Trans. Nonferrous Met. Soc. China 31(2021) 3478-3505
Challenges and new insights for exploitation of deep underground metal mineral resources
Peng LI1,2,3, Mei-feng CAI1,2,3
1. School of Civil and Resources Engineering, University of Science and Technology Beijing, Beijing 100083, China;
2. Key Laboratory of High-Efficient Mining and Safety of Metal Mines (Ministry of Education), University of Science and Technology Beijing, Beijing 100083, China;
3. Beijing Key Laboratory of Urban Underground Space Engineering, University of Science and Technology Beijing, Beijing 100083, China
Received 14August 2021; accepted 21November 2021
Abstract:
ong-term and continuous large-scale exploitation has increasingly exhausted shallow metal mineral resources, and deep mining has become inevitable. The current global status of deep mining of metal mineral resources was presented, a series of engineering challenges faced by deep mining were systematically analyzed, and some progress and future innovation focus in key engineering technologies, such as the prediction and prevention of rockburst, cooling techniques, rock support techniques, deep hoisting techniques, and several nontraditional deep mining techniques, were highlighted. Meanwhile, new insights into development strategies of deep mining technology were proposed. The integration of these forward-looking key innovative technologies will form the overall framework of an innovative technology system for the deep mining of metal minerals. This technology system will help to achieve safe, efficient, and green exploitation of deep underground metal mineral resources and ensure the sustainable development of the metal mining industry.
Key words:
deep metal mineral resources; engineering challenges; disaster control; nontraditional mining technique; sustainable development;
1 Introduction
According to the World Economic Forum’s report on mining and metals scenarios to 2030, “global population growth—together with upward trends in urbanization and industrialization, particularly in emerging economies—has led to a strong increase in demand for commodities from the mining and metals industries. This growth is highly likely to continue and will place pressure on the demand of resources” [1]. Metal mineral resources are the most fundamental source of metal minerals and materials, and are an important material basis for human survival and social development. After hundreds of years of exploitation, the more accessible shallow metal mineral resources are being gradually exhausted, and some have been completely exhausted [2,3]. This means that more mineral resources in the deeper part of the earth need to be developed economically to meet growing societal demands.
At present, many metal mines worldwide have successively engaged in deep mining (here, deep mining refers to mines with a mining depth exceeding 1000 m). According to incomplete statistics, there are at least 112 mines worldwide with a mining depth greater than 1000 m [4], mostly located in South Africa, Canada, Australia, the United States, Russia, India, and Ukraine. The vast majority of gold mines in South Africa are mined at a depth of more than 2000 m [5], among which the mining depth of the Mponeng gold mine reaches 4359 m and the burial depth of ore bodies exceeds 7500 m. Metal mines in Canada have reached over 2000 m, approaching 3000 m, and the mining level of the Kidd copper-zinc mine is approximately 2800 m [6]. The mining depth of metal mines in India has reached 2000-3500 m, for example, the depth of the Champion Reef gold mine has reached 3260 m. The metal mines in Russia will soon reach mining levels of 2000-2500 m [7]. In China, metal mines have engaged deep mining relatively late but developed rapidly, and approximately 32 metal mines currently have a mining depth of over 1000 m [8], among them, the JiapigouGold Mine, HuizeLead-Zinc Mine, and LiujuCopper Mine have reached 1500 m, and the Yinxin gold mine and Hongtoushan copper mine have reached 1600 m. In addition, a number of large- and medium-sized metal mines are under construction or planned for construction in China, such as the Sishanling, Jining, and Chentaigou iron mines, which are deep underground mines with mining depth exceeding 1000 m or even reaching 3000 m. Hence, it can be predicted that the exploitation of deep and even ultradeep metal mineral resources will become more common in the future.
The safe and effective exploitation of deep metal mineral resources is facing a series of engineering challenges. Compared with shallow mining, deep mining encounters a special geological environment of high stress, high temperature, and high water pressure as well as more severe engineering disturbance induced by mining activities [9]. In these cases, the effect of in situ environment on deep rock masses has become more prominent. Furthermore, the deformation and failure of deep rock masses after being strongly disturbed often sudden and lack precursors such as notable time-dependent behavior [10-12]. As a result, deep mining may be associated with various frequently occurring and large-scale nonlinear dynamic disasters such as large roadway deformations, rockbursts, collapsed walls, falling roofs, inrushing water, and ground-surface collapses, which are usually complex and difficult to monitor, warn, and control [13-15]. Among these disasters, rockburst is the number one lethal threat to safe deep mining [16,17]. Thus, ground pressure control and support techniques under high stress need to be achieved. In addition, the high temperature and associated ventilation and cooling measures, the methods and costs of handling deep mined ore and transporting it to the surface, the complex and difficult mining conditions, and the desirability of developing nonentry methods of mining at great depths are also intractable problems that seriously affect normal operations. In general, the existing theories, techniques and methods of extraction have difficulty meeting the requirements of the deep mining environment, and the engineering practice of deep mining is blind, inefficient, and uncertain to a certain extent [5,8]. Notably, current mining models have caused serious resource waste and ecological and environmental problems, which has always been a troublesome issue for mining. All these factors have aroused great concern about the sustainability of future metal raw material supplies. Under these circumstances, new, low-cost, and nontraditional methods for deep mining are necessary to develop solutions for these major challenges and thus achieve the safe, efficient, and green exploitation of deep underground metal mineral resources.
2 Major challenges in deep mining
2.1 High in situ stress
In situ stress is the natural original stress existing in the crust before mining, and all mining excavation activities are carried out by controlling the in situ stress, which is the dominant factor influencing underground deformation and failure in mining engineering [18,19]. Theoretically, the in situ stress increases linearly with increasing depth [20-22]. The stress concentration level caused by engineering excavation, especially large-scale mining activities, far exceeds the compressive strength of engineering rock masses. For example, the in situ stress measurement results of the Sanshandao and LinglongGold Mines in China showed that the stress magnitude at depths of 800–1000 m exceeds 60 MPa [22]. According to the in situ stress measurements in South Africa, the stress magnitude at depths of 3500-5000 m reaches 95-135 MPa [5,11]. It is apparent that a deep rock mass incurs abnormally high stress and accumulates considerable deformation energy. Therefore, as the mining depth increases, the influence of in situ stress on the stability of the surrounding rock becomes more notable. Under the action of high in situ stress, disasters caused by mining disturbances have risen sharply in metal mines in recent years, and the occurrence of disasters is extremely difficult to forecast. Consequently, the deep high-stress environment is the decisive factor of engineering disasters in deep mining. If traditional mining technology and support technology do not adapt to the high-stress environment of deep mines, operational safety will inevitably be endangered.
2.2 High-temperature heat hazard
It is well known that the temperature of underground strata increases with increasing mining depth. The temperature of an underground rock formation increases with depth increasing at a gradient of 1.7-3.0 °C per 100 m. In some areas, such as near faults or abnormal local areas with high thermal conductivity, the geothermal gradient is sometimes as high as 20 °C per100 m [5]. When the mining depth is less than 800 m, a heat hazard will not occur (the temperature is usually lower than 40 °C), but a heat hazard may occur in individual mines, although it will generally not be serious [23]. However, with increasing mining depth, the problem of high-temperature heat hazard in deep mines has become increasingly prominent. The temperature of a rock formation in a mine over a kilometer deep will exceed that of the human body, and the rock temperature could reach above 80 °C after the burial depth reaches 3000 m [4], which is unbearable for workers and equipment. For example, the temperature in mines of western South Africa has reached 50 °C at a depth of 3300 m [24,25]. In the mid-1980s, the mining depth of the Kolar Gold Mine in India was greater than 3000 m, and the rock temperature exceeded 69 °C. Due to the influence of geothermal water, the rock temperature reached 69 °C and the local temperature reached 80 °C at a mining depth of 500 m in the FengyuLead-Zinc Mine in Japan [24,25]. The rock temperature of the LuoheIron Mine in China reached 42 °C at a 700 m depth, and the rock temperature of the SishanlingIron Mine was 30-35 °C at depths of 1000 m and 50-60 °C at depths of 2000 m. Studies indicated that a 1 °C change in temperature in the rock mass can produce a change in the in situ stress of 0.4-0.5 MPa [5,11].
The high-temperature environment will not only affect the physical and mental health of miners by reducing their work efficiency and causing accidents, but also trigger the thermodynamic effect of rock masses and produce unexpected mine disasters [26]. According to the statistics, the underground industrial accident rate can increase by 5%-14% and the labor productivity of workers can decrease by 7%-10% for every 1 °C increase in temperature after the temperature exceeds the safety standard of 28 °C[4,27]. Moreover, in a high-temperature environment, the risk of spontaneous combustion of high-sulfur ore and self-explosion of explosives increases [28], which introduces great psychological pressure on workers and seriously threatens operational safety. Hence, high temperature has become a common threat in deep mines, which must be cooled down to maintain normal production. However, to effectively reduce the temperature, the production costs must be greatly increased. As a result, deep mining is difficult to carry out due to economic challenges (excessive cost). Consequently, to ensure safe and efficient deep mining, it is urgent and necessary to develop high-efficiency and expandable deep mine cooling and heat hazard control and treatment techniques and equipment.
2.3 High water pressure
After entering deep layers, the increase in in situ stress and temperature is accompanied by an increase in water pressure. When the mining depth exceeds 1000 m, the water pressure can reach 10 MPa [5,8]. For example, the water pressure at 1425 m in the ShalingGold Mine of Laizhou, China, reached 11 MPa. A high water pressure environment can also affect the stress state of deep rock masses, which will decrease the effective stress of deep rock structures and probably drive crack expansion and lead to serious engineering disasters such as water inrush in deep mines [5,8,11]. In addition, high water pressure can significantly decrease the effective stress and critical stress of faults (if it exists) [29-31]. In this case, a small stress disturbance or stress concentration may trigger a fault slip, resulting in large-scale instability and collapse of rock masses and even fault slip-type rockburst.
2.4 Deep lithology deterioration
Compared with shallow rock masses, the structure and mechanical properties of deep rock masses can change greatly. Engineering practice shows that shallow rock is hard at a low stress level. With increasing mining depth, the in situ stress level and confining pressure increase significantly, and some hard rocks may become soft rocks, demonstrating significant plastic deformation characteristics [11]. Accordingly, the surrounding rock of underground engineering is transformed from an engineering state dominated by elastic deformation in shallow environments to an engineering state dominated by plastic deformation in deep environments. The depth of engineering state transformation is called the critical softening depth. When the mining depth is less than the critical softening depth, it is generally considered that the rock mass is still in the elastic stage, and its deformation is still continuous. Even when the elastic limit of the rock mass is exceeded, large deformation, spalling and weak impacts can appear, the surrounding rock structure is still relatively stable, and the stability of the surrounding rocks can be controlled by adopting conventional construction methods and support techniques.
In contrast, deeper rock masses are generally in a high-stress environment and often store a large amount of deformation energy. The deformation and failure of the rock mass are sudden and violent, and the ground pressure appears violently, which is prone to engineering disasters such as plastic deformation of surrounding rock, strong rheology, and rockburst, and conventional support control means can no longer play an effective role [32]. In particular, the rheological properties and plastic instability of deep rock masses under the conditions of high stress and high temperature are notably different from those in a shallow environment [8], which is also an important factor affecting the occurrence of deep disasters. Hence, if the mining and supporting design standards and methods applicable to shallow areas are uncritically applied, many serious problems may be induced because shallow conventional support countermeasures and construction techniques cannot effectively control the stability of mining structures in deep conditions.
2.5 Deep hoisting
The mine hoisting system is an important link in the mine production process and plays the role of connecting the underground and aboveground environments. For deep mining, the special geological environment brings forward new demands for hoisting transportation equipment, and deep hoisting has long been a major challenge to be solved. The main problems for deep hoisting are the safety, capacity, and economic rationality of hoisting. With increasing mining depth, the hoisting height of ore and various materials increases significantly, which greatly increases the difficulty and cost of hoisting and significantly reduces safety and reliability. To ensure economic mining, it is necessary to improve the output, which requires a larger single hoisting amount of hoisting machinery.
At present, the hoisting equipment employed in metal mines around the world primarily includes single-rope winding hoists (single drums and dual drums), multirope winding hoists (i.e., Blair hoists), and multirope friction hoists (i.e., Koepe hoists) [33]. According to the statistics, the single-stage maximum hoisting heights of a friction hoist and winding hoist are only approximately 1800 m and 3000 m, respectively. For a traditional rope hoist, efficiency, economy and reliability can be guaranteed in shallow mining. However, a steel wire rope will be lengthened and thickened continuously in deep mining, which not only greatly reduces the effective hoisting capacity due to the weight of the steel wire rope, but also causes damage to the wire rope due to the excessive tension change induced by the large change in tail rope length [4]. If the hoisting height is higher, multistage hoisting must be adopted, which will significantly decrease the effective load of hoisting and greatly increase the hoisting cost. For example, a three-stage hoisting method has been adopted in the TauTonaGold Mine in South Africa [34]. Hence, traditional rope hoisting techniques are difficult to adapt to the demands for deep hoisting and pose a potential threat to production safety. How to reasonably optimize existing hoisting systems or develop new hoisting techniques, reduce hoisting transportation links, and transport deep resources at low cost has become a major technical difficulty for deep mining.
