文章编号:1004-0609(2008)04-0666-05
Al-Mn合金镀层的微观结构及耐蚀性
杨占红1,王小花1,李旺兴2,陈建华2,王升威1
(1. 中南大学 化学化工学院,长沙 410083;
2. 中国铝业公司 郑州研究院,郑州 450041)
摘 要:在AlCl3-NaCl-KCl低温共融盐中,添加无水MnCl2,接通直流电在铁片上获得Al-Mn合金镀层。用扫描电镜、能量色散谱、X射线衍射和极化曲线对分别对该合金镀层的形貌、组成、相结构及耐腐蚀性能进行测试。结果表明:纯铝镀层表面呈针状,锰质量分数9.20%的镀层表面呈花状,锰质量分数25.43%的镀层表面有无规则瘤节状凸起物且晶界模糊,而锰质量分数达到34.42%时,晶粒细化,晶界清晰;合金镀层中锰质量分数与熔盐中无水MnCl2的质量分数呈线性关系;锰质量分数为20.84%~29.74%的镀层为单一的非晶态结构,锰质量分数高于29.74%的镀层为Al8Mn5晶体与非晶态的双相结构;合金镀层的点蚀电压比纯铝镀层高180~360 mV,单相非晶态合金镀层的耐蚀性优于双相镀层。
关键词:Al-Mn合金;低温熔融盐;电镀;微观结构;耐蚀性
中图分类号:TQ 153.2 文献标识码:A
Composition, structure and corrosion resistance of Al-Mn alloy coatings
YANG Zhan-hong1, WANG Xiao-hua1, LI Wang-xing2, CHEN Jian-hua2, WANG Sheng-wei1
(1. School of Chemistry and Chemical Engineering, Central South University, Changsha 410083, China;
2. Zhengzhou Research Institute, Aluminum Corporation of China, Zhengzhou 450041, China)
Abstract: Al-Mn alloy coatings were obtained on iron substrate from AlCl3-NaCl-KCl low temperature molten salt with a controlled content of anhydrous MnCl2. SEM, EDS, XRD and polarization curves were used to investigate the composition, surface morphology, phase structure and corrosion resistance of the obtained deposits. The results show that the surface of the obtained pure aluminum coating is acicular, while the coating with 9.20%(mass fraction) Mn is flowery-like and irregular tumor-like outshoots and dark grain boundaries exist in the coating with 25.43% Mn. As Mn content achieves 34.42%, the obtained crystal is fined and the grain boundaries turn clear. The content of manganese increases linearly with increasing content of MnCl2. A single amorphous phase alloy coating is obtained when Mn content is between 20.84% and 29.74%, when the content of Mn beyond 29.74%, a mixture of amorphous and Al8Mn5 was obtained. The pitting potential of the obtained pure aluminum coating is enhanced by about 180-360 mV when added with Mn. The corrosion resistance of single amorphous phase alloys is better than that of the duel-phase structure deposits.
