文章编号:1004-0609(2007)05-0716-06
激光扫描法制备球形黄铜粉末
欧阳鸿武,余文焘,何世文,陈 欣,黄劲松
(中南大学 粉末冶金国家重点实验室,长沙 410083)
摘 要:利用激光束扫描金属粉末过程中的球化效应,探索了将异形黄铜粉转化为球形粉末的可行途径,研究了激光功率、扫描速度对粉末颗粒球化过程的影响,并对粉末颗粒的熔化、熔滴铺展和收缩球化过程进行了理论分析。结果表明:粉末的球化、铺展和收缩过程非常短暂,分别在10-5、10-2和10-4 s以内完成,且粒度越细,历时越短。熔滴铺展与收缩的协调是成球的关键,理想的球化效果只有在激光工艺参数、粉末物性和球化环境相互协同的条件下才能实现,对于粒度小于50 μm的异形黄铜粉,在激光功率为500 W、扫描速度为30 mm/s时转化为表面平滑、高球形度的黄铜粉。
关键词:黄铜粉末;激光;球化效应
中图分类号:TF 123.1 文献标识码:A
Spherical brass powder fabricated by laser scanning
OUYANG Hong-wu, YU Wen-tao, HE Shi-wen, CHEN Xin, HUANG Jin-song
(Key Laboratory of Powder Metallurgy, Central South University, Changsha 410083, China)
Abstract: The irregular particle may melt rapidly and then retract to spherical particle through balling effect by laser beam scanning. The approach of transferring irregular brass powder into spherical powder by laser scanning was explored. The influences of laser power and scanning speed of laser beam and the process of melting, spreading and retracting were analyzed theoretically. The results show that the times of melting, spreading and retracting are very short, which are about 10-5, 10-2 and 10-4 s. And the smaller the particle size is, the quicker the process is. When the laser power was 500 W and scanning speed was 30 mm/s, the spherical brass powder is made from irregular brass powder with diameter of 50 μm. The interval between spreading and retracting is crucial to the balling process, and the ideal balling effect occurs only under the condition of good combination of process parameters, powder feature and environment.
Key words: brass powder; laser; balling effect
