- Abstract:
- 1 Introduction▲
- 2 Composite model for ful...▲
- 3 Stress—strain relation ...▲
- 4 Results and discussion▲
- 5 Conclusions▲
- References
- Figure
- Fig.1 Microstructure of NC materials: (a) Structure repeated by unit cubic cells; (b) Unit cubic cell consisting of grain interior and grain boundary phase
- Fig.2 Deformation mechanism map showing areas with different values of relative contribution of dislocation glide mechanism (Scale: from zero (no dislocation controlled plasticity) to unity (no diffusion controlled plasticity))[6]
- Fig.3 Comparison between calculated true stress—strain curves of NC Ni and corresponding true stress—strain data converted from experimental result in Ref.[15]
- Fig.4 Calculated rate dependence of yield strength of NC Ni for different grain sizes using conventional semi-log format
- Fig.5 Comparison between published true stress-strain data of NC Fe and predictions by developed model
- Fig.6 Strain rate dependence of calculated yield strength of porous NC Fe in high strain rate range of 1-104 s-1
J. Cent. South Univ. Technol. (2008) 15(s1): 447-452
DOI: 10.1007/s11771-008-397-9
Mechanical model for yield strength of nanocrystalline materials under high strain rate loading
ZHU Rong-tao(朱荣涛)1, ZHOU Jian-qiu(周剑秋)1, MA Lu(马 璐)1, ZHANG Zhen-zhong(张振忠)2
(1. School of Mechanical Engineering, Nanjing University of Technology, Nanjing 210009, China;
2. School of Materials Science and Engineering, Nanjing University of Technology, Nanjing 210009, China)
Abstract:
To understand the high strain rate deformation mechanism and determine the grain size, strain rate and porosity dependent yield strength of nanocrystalline materials, a new mechanical model based on the deformation mechanism of nanocrystalline materials under high strain rate loading was developed. As a first step of the research, the yield behavior of the nanocrystalline materials under high strain rate loading was mainly concerned in the model and uniform deformation was assumed for simplification. Nanocrystalline materials were treated as composites consisting of grain interior phase and grain boundary phase, and grain interior and grain boundary deformation mechanisms under high strain rate loading were analyzed, then Voigt model was applied to coupling grain boundary constitutive relation with mechanical model for grain interior phase to describe the overall yield mechanical behavior of nanocrystalline materials. The predictions by the developed model on the yield strength of nanocrysatlline materials at high strain rates show good agreements with various experimental data. Further discussion was presented for calculation results and relative experimental observations.
Key words:
nanocrystalline materials; deformation mechanism; modeling; yield strength; high strain rate;
1 Introduction
Nanocrystalline(NC) materials have attracted many investigations on their mechanical behaviors due to their ultra-high yield and fracture strengths, superior wear resistance and enhanced superplastic formability. The details can be seen in the review presented by MEYERS et al[1]. Nevertheless, the high strain rate deformation mechanism is not clear so far, and few constitutive models are built based on the deformation mechanisms at high strain rates for NC materials. YOO et al[2] studied the effect of grain size on dynamic compression properties of NC tantalum consolidated by plasma pressure compaction, but they did not present discussion about the deformation mechanism for their tests at high strain rates. JIA et al[3] systematically studied the experimental mechanical behaviors of consolidated iron with average grain sizes from tens of nanometers to tens of microns under uniaxial compression over a wide range of strain rates. But their tests just cover the grain size range from 80 nm to 20 μm and their constitutive model was built on the dislocation mechanism only, and no detail deformation mechanism difference is given between the low strain rate loading and high strain rate loading. Several researchers[4-6] developed their strain rate dependent model for the mechanical behavior of NC materials, but these models did not include the high strain rate loading cases.
The deformation mechanism of the NC material is very complicated. Even for the same material, the deformation mechanism will also change with the further deformation. For example, shear band evolution phenomena during the plastic deformation process have been observed in the high strain rates tension and compression tests[2-3]. This indicates that the deformation will become non-uniform in the plastic deformation. At present, we will focus on the yield behavior of the NC materials under high strain rate loading in this work and uniform deformation will be assumed for simplification. In this work, the grain interior and grain boundary deformation mechanisms under high strain rate loading were analyzed, then a new mechanical model based on their deformation mechanisms for the yield strength of NC materials under high strain rate loading was developed, and the grain size and porosity effect were considered in the developed model. Finally, the model presented in this paper was applied to predicting the yield strength of NC materials at high strain rates and the predictions were compared with experimental data.
2 Composite model for full density NC materials
It is known that NC material is a composite consisting of some distinct phases: grain interior, grain boundary and triple junction. For simplification, triple junction will be incorporated in the grain boundary in term of volume in this paper. It is assumed that the NC materials are composed of an array of repeating unit cubic cells, which is shown in Fig.1(a). The unit cubic cell shown in Fig.1(b) consists of grain interior and grain boundary. Then the volume fraction of grain interior phase, denoted as f, can be written as
(1)
where d and δ are the grain size and grain boundary thickness, respectively. So the volume fraction of grain boundary phase is 1-f.
