
Effect of ball milling time on microstructure and properties of
Laves phase NbCr2 alloys synthesized by hot pressing
XIAO Xuan(肖 璇)1, 2, LU Shi-qiang(鲁世强)1, HU Ping(胡 平)1, HUANG Ming-gang(黄铭刚)1, M. W. FU3
1. School of Materials Science and Engineering, Nanchang Hangkong University, Nanchang 330063, China;
2. College of Electromechanical Engineering, Nanjing University of Aeronautical and Astronautics,
Nanjing 210016, China;
3. Department of Mechanical Engineering, The Hong Kong Polytechnic University, Hung Hom,
Kowloon, Hong Kong, China
Received 18 July 2008; accepted 9 February 2009
Abstract: Laves phase NbCr2 alloys with a composition of Nb-66.7Cr (molar fraction, %) were prepared by mechanical alloying and hot pressing. The microstructures and properties of the Laves phase NbCr2 alloys, prepared from elemental niobium and chromium powders under various ball milling time by hot pressing at 1 250 ℃ for 0.5 h, were investigated. The results indicate that if the ball milling time is longer than 40 h, the synthesizing reaction of Laves phase NbCr2 can be accomplished much sufficiently. Then the nearly full-dense Laves phase NbCr2 alloys can be prepared by hot pressing from ball milled powders with more than 40 h. The hot pressing sample with homogeneous and fine microstructure made from 40 h ball milled powders has the optimum microstructure and properties. It has a relative density of 98.1%, Vickers hardness of 11.4 GPa, compress strength of 1 981 MPa and fracture toughness of 4.82 MPa?m1/2. The effect of fine grain toughening is fully realized.
Key words: Laves phase NbCr2; mechanical alloying; hot pressing; microstructure; mechanical properties
1 Introduction
The drive of developing novel high-temperature structural materials used for aero-engine applications is due to the increase of the thrust-to-weight ratio through elevating the engine operating temperature. The service temperature of Ni-based superalloy has reached about 80%-90% of its melting temperature, thus it is very difficult to further increase the working temperature of this alloy. Intermetallic compound, however, provides a feasible solution for the increment of working temperature. The intermetallic compound NbCr2 with topologically close packed structures is expected to be able to work at a temperature much higher than the service temperature of conventional superalloys due to its advantageous properties, in particular the high melting point (1 770 ℃), relatively low density (7.7 g/cm3), good creep resistance at high temperature, and the potential high oxidation resistance and hot-corrosion resistance. These excellent properties make the Laves phase NbCr2 alloy an attractive material for aero-engine applications[1-4].
Although Laves phase NbCr2 alloy has a great potential in the novel high-temperature structural materials, the conventional casting technique for preparing NbCr2 can cause metallurgical defects such as composition segregation, heterogeneous microstructure and coarse grain, which is harmful to its properties, especially the toughness. The room- temperature fracture toughness of the casting Laves phase NbCr2 is only about 1.2 MPa?m1/2[5]. And its practical application is thus hindered by the severe room-temperature brittleness[6]. The use of mechanical alloying(MA), however, can significantly achieve atomic mutual mixture in solid state to reduce composition segregation and simultaneously refine grain size to the micro and/or nano level[7]. All of these build a basis of producing ultra-fine grained Laves phase NbCr2 alloys by subsequent hot pressing(HP). The fine grained alloys with plenty of grain boundaries lead to fine grain toughening and make it possible to improve the room- temperature ductility of Laves phase NbCr2.