随着先进材料制备技术的不断发展和应用,金属粉末的生产及应用越来越受到人们的重视。目前,金属粉末的生产方法主要有雾化法(气雾化和水雾化)、机械破碎法、化学还原法、蒸发及电解法等。与不规则形状的粉末相比,球形粉末具有流动性好、烧结性好及反应可控等优越性能,在大批量生产和科学研究中得到日益广泛的应用[1-2]。然而,对于某些元素及合金(如铜合金和钛合金等)难以运用常规制备技术获得球形粉末。对于黄铜粉来说,由于铜和锌的熔点相差太大,在熔炼时,锌易挥发且容损,因此难以采用常规的气雾化及水雾化工艺制备[3-5]。球形黄铜粉的制备成本高,很大程度上限制了黄铜粉末的使用。
尽管制备球形黄铜粉很困难,但制备非球形黄铜粉的工艺比较成熟,且生产成本较低。因此,研究出一种低成本少污染的方法和工艺,将异形黄铜粉转化为球形粉末是一个值得探索的问题。
近年来,伴随激光技术的迅速发展,激光器性价比大幅度提高,激光应用领域不断扩展[6-8]。金属粉末的选区激光烧结(SLS)工艺,无需模具就可以通过激光扫描制备出全致密形状复杂的金属零件,在汽车、摩托车和家电等行业得到日益广泛的应用[9-10]。在SLS的早期,“球化效应”(即粉末在适当的激光功率和扫描速度条件下,熔化的金属粉末在表面张力作用下形成球形的行为)曾是一个阻碍其发展的技术难题,人们经过多年的努力才得以克服[10-12]。虽然“球化效应”在SLS技术中不受欢迎,但粉末的球化本身却十分奇妙。人们开始利用“球化效应”来清洁物体表面[[13-17]。本文作者利用激光束与粉末的相互作用中的“球化效应”,以异形黄铜粉末为研究对象,开展了利用激光扫描制备球形黄铜粉末的研究。
1 实验
实验采用DTM公司的Sinterstation2500型选区激光烧结设备,CO2激光,激光功率从0~700 W连续可调,激光扫描速度从0~180 mm/s,激光束直径为0.2 mm。
实验装置如图1所示。实验中,在长×宽×厚为200 mm×120 mm×5 mm平整的不锈钢板上均匀地平铺一薄层粉末,激光束沿往复路径作用于粉末。黄铜粉末形状如图2(a)所示,粒度分布范围为10~60 μm,熔点为1 163 K。通过调节激光功率和扫描速度,探索合适的工艺参数。实验参数的设定如下:激光功率为200~600 W,功率的增量均为100 W,扫描速度为10~130 mm/s,速度的增量均为20 mm/s。调节扫描速度和激光功率,进行正交实验。扫描间距均为0.3 mm。保护气氛分别为氮气,工作腔内氧含量低于6×10-4。粉末的形状和表面形貌采用PHILIPS XL30扫描电镜进行扫描分析和显微放大观测。
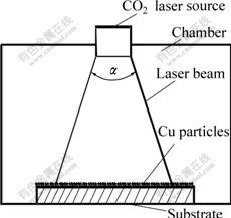
图1 SLS装置示意图
Fig.1 Schematic diagram of SLS equipment
2 结果和讨论
在5×7个不同工艺参数的组合中,粉末在激光扫描下表现出较大的差异。实验结果列于表1中。从整体上分析,当扫描速度过慢,如10 mm/s时,黄铜粉烧结成条块状;当激光功率过大时,黄铜粉形成较大直径的团状,如图2(b)所示;当激光功率较低、扫描速度较高时,基本上没有出现球化,但在一个较窄的工艺参数区间内,出现了较为理想的球化效果,结果如图2(c)所示。
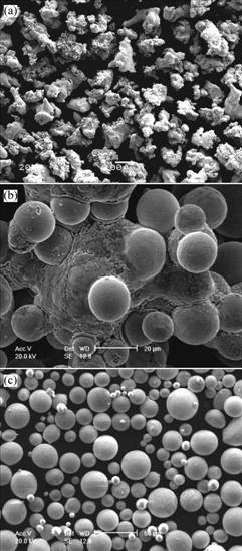
图2 黄铜粉的球化情况
Fig.2 Balling of bronze powder: (a) Irregular bronze powder; (b) Agglomerate; (c) Spherical bronze powder
从表1中可以看出,成球过程对工艺参数非常敏感,在35个不同的工艺组合中,实验结果的整体趋势呈现很好的规律性。以往的研究表明,在SLS过程中,金属粉末球化的基本条件为:随激光功率(P)提高,扫描速度(v)降低,成球的几率越高;相反,当激光功率降低,扫描速度加快,成球的几率将随之下降[11]。或者表述为:P/v的比值提高,球化的趋势增强。本研究结果中,有3个组合能成球,其中P=500 W,v=30 mm/s获得了较为理想的球化效果。