In summary, the high-stress, high-temperature, and high-water-pressure environment of deep rock masses determines the original physical and mechanical characteristics of the rock masses, and the strong engineering disturbance induced by deep mining aggravates the abrupt change of dynamic responses in the rock masses, resulting in frequent disasters. Traditional shallow mining modes and methods are not suitable considering the high stress, high temperature, high water pressure, rock mass structure variation, and complex geological conditions in a deep environment and must undergo major changes. To fundamentally ensure the safety of deep mining and improve the mining efficiency, it is necessary to develop new theories and techniques suitable for deep mining.
3 Mechanism, prediction, and prevention of rockburst
3.1 Rockburst mechanism
The knowledge and mitigation of rockburst have always been major safety and rock engineering challenges for deep mining [35]. Rockburst is a type of artificially induced dynamic disaster in which disturbance energy generated by mining excavation accumulates and evolves in rock masses and is suddenly released under certain inducement, which is completed under the dominance of in situ stress [36,37]. The occurrence location of rockburst is “random”, the gestation process is “slow”, and the occurrence process is “abrupt”. Rockburst was first observed in the Kolar Gold Mine of India in 1900. At present, more than 20 countries worldwide have recorded rockburst events with a maximum burst magnitude of Ms 5.1 in deep mining, especially gold mines in South Africa and India. From 1900 to 1994, more than 69000 miners have died, and 1 million have been injured in mines of South Africa; the main cause of these casualties was rockburst[38]. According to the incomplete statistics, in 2001-2007, more than 13000 rockburst events occurred in metal mines in China, causing 16000 miners injured and resulting in the destruction of a large amount of mining equipment and the inability to exploit a large amount of valuable resources [35]. With increasing mining depth, the frequency and intensity of rockburst hazards are increasing, seriously threatening safe mine production. To ensure the safety of deep mining, it is essential to extensively investigate rockburst mechanisms to achieve a fundamental solution to rockburst prediction and prevention.
The rockburst mechanism is essentially a theoretical explanation of the rockburst phenomenon, and the study of the mechanism must be based on the case histories and recorded data of rockbursts. Only in this way can the research results effectively guide the prediction and control of rockbursts. Using years of theoretical studies and engineering practices, CAI et al [4,39] developed and revealed the rockburst mechanism based on the analyses of in situ stress and disturbance energy caused by mining activities. Before mining excavation, the stratum is in a natural equilibrium state. Mining excavation forms a free space in the expected excavation area and breaks the equilibrium state, which causes in situ stress to be released in the form of energy to the free space, forming an “equivalent release load” (Fig. 1). This equivalent release load drives the deformation, displacement, and local stress concentration of the surrounding rock and generates disturbance energy in the surrounding rock. When the disturbance energy accumulates to a high level in the surrounding rock, the disturbance energy will be abruptly released under the condition that the surrounding rock is broken by high stress applied or along a weak plane in the rock mass, and rockburst will occur [39]. This is an accurate understanding of the rockburst mechanism. Accordingly, CAIet al [4,36,39] proposed two necessary conditions for the possibility of rockburst occurrence: (1) the rock mass can store a large amount of energy and has a strong bumping-prone characteristic when broken;and (2) the geological conditions in the mining area have favorable stress environments that can form high-stress concentrations and strong energy accumulation. These two conditions are also the basic judging criteria for rockburst prediction in metal mines.
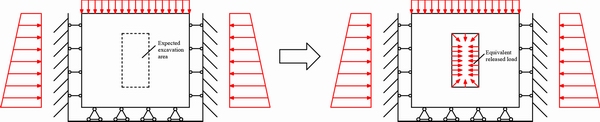
Fig. 1 Illustration of equivalent released load generated by mining excavations [39]
Rockburst usually occurs in hard rock masses bearing high stress, and the induced factors include strong engineering disturbance and high stress concentration induced by superimposed mining and geological structural planes [35,40]. Rocks in metal mines are generally hard. Under high-stress conditions, high-stress concentrations easily occur in rock masses, resulting in large deformation. This indicates that large amounts of energy could accumulate in the surrounding rock in the form of strain energy. A large amount of accumulated strain energy will be suddenly released when the rock mass is ruptured due to high stress or encounters weak planes (such as faults), leading to the occurrence of rockburst. Therefore, rockburst in metal mines is regarded as a kind of shock bump of strain energy [39]. Notably, rockburst is the result of the comprehensive action of compound energy; not all rock masses with accumulated energy can burst, but only when the accumulated energy in the rock mass meets the conditions will rockburst occur.
3.2 Rockburst prediction and prevention
Rockburst is a process in which energy in a rock mass accumulates unevenly in space and transforms unsteadily over time. Because of the complexity of the rockburst mechanism, the randomness of rockburst occurrence, and the uncertainty of the underground rock mass structure, it is very difficult to accurately predict the time and location of rockburst. Thus, the prediction of rockburst is a world-class problem. Due to the serious damage to workers and facilities caused by rockburst, much research has been conducted. The history of rockburst research spans over half a century. Scholars worldwide have proposed various criteria, theories, and hypotheses of rockburst, such as stiffness theory, strength theory, energy theory, instability theory, fractal theory, and catastrophe theory [41]. Most of the above theories are based on the physical and mechanical parameters of the rock itself, which have certain limitations for engineering-scale rock masses. Since there are many factors affecting rockburst, in addition to being controlled by lithologic conditions and stress conditions, mining conditions (including underground engineering geometry, mining methods, mining sequence, etc.) and geological conditions also have a great influence on the occurrence of rockburst[40], and it is difficult to judge whether rockburst occurs only by testing the properties of the rock itself. Moreover, most of the rockburst theories do not involve the conditions of sudden failure of the rock mass. To date, however, most of the theories are still in the stage of exploration and experience, and there is no accurate understanding of the mechanism of rockburst and practical rockburst prediction and prevention techniques.
For rockburst monitoring, various methods have been implemented, including the microgravity method, drilling cuttings method, acoustic emission method, microseismic method, and electromagnetic radiation method. Currently, the microseismic monitoring technique is more mature and widely applied in engineering practice [42]. However, none of the methods has been proven to be reliable, and there are still few successful examples of rockburst prediction. This can be attributed to a lack of correct understanding of the rockburst mechanism and reasonable prediction of rockburst development trends in future mining. In addition, in recent years, various mathematical theories and methods, such as induced seismicity data [43], knowledge-based and data-driven fuzzy modeling [44], random forest regression [45], fuzzy matter–element models [46], intelligent classification models [47], and learning machines [48], have been applied to predict rockburst disasters. These methods are beneficial attempts at rockburst prediction, but their practicability and application range are greatly limited due to their strong subjectivity and poor scientificity. Thus, it is difficult to provide an effective basis for engineering decision-making. The purpose of rockburst prediction is to provide valuable information on the possible spatio-temporal-strength of rockburst prevention and control. All the above methods have some limitations in rockburst prediction. The main reason is the lack of sufficient understanding of the rockburst mechanism caused by mining excavations and suitable rockburst tendency prediction technologies. To date, no theory or method can accurately predict rockburst, so it is essential to study the scientific and effective prediction of rockburst.
Rockburst is an artificial geological process induced by mining excavations and not a purely natural geological phenomenon. When the same underground space is excavated by different excavation methods in the same environment, the surrounding rock may show completely different responses [49]. Moreover, rockburst is not only the response of the surrounding rock to stress redistribution caused by excavations but also the comprehensive response to the whole excavation process and its results. Therefore, rockburst prediction should be closely integrated with the whole mining process [50]. In accordance with mining plans, including volume, position, depth, and procedure, the magnitude of rockburst, initiation time, the spatial distribution of the disturbance energy in the rock mass induced by mining excavations and its variation law with the mining process can be calculated quantitatively through numerical simulation (such as the finite element method and finite difference method), mathematical statistics, and other analytical methods [36]. Subsequently, the spatio-temporal-strength regularity of rockburst in the future can be quantitatively predicted with knowledge of seismology on the relationship of magnitude and related energy.
From the perspective of seismology, rockburst is considered to be an artificially induced earthquake caused by mining. Similar to natural earthquakes, rockburst occurrence is a dynamic process of energy accumulation, evolution, and sudden release. The energy of natural earthquakes derives from the tectonic movement of the earth, and the energy of mine rockburst originates from the disturbance of mining excavations. Hence, according to the magnitude of mining disturbance energy, the development trend magnitude of potential rockburst can be predicted using the relationship between energy and magnitude in seismology [37,39,51], which is given as follows:
lg E=4.8+1.5M (1)
where E is the energy of the inducing earthquake and M is the magnitude of the earthquake.
CAI et al [52] creatively adopted Eq. (1) to predict the rockburst disaster of the LaohutaiCoal Mine in Fushun city, Liaoning Province, China, and successfully predicted the tendency of rockburst and the largest rockburst with a magnitude of 3.7 in 2002 in the history of the mine. Since then, CAIet al [36,50,53] also utilized the same method to evaluate and predict the tendency and time-space-strength relation for rockburst induced by mining excavations in the LinglongGold Mine and SanshandaoGold Mine (Fig. 2). The theoretical prediction results are basically consistent with the field situation, which not only strongly validates the validity and reliability of the prediction theory, but also effectively guides the implementation of rockburst prevention and control measures and greatly reduces the occurrence of rockburst.
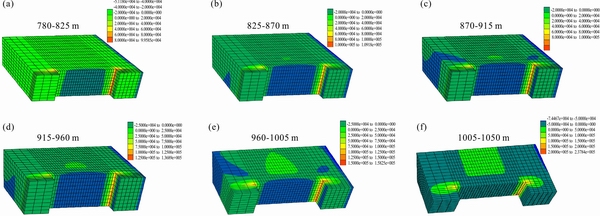
Fig. 2 Elastic strain energy distribution in surrounding rock at different depth intervals in future mining in Sanshandao Gold Mine, China[36]
To meet the safety requirements of deep mining in metal mines, the research focus of rockburst should be shifted from the study of rockburst criteria to the study of prediction and prevention and control. At present, the main problem is that the monitoring and real-time prediction of rockburst still lack mature techniques, and an accurate real-time prediction of rockburst, especially short-term and imminent prediction, cannot be achieved. In this regard, it is necessary to develop intelligent and visual rockburst accurate detection and prediction techniques and equipment as soon as possible based on the mechanism of rockburst[4,39]. On the basis of advanced theoretical prediction, a monitoring network with multiple pieces of information, such as stress, displacement, three-dimensional digital images, geophones, acoustic emissions, and microseisms, should be established to accurately monitor the process of disturbance energy accumulation, evolution, and release during mining, especially to accurately monitor the energy release process. Only through a coupling analysis of multiple energy release information and stress and displacement information can a reliable basis be provided for the real-time prediction of rockburst.
Additionally, some scientific concepts and effective technical measures have been developed to mitigate the rockburst risk in deep metal mines [16,35,39]. Fundamentally, rockburst prevention and control should mainly start with optimizing mining methods, mining layout, and excavation sequences, reducing high-stress concentration and large displacement in surrounding rock alleviating and controlling the accumulation of disturbance energy and its disturbance effect on rock strata and faults during mining, thereby roughly controlling and avoiding the occurrence of rockburst. At the same time, support measures that can absorb energy and prevent impact should be adopted to prevent and weaken the impact damage of rockbursts. Next, some essential and practicable rockburst prediction and prevention techniques and methods, such as the stress relief technique in local high-stress areas, harmless rockburst induction techniques, high-precision monitoring techniques, intelligent and visual detection techniques, and high stress aided blasting methods, need to be further investigated.
4 High-temperature cooling technique
4.1 Common cooling technique
In the special environment of deep mining, many factors can affect the temperature of rock strata. The heat sources of high-temperature mines mainly originate from equipment heat release, mining technology heat release, high rock temperature heat release, abnormal hot water (geothermal) heat release, and so on, which provide a basis for heat hazard control. In 1740, temperature monitoring was carried out in metal mines in France [23]. In 1915, the world’s first mine air-conditioning system was established in the Morro Veino gold mine in Brazil, which marked the rise of the mine cooling technique. After the 1970s, the mine cooling technique developed rapidly and was widely applied. Generally, the commonly used mine cooling techniques around the world can be divided into two categories: nonartificial cooling and artificial cooling techniques. Nonartificial cooling techniques primarily include mine ventilation, heat source isolation, goaf filling, precooling rock stratum, and individual protection, among which mine ventilation is a cooling method that is widely used in the nonartificial cooling technique. By improving the ventilation mode and capacity, an obvious cooling effect can be achieved. However, after the mining depth exceeds 1000 m, conventional ventilation cannot meet the cooling requirement. If the airflow is precooled before it is sent underground, the ventilation and cooling effect will be better, but this will cool down a large number of spaces that do not need to be cooled except for the stope and nearby roadway, resulting in high cost and low efficiency of ventilation and cooling. In addition, other nonartificial refrigeration methods can also have a certain cooling effect. However, engineering practice shows that the cooling capacity of the nonartificial cooling techniques is low and often cannot meet the demands for mines with serious heat damage, thus, this is generally only used as an auxiliary measure for artificial cooling [24].
