Trans. Nonferrous Met. Soc. China 31(2021) 3564-3578
Enhanced sulfidization flotation of cuprite by surface modification with hydrogen peroxide
Guang HAN, Shu-ming WEN, Han WANG, Qi-cheng FENG
State Key Laboratory of Complex Nonferrous Metal Resources Clean Utilization, Faculty of Land Resource Engineering, Kunming University of Science and Technology, Kunming 650093, China
Received 21July 2021; accepted 27October 2021
Abstract:
ydrogen peroxide was used as an oxidant to modify the cuprite surface and enhance its sulfidization. Surface-adsorption and infrared spectroscopy measurements indicated that the modification of the cuprite surface with hydrogen peroxide before sulfidization increased the adsorption capacity of xanthate. Zeta potential, scanning electron microscopy-energy dispersive X-ray spectroscopy, X-ray photoelectron spectroscopy, and time-of-flight secondary ion mass spectrometry results showed that the modification with hydrogen peroxide increased the contents of S2- and Sn2- species on the cuprite surface. Microflotation tests showed that the recovery of cuprite increased from 61.74% to 83.30% after the modification of the surface with hydrogen peroxide. These results confirm that the modification of the cuprite surface with hydrogen peroxide enhances the sulfidization of cuprite, which in turn improves its flotation.
Key words:
cuprite; flotation; hydrogen peroxide; surface modification; sulfidization;
1 Introduction
Among more than 280 kinds of copper-bearing minerals that have been discovered in the world, the copper minerals with industrial value are chalcopyrite, chalcocite, malachite, cuprite, and azurite [1-5]. Copper sulfide ore resources have diminished in recent years, which attracted much attention. Sulfidization flotation is widely used in mineral processing to recover copper oxide ore resources [6,7]. Among the sulfidization flotation methods, surface sulfidization is the most commonly used, economical, and mature process for the treatment of common copper oxide ore resources. Sulfidization flotation is performed by treating copper oxide minerals with a sulfurizing reagent, which is usually sodium sulfide, for pre-sulfidization. This generates a metal sulfide film with improved hydrophobicity on the mineral surface. The sulfide ore is then collected by flotation [8,9].
Many factors affect the sulfidization behavior of oxide minerals, and in turn the flotation. These factors include the pulp temperature, pulp pH, dose and addition method of the sulfurizing reagent, and mineral characteristics, and there may be interactions among these factors [10-12]. An increase in the temperature can improve the reaction rate and degree of sulfidization. Hydrothermal sulfidization uses a high temperature and high pressure to obtain a higher rate of sulfidization and convert all the oxide ores into sulfide [13]. However, industrial applications of hydrothermal sulfidization are limited because of its high setup costs and energy consumption.
The pulp pH can affect the forms of the flotation reagents and mineral surface properties in the pulp. Because of the hydrolytic equilibrium of sodium sulfide in aqueous solution, the form of sodium sulfide in the pulp is controlled by the pH.The dominant components at pH<7, 713.9 are H2S, HS-, and S2-, respectively. Previous research has shown that oxide minerals have better flotation indexes in weakly alkaline pulp than at other pH values, and the dominant sodium sulfide component in this pH range is HS- [14]. The sodium sulfide dose is the most important factor affecting the sulfidization flotation of oxide minerals, with both insufficient and excessive doses not conducive to flotation [15]. With insufficient sodium sulfide, the area of sulfide products on oxide mineral surfaces is not enough to activate flotation of the minerals. With an excess of sodium sulfide, flotation of the minerals is depressed. Although the surface sulfidization has some deficiencies, such as the required dose of sulfurizing reagent, low sulfidization efficiency, high collector dose, and low metal recovery, it is still the most economical and promising process for the flotation of oxide minerals because of its low setup costs and energy consumption. To improve the sulfidization flotation of oxide minerals, surface enhancement has been applied. Previous studies have shown that the addition of a certain amount of activation reagent (e.g., ammonium sulfate or ethylenediamine) can enhance the sulfidization of copper oxide minerals. This decreases the required dose of sulfurizing reagent and greatly enhances the hydrophobicity of the minerals to improve the flotation recovery [16,17].
Cuprite is an important copper oxide mineral for copper extraction. Because of a lack of oxygen in the mineralization process, copper is not oxidized sufficiently and forms cuprous minerals. The surface of cuprite is strongly hydrophilic, therefore, flotation with direct sulfidization is not ideal [18]. In previous work, the flotation recovery of cuprite for a mixed oxide–sulfide copper ore containing cuprite was significantly increased by modification with an oxidant [19]. However, the affecting mechanism of modification by the oxidant on the surface properties and sulfidization of cuprite is not clear. In this work, hydrogen peroxide (H2O2) was used as an oxidant to modify the cuprite surface and improve its subsequent sulfidization. The modified and sulfidized cuprite surfaces were characterized and the influence of H2O2 on sulfidization of the cuprite surface and xanthate adsorption was evaluated. The aim of this work was to investigate the use of H2O2 as an oxidant to modify the cuprite surface and enhance sulfidization. The results of this study will be beneficial to copper oxide sulfidization flotation.
2 Experimental
2.1 Materials
Cuprite samples were collected in Yunnan Province, China. The cuprite blocks were crushed and purified by hand separation. The cuprite surface was then rinsed repeatedly with deionized water. After removing the surface water, an agate grinding machine was used for preliminary grinding of the cuprite samples. A standard sieve was used to screen the cuprite samples to meet the sample size requirements for different tests. The cuprite samples were stored in sealed glass bottles. To determine the purity of the cuprite samples, X-ray diffraction and chemical analyses were performed. The results are shown in Fig. 1 and Table 1. The diffraction peaks of the cuprite sample were consistent with the standard diffraction peaks, and no obvious impurity peaks were observed. The impurity contents of the cuprite samples were very low (Table 1). According to the Cu content (84.43 wt.%), the sample purity was about 95%. The X-ray diffraction and chemical analyses results showed that the cuprite sample purity met the requirements for single mineral tests.
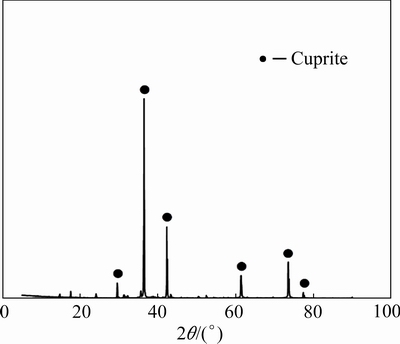
Fig. 1 X-ray diffraction pattern of cuprite sample
Table 1 Mainchemical composition of cuprite sample (wt.%)

2.2 Reagents
H2O2 (Chongqing Maoye Chemical Co., Ltd., China) was used as an oxidant for cuprite. Na2S·9H2O (Sinopharm Chemical Reagent Co., Ltd., China) was used for sulfidization. Sodium butyl xanthate (NaBX; Zhuzhou Flotation Reagents Co., Ltd., China) was used as a collector. HCl and NaOH were used as pH regulators. All reagents were of analytical grade, except for NaBX, which was of industrial grade.
2.3 SEM-EDS measurements
The surface morphologies and energy spectra of cuprite samples were measured using a scanning electron microscope (FEI Quanta 200, FEI Company, USA) and an energy dispersive spectrometer (Genesis 2000, EDAX Company, USA). The particle size of the cuprite was between 45 and 74 μm, and the sample mass for each test was 0.5 g. The modification with H2O2 was performed at a natural pH, and the pulp pH was adjusted to 9.5 during the sulfidization process. Each cuprite sample was placed in a beaker and a H2O2 solution was added with stirring for 5?min. Then, the prepared Na2S solution was added with stirring for 30 min. A solution of HCl or NaOH was also added to adjust the pH during the sulfidization process. Finally, the samples were dried and used for SEM-EDS measurements.
