文章编号:1004-0609(2015)06-1560-07
纳米SiC颗粒对微米Ni-SiC复合镀层性能的影响
王红星1, 2,毛向阳1, 2,沈 彤1, 2
(1. 南京工程学院 江苏省先进结构材料及应用技术重点实验室,南京 211167;
2. 南京工程学院 材料工程学院,南京 211167)
摘 要:采用双脉冲复合电镀技术,在瓦特型镀液中,制备了含微/纳米SiC颗粒的Ni基复合镀层,研究镀液中纳米SiC添加量对复合镀层微观形貌、摩擦性能和抗氧化性能的影响。结果表明:在SiC颗粒(5 μm)浓度为10 g/L的镀液中,添加纳米SiC和Ni-SiC复合镀层镍择优取向由晶面(200)转变为晶面(111);当SiC(40 μm )浓度为4.0 g/L时,复合镀层显微硬度最大,为456 HV;复合镀层摩擦因数最小,平均值为0.28,为微米复合镀层的1/2;经900 ℃氧化100 h后,氧化质量增加为6.025 mg/cm2,为微米复合镀层的1/3。
关键词:Ni-SiC复合镀层;微米SiC;耐磨;抗氧化性能
中图分类号:TG174.44 文献标志码:A
Effect of nano-SiC particles on properties of Ni-SiC micro-composite coatings
WANG Hong-xing1, 2, MAO Xiang-yang1, 2, SHEN Tong1, 2
(1. Key Laboratory of Advanced Structural Materials and Application Technology of Jiangsu Province,
Nanjing Institute of Technology, Nanjing 211167, China;
2. School of Materials Engineering, Nanjing Institute of Technology, Nanjing 211167, China)
Abstract: Ni based composite coatings containing micro- and nano-SiC particles were prepared by dipulse electrodepositing in watts nickel solution. The effect of the nano-SiC content in the solution on the micro morphology, wear and oxidation resistance of the coating was investigated. The results show that the preferred orientation the Ni crystallites transits from (200) crystal face to (111) crystal face of Ni-SiC composite coatings when adding nano-SiC in electrolyte with SiC (5 μm) content of 10 g/L. the maximum value of microhardness of coating with 456 HV is obtained, and the smallest coefficient of coating with 0.28 is about 1/2 than that of micro-SiC composite coating when adding 4.0 g/L nano-SiC in electrolyte, and shows the best oxidation resistance with the mass gain of 6.025 mg/cm2 is about 1/3 than that of micro-SiC composite coating after oxidation at 900 ℃ for 100 h.
