文章编号:1004-0609(2010)10-1941-08
等径角挤压制备的超细晶Al-5%Cu合金块材的腐蚀行为
宋 丹,马爱斌,江静华,林萍华,范俊峰
(河海大学 力学与材料学院, 南京 210098)
摘 要:采用全浸泡腐蚀和电化学腐蚀研究等径角挤压制备的超细晶铝铜合金块材在氯化钠溶液中的腐蚀行为。结果表明:超细晶铝铜合金中基体相α(Al)晶粒细小(为200~300 nm);铸态组织中网状θ相(Al2Cu)破碎、细化成10 μm左右的颗粒并均匀分布于形变α(Al)基体上;形变细化提高铝铜合金在氯化钠介质中的耐蚀性能,表现出全浸泡腐蚀中更轻的腐蚀程度、电化学测试中更大的极化电阻、更正的自腐蚀电位和点蚀电位、更小的腐蚀电流密度。
关键词:Al-Cu合金;等径角挤压;超细晶;腐蚀行为
中图分类号:TG171 文献标志码:A
Corrosion behavior of ultra-fine grain bulk Al-5%Cu alloy fabricated by equal-channel angular pressing
SONG Dan, MA Ai-bin, JIANG Jing-hua, LIN Ping-hua, FAN Jun-feng
(College of Mechanics and Materials, Hohai University, Nanjing 210098, China)
Abstract: The effect of strain-induced grain refinement on the corrosion behavior of ultra-fine grain bulk Al-5%Cu alloy fabricated by equal-channel angular pressing (ECAP) was investigated by constant immersion tests and electrochemical corrosion in NaCl solution. The results show that the ECAP Al-Cu alloy obtains a finer grain size (200-300 nm) of α(Al) matrix, and the original net-like coarse θ phase is also broken into uniformly distributed fine particles with grain size of about 10 μm. The corrosion resistance of ultra-fine grain (UFG) Al-Cu alloy is obviously improved with alleviated corrosion damaged morphologies in constant immersion test, and the alloy has more positive open circuit potential (φ0), higher fitted Rt values, more positive self corrosion potential (φp) and lower corrosion current (Jc) values in electrochemical measurements.
Key words: Al-Cu alloy; equal-channel angular pressing; ultra-fine grain; corrosion behavior
