[key,message]=system(['DEF_ARM_CTL.COM 'File.DB ' B']);% 运行DB文件
特征目标值提取计算模块:
y = StrainUniformityArea(node,element,elementStrain,0.5,1.0);%适应度计算
通过生成各个部分的command.txt命令流文件,控制DEFORM-2D的前处理、提交运算、后处理,并且这些步骤可以自动完成。由于DEFORM-2D没有建模能力,所以需要调用CATIA实现参数化建模、更新模型并输出几何模型。CATIA自动修改参数化模型的参数并输出新的几何模型是通过CATIA自带的宏录制功能,录制出相应操作的命令流。然后在MATLAB中应用“[key, message] = system(['CNEXT .batch .macro ', ' Command .catvbs'])”命令调用命令流文件,从而执行模型的更新。通过上述MATLAB子程序,将有限元仿真模块编写成一个函数;函数的输入是设计变量,输出是粗加工零件内部等效应变不满足要求的比例,这个函数就是遗传算法模块所需的适应度函数。通过编写适应度函数,遗传算法模块和有限元仿真模块之间的自动通信就能搭建。其主要代码如下:
function Fitness=fun(x)% x为1行11列的向量(设计变量)
fileName=['PreForming','.DB'];% DB文件名变量
parameterNamePtop={'x1','x2','x3','x4','x5'};% CATIA模型参数名
parameterValuePtop=[x(1),x(2),x(3),x(4), x(5)];% 需要修改的参数(设计变量)向量
ChangeParameterCATIA('Ptop.CATPart','Ptop.igs',parameterNamePtop, parameterValuePtop);% 生成预成形模具IGS文件
GenerateGeo2D('Ptop.igs','Ptop.KEY',3,1);% 生成刚体预成形模具KEY文件
ReplaceDistance(originalSimCtrlFile,newSimCtrlFile,x(11));% 更新控制欠压KEY文件
…
ReplaceGEO(orignalFile,changeFile,newFile);% 更新DEFORM的KEY文件
RunDB(fileName);% 运行DB文件
Fitness=Post(fileName);% 后处理计算
End
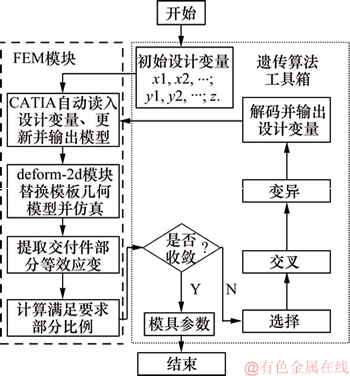
图5 3个软件之间协同优化流程图
Fig.5 Flow chart of collaborative optimization of three softwares
2 整体叶盘预成型模具优化实例
2.1 材料定义