Key words: Ni-SiC composite coating; micro-SiC; wear resistance; oxidation resistance property
复合电镀是通过金属电沉积的方法,将一种或几种不溶性固体颗粒(Al2O3、SiC、TiC等)均匀地夹杂到金属基质中,形成具有良好耐磨性、耐腐蚀性和抗氧化等性能的镀层。镍由于具有良好的耐腐性和较高硬度等优点,已被广泛用作复合镀层的基质金属。
目前,以镍为基质金属,镀液中加入不溶性纳米颗粒,制备如Ni-Al2O3[1-2]、Ni-BN[3]、Ni-SiC[4]、Ni-P-SiC[5-7]、Ni-TiC[8]等具有优良耐蚀性、耐磨性的纳米复合镀层。另外,通过加入具有自润滑性的颗粒,形成如Ni-PTFE[9]、Ni-MoS2[10]和Ni-Cg[11]等具有减摩性能的纳米复合镀层。由于纳米颗粒的高表面能,使其极易在镀液中发生团聚,并最终导致复合镀层中的颗粒以团聚状态存在。当团聚态的颗粒尺寸明显增大时,其弥散强化效果大大降低,起不到提高复合镀层性能的作用。通过分析文献[12-16],通过改变复合镀工艺参数,诸如阴极电流密度、电沉积方式、颗粒浓度、镀液温度、超声波、磁场和表面活性剂等,这些研究结果有助于改善镀层内纳米颗粒的分散性,发挥了纳米颗粒的细化晶粒和弥散强化基体的作用。MEENU等[17]比较研究了微米、纳米SiC颗粒对Ni-Co镀层耐磨性能,结果表明,含微米颗粒的复合镀层的磨损率低于纳米复合镀层;纳米复合镀层的硬度和耐腐蚀性能都高于微米复合镀层。综上所述,关于微/纳米颗粒单独沉积的研究已较多,而镀液中添加微/纳米颗粒共沉积的复合镀层的相关研究尚未见报道。
本文作者采用双脉冲电源,在瓦特型镀液中制备微/纳米SiC混杂的Ni-SiC复合镀层。在镀液中微米SiC浓度一定的条件下,添加纳米SiC颗粒,研究镀液中纳米SiC颗粒添加量对微米Ni-SiC复合镀层组织结构、耐磨性能和抗氧化性能的影响。
1 实验
1.1 镀液的配制
以纯度99.9%电解镍板为阳极,纯铜切割成尺寸为15 mm×15 mm×3.0 mm的试片为阴极,采用多脉冲电镀电源(SMD-30P),在纯铜表面沉积Ni-SiC纳米复合镀层。电镀液组成及工艺条件见表1。
一般在常温下镀液添加微、纳米SiC颗粒,尤其是纳米SiC颗粒,加入到镀液时,常漂浮在镀液表面,需较长时间搅拌才能进入镀液。本实验中,首先取少量预先配制好的基础镀液用水浴锅加热到一定温度,然后加入称量好的SiC颗粒,并滴入表面活性剂(阳离子型表面活性剂)十六烷基三甲基溴化铵,添加量为0.25%(质量分数),SiC颗粒很快被镀液润湿而进入到镀液中。再将润湿好的SiC颗粒加入到剩余的镀液 中,超声波清洗器(KH-300DB)震荡,同时采用数显电动搅拌器(JJ-1200W)以转速800 r/min进行搅拌,时间为15 min,进行复合镀。
1.2 性能测试
采用FM700型显微硬度测试设备测量复合镀层显微硬度。测试条件:压头载荷1 N,加载时间为15 s。在镀层横截面不同部位测试5个值,取平均值。
采用WTM-2E型可控气氛微型摩擦磨损试验仪进行镀层摩擦实验。测试条件:Si3N4球为对磨材料,显微硬度1500 HV,直径4 mm;载荷3 N,转速为250 r/min,环境温度为室温,磨痕半径为4 mm,时间为0.5 h。