铝合金作为轻质结构材料,在诸多工业领域具有广阔的应用前景,特别是航空航天及交通运输等领 域[1]。然而,到目前为止,它们的应用仍受到制约,例如较低的强度及较为严重的局部腐蚀倾向等。有关研究表明,晶粒细化可同时提高铝合金的力学性能及耐蚀性能,因此,人们投入大量的精力以研发具有超细晶粒的变形铝合金[2-3]。在此,等径角挤压(Equal-channel angular pressing,ECAP)作为一种可高效细化晶粒的新型金属加工工艺值得特别关 注[4-5]。近十几年,ECAP技术已被广泛用于超细晶(Ultra-fine grain,UFG)块材的大塑性变形加工。借助该技术,大量金属结构材料(例如铝合金、镁合金和铁合金等)的力学性能和物理特性获得显著提高,甚至材料的耐蚀性也可得到有效改善[6-9]。
ZL203是一种应用广泛的铸造Al-Cu合金,它的主要化学成分为Al-5%Cu(质量分数),合金的典型显微组织由α(Al)基体和θ相(Al2Cu)组成。运用等径角挤压以提高Al-Cu系合金的机械性能已在一些文献中有报道[10-11]。经过等径角挤压后,Al-0.63%Cu合金和Al-3.9%Cu的抗拉强度从78 MPa和125 MPa分别增加到225 MPa和285 MPa,效果显著。然而,目前对ECAP超细晶铝铜合金块材的耐蚀性能研究仍十分有限。众所周知,与常规金属结构材料相比,铝合金在很多介质中具有较好的耐蚀性,但在含Cl-侵蚀介质中仍具有较大的点蚀倾向。ZL203由纯铝中加入一定量的铜元素获得,铜元素的加入大幅度降低了合金的耐蚀性。鉴于ZL203合金双相结构的特性,两大因素决定其耐蚀性能[12]:一是α(Al)基体的耐蚀性,它在很大程度上决定于α(Al)基体表面氧化膜的稳定性,而氧化膜的特性与α(Al)基体的显微组织密切相关;二是θ相的形貌及分布,θ相在合金中作为腐蚀电偶的阴极加速α(Al)基体的阳极溶解。ECAP过程会严重改变α(Al)基体的显微组织和θ相的形貌及分布,从而可能使制备出的超细晶铝铜合金块材表现出完全不同于铸态合金的腐蚀行为。然后,到目前为止关于这一方面的研究仍相当有限。
本文作者主要通过全浸泡和电化学腐蚀试验,结合合金显微组织及表面腐蚀形貌分析,研究ECAP制备的超细晶铝铜合金块材在氯化钠溶液中的腐蚀行为。并通过与铸造合金的对比,讨论ECAP过程中显微组织变化对铝铜合金耐性能的影响。文中所得结果将有助于更好地理解ECAP制备的Al-Cu系合金块材的腐蚀行为及拓展它们的工程应用。
1 实验
1.1 ECAP试样的制备
ECAP所用材料为ZL203铝铜合金铸锭,其化学成分见表1。用线切割技术直接从铸锭切得并加工成20 mm×20 mm×40 mm的坯料,利用ECAP模具按如图1所示进行多道次ECAP挤压。在挤压之前,所有坯料表面及模具内壁都均匀涂敷石墨乳,以减小挤压过程中坯料与模具壁之间的摩擦力。鉴于ZL203铝铜合金中含有大量θ强化相,室温塑性差,挤压时必须对坯料进行加热以获得优质无裂纹的挤压试样。经多次预实验,优化后的挤压温度设定为150 ℃,在此
表1 ZL203铸锭的主要化学成分
Table 1 Chemical composition of as-received cast ZL203 Al-Cu alloy (mass fraction, %)

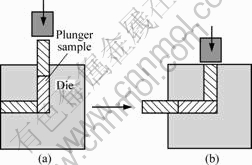
图1 等径角挤压加工示意图
Fig.1 Schematic diagram of ECAP process
温度下进行6道次ECAP挤压,挤压速度为0.5 mm/s。
1.2 显微组织观察