采用高温钛合金整体叶盘的成形验证本文优化算法的有效性。原材料为直径250 mm的钛合金棒材。分别在棒材边缘、1/2R(R为棒材半径)处和中心部取样,进行显微组织观察,结果如图6所示。从图6可以看出:棒料的微观组织主要是
转变基体上存在的等轴和长条状初生
相,大部分
晶界已经充分破碎,并且棒料的相组织大致相同。
相都由球状和长条状组成,形态上稍有差异但均匀性较好,属于等轴组织。
2.2 遗传算法定义
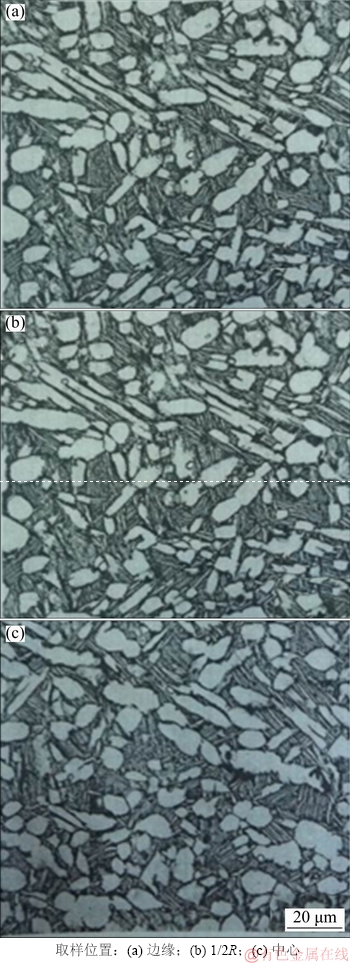
图6 钛合金棒料显微组织
Fig. 6 Microstructure of titanium alloy bar
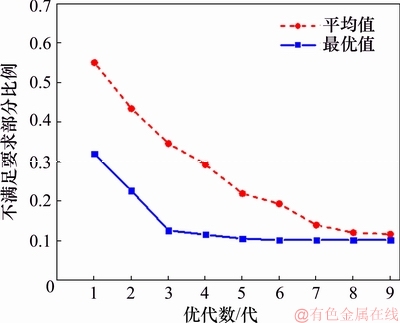
图7 整体叶盘锻件变形量优化过程中适应度函数曲线
Fig.7 Fitness function evolution curve during deformation optimization process of blisk forgings
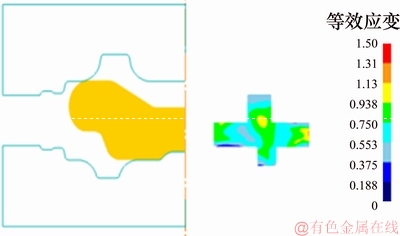
图8 第6代预锻件形状和交付件等效应变分布
Fig. 8 Preform die and effective stain of sixth generation
在遗传算法中,种群数目越多算法的寻优能力越强,但是过多的种群数目会增加计算的次数。通过多次试探可大致得到种群数目。设置遗传算法的种群数目为50,算法的交叉率设为0.8,变异率设为0.2。变异率越大,个体变异的能力越大;因而不容易陷入局部最优解,但是计算次数也会增加[25]。通常遗传算法中的初始个体应该被定义,但是为了测试算法的鲁棒性和智能性,初始个体由计算机在给定的设计空间内自动给定。设计变量的取值范围,被定义如下:
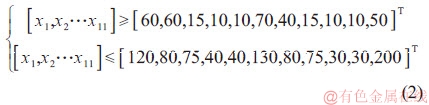
2.3 优化结果
变形量优化的演化过程如图7所示。从图7可见:随着优化代数的增加,所有个体的平均适应度急剧减小,最佳个体的适应度也减小。尤其在前3代优化中最佳个体的适应度减小最快,说明前3代优化效果最为显著。随着优化代数的增加,不满足要求部分的面积减小效率逐渐降低。第6代优化后,适应度基本不变,因此可以终止优化程序。第6代优化后预锻件形状和交付件等效应变分布如图8所示。从图8可见:第6代优化后,等效应变为0.5~1.0区域约占总面积的90%。为了使变形更均匀、计算效果更优化,可适当缩小目标等效应变范围。因为在第3代进化以后,不满足部分面积比值的降低幅度较小,优化程序可以在第3代终止,因而该优化算法所花费的计算成本也可以大大降低。
2.4 智能算法的特点