The application of artificial cooling techniques for mine cooling began in the 1920s and is now widely implemented in metal mines worldwide. In general, artificial cooling techniques can be divided into water cooling systems and ice cooling systems. A water cooling system uses an air conditioning technique and produces cold water through a refrigerating unit and then uses a high-low-pressure heat exchanger and air cooler to cool the airflow input discharged from the ventilation system into the mine to further cool the stope. According to the arrangement of cooling units, water cooling systems can be roughly divided into ground centralized cooling systems, ground heat removal and underground centralized cooling systems, return air heat removal and underground centralized cooling systems, and ground cogeneration cooling systems [54]. These systems have achieved a certain cooling effect in deep metal mines, but they all have their advantages and restrictive operating conditions. The ice cooling system transports granular ice or muddy ice prepared by an ice-making machine on the surface to an underground ice-melting pool through wind or water power, sprays and melts the granular ice or muddy ice using the backwater of the stope, and then sends the cold water formed after ice melting to the stope to reduce the temperature via air cooling or spray cooling [55]. For example, in 1976, the Environmental Engineering Laboratory of South Africa proposed delivering ice to underground mines for cooling, and in 1986, an ice cooling system was first adopted in the Harmony Gold Mine of South Africa for underground cooling, which alleviated the heat hazard induced by high temperature to a certain extent [56-59]. Moreover, an ice slurry was used to adjust the working face temperature in the Mponeng Gold Mine in South Africa. The advantage of an ice cooling system is that the conveying pipeline does not need to bear high pressure, but the mechanical design and blockage of the ice conveying pipeline are two main problems affecting the normal operation of the system, which have higher requirements on the operation management and control of the system [24].
In addition to the above techniques, HE and his colleagues [23-25] proposed a new artificial temperature cooling mode for deep mines using mine water gushing as a cold source. In this mode, an energy extraction system is used to extract the cold energy from the mine water, and then the extracted cold energy is used to exchange heat with the high-temperature gas in the stope, thus reducing the temperature of the stope. Meanwhile, the replaced heat is transported to the ground and is used as the heat source for ground heating and bathing. This temperature control technique can be divided into three modes, i.e., abundant mine water, insufficient mine water, and deficient mine water, to adapt to different mine water conditions. However, this technique is mainly applicable to mines with sufficient water sources. For mines where water sources cannot meet the requirement of extracting cold energy from underground cooling, other water sources are needed as a supplement.
At present, the artificial cooling technique has not been generally accepted in deep mines. This is primarily because artificial refrigeration cooling equipment, such as large refrigeration units, is expensive and consumes considerable power during refrigeration, which makes its operation cost too high. In addition, the cooling effect of artificial cooling systems on deep mine working faces with serious heat damage is not ideal. The above factors make it difficult to popularize and apply artificial refrigeration techniques in more mines.
4.2 Further development of cooling technique in deep mines
The decisive factor of a mine heat hazard is the formation temperature, and the key to heat hazard control in deep mines is to take effective measures to reduce the temperature of the surrounding rock. The existing cooling techniques are passive cooling measures, which not only have high cooling costs but also have unsatisfactory cooling effects in deep mines. To efficiently solve the problem of deep cooling, it is necessary to develop active cooling techniques. Some potential promising techniques and measures are considered and listed as follows:
(1) Heat insulation technique for high-temperature strata. The high-temperature environment in deep mines is mainly caused by the thermal radiation effect of high-temperature rock formations. Developing new and efficient heat insulation materials, techniques and processes to isolate high-temperature heat sources in rock formations and then adopting an artificial cooling technique will achieve a good cooling effect in underground tunnels and working faces.
(2) Heat absorption technique for high-temperature strata. This method develops new low-temperature filling materials with rapid heat absorption and condensation functions, which can be applied to fill mined-out areas and realize mine cooling. To achieve this goal, a reliable conveying system suitable for low-temperature filling materials is needed.
(3) Formation cold storage technique [60,61]. The natural cold energy in the air in winter can be stored in an underground cold storage aquifer through an Inoue transduction system. During the other three seasons, this cold energy can be extracted from the cold storage aquifer through another Inoue matching transduction system and then used to cool the working faces through the underground transduction system.
(4) Geothermal heat recovery technique in deep mines. Geothermal heat is a kind of natural energy. The existing cooling techniques are passive measures that treat geothermal energy as a hazard to prevent. In the process of deep mining, the geothermal energy contained in rock formations can be recovered using the heat exchange technique. Combining deep mining with deep geothermal heat recovery can greatly reduce the comprehensive cost of cooling, thus creating a subversive, economical, and effective technical approach for the cooling of deep mines.
It is worth emphasizing that mine heat hazard control is a systematic project involving many disciplines and fields. Traditional methods cannot fundamentally solve the problem of heat hazards, and the investment and energy consumption are large, which has been proven by the practice of mine cooling around the world. Therefore, it is necessary to improve traditional cooling technology or develop new cooling technology, which will provide strong technical support for the sustainable development of deep metal mineral resources in the future.
5 Deep rock support techniques
In metal mines, weak, broken, and high-stress rock strata are the main objects to be reinforced and supported [62]. As the mining depth increases, the high tectonic stress caused by complex geological structures and the dynamic disturbance caused by mining activities make dynamic disasters a more common phenomenon, which causes serious problems regarding the stability and safety of deep mines [63,64]. The surrounding rock control technology suitable for medium and shallow mines cannot solve the problem of deep rock support. Thus, the development of rock support techniques becomes more vital in deep mining and is the key to preventing various disasters in mines.
To effectively control the stability of the surrounding rock and enhance workplace safety, the corresponding support technique represented by bolts has received extensive attention in recent years. In 1983, ORTLEPP[65] proposed the concept of an energy absorption support system. Afterward, JAGER[66] invented a kind of energy-absorbing cone bolt. Currently, various bolts, such as soft steel bolts [67], Garford dynamic bolts [68], Roofex bolts [69], and D-bolts [70], have been developed and applied to rock supports under high-stress conditions. The development of the abovementioned new energy-absorbing supporting materials has made an important contribution to safe mining. However, these bolts still utilize traditional materials [71]. Although these bolts can provide high support resistance, they cannot provide constant support resistance and large deformation in practical engineering applications because they mainly achieve extensibility by changing the material properties of the rods or through point friction structures [71-73]. As a result, these bolts have difficulty adapting to the deformation and failure characteristics of the surrounding rock in deep mines, resulting in poor support effects and even accidents.
Rock support in deep mines needs to counteract dynamic loads and large rock deformation due to violent rock failure. In this regard, HE et al [72,73] developed a bolt with constant resistance and large elongation (Fig. 3), which can provide constant working resistance and high energy-absorbing capacity and elongations. Under the action of dynamic impact and static tension, the maximum cumulative deformation capacity of the bolt is 500–1000 mm. After that, HE et al [71,74] further proposed the concept of a negative Poisson’s ratio structure and developed a new type of bolt (an NPR bolt) with high constant resistance (350 kN). Compared with the ordinary bolts, the NPR bolt has better impact resistance performance and can absorb the deformation energy of the surrounding rock and resist the large squeeze of rock through its structural deformation. Moreover, KANG et al [75] developed an ultrahigh-strength and high-impact toughness bolt support material. The tensile strength of the bolt rod with a diameter of 22 mm is 859 MPa, the dynamic energy absorption work is 147 J, and the percentage elongation after the bolt failure reaches 22%, which is beneficial to the large deformation of the surrounding rock in deep mines under strong disturbances. In some cases, a deep rock mass is extremely elastic and brittle, which makes the excavation of deep brittle hard rock unstable under the condition of minimal deformation. To address this situation, QIAO et al [76] developed an energy-absorbing rock-support device with high strength and small deformation using high damping rubber for burst-prone and squeezed surrounding rocks. Recently, to further improve the strength and prestress of the anchor rod, a prestressed steel bar anchor rod has been developed, and the tensile strength of the steel bar exceeds 1200 MPa [77].
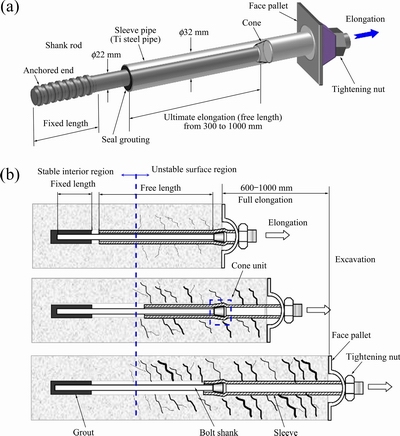
Fig. 3 A bolt with constant resistance and large elongation (a) and working principles (b) [72]
It is clear that relevant technologies and equipment for rock support are emerging one after another. Nevertheless, from the current situation, the protection effect of existing technologies and equipment on disasters occurring during mining, roadway excavation, and service is still not ideal, and disasters occur frequently due to support failure. Some support measures only alleviate the intensity of disasters to a certain extent but fail to cure disasters effectively. The fundamental reason is that most support materials cannot effectively absorb the deformation energy of the surrounding rock and resist the disturbance load induced by mining activities, which leads to the underground support facilities often being severely deformed and even destroyed when disasters occur, thus losing the bearing protection capacity. To adapt to the increasing requirements of the support system in deep mines, the support system should possess the function of safely controlling the whole process of disaster occurrence. Specifically, the functions of the support system should include at least two aspects. (1) The support system allows the surrounding rock to deform to a certain extent and can safely control its deformation speed, so that the energy accumulated in the surrounding rock can be released actively and the high-stress concentration level can be reduced, which is conducive to reducing the possibility of disasters or greatly reducing their intensity, thus preventing or controlling the occurrence of disasters. (2) When a disaster occurs, the support system can adapt to the large squeeze of surrounding rock through its energy absorption and yielding ability and can maintain a strong support resistance while controlling the safe release of deformation energy to minimize the damage caused by the disaster. In the future, the development of support techniques requires the research and development of new support materials with rapid energy absorption and impact resistance. Moreover, it is important to construct an engineering structure system that can effectively absorb energy in combination with the actual mining conditions.
In addition to pursuing the development of supporting materials, it is also very important to choose suitable support methods. Composite support techniques with bolts as the main body, such as bolt-grouting support, bolt-shotcreting support, and bolt-mesh-shotcreting support, are the main reinforcement techniques of rock strata in metal mines [78]. However, the effect of control and prevention in many mines is not good [18]. An important reason is that full-section support is not adopted. If only the surrounding rock at the top and two sides of the roadway is supported and reinforced but the bottom is not reinforced, a complete surrounding rock bearing ring will not be formed around the roadway, which greatly reduces the bearing capacity of the support structure. To realize full-section support, the bottom of the roadway should be reinforced with bottom arches and bolts, and the bolts around the roadway and bottom arch should be connected with steel mesh to form a complete bolt-mesh-shotcreting support retainer. This is necessary for deep mines with poor mechanical and strength conditions of the surrounding rock.
It should be noted that the instability and failure of the rock stratum in mining engineering are principally caused by rock mass damage and its strength deterioration. The fundamental purpose of the surrounding rock support is to improve the mechanical properties and strength of the rock mass, and the surrounding rock cannot be supported as a passive load. The most basic principle of rock mechanics is to give full play to the strength of surrounding rock to achieve stable mining engineering [79,80]. The guidance of this principle is particularly important for improving the stress distribution state of the surrounding rock, controlling the deformation and movement of the rock stratum, and maintaining the stability of mining engineering under the condition of high stress in a deep environment.
6 Deep hoistingtechnique
As mentioned earlier, with increasing mining depth, the existing hoisting techniques are facing great challenges. At present, there are two main ways to address the problems of deep lifting: friction lifting and winding lifting (Fig. 4). The hoisting height of a single rope winding hoisting machine is generally less than 1600 m, the hoisting capacity is small, and the speed is slow, so it is mostly used for hoisting tasks in early mine construction [33]. To ensure that the production capacity of lifting equipment increases with increasing depth, the load capacity of containers must be increased. Therefore, multi-rope hoisting equipment has been widely adopted [81]. A multi- rope friction hoist can be used for deep hoisting, and its hoisting capacity and efficiency are greatly improved compared with a single-rope winding hoist. For example, a four-rope friction hoist has been applied in the HuizeLead-Zinc Mine, China, with a lifting depth of 1526 m, and an eight-rope friction hoist has been employed in the Russian mining industry. However, with increasing hoisting height, the bearing capacity of steel wire rope of a multi-rope friction hoist decreases significantly, and there is an obvious tail rope problem. The multi-rope winding hoist solves the tail rope problem in deep hoisting and has been widely applied in gold mines in South Africa (such as the Gold Fields’ south deep gold mine), with a lifting depth of over 2000 m. However, the lifting capacity of the hoist is small and its efficiency is low, so it is difficult to meet the lifting requirements of ultradeep mining and high production at the same time [33].
In general, the deeper the hoisting, the more the ropes are required. After reaching a greater lifting height, both the friction hoist and winding hoist possess a series of problems caused by the lengthening and thickening of the steel wire rope. Moreover, increasing the load capacity of the skip of multi-rope hoisting equipment is restricted by the limited hoisting height, and the safety factor of the upper section of the steel wire rope will be lower than the allowable value of the equipment safety operation specification under the limited height. Given the limitations of traditional hoists, it is necessary to develop new devices and materials, such as large-capacity skips and steel wire ropes, for deep hoisting machinery to overcome the influence of those factors and improve the hoisting efficiency.