金相试样沿垂直于挤压方向切取,经碳化硅砂纸打磨,蒸馏水浇绒布抛光并用腐蚀剂Keller溶液(2.5% HNO3+1.5%HCl+1%HF+95%H2O,质量分数)侵蚀后在XJG-05型数码显微镜下进行观察。本实验中的透射电镜分析在Tecnai F20(USA)电镜上进行。透射电镜试样用线切割在超细晶试样的芯部沿垂直于挤压方向切得10 mm×10 mm×1 mm的薄片,利用砂纸机械打磨至0.1 mm后进行电解双喷。电解液为10% HClO4+90%酒精(质量分数)混合溶液,电压为20 V,温度为7.8 ℃。
1.3 腐蚀试验
借助全浸泡腐蚀及电化学腐蚀试验法,以铸态ZL203铝铜合金为对比样,对ECAP制备的超细晶铝铜合金块材的腐蚀行为进行研究。
在全浸泡腐蚀试验之前,所有试样均进行打磨抛光及丙酮擦拭除油。将试样在150 mL 3.5%的氯化钠溶液中分别连续浸泡10 d。在S340-N型扫描电子显微镜(Hitachi,Japan)下进行微观腐蚀形貌观察,并在KH-7700型数码显微镜(Hirox,USA)下进行宏观腐蚀形貌观察。
电化学腐蚀试验利用Parstat 2273恒电位仪进行,所用腐蚀溶液为10 mmol/L氯化钠溶液。采用以饱和氯化钾/甘汞电极为参比电极、铂电极为辅助电极的标准三电极系统。电化学试样用环氧密封,留出1 cm2腐蚀电极表面并用铜导线接引。为了更好地对比及可重复,所有试样严格按照金相制备要求打磨并用丙酮清洗,热空气吹干并干燥保存。采用2种电化学检测手段,分别为:电化学阻抗频谱测试(Electrochemical impendence spectrum,EIS);动电位扫描极化曲线测试。电化学试验均在稳定开路腐蚀电位下进行,测试之前将试样在腐蚀溶液中提前浸泡15 min以获得稳定开路腐蚀电位。电化学阻抗频谱频率范围为 10 mHz~10 kHz, 外加扰动信号10 mV;动电位扫描极化测试的扫描速率为0.5 mV/s。
2 结果与分析
2.1 超细晶铝铜合金的显微组织
图2所示为铸态及超细晶铝铜合金块材的金相组织。由图2可看出,铸态铝铜合金由α(Al)和分布在晶界处的网状α(Al)+θ(Al2Cu)共晶体组成,因该成分离共晶点较远,共晶数量较少,在金相显微镜下晶界附近仅能观察到θ相[13]。得益于ECAP大塑性变形,超细晶铝铜合金块材的显微组织发生了剧烈变化。铸态组织中的θ相网状结构完全消失,粗大θ相被细化成直径约为10 μm的细小θ相颗粒,孤立而均匀分布于α(Al)基体。ECAP挤压过程中α(Al)基体的晶粒尺寸、晶界结构、位错等显微组织的变化则需要通过TEM观察。
图3所示为超细晶铝铜合金块材的TEM像,其中图3(a)为较低倍率下的α(Al)基体晶粒形貌,图3(b)
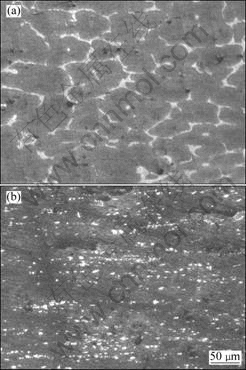
图2 铸态及超细晶铝铜合金的光学显微组织
Fig.2 Optical micrographs of as-cast (a) and UFG (b) Al-Cu alloys
是较高倍率下的α(Al)基体晶粒形貌,图(c)是选区电子衍射花样。经过6道次ECAP挤压后,α(Al)基体积累的大量应变使其晶粒尺寸得到了显著细化。α(Al)基体的晶粒由铸态的约50 μm细化到200~300 nm,已属于超细晶的范畴。同时,形变α(Al)基体晶粒成类等轴晶状。在α(Al)基体晶粒得到明显细化的同时,其晶界
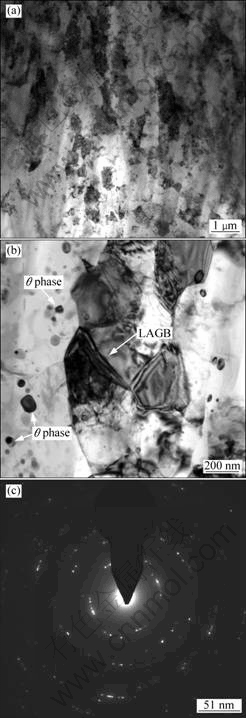
图3 超细晶铝铜合金的TEM像及选区电子衍射花样
Fig.3 TEM images (a), (b) and SAED pattern (c) of UFG Al-Cu alloy
