sketch and AC impedance diagram are shown in Fig.1. Here Rsol is the resistance of solution; Cdl is the capacitance of double layer; Ra and Ca are adsorption resistance and adsorption capacitance caused by hydrogen inhibitor adsorption on electrode surface, respectively; Rw and Cw are Warburg resistance and capacitance caused by hydrogen inhibitor diffusion from solution to electrode surface, respectively.
When existing chemical adsorption, AC impedance diagram is made up of a semicircle representing adsorption and a beeline with angle of 45? to abscissa representing diffusion. While without chemical adsorption, AC impedance diagram is only a beeline with angle of 45? to abscissa. Because there are not oxidation and reduction reactions in cyclic voltammetrical curves, the adsorption type of hydrogen inhibitor can be determined by AC impedance under equilibrium potential.
Fig.1 Equivalent circuit(a) and AC impedance(b) diagrams of adsorption of hydrogen inhibitor
3 Effect of hydrogen inhibitor on partial current density of Zn and Fe
Partial current densities of Zn and Fe with or without hydrogen inhibitor were determined under the conditions of total concentration of Zn and Fe being 0.225 mol/L, molar ratio of Zn to Fe being 4:1, ascorbic acid being 0.6 g/L, complex ZFC being 30 ml/L in order to find out the effect of hydrogen inhibitor on Zn and Fe deposition. The results are shown in Fig.2.
Fig.2 Effect of hydrogen inhibitor on partial current density of Zn, Fe in Zn-Fe alloy codeposition
(Hydrogen inhibitor concentration: 1—20; 2—0; 3—0; 4—20 mL/L)
There is a little change of partial current density of Zn, while a marked improvement of that of Fe can be found. The maximum increase is from 0.10 A/dm2 up to 0.14 A/dm2 when cathodic current density is 0.2 A/dm2. Accordingly, partial current density of hydrogen separation declines. Hydrogen inhibitor improves cathodic current efficiency of Zn-Fe alloy electroplating through acting with Fe and inhibiting evolution of hydrogen, which is consistent with the results of technique experiments[12].
4 Effect of hydrogen inhibitor on differential capacitance of electrode/electrolyte inter- face
It is reasonable to choose Fe electrode to study adsorption behaviours of hydrogen inhibitor. Differential capacitance of electrode/electrolyte interface double layer measured by chronoamperometry under different potentials when the concentration of hydrogen inhibitor is 20 mL/L is shown in Fig.3.
Fig.3 Effect of hydrogen inhibitor on differential capacitance of double layer of electrode/electrolyte interface
(Hydrogen inhibitor concentration: 1—20; 2—0 mL/L)
It is obvious that there is a little change of differential capacitance with the negative movement of cathodic potential when there is not hydrogen inhibitor in electrolyte. The differential capacitance decreases evidently when there is hydrogen inhibitor in electrolyte. A capacitance peak correlated with adsorption appears at the potential of -0.2 V. Accordingly charge on electrode surface changes suddenly and differential capacitance of double layer decreases from 58.35 μF/cm2 to 14.18 μF/cm2 rapidly. Desorption peak of hydrogen inhibitor is not found before -1.0 V of hydrogen evolution. Therefore, the decrease of differential capacitance of electrode/electrolyte interface with addition of hydrogen inhibitor indicates that hydrogen inhibitor adsorbs on electrode surface.
Effect of the concentration of hydrogen inhibitor on differential capacitance at equilibrium potential of -0.6 V(vs Hg/HgO) is shown in Fig.4. Differential capacitance decreases rapidly from 20.3 μF/cm2 to 7 μF/cm2 with the concentration of hydrogen inhibitor increasing gradually. Differential capacitance does not decrease any longer when the concentration of hydrogen inhibitor is up to 20 mL/L, which indicates that the adsorption is saturate and maintains at about 5 μF/cm2. So it can be illustrated that the current efficiency improves with addition of hydrogen inhibitor, and too more hydrogen inhibitor adsorbs on surface of Zn atom and inhibits hydrogen evolution. Accordingly, current efficiency declines when the concentration of hydrogen inhibitor is too large.