2.4 Zeta potential tests
Zeta potential tests were performed using a zeta analyzer (Zetasizer-3000HS, Malvern Panalytical, United Kingdom). Cuprite samples with a particle size less than 2 μm were used in the tests. A planetary ball mill (RETSCH-MM400, Verder Shanghai Instruments and Equipment Ltd.) was used to obtain particles with sizes less than 2 μm. The particle size was determined using a granulometer (BT-9300S, Bettersize Instruments Ltd., China). Each sample was weighed to 0.05 g and transferred to a 100-mL beaker. A certain volume of KCl solution was added and the pulp was stirred. The same reagents used for the SEM-EDS measurements were added successively, with each reagent allowed to react for a certain time.
2.5 XPS measurements
The X-ray photoelectron spectroscopy (XPS) measurements were carried out with a PHI 5000 VersaProbe II instrument (PHI 5000, ULVAC-PHI, Japan) using an Al Kα X-ray source under ultrahigh vacuum. The operating conditions were as follows: pass energy of 46.95 eV, step size of 0.2 eV, power of 50 W, and voltage of 15 kV. The cuprite samples (particle size <38 mm, sample mass of 0.5 g) were weighed and the same reagents used for the SEM-EDS measurements (Section 2.3) were added successively.
2.6 Surface adsorption tests
Surface adsorption tests were conducted using an ultraviolet-visible spectrophotometer (UV-2700, Shimadzu, Japan). Cuprite samples (particle size <38 μm) were weighed (0.5 g) and treated with the same reagents as for the SEM-EDS measurements.
2.7 Infrared spectroscopy measurements
Infrared (IR) spectroscopy was performed using a Fourier-transform IR spectrometer (Nicolet iS50, Thermo Fisher Scientific, USA). The wave- number range was 400-4000?cm-1. The cuprite sample (particle size <38 mm) was weighed (0.5 g) and treated with the same reagents as for the SEM-EDS measurements.
2.8 Time-of-flight secondary ion mass spectro- metry measurements
The chemical properties of the cuprite surface were characterized using time-of-flight secondary ion mass spectrometry (ToF-SIMS; ION-TOF IV, IONTOF, Munster, Germany). High-purity cuprite was manually selected for cutting. Before analysis, the cuprite sample was cleaned in ethanol using ultrasonication. The sample was then placed in a beaker and treated with the same reagents as for the SEM-EDS measurements.
2.9 Microflotation tests
Flotation tests of cuprite were carried out using a Hallimond tube, the effective volume was 50?mL, and N2 was used as the gas source (20?mL/min). Cuprite samples (0.5 g) with a particle size between 45 and 74 mm were used as the flotation feed. Each cuprite sample was treated with reagents before flotation. A solution of H2O2 was added to the pulp and stirred for 5?min. Then, the prepared Na2S solution was added and stirred for 3 min, and a solution of HCl or NaOH was added to adjust the pH for the sulfidization process. The collector (NaBX) was added with stirring for 3 min. Finally, the Hallimond tube was used to float the mixture for 3 min. The tailings and concentrate were collected, dried, and weighed to calculate the flotation recovery. Each group of flotation tests was performed three times, and the final results were averaged.
3 Results and discussion
3.1 Effect of H2O2 on surface properties of cuprite
3.1.1 Surface morphology and zeta potential
SEM can be used to observe the morphologies of localized mineral surfaces to determine changes in the morphology before and after treatment with different reagents [20,21]. We investigated the surface morphology and zeta potential of blank cuprite and H2O2-treated cuprite to study the influence of H2O2 on the surface properties of cuprite. Secondary electron images of cuprite surfaces with and without H2O2 treatment are shown in Fig. 2. The surface of the cuprite without H2O2 treatment was smooth (Fig. 2(a)). After treatment with H2O2, the cuprite surface became rough and multiple cracks appeared (Fig. 2(b)). This increased the specific surface area of the cuprite particles, which would facilitate subsequent adsorption of sulfur ions. The zeta potential of cuprite was measured in the absence and presence of 5×10-4mol/L H2O2 at different pH values (Fig. 3). In the investigated pH range (6.5-11.5), the zeta potential of H2O2-treated cuprite was obviously lower than that of blank cuprite (Fig. 3). This indicated that the treatment of cuprite with H2O2 modified its surface characteristics, which changed the surface potential.
3.1.2 XPS spectra
The elements on the surface of a sample and their chemical environments can be determined by XPS using the binding energies of different elements. Semi-quantitative results for the content of each element can be obtained using the area of the spectral line [22-26]. We conducted XPS measurements for cuprite with and without modification to confirm the influence of H2O2 on the cuprite surface properties. In the O 1s spectra ofcuprite with and without modification (Fig. 4), a peak at approximately 530.11 eV was assigned to O(II) species from cuprite, and a higher intensity peak at approximately 531.62 eV was assigned to O(II) species from compounds containing hydroxyl groups on the cuprite surface [27,28]. After treatment with H2O2, the binding energies and distribution of the O(II) species from compounds containing hydroxyl groups and cuprite did not change significantly. This indicated that the chemical state of the O(II) species on cuprite wasrelatively stable regardless of the addition of H2O2.
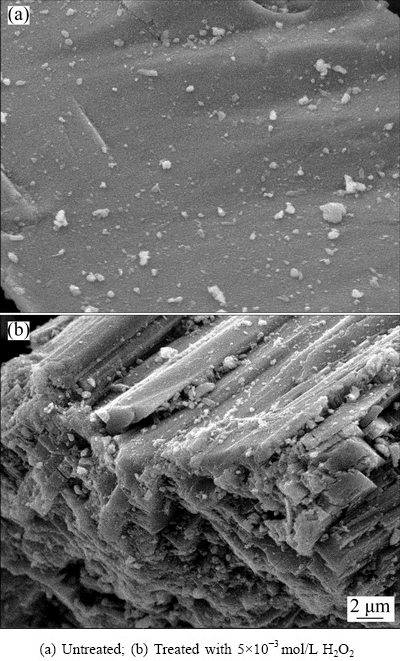
Fig. 2 Secondary electron images of cuprite surfacesat pH 9.5
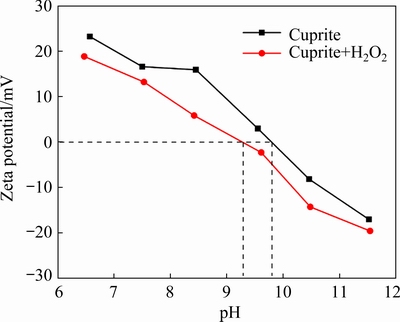
Fig. 3 Zeta potential of cuprite as function of pH in the absence and presence of 5×10-4mol/LH2O2
In the Cu 2p spectra of cuprite with and without modification (Fig. 5), a peak at approximately 934.57 eV was assigned to Cu(II) species on the cuprite surface, and a peak at approximately 932.98 eV was assigned to Cu(I) species [29]. There were no large shifts in the binding energies for copper species on cuprite after treatment with H2O2. However, the proportion of Cu(II) species on the cuprite surface increased significantly, and this change may enhance the adsorption of sulfur ions on cuprite. Figure 6 shows the molar fractions of Cu(I) and Cu(II)specieson the cuprite surfaces with and without modification. After treatment with H2O2, the molar fraction of Cu(I) species decreased from 11.67% to 7.46%, and that of Cu(II) species increased from 10.32% to 12.43%. These results indicated that more Cu(II) species were generated on cuprite, which could interact with sulfur ions and be reduced to Cu(I). Table 2 shows the proportions of Cu(I) and Cu(II) species among the total copper species on the cuprite surfaces with and without modification. The proportion of Cu(II) species among the total copper species increased from 46.92% to 62.51% and the proportion of Cu(I) species decreased from 53.08% to 37.49%. This indicated that some of the Cu(I) species on the cuprite surface were oxidized to Cu(II) species after addition of H2O2. Compared with Cu(I) species, the newly generated Cu(II) species had a superior ability to interact with sulfur ions in the pulp through oxidation–reduction reactions. This implied that the modification of the cuprite surface strengthened the sulfidization process of cuprite. Therefore, we inferred that modification using H2O2 before sulfidization could transform Cu(I) species on cuprite surfaces to Cu(II) species, which would enhance the adsorption of sulfur ions.