结构也发生显著改变。由图3(b)箭头所指处可见,大量α(Al)基体晶粒的晶界呈现出等厚条纹,说明超细晶铝铜合金的晶界为大角度晶界(Large-angle grain boundary,LAGB)。图3(c)选区电子衍射花样成环状,一方面说明超细晶铝铜合金的晶粒细小,另一方面也说明晶体中含有大比例的大角度晶界。ECAP大塑性变形不仅细化晶粒,改变晶界结构,同时也给晶体带来了大量的位错。这些位错在部分晶粒内成团絮状分布于形变α(Al)基体晶内,密度很高。在形变α(Al)基体中还可以发现一些如图3(b)所示的θ相粒子。得益于多道次ECAP过程中积累的大应变,这些θ相粒子已被纳米化,尺寸为30~50 nm。
2.2 全浸泡腐蚀行为
铝铜合金在含氯离子的侵蚀介质中,浸泡初期以试样表面的水化反应生成水合氧化膜(Al2O3·H2O)为主。这一水合氧化膜将与试样表面的自生氧化膜构成混合钝化膜。但在氯离子的连续进攻下,混合钝化膜会逐渐减薄,在部分薄弱环节发生腐蚀破坏[14]。可通过混合钝化膜的破坏程度来判断铝铜合金的耐蚀性能,例如蚀坑的数量、尺寸以及钝化膜的腐蚀开裂程度。图4所示为铸态及超细晶铝铜合金块材在3.5%氯化钠溶液中连续浸泡3 d后的SEM像。随着α(Al)基体表面水化产物的不断堆积,混合钝化膜的厚度增加,
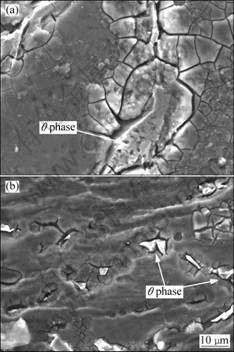
图4 铸态及超细晶铝铜合金的SEM像
Fig.4 SEM images of as-cast (a) and UFG (b)Al-Cu alloys after immersion in 3.5% NaCl solution for 3 d
致密的混合钝化膜可向基体提供良好的腐蚀屏障保护。如图4箭头所示,θ相在氯化钠溶液中性能稳定,并未发生腐蚀。而α(Al)基体上临近θ相部位的混合钝化膜均产生不同程度的腐蚀开裂,且腐蚀裂纹由临近θ相的α(Al)基体向远离θ相的α(Al)基体扩展。由于腐蚀裂纹的存在为腐蚀介质进入铝基体提供了通道,因此腐蚀裂纹将大幅度降低混合钝化膜的屏障保护作用。对比2种试样,铸态合金的混合钝化膜腐蚀破坏严重,裂纹数量最多且裂纹扩展最远。而超细晶铝铜合金的混合钝化膜腐蚀裂纹仅少量分布于细小θ相周围,且裂纹扩展距离较近。从SEM微观腐蚀形貌不难发现:在氯化钠溶液的3 d连续浸泡过程中,铸态及超细晶铝铜合金均发生了不同程度的腐蚀,腐蚀以α(Al)基体上临近θ相的混合钝化膜的腐蚀开裂为主。其中铸态试样的混合钝化膜腐蚀破坏严重,超细晶试样的混合钝化膜腐蚀破坏较轻。
图5所示为铸态及超细晶铝铜合金块材在3.5%氯化钠溶液中连续浸泡10 d后的宏观腐蚀形貌。由图5可看出,铸态及超细晶铝铜合金试样在腐蚀严重的区域表现为大尺寸的宏观腐蚀斑,而腐蚀程度较轻的区域则比未腐蚀时颜色变深,在部分腐蚀斑中间为黑色的非规则宏观腐蚀坑。这些腐蚀坑已向基体深度方向发展。可以肯定,铸态及超细晶铝铜合金块材在氯化
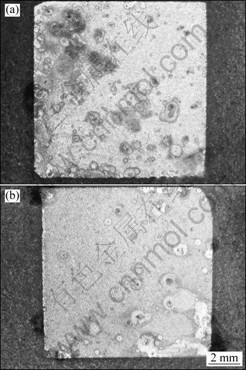
图5 铸态及超细晶铝铜合金的宏观腐蚀形貌
Fig.5 Macro morphologies of as-cast (a) and UFG (b) Al-Cu alloys after immersion in 3.5% NaCl solution for 10 d
钠溶液中的宏观腐蚀行为是非规则点蚀。从宏观腐蚀斑和腐蚀坑的数量及尺寸可以判断出,铸态铝铜合金的腐蚀破坏程度较为严重,而由ECAP大塑性变形获得的超细晶铝铜合金的腐蚀破坏程度得到了明显 缓解。
2.3 电化学腐蚀行为
