Microstructure and tensile properties of magnesium alloy modified by Si/Ca based refiner
DUAN Zhi-chao(段志超)1, SUN Yang-shan(孙扬善)1, WEI Yu(魏 宇)1,
DU Wen-wen(杜温文)1, XUE Feng(薛 烽)1, ZHU Tian-bai(诸天柏)2
(1. Department of Materials Science and Engineering, Southeast University, Nanjing 210096, China;
2. Nanjing Welbow Metals Co Ltd, Nanjing 211221, China)
Abstract: Microstructure and mechanical properties of pure magnesium and AZ31 alloy with Ca/Si based refiner addition were investigated. The results indicate that addition of Ca/Si based refiners to pure magnesium and AZ31 alloy results in remarkable microstructure refinement. With proper amount of refiner addition, the grain size in as cast ingots can be one order of magnitude lower than that without refiner addition. Small amount of refiner addition to AZ31 alloy increases both ultimate strength and yield strength significantly,while the ductility of the alloy with refiner addition is similar to that without refiner addition. Addition of refiner improves the deformability of AZ31 alloy and extruded or hot rolled specimens (rods or sheets) with refiner addition exhibit higher surface quality and mechanical properties than those without refiner addition.
Key words: magnesium alloy; AZ31 alloy; refinement; extrusion; rolling CLC number: TG146
Document code: A
1 INTRODUCTION
The use of magnesium in commercial applications has increased dramatically in recent years and the growth of magnesium products for structural applications has been projected to be around 12% per year for the next decade[1]. The increased demand, especially in household electric appliance and automobile parts, can be contributed to its low density, high specific strength and good castability[2].
The main methods in the industrial manufacturing of magnesium alloy products are the die casting and the semi-solid process, and the other methods, such as extrusion, forging and rolling, are rarely used[3]. One reason for this is its relatively poor formability and limited ductility in comparison with aluminum, copper and iron based alloys owing to its hexagonal close packed (HCP) structure. The traditional strengthening principles, such as solid solution strengthening, precipitation hardening and work hardening, are not very effective on improving mechanical properties of magnesium based alloys since the techniques related with the above principles are deleterious to the ductility of metallic materials. Therefore, grain size seems to be more important for magnesium-based alloys. High strength and ductility as well as good deformation formability can be attained from fine grained magnesium based alloy. In the present paper, Si/Ca based refiner was added to pure magnesium and AZ31 alloy. The grain sizes in the ingots with and without refiner addition were measured and as-cast microstructure of AZ31 alloy was also studied. Some AZ31 ingots were extruded and hot rolled, respectively, and the microstructure and mechanical properties of these extruded and rolled specimens under different conditions were investigated.
2 EXPERIMENTAL
The refiner containing Si, Ca and Al used in the present investigation was prepared in a crucible furnace as a master alloy. The mass ratio of Si to Ca in the refiner is 1.5∶1. Melting of magnesium and AZ31 alloy was conducted in a mild steel crucible under the protection of a mixed gas atmosphere of SF6(1%, volume fraction) and CO2(Bal.). The refiner was added when the temperature of the melt reached 720℃. After the refiner was dissolved, the melt was held at that temperature for several minutes then poured into permanent molds made of cast steel. As-cast specimens were directly cut from the ingots. Some AZ31 ingots were hot extruded into rods with diameter of 15mm, and the others were hot rolled to sheets with thickness of 2mm. Tensile tests were performed on specimens with and without refiner addition and microstructure observations of the alloys were conducted using optical microscopy(OM) and scanning electron microscopy(SEM), respectively. Micro-analysis and determination of crystal structure of precipitates were carried out by X-ray energy dispersive spectroscopy(XEDS) and X-ray diffractometry(XRD), respectively.
3 RESULTS
3.1 Microstructure
Fig.1 shows the grain structure of magnesium ingots with and without refiner addition. It can be clearly seen that the ingot without refiner addition has very coarse grain structure with columnar grains in the area near the edge and equiaxed grains in the central area. The average grain size in the central area is about 5-6mm, as shown in Fig.1(a). With 0.5%(mass fraction) of refiner addition, the grain structure of ingot is significantly refined and the average grain size in the equiaxed grain area decreases to 0.6-0.8mm.
