
Mechanical characterization of cp-Ti produced by investment casting
Khaled M. IBRAHIM1, Mansour MHAEDE2, Lothar WAGNER2
1. Central Metallurgical R&D Institute (CMRDI), P. O. Box 87, Helwan, Cairo, Egypt;
2. Institue of Materials Science and Engineering, TU-Clausthal, Agricolastr. 6, D-38678, Clausthal-Zellerfeld, Germany
Received 27 August 2010; accepted 10 March 2011
Abstract: The influence of hot swaging (SW) and annealing treatment on microstructure and mechanical properties of commercially pure titanium produced by investment casting was evaluated. The as-cast samples showed a typical microstructure consisting of a variety of α-morphologies, while the hot swaged samples exhibited a kinked lamellar microstructure. Annealing at 500 °C did not significantly change this microstructure while annealing at 700 and 870 °C led to recrystallization and formation of equiaxed microstructures. The cast bars exhibited a typical hard α-layer in near-surface regions with a maximum depth and maximum hardness of 720 μm and HV0.5 660, respectively. Due to SW, the tensile strength of the as-cast material drastically increased from 605 MPa to 895 MPa. Annealing at 500 °C decreased the tensile strength slightly from 895 to 865 MPa while annealing at 700 °C led to a further pronounced drop in tensile strength from 865 to 710 MPa. No additional decrease in tensile strength was noticed with increasing the annealing temperature from 700 to 870 °C. The true fracture strain of the as-cast and hot swaged samples was in the range of 0.05 to 0.12, while the annealed samples showed values in the range of 0.25 to 0.53. In addition, the as-cast and hot swaged samples revealed a brittle cleavage fracture surfaces. However, the annealed samples showed a transgranular ductile fracture with formation of dimples.
Key words: pure titanium; investment casting; swaging; thermo-mechanical processing; mechanical properties
1 Introduction
Titanium alloys offer a unique combination of mechanical and physical properties as well as excellent corrosion resistance, which makes them desirable for a variety of critical applications [1-3]. Elevated strength to mass ratio is the primary incentive for selection and design into aerospace applications including engine and airframe components. The expansion of titanium applications to non-aerospace industries, such as automotive, chemical, energy, marine, biomedicals, sports and architecture, entails improvements in the understanding of titanium metallurgy, advances in processing methods, ability to manufacture components without defects and development of low cost titanium alloys [4-5]. Commercially pure titanium (cp-Ti) is one of the most important titanium materials and widely used in many areas such as chemical, nuclear and especially biomedical industries [6-8]. The high cost of titanium makes net shape manufacturing routes very attractive. Casting is a near net shape manufacturing route that offers significant cost advantages over forging or fabricated structures [9]. The phase transformations that occur in titanium and its alloys make understanding of solidification and microstructure development more difficult than that of many other foundry alloys. Under equilibrium conditions, solidification in pure titanium occurs at 1 668 °C. At 882 °C, this high temperature BCC β-phase transforms into the HCP low temperature α-phase [10]. The microstructure of castings made of cp-Ti normally consists of equiaxed prior-β grains, and some castings exhibit a small columnar zone at the mould wall. Within each equiaxed prior-β grain, a multitude of various α-morphologies exist, including Widmanstaetten, acicular, grain-boundary, lamellar, serrated and plate-like α [11-14]. Moreover, the as-cast cp-Ti microstructure yields little information about the solidification aspects of the high temperature β-phase. Only prior-β grains remain, and within these grains various α-morphologies exist. The prior-β grains remain visible because various α-morphologies nucleate from these boundaries, including the grain boundary α. In addition, the α-phase does not cross prior-β grain boundary [10].
Investment casting is considered one of the casting techniques that are used intensively for producing net shape components. Investment casting is applied in the automotive, aerospace and biomedical industries for production of complex shapes [15-17]. In this process, the shape to be produced is formed in wax and coated in a chemically bonded ceramic investment material. The investment is then heated to remove the wax. This process has the advantage of producing complex shapes at relatively low cost, scalability from single items to large numbers of products and low wastage of raw materials [18]. In titanium casting, pores are developed by gas entrapment and metal shrinkage upon solidification. Since volumetric shrinkage of titanium during solidification is high, approximately 3.5%, some of the total volumetric shrinkage will be converted to porosity [19] if casting procedures are not precisely controlled. This type of porosity is quantitatively predictable, concentrated in the areas that solidify last and strongly relate to the geometry of the casting and design of feeding sprues [20].