Fig.4 Effect of concentration of hydrogen inhibitor on differential capacitance
5 Determination of chemical adsorption of hydrogen inhibitor
The hydrogen inhibitor, a kind of organic substance containing sulfur, does not react with other components in electrolyte[19]. Sulfur takes negative charges because of p-π bond of C==S, so hydrogen inhibitor belongs to anion surfactants affecting electrode reaction with adsorption. The selective adsorption on Zn and Fe electrode surface indicates that it may be chemical adsorption of hydrogen inhibitor on Fe surface. Electrode interface process and AC impedance are adopted to determine the adsorption type of hydrogen inhibitor.
AC impedance diagram of electrolyte with or without hydrogen inhibitor is measured under the conditions of potential being -0.7 V(vs Hg/HgO), and disturbance signal being within 0.005 V(Fig.5).
It is obvious that AC impedance diagram is made up of a semicircle representing adsorption within high frequency range and a beeline representing diffusion within low frequency range when hydrogen inhibitor is added into electrolyte, which is similar to the above theoretical AC impedance. AC impedance diagram shows only a beeline in electrolyte without hydrogen inhibitor, which indicates that hydrogen inhibitor adsorbs on the electrode surface, forms chemical bond, and affects the evolution process of hydrogen. Therefore, hydrogen inhibitor adsorbs on active points of Fe atom in Zn-Fe alloy coating during electroplating, inhibits the evolution of hydrogen, and then improves current efficiency.
Fig.5 AC impedance diagram of chemical adsorption of hydrogen inhibitor
(Hydrogen inhibitor concentration: 1—20; 2—0 mL/L)
Element S in hydrogen inhibitor with negative electricity and strong capacity of offering electron shares isolated electrons with Fe, adsorbing on active points of the surface of Fe electrode firstly. The adsorption of H atom is inhibited and overpotential of hydrogen evolution is enhanced, and then current efficiency of Zn-Fe alloy electroplating is improved accordingly. Hydrogen inhibitor has little effect on the current efficiency of Zn electroplating because element S cannot adsorb on its surface chemically owning to its outer orbit being full of valence electrons.
6 Conclusions
1) Partial current density curves indicate that there is little effect of hydrogen inhibitor on electroplating of Zn, while a marked improvement of partial current density of Fe can be found. The maximum increase is from 0.10 A/dm2 up to 0.14 A/dm2 when current density is 0.2 A/dm2. Accordingly, partial current density of hydrogen declines. Hydrogen inhibitor improves current efficiency of Zn-Fe alloy electroplating through acting with Fe and inhibiting evolution of hydrogen, which is consistent with the results of technique experiments.
2) The results of effect of hydrogen inhibitor on differential capacitance of electrode/electrolyte interface indicate that the differential capacitance decreases evidently through adsorption on Fe electrode surface. Differential capacitance decreases rapidly from 20.3 μF/cm2 to 7 μF/cm2 when the concentration of hydrogen inhibitor is up to 20 mL/L. Studies on the selective adsorption and AC impedance of hydrogen inhibitor show that hydrogen inhibitor chemically adsorbs on active points of Fe atom in Zn-Fe alloy coating.
3) Element S in hydrogen inhibitor with negative electricity and strong capacity of offering electron shares isolated electrons with Fe, adsorbing on active points of the surface of Fe electrode firstly; then the adsorption of H atom is inhibited, and at last current efficiency of Zn-Fe alloy electroplating is improved accordingly.
References
[1] YANG C Q, LONG Z L, ZHOU Y C. A sulphate bath for the preparation of Zn-Fe alloy coatings[J]. Trans Inst Metal Finish, 2002, 80(5): 161-163.
[2] TREJO G, ORTEQA R, MEAS Y. et al. Effect of benzylideneacetone on the electroplating mechanism of Zn-Co alloy[J]. Journal of Applied Electrochemistry, 2003, 33(5): 373-379.
[3] ORDINE A P, DIAZ S L, MARQARIT I C P, et al. Zn-Ni and Zn-Fe alloy deposits modified by P incorporation: Anticorrosion properties[J]. Electrochimica Acta, 2004, 49(17/18): 2815-2823.
