DOI: 10.11817/j.issn.1672-7207.2019.06.003
70 t单管RH冶金传输行为的数值模拟
窦为学1, 2,雷洪3,朱苗勇1
(1. 东北大学 冶金学院,辽宁 沈阳,110819;
2. 敬业钢铁有限公司,河北 石家庄,040500;
3. 东北大学 材料电磁过程研究教育部重点实验室,辽宁 沈阳,110819)
摘要:为了深入了解70 t单管RH内的冶金传输过程,分别采用欧拉-欧拉方法、示踪剂输运方程和碳氧质量分数输运偏微分方程组描述RH内钢液流动行为、混匀过程和脱碳过程。数值模拟结果表明:随着真空度由250 Pa降低到50 Pa,循环流量和混匀时间保持不变,钢液中碳质量分数由81.8×10-6降低到34.3×10-6;随着底吹氩气量由100 L/min增大到500 L/min,循环流量由23.1 t/min增加到42.2 t/min,均混时间由179 s下降到100 s,钢液中碳质量分数由72.6×10-6下降到47.5×10-6。预测的脱碳曲线与工业实验数据符合良好;提高单管RH底吹氩气量,有利于提高循环流量,减少均混时间,降低钢液中碳元素质量分数。
关键词:单管RH;真空精炼;均混时间;脱碳;数值模拟
中图分类号:TF769.4 文献标志码:文献标识码:A 文章编号:1672-7207(2019)06-1284-07
Numberical simulation for metallurgical transfer in 70 t single snorkel RH
DOU Weixue1, 2, LEI Hong3, ZHU Miaoyong1
(1. School of Metallurgy, Northeastern University, Shenyang 110819, China;
2. Jingye Iron and Steel Limited Company, Shijiazhuang 040500, China;
3. Key Laboratory of Electromagnetic Processing of Materials, Ministry of Education, Northeastern University, Shenyang 110819, China)
Abstract: In order to get a deep insight into the metallurgical transfer process in 70 t single snorkel RH, Euler-Euler approach, tracer transfer model and partial differential equations for carbon and oxygen transfer were respectively applied to describe the fluid flow, mixing process, and decarburization process in RH. Numerical results show that, while the vacuum degree falls from 250 to 50 Pa, the circulation flow rate and mixing time almost remain unchanged, and the carbon mass fraction decreases from 81.8×10-6 to 34.3×10-6. While the ladle bottom blowing argon flow rate rises from 100 to 500 L/min, the circulation flow rate rises from 23.1 to 42.2 t/min, the mixing time decreases from 179 to 100 s, and carbon mass fraction