在人工优化过程中,需要不断重复调整模拟参数来获得满意的效果,而使用智能优化算法,只要设置1次模拟仿真模板就可以有目标地进行优化,大大节省了生产成本;在优化进程中,遗传算法模块可以实时显示仿真过程中适应度的变化情况,可以根据实际需要来控制结束模拟进程,使仿真次数由几百次降低到几十次;对于一些常用零件,可以根据经验来设定变量初始值,避免遗传算法第1代随机分配变量造成的耗时。因此,利用智能优化算法可以减少工作时间,还可以降低产品设计生产周期提高产品性能,为产品的更新换代提供了基础。

图9 解剖取样示意图
Fig.9 Diagram of anatomic sampling
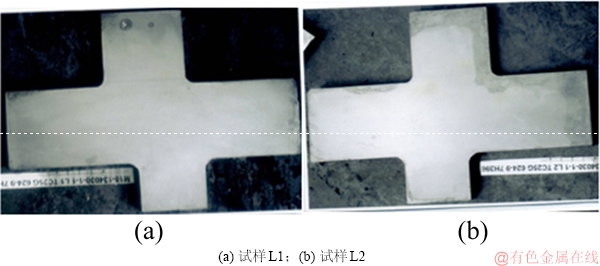
图10 解剖件宏观照片
Fig.10 Anatomical sample macrograph
3 锻件理化检测及性能分析
为了更全面地评估整体叶盘的性能,按照设计的解剖取样图对零件进行取样,如图9所示,然后分别进行高温和室温拉伸试验,获得锻件的抗拉强度
、屈服应力
、伸长率
和断面收缩率
等拉伸性能,并将其作为评价锻件成形质量的指标。检测结果表明:试样室温力学性能与高温力学性能均满足设计要求。在零件上取样观察宏观组织,如图10所示。从图10可见:试样L1和L2组织中未发现缩孔、缩松、折叠等冶金缺陷,与标准低倍评级图中的五级相符。
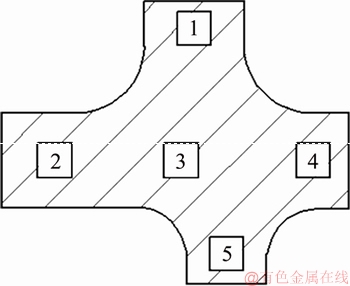
图11 显微组织取样位置示意图
Fig. 11 Diagram of sampling position
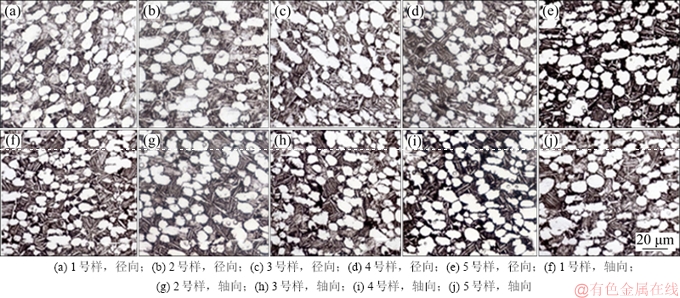
图12 整体叶盘锻件显微组织
Fig. 12 Microstructures of blisk forging
在锻件上容易产生大变形区和变形死区的部位取样进行微观组织观察,取样位置示意图如图11所示。图12所示分别为取样部位径向和轴向的金相照片。从图12可以看到:虽然锻件各个部位的组织在形态上有所差异,但均为双态组织,具有较高的塑形、伸长率和断面收缩率,且抗缺口敏感性和热稳定性最好,与高倍组织评级图中的二级相符。
4 结论
1) 预成形优化算法可以依据定量目标值对预成形模具进行优化,使满足变形要求部分达到90%以上,增加了在工程中的实用性,并且可以直观地反映出优化结果以及预测生产中易出现问题的位置。
2) 本文优化方法能够自动完成回转体类零件预成形模具参数的优化,优化过程中无需人工干预。优化算法的优化效率随着进化代数的增加而降低,因此,在实际使用过程中适当的提前结束优化程序,可以大大降低计算成本和时间。
3) 获得了高温钛合金整体叶盘的预成形模具尺寸,生产试制表明终锻零件的各项力学指标和微观组织均满足要求。
4) 提出了一种塑性成形中多参数组合优化问题的通用解法,将有限元仿真模块替换为其他工艺仿真模块,并建立相应的适应度函数;该算法就能直接应用于其他类型的塑性成形工艺参数优化。
参考文献:
[1] 赵明, 涂冰怡, 陈养惠. 航空发动机关键部件结构及制造工艺的发展[J]. 航空制造技术, 2015, 481(12): 42-46.