LU et al[8] investigated the influence of MA on synthesizing of Laves phase NbCr2 by solid phase thermal reaction and found that MA technique not only provided an approach for obtaining milled powders with microcrystalline/nanocrystalline structure, but also resulted in the decrease of the solid phase reaction temperature from 1 200 ℃ for original elemental powders to 900 ℃ for 20 h ball milled powders. These provide a foundation for this study on fabricating ultra-fine grained NbCr2 alloys with higher toughness by using MA and HP techniques. In this method, the key issue for obtaining ultra-fine grained NbCr2 alloys is to retain small grains and control excessive grain growth from nanocrystalline structured MA powders during HP process. XIAO et al[9-10] investigated the influence of hot pressing time and temperature on the structure and properties of Laves phase NbCr2. However, another important processing parameter, ball-milling time that also influences the microstructure and properties of the alloy, has not yet been studied based on the available literatures. In this work, the effect of ball milling time on the microstructure and properties of NbCr2 alloys was investigated. The appropriate ball milling time based on the required optimum microstructure and properties was determined. The results and findings in this research were expected to provide a guideline for the fabrication of Laves phase NbCr2 alloys or NbCr2-based composite materials with high strength and toughness.
2 Experimental
The original Cr and Nb powders with particle size of 147 nm and purity of more than 99% and 99.5%, respectively, were employed. Based on the stoichiometric composition of Laves phase NbCr2, the pure Cr and Nb elemental powders were blended. The MA process was carried out in a high energy ball-grinding mill QM-ISP2-CL with a ball-to-powder mass ratio of 13?1. The rotating speed of ball-grinding mill was 400 r/min. The volume of the stainless-steel vial was 500 mL. The prepared and mixed powders were sealed in the vial together with ball milled medium. The vial was then evacuated to a vacuum of about 5 Pa and then filled with argon gas. The vacuuming and argon filling process was conducted three times to ensure that the real vacuum condition was obtained in such a way that the oxidation of the mixed powders during the MA process could be avoided. In addition, the interval of the ball milling time of 10 h was determined and the ball milling time was increased up to 70 h. In order to prevent the formation of a thin coating of powders on the vial wall during milling, it is necessary to open the vial, knock down the powders adhered to the vial wall and then load the powders in the vial again according to the above approach.
Following the MA process, the MA powders were subsequently placed in a graphite mould mounted in a vacuum sintering furnace and pressed in a vacuum atmosphere under an applied pressure of 45 MPa. Uniaxial compression was conducted with temperature of 1 250 ℃ and time of 0.5 h[9-10]. The HP samples were then cooled in the furnace spontaneously. The vacuum system could then be turned off only after the temperature was down to 200 ℃. This is to avoid the sample oxidation at high temperature. The densities of the consolidated samples were determined based on the water immersion of Archimedean principle and the relative densities were calculated. The hardness and fracture toughness tests were conducted by using an HV-10 Vickers hardness tester under loads of 9.8 N and 98 N, respectively. The average values of the hardness were calculated based on five sampling measurements. The fracture toughness was calculated and its average values were decided based on three sample measurements. The following equation derived by Anstis according to elasto-plasticity fracture mechanics is used to calculate the fracture toughness of the alloy[3,11]:
=A(E/H)1/2p/C3/2 (1)
where
is the fracture toughness (MPa?m1/2); E is the elastic modulus (GPa), which is assumed to be 218 GPa for Laves phase NbCr2 alloys according to Refs.[12-13]; H is Vickers hardness (GPa); p is the load, which is taken as 98 N in this work; C is the half of the radial crack from the center of the indent to the crack tip (mm); and A is a constant, which is taken as 0.02 for relatively brittle materials. Furthermore, supposing that the capital letter B represents one half of the indent diagonal length, Eq.(1) is available only under the conditions of both C≥2B and the crack length less than 1/10 of the sample thickness. The room temperature compression properties of the consolidated samples were evaluated by using the WDW-100 electronic universal material testing machine. The phase constitutions of the alloys were investigated by X-ray diffraction(XRD) in a D8 ADVANCE diffractometer. The microstructures of HP samples were characterized by QUANTA 200 scanning electron microscope(SEM) and more details were obtained by HITACHI H-800 electron transmission microscope(TEM) operated at 200 kV.