decreases from 72.6×10-6 to 47.5×10-6. The predicted carbon mass fraction is in good agreement with the industrial experimental result. Increasing the flow rate of argon blown into the single snorkel RH is beneficial to increase the flow rate and reduce the mixing time and carbon mass fraction in liquid steel.
Key words: single snorkel RH; vacuum refining; mixing time; decarburization; numerical simulation
钢液真空循环脱气法是西德鲁尔钢铁公司(Ruhrstahl)和赫拉欧斯公司(Hereaeus)共同设计开发的一种钢液炉外精炼方法,简称RH法。为提高精炼效果,缩短精炼时间,提高生产效率,国内外许多冶金学者为RH精炼设备结构和操作进行了多项改进,如增加真空室高度、扩大浸渍管直径、将活动真空室改为固定真空室、增设多功能喷嘴[1],并开发了多种改进型号,如RH-OB,RH-PB,RH-KTB和RH-IJ。目前,RH已经成为具有脱碳、脱磷、脱硫、脱氧、脱氢、去夹杂物、调整钢液成分和升温等多种功能的精炼反应器,在超低碳钢和纯净钢生产方面发挥着重要作用。我国是研究单管RH(单嘴精炼炉)最早的国家[2-5]。1976年,大连钢厂在13 t单管RH上进行坦克轴钢脱氢实验。1992年,长城特殊钢厂四分厂在35 t 单管RH上进行轴承钢脱氧实验。2004年,武钢第三炼钢厂在250 t单管RH上进行2炉深脱碳实验。2008年,太钢第二炼钢厂在80 t单管RH上进行普碳钢、无取向硅钢等共143炉实验[2]。2011年,石钢在60 t单管RH上进行脱氢实验。在此期间,马钢开发扁平单管RH,首钢首秦公司也在110 t RH的基础上开发单管RH精炼技术[5]。2018年,敬业钢铁公司在70 t单管RH进行工业试生产。为改善DH脱气性能,日本新日铁公司也开展单管RH的研究工作[6]。1991年,八幡厂175 t DH(真空提升脱气精炼装置)被改造为单管RH,并取名为REDA (revolutionary degassing activator)[6]。到目前为止,日本有10多台单管RH处于运行状态,主要产品是低碳和超低碳不锈钢。与传统双管RH相比,单管RH具有结构简单、维护容易、精炼效率高等优点。鉴于单管RH将传统RH的上升管和下降管合并为一个大圆柱状浸渍管,吹氩方式由上升管的侧吹改为钢包底吹,因此,单管RH内钢液流动和冶金行为与传统RH存在较多差异。但是,现有的RH研究极少关注单管RH。为此,本文作者以敬业钢铁公司单管RH作为研究对象,通过数值模拟与现场实验相结合的方法,剖析单管RH内冶金传输过程,以便为有效地提高单管RH的冶金效率提供理论依据。
1 数学模型
1.1 RH流场数学模型
1.1.1 基本假设
1) RH内气相(氩气)和液相(钢液)的流动行为均是不可压缩牛顿流体的等温稳态流动;
2) 不考虑顶渣对钢液流场的影响,钢包和真空室的钢液面视为平面;
3) 氩气泡在运动过程中始终保持球形并且直径也保持恒定。
1.1.2 流场控制方程
RH内气液两相流动行为采用连续性方程、动量守恒方程和湍流k-ε模型来描述。为准确描述流动过程中氩气泡和钢液之间的相互作用,多相流模型选用欧拉-欧拉模型[7-8]。
氩气连续性方程:
(1)
钢液连续性方程:
(2)
式中:下标g和l分别表示氩气和钢液;α为流体体积分数,
;u为流体的速度,m/s;ρ为流体密度,kg/m3。
氩气动量方程:
(3)
钢液动量方程:
(4)
式中:p表示压力,Pa;g表示重力加速度,m/s2;μeff表示流体有效黏度,Pa·s;
表示氩气相对钢液相的动量交换,N/m3;