Key words: Al-Mn alloys; low temperature molten salt; electroplating; microstructure; corrosion resistance
铝和铝合金因具有密度低、耐腐蚀、强度高、美观等优良品质而发展非常迅速,在国民经济各领域及国防建设的应用中占有很大的份额。用铝或铝合金制成各种金属材料的表面镀层,可获得美观、耐蚀,且具有优良力学性能的复合材料[1-4]。Al-Mn 合金镀层出色的耐蚀性和装饰性引起广泛注意[5],金属玻璃结构的发现,更加引起人们对Al-Mn合金镀层的兴 趣[6-10]。但铝是一种非常活泼的金属,只能在非水溶液中电镀。随着熔融盐化学的应用和发展,熔融盐电镀铝和铝合金作为一种新型工艺,越来越引起人们的极大兴趣和关注[11-12]。低温熔盐电镀铝合金具有工艺简单、镀层厚度易控制、镀层耐蚀性能好、成本低廉等优点,具有较大的开发价值[13]。国外近几年的研究甚为活跃,并已建造了低温熔盐电镀铝合金钢板生产线,而我国这方面的研究却较少,大多仍处于实验室研究或小批量试制阶段, 不能进行大规模工业化生 产[3, 14]。
本文作者在无惰性气氛保护的AlCl3-NaCl-KCl低温熔融盐中,添加一定量的无水MnCl2,在铁片基体上得到了Al-Mn合金镀层。对各含锰量镀层的表面形貌和相结构进行分析,确定熔盐中无水MnCl2的浓度与所得合金镀层中锰含量的关系,并通过3.5%NaCl溶液中所得的极化曲线对镀层的耐蚀性进行评价,为工业上低温熔盐电镀Al-Mn合金提供实验基础和数据支持。
1 实验
1.1 样品制备
将NaCl和KCl在400 ℃下干燥5 h待用,无水MnCl2在250 ℃下干燥5 h,无水AlCl3使用前密封保存。将 125 g分析纯无水AlCl3、NaCl和KCl按摩尔比0.66?0.17?0.17在三口瓶中混合均匀后,加热至混合盐完全熔融。以纯度为99.9%的铝片为工作电极和参比电极,控制阴极电位为-30 mV,预电解12 h后得到浅黄色透明熔体。
在所得的熔体中加入一定量的无水MnCl2,以纯铝片作为阳极,将经打磨、除油和除锈的电化学活化铁片为阴极,控制熔体温度为(160±2) ℃,阴极电流密度40 mA/cm2,通电30 min。电镀结束,取出镀片,在超声波清洗器中清洗后吹干。
1.2 测试方法
采用JSM-6360LV型扫描电镜分析镀层表面和断面形貌;采用X’ Pert Pro 型X射线衍射仪分析其相结构 (Cu Kα,扫描速率4 (?)/min,扫描范围10?~75?);EDS测试也在JSM-6360LV型扫描电镜上进行,用以确定镀层的组成及进行元素线分析,断面样品分析前需先经镶嵌、打磨、抛光和喷金处理。
极化曲线测试在普林斯顿263A型恒电位仪上进行,测量介质为3.5%的NaCl溶液,电位扫描速度为5 mV/s。测试时采用三电极体系,所得Al-Mn合金镀片为研究电极,Pt片为辅助电极,饱和甘汞电极(SCE)为参比电极。
2 结果与讨论
2.1 Al-Mn合金镀层的表面形貌
图1所示为不同锰含量合金镀层的SEM表面形貌。从图中可看出,纯铝镀层表面晶体呈针状,锰质量分数为9.20%的镀层表面呈花状。锰质量分数25.43%的镀层表面有不规则的瘤节状凸起,晶界变得模糊,与图4(b)相比晶粒变小,对照图4(d)结果可知,此时镀层转化为完全非晶态结构。当锰质量分数增加到34.42%时,晶粒进一步细化,但晶界又趋明显,对照图4(g)衍射结果可知,此时镀层中出现Al8Mn5晶体。
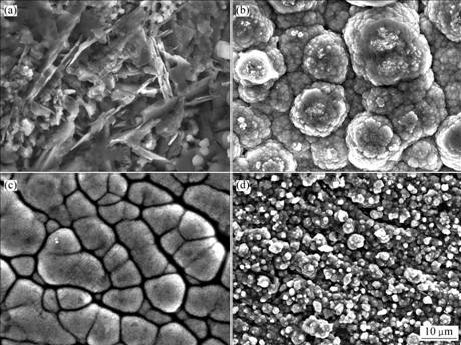
图 1 不同Mn含量合金镀层的SEM表面形貌
Fig.1 SEM surface morphologies of Al-Mn alloys with various Mn contents: (a) Mn-free; (b) 9.20%Mn; (c) 25.43%Mn; (d) 34.42%Mn