表1 不同工艺参数组合下,黄铜粉末的状况变化情况
Table 1 Variation of brass powder with different process parameters
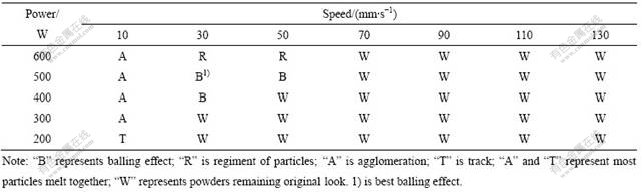
2.1 球化过程的理论分析
当粉末在激光束作用下,表面和整体熔化后才能出现球形现象。如果在适当的激光功率和扫描速度组合下,粉末表面和整体熔化后,熔体(滴)的球化取决于熔体的表面张力及相应的收缩速度。事实上,熔滴在球化之前,有一个润湿底板的过程,即熔滴在底板上铺展成薄膜的变形过程,随后在表面张力作用下,收缩成球。熔化、铺展和收缩过程如图3所示。能否球化取决于熔滴的铺展与收缩运动的协调。
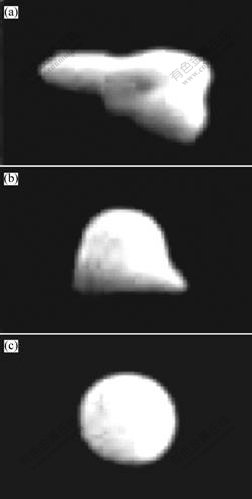
图3 熔化粉末(熔滴)的铺展和球化过程
Fig.3 Process of spreading, retracting and balling of molten drop: (a) Melting and spreading; (b) Retracting; (c) Balling
2.1.1 粉末的熔化过程
设激光功率为P(W),激光束的光斑面积为A(mm2),粉末的激光吸收率为a,激光强度Q为:

忽略粉末颗粒在激光作用下的蒸发行为以及粉末颗粒与底板间的热传导(当异形粉末静止地放置在平整的不锈钢板时,粉末颗粒与底板的接触面积很小),粉末颗粒在激光束作用下熔化的时间(ti)可根据式(2)计算[12]:

式中 Tm和T0分别为熔化温度和室温;dd为粉末颗粒直径;a为激光吸收率;ρd为密度;cd为定热容。
2.1.2 熔滴的铺展过程
不蒸发的熔滴在可润湿的表面上存在铺展的趋势,逐步形成薄膜,铺展过程服从普遍定律[18]:

式中 t为铺展时间。对式(4)进行微分,得出液膜的铺展速度:

熔滴的铺展速度与熔滴直径成正比,并随铺展时间的延长而迅速降低。为了降低或避免熔滴的铺展,激光扫描速度既要保障粉末充分熔化,又要提高工作
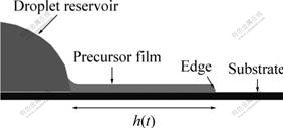
图4 熔滴在可润湿底板上的铺展
Fig.4 Spread of droplet reservoir on complete wettable substrate
效率,还必须确保随后的球化过程顺利进行,不至于结块和结团。
2.1.3 熔滴的收缩和球化过程
对于平铺在物体表面的薄层熔膜在表面张力作用下的收缩速度vr可表示为[17]:

式中 df为熔膜厚度,熔体的铺展系数S=1.904 N/ m。
液膜的收缩(球化)时间tr为:

收缩速度与熔膜密度和厚度倒数的平方根成比例,总的趋势是熔膜的密度和厚度降低,收缩速度提高。
2.2 工艺参数的影响
异形黄铜粉的激光吸收率为0.26[19],黄铜的其它物性参数以及上述公式相关的边界和初始条件如表2所列。由此得到图5所示的黄铜熔化、铺展和收缩球化过程。
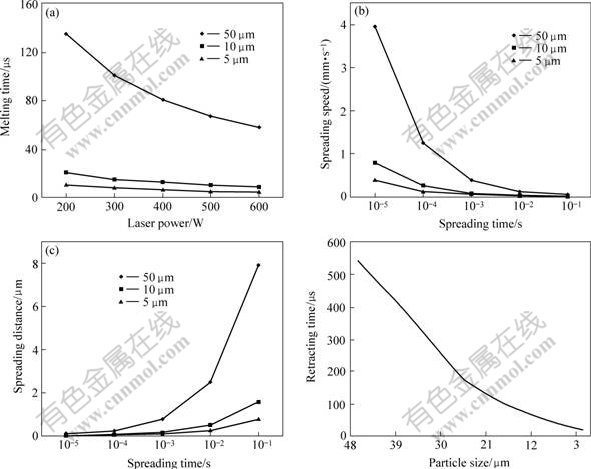
图5 黄铜粉的熔化和球化过程
Fig.5 Melting and balling process of bronze powder: (a) Melting times of different size particles; (b) Spreading distances of molten drop with different sizes; (c) Spreading speeds of molten drop with different sizes; (d) Retracting times of balling with different sizes