Fig.1 Microstructure of NC materials: (a) Structure repeated by unit cubic cells; (b) Unit cubic cell consisting of grain interior and grain boundary phase
2.1 Mechanical model for grain interior phase under high strain rate loading
For NC materials under quasi-static loading, dislocation glide mechanism and diffusion controlled mechanism are the main carriers of plastic deformation[6]. But, diffusion controlled mechanism has no enough time to operate under high strain rate loading. The deformation mechanism map (presented by KIM and ESTRIN[6]) shown in Fig.2 also shows that the relative contribution of diffusion controlled mechanism decreases with increasing strain rate. Therefore, diffusion controlled mechanism can be neglected in the mechanical modeling for grain interior phase under high strain rate loading. However, the dislocation controlled mechanisms are different between FCC and BCC NC materials in a numerical way.
2.1.1 Constitutive relation of FCC NC metals
The contribution of dislocation glide to the plastic strain rate of the grain interior phase in FCC metals is related to the dislocation density(ρ) and to the stress acting
Fig.2 Deformation mechanism map showing areas with different values of relative contribution of dislocation glide mechanism (Scale: from zero (no dislocation controlled plasticity) to unity (no diffusion controlled plasticity))[6]
in the grain interior phase (σGI), which can be written as follows[6]:
, (2)
where is the strain rate of grain interior phase; ρ0 is the initial value of ρ; and
σ0 and m are the material parameters for a given temperature. The Heaviside step-function Θ(d-dc) item used in Eqn.(2) was taken into account the possible event that dislocation mechanism may cease operating and the dislocation contribution to
vanishes when d is smaller than a critical value dc. The evolution equation considering the dislocations storage and annihilation for the dislocation density is
(3)
where t denotes the time and n is constant at a fixed temperature; C is an extra term accounting for the static recovery; C1 is a constant accounting for the dislocation storage, which is an athermal process; and C2 is a constant to represent the thermally activated dynamic recovery process. Their detail determination methods can be seen in Ref.[7].
2.1.2 Constitutive relation of BCC NC metals
For grain interior phase of BCC materials it has been established that the primary barriers to the motion of the screws are lattice related peierls barriers, the screw dislocations themselves move by the nucleation and propagation of kink pairs. The flow stress needed to overcome the short-range and these long-range barriers can be written as[3]
(4)
(5)
(6)
where τathermal is athermal stress and not affected by strain rate or temperature in the low temperature regime. At very low strain rate (≤10-4 s-1), is close to zero, thus the material constants
, β and strain hardening function can be determined by experimental stress—strain data of coarse-grained materials at low strain rate. ΔGk0 is taken as 0.675 eV for BCC metals, the detail determination of
can be seen in Ref.[3].
2.2 Mechanical model for grain boundary phase under high strain rate loading
The nature of the grain boundaries and the triple junctions is not very well known so far and it is actually impossible to produce and mechanically test a grain boundary specimen. Atomic simulations[8-9] revealed that no regular organization for atomic structure exists in the grain boundary regions, thus the grain boundary phase is usually amorphous and taken as a metallic glass-producing system.
As mentioned before, diffusion controlled mechanism has no enough time to operate under high strain rate loading, thus grain boundary sliding controlled mechanism with rate-independent properties is assumed in this paper for the deformation of grain boundary phase. For the description of this rate-independent mechanical behavior, Drucker’s constitutive equation which has been proven to be suitable for the modeling of metallic glasses[10] and the grain boundary[11] of NC materials will be used to mechanically model the grain boundary. It is written as
(7)
where σGB, and
are denoted as the flow stress, yield stress and plastic strain of grain boundary; hGB, nGB and m are material constants of the grain boundary; p=(-1/3)σkk is the hydrostatic pressure. It is commonly accepted that the yield strength of amorphous materials ranges from 50% to 80% of the corresponding coarse-grained materials.
2.3 Composite model for yield strength
For the NC materials treated as composite materials with grain interior phase and grain boundary phase, the methods based on the rule of mixtures are relatively simple and intuitive. Voigt model (the strain in both grain interior phases and grain boundary phase are the same and equal to the overall strain) is usually used in the mixtures-based models since it is much more favorable computationally compared with Reuss model, thus it will be applied here to coupling the grain boundary constitutive relation with mechanical model for grain interior phase. Therefore, the overall stress of the NC materials, consisting of grain interior phase and grain boundary phase, reads
σ=fσGB+(1-f)σGB (8)
Then by increasing the overall stain level, one can get the entire overall stress—strain curve, further the yield strength of such a composite system can be evaluated by the stress at 0.2% offset strain.
