- Abstract:
- 2 Experimental▲
- 3 Results and discussion▲
- 4 Conclusions▲
- References
- Figure
- Fig.1 XRD patterns of LiNixMn2-xO4 sample
- Fig.2 XRD patterns of LiNi0.4Mn1.6O4 prepared at different temperatures
- Fig.3 Metallic element extraction ratios of Li-Mn-Ni composite oxides
- Fig.4 Metallic element extraction ratios of LiNi0.4Mn1.6O4 prepared at different temperatures
- Fig.5 XRD patterns of sample 4-800 before and after acid treatment
- Fig.6 SEM images of sample 4-800: (a) Before acid treatment; (b) After acid treatment
J. Cent. South Univ. Technol. (2011) 18: 314-318
DOI: 10.1007/s11771-011-0697-3
Structure and stability of Li-Mn-Ni composite oxides as lithium ion sieve precursors in acidic medium
MA Li-wen(马立文), CHEN Bai-zhen(陈白珍), SHI Xi-chang(石西昌),
ZHANG Wen(张文), YANG Xi-yun(杨喜云)
School of Metallurgical Science and Engineering, Central South University, Changsha 410083, China
? Central South University Press and Springer-Verlag Berlin Heidelberg 2011
Abstract:
A series of spinel Li-Mn-Ni composite oxides with theoretical chemical formula of LiNixMn2-xO4 (0≤x≤1.0) were synthesized by liquid phase method. Their structure and morphology were characterized by X-ray diffractometry (XRD) and scanning electron microscopy (SEM), respectively. The stability of these Ni-substituted spinel oxides prepared at different temperatures was investigated in acidic medium as well. The results show that Ni can be brought into the spinel framework completely to form well-crystallized product when x≤0.5 and the optimized synthesis temperature is 800 °C. LiNi0.4Mn1.6O4 prepared at 800 °C can maintain the spinel structure and morphology with Li extraction ratio of 30.37%, Mn extraction ratio of 8.78% and Ni extraction ratio of 1.82% during acid treatment. The incorporated Ni not only inhibits the dissolution of Mn, but also reduces the extraction of Li due to the lattice contraction.
Key words:
lithium ion sieve; Li-Mn-Ni composite oxide; structure; stability;
1 Introduction
Lithium and its compounds are widely applied in the battery, ceramic, nuclear and optoelectronic industries. They are not only linked with human life closely, but also have a very high strategic value. The costs of lithium ore are growing higher and higher because the resources are getting depleted. Therefore, the utilization of the liquid lithium resources has become a new interest [1].
Manganese oxide as lithium ion sieve can directly extract lithium from brine or seawater, making it the most promising inorganic lithium ion exchanger. It has many advantages such as simple preparation, high recovery rate, high ion selectivity and environmental friendliness [2]. Lithium ion sieve (spinel manganese oxide) can be transformed from LiMn2O4 after acid treatment. During the acid treatment, the Li+ in LiMn2O4 exchanges with the H+ in the solution [3]. However, the Mn3+ in typical lithium ion sieve precursor LiMn2O4 will disproportionate to Mn4+ and Mn2+ in acidic medium, leaving Mn4+ in the spinel skeleton to form λ-MnO2 and Mn2+ dissolved in acidic solution. This process gradually destroys the spinel structure. So, the key issue to enhance the recycling of the lithium ion sieve is to restrict the dissolution of Mn3+ in LiMn2O4 [4-5].
Using other low valence metal ions such as Mg2+, Al3+, Cu2+ and Fe2+ to replace some manganese ions, in particular Mn3+, can increase the average valence of Mn and inhibit the dissolution of Mn in spinel LiMn2O4. Thus, the stability of the spinel structure is improved and the recycling utilization of the lithium ion sieve is enhanced [6-12]. Although there have been many literatures about Ni-doped LiMn2O4 in the lithium ion battery field as it can often improve the Li+ migration activity [13-14], this material applied to lithium ion sieve has seldom been reported. In this work, a series of spinel Li-Mn-Ni composite oxides (theoretical chemical formula as LiNixMn2-xO4, 0≤x≤1.0) were synthesized by liquid phase route. As the lithium ion sieve precursors, their structure and stability in acidic medium were investigated systematically.