ZHAO Ming, TU Bingyi, CHEN Yanghui. Development of structure and manufacturing technology of critical component in aeroengine[J]. Aeronautical Manufacturing Technology, 2015, 481(12): 42-46.
[2] 蔡建明, 田丰, 刘东, 等. 600℃高温钛合金双性能整体叶盘锻件制备技术研究进展[J]. 材料工程, 2018, 46(5): 36-43.
CAI Jianming, TIAN Feng, LIU Dong, et al. Research progress in manufacturing technology of 600 ℃ high temperature titanium alloy dual property blisk forging[J]. Journal of Materials Engineering, 2018, 46(5): 36-43.
[3] 蔡建明, 弭光宝, 高帆, 等. 航空发动机用先进高温钛合金材料技术研究与发展[J]. 材料工程, 2016, 44(8): 1-10.
CAI Jianming, MI Guangbao, GAO Fan, et al. Research and development of some advanced high temperature titanium alloys for aero-engine[J]. Journal of Materials Engineering, 2016, 44(8): 1-10.
[4] SUN Weiyan, CHEN Liang, ZHANG Tailiang, et al. Preform optimization and microstructure analysis on hot precision forging process of a half axle flange[J]. The International Journal of Advanced Manufacturing Technology, 2018, 95(5/6/7/8): 2157-2167.
[5] 赵新海, 赵国群, 王广春. 金属体积成形预成形设计的现状及发展[J]. 塑性工程学报, 2000, 7(3): 1-6.
ZHAO Xinhai, ZHAO Guoqun, WANG Guangchun. The current situation and development of preform design in bulk metal forming[J]. Journal of Plasticity Engineering, 2000, 7(3): 1-6.
[6] PARK J J, REBELO N, KOBAYASHI S. A new approach to preform design in metal forming with the finite element method[J]. International Journal of Machine Tool Design and Research, 1983, 23(1): 71-79.
[7] KANG B S, KOBAYASH I S. Preform design in rolling processes by the three-dimensional finite element method[J]. International Journal of Machine Tools and Manufacture, 1991, 31(1): 139-151.
[8] LU Bin, OU Hengan, CUI Z S. Shape optimisation of preform design for precision close-die forging[J]. Structural and Multidisciplinary Optimization, 2011, 44(6): 785-796.
[9] SHAO Yong, LU Bin, OU Hengan, et al. A new approach of preform design for forging of 3D blade based on evolutionary structural optimization[J]. Structural and Multidisciplinary Optimization, 2015, 51(1): 199-211.
[10] 邵勇, 陆彬, 陈军, 等. 体积成形预成形设计及优化方法的研究与应用[J]. 塑性工程学报, 2012, 19(6): 1-9.
SHAO Yong, LU Bin, CHEN Jun, et al. Research and application of bulk metal preform design and optimization methods [J]. Journal of Plasticity Engineering, 2012, 19(6): 1-9.
[11] 邵勇, 陆彬, 任发才, 等. 基于变形均匀的叶片锻造预成形拓扑优化设计[J]. 上海交通大学学报, 2014, 48(3): 399-404, 411.
SHAO Yong, LU Bin, REN Facai, et al. Preform design with improvement of deformation uniformity in blad forging based on topology optimization method [J]. Journal of Shanghai Jiao Tong University, 2014, 48(3): 399-404, 411.
[12] SHAO Yong, LU Bin, OU Hengan, et al. Evolutionary forging preform design optimization using strain-based criterion[J]. The International Journal of Advanced Manufacturing Technology, 2014, 71(1/2/3/4): 69-80.
[13] LEE S R, LEE Y K, PARK C H, et al. A new method of preform design in hot forging by using electric field theory[J]. The International Journal of Mechanical Sciences, 2002, 44(4): 773-792.