3 Results and discussion
3.1 Relative density and optical microstructures
Fig.1 shows the relative density of the bulk samples hot pressed at 1 250 ℃ for 0.5 h made from stoichiometric Nb-66.7Cr powders prepared by ball milling. As shown in Fig.1, the 10 h ball milled consolidated sample has much lower relative density of 92.1%. When the ball milling time is increased up to 20 h, the relative density of the sample is increased significantly. With the further increase of the ball milling time, the relative density increases steadily. However, if ball milling time exceeds 40 h, there is no effect of this increase on the relative density of the samples, which is a stable value of about 98% and nearly fully dense. Fig.2 shows the optical microstructures of the samples with different ball milling times; and those of the samples ball milled for other time are similar to Fig.2(c). It can be found from Fig.2 that there exist plenty of irregular and unclosed pores in the 10 h ball milled sample. With an increase of ball milling time, the pores are reduced significantly. The pores of the 20 h ball milled sample are reduced quite obviously and 40 h ball milled samples are nearly fully dense and have almost no pore.
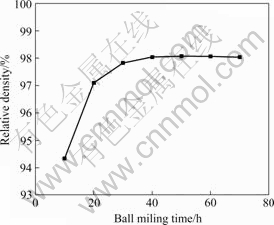
Fig.1 Effect of ball milling time on relative density of samples hot pressed at 1 250 ℃ for 0.5 h
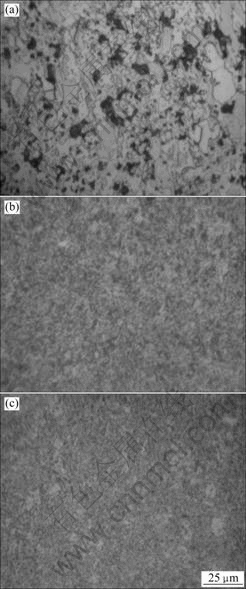
Fig.2 Optical images of samples ball milled for various time followed by hot pressing at 1 250 ℃ for 0.5 h: (a) 10 h; (b) 20 h; (c) 40 h
Furthermore, OHTA[14] obtained the powder metallurgy powders made by mechanically milling the arc-melted casting products with just-stoichiometric composition, and prepared highly dense samples through hot-pressing at 1 500 ℃ under 50 MPa for 2 h. In the present work, much highly dense Laves phase NbCr2 alloy can be prepared from the more than 40 h MA powders, made from elemental chromium and niobium powders via hot pressing at 1 250 ℃ for 0.5 h. The HP temperature and time are reduced greatly compared with the conventional hot consolidation process. This is due to the effect of mechanical activation from MA technique. During the MA process, the grain sizes of powders reach a nanometer level; the high density crystal defects and huge lattice strains are created; and the atomic array disorder is generated on the surfaces of powders and grain boundaries[7-8]. All of these microstructure changes are helpful for shortening the diffusion distance of the atoms, increasing diffusion channels and enhancing the number of diffusion atoms. The MA process facilitatesthe activated solid phase thermal reaction and sintering process. The higher consolidation temperature and longer HP time may result in the coarse grains of the NbCr2 alloy hot pressed at 1 500 ℃ for 2 h. However, after the reaction synthesizing temperature and the consolidation temperature and time are all reduced through the MA activating treatment, the Laves phase NbCr2 alloy with ultra-fine grained structures can be generated.
In addition, there is less influence of the increase of ball milling time exceeded 40 h on the relative density of the samples, which is a stable value of about 98% and the samples are nearly fully dense. These could be due to the fact that the ball milling time affects the refinement extent of the Nb and Cr powders. The powders were refined and activated remarkably at the stage of MA. However, the quite high surface energies would result in the refinement of powders to a certain extent to be adsorbed and adhered to each other over again. In the case of the determined ball milling process, the ball milling efficiency was fixed at a particular level. With respect to reducing the process time, the appropriate ball milling time of 40 h is suggested in order to prepare highly dense Laves phase NbCr2 alloy.