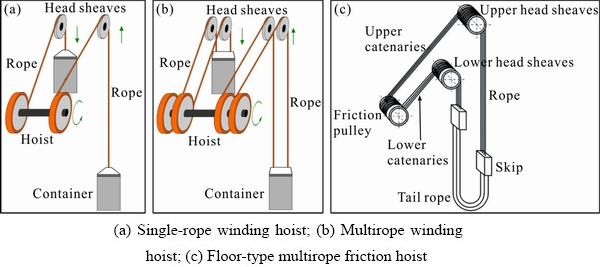
Fig. 4 Typical mine hoisting systems (after LIANG et al [33])
However, when the lifting height is greater than 3000 m or 4000 m, the heavy load, large inertia, and high torque induced by steel wire ropes in the rope lifting technique are unavoidable problems. Great difficulties will occur in the theory and practice of wire rope hoisting in mines, which leads to the denial of wire rope as the main load-bearing component, and shows that qualitative changes will occur in the field of mine hoisting. Thus, developing cordless vertical hoisting techniques, such as magnetic suspension-driven hoisting systems and linear motor-driven hoisting systems, is necessary. A schematic diagram of the vertical lifting of a bilateral permanent magnet linear synchronous motor is illustrated in Fig. 5 [4]. When a three-phase symmetrical current is introduced into the primary unit of the motor, a magnetic field is generated in the middle air gap.The air gap magnetic field is distributed sinusoidally along the straight line, and its peak value shifts with time, which is called the traveling wave magnetic field. Electromagnetic thrust is generated when the traveling wave magnetic field interacts with the magnetic field established by the permanent magnet. Under the action of this electromagnetic thrust, the cage moves up straight.
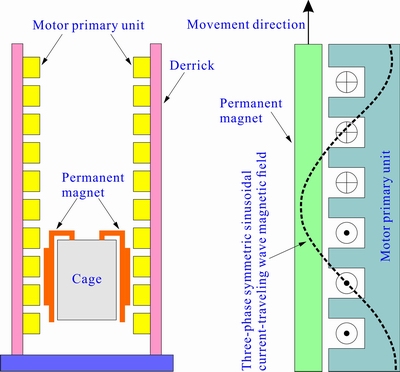
Fig. 5 Schematic diagram of bilateral permanent magnetic linear synchronous motor system [4]
Moreover, it is well known that maglev trains have been applied in many countries worldwide. Researchers are considering the method of using a magnetic field to control the lifting system. Because of the low friction, this kind of magnetic lifting system can not only run up and down quickly but also connect several elevator cars together to improve the lifting and transportation capacity. In addition, a magnetic lifting system has the advantages of low consumption, environmental protection, and safety and has broad application prospects. In this system, the linear motor is used to directly provide traction force for the cage to move vertically, and there is no tail rope in the whole system. Overall, the cordless vertical hoisting technique yields the advantages of flexible movement, high efficiency, and no limit on the hoisting height, and is suitable for hoisting in deep mines. Although research on cordless vertical hoisting systems is still in the primary stage or the early stage of industrial testing, this may be a development direction for deep hoisting techniques in the future.
In addition, the closed belt conveyor system (Fig. 6) applied in ground construction, smelting, and other industries rolls a belt into a closed tubular shape, thus wrapping bulk materials, which can realize the long-distance, large-drop, and high-efficiency continuous hoisting and transportation of materials [82]. Furthermore, the system has the advantages of simple structure, small occupied space, flexible turning, and low energy consumption. Thus, this system is expected to be applied to hoisting in deep mines in the future after proper improvements.
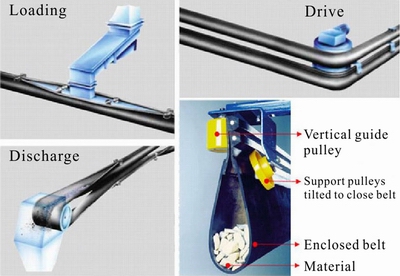
Fig. 6 A closed belt conveyor system [82]
In addition to mechanical lifting, hydraulic lifting is also a lifting technology with development potential. At present, hydraulic lifting is mainly used in deep-sea mining. In recent years, some researchers have tried to apply hydraulic lifting to deep mines (Fig. 7). A hydraulic lifting system combines the horizontal transportation technique of a high-concentration slurry in the roadway with the traditional vertical lifting technique of a low-concentration slurry. The ore is crushed and adjusted into a high-concentration slurry near the underground working faces, which is horizontally pumped to the shaft. The high-concentration slurry is continuously diluted by the high-pressure pump and then transported to the surface by the vertical pipeline of the shaft. After dehydration, the ore is sent to the concentrator. The transportation capacity of the pipeline is very large. A pipeline with a diameter of 100 mm can transport ore up to 500 kt per year [83]. When the mine drainage device is combined with the hydraulic lifting system, the cost of drainage, ventilation, and waste rock transportation can be greatly reduced compared with other lifting methods of conveying solids to the surface. This method of lifting roughly separates, crushes, and grinds the ore underground and then pumps it to the ground concentrator, which can reduce the lifting cost [84,85]. At the same time, the waste rock can be directly filled in the goaf. In addition, hydraulic lifting has a series of advantages in other aspects, such as strong adaptability to terrain, little interference from external conditions, and a high degree of automation. However, this method needs to establish an underground ore crushing and grinding system, and its practical application is still limited at present. In addition, after entering ultradeep mining, hydraulic lifting must be completed in multiple stages, as one stage of lifting is not acceptable.
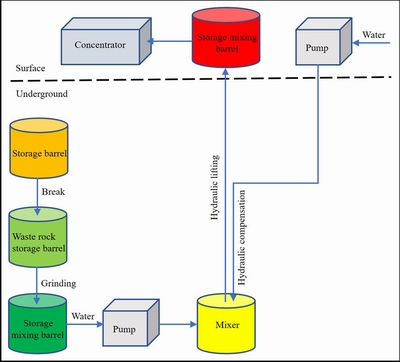
Fig. 7 Schematic diagram of hydraulic lifting
Additionally, the wind lifting technique has also been proposed to solve the problem of deep lifting[81,86]. After the lifted container is loaded from the bottom ore bin, the working mechanism (turbine blower) is started to deliver compressed air to the bottom of the container. When the unit pressure on the bottom area of the container reaches the rated value, the container starts to run to the wellhead and unloads ore to the mine bin after reaching the wellhead. After unloading, the container gradually descends under the action of self-weight and compresses the air cushion below it. The descending speed of the container is regulated by partially compressed air discharged from the lower space of the container. After the container descends to the bottom of the shaft, it is loaded with minerals again, and the next lifting cycle is repeated. The wind lifting technique has many theoretical advantages [81,86]. For example, the lifting height is practically unlimited, and the load capacity of containers is large, thus ensuring the required output of mines. The lifting structure is simple and compact, and there is no need to use components such as steel wire ropes, derricks, or lifting winches, so the basic investment in lifting equipment can be reduced. Because the wall of the shaft can be sealed by the floating type, the efficiency of the lifting equipment can be greatly improved, the wear of the sealing device can be greatly reduced, and the construction of the shaft can be simplified. More importantly, the technology is safe to operate and has less air leakage. However, this technique has not been successfully applied to mine lifting works.
The abovementioned new techniques, methods and processes have brought new ideas to hoisting and transportation in deep mines and greatly promoted the innovation of the deep hoisting technique. Notably, for deep mines, regardless of what kind of hoisting techniques and processes are developed, lightweight, heavy-load, high-performance, and highly automated lifting equipment is the general tendency in the future.
7 Nontraditional deep mining techniques
7.1 Precise-cutting mining
The traditional method of rock breaking in metal mine excavation is drilling and blasting. This technology can cause great damage to the stability of the surrounding rock and threaten mining safety. Moreover, ore and waste rock are mined together, which greatly increases the amount of waste rock and the workload of mineral processing operations. To improve the levels of automatic, precise, and efficient mining in deep mines, it is necessary to develop a method for precise cutting mining. This requires great efforts in the following aspects.
7.1.1 Mechanical continuous-cutting tunneling and mining technology
As a long-term goal, it is important to adopt the methods of mechanical tunneling and mechanical rock drilling and replace traditional blasting technology with continuous cutting equipment. According to different rock-breaking tools and principles, the current high-efficiency mechanical rock-breaking methods include cutting rock-breaking, impact rock-breaking, and impact or vibration cutting rock-breaking. The use of mechanical equipment for direct excavation and mining can accurately mine the target ore, implement precise mining, and minimize the mining loss rate and ore dilution rate, thus greatly reducing the lifting workload and the operation amount of mineral processing. Cutting, ore dropping, loading, and transportation are conducted in parallel and continuously, which is conducive to realizing continuous mining. In addition, mechanical cutting can achieve high production capacity and improve working environments, creating favorable conditions for ensuring mining safety. Mechanized continuous mining has been realized in most coal mines and some soft rock mines. However, for metal mines, the operation of mining machines is largely affected by the changeable shape of the metal deposit, the limitation of complex geological conditions, and the life and cost of the cutting head. These are the keys to determining whether this technology can be successfully implemented in metal mines.
LI et al [87] suggested that the realization of nonexplosive continuous mining in hard rock mines needs to meet two necessary conditions: high-efficiency mining equipment and developed rock mass joints. In deep mining, the phenomenon of “easy drilling and easy blasting” in hard ore and rock provides enlightenment, which should be caused by high stress. A large amount of energy is stored in deep hard rock under high-stress conditions. Mining excavation causes the change, transfer, and redistribution of stored energy, which intensifies the generation and propagation of cracks in the rock. Hence, the energy implied by high stress is beneficial to the fracturing and crushing of extremely hard ore and rock under appropriate induction engineering, so a high stress-induced crushing method can be created to realize high stress-induced fragmentation and nonblasting continuous mining [82,87,88]. This technical concept has been preliminarily tested in the KaiyangPhosphate Mine, China, and the results show that it can improve the machinability and mining efficiency of deep hard rock. High stress-induced fragmentation and nonblasting continuous mining technology is a new subject for hard rock metal mining, and there are still many aspects to be explored [9], such as the characterization and understanding methods of high-stress fields and geological structures in deep mining, the knowledge of whole block fracturing of hard rock under high stress, and the support measures suitable for this technology.
7.1.2 Nonmechanical rock-breaking tunneling and mining technology
Nonmechanical rock breaking refers to the way that rock breaks under hydraulic power, thermal power, magnetic field force, and laser power, which fundamentally changes the conventional rock breaking method. At present, the most representative rock-breaking methods are high-pressure water jet, particle jet, plasma, electron beam, laser, and ultrasonic rock breaking technologies, which are briefly introduced as follows.
(1) A high-pressure water jet is a high-speed jet that takes water as the energy carrier and converts the mechanical energy of the motor into the kinetic energy of water through a liquid booster and a specific nozzle, which can be used to cut and break rocks. This technology can cut rocks with compressive strengths of 60-120 MPa. At present, rock breaking with high-pressure water jets has been realized in soft rock and medium hard rock engineering and is widely used in coal mines. However, when crushing hard ore and rock, it is necessary to use a higher water jet pressure, which will reduce the reliability and life of the jet launcher system. The insufficient water jet pressure makes it difficult to break hard rocks in large areas, so its application in metal mines is limited. To solve the problem of rock breaking in hard rock, a high-pressure water jet needs to develop toward an ultrahigh pressure and high power.
(2) Particle jet rock-breaking technology injects a proper proportion of high-hardness and high-abrasiveness particles into drilling through a particle injection system. The particles reach the particle impact drilling bit through the drill string and are ejected from the nozzle of the drilling bit at a high speed to form a high-speed particle jet [89]. The high-speed particle jet impacts and breaks the rock, which produces a series of impact cracks on the rock surface. After cracks are generated, the strength of the rock decreases rapidly. Subsequently, drill bits can easily break the rock by mechanical action, resulting in large pieces of broken rocks. However, the ground equipment and drill bit need to be further improved and perfected, and research on the process parameters of the particle jet and the impact process and mechanism of particle rock breaking is still lacking.
(3) In the mid-1960s, the technology of plasma cutting metal was introduced into rock breaking. A conventional DC voltage is applied between the cathode and anode of the plasma gun, which can be excited by a high-frequency electric spark or short-circuit of carbon particles to produce an arc [90]. Under the action of a high-temperature and high-speed plasma arc, the thermal stress generated exceeds the strength limit of rock and breaks it. Plasma rock breaking is based on the stress state produced in the rock under the action of the plasma arc.
(4) Electrons gain kinetic energy under the action of a strong electric field and form directional high-speed electron beams after focusing in a vacuum, which can be used to break rocks. At present, an electron beam rock-breaking device with a power of 150 kW has been developed [91]. Under the action of an electron beam, rock is separated from the host rock mass in the form of melting and vaporization, so the heating effect on rock is not affected by the type and hardness of rock. Compared with other rock breaking methods, electron beam rock breaking has a higher power density and energy conversion rate (up to 75%).
(5) Since the 1960s, many countries have carried out research work on rock breaking by lasers. Laser rock breaking uses the heat generated by a high-energy laser beam to heat the rock locally and rapidly. When the thermal stress is higher than the ultimate strength of rock, the rock will be thermally broken, and the rock will be cut and broken. Microcracks and pores on the rock surface reduce its ultimate strength, which will promote the cutting effect of thermal crushing. By using the high-energy focused radiation emitted by the laser, deep and thin slits can be cut into various hard rocks. When tunneling hard rock roadways, the laser cutter is economically superior to the mechanical method. Laser rock breaking technology is cutting-edge technology, and its development prospects are broad.