复合镀后的试样以丙酮为清洗液,进行超声波清洗、干燥后置于Al2O3坩埚中,连同坩埚一起,用精度为0.1 mg分析天平称量氧化前的质量。为了保证实验数据的准确性,在实验前瓷坩埚在1000 ℃中烧至恒质量,以除去其中的水分和杂质。将试样同坩埚一起称取质量做为起始质量,称取质量后放入箱式炉内,在900 ℃下静止空气中分别氧化20、40、60、80和100 h。在预先设定的时间内氧化后,炉冷却到室温,将试样连同坩埚一起称取质量。
1.3 检测方法
采用JSM-6380LV扫描电镜(SEM)配能谱分析仪(EDS)分析复合镀层表面及磨损的微观形貌;采用 Bruker D8 Advance 型转靶 X 射线衍射仪(XRD)分析镀层结构,旋转靶为铜靶,采用 Cu Kα激发源,管电流40 mA,管电压40 kV,步长0.02°,扫描速度为5.0 (°)/min。
2 结果与讨论
2.1 纳米SiC添加量对复合镀层微观形貌的影响
表1 Ni/SiC复合镀层的制备的工艺参数
Table 1 Electrodeposition parameters for Ni/SiC composite coatings


图1 镀液中不同纳米SiC颗粒添加量复合镀层的表面微观形貌
Fig. 1 Surface morphologies of composite coatings with different nano-SiC contents in solution
图1所示为镀液中纳米SiC颗粒添加量不同时Ni-SiC复合镀层的微观形貌。由图1看出,镀液中添加纳米SiC颗粒后,对复合镀层的微观形貌有明显的影响。镀液中未添加纳米SiC时,Ni-SiC复合镀层表面晶粒尺寸较大,呈棱锥状,镀层致密,如图1(a)所示;镀液中添加2.0 g/L 纳米SiC后,镀层表面呈胞状,胞状结构由尺寸更小的晶粒组成,但胞状结构尺寸不均匀,镀层表面疏松,如图1(b)所示;添加量为4.0 g/L时,复合镀层的表面形貌与2.0 g/L 时的相类似,呈胞状结构,如图1(c)所示;当纳米SiC颗粒添加量增加到8.0 g/L时,复合镀层的致密度有所增加,镀层的表面胞状结构尺寸随镀液中纳米SiC颗粒添加量增加而增大。这是因为镀液中添加少量纳米SiC颗粒时,在基质金属沉积过程中,SiC颗粒吸附在基质金属表面的活化位置,增加了镍金属的形核位置,细化了晶粒,使镀层表面呈颗粒状;随镀液中纳米颗粒量多,颗粒间碰撞几率加大,出现团聚体,镀层中纳米SiC颗粒增多,形成表面堆积,复合镀层表面呈胞状结构;继续增加镀液中纳米颗粒添加量,纳米颗粒团聚现象更加严重,镍金属包裹在纳米颗粒团表面进行沉积,而纳米团颗粒之间镍晶粒的生长滞后,颗粒间隙得不到镍晶粒的补充,形成了疏松结构的镀层表面。
图2所示为镀液中纳米SiC颗粒不同添加量时Ni-SiC复合镀层的截面微观形貌。由图2看出,当镀液中纳米SiC颗粒添加量为2.0~4.0 g/L时,纳米SiC颗粒较均匀分散在镀层内,且含量随镀液中颗粒添加量的增加而增加,当镀液中纳米SiC颗粒添加量为8.0 g/L时,纳米SiC颗粒在镀层内分散性变差,出现团聚现象,如图2(d)所示。
2.2 纳米SiC颗粒添加量对复合镀层组织结构的影响
图3所示为镀液中纳米SiC颗粒添加量不同时镀层的XRD谱。由图3看出,镀层均为单一的面心立方(fcc)结构。当镀液中只有微米SiC颗粒时,基质金属Ni在(200)晶面择优生长。当镀液中添加纳米SiC颗粒后,在添加量2.0~8.0 g/L范围内,基质金属Ni在(111)晶面呈择优生长。这可能是镀液中纳米SiC颗粒的存在,在镍结晶过程中,改变了Ni与SiC颗粒间界面相匹配关系,改变了Ni结晶过程中晶面的择优取向。另外,纳米颗粒可能充当了形核质点,影响了(200)晶面的生长趋势。
2.3 纳米SiC添加量对复合镀层摩擦性能的影响