3 Stress—strain relation of porous NC materials with small plastic deformation
Porosity often exists in NC materials. To get the stress—strain relation of porous NC materials, Budiansky’s self-consistent approach[12], for the composites considered consist of random mixtures of N isotropic constituents, is applied in this paper. Previously, KIM and BUSH[13] ever applied Budiansky’s self-consistent approach to evaluating the effect of porosity on plastic modulus of NC materials, here, Budiansky’s self- consistent method is extended to describe the stress—strain relation of porous NC materials in conjunction with the secant-moduli approach.
For the full density NC materials, its secant plastic modulus () and secant Poisson ratio
at a given level of stress σ (the corresponding strain is ε, which can be determined by the method in Section 2), can be written as
(9)
where Ef and νf are the plastic modulus and Poisson ratio of the full density NC materials, respectively, and they can be determined by other method[13-14]. One can get the secant bulk and shear modulus of the full density NC materials
(10)
Meanwhile, pore is also treated as an independent phase in NC materials with zero strength, and its secant bulk and shear modulus are zero also. If the volume fraction of pore is denoted as p, then the volume fraction of full density NC can be determined as 1-p. According to Budiansky’s self-consistent method, the overall secant bulk modulus Ks and shear modulus Gs of the porous NC materials can be solved by the secant and shear modulus data of the full density NC materials
(11)
(12)
(13)
where νs is the overall secant Poisson ratio of porous NC materials and can be given by
(14)
thus the overall secant elastic modulus of porous NC materials can be expressed as
(15)
It is further assumed that the strain ε in the full density NC equals that of pore phase, then the overall strain can be determined as
(16)
and the overall stress follows immediately at a given level of applied overall strain
(17)
Here, it should be noted that this sort of iso-strain assumption is approximately reasonable for the small plastic deformation. By changing the level of applied overall strain, the corresponding overall secant plastic modulus and overall stress can be calculated respectively. Therefore, the over stress—strain relation of porous NC materials can be determined.
4 Results and discussion
4.1 Tensile strength of full density NC Ni
The developed method is firstly applied to predicting the high strain rate tensile behavior of full density NC electroplated Ni (FCC metal), which has been tested by DALLA et al[15]. In their experimental work, one batch of NC Ni with the grain size of 20.6 nm was tested at high strain rates. In order to compare with the calculated value with the developed method, those engineering stress—strain curves are converted into true stress—strain curves. During the numerical calculations, the material constants used in the calculations are given in Ref.[16]. Fig.3 gives the comparison results between the calculated true stress—strain curves and the corres- ponding true stress—strain data converted from the published experimental results[15]. It can be seen that most of the numerical results are in good agreement with the experimental data in the literature. Although the experimental engineering plastic strains in Ref.[15] only reach 1.2% to 1.8%, which is enough to determine the yield strength (σ0.2) of this sort of material. Fig. 4 shows the rate dependence of the calculated yield strength values. Strain rate hardening is evident overall in the figure and the developed method can fit this sort of strain rate hardening propensity.
Fig.3 Comparison between calculated true stress—strain curves of NC Ni and corresponding true stress—strain data converted from experimental result in Ref.[15]
Fig.4 Calculated rate dependence of yield strength of NC Ni for different grain sizes using conventional semi-log format
4.2 Compression strength of porous NC Fe
JIA et al[3] performed five dynamic compression tests on the consolidated NC Fe (BCC metal) with small porosity at the strain rate of 3×103-6×103 s-1. The density and average grain sizes of the five samples are listed in Table 1 and their experimental true stress-strain curves together with the corresponding predictions by the developed model in this mode are plotted in Fig.5. The material constants used in the calculations can be found in Ref.[3]. Obviously, the developed model can make good predictions on the yield strength and strain hardening behaviors of those samples. With the decrease of grain size, the yield strength also gets enhanced, but the strain hardening is changed into strain softening gradually. It is well known that the strain hardening behavior of grain boundary phase is different from that of grain interior phase, and increasing volume fraction of grain boundary with the decrease of grain size will lead to gradually decreasing of strain hardening rate. On the other hand, JIA et al[3] observed non-uniform deformation in their compression experiments. This mechanism can also cause a change of overall strain hardening behavior.
Table 1 Density and grain sizes of five samples in Ref.[3]
Fig.5 Comparison between published true stress-strain data of NC Fe and predictions by developed model
Strain rate dependence of the calculated yield strength of the five NC Fe samples in Table 1 in a high strain rate range of 10-105 s-1 is plotted in Fig.6. It can be found that the smaller grain size material shows less relative strengthening of yield strength at high strain rate condition. This fits well with the similar experimental observations by JIA et al[3] about the strain rate dependence of the flow stress (at a fixed strain of 4%) of the consolidated Fe. This indicates that the model developed in this paper can reflect the rate-strength behaviors of the yield strength over a wide grain size and strain rate range. Due to different strain rate sensitivity behaviors of grain boundary phase and grain interior phase, the rate-strength of the yield strength of NC materials that have much higher volume fractions than that of coarse-grained materials, is much smaller than that observed at conventional grain sizes.