表示钢液相对氩气相的动量交换,N/m3。
基于多相流理论,各相之间的动量传输项M主要取决于曳力、Saffman升力、虚拟质量力、壁面润滑力和湍流耗散力等[8]。
根据JAKOBSEN等[9]的研究,氩气的有效湍流黏度为
(5)
钢液的有效湍流黏度为[10-11]
(6)
式中:μl为钢液的分子黏度,Pa·s;μl,t为钢液的湍流黏度,Pa·s;μg,t为气泡诱导湍流黏度,Pa·s,根据SATO模型[10-11]表示如下:
(7)
式中:
为模型常数,取值0.6。
1.1.3 边界条件
1) 氩气入口:将氩气入口设置为入口边界。具体而言,在氩气入口处,钢液体积分数设置为0,氩气体积分数设置为1,氩气流量则根据RH的实际吹氩量来确定。
2) 液面:当氩气泡到达液面时,氩气泡以上浮速度逸出液面;钢液不能流出液面边界,只能沿着液面向四周流动。
3) 壁面:壁面采用无滑移边界条件。在壁面处,速度的3个分量均设置为0,压力及含气率的法向梯度设置为0;在近壁区的节点则应用壁面函数法。
1.2 RH均混时间数学模型
RH混合效率可以用均混时间来描述[12]。冶金学者通常在RH反应器内脉冲加入一定量的示踪剂后,测量RH监测点处示踪剂质量分数随时间的变化。
1.2.1 基本假设
1) 示踪剂在钢液中的扩散是在等温条件下各向同性扩散。
2) 不考虑钢包液面波动和真空室液面波动对示踪剂输运的影响。
1.2.2 控制方程
在RH内,示踪剂在钢液中的传输行为通常采用示踪剂质量分数输运方程来描述。
(8)
式中:Ctracer为示踪剂质量分数;
;
。
1.2.3 初始条件和边界条件
在初始时刻,除了在钢包内壁和浸渍管外壁中间位置液面处脉冲加入示踪剂外,RH其他位置的示踪剂质量分数均设置为0。在示踪剂的混合过程中,示踪剂在壁面和自由液面处不发生扩散,即在壁面和自由液面处示踪剂质量分数梯度为0。为定量地描述示踪剂的混合过程,分析在监测点(示踪剂加入位置的液面下300 mm)处示踪剂质量分数随时间的变化,并选取监测点处示踪剂质量分数变化不超过示踪剂质量分数稳定值的±5%所需时间作为本工况下RH的均混时间[13-14]。
1.3 RH脱碳数学模型
脱碳是RH精炼的一个主要的冶金功能,也是冶金学者关注的重点内容[15-17]。近几十年来,冶金学者关注的RH脱碳数学模型有两大类:一类是基于质量衡算的均相模型,计算关于钢液本体脱碳、氩气泡表面脱碳等脱碳机制的常微分方程;另一类是基于钢液流场的碳氧质量分数输运偏微分方程组。
1.3.1 基本假设
1) 钢液脱碳存在3种反应机制:氩气泡表面脱碳、钢液内部一氧化碳本体脱碳和真空室自由液面脱碳[17-18];
2) 钢液中碳氧反应的限制环节取决于钢液内部碳元素和氧元素的传质[19-21];
3) 在真空室内,喷溅造成的钢液液滴群所产生的脱碳效果可以合并到真空室自由液面脱碳效果中;
4) 钢液内部一氧化碳本体脱碳速率正比于钢液中碳元素和氧元素的过饱和度[15-17,22];
5) 不考虑体系内钢渣界面反应等其他化学反应对RH内碳氧反应的影响;
6) 在初始时刻,钢液中碳和氧呈均匀分布状态;
7) 真空室和钢包的自由液面按平面处理;
8) 钢液脱碳反应在等温条件下进行。
1.3.2 碳氧质量分数守恒方程
钢液中碳元素质量守恒方程:
(9)
钢液中氧元素质量守恒方程:
(10)
式中:w(C)和w(O)分别为钢液中碳元素和氧元素的质量分数;DC,eff和DO,eff分别为钢液中碳元素和氧元素的有效扩散系数,m2/s;SC和SO分别为钢液中碳元素和氧元素的运输方程的源项,kg/(m3·s)。
在RH内,钢液脱碳的整个过程可以分为碳元素和氧元素向碳氧反应界面的传质、在反应界面处迅速发生碳氧反应、CO气体的生成和逸出这3个步骤[22-23]。由于钢液中碳氧反应速度很快,可以认为钢液中的碳元素和氧元素到达反应界面后,碳元素和氧元素的质量分数将迅速趋近于化学反应平衡时的质量分数。碳元素和氧元素的源项可采用下式表达。
(11)
(12)
(13)
(14)
(15)