(6) Ultrasonic rock-breaking technology is a new rock-breaking technology derived from ultrasonic machining that has the characteristics of high vibration frequency (up to 20 kHz) [92,93]. The use of ultrasonic technology can realize the high frequency and low amplitude axial vibration of the drill bit, thus achieving the purpose of rock breaking. When the frequency of an ultrasonic wave is the same as the natural frequency of rock, resonance will occur. In this case, the vibration displacement of rock is the largest, and the rock is easily broken.
Given the difficulty and high development cost of deep metal mineral resources, the quality and efficiency of rock breaking should be improved. Most of these nonmechanical rock breaking technologies have higher requirements for equipment and are still in the stage of experimental exploration, which is far from industrial application. It can be predicted that through theinnovations in material science and engineering design and the development of mining technology, mechanical rock breaking and its combination with nonmechanical rock breaking technology will gradually become the leading method of rock breaking in metal mines in the future, especially mechanical rock breaking technology, which will be widely applied. The implementation of these technologies can greatly improve the working environment and reduce the impact and damage of traditional blasting on the surrounding rock and environment.
7.2 Filling mining
At present, metal mines determine applicable mining methods largely depending on the ore value and difficulty of goaf maintenance. Gold mines and some nonferrous metal mines with high ore values are mostly mined using the filling method. For other mines with low ore values, such as iron ore, the filling method is not the first choice. However, to realize green mining, control strata movement and surface subsidence, especially to control violent ground pressure activities in deep mines and avoid various disasters and accidents caused by instability and failure of roadways and stopes, filling mining is gradually becoming the main method for the underground mining of various metal mines, including iron mines. This method uses an ancient technology of backfilling mined-out areas with filling materials (Fig. 8) [94], which aims to maintain the stability of mined-out areas and solve the environmental problems caused by the surface stacking of mine wastes from the source. In recent decades, the innovative development of filling technology and equipment has made this method look brand-new, which is of great significance in promoting the reform of metal mining modes, ensuring production safety, improving resource recovery rates, protecting the ecological environment, and building a harmonious mining area.
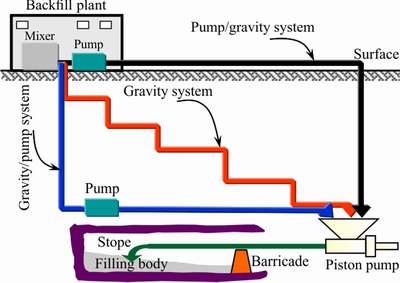
Fig. 8 Illustration of mine filling system (after BELEM and BENZAAZOUA[94])
The filling technologies commonly used in the world roughly include hydraulic stowing filling, dry filling, high-water-solidifying filling, and cemented filling. Among them, cemented filling is widely adopted in many metal mines worldwide, especially in China, because of its excellent performance in ensuring mine safety and improving ore recovery. Since the 1930s, sand has been widely used as a filling material in underground mines in Canada. In 1992, paste filling technology was first applied in the CreightionMine in Canada [95]. At present, at least 12 mines in Canada have used high-concentration paste to fill the goaf. The RammelsbergLead-Zinc Mine in Germany utilized the downward slicing cemented filling mining method combined with wind filling to recover high-grade lead-zinc-copper ore, using a mixture of crushed stone and blast furnace slag cement as the filling material. Cemented filling technology has been applied in many mines in South Africa, and new paste filling systems have been put into operation. Underground nonferrous metal mines such as Cannington and Mount Isa silver-lead-zinc mines in Australia are mined by the filling method. In addition, China has also made great progress in the research and development and engineering application of new filling technology. The No.2 mining area of the JinchuanNickel Mine is the first mine in China to adopt high-concentration cemented filling, and this filling technology is combined with large trackless equipment, which greatly improves the production capacity [96]. The length of the paste filling pipeline in the HuizeLead-Zinc Mine has gradually increased from 4000 m to over 7000 m, and the automation of paste preparation and transportation has been realized [97]. High slicing and filling mining technology was developed in the FankouLead-Zinc Mine and was applied to ore recovery under high stress and inclined refractory mining conditions. Moreover, China has built the world’s first industrial-grade paste filling test platform, which can carry out experiments and parameter detection on the whole process of paste filling and guide system design and engineering practice [78]. Especially for multidiameter, multidirection, and multiflow loop experimental systems, the test results are closer to the actual situation than the traditional methods. These achievements show that cemented filling technology has made outstanding contributions to the development of the metal mining industry.
However, we should be soberly aware that cemented filling technology is still facing severe challenges in deep resource exploitation. According to YU[97], four critical issues remain for deep mining: (1) the method of maintaining the stable concentration of cemented filling slurry, (2) the process of reasonably controlling the residual pressure head and keeping the filling system always transported in the full pipe, (3) the super large-scale filling technology, and (4) the tailings recycling technology. Moreover, the wear-resistant and corrosion-resistant methods of filling equipment, the intelligent control system of filling equipment, and the theory of efficient transportation of filling materials in a deep environment are also the basic key scientific problems that need to be extensively studied and solved.
On the other hand, the filling cost is high, and paste filling accounts for approximately 20% of the total mining cost, which seriously restricts the application and popularization of the filling mining method. Therefore, it is necessary to reform the filling technology and materials and to reduce the filling cost. The filling process using mine solid waste is the most promising technical solution. The cemented filling technology with high-concentration tailings was successfully tested in the FankouLead-Zinc Mine in China in the early 1990s, and it has been widely popularized and applied. On this basis, the full tailings paste filling technology developed in recent years can obtain a high-quality filling body under the condition of low cement consumption, uniform paste strength and a high tight-filling ratio of goafs, which can effectively control the ground pressure activity and strata movement. This represents the future development direction of filling mining technology in deep metal mines. For example, Jinchuan Company of China adopted paste filling technology to prepare a paste with a concentration of 81%-83% using Gobi crushed stone aggregate, whole tailings, and cement, and the compressive strength of the filling body reached over 40 MPa [98]. This technology should be further studied to create conditions for wide popularization and application. However, cementitious materials account for a large proportion of paste filling costs. According to statistics, cement accounts for 60%-80% of the cost of cemented filling materials [99], so an important way to reduce the cost of cemented filling is to find cement substitutes to reduce cement consumption. The study of new ultrafine, high-strength, low-price, and quick-setting filling materials can effectively reduce the filling cost. Among them, adding admixture is an effective way to improve the fluidity and mechanical properties of the filling body, and filling admixtures (such as pumping agents, flocculants, early strength agents) need to be further studied.
7.3 Wasteless mining
Wasteless mining is a direction for the comprehensive utilization of useful minerals and for the protection of the environment against pollution, which means the maximal extraction of all valuable components from mineral raw materials, with minimal emission or complete absence of wastes in the form of solid, liquid, and gas. Traditional mining technology can produce considerable waste while obtaining mineral resources. After long-term accumulation, these wastes will not only destroy the vegetation and farmland on the surface but also significantly increase the load on the surface environment. Due to the requirements of environmental protection and sustainable development and the need to improve the economic benefits of mining enterprises, wasteless mining has attracted increasing attention in recent years. Wasteless mining is a technology that minimizes the output and emission of waste, improves the comprehensive utilization rate of mineral resources, and reduces or eliminates the negative impacts of resource development. The wasteless mining mode of mineral resources should not only consider economic benefits but also pay attention to social benefits and ecological environmental benefits to realize the sustainable development of mineral resources.
To realize wasteless mining, a mining method with a small mining-cutting ratio should be adopted first, the ore dilution rate should be greatly reduced, the waste output should be minimized, and the waste rock output rate should be controlled from the source. At the same time, it is necessary to improve the technical level of mineral processing, the recovery rate of mineral processing, the comprehensive utilization degree, and the utilization rate of resources as much as possible and reduce the discharge of tailings. More importantly, innovative beneficial technology and equipment should be developed to minimize the unusable components in ore resources due to the low level of benefit and metallurgy. In addition, it is necessary to introduce waterless process flow, adopt the process flow with the least water consumption, select the production complex where water is continuously used many times, develop a circulating water system to the maximum extent, locally clean the wastewater by recovering valuable components, improve the existing wastewater cleaning methods and develop new methods, thus creating a sewage-free technology.
On the other hand, building a concentrator underground and conveying concentrate directly to the ground after underground beneficiation can greatly reduce the lifting amount of waste rock. This is an important way to solve the problem of deep hoisting. At the same time, waste rock, tailings, and other mining wastes are left underground for goaf filling to realize in situ effective utilization. This method fundamentally eliminates the influence of goafs on the surface and reduces pollution and destruction to the ecological environment, which is an important means to realize wasteless mining. Moreover, there is no concentrator or tailing pond on the surface, which saves the cost of land acquisition, construction, and management of tailing ponds and plays a multipurpose role.
In addition, nonferrous metal deposits are mostly polymetallic deposits, which are symbiotic and associated with many kinds of useful minerals. Hence, comprehensive recovery should be strengthened to realize the recycling of wastes, improve the overall utilization level of wastes, and strive to achieve zero discharge and zero storage of mine solid waste. For example, the QixiashanLead-Zinc-Silver Mine in China introduced wasteless mining technology and basically realized the resource utilization of all tailings and zero discharge of mine waste rock by adopting a new flotation process, wastewater purification treatment technology, and solid waste backfilling goaf technology, and achieved satisfactory results [100]. A waste rock filling system was established in the HongtoushanCopper Mine in 1995, and all the waste rocks were filled into the underground mined-out area in 2012 after multistage improvement, which achieved good economic and social benefits [101]. These examples provide good suggestions for similar mines worldwide. The successful development of wasteless mining technology is related to the development of technical methods for extracting low-concentration components from solid and liquid mixtures, the development of methods for recycling waste by processing waste into a marketable state, and the optimization of wasteless technical schemes, with taking into account ecological requirements. Hence, wasteless mining technology is an organic synthesis of various harmless technologies throughout the production process. Notably, due to the uneven distribution of mineral resources and the different mining techniques of different mines, the planning and design in the practice of wasteless mining should be combined with the actual situation of each mine.
7.4 Solution mining
Solution mining is a flexible and constantly developing mineral processing and extraction technique that uses chemical solvents or microorganisms to react with the target minerals in physical, chemical, and biological ways to selectively dissolve, leach, and recover the useful components in deposits, ores, or waste rocks, primarily including three types: surface heap leaching, in situ crushing leaching, and in situ drilling leaching [102]. Surface heap leaching accumulates mined ore on the ground as required, sprays the leaching solution from the upper part of the heap and collects the rich solution from the bottom. In situ crushing leaching involves spraying leaching solution on the upper middle section after blasting and crushing the ore block and collecting rich solution in the lower middle section. In situ drilling leaching involves injecting leaching solution into underground ore bodies through drilling holes, selectively leaching valuable components, generating soluble ions into the solution, and then pumping the solution out to the workshop to recover valuable metals. According to the conditions of the target ore body, these three methods can be flexibly selected.
As a low-cost, high-efficiency, and green mining technology, solution mining is gaining popularity and recognition from mining enterprises and has been widely used in the recovery of low-grade and complex polymetallic deposits in the United States, Australia, South Africa, Canada, India, China, and other countries. In the 1960s, the United States began to leach uranium ore in situ by acid leaching and built the world’s first in situ leaching uranium mine in Wyoming [103]. Moreover, there are more than 20 mines in the United States that use in situ blasting to leach copper, and the leached copper output accounts for more than 20% of the total output. The uranium metal output from heap leaching and in situ blasting leaching in the Ural mining area of Russia accounts for 40%-50% of the total output. In 1970, China began to test in situ drilling leaching in uranium mines, which was officially applied industrially in 1991. Since the 1990s, heap leaching has been applied in many gold and copper mines in China. In 1997, China’s first large-scale industrial heap leaching site was built in the DexingCopper Mine, with an annual output of 2000 t of electrodeposited copper [104]. In 2005, the first 10000 t bioleaching copper mine was built in the ZijinshanGold-Copper Mine. Furthermore, surface heap leaching was adopted in the ZijinshanGold Mine to recover gold from low-grade ore, with great scale and benefit, reaching the world’s leading level. In addition, in situ crushing leaching has been employed in the Dongxiang and Zhongtiaoshan copper mines to recover copper [105,106]. In particular, approximately 150 major gold-silver mines worldwide utilized surface heap leaching technology and recovered approximately 15 million troy ounces of gold in 2014 [1]. Under the background of continuous efforts to improve recovery efficiency, solution mining technology has emerged as a breakthrough method experiencing amazing growth in recent decades.
Solution mining is an integrated technology of mining, beneficiation, and metallurgy that can directly recover metals from ore bodies by leaching solutions, greatly reduce the workload of mining and processing operations and production costs, and provide an economical and feasible way to recover of metal mineral resources that are currently considered abandoned or uneconomic, such as low-grade deposits, tailings, and waste stockpiles. No waste rocks or tailings are produced, there is no excavation disturbance, there is little influence on the ground environment, and there are low energy and water requirements. This is also one of the main initiatives used to realize wasteless mining. Furthermore, solution mining possesses strong advantages over traditional metallurgical technologies, where economically feasible options have become limited. In recent years, with increasing mining depth, deep rock masses have become highly dense, especially for deep metal mining below 2000 m, and existing traditional in situ crushing leaching will become obsolete [106]. Deep in situ drilling leaching technology, with its advantages of high efficiency, unmanned implementation, and green technology, will become an important development technique for deep mining in the future and has wide application prospects.