图4所示为镀液中纳米SiC颗粒添加量与复合镀层的显微硬度和摩擦因数之间的关系。由图4(a)看出,随镀液中纳米颗粒添加量增加,镀层显微硬呈先增后降低的变化趋势。微米SiC/Ni复合镀层的显微硬度最小,为368 HV,镀液中纳米SiC颗粒添加量为4.0 g/L时,达到最大值,为456 HV。在纳米SiC颗粒添加前,微米颗粒的细化晶粒的效果不明显,复合镀层晶粒尺寸较大;添加纳米颗粒后,纳米颗粒沉积在微米颗粒间,细化了微米颗粒间的镍晶粒,起到局部强化作用。同时,由于微/纳米共同细化镍晶粒,提高镀层的显微硬度;但镀液中纳米颗粒浓度超过一定值后,纳米颗粒以团聚态复合共沉积进入镀层,团聚态内部的结合力低,同时,也降低了镀层的致密度,在外力作用下,镀层内团聚态碎裂,导致复合镀层的显微硬度随镀液中纳米颗粒添加量的增加而降低。
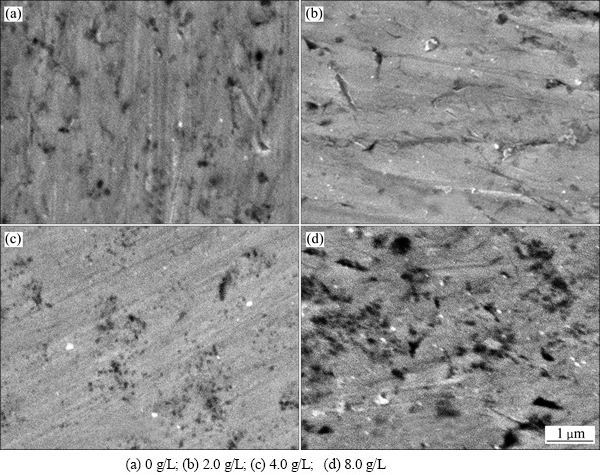
图2 镀液中不同纳米SiC颗粒添加量复合镀层的截面微观形貌
Fig. 2 Cross-section morphologies of composite coatings with different nano-SiC contents in solution
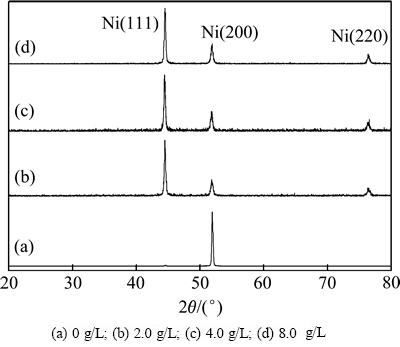
图3 镀液中不同纳米SiC颗粒添加量复合镀层XRD谱
Fig. 3 XRD patterns of composite coatings with different SiC contents in solution: (a) 0 g/L; (b) 2.0 g/L; (c) 4.0 g/L; (d) 8.0 g/L
由图4(b)看出,随镀液中纳米颗粒添加量增加,摩擦因素大致呈先降后增的变化趋势。微米SiC/Ni复合镀层在滑动30 min内,镀层的摩擦因数平稳,基本维持在0.6左右;镀液中纳米SiC颗粒添加量为2.0 g/L时,镀层的摩擦因数有所降低,约为0.45;镀液中纳米SiC颗粒添加量为4.0 g/L时,摩擦因素在0.26~0.29间波动;镀液中纳米SiC颗粒添加量为8.0 g/L时,摩擦因数上升,在0.38~0.41之间波动。结合前面镀液中纳米颗粒添加量与显微硬度的变化趋势,镀层的显微硬度与摩擦因素之间存在一定的对应关系,显微硬度高的复合镀层,摩擦因素较低。摩擦因素除了与硬度相关外,还受镀层表面形貌、致密度和晶粒尺寸等多种因素的综合影响[18]。
图5所示为镀液中纳米SiC颗粒不同添加量时复合镀层表面磨痕的微观形貌。由图5看出,复合镀层磨痕表面都存在犁沟现象,磨损机制为典型的磨粒磨损。微米SiC/Ni复合镀层的磨痕表面具有宽度较小的犁沟,呈轮胎花纹状并紧密排列,如图5(a)所示;镀液中纳米SiC颗粒添加量为 2.0 g/L时,磨痕表面存在宽度差异较大的犁沟,还出现了明显的挤压,形成棱状的凸起物,如图5(b)所示;纳米SiC颗粒添加量增加到4.0 g/L,磨痕表面的犁沟深度较浅,同时磨痕表面出现裂纹,如图5(c)所示;添加量增加到8.0g/L,磨痕表面犁沟深而且密集,局部出现较大面积的材料转移,如图5(d)所示。复合镀层的磨损失效主要是由于硬质颗粒的挤压、犁削后生成的磨屑充填于空隙中,或介于磨损表面之问,充当新的磨粒时,主要磨损机理为磨粒磨损。微米复合镀层表面的微米级颗粒作为硬质点,磨球压入镀层表面的深度较浅,减小了摩擦副和镀层的接触面积,形成了深度较浅的犁沟状磨痕形貌。微-纳米复合镀层中,由于纳米SiC颗粒的添加,造成微米颗粒沉积量减少,在磨损过程中,硬质点微米SiC颗粒的数量减少,微/纳米颗粒共同起硬质点作用,增加了摩擦副之间的接触面积。同时,由于镀液纳米颗粒浓度过高造成的内部结合力差的团聚态SiC沉积到镍镀层内,且分散性差,表面疏松,滑动摩擦过程中,在压力和剪切力的作用下,团聚态的SiC颗粒破碎,被剥落,充当磨粒,加剧磨损。