2 Experimental
2.1 Preparation of Li-Mn-Ni composite oxides
Stoichiometric amounts of nickel acetate (Ni(CH3COO)2·4H2O) and manganese acetate (Mn(CH3COO)2·4H2O) were dissolved in distilled water to form a mixed solution. Then, a supersaturated solution of lithium carbonate (Li2CO3) was added dropwise to the above mixed solution with continuous stirring for 1 h at 50 °C. The molar ratio of Ni to Mn varied between 0 and 1, while the molar ratio of Li to (Ni+Mn) was kept at 0.5. The mixtures were then heated to 150 °C until the excess water was removed. The dry mixtures were the precursors of Li-Mn-Ni composite oxides. Then, the precursors were ground and calcined at 750 °C in air for 12 h with a heating rate of 10 °C/min to obtain the final spinel products. The products were referred as sample No.0, 2, 4, 6, and 10 according to the various Ni contents in LiNixMn2-xO4 (x=0, 0.2, 0.4, 0.5, 0.6, 0.8, 1.0). In addition, three samples of a certain ratio of x=0.4 were synthesized at different temperatures of 750, 800 and 850 °C to study the temperature influence. They were numbered as 4-750, 4-800, 4-850, respectively.
2.2 Acid treatment
A constant mass (0.100 g) of sample was immerged in 100 mL HCl solution (0.5 mol/L) at 25° C. The lithium, manganese and nickel concentrations in the supernatant solution were determined after the attainment of equilibrium with an atomic absorption spectrophotometer (TAS-999F, Beijing). The lithium, manganese and nickel extraction ratios of each sample were calculated by the following equation:
(1)
where RM is the extraction ratio of the element M (M=Li, Mn, Ni), mM is the mass of M in the solution, is the mass of M in the original sample.
2.3 Characterization
The Li, Ni and Mn contents for samples were detected by atomic absorption spectrophotometry after dissolving each sample in boiling HCl solution (6 mol/L). The powder XRD patterns of the Li-Mn-Ni composite oxides were obtained on a Rigaku X-ray diffractometer (D/max 2550) equipped with a Cu anticathode (Cu Kα radiation, λ=1.540 56 ?) at room temperature. The measurements were recorded under Bragg-Brentano geometry at 2θ with a speed of 10 (°)/min in the range of 10°-80°. The structure and particle morphology of the acid-treated sample No.4 as a representative of the Li-Mn-Ni composite oxides were examined by XRD and scanning electron microscopy (SEM, Sirion200), respectively.
3 Results and discussion
3.1 Chemical and structural analysis of Li-Mn-Ni composite oxides
Samples were dissolved in boiling HCl solution (6 mol/L) to detect their Li, Ni and Mn contents by atomic absorption spectrophotometry. The experimental and theoretical data of Li, Ni and Mn contents are listed in Table 1. As can be seen from Table 1, the experimental values of Li, Ni and Mn contents are close to their corresponding theoretical values. This means that although lots of chemical reactions occur during the synthesis process, the chemical constitutions of the Li-Mn-Ni composite oxides accord with their theoretical chemical formulas. The experimental Li, Ni and Mn contents are chosen as the basis for the calculation of the metallic element extraction ratios.
The chemical analysis only gives the information about the chemical constitution of the compounds, while the XRD analysis can reveal the phase composition of compounds. Fig.1 shows the XRD patterns of samples. They all show spinel type crystals indexed in the cubic Fd3m space group whose characteristic peaks are marked in Fig.1. However, it is different from the results of chemical analysis that not every sample has the same phase composition as its theoretical chemical formula of LiNixMn2-xO4. It is seen from Fig.1 that spinel is the only phase of the Li-Mn-Ni composite oxides in a certain range of Ni content (x≤0.5), which means that Ni can be fully incorporated into the lattice. When x≥0.6, impurity Ni6MnO8 is formed and the content of the impurity increases with increasing the x value. For x=1.0, a great amount of impurity Ni6MnO8 is found. The emergence of impurity Ni6MnO8 indicates that Ni will not be completely integrated into the spinel lattice and will form a separate phase when Ni is excessively added.