Solution mining technology is a sophisticated process and is also a marginal interdisciplinary subject, and its basic theory is still very weak at present. Further theoretical research is needed in the aspects of granular seepage dynamics, cultivation of highly efficient strains, and strong correlation mechanism of multiple factors in the leaching process, which helps to gain insight into technical problems such as the use of highly efficient strains, the amelioration of the uniformity of the leaching field, and the improvement of the ability to manually control the leaching temperature field and concentration field, thus solving the problems of a long leaching cycle and low leaching rate in this technology [102]. In particular, at present, this process can only effectively recover rare metal minerals such as uranium, copper, and gold, so it is necessary to study the leaching process and recovery technology of more metal minerals to make it the main mining method for mineral resource recovery. It is highly hoped that recent developments will also allow the use of solution mining technology to treat primary sulfide ores. This would lead to a rapid expansion of this technology because approximately 80% of ore types are sulfide in nature. In addition, it is important to note that the current solution mining technology still has some shortcomings, such as the difficulty in controlling leaching liquid during in situ leaching mining, which leads to underground environmental pollution and resource loss [107]. Bioleaching technology also has some hidden dangers in ecological protection, biodiversity disturbance, the stability of ore heaps and so on [108]. All these problems need further attention.
7.5 Intelligent unmanned mining
Informatization, automation and intelligence, the three core technologies of modern engineering science and technology, are important driving forces to promote the transformation of traditional industries such as the mining industry. Intelligent unmanned mining is a mining process with the characteristics of a digitalized mining environment, intelligent mining equipment, remote control production process, networked information transmission, and information management that aims to achieve safe, efficient, green, and sustainable development of mineral resources, which is the most fundamental, effective, and reliable method to cope with deteriorating deep mining conditions and environmental conditions.
In the 1960s, Sweden, Finland, Australia, Canada, South Africa, and other countries began to study automatic, digital and intelligent mining technology. To gain a competitive advantage in the mining industry, the “intelligent mine” and “unmanned mine” development plans were formulated successively. In the 1980s, fully automatic and remote-controlled trackless mining equipment was applied in the Kiruna Iron Mine in Sweden. In this mine, automatic unmanned operation has been realized in rock drilling and shipping in the underground stope, and unmanned driving has been realized in underground rock drilling jumbos, scrapers, and electric transport locomotives. In the mid-1980s, the Noranda Technology Center of Canada developed a variety of automation equipment, including optical navigation systems of scrapers and trucks, automatic walking systems, remote auxiliary loading systems of scrapers, etc, which were used for the remote automation of unmanned mining operations [109]. In 1994, the Australian Commonwealth Scientific and Industrial Research Organization (CSIRO) initiated a research project of a mining robot and developed the load-haul-dump (LHD) automatic control system of underground metal mines.
At the beginning of the 21st century, China introduced foreign automatic mining equipment and carried out the development of mine automatic control systems and digital mine construction. Typically, the XingshanIron Mine in China has basically achieved automatic control of the whole mining operation process and realized underground remote control unmanned driving, automatic ore loading and unloading, and remote-control automatic operation of medium-deep hole rock drilling jumbos. The SanshandaoGold Mine has built information systems such as an information integrated service platform, integrated safety management system, and geological reserve management system, which have realized the effective management of geological reserves, mining processes, site safety, production information, and implementation statistics. Moreover, an intelligent mining system was established in the FankouLead-Zinc Mine (Fig. 9), and the corresponding underground intelligent mining integrated equipment, including the centralized control, high-speed communication,automatic driving and intelligent operation of scrapers, mining trucks, rock jumbos, and down-the-hole drilling rigs, was tested [110]. The site test results showed that the intelligent mining system has excellent performance and can adapt to the mining environment of the mine.
Currently, with the progress of science and technology, an increasing number of frontier information techniques, such as 5G, big data, artificial intelligence, the Internet of Things, and unmanned aerial vehicle techniques, are being deeply integrated with mining technologies and applied to mines to achieve intelligent unmanned mining. As a consequence, intelligent unmanned mining not only improves the effectiveness of mining equipment and intelligent monitoring of the mining process, but also significantly improves mining efficiency, thus reducing mining costs and improving the competitiveness of mining enterprises. Meanwhile, intelligent unmanned mining can reduce the number of field operations and disaster risks and is an effective way to realize the cleaner production and sustainable development of deep metal mines.
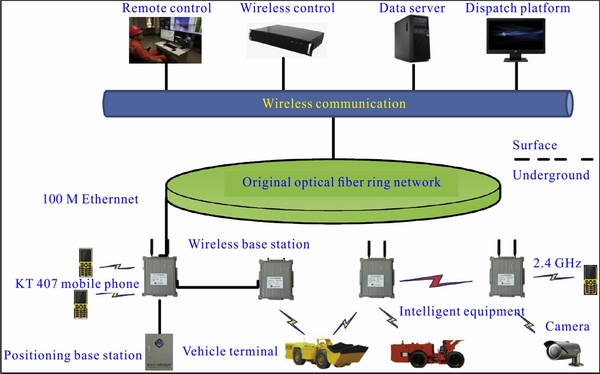
Fig. 9 Intelligent mining system established in FankouLead-Zinc Mine, China [110]
Great progress has been made in the construction of intelligent unmanned mining worldwide. Despite these positive achievements, the task of construction is still quite arduous. Obviously, compared with the total number of mines worldwide, the number of intelligent mines that have been built is too small. In addition, the innovation of intelligent mining technology depends on the innovation of mining equipment to a great extent. However, the mining equipment of some small and medium-sized metal mines in some countries, especially in China, is still relatively backward. The high price of advanced equipment restricts the upgrading of mining equipment and the popularization and application of advanced mining technology in these mines. In general, the construction of intelligent unmanned mines is still in the primary stage, and the core technique of intelligent unmanned mining at this stage is still the automation and intelligent control of traditional mining techniques and production organization and management, which is mainly realized by field or remote control. The equipment and control system of intelligent unmanned mining in the advanced stage should have the functions of intelligent target recognition and perception, independent memory, independent judgment, and independent decision-making, similar to an intelligent brain but without external remote control. To realize the transition from the primary stage to the advanced stage of unmanned mining, it is absolutely necessary to develop and innovate a series of disruptive new mining technologies and methods.
Intelligent unmanned mine construction is a complex system engineering involving modern information, automatic control, visualization, and virtual reality technology, as well as mining, geology, surveying and mapping, system engineering, and other disciplines, which can promote intelligent mine production, management, and decision-making processes [9,11]. The new task of intelligent mine construction is to build the mine Internet of Things and access the digital integration platform in real time and establish a multidimensional and dynamic mine virtual reality system to provide comprehensive, real-time, and accurate information guarantees and intelligent services for unmanned mining [111]. Metal mining has the characteristics of complex process, scattered operation, hard rock, and changeable occurrence. Under the new situation of deep mining, intelligent unmanned mining needs to realize ambient intelligence perception, intelligent operation in the mining process, and intelligent management and control of mining systems. In this regard, seven key technologies are addressed: (1) digital mine integration platforms, (2) virtual reality and visualization technology, (3) advanced sensing and detection monitoring technology, (4) high-speed digital communication network technology, (5) remote control and intelligent technology of mining equipment, (6) underground trackless navigation and control technology, and (7) new automatic mining technology.
7.6 Fluidized mining
XIE et al [112-114] noted that in theory, traditional mining technology has an extreme mining depth. According to the measured results of in situ stress in more than 30 countries around the world, combined with rock mechanics experiments and mechanical theory analysis, a rock mass with a depth of 6000 m is basically in a three-dimensional isobaric state, and the deep rock mass enters a full-range plastic rheological state [5]. When the depth exceeds 6000 m, rock movement, surrounding rock support, and disaster early warning and prevention will be difficult to control, and all the currently available metal mining methods will fail. Thus, to realize the effective exploitation of deep underground metal mineral resources in the future, it will be necessary to supplant the existing mining theory and technology. To address this issue, XIE et al [112-114] proposed a theoretical and technical conception of the fluidized mining of deep mineral resources, taking the mining mode similar to TBM operation as the forerunner, realizing in situ, real-time, and integrated development of deep mineral resources through the mining, sorting, refining, and backfilling of resources. For the exploitation of deep metal mineral resources, the fluidized mining concept includes the following three main procedures [112,113]: (1) unmanned mining, (2) fluidized conversion of mineral resources, and (3) controlled backfilling.
In situ conversion is the most important link in fluidized mining, involves a complex conversion process and is the key to realizing the fundamental conversion of deep metal ore from solid development to fluid development. According to different in situ conversion methods, WU et al [106] further divided the in situ fluidized mining of deep metal ore into two fields: the in situ solution mining of deep metal ore and the integration of mining, refining, and backfilling. The latter includes two modes (Fig. 10): one is to directly build the concentrator and filling station deep underground to form a mining-refining-backfilling system (Fig. 10(a)); the other is a TBM-like development mode, i.e., a TBM conversion shield chamber, which consists of a mining chamber, a refining chamber, and a backfilling chamber (Fig. 10(b)).
Fluidized mining is indeed a disruptivetechnology that changes the traditional mining mode of bulk materials of raw ore, converts deep metal mineral resources into liquid or solid-liquid mixed substances in situ, and realizes the unmanned intelligent mining of deep metal mineral resources underground. Fluidized mining of deep metal mineral resources can solve a series of problems, such as low production efficiency, poor safety, serious ecological damage, low resource recovery rate, and large energy loss of ground transportation/conversion, and realize fundamental changes in the mining mode of metal mineral resources. This new method will lead to the development of mining technology and help to realize safe, clean, efficient, and green deep underground mining. However, the application of fluidized mining in the underground mining of metal mines is only a theoretical conception at present. To achieve this goal, many major problems, in theory, technology, and equipment, need to be overcome [106,112], such as the rock mechanics theory under fluidized mining, the fluidized conversion process of metal mineral resources, the fluidized conversion mechanism and control method, complex terrain space navigation and positioning technology, high-precision directional tunneling equipment, mining process support technology, high-efficiency automatic support complete sets of equipment, long-distance high-speed and high-reliability communication technology, and underground hazard source monitoring technology. In particular, integrating mining, refining, and backfilling equipment involves many mining processes and complex functions, which is a comprehensive integration of multiple technologies, and its research and development are unprecedentedly difficult.
8 Concluding remarks
The mining industry is an indemnificatory industry for the development of human society and the economy. With the increasing world population, mineral raw materials are being used at an increasing speed, resulting in the continuousadvancement of the exploitation of underground metal mineral resources to a deeper level. However, due to the special geological conditions of deep strata, deep mining faces a series of theoretical and technical challenges. These challenges are caused by many factors, such as high stress and mining-induced stress, with the dynamic responses of rock mass to these stresses and corresponding support requirements; high temperature and related ventilation and cooling measures; methods and costs of processing the mined ore and transporting it to the surface; complex and difficult mining conditions that are often encountered; green mining mode in response to environmental requirements; and the desirability of developing nonentry methods of mining. To address these challenges, it is necessary to extensively absorb high-tech data from various disciplines and develop advanced and nontraditional novel mining theories, technologies, and processes.
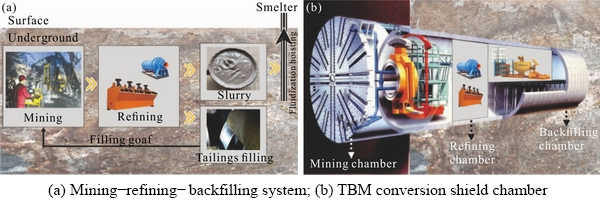
Fig. 10 Conceptual map showing fluidized mining for deep underground mineral resources [106]
This paper reviews the current global status of the deep mining of metal mineral resources, outlines the major engineering and technical problems faced by deep mining, and highlights the key engineering and technical development strategy suggestions to address the deep mining problems from the aspects of prediction and prevention of mining dynamic disasters, control and treatment of high-temperature heat hazard, rock support, deep hoisting, and the reform of traditional mining methods and techniques. The nontraditional deep mining techniques include precise cutting mining, filling mining, wasteless mining, solution mining, intelligent unmanned mining, and fluidized mining. The integration of forward-looking key innovative technologies in the above aspects will form the overall framework of an innovative technology system for the deep mining of metal mines. In this technical framework, intelligent unmanned mining is the most effective way to address and solve those problems, and fluidized mining is a disruptive innovation for future deep mining. In summary, a green intelligent mining mode with higher efficiency, lower cost, minimal environmental pollution, and the highest safety conditions should be established to improve the output and production efficiency of metal mineral products, thus ensuring the safe supply of deep metal mineral resources and the sustainable development of the metal mining industry.
Acknowledgments
The authors are grateful for the financial supports fromthe Fundamental Research Funds for the Central Universities, China(No. FRF-TP-20-041A1), the National Natural Science Foundation of China(Nos. U2034206, 52074020)
References
[1] BASOV V. Heap leach: Mining’s breakthrough technology 2015 [EB/OL]. https://www.mining.com/heap-leach-minings-break-through-technology/. [2015-08-20]
[2] CAI MF, BROWN ET. Challenges in the mining and utilization of deep mineral resources[J]. Engineering, 2017(3): 432-433.