从宏观上看,所得的各合金镀层均平整光滑,含锰质量分数低于16.26%的Al-Mn合金为类似普通铝合金的银白光亮;锰质量分数在16.26%~34.42%的合金镀层镜面光亮;当锰质量分数超过34.42%时,所得镀层发黑。
2.2 镀层元素扫描分析
图2(a)所示为锰质量分数25.43%的镀层表面形貌及Al和Mn元素的线分布曲线,图2(b)所示为该镀层断面的形貌及Al、Mn和Fe元素的线分布曲线。从图2(a)可看出,Al、Mn 元素在镀层表面分布很均匀,没有出现富集现象;从图2(b)可看出,元素Al和Mn在镀层厚度方向的分布很均匀,且在镀层与基底交界处没有Fe-Al合金层生成,这说明Al-Mn合金镀层是在基底上直接外延生长,这与热浸镀不同[15-16]。
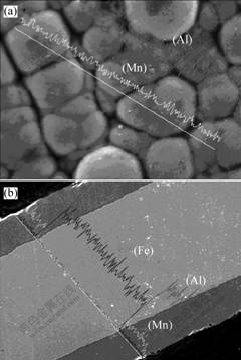
图 2 锰质量分数25.43%的镀层表面形貌和断面元素线分布曲线
Fig.2 SEM surface morphologies of linearly element analysis of surface(a) and cross-section(b) of alloy with 25.43% Mn
2.3 Al-Mn合金镀层的组成分析
熔融盐中无水MnCl2浓度对合金镀层的组成影响如图3所示。由图可见,在熔融盐中无水MnCl2质量分数不高于3.0%的范围内,所得合金镀层中Mn含量与熔融盐中MnCl2添加量近似呈线性关系,因而在此范围内,可通过控制熔融盐中MnCl2的加入量来控制镀层中的锰含量;当MnCl2质量分数高于3.0%时,随着熔融盐中MnCl2的增加,所得合金镀层中Mn含量增加,但图中点偏离原来的直线,此时熔盐体系的电镀性能很差,所得镀层表面发黑,且冲洗时易剥落造成镀层不连续。
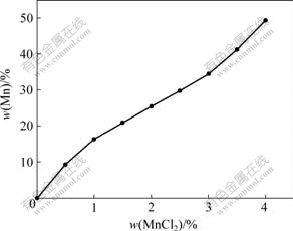
图 3 MnCl2质量分数与合金层Mn含量关系
Fig.3 Relationship between mass fraction of MnCl2 and Mn content
Mn在熔融盐中的电沉积过程主要包括Mn2+向阴极的迁移、电化学反应和Mn在沉积层中的扩散。熔融盐中无水MnCl2浓度较低时(低于3.0%),Mn2+的扩散为主要控制步骤,所得镀层中的Mn含量与熔融盐中MnCl2浓度呈线性关系;熔融盐中无水MnCl2浓度超过该值后,电化学反应成了电沉积过程的主要控制步骤,因此所得镀层中的Mn含量与熔融盐中MnCl2浓度偏离原线性关系。且在一定的无水MnCl2浓度范围内,Mn2+的加入可以使铝的沉积电位发生负移,在同一定电位下铝锰发生共沉积而获得优良的合金镀层;但Mn2+的浓度超过某一值时,铝锰的共沉积被破坏,先单独析出锰导致镀层表面发黑并破坏镀层的连续性。
2.4 合金镀层的相结构
图4所示为不同锰含量镀层的XRD谱。由图可知,纯铝镀层在38.4?,44.6?处出现尖锐衍射峰,分别对应Al的(111)和(200)面的衍射峰,此时所得的沉积铝为面心立方结构;当镀层的锰质量分数不高于9.20%时,可以观察到尖锐的衍射峰,对比标准卡可知,此条件下为锰溶于铝的固熔体;锰质量分数为16.26%时,只能看到很弱的Al(111)面的衍射峰。此时合金镀层主要由非晶态结构组成,但仍存在少量的晶态结构;在锰质量分数为20.84%~29.74%时,镀层完全由非晶态结构组成,在XRD谱中看不到尖锐的结晶峰而只有漫反射峰;锰质量分数为34.42%的镀层,在42.5?处出现较弱的衍射峰出现,锰含量41.21%的衍射谱中,该结晶峰强度变强。对比标准卡可知,此峰为Al8Mn5(330)面的衍射峰,此时镀层由非晶态和晶态Al8Mn5的混合结构。锰在面心立方结构的铝中溶解度为8.8%[6],镀层中锰的质量分数超过它在铝中的溶解度后,面心立方结构被破坏并在电场作用下形成非晶结构,且非晶结构所占比重随锰含量的增加而增大。
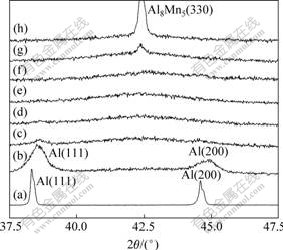
图4 不同Mn含量合金镀层的XRD谱
Fig.4 XRD patterns for Al-Mn alloy deposits with different Mn contents: (a) Mn-free; (b) 9.20%Mn; (c) 16.26%Mn; (d) 20.84%Mn; (e) 25.43%Mn; (f) 29.74%Mn; (g) 34.42%Mn; (h) 41.21%Mn