3.2 Electron microscope microstructures and phase changes
Fig.3 shows the secondary electron SEM images of the samples hot pressed at 1 250 ℃ for 0.5 h from the 10 h, 20 h and 40 h ball milled Nb-66.7Cr powders, and those of the other time ball milled samples are similar to Fig.3(c). As shown in Fig.3(a), many pores appear and the microstructure is coarse and non-uniform. The microstructures of more than 20 h ball milled samples are very fine and uniformly distributed like the connected net. These highly dense samples have only a few tiny spherical pores. It is in a good agreement with the above results about the relative density (see Figs.2(b) and (c)). Furthermore, Fig.4 presents the TEM image of the sample from 20 h ball milled Nb-66.7Cr powders. It can be seen that the smallest grain size is about 87 nm and the mean grain size is about 248 nm. Although the grain sizes do not reach the nanometer level, they are at the ultrafine level.
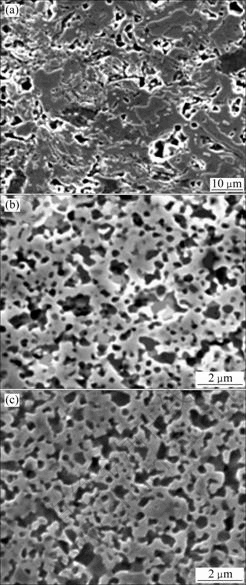
Fig.3 SEM images of samples hot pressed at 1 250 ℃ for 0.5 h from Nb-66.7Cr powders ball milled for different time: (a) 10 h; (b) 20 h; (c) 40 h
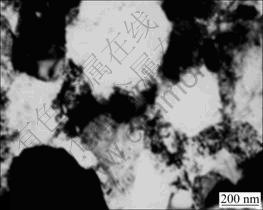
Fig.4 TEM image of sample hot pressed at 1 250 ℃ for 0.5 h from Nb-66.7Cr powders ball milled for 20 h
With respect to the results given in the Ref.[15], the effect of ball milling time on the synthesis of Laves phase NbCr2 through solid phase thermal reaction was investigated and the Laves phase NbCr2 could not be synthesized by the Nb and Cr elemental powders during 50 h ball milling process. This process resulted in the non-equilibrium supersaturated solid solution with nanocrystalline structure, and then the NbCr2 intermetallics were synthesized sufficiently under 3 h annealing solid phase thermal reaction at 900 ℃ from ball milled powders. Fig.5 presents the XRD patterns of the consolidated samples from the 10 h, 20 h and 40 h ball milled Nb-66.7Cr powders. It can be found that the synthesizing reaction of NbCr2 could be carried out but not accomplished from the 10 h ball milled powders. This is due to the fact that the most intense peaks of Nb and Cr overlapped with the diffraction peaks of NbCr2 have a bit high relative intensities (see Fig.5(a)). In the XRD pattern of the 20 h ball milled sample by the same HP process, the diffraction relative intensities of the most intense peaks of Nb and Cr reduce significantly (see Fig.5(b)). These indicate that the reaction of synthesizing NbCr2 is conducted sufficiently. In the same way, with the increase of ball milling time to 30 h, all peaks in the XRD pattern of the sample by the same HP process are those of the Lave phase NbCr2. Meanwhile, the diffraction peaks of Nb and Cr disappeared absolutely (see Fig.5(c)). These results show that the thermal reaction of the synthesized NbCr2 is conducted extensively and completely and the fabrication of single phase NbCr2 alloy is feasible under this condition.
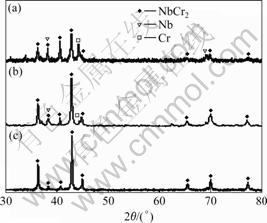
Fig.5 XRD spectra of 10 h (a), 20 h (b), and 40 h (c) ball milled samples hot pressed at 1 250 ℃ for 0.5 h
The comparison analysis of the XRD patterns indicates that the amount of storage energies in the milled powders varies depending on the ball milling time. With the increase of the ball milling time, the storage energies in the powders get much larger and the reaction activated energies which are required for the synthesis of NbCr2 get much smaller. Therefore, by the same HP process and with the increase of ball milling time, the thermal reaction of synthesizing NbCr2 is conducted more sufficiently. As for the X-ray spectra of the 50 h ball milled sample, we found that the spectra are similar to those of the 40 h ball milled sample significantly. All of these indicate that the thermal reaction of synthesizing NbCr2 by hot pressing at 1 250 ℃ for 0.5 h could be ensured completely on the condition of 40 h ball milling time.