The present work is undertaken to cast cp-Ti in ceramic mould using investment casting technique. Hot swaging (SW) and annealing treatment are applied to enhancing the mechanical properties of the cast samples. Microstructure and mechanical properties of the as-cast, hot swaged and annealed conditions are studied.
2 Experimental
Commercially pure titanium (Grade 4) samples were produced by melting in a vacuum induction skull melting furnace. This was done twice in order to get homogenous material. Investment casting technique was used to prepare two bars with diameter and length of 30 mm and 300 mm, respectively. An aluminum die was first prepared to form the wax pattern and then a ceramic mould was built on, as shown in Fig. 1(a). The ceramic mould was heated to 900 °C using a mould heater inside the induction furnace. The cast cp-Ti bars are shown in Fig. 1(b). In order to investigate the influence of ceramic mould on the structure of the cast cp-Ti alloy, the samples were longitudinally sectioned and photographed using stereo-microscopy. These bars were pre- conditioned by removing 2.5 mm from the surface by turning in order to get rid of the hard a-layer and to smooth the surface. As illustrated in Fig. 2, SW at 700 °C was applied to reducing the bars diameter from 25 mm to 8.5 mm. This was done using 14 steps with intermediate re-heating of 2 min. Part of the SW samples were annealed at either 500 °C, 700 °C or 870 °C for 1 h. The microstructures of the various conditions were investigated using optical microscopy. Tensile properties of the as-cast, SW and SW + annealed conditions were evaluated. The fracture surfaces of the tensile samples were examined using scanning electron microscopy.
3 Results and discussion
The chemical composition of the cast bars is given in Table 1. All measured element concentrations are within typical values of cp-titanium (Grade 4) reported in Ref. [11]. The as-investment cast microstructure is shown in Fig. 3(a). The microstructure consists mainly of equiaxed prior-β grains and a variety of α-morphologies inside these grains. The α-morphologies at different locations can be identified as grain boundary α(A), fine acicular α(B) and Widmanstaetten α(C) (Fig. 3(a)). As shown in Fig. 3(b), the as-swaged microstructure is characterized by bent and kinked lamellae resulting from the severe plastic deformation applied during rotary swaging at 700 °C. Figure 4 illustrates the SW microstructures after annealing at temperatures ranging from 500 °C to 870 °C. Annealing at 500 °C (Fig. 4(a)), 700 °C (Fig. 4(b)) and 870 °C (Fig. 4(c)) leads to equiaxed grain sizes of roughly 12, 32 and 41 μm, respectively.
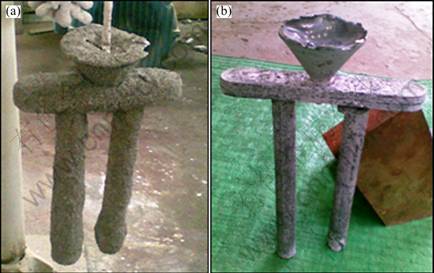
Fig. 1 Cast cp-Ti bars by investment casting: (a) Ceramic mould; (b) Cast bars
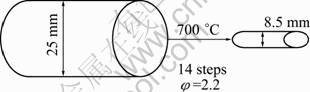
Fig. 2 Schematic of bar reduction by swaging
Table 1 Chemical composition of investigated cp-Ti (mass fraction, %)
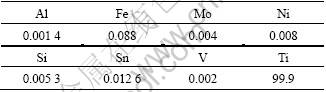
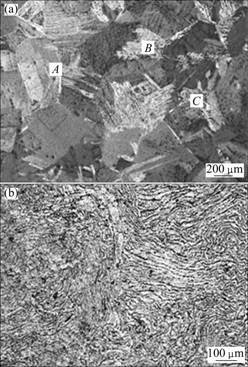
Fig. 3 Microstructures of cp-Ti: (a) As-investment cast; (b) As-swaged
The cross-sectional morphologies of the as-cast material is shown in Fig. 5. As expected, a reaction layer caused by oxygen pick-up during casting is clearly visible in near-surface regions of the investment cast bars (Fig. 5(a)). Below this oxygen enriched layer, the typical lamellar microstructure is formed (Fig. 5(b)). This gradient in microstructure from the surface to the interior is also reflected in the microhardness-depth distribution, as shown in Fig. 6. The hardness decreases from a maximum of HV0.5 660 at the outer surface gradually to a constant value of HV0.5 265 as a distance of about 720 μm from the surface is reached. This hard oxygen-induced alpha case is unavoidable in investment casting of Ti-alloys and can also reach hundreds of microns in other titanium alloys [21].