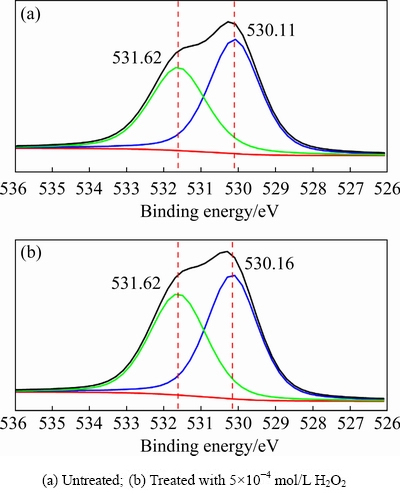
Fig. 4 O 1s XPS spectra of cuprite surfaces
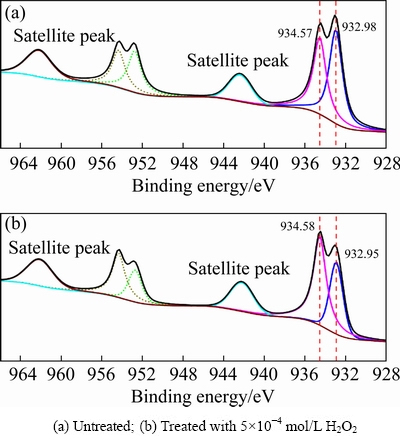
Fig. 5 Cu 2p XPS spectra of cuprite surfaces
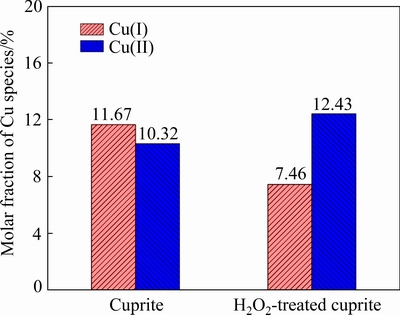
Fig. 6 Molar fractions of copper species on blank cuprite surface and H2O2-treated cuprite surface
Table 2 Quantification of Cu 2p species on cuprite surfacesuntreated and treated with 5×10-4mol/L H2O2
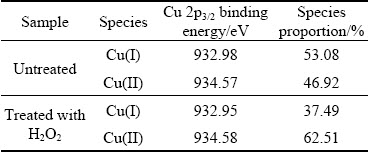
3.2 Effect of modification on sulfidization of cuprite and xanthate adsorption
3.2.1 Surface-adsorption behavior
Xanthate (NaBX) can be ionized in aqueous solution to produce anions containing sulfur atoms, which can interact with the mineral surface. This interaction forms a metal xanthate that is firmly connected to the interior of the crystal lattice. In this way, xanthate is fixed on the mineral surface, so it can play a role in collection. The amount of xanthate adsorbed on cuprite surfaces is critical in determining the hydrophobicity of cuprite. Therefore, to study the impact of modification on the adsorption of NaBX, we investigated the quantity of NaBX adsorbed on cuprite surfaces with changes in the H2O2 and NaBX concentrations. The Na2S concentration was set to be 1×10-3mol/L and the pH to be 9.5 (Fig. 7). The consumption of NaBXwas significantly higher with H2O2 modification than without modification (Fig. 7(a)). This result indicated that modification with H2O2 beforesulfidization could enhance the adsorption capacity of cuprite surfaces for NaBX. Higher consumption of NaBX on modified cuprite compared with unmodified cuprite was observed for all the investigated NaBX concentrations (Fig. 7(b)). This result also indicated that with the same collector dose, modification using H2O2 could increase the amount of collector adsorbed on the cuprite surface. This could reduce the collector dose required for use in industrial production. A decrease in collector consumption could enhance the selectivity of the collector during the flotation process and improve the flotation pulp environment. The surface-adsorption results indicated that modification with H2O2 before sulfidization increased the amount of NaBX adsorbed on the cuprite surface. This would improve the hydrophobicity of the cuprite surface and enhance the floatability.
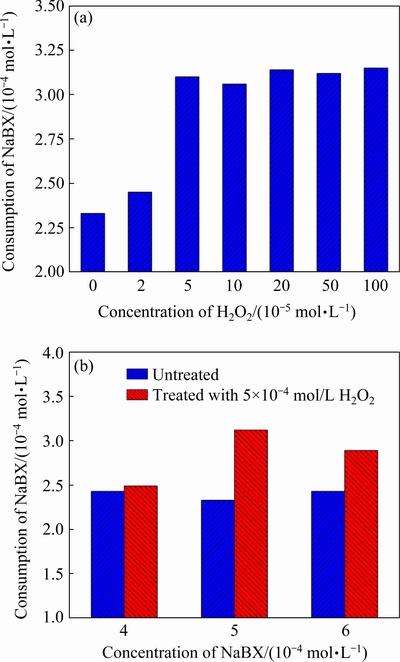
Fig. 7 Quantity of NaBX adsorbed on cuprite surface as function of H2O2 concentration (a) and NaBX concentration(b)at 1×10-3mol/L Na2S and pH 9.5
3.2.2 IR spectra
IR spectroscopy was used to investigate the effect of modification on the adsorption of NaBX on sulfide-treated cuprite by analyzing specific peaks for the mineral and reagents in the spectra [30,31]. The peaks observed for cuprite and NaBX (Fig. 8) were consistent with those in Refs. [32,33]. In the IR spectrum of NaBX, peaks at 1190 and 1167 cm-1 were assigned to the C—O—C asymmetric stretching vibration. Peaks at 1108 and 1063 cm-1 were attributed to the C—O—C symmetric stretching vibration and C=S stretching vibration, respectively. After treatment with NaBX, a new peak appeared at 1202 cm-1 in the IR spectrum of the directly sulfidized cuprite surface. This could be attributed to a shift in the C—O—C asymmetric stretching vibration for NaBX from 1190 to 1202 cm-1 after its interaction with cuprite surfaces. For the cuprite treated with H2O2, Na2S, and NaBX, the C—O—C asymmetric stretching vibration peak at 1201 cm-1 in the IR spectrum increased in intensity. This result showed that NaBX could interact with cuprite surface more strongly after it was modified. These results were consistent with the results of the surface-adsorption measurements. Therefore, the hydrophobicity of the cuprite surface could be enhanced by modification with H2O2 before sulfidization of cuprite, and this change would considerably improve the cuprite flotation.