3.3 Room temperature mechanical properties
Fig.6 shows the relationship between the ball milling time and the ultimate strength and Vickers hardness of the samples. There is no plastic deformation in all the samples during the room-temperature compression test. As shown in Fig.6, in the initial 40h balling milling time, the Vickers hardness values are much high as the ball milling time increases. The Vickers hardness of the 10 h ball milled consolidated sample is only 7.0 GPa. However, the Vickers hardness of the 40 h ball milled sample increases up to 11.4 GPa. This may be attributed to the more sufficient synthesizing reaction of NbCr2 and the augmented relative densities with the increase of the ball milling time. Furthermore, when the ball milling time exceeds 40 h, the Vickers hardness variation is much smaller with the prolongation of ball milling time. As the ball milling time increases from 10 h to 20 h, the ultimate strength of the samples increases remarkably, as shown in Fig.6. With the continuous increase of ball milling time, the ultimate strength increases gradually. The ultimate strength of the 40 h ball milled sample is up to 1 981 MPa, and when the ball milling time exceeds 50 h, the ultimate strength is reduced evidently. The lower strength of the 10 h ball milled sample is due to the fact that the synthesizing reaction of Laves phase NbCr2 is not conducted sufficiently and the sample with a few residual Nb and Cr solid solutions has a lower relative density. However, the gradual enhancement of the samples with the ball milling time from 20 h to 40 h is caused by the more sufficient synthesizing reaction and the much higher relative densities.
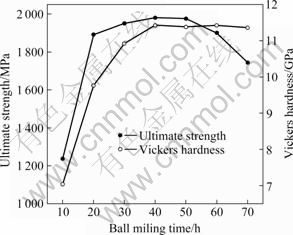
Fig.6 Effect of ball milling time on ultimate strength and Vickers hardness of samples hot pressed at 1 250 ℃ for 0.5 h
After the 50 h ball milling, the reduction of the ultimate strength may be due to the fact that the powders milled for the longer time could reach a higher activated extent and facilitate the reaction with the gas in the air after opening the milling vial and knocking down the adherent powders. The reaction may produce oxide impurities. In addition, the longer time ball milling would introduce more Fe impurities from the attrited stainless-steel vial wall into the powders. These impurities are not useful to the compression properties of the alloys[7-16]. The surface scanning energy spectrum analysis for the 70 h ball milled sample indicates that a trace of Fe and O elements exists in the sample. However, these trace impurities had not been examined in the X-ray spectra due to the much lower content.
Fig.7 shows the relationship between the ball milling time and the fracture toughness of the samples. The fracture toughness of the 10 h ball milled sample could not be examined since the relative density was quite low and the full cracks could not be obtained because the pores blocked the crack propagation. As shown in Fig.7, the 30 h and 40 h ball milled samples have the fracture toughness of 4.91 MPa?m1/2 and 4.82 MPa?m1/2, respectively. There is a little difference between the two values. The values are increased significantly compared with the fracture toughness values by about 1.2 MPa?m1/2[5] for the casting single phase NbCr2 alloy and 2 MPa?m1/2[14] for the hot pressed NbCr2 alloy made from the NbCr2 pre-alloyed powders. The fracture toughness of the 20 h ball milled sample is the highest which has the indentation and pointed cracks, as shown in Fig.8. In this scenario, the condition for indentation tests, viz, C≥2B, is not met. This means that the crack propagation could be controlled effectively in such a way that the fracture toughness value of this sample could be more than 4.7 MPa?m1/2. The fracture toughness reduces slightly with further increasing the ball milling time up to 70 h. This could be caused by the trace impurities in the samples.