图6所示为铸态及超细晶铝铜合金块材在10 mmol/L氯化钠溶液中浸泡初期稳定开路电位下测得的EIS Nyquist谱及等效电路图。由图6可看出,铝铜合金试样表面混合钝化膜的厚度、致密度及稳定性在一定程度上决定合金在氯化钠侵蚀介质中的耐蚀性能。可通过EIS Nyquist曲线来评价铝铜合金的混合钝化膜的电化学特性(见图6(a)),铸态及超细晶铝铜合金在氯化钠溶液浸泡初期的Nyquist曲线由两部分组成,即中高频段的容抗弧及低频段的感抗弧。曲线中低频感抗弧的出现,说明铝铜合金在浸泡初期试样表面的钝化膜已开始发生一定程度的腐蚀破坏。根据文 献[15],容抗弧的直径可直观地表征钝化膜的极化电阻,容抗弧的直径越大,钝化膜极化电阻越高,钝化膜耐蚀性越好。很明显,超细晶铝铜合金试样的容抗
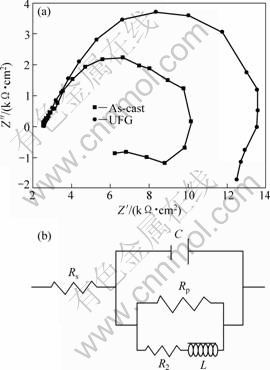
图6 铸态及超细晶铝铜合金在10 mmol/L NaCl溶液中的EIS Nyquist谱及等效电路图
Fig.6 EIS nyquist plots (a) and equivalent circuit electrochemical impedance spectra (b) of as-cast and UFG Al-Cu alloys in 10 mmol/L NaCl solution
弧的直径远大于铸态试样的容抗弧的直径。鉴于Nyquist曲线中高频容抗弧及低频感抗弧特性,本文作者在Randles R—C等效电路基础上中加入感抗元件来拟合铝铜合金基体/混合钝化膜/氯化钠侵蚀介质构成的腐蚀体系的反应过程。利用ZSimpWin(USA)电化学阻抗频谱拟合软件结合如图6(b)所示的等效电路图进行拟合。拟合所得超细晶试样的混合钝化膜极化电阻Rp值为13.8 kΩ·cm2,远高于铸态试样混合钝化膜的极化电阻Rp值(7.3 kΩ·cm2)。从显著增大的Nyquist容抗弧直径及混合钝化膜极化电阻Rp值可以判断出,在NaCl溶液中超细晶铝铜合金试样钝化膜的耐蚀性能优于铸态试样钝化膜的耐蚀性。
图7所示为铸态及超细晶铝铜合金块材在10 mmol/L氯化钠溶液中动电位扫描极化曲线。由图7可看出,极化曲线在稳定开路腐蚀电位下测得,其中超细晶铝铜合金试样的开路腐蚀电位为-533.26 mV,正于铸态试样的开路腐蚀电位(-583.81 mV)。铸态及超细晶铝铜合金试样的动电位扫描极化曲线形状相同,说明两者在氯化钠溶液中具有相似的电化学腐蚀行为。MULLER和GALWELE[16]研究指出,铝铜合金在氯化钠溶液的电化学腐蚀行为为点蚀。2种试样在强极化条件下,均未表现出良好的钝化效果,在开始进行阳极极化时即发生点蚀破坏。因此,可用自腐蚀电位φc来表征铝铜合金的点蚀电位φp,从而来判断铝铜合金在氯化钠溶液中的点蚀热力学特性。即用点蚀电位φp表征合金的点蚀倾向,φp值越高,合金耐点蚀性能越好。超细晶铝铜合金的φp为-492 mV,远正于铸态试样的φp(-544 mV)。除可用φp来表征铝铜合金的点蚀热力学特性外,亦可用腐蚀电流密度Jc表征合金的腐蚀动力学特性。即用腐蚀电流密度Jc来判断合
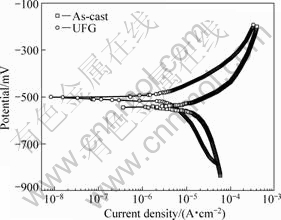
图7 铸态及超细晶铝铜合金在氯化钠溶液中的极化曲线
Fig.7 Potentiodynamic polarization curves of as-cast and UFG Al-Cu alloys in 10 mmol/L NaCl solution
金在侵蚀介质中的腐蚀速度。腐蚀电流密度越小,腐蚀速度越低,试样耐蚀性能越好。通过Tafel外推法测得2种试样的腐蚀电流密度。由于超细晶试样具有较低的阴极极化率和较大的阳极极化率,其腐蚀电流密度(10.9 μA/cm2)远小于铸态试样的腐蚀电流密度(23.1 μA/cm2)。从动电位扫描极化曲线中更正的点蚀电位、更小的腐蚀电流密度可以判断出,超细晶铝铜合金块材在NaCl溶液中的耐点蚀性能优于铸态铝铜合金块材的耐点蚀性。