本实验中,镀液中纳米SiC颗粒添加量为4.0 g/L时,硬度最大、摩擦因素较小。这是由于镀液中纳米颗粒团聚现象较轻,纳米SiC颗粒的分散性好,弥散分布在镀层内,强化了微米SiC颗粒周围的镍镀层,提高了微米颗粒在镀层内的结合力,与微米SiC颗粒共同强化基质镍金属,提高了复合镀层的显微硬度,并降低了摩擦因素。综上所述,当镀液中纳米SiC颗粒浓度在一个适当范围内,复合镀层中SiC颗粒在金属基质中的分散性好,减少纳米颗粒的添加量,有效降低纳米颗粒的团聚现象,实现纳米与微米颗粒混杂共沉积,提高复合镀层的性能。
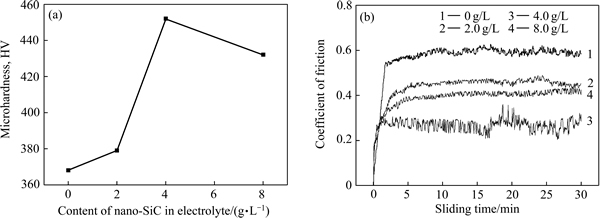
图4 镀液中纳米SiC颗粒添加量与显微硬度关系以及摩擦因数与时间关系
Fig. 4 Relationship between contents of nano-SiC in electrolyte and microhardness(a) and relationship between coefficient of friction and sliding time(b)
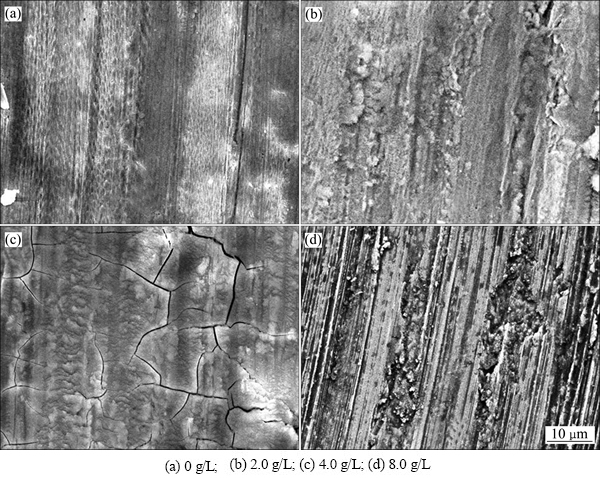
图5 镀液中纳米SiC颗粒不同添加量时复合镀层的磨痕形貌
Fig. 5 Wear tracks morphologies of composites coatings deposited with different contents of nano-SiC particles in electrolyte
2.4 纳米SiC添加量对复合镀层抗氧化性能的影响
图6所示为Ni-SiC复合镀层在900 ℃分别氧化20、40、60、80和100 h后的氧化增加质量曲线。由图6看出,在900 ℃条件下氧化100 h后,复合镀层的氧化增加质量随镀液中纳米SiC颗粒添加量的增加呈先降低后增加的变化趋势。微米SiC/Ni复合镀层的氧化增加质量最大,为20.153 mg/cm2,镀液中纳米SiC颗粒添加量为4.0 g/L时,复合镀层的氧化增加质量最小,为6.025 mg/cm2,为微米复合镀层的1/3。由文献[19]可以得到氧化增加质量ΔG与时间t的关系为(ΔG)2=Kpt+C(式中C为常数,Kp为氧化速度系数)。Kp与金属表层组织、温度及氧化膜的性质等因素有关,可以用来定量评价金属的抗高温氧化性能,Kp越大,金属的抗高温氧化性能越差,反之越好。根据实验数据可以算出,样品在900 ℃、100 h氧化后,微米Ni-SiC复合镀层和微、纳米Ni-SiC(纳米SiC添加量为4.0 g/L)复合镀层的Kp分别为1.128×10-3 mg2·cm-4·s-1和1.008×10-4 mg2·cm-4·s-1。
图7所示为Ni-SiC复合镀层在900 ℃经100 h恒温氧化后的表面形貌。由图7看出,氧化100 h后,相比于微米Ni-SiC复合镀层,镀液中添加纳米SiC颗粒后,复合镀层氧化膜晶粒尺寸明显减小。这是由于在氧化过程中,镀层内纳米SiC颗粒对氧化物长大起阻碍作用;另外,镀态下镍晶胞为由更细小的晶粒构成的结构。
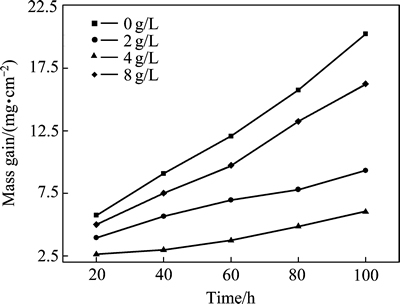
图6 Ni-SiC复合镀层在900 ℃氧化不同时间后的氧化质量增加曲线
Fig. 6 Mass gain curves of Ni-SiC composite coatings after oxidized at 900℃ for different times
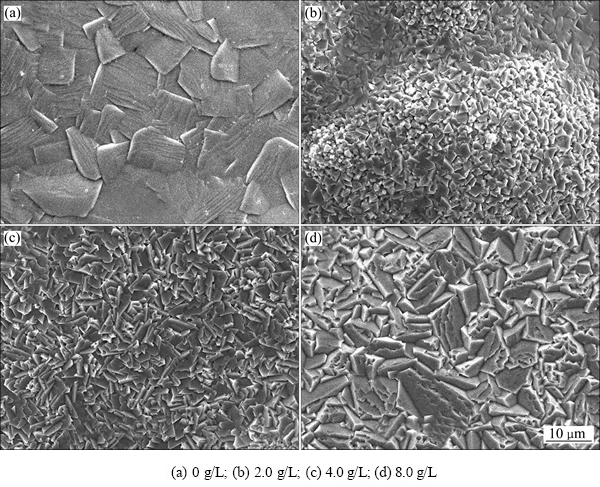
图7 Ni-SiC复合镀层在900℃经100 h恒温氧化后的表面形貌