Detailed analysis for XRD data can demonstrate further information about the structure of these Li-Mn-Ni composite oxides. Table 2 lists the 2θ and d values of the main diffraction peak for (111) plane of the spinel. As it is seen from Table 2, XRD diffraction peaks of all samples move slightly to higher angle direction with crystal face distance d decreasing compared with the pure LiMn2O4. When x≤0.5 the d value of the samples decreases continuously with increasing the x value, which indicates a cell contraction attributed to the incorporation of Ni2+. The incorporated Ni2+ induces the cell contraction through two functions. On one hand, the Ni—O bond is stronger than the Mn—O bond, and Ni replacing Mn will decrease the average atomic distance [15]. On the other hand, Ni2+ substituting partial Mn3+ can increase the content of Mn4+ to keep the charge balance, and Mn4+ has smaller ionic radius than Mn3+ [16]. When x≥0.5, the real Ni content in spinel is not the same as the theoretical one due to the formation of large amount of Ni6MnO8. So, the 2θ and d values are not regularly changed with x.
Table 1 Experimental and theoretical data of Li, Ni and Mn contents of samples (Mass fraction)
Fig.1 XRD patterns of LiNixMn2-xO4 sample
Table 2 2θ and d values of diffraction peak for (111) plane of samples
3.2 Structural analysis of LiNi0.4Mn1.6O4 calcined at different temperatures
The samples with chemical formula of LiNi0.4Mn1.6O4 were calcined at 750, 800 and 850 °C for 12 h, respectively. They were named as 4-750, 4-800, 4-850. Fig.2 shows their XRD patterns. They are all pure spinel phases, indicating that the change of temperature within a certain range does not cause impurities generation when Ni can be fully integrated into the spinel structure. Ni content seems to have a dominating effect on the phase composition, but the temperature has more effects on the crystallinity. Table 3 shows the 2θ and d values of diffraction peak for (111) plane for samples 4-750, 4-800 and 4-850. From Table 3, it can be seen that 2θ increases, and d together with the full width at half maximum (FWHM) decreases with increasing the calcination temperature. Because the crystallinity of crystals can be qualitatively characterized by the value of FWHM (a smaller FWHM means a higher crystallinity degree [17]), increasing the temperature results in a more complete lattice and a higher degree of crystallinity for Li-Mn-Ni composite oxide. As samples 4-800 and 4-850 have similar structural parameters, 800 °C can be considered as the optimized temperature.
Fig.2 XRD patterns of LiNi0.4Mn1.6O4 prepared at different temperatures
Table 3 Value of 2θ, d and FWHM of (111) plane for 4-750, 4-800 and 4-850 samples
3.3 Stability of Li-Mn-Ni composite oxides in acidic medium
Fig.3 shows the equilibrium extraction ratio of metallic element for samples. All Ni-substituted samples show lower Mn as well as lower Li extraction ratios than those of Ni-free sample. This means that the substituent Ni can not only inhibit the dissolution of Mn but also reduce the extraction of Li due to the cell contraction. When x≤0.5, Mn and Li extraction ratios are reduced with increasing the x value. When x >0.5, larger metallic extraction ratios than the expected ones are observed because the “real” Ni content in the samples (No.6, 8 and 10) is smaller than the theoretical one due to the formation of Ni6MnO8 impurity phase. The behavior of dissolution of Ni is similar to that of Li and Mn.
Fig.3 Metallic element extraction ratios of Li-Mn-Ni composite oxides
Fig.4 demonstrates the equilibrium extraction ratio of metallic element for 4-750, 4-800 and 4-850 samples. As the temperature increases, the Mn dissolution of the samples is close to each other, which indicates that the incorporated Ni can improve the average valence of Mn and can suppress its dissolution. Li extraction ratios of samples 4-800 and 4-850 are higher and their Ni extraction ratios are lower than those of 4-750. This may indicate that elevated temperature can promote crystal crystallinity and make the internal atomic arrangement more regular. The higher Ni extraction ratio and lower Li extraction ratio of 4-750 may be ascribed to relatively low crystallinity and parts of Ni entering into the more easily dissoluble position of 8a while parts of Li entering into the indissoluble position of 16d or 16c. The similar Li, Mn and Ni extraction ratios of sample 4-800 and 4-850 reveal that LiNi0.4Mn1.6O4 prepared above 800 °C has similar structures and dissolution behavior in acidic medium. Thus, the optimized temperature is 800 °C, which accords with the structural analysis. The Li, Mn and Ni extraction ratios of samples 4-800 are 30.37%, 8.78% and 1.82%, respectively.