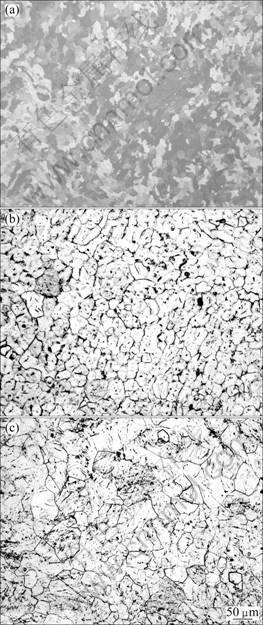
Fig. 4 Microstructures of SW samples annealed at various temperatures for 1 h: (a) 500 °C; (b) 700 °C; (c) 870 °C
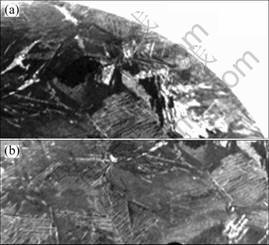
Fig. 5 Cross-sectional macrostructures of as-cast bars: (a) Near-surface region; (b) Central region
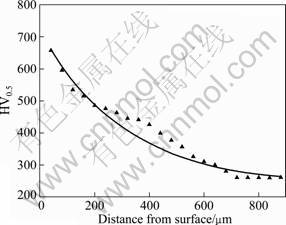
Fig. 6 Microhardness-depth profile in as-cast bars
The tensile properties of the as-cast, SW, and SW + annealed conditions are listed in Table 2. Swaging increases the ultimate tensile strength (UTS) of the as-cast bar by as much as 290 MPa from 605 to 895 MPa. This increase in strength is due to the swaging-induced high dislocation densities and the refined microstructure (Figs. 3 and 4). Annealing at 500 °C for 1 h slightly decreases strength from 895 to 865 MPa, while annealing at higher temperatures of 700 and 870 °C shows a marked loss in strength amounting to 250 and 245 MPa, respectively (Table 2).
Table 2 Tensile properties of cp-Ti at various conditions
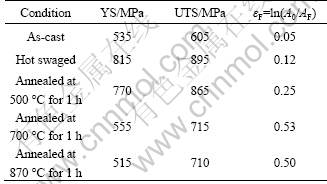
As expected, the true fracture strain of the as-cast condition is the lowest with eF = 0.05. After hot swaging, this value clearly increases to eF = 0.12 due to breaking down the as-cast coarse microstructure. The effect of the annealing temperature on YS, UTS and eF is illustrated in Fig. 7. YS as well as UTS gradually decreases with an increase in annealing temperature. As the strength values decrease, the true fracture strain markedly increases. With an increase in annealing temperature, the difference between UTS and YS clearly increases amounting to 195 MPa at the highest annealing temperature of 870 °C (Fig. 7). However, the difference between UTS and YS is estimated to be 80 MPa at ambient temperature (SW-condition).
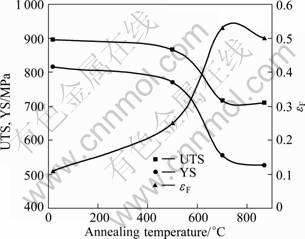
Fig. 7 Effect of annealing temperature after SW on tensile properties of cp-Ti
The fracture surfaces of the tensile samples in the various conditions were carefully examined by SEM, as illustrated in Fig. 8. The as-cast samples show typically cleavage fracture that normally occurs along a crystallographic plane, which in α titanium is the basal plane [22]. Because the propensity for cleavage fracture decreases with decreasing grain size, the fracture surface of the SW-samples shows cleavage facets with large amounts of dimples at the grain boundaries (Fig. 8(b)). The samples annealed at 700 °C and 870 °C show a transgranular ductile fracture with a strong formation of dimples due to the high ductility (Figs. 8(c) and (d)).