The effect of refiner addition on the microstructure of AZ31 alloy is similar to that in pure magnesium. The as-cast microstructure of AZ31
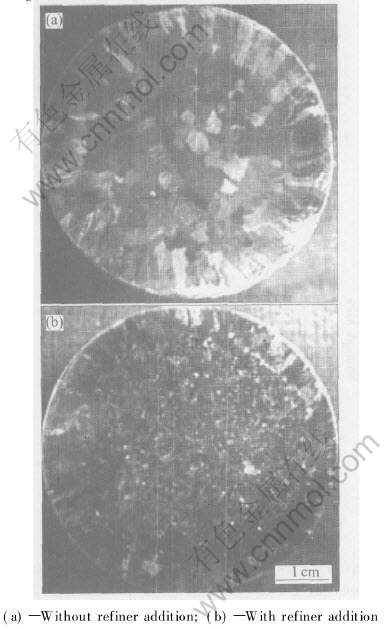
Fig.1 Grain structures of as cast magnesium ingots
alloy without refiner addition is also coarse (Fig.2(a)) and the β phase network distributes at gain boundaries. Fig.2(b) shows the as-cast microstructure of AZ31 with refiner addition. In comparison with Fig.2(a), the effect of grain refinement caused by the refiner is also apparent. SEM observations reveal some tiny particles in the as extruded alloy with refiner addition, as shown in Fig.3. Microanalysis performed on these particles indicates that the compositions of these particles are approximately Mg-45%Si(mass fraction). Fig.4 shows the XRD pattern taken from AZ31 alloy with refiner addition, in which all peaks are indexed as arising from two phases, α-Mg and Mg2Si, which has a cubic structure C1 (S.G. Fm3m). Thus, the particles shown in Fig.3 can be identified as Mg2Si.
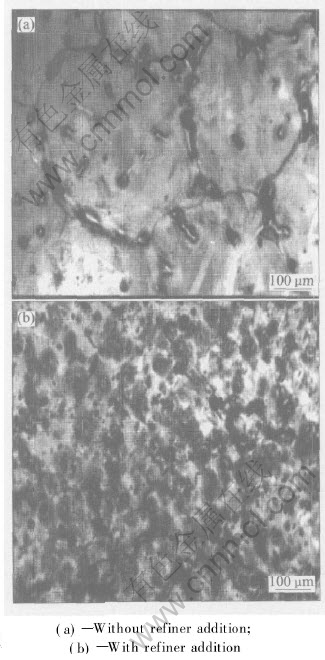
Fig.2 OM micrographs of as cast AZ31 ingots
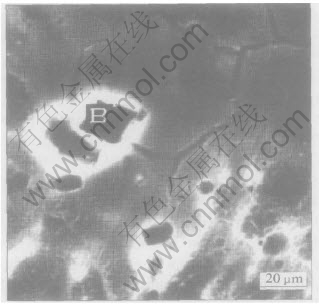
Fig.3 SEM micrograph showing Mg2Si particles in AZ31 alloy with refiner addition
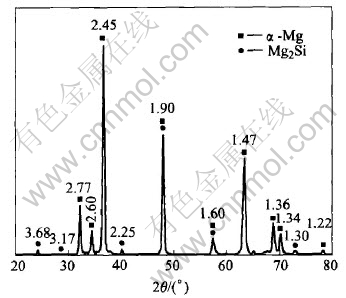
Fig.4 XRD pattern taken from AZ31 alloy with refiner addition
Hot extrusion of the alloys with and without refiner addition causes partially dynamic recrystallization as shown in Fig.5(a), however, it does not occur during hot rolling and finer grain structure is observed in as-rolled specimens as shown in Fig.5(b). The as-extruded and as-rolled structures of the alloys with and without refiner addition are similar; however, the deformability of the ingots with refiner addition is much better. The extruded rods and hot rolled sheets are crack free and show high smoothness on surface.