式中:KC和KO分别为钢液中碳元素和氧元素的表观速率常数,s-1;w(C)e和w(O)e分别为反应界面处碳元素和氧元素的平衡质量分数;KCO为钢液中碳氧反应的平衡常数;SCO为熔池内一氧化碳本体脱碳源项;SAr为氩气泡表面脱碳源项;SVS为真空室自由液面脱碳源项。
1.3.3 初始条件和边界条件
在t=0时刻,钢液中碳元素和氧元素的质量分数分别设置为0.03%和0.045%;在RH的所有边界处,钢液中碳元素和氧元素质量分数在边界的法向梯度为0。
2 计算条件和求解方法
根据表1所示的RH尺寸建立三维实体模型,并考虑浸渍管耐火材料厚度的影响。然后,采用ICEM进行网格剖分,所形成的网格均为六面体网格,网格总数量约20万个。计算中所涉及的钢液和氩气的物性参数如表2所示,收敛标准为离散方程的残差,小于0.000 1。
表1 单管RH的主要几何参数
Table 1 Key geometric parameters of single snorkel RH mm
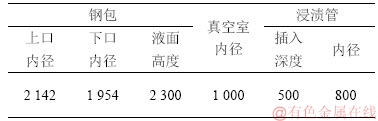
表2 钢液和氩气的物性参数
Table 2 Physical parameters of molten steel and argon gas
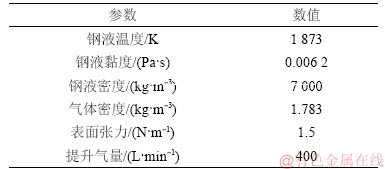
RH内传输过程是一个涉及化学反应、多相流动的复杂过程。整个计算全部采用流体力学软件CFX来完成,具体计算步骤如下:
1) 求解包含钢液和氩气两相的质量守恒方程、动量守恒方程和k-ε湍流模型,获得RH流场,得到RH循环流量。
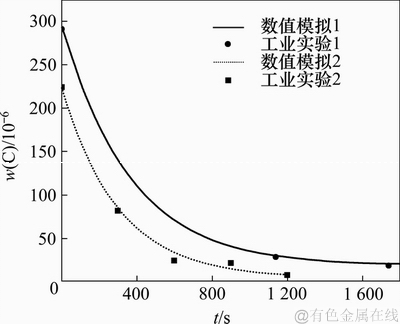
图1 在监测点处钢液的碳质量分数
Fig. 1 Carbon mass fraction in the molten steel at the monitoring point
2) 在RH流场已知的前提下,求解示踪剂输运方程,获得监测点处示踪剂随时间的变化曲线,得到均混时间。
3) 在流场已知的前提下,求解钢液中碳元素和氧元素的输运方程,获得监测点处的碳元素和氧元素随时间的变化曲线。
3 结果与讨论
3.1 模型验证
在监测点处钢液的碳质量分数如图1所示。由图1可见:2组单管RH真空脱碳过程预测值和工业实验结果之间符合良好。根据2组钢液中碳质量分数的预测结果,在RH真空处理前300 s,钢液脱碳速度最快,然后脱碳速度逐渐减缓。对第1组,真空脱碳的前300 s,钢液中碳元素质量分数由300×10-6快速地降低到141×10-6;又经过600 s,钢液中碳元素质量分数逐渐降低到72×10-6;再经过300 s,钢液中碳质量分数继续降到29×10-6。

图2 单管RH钢液流场
Fig. 2 Flow field of molten steel in single snorkel RH
3.2 RH流场
图2所示的RH内钢液流场分布具有如下特点:
1) 从钢包底部吹入的氩气泡,在浮力的作用下,在钢液中逐渐上升,并驱动钢液随之运动。
2) 单管RH采用偏心底吹方式。钢液上升流股并不是严格的垂直上升,而是在钢包内发生弯曲并偏向右侧的钢包内壁和浸渍管内壁。
3) 在氩气泡的驱动下,流动的钢液经浸渍管进入真空室后,钢液流速逐渐达到最大值;在真空室自由液面的约束下,钢液沿真空室液面向左流动,再沿真空室和浸渍管的另一侧向下流动,形成下降流股流回钢包;下降流股以较大的速度冲击钢包包底后,沿包底流向四周。最后,钢液在真空室、浸渍管和钢包内部形成一个范围较大的逆时针回流区。
4) 受氩气气泡提升的钢液并不是全部进入到浸渍管内部,部分流动的钢液向右流向钢包液面,形成一个范围较小的顺时针回流区。
5) 真空室钢液表面形成2个对称的回流区。
图3所示为不同时刻单管RH内钢液中碳元素的空间分布。经过600 s处理后,钢液中碳元素的分布具有如下特点:
1) 在真空室液面附近,碳元素质量分数较低。这是因为真空室内绝对压力较小,气泡在经过液面时会产生大量飞溅的小液滴,真空室液面波动变得比较剧烈,此处的碳氧反应剧烈。