3 讨论
一些研究表明,细化晶粒可以有效提高材料的耐蚀性,不仅可以降低材料的整体腐蚀速度,还可以缓解局部腐蚀破坏[17]。ECAP制备的超细晶纯Ti、纯Cu和工业纯Al均表现出比铸造金属更好的耐蚀性[8, 18]。从上述实验结果可以清楚地发现,采用ECAP制备的超细晶铝铜合金在晶粒尺寸得到显著细化的同时,其在氯化钠溶液中的耐点蚀性能也得到明显的提高。耐点蚀性能的提高应与超细晶铝铜合金特有的显微组织密切相关。鉴于铸造铝铜合金自身特殊的腐蚀机理,超细晶铝铜合金在氯化钠溶液中改善的点蚀行为应与形变α(Al)基体的耐蚀性和细化的θ相密切相关。
3.1 ECAP对α(Al)基体氧化膜的影响
铝是一种很活泼的金属,在结构金属材料中其热力学活性仅次于铍和镁。但是铝在许多氧化性介质、水、大气、部分中性溶液中均表现出较高的耐蚀性。这是因为铝在上述介质中,在表面上很快形成一层致密连续的氧化膜,当铝与水溶液接触时即会发生氧化,在试样表面形成AlOOH(即为Al2O3·H2O)水合氧化膜[19]:
Al+H2O→AlOH+H++e (1)
AlOH+H2O→Al(OH)2+H++e (2)
Al(OH)2→AlOOH+H++e (3)
总电极反应为:
Al+H2O→AlOOH+H++e (4)
AlOOH水合氧化膜具有一定的空隙,但是这一氧化膜具有很高的离子电流电阻,可有效阻止腐蚀而使铝在水溶液中表现出良好的钝化效果。AlOOH水合氧化膜与空气中形成的自生氧化膜构成了铝在水溶液中的混合氧化膜,一般情况下其厚度约为10 nm。当铝基体与氯化物溶液接触时,由于氯离子的存在,在氧化膜的局部薄弱位置,反应(1)之后进行的不是成膜反应而是阳极溶解反应:
AlOH+Cl-
AlOHCl+e (5)
AlOHCl+Cl-→AlOHCl2+e (6)
在阳极溶液反应的中间产物AlOHCl及最终腐蚀产物AlOHCl2具有较高的水溶性,促进氧化膜的阳极溶解。因此,对于铝铜合金,α(Al)基体表面的氧化膜在侵蚀介质中的稳定性决定了α(Al)基体的耐蚀性,氧化膜稳定性越高,则α(Al)基体耐蚀性越好。
众所周知,材料表面的氧化膜倾向于在一些晶体缺陷处优先形核生成[20]。从超细晶铝铜合金TEM显微组织可以观察到,ECAP大塑性变形不仅显著细化α(Al)基体晶粒,同时还使形变α(Al)晶体获得了大量的晶体缺陷,例如高比率的大角度晶界、高密度的晶内位错。形变α铝基体中大量高能晶体缺陷的存在,为超细晶铝铜合金提供了更多的氧化膜形核源。当超细晶试样表面与水溶液接触时,水合氧化膜的成膜反应将会更加剧烈,氧化膜的形成将更为迅速,所得氧化膜的厚度、致密度将优于铸造试样表面的氧化膜。文献[6]中报道了ECAP超细晶纯Ti表面快速生成钝化膜的类似现象。
EIS测试结果可有利证明ECAP引起的高能晶体缺陷对试样表面氧化膜的影响。得益于形变α(Al)基体内的大量高能晶体缺陷,在浸泡初期铝铜合金试样表面迅速形成体积比更高且更为致密的混合氧化膜层,从而使超细晶试样具有比铸态试样更大的容抗弧直径及拟合极化电阻值。我们亦可用上述结论来解释铸态及超细晶试样自腐蚀电位的差异。电化学测试浸泡初期,超细晶试样具有比铸态试样更正的开路腐蚀电位值,这一现象亦与试样表面氧化膜体积比的变化密切相关。α(Al)基体表面氧化膜具有很高的电阻值,在侵蚀介质中其电极电位远高于α(Al)基体的。由氧化膜和α(Al)基体所构成的混合电极电位在很大程度上决定于表面氧化膜。氧化膜所占体积比越高,则试样电极的电位越高。经过ECAP加工后,α(Al)基体的成分没有变化,但显微组织却发生了显著改变。由于ECAP大塑性变形所提供的大量高能晶体缺陷,使得形变α(Al)基体表面具有比铸态试样更高体积比的氧化膜,这样就使得超细晶试样在浸泡初期表现出比铸态试样更正的开路腐蚀电位。