Fig.6 Strain rate dependence of calculated yield strength of porous NC Fe in high strain rate range of 1-104 s-1
5 Conclusions
A new mechanical model based on the deformation mechanism is developed to describe the grain size, strain rate and porosity dependent yield strength of NC materials under high strain rate loading. The NC materials are treated as a composite which consists of grain interior phase and grain boundary phase. Meanwhile, the constitutive relations of grain interior and grain boundary phase are determined in term of their main deformations, and the overall stress—strain relation of NC materials is established on the base of Voigt model. In addition, the established model is extended to describe the yield strength of porous NC materials in conjunction with Budiansky’s self-consistent approach and secant- moduli approach. The predictions on the yield strength of NC materials at high strain rates show good agreements with various experimental data.
References
[1] MEYERS M A, MISHRA A, BENSON D J. Mechanical properties of nanocrystalline materials [J]. Prog Mater Sci, 2006, 51: 427-557.
[2] YOO S H, SUDARSHAN T S, SETHURAM K. Consolidation and high strain rate mechanical behavior of nanocrystalline tantalum powder [J]. Nanostruct Mater, 1999, 12: 23-28.
[3] JIA D, RAMESH K T, MA E. Effects of nanocrystalline and ultrafine grain sizes on constitutive behavior and shear bands in iron [J]. Acta Mater, 2003, 51: 3495-3509.
[4] CAPOLUNGO L, JOCHUM C, CHERKAOUI M, QU J. Homogenization method for strength and inelastic behavior of nanocrystalline materials [J]. Int J Plast, 2005, 21: 67-82.
[5] CONRAD H, NARAYAN J. On the grain size softening in nanocrystalline materials [J]. Scripta Mater, 2000, 42: 1025-1030.
[6] KIM H S, ESTRIN Y. Phase mixture modeling of the strain rate dependent mechanical behavior of nanostructured materials [J]. Acta Mater, 2005, 53: 765-772.
[7] KIM H S, BUSH M B, ESTRIN Y. Constitutive modelling of strength and plasticity of nanocrystalline metallic materials [J]. Mater Sci Eng A, 2001, 316: 195-199.
[8] van SWYGENHOVEN H, SPACZER M, CARO A. Microscopic description of plasticity in computer generated metallic nanophase samples: A comparison between Cu and Ni [J]. Acta Mater, 1999, 47: 3117-3126.
[9] GLEITER H. Nanostructured materials: basic concepts and microstructure [J]. Acta Mater, 2000, 48: 1-29.
[10] JIANG B, WENG G J. A theory of compressive yield strength of nano-grained ceramics [J]. Int J Plast, 2004, 20: 2007-2026.
[11] DONOVAN P E. A yield criterion for Pd40Ni40P20 metallic glass [J]. Acta Metall Mater, 1989, 37: 445-456.
[12] BUDIANSKY B. Thermal and Thermoelastic properties of isotropic composites [J]. J Compos Mater, 1970, 4: 286-295.
[13] KIM H S, BUSH M B. The effects of grain size and porosity on the elastic modulus of nanocrystalline materials [J]. NanoStruct Mater, 1999, 11: 361-367.
[14] WANG N, WANG Z, AUST K T, ERB U. Effect of grain size on mechanical properties of nanocrystalline materials [J]. Acta Metall Mater, 1995, 43: 519-528.
[15] DALLA T F, van SWYGENHOVEN H, VICTORIA M. Nanocrystalline electrodeposited Ni: microstructure and tensile properties [J]. Acta Mater, 2002, 50: 3957-3970.
[16] ZHOU Jian-qiu, ZHU Rong-tao, ZHANG Zheng-zhong. A constitutive model for the mechanical behaviors of bcc and fcc nanocrystalline metals over a wide strain rate range [J]. Mater Sci Eng A, 2008, 480: 419-427.
Foundation item: Project(10502025) supported by the National Natural Science Foundation of China; Project(101005) supported by Fok Ying Tong Education Foundation; Project(BK2007528) supported by the Natural Science Foundation of Jiangsu Province, China
Received date: 2008-06-25; Accepted date: 2008-08-05
Corresponding author: ZHOU Jian-qiu, Professor; Tel: +86-25-83587299; E-mail: zhouj@njut.edu.cn
- Mechanical model for yield strength of nanocrystalline materials underhigh strain rate loading
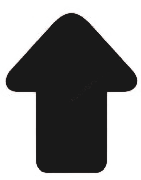