J. Cent. South Univ. Technol. (2011) 18: 1063-1067
DOI: 10.1007/s11771-011-0804-5
Hydrogen permeability of slags containing calcium fluoride
DONG Yan-wu(董艳伍)1, 2, JIANG Zhou-hua(姜周华)1, LIANG Lian-ke(梁连科)1, LI Zheng-bang(李正邦)2
1. School of Materials and Metallurgy, Northeastern University, Shenyang 110004, China;
2. Central Iron and Steel Research Institute, Beijing 100081, China
? Central South University Press and Springer-Verlag Berlin Heidelberg 2011
Abstract: To investigate the hydrogen permeability of calcium fluoride used for electroslag remelting (ESR) process, “Gas-slag- metal” osmosis process under argon atmosphere saturated with water vapor at 318 K was used to study the hydrogen permeability of slag containing calcium fluoride. The results indicate that the conventional slag, consisting of 70% CaF2 and 30% Al2O3, has the lowest hydrogen permeability. A parameter EH was proposed for evaluation of the hydrogen permeability of slags containing calcium fluoride. The hydrogen permeability decreases with increasing EH to a certain extent. An appropriate choice of slag for the ESR process can be obtained. These results also suggest that the hydrogen pick-up in steel after remelting might be reduced when a slag with low hydrogen permeability is used.
Key words: electroslag remelting; hydrogen permeability; diffusion; calcium fluoride; slag
1 Introduction
Hydrogen is an extremely harmful element present in the forging of ingots, especially large ingots [1-4]. However, the hydrogen content is difficult to control during the electroslag remelting (ESR) process in open air. An important source of hydrogen is water vapor in the atmosphere that is transferred via the molten slag into the metal bath [5]. The hydrogen permeability of the slag results in a continuous increase of hydrogen content during the remelting process. The hydrogen permeability of the slag dominates the resulting hydrogen content of the steel, especially when the remelting is carried out in a moist atmosphere. Therefore, the choice of slag is very important for controlling the hydrogen content in steel produced by ESR.
KULIKOV and IODKOVSKII [5] and ROMANOV et al [6] studied the hydrogen permeability of standard ESR fluxes. However, data for the hydrogen permeability of slag containing calcium fluoride are still scarce. Although some researches [7-14] concerning hydrogen behavior were carried out, little effective data was obtained for calculating the hydrogen permeability because the molten pool in the ESR varied with time. In addition, all the results mentioned above are obtained far back in the past, and no fresh and further results exist recently.
The purpose of the present study is to investigate the hydrogen permeability of slags containing calcium fluoride under argon atmospheres saturated with water vapor at 318 K, which are often used for the ESR process at present. “Gas-slag-metal” osmosis process under argon atmosphere saturated with water vapor at 318 K was used to study the hydrogen permeability of slag containing calcium fluoride. The influencing factors are discussed and the results obtained will be helpful in choosing slags for the ESR process, and consequently controlling the hydrogen content in steel.
2 Experimental
Before all experiments, the bulk slags were prepared. Slag materials used in the experiment are analytical reagents and masses were weighed using a high-precision electronic balance. Slags charged in an alumina crucible were calcined at 1 123 K for 4 h after thorough mixing in an agate mortar. The alumina crucible was then stored in a desiccator before the experiment. Experiments were carried out with six slag mixtures, as listed in Table 1.
Generally, the basicity of CaO/SiO2 was adopted in steelmaking slag, which consists of a small amount of CaF2. However, slag for electroslag remelting usually contains a large amount of CaF2 without any addition of SiO2. Therefore, the optical basicity was used to estimate the basicity of the ESR slag. Analysis shows that both the basicity of CaO/SiO2 and the optical basicity have a great impact on the hydrogen permeability of slag containing calcium fluoride. For this reason, two different methods of basicity calculations were considered in this work. Equation (1) is the method for calculating the optical basicity:
(1)
where Xi=(Vi/2)·ni·Ni/∑[(Vi/2)·ni·Ni], Vi is the charge number of negative ion of the i-th component, ni is the number of negative ions, Ni is the mole fraction of the i-th component, Λi represents the optical basicity of the i-th component and Λ is the optical basicity.
Table 1 Compositions of slags
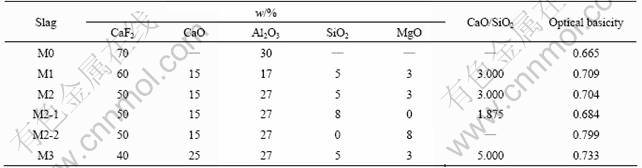
The hydrogen permeability was determined by the method of “gas-slag-metal” osmosis process. The average permeability within 5 min at the beginning of the process was looked as the hydrogen permeability of relevant slag. The experimental apparatus is illustrated in Fig.1. The heating unit is made of molybdenum disilicide.