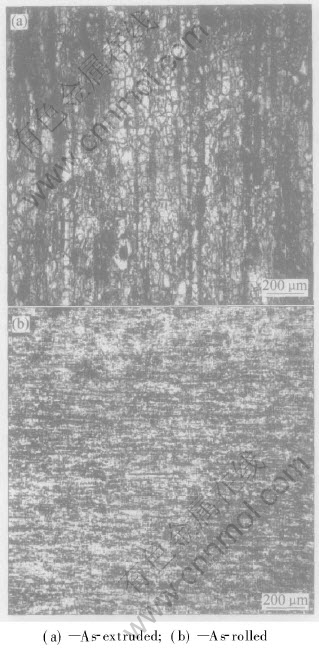
Fig.5 Microstructures of AZ31 alloy with refiner addition
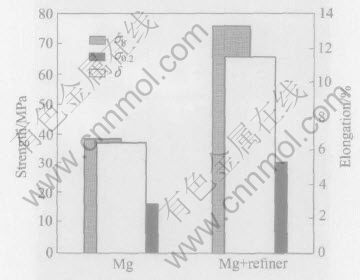
Fig.6 Tensile properties of as-cast magnesium specimen
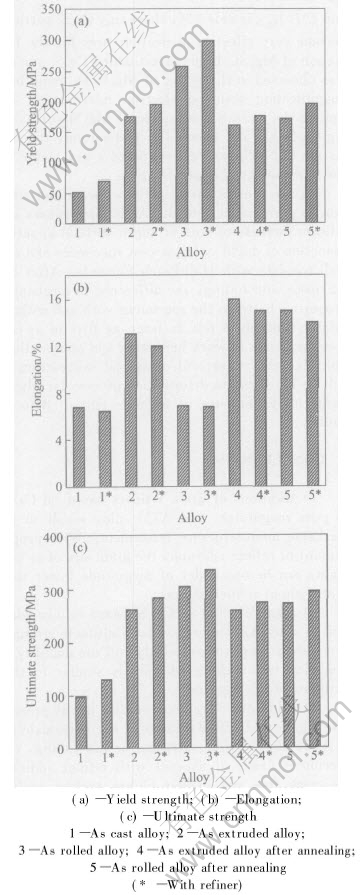
Fig.7 Tensile properties of AZ31 alloy with and without refiner addition
3.2 Tensile properties
Tensile properties of as-cast magnesium specimens cut from ingots with and without refiner addition are shown in Fig.6. It can be seen that not only strength but also ductility has remarkably increased with refiner addition. The improvement of mechanical properties caused by refiner addition has also been obtained in AZ31 alloy. Fig.7 illustrates the tensile properties of AZ31 alloy with and without refiner addition. For the specimens under all the conditions studied (as-cast, as-extruded and as-rolled), both ultimate strength and yield strength of the alloy have increased with refiner addition and the ductility of the alloy with refiner addition is similar to that without refiner addition. Annealing of as-extruded and as-rolled specimens results in the increase of ductility and slight reduction of ultimate strength and yield strength. The data of tensile properties of the specimens annealed at 250℃ are also shown in Fig.7.
4 DISCUSSION
Efforts have been made to search refiners for magnesium based alloys for several decades and zirconium has been found very effective on grain refinement for aluminum free magnesium alloys[4], but it can not be used in Mg-Al based alloys because of the reaction between Zr and Al. However, Mg-Al based alloys, such as AZ91, AZ31 and AM60 alloys, are most important magnesium alloys and have being used in approximately 90% of all magnesium products as structural materials. Therefore it is still necessary to develop new refiners suitable for Mg-Al based alloys. Recently, Liu et al[5] reported Al4C3-SiC/Al was effective on the Mg-Al-Zn alloys and Jin et al[6] , Eiji et al[7] declared that carbon addition was also able to result in grain refinement.