[3] CAI MF, LI P, TAN WH, REN FH. Key engineering technologies to achieve green, intelligent, and sustainable development of deep metal mines in China[J]. Engineering, 2021. https://doi.org/10.1016/j.eng.2021.07.010.
[4] CAI MF, XUE DL, REN FH. Current status and development strategy of metal mines[J]. Chinese Journal of Engineering, 2019, 41(4): 417-426. (in Chinese)
[5] XIE HP, GAO F, JU Y. Research and development of rock mechanics in deep ground engineering[J]. Chinese Journal of Rock Mechanics and Engineering, 2015, 34(11): 2161-2178. (in Chinese)
[6] STACHULAK JS, HENSEL V. Successful application of DPF system at Vale Inco’s Creighton mine[C]//Proceedings of 13th US/North American Mine Ventilation Symposium, 2010: 13-17.
[7] ZHAO SC. Resources exploitation and underground engineering under high in-situ stress: Xiangshan Conference for the 175th Time[J]. Advance in Earth Sciences, 2002, 17(2): 295-298. (in Chinese)
[8] XIE HP. Research framework and anticipated results of deep rock mechanics and mining theory[J]. Advanced Engineering Sciences, 2017, 49(2): 1-16. (in Chinese)
[9] RANJITH PG, ZHAO J, JU M, de SILVA RVS, RATHNAWEERA TD, BANDARA AKMS. Opportunities and challenges in deep mining: A brief review[J]. Engineering, 2017(3): 546-551.
[10] MALAN DF. Time-dependent behaviour of deep level tabular excavations in hard rock[J]. Rock Mechanics and Rock Engineering, 1999, 32: 123-155.
[11] HE MC, XIE HP, PENG SP, JIANG YD. Study on rock mechanics in deep mining engineering[J]. Chinese Journal of Rock Mechanics and Engineering, 2005, 24(16): 2803-2813. (in Chinese)
[12] ZHENG D, FROST JD, HUANG RQ, LIU FZ. Failure process and modes of rockfall induced by underground mining: A case study of KaiyangPhosphorite Mine rockfalls[J]. Engineering Geology, 2015, 197: 145-157.
[13] LI P, WU YQ, ZHANG Y. Mechanical and acoustic responses of brittle geomaterials with a hole under a compressive disturbance[J]. Advances in Materials Science and Engineering, 2021, 2021: 5292925.
[14] LI P, CAI MF. Energy evolution mechanism and failure criteria of jointed surrounding rock under uniaxial compression[J]. Journal of Central South University, 2021, 28(6): 1857-1874.
[15] LI P, CAI MF, WANG PT, GUO QF, MIAO SJ, REN FH. Mechanical properties and energy evolution of jointed rock specimens containing an opening under uniaxial loading[J]. International Journal of Minerals, Metallurgy and Materials, 2021, 28(12): 1875-1886.
[16] CAI MF. Application of rock mechanics in mining engineering in metal mines[J]. Metal Mine, 2006(1): 28-33. (in Chinese)
[17] LI XB, YAO JR, GONG FQ. Dynamic problems in deep exploitation of hard rock metal mines[J]. The Chinese Journal of Nonferrous Metals, 2011, 21(10): 2551-2563. (in Chinese)
[18] CAI MF. Key theories and technonogies for surrounding rock stability and ground control in deep mining[J]. Journal of Mining and Strata Control Engineering, 2020, 2(3): 5-13. (in Chinese)
[19] LI P, WU Y, CAI MF. Implications of in-situ stress measurement in mining engineering[C]//IOP Conference Series: Earth and Environmental Science. IOP Publishing, 2021, 833(1): 12140.
[20] LI P, MIAO SJ. Analysis and application of in-situ stress in metal mining area of Chinese mainland[J]. Chinese Journal of Engineering, 2017, 39(3): 323-334. (in Chinese)
[21] LI P, CAI MF, GUO QF, MIAO SJ. Characteristics and implications of stress state in a gold mine in Ludong area, China[J]. International Journal of Minerals, Metallurgy and Materials, 2018, 25(12): 1363-1372.
[22] LI P, CAI MF, GUO QF, MIAO SJ. In situ stress state of the northwest region of the Jiaodong Peninsula, China from overcoring stress measurements in three gold mines[J]. Rock Mechanics and Rock Engineering, 2019, 52: 4497-4507.
[23] HE MC, GUO PY. Deep rock mass thermodynamic effect and temperature control measures[J]. Chinese Journal of Rock Mechanics and Engineering, 2013, 32(12): 2377-2393. (in Chinese)
[24] HE MC, XU M. Research and development of HEMS cooling system and heat-harm control in deep mine[J]. Chinese Journal of Rock Mechanics and Engineering, 2008, 27(7): 1353-1361. (in Chinese)
[25] HE MC. Application of HEMS cooling technology in deep mine heat hazard control[J]. Mining Science and Technology, 2009, 19(3): 269-275.
[26] WU XH, GUO QF, LI P, REN FH, ZHANG J, CAI MF. Investigating the effect of temperature changes on the physical field of surrounding rock in a deep gold mine[J]. Advances in Materials Science and Engineering, 2021, 1:1-13.
[27] CAI MF. Main issues metallic mines now are facing and solutions of the problems[J]. Mining Engineering, 2003, 1(1): 40-43. (in Chinese)
[28] GU DS, ZHOU KP. Development theme of the modern metal mining[J]. Metal Mine, 2012(7): 1-8. (in Chinese)
[29] LI P, CAI M. Distribution law of in situ stress field and regional stress field assessments in the Jiaodong Peninsula, China[J]. Journal of Asian Earth Sciences, 2018, 166: 66-79.
[30] LI P, REN FH, CAI MF, GUO QF, MIAO SJ. Present-day stress state and fault stability analysis in the capital area of China constrained by in situ stress measurements and focal mechanism solutions[J]. Journal of Asian Earth Sciences, 2019, 185: 104007.
[31] LI P, CAI MF, MIAO SJ, GUO QF. New insights into the current stress field around the Yishu fault zone, eastern China[J]. Rock Mechanics and Rock Engineering, 2019, 52: 4133-4145.
[32] HE MC. Conception system and evaluation indexes for deep engineering[J]. Chinese Journal of Rock Mechanics and Engineering, 2005, 24(16): 2854-2858. (in Chinese)
[33] LIANG PF, LENG K, MA Q. Research on the key hoisting technology in deep shafts of metal mines[J]. Journal of Liaoning University of Technology (Natural Science Edition), 2018, 38(1): 29-32. (in Chinese)
[34] RAMPEDI MSP, GENC B. An investigation into the optimization of personnel transportation to level 15 and below at Khuseleka No. 1 Shaft, Anglo Platinum[J]. The Journal ofthe Southern African Institute of Mining and Metallurgy, 2012, 112(4): 323-330.
[35] FENG XT, LIU JP, CHEN BR, XIAO YX, FENG GL, ZHANG FP. Monitoring, warning, and control of rockburst in deep metal mines[J]. Engineering, 2017, 3: 538-545.
[36] CAI MF, JI D, GUO QF. Study of rockburst prediction based on in-situ stress measurement and theory of energy accumulation caused by mining disturbance[J]. Chinese Journal of Rock Mechanics and Engineering, 2013, 32(10): 1973-1980. (in Chinese)
[37] MIAO SJ, CAI MF, GUO QF, HUANG ZJ. Rock burst prediction based on in-situ stress and energy accumulation theory[J]. International Journal of Rock Mechanics and Mining Sciences, 2016, 83: 86-94.
[38] FAIRHURST C. Some challenges of deep mining[J]. Engineering, 2017(3): 527-537.
[39] CAI MF. Prediction and prevention of rockburst in metal mines—A case study of Sanshandao gold mine[J]. Journal of Rock Mechanics and Geotechnical Engineering, 2016, 8(2): 204-211.
[40] HE MC, MIAO JL, LI DJ, WANG CG. Experimental study on rockburst processes of granite specimen at great depth[J]. Chinese Journal of Rock Mechanics and Engineering, 2007, 26(5): 865-876. (in Chinese)
[41] LI P, CAI MF, GUO QF, LU XG, YAN BQ. Research situations and development tendencies of fault slip rockburst in coal mine[J]. Journal of Harbin Institute of Technology, 2018, 50(3): 1-17. (in Chinese)
[42] LUO ZQ, WANG W, QIN YG, XIANG J. Early warning of rock mass instability based on multi-field coupling analysis and microseismic monitoring[J]. Transactions of Nonferrous Metals Society of China, 2019, 29(6): 1285-1293.
[43] MANSUROV VA. Prediction of rockbursts by analysis of induced seismicity data[J]. International Journal of Rock Mechanics and Mining Sciences, 2001, 38: 893-901.
[44] ADOKO AC, GOKCEOGLU C, WU L, ZUO QJ. Knowledge-based and data-driven fuzzy modeling for rockburst prediction[J]. International Journal of Rock Mechanics and Mining Sciences, 2013, 61: 86-95.
[45] DONG LJ, LI XB, PENG K. Prediction of rockburst classification using random forest[J]. Transactions of Nonferrous Metals Society of China, 2013, 23(2): 472-477.
[46] WANG C, WU A, LU H, BAO T, LIU X. Predicting rockburst tendency based on fuzzy matter–element model[J]. International Journal of Rock Mechanics and Mining Sciences, 2015, 75: 224-232.
[47] AFRAEI S, SHAHRIAR K, MADANI SH. Developing intelligent classification models for rock burst prediction after recognizing significant predictor variables, Section 1: Literature review and data preprocessing procedure[J]. Tunnelling and Underground Space Technology, 2019, 83: 324-353.
[48] XUE Y, BAI C, QIU D, KONG F, LI Z. Predicting rockburst with database using particle swarm optimization and extreme learning machine[J]. Tunnelling and Underground Space Technology, 2020, 98: 103287.
[49] XU ZM, HUANG RQ, FAN ZG, WU PG. Progress in research on rock burst hazard of long tunnel with large section[J]. Journal of Natural Disasters, 2004, 13(2): 16-24. (in Chinese)
[50] CAI MF, WANG JN, WANG SH. Prediction of rock burst with deep mining excavation in Linglong gold mine[J]. Journal of University of Science and Technology Beijing (English Edition), 2001, 8(4): 241-243.
[51] CAI MF, GUO QF, LI Y, DU ZF, LIU JH. In situ stress measurement and its application in the 10th mine of Pingdingshan coal group[J]. Journal of University of Science and Technology Beijing, 2013, 35(11): 1439-1406. (in Chinese)
[52] CAI MF, JI HG, WANG JA. Study of the time–space–strength relation for mining seismicity at Laohutai coal mine and its prediction[J]. International Journal of Rock Mechanics and Mining Sciences, 2005, 42(1): 145-151.
[53] CAI MF, WANG JA, WANG SH. Analysis on energy distribution and prediction of rock burst during deep mining excavation in Linglong gold mine[J]. Chinese Journal of Rock Mechanics and Engineering, 2001, 20(1): 38-42. (in Chinese)
[54] YANG J, MIN TJ, LIU BH, CHEN KK, YANG L. Research progress on disasters and prevention in deeping mining[J]. Science Technology and Engineering, 2020, 20(36): 14767-14776.
[55] Du PLESSIS GE, LIEBENBERG L, MATHEWS EH. The use of variable speed drives for cost-effective energy savings in South African mine cooling systems[J]. Applied Energy, 2013, 111: 16-27.
[56] HEINZ A. Ritical questions in mining front air conditioning[J]. Glueckauf: ZeitschriftfuerTechnik und Wirtschaft des Bergbaus, 1984, 120(12): 218-220.
[57] MOSER P. Mine cooling systems[J]. Sulzer Technical Review, 1985, 67(2): 21-24.
[58] WALT JVD, PYE R, PIETERSE H, DIONNE L. Ventilating and cooling at Barrick’s Meikle underground gold mine[J]. Mining Engineering, 1996, 48(4): 36-39.
[59] KOLARCZYK M. Cooling of mine air by means of surface ice coole[J]. PraceNaukoweInstytutuGornictwaPolitechnikiWroclawskiej, 1998, 85: 31-32.
[60] HE MC, ZHANG Y, QIAN ZZ, GUO DM. Research on doublets wells to store cold energy for heat-harm treatment in deep mine[J]. Coal Geology and Exploration, 2006, 34(5): 23-26. (in Chinese)
[61] HE MC, ZHANG Y, QIAN ZZ, GUO DM, CHEN DP. Numerical simulation study on utilizing aquifers to store cool energy in fathing deep mine heat-harm[J]. Journal of Hunan University of Science and Technology (Natural Science Edition), 2006, 21(2): 13-16. (in Chinese)
[62] LI P, WU YQ, CAI MF, ZHANG Y. Analysis of technical measures for controlling instability of surrounding rock in jointed rock masses[C]//IOP Conference Series: Earth and Environmental Science. IOP Publishing, 2021, 861: 052065.
[63] LI P, REN FH, CAI MF, GUO QF, WANG HF, LIU K. Investigating the mechanical and acoustic emission characteristics of brittle failure around a circular opening under uniaxial loading[J]. International Journal of Minerals, Metallurgy, and Materials, 2019, 26(10): 1217-1230.