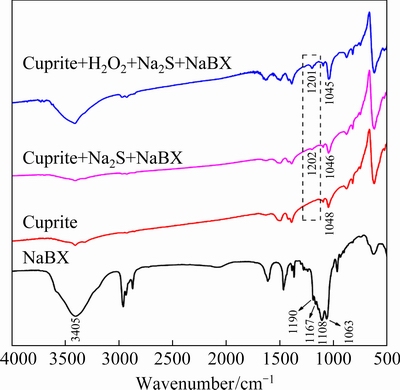
Fig. 8 IR spectra of NaBX, cuprite, cuprite treated with Na2S and NaBX, and cuprite treated with H2O2, Na2S, and NaBXat pH 9.5
3.2.3 Zeta potential
Sulfur ions in the pulp can shield the charge on the cuprite surface by interacting with copper sites, which will change the electrical properties of the cuprite surface. Our earlier results suggested that modification with H2O2 could improve the floatability of cuprite by enhancing the adsorption of Na2S on cuprite surfaces. Next, we studied the effect of modification on the sulfidization of cuprite by measuring the zeta potentials of cuprite surfaces. The zeta potentials of cuprite surfaces were measured in the absence and presence of H2O2 at different pH values. The NaBX concentration was set to be5×10-4mol/L (Fig. 9). In the investigated pH range (6.5-11.5), the zeta potential of the oxidant- and sulfide-treated cuprite was obviously lower than that of sulfide-treated cuprite (Fig. 9). This result indicated that modification increased the adsorption of sulfur ions on the cuprite surface. Therefore, H2O2 and Na2S in cuprite flotation had a positive synergistic effect on the adsorption of sulfur ionson cuprite, which could improve its hydrophobicity. The zeta potential results proved that modification using H2O2 before sulfidization could enhance the adsorption of sulfur ions on cuprite. This would provide favorable conditions for the subsequent interaction of NaBX with the cuprite surface.
3.2.4 SEM-EDS images
SEM-EDS can be used for the qualitative and semi-quantitative analysis of localized cupritesurfaces [34,35]. We performed SEM-EDS analysis to support the zeta potential results and investigate the effect of modification on the sulfidization of cuprite. Secondary electron images and EDS results were obtained for the sulfide-treated cuprite surfaces with and without modification (Fig. 10). Copper sulfide particles appeared in some areas on the cuprite surface (Fig. 10(a)). These particles were produced by sulfur ions interacting with copper sites on cuprite surface. Compared with the sulfide-treated cuprite surfaces without modification, there were more copper sulfide particles on the oxidant- and sulfide-treated cuprite surfaces (Fig. 10(b)). The molar fractions of sulfur in these areas increased from 8.69% to 21.10% compared with the non-modified cuprite. This increase indicated that the cuprite surface treated with H2O2 could interact better with sulfur ions than the untreated surface. This meant that more sulfide species could be generated on the cuprite surface. The SEM-EDS further proved that modification with H2O2 could enhance the sulfidizationof cuprite, which would promote subsequent xanthate adsorption on the mineral surface.
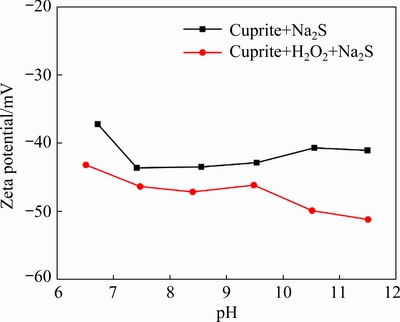
Fig. 9 Zeta potential of sulfide-treated cuprite as function of pH in the absence and presence of H2O2at 1×10-3 mol/L Na2S
3.2.5 ToF-SIMS images
ToF-SIMS images of selected ions for the sulfide-treated cuprite surfaces without and with modification are shown in Figs. 11 and 12, respectively. The normalized intensities of the secondary ions on the sulfide-treated cuprite surfaces with and without modification are shown in Fig. 13. The ions selectively detected in the secondary ion images of the sulfide-treated cupritesurface and sulfide-treated cuprite surface with modification were CuS+ (m/z=94.895), S- (m/z=31.973), S2- (m/z=63.945), and S3- (m/z=95.921). The normalized intensities of CuS+, S-, S2-, and S3- were greatly enhanced on sulfide-treated cuprite surface with modification compared with that without modification. This indicated that the modification using H2O2 could strengthen the adsorption of Na2S on cuprite. In addition, the ToF-SIMS results confirmed that the normalized intensities of the copper sulfide species and polysulfide species on cuprite increased after treatment with H2O2, which improved the hydrophobicity of the cuprite surface. These results supported the zeta potential and SEM-EDS results.
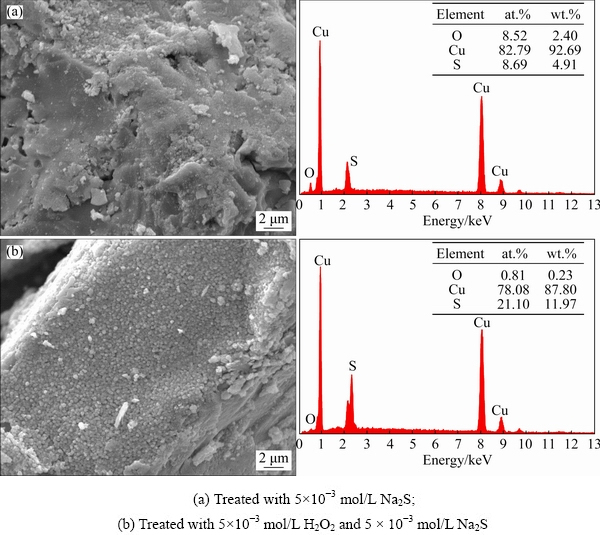
Fig. 10 Secondary electron images and EDS results for cuprite surfaces at pH 9.5
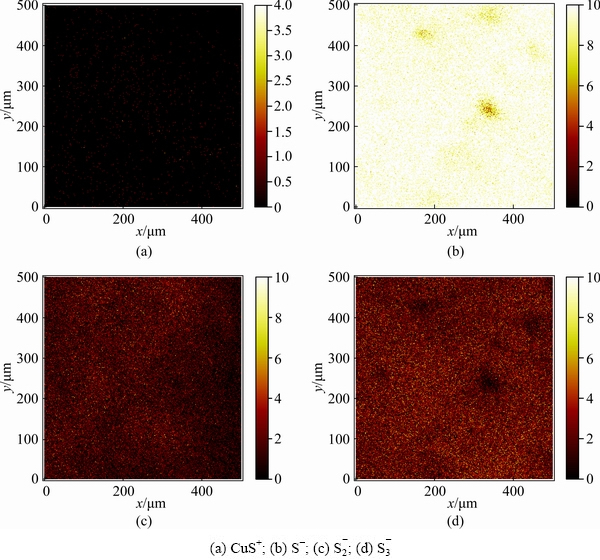
Fig. 11 ToF-SIMS images of selected ions for Na2S-treated cuprite surface obtained in surface imaging operational mode
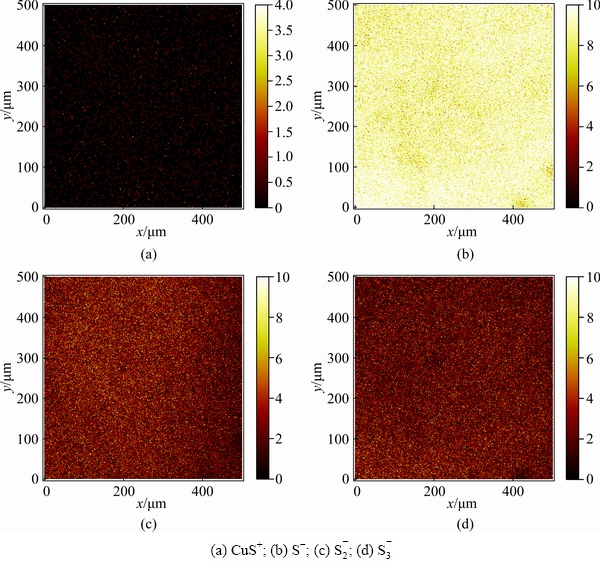
Fig. 12 ToF-SIMS images of selected ions for H2O2- and Na2S-treated cuprite surface obtained in surface imaging operational mode
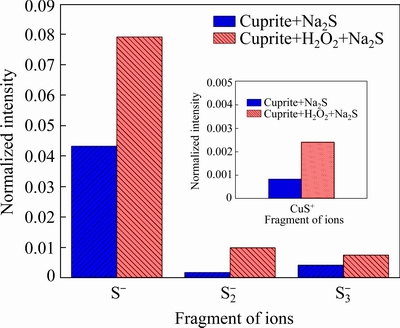
Fig. 13 Normalized intensities of secondary ions on Na2S-treated cuprite surfaces with and without modification
3.2.6 XPS spectra