4 Conclusions
1) The microstructure of the as-cast cp-Ti contains a variety of α-morphologies, grain boundary α, fine acicular α and Widmanstatten α inside the prior β-grains. The hot swaged samples show a kinked lamellar microstructure with existing of α-phase flow due to the superplasticity during the swaging process.
2) The as-cast bars show a hard α-layer on the surface of about 720 μm depth and the maximum hardness on the outer layer of the as-cast bars is HV0.5 660, while the base metal hardness is HV0.5 265.
3) As-cast samples obtain a tensile strength of 605 MPa, which is markedly increased by swaging up to 895 MPa, and further annealing up to 870 °C results in a loss of the strength to 710 MPa. The true fracture strain of the as-cast conditions is significantly increased with SW and SW + annealing.
4) As-cast and hot swaged tensile samples obtain a brittle cleavage fracture surface, while the annealed samples show a transgranular ductile fracture with formation of dimples.
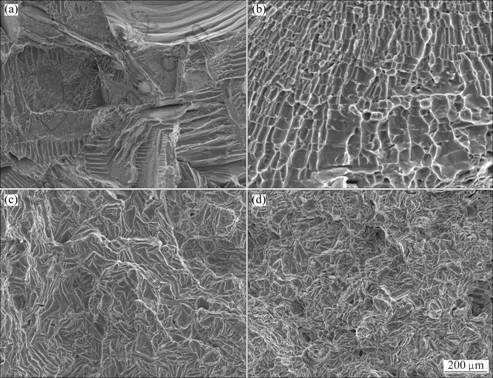
Fig. 8 Tensile fracture surfaces of cp-Ti in various conditions: (a) As-cast; (b) SW; (c) SW + annealing at 700 °C; (d) SW + annealing at 870 °C
Acknowledgements
The financial support by the Egyptian Science and Technology Development Fund (STDF) and the German International Bureau of the Federal Ministry of Education and Research under project number EGY 08-070 is gratefully acknowledged.
References
[1] TAMIRISAKANDALA S, VEDAM B V, BHAT R B. Recent advances in the deformation processing of titanium [J]. J Mater Eng Perform, 2003, 12: 661-673.
[2] BALAZIC M, KOPAC J, JACKSON M, AHMED W. Review: Titanium and titanium alloys applications in medicine [J]. Intern J Nano Biomater, 2007, 1: 3-34.
[3] CHENG W W, JU C P, LIN J H. Structure, castability and mechanical properties of commercially pure and alloyed titanium cast in graphite mould [J]. J Oral Rehabit, 2007, 34: 528-540.
[4] CLEMENT N, LENAIN A, JACQUES P J. Mechanical property optimization via microstructural control of new metastable beta titanium alloys [J]. JOM, 2007, 59: 50-53.
[5] FERRERO J G. Candidate materials for high strength fastener applications in both the aerospace and automotive industries [J]. J Mater Eng and Perform, 2005, 14: 691-695.
[6] TAN M J, ZHU X J. Microstructure evolution of cp titanium during high temperature deformation [J]. J Archiv Mater Sci Eng, 2007, 28: 5-11.
[7] TAN M J, ZHU X J. Dynamic recrystallization in commercially pure titanium[J]. J Achiev Mater Manuf Eng, 2006, 18: 183-186.
[8] WATANABE K, MIYAKAWA O, TAKADA Y, OKUNO O, OKABE T. Casting behaviour of titanium alloys in a centrifugal casting machine [J]. Biomater, 2003, 24: 1737-1743.
[9] ROCHN S S, ADABO G L. Vickers hardness of cast commercially pure titanium and Ti-6Al-4V alloy submitted to heat treatment [J]. J Braz Dent, 2006, 17: 126-129.
[10] BERMINGHAM M J, McDONALD S D, DARGUSCH M S, JOHN D H. Microstructure of cast titanium alloys [J]. Mater Forum, 2007, 31: 84-89.
[11] BERMINGHAM M J, McDOLAND S D, DARGUSCH M S, JOHN D H. The mechanism of grain refinement of titanium by silicon [J]. Script Mater, 2008, 58: 1050-1053.