The mechanism of grain refinement can be described as a result of constitutional undercooling generated by the growth of a grain adjacent to a nucleant particles suspended in the melt[8-11]. There are two factors which can enhance the number of successful nucleation events. The first is the solute elements present in the melt and the other is the number and potency of the nucleant particles. The effect of solute elements on the grain refinement can be defined by the alloys growth restriction factor when the potency of the nucleant is very high. The growth restriction factor (GRF) is defined by[8]

where m is the slope of the liquidus line, c0 is the initial composition, and ki is the equilibrium partition coefficient for element i. A large GRF indicates that the growing crystal generates constitutional undercooling quickly and the liquid around the adjacent nucleants is therefore more quickly undercooled sufficiently to allow a stable nucleus to form on nucleant particles compared with anal-oy having a small GRF. Fig.8 shows the relation-
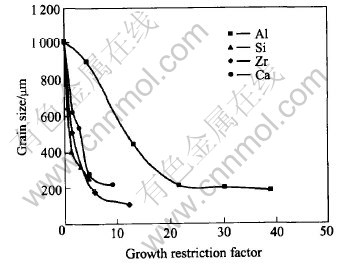
Fig.8 Relationship between grain size and growth restriction factor (GRF) of elements Al, Ca, Si and Zr for binary magnesium alloys[8]
ship between grain size and GRF of the elements Al, Ca, Si and Zr for binary magnesium alloys. It can be seen that both Ca and Si are much efficient elements on the grain refinement for magnesium alloys. This is well consistent with the results of the present work.
According to Mg-Ca and Mg-Si binary phase diagrams, the solubility of Ca and Si in the α matrix of magnesium is very low. Small amount of Si addition to magnesium results in the formation of Mg2Si interphase, which has a cubic C1 structure. Min[12] has calculated that the mismatch between the α-Mg and Mg2Si on some crystallographic planes with low indices and the results are listed in Table 1. It can be seen that the mismatches between (1122)Mg and (011)Mg2Si, (1010)Mg and (011)Mg2Si are 9.7% and 6.5% , respectively, lower than 12%. According to the theory proposed by Bramfitt[13] that the particles are very effective nucleation sites for heterogeneous nucleation during solidification if the mismatch between the matrix and particle is lower than 12% . In the present investigation, some tiny Mg2Si particles are found in SEM image (Fig.3), verifying that the nucleation sites in the melt of AZ31 alloy with Si/Ca based refiner addition are Mg2Si particles. On the other hand, Ca plays a role of modifying the morphology of Mg2Si particles. In the Mg-Al-Si based alloys, Mg2Si particles have a unique morphology, which is described as Chinese Script Type[14]. Small amount of Ca addition modifies the morphology of Mg2Si so that the mechanical properties of the alloy are improved[14, 15]. Min proposed that the modification of Mg2Si morphology is due to the formation of Ca2Si, which has a complex cubic C23 structure. When the temperature of melt contain-ing Si and Ca decreases, Ca2Si nuclei form in the
Table 1 Match factor of α-Mg matrix and Mg2Si phase in plane with low crystal factor[12]
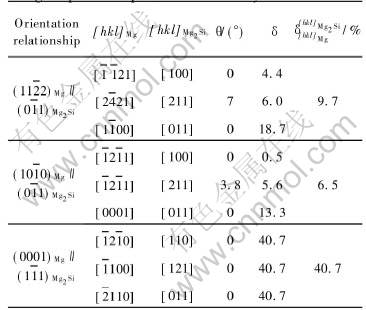
liquid first. As the mismatch between (010)Mg2Si and (010)Ca2Si is only 4%, these tiny Ca2Si particles become very effective nucleation sites for the formation of Mg2Si. In his investigation Ca2Si nucleus was observed in the center of Mg2Si by using high magnification scanning electron microscopy. Although the growth mechanism of Mg2Si surrounding Ca2Si has not been fully understood, the formation of Ca2Si can be considered a key factor for the morphology change of Mg2Si.
In the present investigation, the refiner addition to pure magnesium and AZ31 alloy causes significant increase of both strength without apparent reduction of ductility for as-cast specimens and this well consists with Hall-Patch Formula. After hot extrusion and rolling, the difference of mechanical properties between the specimens with and without refiner addition is not as large as that in as-cast specimens due to work hardening and recrystallization, but the refinement of as-cast microstructure will be beneficial to deformation process for Mg-Al based alloys because of improvement of deformability.