[64] LI P, CAI MF, GUO QF, HUANG ZJ, REN FH. Physical simulation test on failure behavior of the underground opening: A review[C]//5th ISRM Young Scholars’ Symposium on Rock Mechanics and International Symposium on Rock Engineering for Innovative Future, YSRM 2019. Okinawa, Japan, 2019: 990-995.
[65] ORTLEPP WD. Considerations in the design of support for deep hard-rock tunnels[C]//Proceedings of the Fifth Congress of the International Society for Rock Mechanics. Melbourne, Australia, 1983: 179-187.
[66] JAGER AJ. Two new support units for the control of rockburst damage[C]//Proc International Symposium on Rock Support. Sudbury, 1992: 621-631.
[67] ANSELL A. Dynamic testing of steel for a new type of energy absorbing rock bolt[J]. Journal of Constructional Steel Research, 2006, 62(5): 501-512.
[68] VARDEN R, LACHENICHT R, PLAYER J, THOMPSON A, VILLAESCUSA E. Development and implementation of the Garford dynamic bolt at the Kanowna belle mine[C]//10th Underground Operators’ Conference. Launceston, 2008: 95-104.
[69] CHARETTE F, PLOUFFE M. A new rock bolt concept for underground excavations under high stress conditions[C]//6th International Symposium on Ground Support in Mining and Civil Engineering Construction. SAIMM, Johannesburg, 2008: 225-240.
[70] CHUNLIN LI C. A new energy-absorbing bolt for rock support in high stress rock masses[J]. International Journal of Rock Mechanics and Mining Sciences, 2010, 47(3): 396-404.
[71] HE MC, LI C, GONG WL, WANG J, TAO ZG. Support principles of NPR bolts/cables and control techniques of large deformation[J]. Chinese Journal of Rock Mechanics and Engineering, 2016, 35(8): 1513-1529. (in Chinese)
[72] HE MC, GONG WL, WANG J, QI P, TAO ZG, DU S, PENG YY. Development of a novel energy-absorbing bolt with extraordinarily large elongation and constant resistance[J]. International Journal of Rock Mechanics and Mining Sciences, 2014, 67: 29-42.
[73] HE MC, GUO ZB. Mechanical property and engineering application of anchor bolt with constant resistance and large deformation[J]. Chinese Journal of Rock Mechanics and Engineering, 2014, 33(7): 1297-1308. (in Chinese)
[74] HE MC, WANG J, SUN XM, YANG XJ. Mechanics characteristics and applications of prevention and control rock bursts of the negative poisson’s ratio effect anchor[J]. Journal of China Coal Society, 2014, 39(2): 214-221. (in Chinese)
[75] KANG HP, JIANG PF, HUANG BX, GUAN XM, WANG ZG, WU YZ, GAO FQ, YANG JW, CHENG LX, ZHENG YF, LI JZ. Roadway strata control technology by means of bolting-modification-destressing in synergy in 1000 m deep coal mines[J]. Journal of China Coal Society, 2020, 45(3): 845-864. (in Chinese)
[76] QIAO L, ZHOU M, YANG JM, LI QW. Experimental study on energy absorption of high damping rubber for rock under dynamic loads[J]. Chinese Journal of Rock Mechanics and Engineering, 2018, 37(4): 961-968. (in Chinese)
[77] WU YZ, KANG HP, WU JX, FAN RX. Development and application of mine prestressed steel bars supporting technology[J]. Chinese Journal of Rock Mechanics and Engineering, 2015, 34(S1): 3230-3237. (in Chinese)
[78] WU AX, WANG Y, ZHANG MZ, YANG GF. New development and prospect of key technology in underground mining of metal mines[J]. Metal Mine, 2021, 1: 1-13. (in Chinese)
[79] CAI MF, GAO YT, LI CH, QIAO L. Study on techniques for reinforcing collapsed main transport tunnel by bolting and grouting in Linglong gold mine[J]. Chinese Journal of Geotechnical Engineering, 1999, 21(4): 388-391. (in Chinese)
[80] CAI MF, KONG LA, LI CH, LAI XP. Dynamic synthetical monitoring and assessment for reinforced collapsing area of main transport tunnel in Linglong gold mine[J]. Chinese Journal of Rock Mechanics and Engineering, 2007, 26(5): 886-894. (in Chinese)
[81] LI YY. Mine wind lifting equipment[J]. Mining Technology, 1985, 11: 27-28. (in Chinese)
[82] LI XB, ZHOU J, WANG SF, LIU B. Review and practice of deep mining for solid mineral resources[J]. The Chinese Journal of Nonferrous Metals, 2017, 27(6): 1236-1262. (in Chinese)
[83] XIAO TY. Hydraulic lifting-An economic scheme for deepening underground mines[J]. Mining Engineering, 1990(3): 32-34. (in Chinese)
[84] CHEN LG. An economical and feasible scheme for deep mining of underground mines—Hydraulic lifting[J]. China Gems and Jades, 1990(2): 7-9. (in Chinese)
[85] GAO L, HAN KF. The technology of ore lifted by water-power for mining from underground[J]. Shandong Metallurgy, 1996, 18(4): 1-3. (in Chinese)
[86] XUE TK. Pneumatic hoisting equipment for mine and open-pit mine[J]. Mining and Processing Equipment, 1979(6): 39-40. (in Chinese)
[87] LI XB, YAO JR, DU K. Preliminary study for induced fracture and non-explosive continuous mining in high-geostress hard rock mine—A case study of Kaiyang phosphate mine[J]. Chinese Journal of Rock Mechanics and Engineering, 2013, 32(6):1101-1111. (in Chinese)
[88] WANG SF, SUN LC, HUANG LQ, LI XB, SHI Y, YAO JR, DU SL. Non-explosive mining and waste utilization for achieving green mining in underground hard rock mine in China[J]. Transactions of Nonferrous Metals Society of China, 2019, 29(9): 1914-1928.
[89] WANG RH, WANG FX, ZHOU WD, XU YJ, WANG MB, ZHONG GY. Particle impact drilling technology: The state of the art and perspective development[J]. Journal of China University of Petroleum(Edition of Natural Science), 2016, 40(6): 71-79. (in Chinese)
[90] YAN T, DU JY, LI W, BI XL, YAO SL. Syntesizing comment on efficient rock fragmentation method in frontier drilling technology[J]. Oil Field Equipment, 2012, 41(1): 50-55. (in Chinese)
[91] LIU BL, PAN JZ, XIE SY. On the research development of rock fragmentation and its prospect[J]. China Tungsten Industry, 2011, 26(1): 15-19. (in Chinese)
[92] GRAFF KF. Macrosonics in industry: 5. Ultrasonic machining[J]. Ultrasonics, 1975, 13(3): 103-109.
[93] HUANG JG, WANG HG, JI GD, ZHAO F, MING RQ, HAO YL. The rock breaking mechanism of ultrasonic high frequency rotary-percussive drilling technology[J]. Petroleum Drilling Techniques, 2018, 46(4): 23-29. (in Chinese)
[94] BELEM T, BENZAAZOUA M. Design and application of underground mine paste backfill technology[J]. Geotechnical and Geological Engineering, 2008, 26: 147-174.
[95] SIVAKUGAN N, RANKINE RM, RANKINE KJ, RANKINE KS. Geotechnical considerations in mine backfilling in Australia[J]. Journal of Cleaner Production, 2006, 14(12-13): 1168-1175.
[96] LI X, WANG SJ, LIU TY, MA FS. Engineering geology, ground surface movement and fissures induced by underground mining in the Jinchuan nickel mine[J]. Engineering Geology, 2004, 76(1-2): 93-107.
[97] YU RC. New challenges faced by cemented filling technology in metal mines—Speech of the 10th China filling mining technology and equipment conference[J]. Mining Research and Development, 2020, 40(12): 1. (in Chinese)
[98] CHEN CJ, CAI SJ. Study on the reliability of paste pumping-filling system in Jinchuan No.2 mine[J]. Metal Mine, 2002(1): 8-9. (in Chinese)
[99] WU AX, WANG Y, WANG HJ. Status and prospects of the paste backfill technology[J]. Metal Mine, 2016(7): 1-9. (in Chinese)
[100] PENG HS. Application status and case analysis of wasteless mining technology[J]. Mining Equipment, 2011(8): 54-57. (in Chinese)
[101] XU S, LI Y, LIU J. Application of wasteless mining in Hongtoushan copper mine[J]. Advanced Materials Research, 2013, 734-737: 722-726.
[102] WU AX, WANG HJ, YANG BH, YIN SH. Progress and prospect of solution mining[J]. Mining Technology, 2006, 6(3): 39-48. (in Chinese)
[103] GHORBANI Y, FRANZIDIS JP, PETERSEN J. Heap leaching technology—Current state, innovations, and future directions: A review[J]. Mineral Processing and Extractive Metallurgy Review, 2016, 37(2): 73-119.
[104] YIN SH, WANG LM, WU AX, CHEN X, YAN RF, QI Y. Progress of research in copper bioleaching technology in China[J]. Chinese Journal of Engineering, 2019, 41(2): 143-158. (in Chinese)
[105] HE ZG, XIE XH, XIAO SM, LIU JS, QIU GZ. Microbial diversity of mine water at ZhongTiaoshan copper mine, China[J]. Journal of Basic Microbiology, 2007, 47: 485-495.
[106] WU AX, WANG HJ, YIN SH, RUAN ZE. Conception of in-situ fluidization mining for deep metal mines[J]. Journal of Mining Science and Technology, 2021, 6(3): 255-260. (in Chinese)
[107] BHARGAVA SK, RAM R, POWNCEBY M, GROCOTT S, RING B, TARDIO J, JONES L. A review of acid leaching of uraninite[J]. Hydrometallurgy, 2015, 151: 10-24.
[108] ZECHENDORF B. Sustainable development: how can biotechnology contribute?[J]. Trends in Biotechnology, 1999, 17(6): 219-225.
[109] SCOBLE M. Canadian mining automation evolution: The digital mine en route to minewide automation[J]. CIM Bulletin, 1995, 88(990): 30–37.
[110] LI JG, ZHAN K. Intelligent mining technology for an underground metal mine based on unmanned equipment[J]. Engineering, 2018, 4: 381-391.
[111] WU LX, WANG YJ, DING EJ, ZHU WX, ZHANG RX, ZHANG S, WANG Z. Thirdly study on digital mineserve for mine safety and intellimine with support from IoT[J]. Journal of China Coal Society, 2012, 37(3): 357-365. (in Chinese)
[112] XIE HP, GAO F, JU Y, GE SR, WANG GF, ZHANG R, GAO MZ, WU G, LIU JZ. Theoretical and technological conception of the fluidization mining for deep coal resources[J]. Journal of China Coal Society, 2017, 42(3): 547-556. (in Chinese)
[113] XIE HP, JU Y, GAO F, GAO MZ, ZHANG R. Groundbreaking theoretical and technical conceptualization of fluidized mining of deep underground solid mineral resources[J]. Tunnelling and Underground Space Technology, 2017, 67: 68-70.
[114] XIE HP, JU Y, GAO MZ, GAO F, LIU JZ, REN HW, GE SR. Theories and technologies for in-situ fluidized mining of deep underground coal resources[J]. Journal of China Coal Society, 2018, 43(5): 1210-1219. (in Chinese).
深部金属矿产资源开发面临的挑战及新见解
李鹏1,2,3,蔡美峰1,2,3
1. 北京科技大学 土木与资源工程学院,北京 100083;
2. 北京科技大学 金属矿山高效开采与安全教育部重点实验室,北京 100083;
3. 北京科技大学 城市地下空间工程北京市重点实验室,北京 100083
摘要:长期持续的大规模开采使浅部金属矿产资源日益枯竭,深部开采已成为必然。介绍了当前全球金属矿产资源深部开采现状,系统梳理深部开采面临的一系列工程挑战,重点探讨在岩爆预测与防控、深井降温制冷技术、围岩支护技术、深井提升技术及一些非传统深部开采技术等关键工程技术方面取得的一些进展和未来创新重点。同时,对深部开采技术发展战略提出一些新的见解。这些前瞻性关键创新技术的集成,将形成金属矿深部开采创新技术体系的整体框架。该技术体系将有助于实现深部金属矿产资源的安全、高效、绿色开采,保障金属矿业的可持续发展。
关键词:深部金属矿产资源;工程挑战;灾害控制;非传统采矿技术;可持续发展
(Edited by Sai-qian YUAN)
1003-6326/
2021 The Nonferrous Metals Society of China. Published by Elsevier Ltd & Science Press
Abstract:Long-term and continuous large-scale exploitation has increasingly exhausted shallow metal mineral resources, and deep mining has become inevitable. The current global status of deep mining of metal mineral resources was presented, a series of engineering challenges faced by deep mining were systematically analyzed, and some progress and future innovation focus in key engineering technologies, such as the prediction and prevention of rockburst, cooling techniques, rock support techniques, deep hoisting techniques, and several nontraditional deep mining techniques, were highlighted. Meanwhile, new insights into development strategies of deep mining technology were proposed. The integration of these forward-looking key innovative technologies will form the overall framework of an innovative technology system for the deep mining of metal minerals. This technology system will help to achieve safe, efficient, and green exploitation of deep underground metal mineral resources and ensure the sustainable development of the metal mining industry.