[12] BERMINGHAM M J, McDOLAND S D, JOHN D H, DARGUSCH M S. Beryllium as a grain refiner in titanium alloys [J]. J Alloys Compd, 2009, 48: 120-123.
[13] KOIKE M, CAI Z, FUJII H, REZNER M, OKABE T. Corrosion behaviour of cast titanium with reduced surface reaction layer made by a face-coating method [J]. Biomater, 2003, 24: 4541-4549.
[14] BERMINGHAM M J, McDOLAND S D, DARGUSCH M S, JOHN D H. Grain-refinement mechanisms in titanium alloys [J]. J Mater Res Soc, 2008, 23: 97-104.
[15] ATWOOD R C, LEE P D, CURTIS R V, MAIJER D M. Modeling the investment casting of a titanium crown [J]. Dent Mater, 2007, 23: 60-70.
[16] ELIOPOULOS D, ZINELIS S, PAPADOPOULOS T. The effect of investment material type on the contamination zone and mechanical properties of commercially pure titanium castings [J]. J Prosthet Dent, 2005, 94: 539-548.
[17] SHIMIZU H, HABU T, TAKADA Y, WATANABE K, OKUNO O, OKABE T. Mold filling of titanium alloys in two different wedge-shaped molds [J]. Biomater, 2002, 23: 2275-2281.
[18] OLIVEIRA P, ADABO G L, RIBEIRO R F, ROCHA S, AVILA F A, VALLE A L. Influence of the final temperature of investment heating on the tensile strength and Vickers hardness of cp-Ti and Ti-6Al-4V alloy [J]. J Appl Oral Sci, 2007, 15: 44-48.
[19] WU M, SCHADLICH J, AUGTHUN M, SPIELERMAN H. Computer-aided prediction and control of shrinkage porosity in titanium dental casting [J]. Dent Mater, 1998, 14: 321-328.
[20] ELIOPOULOS D, ZINELIS S, PAPADOPOULOS T. Porosity of cp-Ti casting with four different casting machines [J]. J Prosthet Dent, 2004, 92: 377-381.
[21] FRUEH C, POIRIER D R, MAGUIRE M C. The effect of silicon containing binders on titanium/face coat reaction [J]. Metall Mater Trans B, 1997, 28: 919-926.
[22] LUETERING G, WILLIAMS J C. Titanium [M]. Berlin, Heidelberg: Springer-Verlag, 2003. (in German)
精密铸造工业纯Ti的力学性能
Khaled M. IBRAHIM1, Mansour MHAEDE2, Lothar WAGNER2
1. Central Metallurgical R&D Institute (CMRDI), P. O. Box 87, Helwan, Cairo, Egypt;
2. Institue of Materials Science and Engineering, TU-Clausthal,
Agricolastr. 6, D-38678, Clausthal-Zellerfeld, Germany
摘 要:研究了热旋锻和退火处理对精密铸造工业纯钛显微组织和力学性能的影响。铸造样品为典型的含有不同形貌的α相组织;而旋锻样品是缠绞的层状组织。在500 °C退火处理不会显著改变样品的显微组织,但在700 °C和870 °C退火会导致再结晶发生和生成等轴晶组织。铸造棒在近表层生成典型的硬化α层,其最大深度达720 μm,最大硬度达HV0.5660。旋锻能使铸造样品的拉伸强度从605 MPa增加到895 MPa。在500 °C退火会导致拉伸强度轻微降低,从895 MPa降到865 MPa。然而在700 °C退火会导致拉伸强度显著下降,从865 MPa降到710 MPa。当退火温度升高到870 °C时,拉伸强度的下降不再明显。铸造和热旋锻样品的断裂应变在0.05~0.12的范围内,而退火后的样品在0.25~0.53的范围。铸态和旋锻态样品表现为脆性解理断裂,而退火态样品为穿晶塑性断裂,伴有韧窝的生成。
关键词:工业纯钛;精密铸造;旋锻;热力加工;力学性能
(Edited by YUAN Sai-qian)
Corresponding author: Khaled M. IBRAHIM; Tel: +20-105769514; Fax: +20-225010639; E-mail: khaledabouelela@yahoo.com
DOI: 10.1016/S1003-6326(11)60923-0