Modification with H2O2 could enhance the sulfidization of cuprite and increase the adsorption of NaBX on the cuprite surface. We performed XPS analysis of sulfide-treated cuprite surfaces with and without modification to confirm the influence of modification on sulfidization of cuprite. The results were used to study the properties of sulfidization products on cuprite surfaces with and without modification and to identify the mechanism of modification. The molar fractions of major elements on the sulfidized cuprite surfaces with and without modification are shown in Table 3. After treatment with H2O2, the molar fraction of Cu decreased from 28.08% to 26.27%. This reduction could occur because cuprous oxide species on the cuprite surface were converted to copper oxide species after modification, resulting in a decrease in the relative content of Cu on cuprite. The molar fraction of S increased from 15.96% to 18.47% on the sulfide-treated cuprite surface after modification. This result indicated that modification with H2O2 could enhance the sulfidization of cuprite, resulting in an increase in the content of effective sulfur species on cuprite. These changes would create favorable conditions for subsequent interaction with the collector. Figure 14 shows the O 1s spectra of sulfidized cuprite surfaces with and without modification. After treatment with H2O2, the binding energies of O(II) species on the cuprite surface did not change significantly.
Figure 15 shows the Cu 2p spectra of the sulfidized cuprite surfaces with and without H2O2modification. The binding energy of copper species on the cuprite surface did not change greatly after treatment with H2O2, and the observed small shifts in the binding energies may have been caused by a charging effect. Figure 16 shows the molar fractions of Cu(I) and Cu(II) species on the sulfidized cuprite surfaces with and without modification. After treatment with H2O2, the molar fractions of Cu(I) and Cu(II) species decreased from 24.08% to 22.86% and 4.00% to 3.41%, respectively. In consideration of the results obtained for the molar fractions of major elements on the sulfidized cuprite surfaces with and without modification, the decrease in the molar fractions of Cu(I) and Cu(II) species may be caused by a decrease in the total content of Cu on the cuprite surface. Table 4 shows the proportions of Cu(I) and Cu(II) species among the total copper species on the sulfidized cuprite surfaces with and without modification. The proportion of Cu(I) species among the total copper species increased from 85.77% to 87.04% compared with that of non-modified sample. This result suggested that more Cu(II) species on the cuprite surface treated with H2O2 could interact with sulfur ions and were reduced to Cu(I) species than that on untreated cuprite surface. The increase in the proportion of Cu(I) species suggested that modification with H2O2 gave a Na2S-modified cuprite surface that would be beneficial to the flotation.
Table 3 Molar fractions of major elements on sulfidized cuprite surfaces treated with 1×10-3mol/L Na2S, and 5×10-4mol/L H2O2 and 1×10-3mol/L Na2S
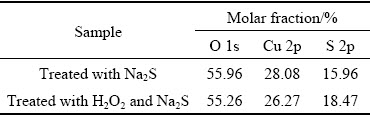
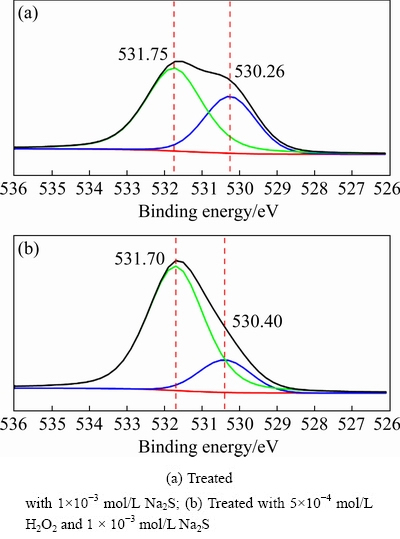
Fig. 14 O 1s XPS spectra of cuprite surfaces
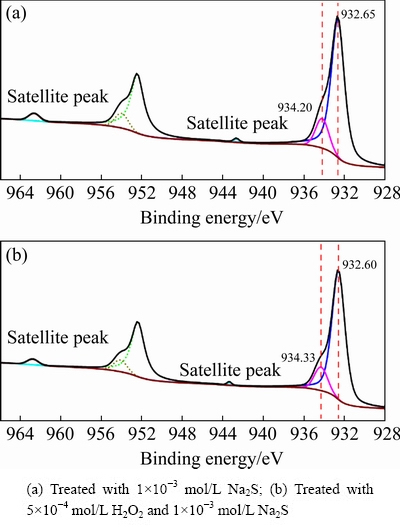
Fig. 15 Cu 2p XPS spectra of cuprite surfaces
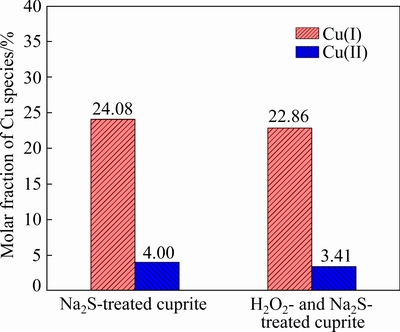
Fig. 16 Molar fractions of copper species on Na2S-treated cuprite and H2O2- and Na2S-treated cuprite
Table 4 Quantification of Cu 2p species on sulfidized cuprite surfaces treated with 1×10-3mol/L Na2S, and 5×10-4mol/L H2O2 and 1×10-3mol/L Na2S
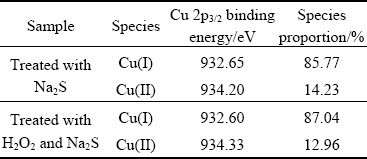
Figure 17 shows the S 2p XPS spectra of sulfidized cuprite surfaces with and without modification. The peaks at 161.71, 163.98, and 168.44 eV were attributed to S2-, Sn2-, and SOn2- species on the cuprite surface, respectively [36]. After treatment with H2O2, the binding energy of SOn2- species on the sulfidized cuprite surface shifted to 168.29 eV. This shift suggested that the chemical state of the SOn2- species changed. Figure 18 shows the molar fractions of S2- and Sn2- species on sulfidized cuprite surfaces with and without modification. The molar fractions of S2- and Sn2- species increased from 12.81% to 15.10%, and 1.44% to 2.11% compared with non-modified, respectively. This indicated that modification using H2O2 before sulfidization could enhance the adsorption of sulfur ions on cuprite and increase the generation of hydrophobic copper sulfide species. Meanwhile, the increase in Sn2- species may facilitate the floatability of cuprite through the generation of active Cu-Sn species. Table 5 shows the proportions of S2-, Sn2-, and SOn2- species among the total S species on thesulfidized cupritesurfaces with and without modification. The proportions of S2- and Sn2- species among the total S species increased from 80.29% to 81.75% and 9.00% to 11.42%compared with those of non-modified sample, respectively. These results suggested that more Cu-S and Cu-Sn species were generated on cuprite when it was treated with H2O2 before sulfidization. An increase in Cu-Sn species is important for enhancing the hydrophobicity of cuprite because of the high activities of these species with collectors. In addition, the proportion of SOn2- species among the total S species decreased from 10.71% to 6.83% compared with non-modified, which was favorable to the flotation of cuprite because of the hydrophilic characteristics of SOn2- and its compounds. The XPS results showed that the proportion of Cu(I) species among the total copper species and the molar fractions of S2- and Sn2- species on the sulfidized cuprite surfaces increased with H2O2 treatment. Therefore, modification with H2O2 could strengthen the sulfidization process of cuprite and promote the formation of copper sulfide species on the cuprite surface. This would enhance adsorption of the collector and the hydrophobicity of the cuprite surface, which would improve the conditions for sulfidization flotation of cuprite.