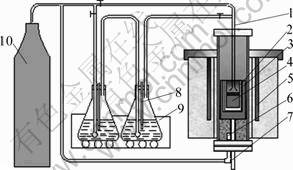
Fig.1 Experimental apparatus for hydrogen permeability measurement: 1—Alundum tube; 2—Crucible of magnesia; 3—Crucible of graphite; 4—Molten steel; 5—Heating unit; 6—Shielding gas; 7—Thermocouple; 8—Thermometer; 9—Thermostatted water bath; 10—Argon gas
A thermostatted water bath was used to control the temperature of the water, which produced water vapor at a certain temperature. By adjusting the temperature of the thermostat water bath, the water pressure in the H2O-Ar mixture could be controlled. A glass tube was inserted into the water to provide good contact between the water and argon gas so that argon gas had the equilibrium water partial pressure when it left the water during the actual experiment. The H2O-Ar mixture was introduced into the chamber through an alundum tube, the tip of which was about 50 mm above the liquid pool.
At first, a sample of 5% Cr cold-rolled steel of about 800 g surrounding by a 0.3 mm-thick molybdenum film was placed into a magnesia crucible. Then, the crucible was placed in a graphite crucible to prevent any leakage of molten steel. The power was switched on and the crucible was placed in the chamber. The furnace was heated to the experimental temperature at a rate of 6 K/min.
The argon, used as the shielding gas, was introduced into the chamber from the top and bottom over the period when the chamber temperature rose from 573 K to 1 823 K. The depth of liquid metal, D1, was measured with a molybdenum wire after the steel had been melted. The slag samples, weighing 80 g each, were introduced onto the liquid metal with a special device when the chamber temperature had reached 1 833 K. The temperature of the liquid pool was maintained at (1 823±1) K until the slag sample had been melted and then the total depth of liquid, D2, was measured.
After a period of stabilization, the firstly hydrogenated specimen was extracted immediately with a quartz tube of 4 mm in inner diameter and then H2O-Ar gas mixture was introduced onto the surface of the liquid slag at constant pressure and constant flow rate. Timing began simultaneously. The mixed gas was achieved by argon flowing through the thermostatted water bath at 318 K. The mixed gas flow rate was maintained at 1.67×10-5 m3/s so that the molten slag surface could be kept in an atmosphere with a partial pressure of water.
The hydrogen specimen was taken from the molten steel, quenched in liquid nitrogen, and then stored in it. Several specimens were taken in the following 20 min. Specimens were analyzed immediately after weighing the samples. The whole experiment process lasted for about 4 h.
3 Results and discussion
3.1 Results of hydrogen permeability
The specimens taken from the liquid pool were analyzed with a LECO TCH600 nitrogen-oxygen- hydrogen determination apparatus. To confirm the reliability of the experimental data, at least two analyses were performed for every specimen. Figure 2 shows the curve of average hydrogen content as a function of time.
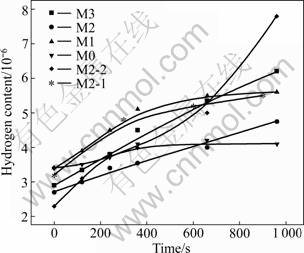
Fig.2 Curves of hydrogen content as function of time
It can be seen from Fig.2 that the hydrogen content is low at the beginning of the experiment and gradually increases with time.
The differences of initial hydrogen content between different samples must be ascribed to experimental uncertainties, which may be due to the different time more or less from the beginning of the melting of the steel to the starting time of the experiment. In addition, different compositions of slag samples used may be one of the reasons. It is very difficult to obtain the same initial hydrogen content for every heating, even for the same slag. The differences of the ultimate hydrogen content in the steel samples shown in Fig.2 may be due to the distinct partition coefficient between different slags and steel [15].
The hydrogen permeability at the beginning of the process is described as a function of the thickness of the slag film and the cross-sectional area as
(2)
where JH is the increase of hydrogen per unit time, in mol/s; PH is the hydrogen permeability, in mol/(m·s); S is the cross-sectional area, in m2; L represents the thickness of the slag film, which can be calculated from D2-D1.
The hydrogen permeabilities of different slag samples, as illustrated in Fig.3, are calculated using Eq.(2). The results obtained are almost coincident with the hydrogen permeability measurements on fluoride free slags, from 1.56×10-10 to 9.42×10-9 mol/(m·s), reported by LIU et al [11].