Fig.4 Metallic element extraction ratios of LiNi0.4Mn1.6O4 prepared at different temperatures
3.4 Structure and morphology for sample 4-800 before and after acid treatment
The XRD patterns of the sample 4-800 before and after acid treatment are presented in Fig.5. The diffraction patterns before acid treatment completely correspond to the characteristic patterns of spinel lithium manganese oxide, while the XRD patterns are almost unchanged after acid treatment, only with the peaks shifting to higher angle direction. This indicates that during acid treatment the spinel structure of LiNi0.4Mn1.6O4 can be maintained but its lattice shrinks as a result of the Li-H ion exchange reaction. There are three mechanisms of the dilithiation process for LiMn2O4 during acid treatment, namely the redox, the ion-exchange and the redox and ion-exchange combined mechanism. If the average valence of Mn is close to +4, the ion-exchange between Li+ and H+ should be the main mechanism [5]. The average valence of Mn in LiNi0.4Mn1.6O4 is about 3.875, so its main mechanism is ion-exchange. After H+ exchanges with Li+ into the spinel lattice, the XRD patterns will consequentially shift to higher angle direction with a cell contraction because of the smaller radius of H+. Meanwhile, the intensity of the diffraction patterns for LiNi0.4Mn1.6O4 after acid treatment becomes lower. This may be explained by the crystal defects and small crystalline grains produced during acid treatment.
Fig.5 XRD patterns of sample 4-800 before and after acid treatment
Fig.6(a) and Fig.6(b) show the morphologies of sample 4-800 before and after acid treatment, respectively. Composite oxide 4-800 has even and fine particles with a slight aggregation before acid treatment. After acid treatment, the particles of the sample become larger with good dispersion. The particles usually consist of amounts of crystalline grains. Although the crystalline grains become smaller during acid treatment demonstrated by XRD analysis, it is possible for the particles to grow at the same time. As the delithiation process of sample 4-800 during acid treatment is mainly composed of the Li-H ion exchange reaction and mass transfer, the small particles grow up because of the ion mobilization through the grain boundary. This might imply a good stability of the skeleton for LiNi0.4Mn1.6O4, otherwise the particles will be refined due to the element dissolution and spinel skeleton destruction.
Fig.6 SEM images of sample 4-800: (a) Before acid treatment; (b) After acid treatment
4 Conclusions
1) Li-Mn-Ni composite oxides with theoretical chemical formula of LiNixMn2-xO4 (0≤x≤1) were prepared. XRD analysis demonstrates that Ni is completely incorporated into the spinel lattice with a lattice contraction when x≤0.5. Impurity Ni6MnO8 begins to form when x≥0.5.
2) The elevated temperature can promote the crystal crystallinity and make the internal atomic arrangement more regular. The optimized synthesis temperature for LiNi0.4Mn1.6O4 is 800 °C.
3) LiNi0.4Mn1.6O4 prepared at 800 °C can maintain the spinel structure and morphology with Li extraction ratio of 30.37%, Mn extraction ratio of 8.78% and Ni extraction ratio of 1.82% during acid treatment.
4) The incorporated Ni not only inhibits the dissolution of Mn, but also reduces the extraction of Li due to the lattice contraction.
References
[1] CHEN Ting, YAN Shu-yi, KANG Zi-hua. Progress on the extraction of lithium from the salt lake brine in China [J]. Salt and Chemical Industry, 2006, 36(2): 19-21. (in Chinese)
[2] CHEN Bai-zhen, MA Li-wen, SHI Xi-chang, XU Hui, YANG Xi-yun. Research progress on preparation methods for precursors of lithium ion sieve [J]. Inorganic Chemicals Industry, 2009, 41(7): 1-4. (in Chinese)
[3] HUNTER J C. Preparation of a new crystal form of manganese dioxide: λ-MnO2 [J]. Journal of Solid State Chemistry, 1981, 39: 142-147.
[4] OOI K, MIYAI Y, SAKAKIHARA, Mechanism of Li+ insertion in spinel-type manganese oxide: Redox and ion-exchange reactions [J]. Langmuir, 1991, 7: 1167-1171.