Fig. 7 Surface morphologies of Ni-SiC composite coatings after isothermal oxidation at 900 ℃ for 100 h
3 结论
1) 镀液中添加纳米SiC颗粒后,对复合镀层的微观组织结构无明显影响微,组织为Ni相,但镍镀层择优生长由晶面(200)转变为晶面(111)。
2) 复合镀层的显微硬度随镀液中纳米颗粒浓度增加呈先增后降低的趋势,而摩擦因素则呈先降低后增加的趋势,当镀液中添加SiC颗粒浓度为4.0 g/L时,复合镀层的显微硬度最大,为456 HV,摩擦因素最小,平均值为0.28左右,为微米复合镀层的1/2,在900 ℃、100 h 氧化质量增加为6.025 mg/cm2,为微米复合镀层的1/3。
REFERENCES
[1] 彭成章, 朱玲玲, 张晓菲. 脉冲电沉积/纳米复合镀层的组织结构与性能[J]. 润滑与密封, 2010, 35(6): 85-88.
PENG Cheng-zhang, ZHU Ling-ling, ZHANG Xiao-fei. Structure and properties of pulse electroplated Ni/nano-Al2O3 composite coatings[J]. Lubrication Engineering, 2010, 35(6): 85-88.
[2] FENG Qiu-yuan, LI Ting-ju, YUE Hong-yun, QI Kai, BAI Fu dong, JIN Jun-ze. Preparation and characterization of nickel nano-Al2O3 composite coatings by sediment co-deposition[J]. Applied Surface Science, 2008, 254(8): 2262-2268.
[3] POMPEI E, MAGAGNIN L, LECIS N, CAVALLOTTI P L. Electrodeposition of nickel-BN composite coatings[J]. Electrochimica Acta, 2009, 54 (9): 2571-2574.
[4] 马明硕, 常立民, 徐 利. 脉冲电沉积纳米镍-碳化硅复合镀层的性能[J]. 电镀与涂饰, 2011, 31(2): 14-16.
MA Ming-shuo, CHANG Li-min, XU Li. Properties of nickel-silicon carbide nanocomposite coating prepared by pulse electrodeposite[J]. Electroplating and Finishing, 2011, 31(2): 14-16.
[5] 郑学斌, 谭澄宇, 赵旭山, 刘 宇. Ni/SiC复合镀层腐蚀行为研究[J]. 材料保护, 2008, 41(2): 17-19.
ZHENG Xue-bin, TAN Cheng-yu, ZHAO Xu-shan, LIU Yu. Corrosion behavior of Ni/SiC composite coating in saline solution[J]. Journal of Materials Protection, 2008, 41(2): 17-19.
[6] ZHOU Yue-bo, DING Yuan-zhu. Oxidation resistance of co-deposited Ni-Sic nanocomposite coating[J]. Transaction of Nonferrous Metals Society of China, 2007, 17(5): 925-928.