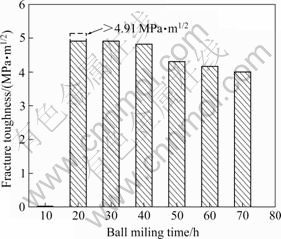
Fig.7 Effect of ball milling time on fracture toughness of samples hot pressed at 1 250 ℃ for 0.5 h
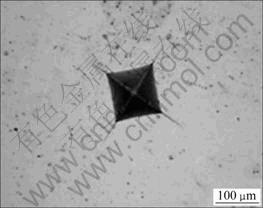
Fig.8 Indentation and pointed cracks of sample hot pressed at 1 250 ℃ for 0.5 h from Nb-66.7Cr powders ball milled for 20 h
The above results and discussion indicate that the optimum ball milling time of 40 h is suggested in order to obtain single-phase NbCr2 alloys with the better combination of properties.
The significant increase of the fracture toughness of the Laves phase NbCr2 alloys fabricated by MA and HP techniques may be due to the following reasons. Firstly, the preferable fracture toughness of alloy is attributed to the ultrafine and uniform microstructure. Figs.2-4 show that the more than 20 h ball milled samples have homogeneous microstructure and the mean grain sizes reach the sub-micron level. The cracks in the ultrafine grains can be branched and deflected effectively in such a way that the initial cracks propagate more difficultly. More energy is needed for the fracture process. All of these result in the enhancement of the fracture toughness. In addition, the ultrafine grained structure produces a great deal of grain boundaries and the diffusion coefficients of metal elements are relatively high. Many diffused shortcuts exist on the grain boundaries. These shortcuts make a few initial tiny cracks disappear quickly during the deformation process. Therefore, the crack growth and propagation can be avoided to a certain extent. This contributes to the fine grain toughening[17]. However, the conventional casting technique for preparation of Laves phase NbCr2 unavoidably introduces the metallurgical defects such as composition segregation, heterogeneous microstructure, and coarse grains, which are harmful to its properties, especially for the toughness. Thus, it can be seen that the MA and HP for preparing Laves phase NbCr2 alloy is an effective method due to the significantly improving room temperature fracture toughness.
4 Conclusions
1) The nearly full dense Laves phase NbCr2 alloys were prepared by HP at 1 250 ℃ for 0.5 h from the more than 40 h ball milled Nb-66.7Cr powders. The relative density of the samples is high up to 98.1%. The HP consolidated temperature and time are reduced remarkably by mechanical activation.
2) The solid phase synthesizing reaction of the Laves phase NbCr2 alloy fabricated from the 10 h ball milled Nb-66.7Cr powders cannot be fully accomplished. However, the synthesizing reaction from the 20 h ball milled powders is conducted sufficiently and the Laves phase NbCr2 alloy can be synthesized to a great degree from the over 40 h ball milled powders.
3) The microstructures of the more than 20 h ball milled samples are very fine and uniformly distributed. The mean grain size of the sample hot pressed at 1 250 ℃ for 0.5 h from the 20 h ball milled Nb-66.7Cr powders is about 248 nm, which reaches the sub-micron level.
4) The Laves phase NbCr2 alloy with the better properties is fabricated by HP at 1 250 ℃ for 0.5 h from the 40 h mechanically alloyed Cr-Nb powders. The alloy has a Vickers hardness of 11.4 GPa, an ultimate strength of 1 981 MPa and a fracture toughness of 4.82 MPa?m1/2. Its room temperature fracture toughness is increased greatly compared with that of the Laves phase NbCr2 prepared by conventional ingot metallurgy. The effect of the fine grain toughening is fully realized in this process.
References
[1] CHAN K S, DAVIDSON D L. The fracture resistance and crack-tip micromechanics of in-situ intermetallic composites [J]. JOM, 1996, 9: 62-67.
[2] TAKEYAMA M, LIU C T. Microstructure and mechanical properties of Laves-phase alloys based on Cr2Nb [J]. Mater Sci Eng A, 1991, 132: 61-66.
[3] THOMA D J, NIBUR K A, CHEN K C, COOLEY J C, DAUELSBERG L B, HULTS W L, KOTULA P G. The effect of alloying on the properties of (Nb, Ti)Cr2 C15 Laves phases [J]. Mater Sci Eng A, 2002, 329/331: 408-415.