[5] FENG Q, MIYAI Y, KANOH H, OOI K. Li+ extraction/insertion with spinel-type lithium manganese oxides: Characterization of redox-type and ion-exchange-type sites [J]. Langmuir, 1992, 8: 1861-1867.
[6] FENG Q, MIYAI Y, KANOH H, OOI K. Li+ and Mg2+ extraction and Li+ insertion reactions with LiMg0.5Mn1.5O4 spinel in the aqueous phase [J]. Chem Mater, 1993, 5: 311-316.
[7] LIU Yi-fan, FENG Qi, OOI K. The synthesis and ion-exchange property of Li+ memorized spinel LiAlMnO4 [J]. Ion Exchange and Adsorption, 1995, 11(3): 216-222.
[8] DONG Dian-quan, ZHONG Jie, LIU Dun-lei, LIU Yi-fan. Synthesis of LiCu0.5Mn1.5O4 and its Li+ extraction/insertion reaction in aqueous solution [J]. Chinese Journal of Applied Chemistry, 1998(3): 114-115. (in Chinese)
[9] DONG Dian-quan, ZHANG Feng-bao, ZHANG Guo-lian, LIU Yi-fan. LiMg0.5Mn1.5O4 synthesis and its selectivity to Li+ exchange [J]. Chinese Journal of Inorg Chem, 2004, 20(9): 1126-1130. (in Chinese)
[10] LIU Y F, FENG Q, OOI K. Li+ extraction/insertion reactions with LiAlMnO4 and LiFeMnO4 spinels in the aqueous phase [J]. J Colloid Interface Sci, 1994, 163(1): 130-136.
[11] CHITRAKAR R, KANOH H, MAKITA Y, MIYAI Y, OOI K. Synthesis of spinel-type lithium antimony manganese oxides and their Li+ extraction/insertion reactions [J]. J Mater Chem, 2000, 10: 2325-2329.
[12] TIAN Li-yan, MA Wei, HAN Mei. Adsorption behavior of Li+ onto nano-lithium ion sieve from hybrid magnesium/lithium manganese oxide [J]. Chemical Engineering Journal, 2010, 156: 134-140.
[13] GUO Hua-jun, LI Xin-hai, ZHANG Xin-ming, ZENG Su-ming, WANG Zhi-xin, PENG Wen-jie. Characteristics of LiCoO2, LiMn2O4 and LiNi0.45Co0.1Mn0.45O2 as cathodes of lithium ion batteries [J]. J Cent South Univ Technol, 2005, 12(s1): 44-49.
[14] WANG Zhi-xing, FANG Hai-sheng, YIN Zhou-lan, LI Xin-hai, GUO Hua-jun, PENG Wen-jie. Synthesis and characterization of high-voltage cathode material LiNi0.5Mn1.5O4 by one-step solid-state reaction [J]. J Cent South Univ Technol, 2005, 12(s1): 54-58.
[15] YANG S H, RICHARD L M. Redox reactions of cobalt, aluminum and titanium substituted lithium manganese spinel compounds in lithium cells [J]. Solid State Ionics, 2001, 139: 13-25.
[16] RAJA M W, MAHANTY S, BASU R N. Influence of S and Ni co-doping on structure, band gap and electrochemical properties of lithium manganese oxide synthesized by soft chemical method [J]. Journal of Power Sources, 2009, 192: 618-626.
[17] LIAO Li-bin, LI Guo-wu. X-ray diffraction methods and their application [M]. Beijing: Geology Press, 2008: 113-114. (in Chinese)
(Edited by YANG Bing)
Foundation item: Project(2008BAB35B04) supported by the National Key Technology R&D Program of China; Project(CX2010B111) supported by the Innovation Program of Doctoral Research of Hunan Province, China; Project(2010QZZD003) supported by Advanced Research Program of Central South University, China
Received date: 2010-03-05; Accepted date: 2010-06-10
Corresponding author: SHI Xi-chang, Associate Professor, PhD; Tel: +86-731-88877352; E-mail: xichang.shi@gmail.com
- Structure and stability of Li-Mn-Ni composite oxides aslithium ion sieve precursors in acidic medium
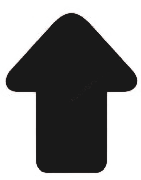