3.2 ECAP过程中θ相的细化对铝铜合金耐点蚀性能的影响
铝铜系合金的腐蚀,主要是由θ相与α(Al)基体的电偶腐蚀所引起的[12]。图8所示为铸造态铝铜合金的SEM像及其能谱分析。从图8可知,θ相的铜含量远高于α(Al)基体的。由于θ相含有更多的铜原子,其在氯化钠侵蚀介质中的电极电位正于α(Al)基体的。在侵蚀介质中,θ相具有很好的稳定性,作为腐蚀电偶的阴极;而α(Al)基体电极电位低,作为腐蚀电偶的阳极。因此,铝铜合金的腐蚀破坏往往发生在α(Al)基体,且临近θ相的α(Al)基体会被优先腐蚀。根据“小阴极、大阳极”机制,阴极相尺寸的减小将显著削弱微观腐蚀电偶的腐蚀倾向,从而提高材料的耐蚀性[18]。从图2所示的超细晶铝铜合金显微组织可知,得益于多道次ECAP过程中大应变的逐渐累积,铸态铝铜合金中的粗大的网状θ相被完全细化成细小的θ相粒子,孤立而均匀地分布于α(Al)基体。从超细晶铝铜合金的TEM显微组织可知,部分θ相甚至已被细化成纳米颗粒。θ相阴极尺寸的减小将显著削弱阴极相的腐蚀促进作用,降低θ相与α(Al)基体所构成的腐蚀电偶的腐蚀倾向,从而提高铝铜合金的耐点蚀性能。图4所示的SEM像可有利证明ECAP过程中θ相细化对铝铜合金耐点蚀性能的提高作用。超细晶铝铜合金微观腐蚀破坏程度的降低应是由θ相的细化与α(Al)基体表
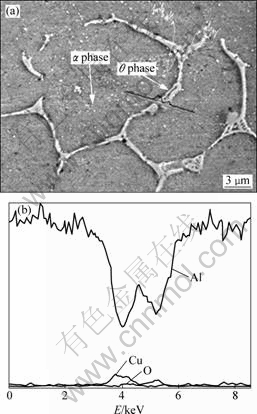
图8 铸态铝铜合金的SEM像及能谱分析
Fig.8 SEM image (a) and EDS spectrum (b) of as-cast Al-Cu alloy
面氧化膜耐蚀性能提高共同作用所引起的。
4 结论
1) 采用ECAP制备的超细晶铝铜合金块材的耐蚀性能优于铸态合金的,表现为全浸泡腐蚀中腐蚀破坏程度的降低,电化学测试浸泡初期更正的开路腐蚀电位(提高50.6 mV),电化学阻抗频谱测试中更高的极化电阻(Rp提高89%),动电位扫描极化测试中更正的点蚀电位(φp提高52 mV)及更小的腐蚀电流密度(Jc下降52.8%)。
2) 在ECAP大塑性变形过程中,α(Al)基体氧化膜稳定性的提高及θ相的细化是引起超细晶铝铜合金块材耐蚀性能提高的主要原因。
3) 在形变α(Al)基体中存在的大量高能晶体缺陷,如大角度晶界、高密度位错等,是引起α(Al)基体氧化膜耐蚀性能提高的主要原因。大量高能晶体缺陷的存在,使得α(Al)基体表面快速形成体积比更高、耐蚀性能更好的混合氧化膜。
4) ECAP大塑性变形使铸态合金中粗大的网状θ相的破碎、细化成孤立的细小θ相颗粒,均匀分布于α(Al)基体中。根据“小阴极、大阳极”机制,θ相尺寸的减小显著削弱了θ相与α(Al)基体所构成的微观腐蚀电偶的腐蚀倾向,从而提高了铝铜合金块材的耐蚀性能。
REFERENCES
[1] 潘复生, 张丁非. 铝合金及应用[M]. 北京: 化学工业出版社, 2006: 1-5.
PAN Fu-sheng, ZHANG Ding-fei. Aluminum alloy and its application[M]. Beijing: Chemical Industry Press, 2006: 1-5.
[2] SABIROV I, ESTRIN Y, BAENETT M, TIMOKJOMA I, HOGGSON P. Tensile deformation of an ultrafine-grained aluminium alloy: Micro shear banding and grain boundary sliding[J]. Acta Materialia, 2008, 56: 2223-2230.