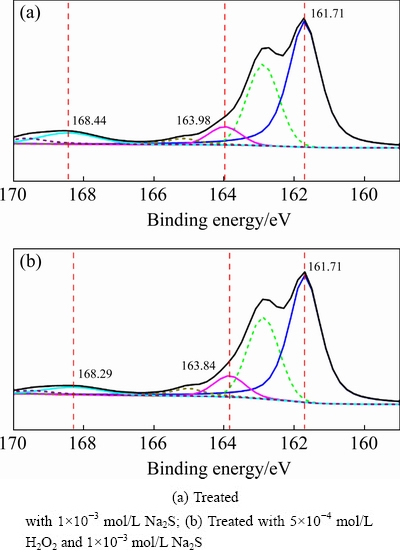
Fig. 17 S 2p XPS spectra of cuprite surfaces
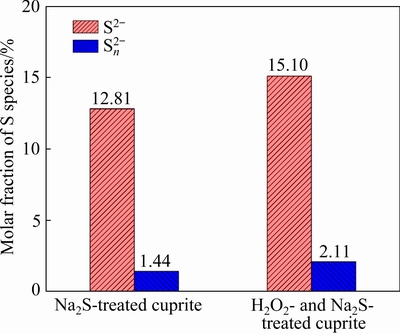
Fig. 18 Molar fractions of S species on surfaces of Na2S-treated cuprite and H2O2- and Na2S-treated cuprite
Table 5 Quantification of S 2p species on sulfidized cuprite surfaces treated with 1×10-3 mol/L Na2S, 5×10-4 mol/L H2O2 and 1×10-3mol/L Na2S
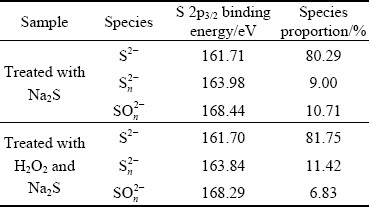
3.2.7 Microflotationbehavior
To confirm our earlier experimental results, we comprehensively investigated the effects of the oxidant, sulfurizing reagent, and collector doses on the flotation of cuprite. Sulfidization flotation tests of cuprite with different concentrations of H2O2 were carried out to study the influence of modification on cuprite sulfidization flotation (Fig. 19). During the sulfidization process, the pulp pH was adjusted to 9.5. Without modification, the recovery of the cuprite was 61.74% (Fig. 19), which indicated that the direct sulfidization flotation of cuprite was not ideal. When cuprite was oxidized with H2O2 before sulfidization, the flotation recovery of cuprite increased. When the H2O2 concentration was 5×10-5mol/L, the flotation recovery of cuprite increased to 72.21%. When the H2O2 concentration was increased to 5×10-4mol/L, the flotation recovery of cuprite reached 83.30%. These results showed that modification of the cuprite surface greatly improved the flotation recovery of cuprite. However, with further increase in the H2O2concentration, the flotation recovery of cuprite decreased. With 2×10-3mol/L H2O2, the flotation recovery of cuprite was 76.88%. This decrease could be caused by the presence of residual oxidant in the pulp, which would consume Na2S. As a result, it was difficult to sufficiently sulfidize the cuprite surface and the collector was not adsorbed stably on the mineral surface. The effect of the H2O2 concentration on the flotation results of cuprite showed that an appropriate dose of H2O2 was required to pre-oxidize the cuprite surface to improve the flotation behavior of cuprite. Excess H2O2 was not conducive to the sulfidization of cuprite and would be detrimental to the flotation environment for cuprite.
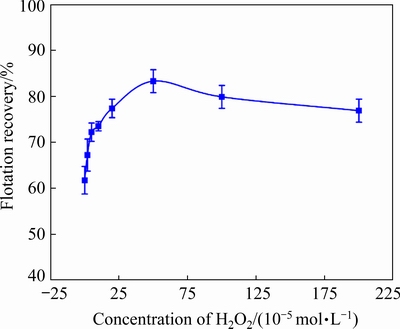
Fig. 19 Flotation recovery of cuprite as function of H2O2 concentration at 1×10-3 mol/L Na2S, 5×10-4mol/L NaBX, and pH 9.5
We also performed flotation tests of cuprite with changes in the NaBX concentration (Fig. 20) and Na2S concentration (Fig. 21) in the absence andin the presence of H2O2. Within the investigated concentration range of NaBX, the flotation recovery of pre-oxidized cuprite was obviously higher than that for the direct sulfidization flotation (Fig. 20). When the NaBX concentration was 4×10-4mol/L, the flotation recovery of oxidant-treated cuprite was 74.48% and the recovery of cuprite without modification was 55.42%. When the NaBX concentration exceeded 5×10-4mol/L, the flotation recovery of cuprite with and without modification plateaued. In the investigated concentration range for Na2S, the floatability of modified cuprite was better than that of directly sulfidized cuprite(Fig. 21). However, when the concentration of Na2S exceeded 1×10-3 mol/L, an obvious downward trend was observed in the cuprite recovery. When the concentration of Na2S was 5×10-3 mol/L, the recovery of directly sulfidized cuprite was only 27.86% and that of oxidant- and sulfide-treated cuprite was only 61.44%. These results could be caused by an excess of Na2S, resulting in sulfur ions remaining in the pulp. Sulfur ions would compete with the collector for adsorption on the cuprite surface. In addition, the adsorption of excess sulfur ions on the mineral surface would give the surface a negative charge, which would not be conducive to adsorption of the anionic collector. The flotation results indicated that H2O2 treatment of cuprite was beneficial to the flotation. This was attributed to the fact that pre-oxidization of the cuprite surface could strengthen the adsorption of sulfur ions in the sulfidization process. The increased adsorption would ensure that the surface of cuprite was sufficiently sulfidized to promote the adsorption of xanthate and enhance the hydrophobicity of the cuprite surface.