2) 在吹氩口上方(即上升流股)区域,氩气体积分数较高,碳元素质量分数较低。这是因为在钢液内的每个氩气气泡都相当于1个小型真空室,是脱碳反应发生的重要场所。
3) 在下降流股区域,氩气体积分数变低,而碳元素的质量分数略有下降。这是因为氩气气泡在到达真空室液面后立即逸出,造成在下降流股区域内氩气气泡较少,碳氧反应场所较少,不利于钢液中碳氧反应的发生。下降流股区域碳质量分数下降是运动钢液将在上升流股区域发生碳氧反应的钢液输运到下降流股区域的结果。
4) 在浸渍管和钢包内壁之间的区域,碳质量分数较高,这是因为这些区域的氩气体积分数低,钢液流动缓慢,更新不及时。
3.3 RH工艺参数分析
在进行RH参数分析时,计算的基准参数如下:真空度为100 Pa,浸渍管直径为800 mm,浸渍管插入深度为500 mm,吹氩量400 L/min,RH处理时间为1 200 s。混匀时间、脱碳时的碳质量分数和氧质量分数均是在监测点处获得。
表3所示为真空度对单管RH冶金行为的影响。总体而言,在目前真空室真空度变化范围内对真空室液面高度影响较小,因此,在其他条件不变时,RH的循环流量和监测点处的混匀时间基本保持不变,分别为37.3 t/min和115 s。
图4所示为真空室压力对钢液脱碳和脱氧的影响。由图4可见:真空度的改变会对脱碳产生较大的影响。当RH的处理时间为1 200 s时,若真空度由50 Pa上升到250 Pa,则监测点处的碳元素质量分数由34.3×10-6上升到81.8×10-6;而监测点处的最终氧元素质量分数由95.7×10-6上升到151.9×10-6。这是因为真空度下降,造成化学反应平衡时钢液中碳氧元素质量分数积的减小,因此,造成钢液中碳元素和氧元素质量分数迅速下降。在不同真空度下,钢液终点碳元素质量分数和氧元素质量分数存在明显差异,这是因为真空度直接影响碳氧反应的平衡碳元素质量分数和平衡氧元素质量分数。
表4所示为不同吹氩量下RH冶金特性。随着吹氩量增加,RH循环流量逐渐增加,混匀时间依次减小。当RH的吹氩量由100 L/min提高到500 L/min时,循环流量增加0.8倍,均混时间约下降44%。这是因为增加吹氩量会提高气泡提升钢液的能力,从而加快钢液的流动,提高了RH对流输运的能力,减小混匀时间。
表4表明,当RH的吹氩量由100 L/min提高到500 L/min时,进行真空处理1 200 s后,监测点处碳元素质量分数由72.6×10-6下降到47.5×10-6。这是因为吹氩量的增加能够促进氩气泡表面的脱碳,其脱碳过程如图5所示。从图5可见:随着吹氩量的增加,不同吹氩量下钢液终点碳元素质量分数和氧元素质量分数之间的差异逐渐缩小。这是因为增加吹氩量有助于改善碳氧反应的动力学条件,能够尽快地达到化学平衡。
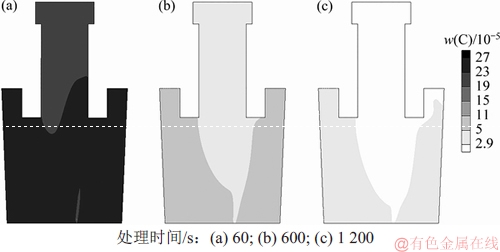
图3 单管RH内钢液中碳质量分数空间分布
Fig. 3 Spatial distribution of carbon mass concentration of molten steel in single snorkel RH
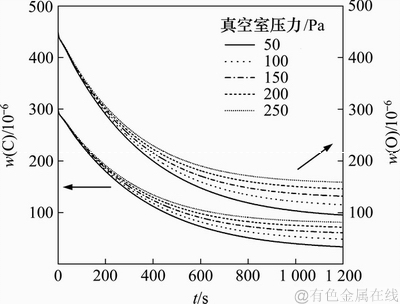
图4 真空室压力对钢液脱碳脱氧的影响
Fig. 4 Effect of vacuum pressure on decarburization and deoxidation in molten steel
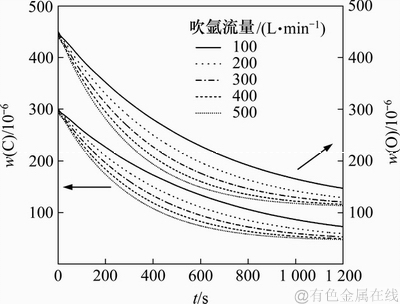
图5 吹氩量对钢液脱碳脱氧的影响
Fig. 5 Effect of argon flow rate on decarburization and deoxidation in molten steel
表3 不同真空度下RH冶金特性
Table 3 Effect of vacuum pressure on RH metallurgical behaviors