[14] GUAN Yanjin, BAI Xue, LIU Mujuan, et al. Preform design in forging process of complex parts by using quasi-equipotential field and response surface methods[J]. International Journal of Advanced Manufacturing Technology, 2015, 79(1/2/3/4): 21-29.
[15] WANG Xiaona, LI Fuguo. A quasi-equipotential field simulation for preform design of P/M superalloy disk[J]. Chinese Journal of Aeronautics, 2009, 22(1): 81-86.
[16] 王晓娜, 李付国, 肖军, 等. 基于类等势场的粉末高温合金盘件预成形设计及有限元模拟[J]. 机械工程学报, 2009, 45(5): 237-243.
WANG Xiaona, LI Fuguo, XIAO Jun, et al. Preform design and finite element simulation of new-type P/M superalloy disk based on equipotential field[J]. Journal of Mechanical Engineering, 2009, 45(5): 237-243.
[17] 蔡军, 李付国, 韩莹莹. 基于静电场模拟的FGH96合金盘件预成形设计[J]. 兵器材料科学与工程, 2015, 38(4): 41-44.
CAI Jun, LI Fuguo, HAN Yingying. Preforming design of FGH96 alloy disc based on electrostatic fields[J]. Ordnance Material Science and Engineering, 2015, 38(4): 41-44.
[18] 赵新海, 马新武, 郑毅, 等. 锻造过程中变形均匀性控制及模具优化设计[J]. 材料科学与工艺, 1999, 7(s1): 237-240.
ZHAO Xinhai, MA Xinwu, ZHENG Yi, et al. Uniformity deformation control and optimal preform die design in metal forging[J]. Material Science &Technology, 1999, 7(s1): 237-240.
[19] YANG Yanhui, LIU Dong, HE Ziyan, et al. Optimization of preform shapes by RSM and FEM to improve deformation homogeneity in aerospace forgings[J]. Chinese Journal of Aeronautics, 2010, 23(2): 260-267.
[20] SEDIGHI M, TOKMECHI S. A new approach to preform design in forging process of complex parts[J]. Journal of Materials Processing Technology, 2008, 197(1/2/3): 314-324.
[21] TORABI S H R, ALIBABAEI S, BONAB B B, et al. Design and optimization of turbine blade preform forging using RSM and NSGA II[J]. Journal of Intelligent Manufacturing, 2017, 28(6): 1409-1419.
[22] ZHANG Dawei, YANG He. Preform design for large-scale bulkhead of TA15 titanium alloy based on local loading features[J]. The International Journal of Advanced Manufacturing Technology, 2013, 67(9/10/11/12): 2551-2562.
[23] KNUST J, PODSZUS F, STONIS M, et al. Preform optimization for hot forging processes using genetic algorithms[J]. The International Journal of Advanced Manufacturing Technology, 2017, 89(5/6/7/8): 1623-1634.
[24] 孙曙宇, 傅建. 文本模式下的DEFORM应用[J]. 锻压装备与制造技术, 2008, 43(1): 99-102.
SUN Shuyu, FU Jian. Application of DEFORM based on text-only model[J]. China Metal Forming Equipment & Manufacturing Technology, 2008, 43(1): 99-102.
[25] 雷英杰, 张善文. MATLAB遗传算法工具箱及应用[M]. 2版. 西安: 西安电子科技大学出版社, 2005: 23-69.
LEI Yingjie, ZHANG Shanwen. Genetic algorithm toolbox and application of MATLAB[M]. 2nd. ed. Xi'an: Xidian University Press, 2005: 23-69.
(编辑 赵俊)
收稿日期: 2018 -09 -05; 修回日期: 2018 -11 -15
基金项目(Foundation item):工信部绿色制造系统集成项目(2018272106-1)(Project(2018272106-1) supported by Green Manufacturing System Integration Program of Industry and Information Technology Ministry of China)
通信作者:王梦寒,博士,副教授,从事金属塑性成形工艺及模具CAD/CAE/CAM研究;E-mail: cquwmh@163. com