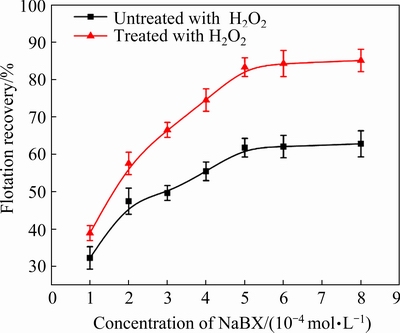
Fig. 20 Flotation recovery of cuprite as functionof NaBX concentration at 5×10-4 mol/L H2O2,1×10-3mol/L Na2S, and pH 9.5
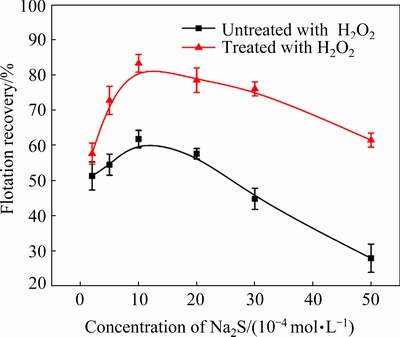
Fig. 21 Flotation recovery of cuprite as function of Na2S concentration at 5×10-4 mol/L H2O2, 5×10-4 mol/L NaBX, and pH 9.5
Figure 22 shows a schematic diagram of the mechanism of enhanced sulfidization of cuprite after modification with H2O2. It is difficult to obtain fully sulfidized cuprite surfaces by direct sulfidization. However, after modification of the cuprite surface with H2O2, the copper species on the surface change from Cu(I) to Cu(II), which has stronger affinity than Cu(I) for sulfur ions. This greatly enhances the sulfidization of cuprite. The surface of the modified cuprite can react strongly with xanthate after sulfidization, which significantly enhances the floatability of cuprite. These results will be very important for realizing efficient and clean recovery and utilization of copper oxide ores from cuprite in industry.
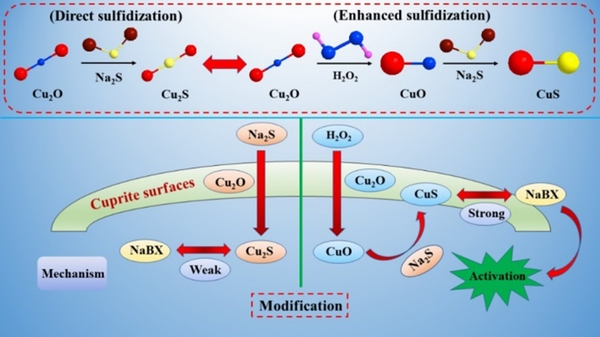
Fig. 22 Schematic diagram of surface-enhanced sulfidization mechanism of cuprite via modification with H2O2 and its response to xanthate adsorption and flotation
4 Conclusions
(1) Modification using H2O2 increased the amount of NaBX adsorbed on the cuprite surface.
(2) More Cu-S and Cu-Sn species were generated on the cuprite surface after modification with H2O2.
(3) The flotation recovery of cuprite modified with H2O2 was obviously higher than that obtained after direct sulfidization flotation.
(4) Modification with H2O2 could enhance thesulfidization of cuprite and provide a Na2S-modified cuprite surface that is beneficial to the flotation.
Acknowledgments
The authors would like to acknowledge the Project funded by Ten Thousand Talent Plans for Young Top-notch Talents of Yunnan Province, China (No. YNWR-QNBJ-2018-051).
References
[1] WEI Qian, JIAO Fen, DONG Liu-yang, LIU Xue-duan, QIN Wen-qing. Selective depression of copper-activated sphalerite by polyaspartic acid during chalcopyrite flotation [J]. Transactions of Nonferrous Metals Society of China, 2021, 31: 1784-1795.
[2] CHEN X M, PENG Y J, BRADSHAW D. The separation of chalcopyrite and chalcocite from pyrite in cleaner flotation after regrinding [J]. Minerals Engineering, 2014, 58: 64-72.
[3] LIU Sheng, LIU Guang-yi, HUANG Yao-guo, ZHONG Hong. Hydrophobic intensification flotation: Comparison of collector containing two minerophilic groups with conventional collectors [J]. Transactions of Nonferrous Metals Society of China, 2020, 30: 2536-2546.
[4] SUN Qian-yu, YIN Wan-zhong, LI Dong, FU Ya-feng, XUE Ji-wei, YAO Jin. Improving the sulfidation-flotation of fine cuprite by hydrophobic flocculation pretreatment [J]. International Journal of Minerals, Metallurgy, and Materials, 2018, 25: 1256-1262.
[5] YIN Wan-zhong, SUN Qian-yu, LI Dong, TANG Yuan, YU Ya-feng, YAO Jin. Mechanism and application on sulphidizing flotation of copper oxide with combined collectors [J]. Transactions of Nonferrous Metals Society of China, 2019, 29: 178-185.
[6] KONGOLO K, MIPOKA M, MINANGA K, MPOYO M. Improving the efficiency of oxide copper–cobalt ores flotation by combination of sulphidisers [J]. Minerals Engineering, 2003, 16: 1023-1026.
[7] MEHDILO A, IRANNAJAD M, ZAREI H. Smithsonite flotation from zinc oxide ore using alkyl amine acetate collectors [J]. Separation Science and Technology, 2014, 49: 445-457.
[8] LIU C, SONG S X, LI H Q, LI Y B, AI G H. Elimination of the adverse effect of calcite slimes on the sulfidization flotation of malachite in the presence of water glass [J]. Colloids and Surfaces A: Physicochemical and Engineering Aspects, 2019, 563: 324-329.
[9] LIU C, SONG S X, LI H Q, AI G H. Sulfidization flotation performance of malachite in the presence of calcite [J]. Minerals Engineering, 2019, 132: 293-296.
[10] HERRERA-URBINA R, SOTILLO F J, FUERSTENAU D W. Effect of sodium sulfide additions on the pulp potential and amyl xanthate flotation of cerussite and galena [J]. International Journal of Mineral Processing, 1999, 55: 157-170.
[11] ZHANG S, WEN S M, XIAN Y J, LIANG G Y, LI M H. Pb ion pre-modification enhances the sulfidization and floatability of smithsonite [J]. Minerals Engineering, 2021, 170: 107003.
[12] ZHANG S, WEN S M, XIAN Y J, ZHAO L B, FENG Q C, BAI S J, HAN G, LANG J T. Lead ion modification and its enhancement for xanthate adsorption on smithsonite surface [J]. Applied Surface Science, 2019, 498: 143801.
[13] LIANG Y J, CHAI L Y, MIN X B, TANG C J, ZHANG H J, KE Y, XIE X D. Hydrothermal sulfidation and floatation treatment of heavy-metal-containing sludge for recovery and stabilization [J]. Journal of Hazardous Materials, 2012, 217-218: 307-314.
[14] YIN W Z, SHENG Q Y, MA Y Q, SUN H R, YANG B, TANG Y. Effects of copper ions on malachite sulfidization flotation [J]. Physicochemical Problems of Mineral Processing, 2020, 56: 300-312.
[15] HAN G, WEN S M, WANG H, FENG Q C. Surface sulfidization mechanism of cuprite and its response to xanthate adsorption and flotation performance [J]. Minerals Engineering, 2021, 169: 106982.
[16] WU DD, MA W H, MAO Y B, DENG JS, WEN S M. Enhanced sulfidation xanthate flotation of malachite using ammonium ions as activator [J]. Scientific Reports, 2017, 7: 2086.