表2 黄铜的物性参数和边界条件
Table 2 Material properties and boundary condition
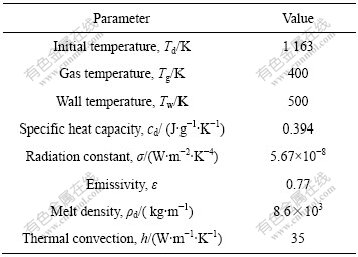
从图4(a)可看出,粉末的熔化时间非常短暂,粒径为50 μm的颗粒随激光功率的提高,熔化时间由14 μs降低到6 μs;而10 μm粒径以下的颗粒在不到时间2 μs内就完全熔化了。熔滴的铺展经历了一个由快到慢的过程,如图2(b)和2(c)所示。以50 μm直径的熔滴为例,其铺展速度在10-5到10-1 s时间内由4降低到0.04 mm/s,相应的最大铺展距离为8 μm。然而,球化过程在不到0.6 ms就完成了,且熔滴粒径越小,球化时间越短。小颗粒比大颗粒球化更快,如图2(d)所示。
结合表1的实验结果可以看出,激光功率和扫描速度对颗粒的熔化、铺展和球化过程是共同起作用的。如果激光功率过高(扫描速度不变),不仅可能导致颗粒很快熔化,同时可能使底板的温度提升起来,增大了熔体的铺展而成团或成块的趋势,甚至导致熔体与底板产生冶金结合,彼此烧结起来;如果激光功率过低,粉末颗粒未能充分熔化,也不可能完成球化过程。类似地,保持激光功率不变,而改变激光扫描速度时,过快或过慢的扫描速度都难以保障颗粒熔化、铺展和球化过程的充分有序进行。
可见,激光功率和扫描速度必须协同地配合起来。虽然P/v的比值相同,但由于激光功率不够,或扫描速度过快,可能导致粉末没有充分熔化,或来不及收缩,因此,难以获得所期望的球化效应。如果扫描速度过慢,熔体润湿面积过大,使熔体来不及收缩就冷却固化了,也无法收缩成球。上述计算也清楚表明,颗粒的熔化和球化过程受到颗粒粒度的直接影响,颗粒直径越大,熔化越慢,铺展越大,收缩时间也越长。因此,球化过程必须考虑颗粒粒度的影响。
综合上述分析,选择一个综合参数M来确定工艺参数和物性参数对球化过程的影响:
(8)
式中 P为激光功率;D粉末直径;v激光扫描速度。
式(8)将工艺参数和主要的粉末物性参数归结为一个综合评价参数,对产生球化效应的范围和条件进行限制。根据颗粒粒度的不同,在保障M值满足其球化的前提下,激光功率和扫描速度必须作协调的变化,且激光功率应高于熔化所需的功率,但必须低于熔体与底板发生冶金结合的功率;扫描速度v应高于导致熔体结团的最低速度(即速度不能过低),但必须低于某一临界值,以保障粉末充分熔化,即扫描速度不能过高。由此可见,激光功率和扫描速度的取值往往限制在一个非常狭小的范围,要保证“球化效应”的形成必须使激光功率和扫描速度处于适当的取值范围,并相互协同起来。
结果表明:黄铜粉末在工艺参数为M=8~9,400 W<P<500 W,30 mm/s<v<50 mm/s的范围内能得到球化效应的机理。且在M=8.33,P=500 W,v=30 mm/s获得了最为理想的球化效果。
3 结论
1) 选择适当的工艺参数,利用“球化效应”激光扫描快速熔化异形粉末使其球化,是获取球形粉末的一种可行途径,具有节能、少污染的特点。
2) 采用参数M(=DP/v)综合评价粉末粒度、激光功率和扫描速度对球化过程的影响。异形黄铜粉转化为球形粉末的条件为:M=8.33, P=500 W,v=30 mm/s。
3) 球化后粉末颗粒的形貌和表面质量受粉末粒度的影响,且粒度越细,粉末的球形度越高,表面越光滑。
REFERENCES
[1] Wu C Y, Dihoru L, Cocks A C F. The flow of powder into simple and stepped dies[J]. Powder Technology, 2003, 134: 24-39.