[3] HU Lian-xi, LI Yu-ping, WANG Er-de, YU Yang. Ultrafine grained structure and mechanical properties of a LY12 Al alloy prepared by repetitive upsetting-extrusion[J]. Material Science and Engineering A, 2006, 422: 327-332.
[4] VALIEV R Z, ALEXANDROV I V. Nanostructured materials produced by severe plastic deformation[M]. Moscow, Russia: Logob Publishing, 2000, 272.
[5] MA Ai-bin, JIANG Jing-hua, SAITO NAOBUMI. Improving both strength and ductility of a Mg alloy through a large number of ECAP passes[J]. Material Science and Engineering A, 2009, 513/514: 122-127.
[6] STOLYAROV V V, ZHU Y T, ALEXANDROV I V, LOWE T C, VALIEV R Z. Grain refinement and properties of pure Ti processed by warm ECAP and cold rolling[J]. Material Science and Engineering A, 2003, 343: 43-50.
[7] PRADOS E, SORDI V, FERRANTE M. Tensile behaviour of an Al-4%Cu alloy deformed by equal-channel angular pressing[J]. Material Science and Engineering A, 2009, 503: 68-70.
[8] VINOGRADOV A, MIMAKI T, HASHIMOTO S, VALIEV R. Corrosion of ultra-fine grained copper fabricated by equal-channel angular pressing[J]. Scripta Materialia, 1999, 14: 319-326.
[9] FENG Xiao-ming, AI Tao-tao. Microstructure evolution and mechanical behavior of AZ31 Mg alloy processed by equal-channel angular pressing[J]. The Nonferrous Metals Society of China, 2009, 19(2): 293-298.
[10] KIM W J, CHUANG C S, MA D S, HONG S I, KIM H K. Optimization of strength and ductility of 2024 Al by equal channel angular pressing (ECAP) and post-ECAP annealing[J]. Scripta Materialia, 2003, 49: 333-338.
[11] FAN D R, ZHANG Z F, WU S D, HUANG C X, ZhAO N Q, LI J J. Effect of equal channel angular pressing on tensile properties and fracture modes of casting Al-Cu alloys[J]. Materials Science and Engineering A, 2006, 426: 305-313.
[12] WISLEI R O, LEANDRO C P, LEONARDO R G, AMAURI G. Corrosion behavior of hypoeutectic Al-Cu alloy in H2SO4 and NaCl solutions[J]. Acta Metallurgica Sinica, 2009, 22: 241-246.
[13] ZOQUI E J, ROBERT M H. Structural modifications in rheocast Al-Cu alloys by heat treatment and implications on mechanical properties[J]. Materials Processing Technology, 1998, 78: 198-203.
[14] SZKLARSKA-SMIALOWSKA Z. Pitting corrosion of aluminum[J]. Corrosion Science, 1999, 41: 1743-1767.
[15] LEE W J, PYUN Su-Ⅱ. Effects of sulphate ion additives on the pitting corrosion of pure aluminium in 0.01 M NaCl solution[J]. Electrochimica Acta, 2009, 28: 1901-1910.
[16] MULLER I L, GALWELE J R. Pitting potential of high purity binary aluminum alloys-I. Al-Cu alloys. Pitting and intergranular corrosion[J]. Corrosion Science, 1977, 17: 179-193.
[17] SCHINO A D, KENNY J M. Effects of the grain size on the corrosion behavior of refined AISI 304 austenitic stainless steels[J]. Material Science Letter, 2002, 21: 1631-1634.
[18] CHUNG M K, CHOI Y S, KIM J G. Effect of the number of ECAP pass time on the electrochemical properties of 1050 Al alloys[J]. Material Science and Engineering A, 2004, 366: 282-291.
[19] GORMAN J D, HUGHES A E, JAMIESON D, PATERSON P J K. Oxide formation on aluminium alloys in boiling deionised water and NaCl, CeCl3 and CrCl3 solutions[J]. Corrosion Science, 2003, 45: 1103-1124.
[20] AUST K T, ERB U, PALUMBO G.. Interface control for resistance to intergranular cracking[J]. Material Science and Engineering A, 1994, 176: 329-334.
(编辑 李艳红)
收稿日期:2009-09-01;修订日期:2010-04-09
通信作者:马爱斌,教授,博士;电话:025-83787239;E-mail:aibin-ma@hhu.edu.cn