[17] FENG Q C, ZHAO W T, WEN S M. Surface modification of malachite with ethanediamine and its effect on sulfidization flotation [J]. Applied Surface Science, 2018, 436: 823-831.
[18] HAN G, WEN S M, WANG H, FENG Q C. Identification of copper-sulfide species on the cuprite surface and its role in sulfidization flotation [J]. Colloids and Surfaces A: Physicochemical and Engineering Aspects, 2021, 624: 126854.
[19] WEN Shu-ming, LIU Dian-wen, FANG Jian-jun, SHEN Hai-ying, FENG Qi-cheng, DENG Jiu-shuai, LIU Jian. Method of enhancing sulfidization of cuprite in flotation of mixed copper ore: CN patent, 2013101424069 [P]. 2013-04-23. (in Chinese)
[20] FENG JJ, WANG E Y, HUANG Q S, DING H C, ZHANG X Y. Experimental and numerical study of failure behavior and mechanism of coal under dynamic compressive loads [J]. International Journal of Mining Science and Technology, 2020, 30: 613-621.
[21] ASIF M, PANIGRAHI D C, NAVEEN P, OJHA K. Construction of high-pressure adsorption isotherm: A tool for predicting coalbed methane recovery from Jharia coalfield, India [J]. International Journal of Mining Science and Technology, 2019, 29: 765-769.
[22] YANG Rui-qing, LIANG Na, CHEN Xuan-yu, WANG Long-wei, SONG Guo-xin, JI Yan-chen, REN Na, LU Ya-wei, ZHANG Jian, YU Xin. Sn/Sn3O4-xheterostructure rich in oxygen vacancies with enhanced visible light photocatalytic oxidation performance [J]. International Journal of Minerals, Metallurgy and Materials, 2021, 28: 150-159.
[23] LI Fang-xu, ZHOU Xiao-tong, LIN Ri-xiao. Flotation performance and adsorption mechanism of novel 1-(2-hydroxyphenyl)hex-2-en-1-one oxime flotation collector to malachite [J]. Transactions of Nonferrous Metals Society of China, 2020, 30: 2792-2801.
[24] CUI Ya-fang, JIAO Fen, QIN Wen-qing, DONG Liu-yang, WANG Xu. Synergistic depression mechanism of zinc sulfate and sodium dimethyl dithiocarbamate on sphalerite in Pb-Zn flotation system [J]. Transactions of Nonferrous Metals Society of China, 2020, 30: 2547-2555.
[25] HU H S, LI M, LI LL, TAO XX. Improving bubble-particle attachment during the flotation of low rank coal by surface modification [J]. International Journal of Mining Science and Technology, 2020, 30: 217-223.
[26] SUN Yue-quan, ZHANG Xin-yue, LIU Li-ming, ZHAO Yi-ting, LIU Fang, HUANG Qing-song. Optimization of battery life and capacity by setting dense mesopores on the surface of nanosheets used as electrode [J]. International Journal of Minerals, Metallurgy and Materials, 2021, 28: 142-149.
[27] DENG R D, HU Y, KU J G, ZUO W R, YANG Z G. Adsorption of Fe(III) on smithsonite surfaces and implications for flotation [J]. Colloids and Surfaces A: Physicochemical and Engineering Aspects, 2017, 533: 308-315.
[28] ZHOU J H, SUI Z J, ZHU J, LI P, CHEN D, DAI Y C, YUAN W K. Characterization of surface oxygen complexes on carbon nanofibers by TPD, XPS and FT-IR [J]. Carbon, 2007, 45: 785-796.
[29] HAN G, WEN S M, WANG H, FENG Q C. Effect of ferric ion on cuprite surface properties and sulfidization flotation [J]. Separation and Purification Technology, 2021, 278: 119573.
[30] JARA A D, WOLDETINSAE G, BETEMARIAM A, KIM J Y. Mineralogical and petrographic analysis on the flake graphite ore from Saba Boru area in Ethiopia [J]. International Journal of Mining Science and Technology, 2020, 30: 715-721.
[31] NIU Yan-ping, SUN Chuan-yao, YIN Wan-zhong, ZHANG Xing-rong, XU Hong-feng, ZHANG Xu. Selective flotation separation of andalusite and quartz and its mechanism [J]. International Journal of Minerals, Metallurgy, and Materials, 2019, 26: 1059-1068.
[32] WANG X H, FORSSBERG K S E. The solution electrochemistry of sulfide-xanthate-cyanide systems in sulfide mineral flotation [J]. Minerals Engineering, 1996, 9: 527-546.
[33] ZHANG Q, XU Z, BOZKURT V, FINCH J A. Pyrite flotation in the presence of metal ions and sphalerite [J]. International Journal of Mineral Processing, 1997, 52: 187-201.
[34] JIANG Y, XIE Q, ZHANG Y H, GENG C Y, YU B, CHI J. Preparation of magnetically separable mesoporous activated carbons from brown coal with Fe3O4 [J]. International Journal of Mining Science and Technology, 2019, 29: 513-519.
[35] DEY S, SAHU L, CHAURASIA B, NAYAK B. Prospects of utilization of waste dumped low-grade limestone for iron making: A case study [J]. International Journal of Mining Science and Technology, 2020, 30: 367-372.
[36] KHOSO S A, HU Yue-hua, LU Fei, GAO Ya, LIU Run-qing, SUN Wei. Xanthate interaction and flotation separation of H2O2-treated chalcopyrite and pyrite [J]. Transactions of Nonferrous Metals Society of China, 2019, 29: 2604-2614.
过氧化氢表面改性强化硫化浮选赤铜矿
韩广,文书明,王涵,丰奇成
昆明理工大学 国土资源工程学院 省部共建复杂有色金属资源清洁利用国家重点实验室,昆明 650093
摘 要:使用过氧化氢作为氧化剂对赤铜矿表面进行改性处理以实现赤铜矿的强化硫化。表面吸附和红外光谱实验结果表明,硫化前使用过氧化氢对赤铜矿表面进行改性可增加黄药在赤铜矿表面的吸附量。Zeta电位、扫描电子显微镜、X射线光电子能谱和飞行时间二次离子质谱实验结果表明,经过氧化氢改性后的赤铜矿表面生成了更多的S2-和Sn2-组分。微浮选实验结果表明,经过氧化氢改性后的赤铜矿浮选回收率从61.74%增加到83.30%。微浮选实验与表面测试分析结果证实,过氧化氢对赤铜矿表面的改性处理能增强赤铜矿表面的硫化过程,从而改善赤铜矿的浮选行为。
关键词:赤铜矿;浮选;过氧化氢;表面改性;硫化
(Edited by Wei-ping CHEN)
1003-6326/
2021 The Nonferrous Metals Society of China. Published by Elsevier Ltd & Science Press
Abstract:Hydrogen peroxide was used as an oxidant to modify the cuprite surface and enhance its sulfidization. Surface-adsorption and infrared spectroscopy measurements indicated that the modification of the cuprite surface with hydrogen peroxide before sulfidization increased the adsorption capacity of xanthate. Zeta potential, scanning electron microscopy-energy dispersive X-ray spectroscopy, X-ray photoelectron spectroscopy, and time-of-flight secondary ion mass spectrometry results showed that the modification with hydrogen peroxide increased the contents of S2- and Sn2- species on the cuprite surface. Microflotation tests showed that the recovery of cuprite increased from 61.74% to 83.30% after the modification of the surface with hydrogen peroxide. These results confirm that the modification of the cuprite surface with hydrogen peroxide enhances the sulfidization of cuprite, which in turn improves its flotation.