Fig.3 Results of hydrogen permeability measurements for different slags
3.2 Discussion
The results indicate that the optical basicity has a significant influence on the hydrogen permeability. Slag M2-2 has the highest optical basicity of about 0.799, which leads to the highest hydrogen permeability of 7.03×10-10 mol/(m·s); in contrast, slag M0 has the lowest optical basicity of 0.665, which results in the lowest permeability of 0.80×10-10 mol/(m·s) among the slags. It seems that higher optical basicity is correlated with higher permeability, except for the slag M2-1.
The difference of hydrogen permeability can be explained using the basicity value w(CaO)/w(SiO2) for slags M2 and M2-1 because the other components, except MgO and SiO2, are identical. The relationship between hydrogen permeability and basicity coincides with the relationship obtained by BOGATENCOV [16], which is also a parabola opening downward. The permeability reaches a peak value when the basicity is approximately 1.75. The closer the basicity is to the peak, the higher the hydrogen permeability is. This can be used to explain the value of hydrogen permeabilities of slags M2 and M2-1.
Slag M2-2 has the highest hydrogen permeability because it clearly has the highest basicity and is prone to absorb water vapor from the atmosphere. Slag M3 can not be compared with slags M2, M2-1 and M2-2 due to the differences of CaF2 content.
CaF2, CaO and Al2O3 are the main components of slag used for electroslag metallurgy. Figure 4 shows the distribution coefficient of hydrogen between iron and slags [17]. It can be seen that the distribution coefficient (H)/[H] between the slag and metal decreases monotonically with decreasing CaF2 and CaO contents. However, the distribution coefficient (H)/[H] decreases with increasing Al2O3 content. A higher distribution coefficient (H)/[H] is prone to be influenced by the water vapor in the atmosphere.
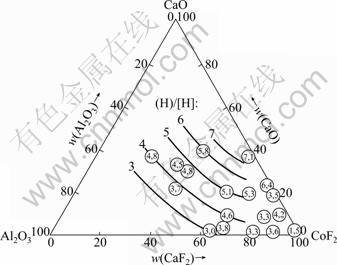
Fig.4 Partition coefficient of hydrogen for iron and slag melt (Number in circle means distribution coefficient of hydrogen between iron and slags)
In addition, the results obtained by CHATTOPADHYAY and MZTCHELL [18] indicate that the activity of CaO increases with increasing the ratio of Al2O3 and CaO in the ternary CaF2-CaO-Al2O3 slag. Whether the activity of CaO increases with increasing the ratio of Al2O3 and CaF2 can be determined by further research. The higher the activity of CaO is, the higher the oxygen ion concentration is [13].
The oxygen ion reacts with H2O in the atmosphere above the liquid slag and transfers the hydrogen in the form of hydroxyl ion. The reaction at the gas/slag interface can be expressed as
{H2O}+(O2-)=2(OH-) (3)
The reaction is one of the important processes for the hydrogen permeability of slag. Therefore, we put forward a parameter EH defined as the sum of the values of w(Al2O3)/w(CaF2) and w(Al2O3)/w(CaO) in this work. It can be used to evaluate the extent of hydrogen permeability for slags M1, M2 and M3 due to the same constituents except CaF2, Al2O3 and CaO. However, we cannot evaluate the hydrogen permeability of slag M2-1 and M2-2 according to EH due to the additional compositions including SiO2 and MgO in them:
EH=w(Al2O3)/w(CaF2)+w(Al2O3)/w(CaO) (4)
Figure 5 shows the values of EH for slags M1, M2 and M3. According to Fig.3 and Fig.5, the hydrogen permeability decreases with increasing the value of EH. Therefore, it is possible to increase the value of EH by adjusting the slag composition in order to reduce the hydrogen permeability of ESR slags. The results obtained above will be helpful in choosing the perfect slag for ESR.
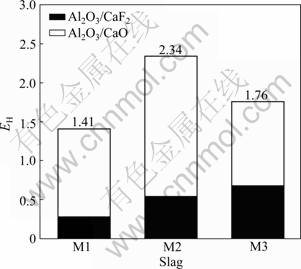
Fig.5 Evaluation index of hydrogen permeability
4 Conclusions
1) Conventional slag used for the ESR process consisting of 70% CaF2 and 30% Al2O3 has the lowest hydrogen permeability.
2) The hydrogen permeability increases monotonically with the increase of the optical basicity of the slag.
3) A parameter EH is put forward for the evaluation of the hydrogen permeability of slags containing calcium fluoride. The hydrogen permeability decreases with the increase of EH.