[2] Dupont A, Largeteau A, Parent C. Influence of the yttria powder morphology on its densification ability[J]. Journal of the European Ceramic Society, 2005, 25: 2097-2103.
[3] 美国金属学会. 金属手册[M]. 北京: 机械工业出版社, 1994: 149-172.
American Metal Society. Metal Handbook[M]. Beijing: China Mechane Press, 1994: 149-172.
[4] Belyakov V A, Medvedovskii A B, Nichiporenko O S. Properties of atomized brass powder[J]. Powder Metallurgy and Metal Ceramics, 1981, 20(6): 375-377.
[5] 李 勇, 韩德强. 雾化参数对H70黄铜粉粒度分布的影响[J]. 粉末冶金技术, 2005, 23(4): 287-290.
LI Yong, HAN De-qiang. Atomization parameter influence to the particle attribution of H70 brass powder[J]. Powder Metallurgy Technology, 2005, 23(4): 287-290.
[6] Wang X C, Laoui T, Bonse J, Kruth J P, Lauwers B, Froyen L. Direct selective laser sintering of hard metal powders: experimental study and simulation[J]. The International Journal of Advanced Manufacturing Technology, 2002, 19: 351-357.
[7] Kruth J P, Froyen L, Vaerenbergh J V, Mercelis P, Rombouts M, Lauwers B. Selective laser melting of iron-based powder[J]. Journal of Materials Processing Technology, 2004, 149: 616-622.
[8] Tolochko N, Mozzharov S, Laoui T, Froyen L. Selective laser sintering of single- and two-component metal powders[J]. Rapid Prototyping Journal, 2003, 9(2): 68-78.
[9] Shiomi M, Yoshidome A, Abe F, Osakada K. Finite element analysis of melting and solidifying processes in laser rapid prototyping of metallic powders[J]. International Journal of Machine Tools & Manufacture, 1999, 39: 237-252.
[10] Gibson I, Shi D P. Material properties and fabrication parameters in selective laser sintering process[J]. Rapid Prototyping Journal, 1997, 3(4): 129-136.
[11] Ryu D Y, Shin K, Drockenmuller K, Hawker C J, Russell T P. A generalized approach to the modification of solid surfaces[J]. Science, 2005, 308: 236-239.
[12] Pinkerton A J, Li L. Multiple-layer laser deposition of steel components using gas-and water-atomised powders: the differences and the mechanisms leading to them[J]. Applied Surface Science, 2005, 247: 175-181.
[13] Qiao Z Y, Yan L J, Cao Z M, Xie Y N. Surface tension prediction of high-temperature melts[J]. Journal of Alloys and Compounds, 2001, 325: 180-189.
[14] Bonn D, Bertrand E, Meunier J. Dynamics of wetting layer formation[J]. Phys Rev Lett, 2000, 84: 4661-4664.
[15] Chung H, Das S. Numerical modelling of scanning laser-induced melting, vaporization and resolidification in metals subjected to step heat flux input[J]. International Journal of Heat and Mass Transfer, 2004, 47: 4153-4164.
[16] Zhu H H, Lu H, Fuh J Y H. Influence of binder’s liquid volμme fraction on direct laser sintering of metallic powder[J]. Mater Sci Eng A, 2004, A371: 170-177.
[17] Habenicht A, Olapinski M, Burneister F, Leiderer P, Boneberg P. Jμmping nanodroplets[J]. Science, 2005, 309: 2043-2044.
[18] Bergeron V, Bonn D, Martin J Y, Vovelle L. Controlling droplet deposition with polymer additives[J]. Nature, 2002, 405: 772-775.
[19] Tolochko N K, Laoui T, Khlopkov Y V, Mozzharov S E, Titov V I, Ignatiev M B. Absorptance of powder materials suitable for laser sintering[J]. Rapid Prototyping Journal, 2000, 6(3): 155-160.
基金项目:国家自然科学基金资助项目(50574103; 10476034)
收稿日期:2006-06-28;修订日期:2007-02-09
通讯作者:欧阳鸿武,教授,博士; 电话: 0731-8877192; E-mail: oyxy163@163.com
(编辑 李艳红)