5 CONCLUSIONS
1)Additions of grain refiners based on Ca/Si to pure magnesium and AZ31 alloy result in remarkable microstructure refinement. With proper amount of refiner addition, the grain size of as-cast ingots can be one order of magnitude lower than that without refiner addition.
2) Small amount of Ca/Si based refiner addition to alloy AZ31 increases both ultimate strength and yield strength significantly and the ductility of the alloy with refiner addition is similar to that without refiner addition.
3) Additions of refiners studied in the present investigation effectively improve the deformability of AZ31 alloy. After extrusion or hot rolling, the specimens (rods or sheets) with refiner addition are crack free and exhibit higher surface quality and mechanical properties than those without refiner addition.
REFERENCES
[1]Magers D, Burssels J. Global outlook on the use of magnesium diecasting in automotive application[A]. Mordike B L, Kainer K U. Magnesium Alloys and Their Applications[C]. Wolfsburg, Germany, 1998. 105-112.
[2]Takamura H, Miyashita T, Kamegawa A, et al. Grain size refinement in Mg-Al-based alloy by hydrogen treatment[J]. Journal of Alloys and Compounds, 2003, 356-357(11): 804-808.
[3]Luo A, Renaud J, Nakatsugawa I, et al. Magnesium castings for automotive applications[J]. JOM, 1995, 47(7): 28-31.
[4]Polmear I J. Magnesium alloys and applications[J]. Materials Science and Technology, 1994, 10:1-15.
[5]LIU Yan-hui, LIU Xiang-fa, BIAN Xiu-fang. Grain refinement of Mg-Al alloys with Al4C3-SiC/Al master alloy[J]. Materials Letters, 2004, 58(7-8): 1282-1287.
[6]JIN Qing-lin, Eom J P, Lim Su-gun, et al. Grain refining mechanism of a carbon addition method in a Mg-Al magnesium alloy[J]. Scripta Materialia, 2003, 49(11): 1129-1132.
[7]Eiji Y, Yousuke T, Tetsuichi M, et al. Effect of pure carbon powder on grain refining of cast magnesium alloy AZ91[J]. Journal of Japan Institute of Light Metals, 2001, 51(11): 599-603.
[8]Dahle A K, Lee Y C, Nave M D, et al. Development of the as-cast microstructure in magnesium-aluminium alloys[J]. Journal of Light Metals, 2001, 1: 61-72.
[9]Hutt J E C, StJohn D H, Hogan L, et al. Equiaxed solidification of Al-Si alloys[J]. Mater Sci Technol, 1999, 15(5): 495-500.
[10]Hutt J E C, Dahle A K, Lee Y C, et al. Effects of growth restriction and effective nucleant potency on grain size and morphology in Al-Si and Al-Cu alloys[A]. Ecker C E. Light Metals: Proceedings of Sessions, TMS Annual Meeting[C]. Warrendale, PA, USA, 1999. 685-692.
[11]Easton M, StJohn D. Grain refinement of aluminum alloys: Part Ⅰ. The nucleant and solute paradigms—a review of the literature[J]. Metall Mater Trans A, 1999, A30: 1613-1623.
[12]MIN X G. Microstructure, Mechanical Properties and Creep Resistance of AZ91 Based Alloys[D]. Nanjing: Southeast University, 2002.
[13]Bramfitt B L. Effect of carbide and nitride additions on the heterogenous nucleation behavior of liquid iron[J]. Metall Trans, 1970, 1(7): 197-201.
[14]Luo A. Magnesium Automotive Applications[R]. Shanghai: Sinomag Die Casting Magnesium Seminar, 2001-08-26.
[15]Kim J J, Kim D H, Shin K S, et al. Modification of Mg2Si morphology in squeeze cast Mg-Al-Zn-Si alloys by Ca-P addition[J]. Scripta Materialia, 1999, 41(3): 333-340.
(Edited by YANG Bing)
Foundation item: Project(BE2002001) supported by the Natural Science Foundation of Jiangsu Province, China
Received date: 2004-10-08; Accepted date:2005-01-06
Correspondence: SUN Yang-shan, Professor; Tel: +86-25-83792454; E-mail: yssun@seu.edu.cn