[4] YANG C Q, ZHOU Y C, LONG Z L. Electroplating and physico-chemical properties of Zn-Fe alloy coatings from sulfate solution[J]. Journal of Materials Science Letters, 2002, 21(21): 1677-1680.
[5] LONG Z L, ZHOU Y C, XIAO L. Characterization of black chromate conversion coating on the electrodeposited zinc-iron alloy[J]. Applied Surface Science, 2003, 218(1/4): 123-136.
[6] BAJAT J B, MISKOVIC-STANKOVIC V B, KACAREVIC- POPOVIC Z. The influence of steel surface modification by electrodeposited Zn-Fe alloys on the protective behaviour of an epoxy coating[J]. Progress in Organic Coatings, 2003, 47(1): 49-54.
[7] PAATSCH W, KAUTEK W, SAHRE M. Corrosion behavior and mechanical properties of plated Zn-alloys[J]. Trans Inst Metal Finish, 1997, 75(6): 216-218.
[8] SHORT N R, DENNIS J K. Corrosion resistance of zinc-alloy coated steel in construction industry environments[J]. Trans Inst Metal Finish, 1997, 75(2): 47-52.
[9] BIKULCIUS G. Control of thickness of corrosion-resistant Zn-Fe, Zn-Co and Zn-Ni coatings[J]. Plate surface Finishing, 1997, 84(8): 31-32.
[10] WANG Yun-yan, PENG Wen-jie, SHU Yu-de, et al. Cathodic current efficiency of Zn electroplating in zincate solutions[J]. Electroplating and Pollution, 2003, 23(6): 12-16. (in Chinese)
[11] WANG Yun-yan, PENG Wen-jie. Cathodic current efficiency of Zn-Fe alloy electroplating in zincate solutions[J]. Material Protection, 2004, 37(5): 16-18. (in Chinese)
[12] WANG Yun-yan, PENG Wen-jie, SHU Yu-de, et al. Study on the process of Zn-Fe alloy electroplating in alkaline zincate solution[J]. Electroplating and Pollution, 2003, 23(2): 11-14. (in Chinese)
[13] WANG Yun-yan, PENG Wen-jie, CHAI Li-yuan, et al. Electrochemical behaviors of Zn-Fe alloy and Zn-Fe-TiO2 composite electroplating[J]. Journal of Central South University of Technology, 2003, 10(3): 183-189.
[14] WANG Yun-yan. Study on the Technics and Foundational Theories of Zn-Fe Alloy Electroplating and Zn-Fe-TiO2 Composite Electroplating[D]. Changsha: Central South University, 2002: 5. (in Chinese)
[15] TU Zhen-mi. Principle and Techniques of Alloy Electroplating[M]. Beijing: National Defence Industry Press, 1993: 231-243. (in Chinese)
[16] WANG Yun-yan, SHU Yu-de, XIE Qin. Spectrophotometric analysis of iron concentration in zinc-iron alloy electroplate coating and solution[J]. Electroplating and Pollution, 2002, 22(1): 23-25. (in Chinese)
[17] SHU Yu-de, CHEN Bai-zhen. Research Technique of Metallurgical Electrochemistry[M]. Changsha: Central South University of Technology Press, 1990: 95-232. (in Chinese)
[18] TIAN Zhao-wu. Research Methods of Electrochemistry[M]. Beijing: Science Press, 1984: 240-246; 327. (in Chinese)
[19] ZHA Quan-xing. Introduction to Dynamics of Electrode Process(edition II)[M]. Beijing: Science Press, 1987: 407-415. (in Chinese)
(Edited by YANG Bing)
Foundation item: Projects(50274073) supported by the National Natural Science Foundation of China
Received date: 2006-08-20; Accepted date: 2006-10-27
Corresponding author: CHAI Li-yuan, Professor, PhD; Tel: +86-731-8836921; E-mail: lychai@mail.csu.edu.cn
- Mechanism of current efficiency improvement of Zn-Fe alloy electroplating by hydrogen inhibitor
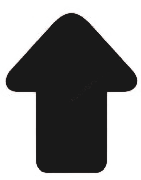