2.5 合金镀层的耐腐蚀性能
铝和铝合金属于钝性金属,其腐蚀破坏主要是在含Cl-介质中发生的点腐蚀[8],因此选用3.5%的NaCl溶液作腐蚀液,采用强化腐蚀手段来测定其耐蚀性,图5所示为所测得的极化曲线。
从图5可知,在实验条件下,与纯铝镀层相比,Al-Mn合金的点蚀电位有所提高,可以获得较宽的钝化区域。锰质量分数9.20%的镀层比纯铝镀层的点蚀电位高180 mV左右;锰质量分数低于29.74%时,随着锰质量分数的增加,镀层的点蚀电位逐渐提高;但研究发现,锰质量分数34.42%的镀层点蚀电位比锰质量分数29.74%的镀层略低,锰质量分数41.21%的镀层点蚀电位比锰质量分数34.42%的镀层低。这是由于非晶态结构的耐蚀性优于晶态结构,锰质量分数低于29.74%,随锰质量分数增加镀层中非晶态组分增加,耐蚀性能变好;锰质量分数高于29.74%,随锰质量分数增加镀层中晶态组分增加,导致耐蚀性降低。
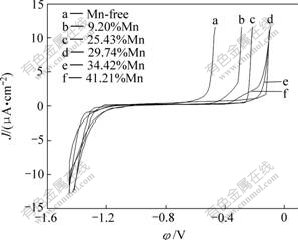
图 5 Al-Mn合金镀层的极化曲线
Fig.5 Polarization curves of Al-Mn alloys
3 结论
1) 在摩尔比0.66?0.17?0.17 的AlCl3-NaCl-KCl低温熔融盐中,添加适量的无水MnCl2,能在铁片上获得银白光亮的Al-Mn合金镀层。合金镀层中Mn含量与添加无水MnCl2的量近似呈线性关系。
2) 合金镀层的表面形貌与锰含量有关,纯铝镀层表面晶体呈针状,锰质量分数9.20%的镀层表面呈花状,锰质量分数25.43%的镀层表面呈不规则的瘤状,锰质量分数增加到34.42%时,晶粒进一步细化,晶界变明显。Al-Mn合金镀层在基底上直接外延生长,Al元素和Mn元素在镀层的表面和断面方向均匀分布。
3) XRD结果表明,合金中Mn质量分数低于9.20%时,为面心立方铝固熔体;Mn质量分数为16.26%时,为固熔体与非晶相的混合结构;Mn质量分数为20.84%~29.74%时,为单一的非晶态结构;Mn质量分数超过29.74%后,为晶态Al8Mn5与非晶相的混合结构。
4) 极化曲线结果表明,在Mn质量分数低于29.74%时,随着镀层中Mn质量分数的增加,合金镀层点蚀电位增加;但继续增加镀层中的Mn质量分数,点蚀电位又略降低。
REFERENCES
[1] STAFFORD G R, GRUSHKO B, MCMICHAEL R D. The electrodeposition of Al-Mn ferromagnetic phase from molten salt electrolyte[J]. Journal of Alloys and Compounds, 1993, 200(1/2): 107-113.
[2] RICHARD T C, WAYNE C, MICHAEL B. Nucleation and morphology studies of aluminum deposited from an ambient- temperature chloroaluminate molten salt[J]. Electrochem Soc, 1992, 139(10): 2720-2727.
[3] 黄伯云. 我国有色金属材料现状及发展战略[J]. 中国有色金属学报, 2004, 14(S1): 122-127.
HUANG Bai-yun. Status and developing strategy for China’s nonferrous metal materials industry[J]. The Chinese Journal of Nonferrous Metals, 2004, 14(S1): 122-127.
[4] YUKIHIRO K, NOBUKAZU F, MASATO Y. Long-term corrosion resistance of Al-Ni-plated material and Al-plated material in molten carbonate environment[J]. Journal of Power Sources, 2000, 86: 324-328.