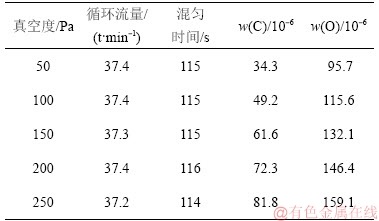
4 结论
1) 数学模型的脱碳曲线与实验数据符合良好,说明数学模型能够准确地预测RH脱碳过程。
2) 随着真空度由250 Pa降低到50 Pa,循环流量和混匀时间保持不变,但钢液中碳元素、氧元素质量分数降低。经1 200 s真空处理后,钢液中碳元素质量分数由81.8×10-6降低到34.3×10-6,氧元素质量分数由159.1×10-6降低到95.7×10-6。
3) 提高底吹氩气量,有利于增大循环流量,降低钢液中碳质量分数。随着底吹氩量由100 L/min增大到500 L/min,循环流量由23.1 t/min增加到42.2 t/min;均混时间由179 s下降到100 s;经1 200 s真空处理后,钢液中碳元素质量分数由72.6×10-6下降到47.5×10-6,钢液中氧元素质量分数由146.7×10-6下降到113.3×10-6。
表4 不同吹氩量下RH冶金特性
Table 4 Effect of argon flow rate on RH metallurgical behaviors
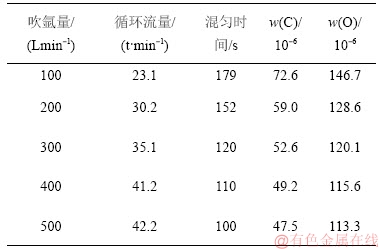
参考文献:
[1] SEMURA K, MATSUURA H. Past development and future prospects of secondary refining technology[J]. Tetsu to Hagane, 2014, 100(4): 456-471.
[2] 陈泽民. 80 t 单嘴精炼炉生产实践[J]. 山西冶金, 2015, 38(1): 59-60.
CHEN Zemin. Production practices of 80 t single mouth refining furnace[J]. Shanxi Metallurgy, 2015, 38(1): 59-60.
[3] 刘晓峰. 我国单嘴真空精炼炉技术的开发与实践现状[J]. 重钢技术, 2017, 30(1): 22-31.
LIU Xiaofeng. Development and practice of single snorkel refining furnace technology in China[J]. CISC Technology, 2017, 30(1): 22-31.
[4] 段建平, 张永亮, 杨学民, 等. 80 t单嘴真空精炼炉冶金功能的生产实验分析[J]. 特殊钢, 2012, 33(1): 26-29.
DUAN Jianping, ZHANG Yongliang, YANG Xuemin, et al. Analysis of commercial production test on metallurgical functions of an 80 t single snorkel vacuum refining furnace[J]. Special Steel, 2012, 33(1): 26-29.
[5] 成国光, 芮其宣, 秦哲, 等. 单嘴精炼炉技术的开发与应用[J]. 中国冶金, 2013, 23(3): 1-10.
CHENG Guoguang, RUI Qixuan, QIN Zhe, et al. Development and application of single snorkel refining furnace[J]. China Metallurgy, 2013, 23(3): 1-10.
[6] KITAMURA S, AOKI H, MIYAMOTO K, et al. Development of a novel degassing process consisting with single large immersion snorkel and a bottom bubbling ladle[J]. ISIJ International, 2000, 40(5): 455-459.