[4] KAZANTZIS A V, AINDOW M, JONES I P, TRIANTAFYLLIDIS G K, HOSSON J T M D. The mechanical properties and the deformation microstructures of the C15 Laves phase Cr2Nb at high temperatures [J]. Acta Materialia, 2007, 55: 1873-1884.
[5] LIU C T, ZHU J H, BRADY M P, MCKAMEY C G, PIKE L M. Physical metallurgy and mechanical properties of transition-metal Laves phase alloys [J]. Intermetallics, 2000, 8: 1119-1129.
[6] KUMAR K S, PANG L, HORTON J A, LIU C T. Structure and composition of Laves phases in binary Cr-Nb, Cr-Zr and ternary Cr- (Nb, Zr) alloys [J]. Intermetallics, 2003, 11: 677-685.
[7] SURYANARAYANA C. Mechanical alloying and milling [J]. Progress in Materials Science, 2001, 46: 1-184.
[8] LU Shi-qiang, HUANG Bai-yun,HE Yue-hui. Effect of mechanical alloying on synthesizing of Laves phase Cr2Nb by solid phase thermal reaction [J]. Acta Aeronautica et Astronautica Sinica, 2003, 24: 568-571. (in Chinese)
[9] XIAO Xuan, LU Shi-qiang, MA Yan-qing, YAN Jiang-wu, HU Ping. Investigation on microstructures and properties of NbCr2 Laves phase alloys prepared by mechanical alloying followed by hot pressing [J]. Journal of Aeronautical Materials, 2007, 27: 7-11. (in Chinese)
[10] XIAO X, LU S Q, HU P, HUANG M G, NIE X W, FU M W. The effect of hot pressing time on the microstructure and properties of Laves phase NbCr2 alloys [J]. Mater Sci Eng A, 2008, 485(1/2): 80-85.
[11] FUJITA M, KANENO Y, TAKASUGI T. Phase field and room-temperature mechanical properties of C15 Laves phase in Nb- Hf-Cr and Nb-Ta-Cr alloy systems [J]. Journal of Alloys and Compounds, 2006, 424(1/2): 283-288.
[12] ZHU J H, LIU C T, LIAW P K. Phase stability and mechanical behavior of NbCr2-based Laves phases [J]. Intermetallics, 1999, 7: 1011-1016.
[13] SANBOTH L, LIAW P K, LIU C T, CHOU Y T. Cracking in Cr-Cr2Nb eutectic alloys due to the thermal stresses [J]. Mater Sci Eng A, 1999, 268: 184-192.
[14] OHTA T, NAKAGAWA Y, KANENO Y, INOUE H, TAKASUGI T. Microstructures and mechanical properties of NbCr2 and ZrCr2 Laves phase alloys prepared by powder metallurgy [J]. Journal of Materials Science, 2003, 38: 657-665.
[15] LU Shi-qiang. Investigation on mechanically activated reaction synthesizing of Laves phase Cr2Nb [D]. Changsha: Central South University, 2003. (in Chinese)
[16] XIAO Ping-an, QU Xuan-hui, QIN Ming-li, HUANG Pei-yun. Influence of milling rate and process control agents on mechanical alloying of Ti-26Cr [J]. Rare Metal Materials and Engineering, 2003, 32: 765-768. (in Chinese)
[17] YIN Yan-sheng, LI Jia, TAN Xun-yan, ZHANG Jin-sheng. Synthesis of Fe3Al intermetallics by mechanical alloying and pressing sintering [J]. Powder Metallurgy Technology, 2004, 22: 151-155. (in Chinese)
Foundation item: Project(50474009) supported by the National Natural Science Foundation of China; Project(05G56003) supported by the Aviation Science Foundation of China; Project(ZX200401001) supported by the Natural Science Foundation of Jiangxi Province, China
Corresponding author: XIAO Xuan; Tel: +86-791-3863039; E-mail: x56781234@126.com
DOI: 10.1016/S1003-6326(08)60310-6
(Edited by YANG Bing)