[5] DAVOODI A, PAN J, LEYGRAF C. Integrated AFM and SECM for in situ studies of localized corrosion of Al alloys[J]. Electrochimica Acta, 2007, 52: 7697-7705.
[6] LI J C, NAN S H, JIANG Q. Study of the electrodeposition of Al-Mn amorphous alloys from molten salts[J]. Surface and Coatings Technology, 1998, 106(2/3): 135-139.
[7] 李建忱, 马丽杰, 于 燕. Al-Mn非晶合金镀层[J]. 中国有色金属学报, 1997, 7(1): 172-175.
LI Jian-chen, MA Li-jie, YU Yan. Electrodeposition of Al-Mn amorphous alloy[J]. The Chinese Journal of Nonferrous Metals, 1997, 7(1): 172-175.
[8] 褚松竹, 邱竹贤, 杨振海. 熔盐电镀Al-Mn合金镀层的结构与性能[J]. 中国有色金属学报, 1998, 8(1): 95-100.
CHU Song-zhu, QIU Zhu-xian, YANG Zhen-hai. Structure and properties of Al-Mn alloy coatings electroplated from molten salt[J]. The Chinese Journal of Nonferrous Metals, 1998, 8(1): 95-100.
[9] MIKITO U, HIROKUNI K, TOSHIAKI O. Co-deposition of Al-Cr-Ni alloys using constant potential and potential pulse techniques in AlCl3-NaCl-KCl molten salt[J]. Electrochimica Acta,2007, 52(7): 2515-2519.
[10] JAMES M F, DEREK T G, ELIZABETH J P. A laboratory porous flow-through electrode reactor with interchangeable electrodes[J]. Electrochem Soc, 1990, 137(9): 2809-2811.
[11] MUHAMMAD R A, ATSHUSHI N, TOORU T. Electro- deposition of Al-Ni intermetallic compounds from aluminum chloride -N-(n-butyl) pyridinium chloride room temperature molten salt[J]. Journal of Electroanalytical Chemistry, 2001, 513(2): 111-118.
[12] TETSUYA T, TOSHIYUKI N, YASUHIKO I. Nucleation and surface morphology of aluminum-/lanthanum alloy electro- depsited in a LaCl3-saturated AlCl3-EtMeImCl room temperature molten salt[J]. Electrochimica Acta, 2002, 47: 2817-2822.
[13] JAFARIAN M, MAHJANI M G, GOBAL F. Effect of potential on the early stage of nucleation and growth during aluminum electrocrystallization from molten salt (AlCl3-NaCl-KCl)[J]. Journal of Electroanalytical Chemistry,2006, 588(2): 190-196.
[14] 温乃盟, 郑建平. 铝锰合金镀层的组织结构与耐蚀性[J]. 材料保护, 1999, 32(10): 14-16.
WEN Nai-meng, ZHENG Jian-ping. Structure and corrosion res istance of Al-Mn alloy deposit[J]. Materials Protection, 1999, 32(10): 14-16.
[15] 张 伟, 郭献军, 李海涛. 热浸镀稀土铝合金层的生长动力学及其计算机拟合[J]. 金属热处理, 2006, 31(1): 49-52.
ZHANG Wei, GUO Xian-jun, LI Hai-tao. Growth kinetics of Fe-Al alloy layer of hot dip aluminizing with rare earths and computer fitting[J]. Heat Treatment of Metals, 2006, 31(1): 49-52.
[16] 夏 原, 姚 枚, 张瑞平. A3钢热浸铝镀层生长规律的影响因素[J]. 中国有色金属学报, 1996, 6(1): 74-77.
XIA Yuan, YAO Mei, ZHANG Rui-ping. The affecting of temperature and time to the growth of hot-dip aluminizing coating on A3 steel[J]. The Chinese Journal of Nonferrous Metals, 1998, 6(1): 74-77.
基金项目:国家科技支撑计划资助项目(2006BAE03B03)
收稿日期:2007-09-14;修订日期:2008-01-07
通讯作者:杨占红,教授,博士;电话:0731-8879616;E-mail: zhyang@mail.csu.edu.cn
(编辑 龙怀中)