[7] CHEN Gujun, HE Shengping, LI Yugang, et al. Investigation of gas and liquid multiphase flow in the Rheinsahl-Heraeus(RH) reactor by using the Euler-Euler approach[J]. The Journal of the Minerals, Metals & Materials Society, 2016, 68(8): 2138-2148.
[8] ZHU Bohong, LIU Qingcai, KONG Ming, et al. Effect of interphase forces on gas-liquid multiphase flow in RH degasser[J]. Metallurgical and Materials Transactions B, 2017, 48(5): 2620-2630.
[9] JAKOBSEN H A, GREVSKOTT S, SVENDEN H F, et al. Modeling of vertical bubble-driven flows[J]. Industrial & Engineering Chemistry Research, 1997, 36(10): 4052-4074.
[10] SATO Y, SEKOGUCHI K. Liquid velocity distribution in two-phase bubble flow[J]. International Journal of Multiphase Flow, 1975, 2(1): 79-95.
[11] SATO Y, SADATOMI M, SEKOGUCHI K. Momentum and heat transfer in two-phase bubble flow-I. Theory[J]. International Journal of Multiphase Flow, 1981, 7(2): 167-177.
[12] ZHU Bohong, CHATTOPADHYAY K, HU Xunpu, et al. Optimization of sampling location in the ladle during RH vacuum refining process[J]. Vacuum, 2018, 152: 30-39.
[13] RUI Qixuan, JIANG Fang, MA Zhuang, et al. Effect of elliptical snorkel on the decarburization rate in single snorkel refining furnace[J]. Steel Research international, 2013, 84(2): 192-197.
[14] LING Haitao, ZHANG Lifeng. Investigation on the fluid flow and decarburization process in the RH process[J]. Metallurgical and Materials Transactions B, 2018, 49(5): 2709-2721.
[15] TAKAHASHI M, MATSUMOTO H, SAITO T. Mechanism of decarburization in RH degasser[J]. ISIJ International, 1995, 35(12): 1452-1458.
[16] WEI Jihe, ZHU Deping. Mathematical modeling of the argon-oxygen decarburization refining process of stainless steel: part I. mathematical model of the process[J]. Metallurgical and Materials Transactions B, 2002, 33(1): 111-119.
[17] PARK Y G, YI K W. A new numerical model for predicting carbon concentration during RH degassing treatment[J]. ISIJ International, 2003, 43(9): 1403-1409.
[18] GENG Dianqiao, ZHENG Jinxing, WANG Kai, et al. Simulation on decarburization and inclusion removal process in the Ruhrstahl-Heraeus (RH) process with ladle bottom blowing[J]. Metallurgical and Materials Transactions B, 2015, 46(3): 1484-1493.
[19] ZHAN Dongping, ZHANG Yangpeng, JIANG Zhouhua, et al. Model for Ruhrstahl-Heraeus(RH) decarburization program[J]. Journal of Iron and Steel Research International. 2018, 25(4): 409-416.
[20] CHEN Gujun, HE Shengping. Circulation flow rate and decarburization in the RH degasser under low atmospheric pressure[J]. Vacuum, 2018, 153: 132-138.
[21] YOU Zhimin, CHENG Guoguang, WANG Xinchao, et al. Mathematical model for decarburization of ultra-low carbon steel in single snorkel refining furnace[J]. Metallurgical and Materials Transactions B, 2015, 46(1): 459-472.
[22] GENG Dianqiao, LEI Hong, HE Jicheng. Decarburization and inclusion removal process in single snorkel vacuum degasser[J]. High Temperature Materials and Processes, 2017, 36(5): 523-530.
[23] ZHANG Jiongming, LIU Liang, ZHAO Xinyu. Mathematical model for decarburization process in RH refining process[J]. ISIJ International, 2014, 54(7): 1560-1569.
(编辑 秦明阳)
收稿日期: 2018 -12 -24; 修回日期: 2019 -02 -13
基金项目(Foundation item):国家自然科学基金与宝钢联合资助项目(U1460108)(Project(U1460108) supported by the National Natural Science Foundation of China and Shanghai Baosteel)
通信作者:雷洪,博士,教授,从事高品质钢的精炼和连铸理论与工艺研究;E-mail: leihong@epm.neu.edu.cn