4) The relationship between the hydrogen permeability and basicity, w(CaO)/w(SiO2), forms a parabola such that the permeability reaches its peak value when the basicity is approximately 1.75. The hydrogen pick-up in steel after remelting may be reduced when a slag with low hydrogen permeability is used.
References
[1] PYUN S, LIE H G. Relationship between hydrogen-assisted crack propagation rate and the corresponding crack path in AISI 4340 steel [J]. Steel Research, 1990, 61(9): 419-425.
[2] ZHANG Y P, SHI D M, CHU W Y, QIAO L J, SHI Y L, ZHENG S L, WANG S B. Hydrogen-assisted cracking of T-205 maraging steel [J]. Materials Science and Engineering A, 2007, 471(1): 34-37.
[3] PISHKO R, MCKIMPSON M, SHEWMON P G. The effect of steelmaking on the hydrogen attack of carbon steel [J]. Metallurgical Transactions A, 1979, 10(7): 887-894.
[4] TAKAGI S, TERASAKI S, TSUZAKI K. A new evaluation method of hydrogen embrittlement fracture for high strength steel by local approach [J]. ISIJ International, 2005, 45(2): 263-271.
[5] KULIKOV A P, IODKOVSKII, S A. Investigation of behaviour of hydrogen in atmosphere-slag-metal system [J]. Steel in the USSR, 1985, 15(8): 378-379.
[6] ROMANOV O N, NOVOKHATSKII I A, KOZHUKHAR V Y, BELOV B F, BEREIHKO B I, MAZUR Y V. Hydrogen permeability of standard electroslag remelting fluxes [J]. Steel in the USSR, 1989, 19(7): 295-297.
[7] NOVOKHATSKII I A, BEREZHKO B I, KOZHUKHAR V Y, ROMANOV O N, KRAVCHENKO T G. Hydrogen content of electroslag remelting fluxes at different stages in their production [J]. Steel in the USSR, 1989, 19(5): 215-218.
[8] POCKLINGTON D N. Hydrogen pickup during electroslag refining [J]. Journal of the Iron and Steel Institute, 1973, 211(6): 419-425.
[9] JAUCH R, CHOUDHURY A, TINCE F, LEMOR W R. Electroslag remelting process at Roechling-burbach for heavy forging ingots of 2300 mm diameter [J]. Iron and Steelmaking, 1979, 6(2): 75-83.
[10] NAKAMURA Y, HARASHIMA R. Hydrogen contents of slag and ingot in the electroslag remelting process (ESR) [J]. Journal of the Iron and Steel Institute of Japan, 1977, 63(8): 1235-1243.
[11] LIU Pei-huan, FENG Qi-chen, XING Yu-lu. On the hydrogen permeability in molten CaO-SiO2-Al2O3-MgO slag system [J]. Journal of Northeastern University, 1985, 44(3): 61-66. (in Chinese)
[12] HASEGAWA M, MCLEAN A. Hydrogen dissolution in an iron melt from slag exposed to an atmosphere of controlled humidity [J]. Iron & Steelmaker, 1987, 14(5): 73-82.
[13] BRANDBERG J, SICHEN D. Water vapor solubility in ladle- refining slags [J]. Metallurgical and Materials Transactions B, 2006, 37(3): 389-393.
[14] MEDVEDEV E F. The structure connectivity factor as applied to the determination of the hydrogen permeability coefficient of glasse [J]. Glass Physics and Chemistry, 2006, 32(5): 565-573.
[15] BANYA S, HINO M, NAGASAKA T. Thermodynamics of CaO-based slags for refining of high purity steel [J]. The Japan Institute of Metals, 1995: 86-100.
[16] BOGATENCOV V F, КUROCHKIN К Т, UMRIHIN P V. Hydrogen permeability of basic slag [C]// Proceedings of the Higher Education Institutions Black Metallurgy. 1958: 13-20.
[17] ALLIBERT M, GAYE H, GEISELER J. Solubility of gases in liquid slags [M]. Germany: Verlag Stahleisen GmbH, 1995.
[18] CHATTOPADHYAY S, MITCHELL A. Thermochemistry of calcium oxide and calcium hydroxide in fluoride slags [J]. Metallurgical Transactions B, 1990, 21(8): 621-627.
(Edited by YANG Bing)
Foundation item: Project(50904015) supported by the National Natural Science Foundation of China; Project(N090402012) supported by the Fundamental Research Funds for Central Universities of China
Received date: 2010-04-09; Accepted date: 2011-01-14
Corresponding author: DONG Yan-wu, PhD; Tel: +86-24-83691689; E-mail: yanwu_dong@163.com