[7] GüL H, UYSAL F K M, ASLAN S, ALP A, AKBULUT H. Effect of particle concentration on the structure and tribological properties of submicron particle SiC reinforced Ni metal matrix composite (MMC) coatings produced by electrodeposition[J]. Applied Surface Science, 2012, 258(10): 4260-4267.
[8] KARBASI M, YAZDIAN N, VAHIDIAN A. Development of electro-co-deposited Ni-TiC nano-particle reinforced nanocomposite coatings[J]. Surface and Coatings Technology, 2012, 207: 587-593.
[9] ZHAO Q, LIU Y, ABEL E W. Effect of Cu content in electroless Ni-Cu-P-PTFE composite coatings on their anti-corrosion properties[J]. Materials Chemistry and Physics, 2004, 8(7): 332-335.
[10] 朱乃龙, 杨顺贞, 纪秀林. Ni-P-MoS2复合镀层的制备和耐磨性能研究[J]. 热加工工艺, 2011, 40(12): 137-139.
ZHU Nai-long, YANG Shun-zhen, JI Xiu-lin. Preparation of Ni-P-MoS2 composite coating and study on its wear resistance[J]. Hot Working Technology, 2011, 40(12): 137-139.
[11] CARDINAL M F, CASTRO P A, BAXI J, LIANG H, WILLIAMS F J. Characterization and frictional behavior of nanostructured Ni-W-MoS2 composite coatings[J]. Surface and Coatings Technology, 2009, 204(1/2): 85-90.
[12] 王 平, 程英亮, 张 昭. 不同的SiC纳米颗粒镀前处理对Ni-SiC纳米复合镀层性能的影响[J]. 材料保护, 2010, 43(11): 23-26.
WANG Ping, CHENG Ying-liang, ZHANG Zhao. Effect of pretreatment modes of silicon carbide nanoparticulates on the properties of electroplated Ni-SiC nanocomposite coatings[J]. Materials Protection, 2010, 43(11): 23-26.
[13] 王 琳, 孙本良, 许 为, 姜秀明, 张 雷, 林辉龙. 工艺参数对 Ni-SiC 纳米复合镀层硬度的影响[J]. 电镀与精饰, 2012, 34(5): 8-11.
WANG Lin, SUN Ben-liang, XU Wei, JIANG Xiu-ming, ZHANG Lei, LIN Hui-long. Influences of Technological Parameters on the Hardness of Ni-SiC Nano-composite[J]. Plating and Finishing, 2012, 34(5): 8-11.
[14] RANJAN S, SIDDHARTHA D, KARABI D. The effect of bath temperature on the crystallite size and microstructure of Ni-CeO2 nanocomposite coating[J]. Materials Characterization, 2011, 62(3): 257-262.
[15] AUEZHAN A, OLEKSIY V P, YOUNG S P, DAE E K. Effects of ultrasonic nanocrystalline surface modification on the tribological properties ofAZ91Dmagnesiumalloy[J]. Tribology International, 2012, 54: 106-113.
[16]
, ASLAN S, ALP A, AKBULUT H. Effect of CTAB concentration in the electrolyte on the tribological properties of nanoparticle SiC reinforced Ni metal matrix composite (MMC) coatings produced by electrodeposition[J]. Colloids and Surfaces A, 2013, 419: 53-60.
[17] MEENU S, WILLIAM G, ANJANA J, RAJAM K S. Influence of SiC particle size on the structure and tribological properties of Ni-Co composites[J]. Surface and coatings Technology, 2007, 202(2): 310-318.
[18] BABAK B, ALIREZA A. Effect of particle size and co-deposition technique on hardness and corrosion properties of Ni-Co/SiC composite coatings[J]. Surface and Coatings Technology, 2012, 206(23): 4964-4975.
[19] 李铁藩. 金属高温氧化和热腐蚀[M]. 北京: 化学工业出版社, 2003: 56-57.
LI Tie-fan. High temperature oxidation and hot corrosion of metal[M]. Beijing: Chemical Industry Press, 2003: 56-57.
(编辑 李艳红)
基金项目:国家青年科学基金资助项目(51301086);南京工程学院资助项目(N20130212,CKJB201205)
收稿日期:2014-10-09;修订日期:2015-02-10
通信作者:王红星,副教授,博士;电话:025-86118274;E-mail: wanghx@njit.edu.cn