DOI:10.19476/j.ysxb.1004.0609.2018.06.18
钠硅渣在氧化铝熟料烧结过程中的物相变化
李小斌1,刘井辉1,王一霖1,曾璐2,彭志宏1,刘桂华1,周秋生1,齐天贵1
(1. 中南大学 冶金与环境学院,长沙 410083;
2. 中国恩菲工程技术有限公司,北京 100038)
摘 要:结合相关热力学计算结果,推测钠硅渣在氧化铝熟料烧结法处理过程中存在的多级反应及其产物组成,并通过研究钠硅渣在不同条件下的反应行为,验证中间相Na2-xAl2-xSixO4的存在及其溶出性能的差异。结果表明:在烧结过程中,硅系数x为0、0.05、0.25、0.35、0.45、0.55、0.85的Na2-xAl2-xSixO4均可以生成;烧结产物组成形态受反应温度和生料配比影响;当配钙比为2、烧结温度由750 ℃升高至1200 ℃时,或当配钙比由1.0升高至2.5、温度为900 ℃时,反应产物的硅系数x均可由0.85逐渐下降至0;硅系数决定反应产物的溶出性能,当x≤0.25时,Na2-xAl2-xSixO4中间相可以溶解于铝酸钠溶液。
关键词:烧结法;钠硅渣;石灰;硅系数
文章编号:1004-0609(2018)-06-1225-08 中图分类号:TF802 文献标志码:A
近年来,我国氧化铝产业持续快速发展,产能已超过7000万t[1],年赤泥堆存量近1亿t,依目前的技术现状,绝大多数赤泥不能进行高效利用,给资源与生态带来了极大的挑战[2-3]。赤泥中的有价矿物组成(如铝、钠等),多以钠硅渣或钙硅渣形态存在,与此同时,在烧结法生产氧化铝的粗液脱硅过程中,溶液中的硅酸根离子与铝酸根离子反应也会生成钠硅渣,这部分纯度较高的脱硅产物同样未得到经济的处理[4-6]。
针对赤泥与钠硅渣(DSP)中有价元素提取的研究主要有高压水化学法[7]、石灰-二氧化碳转型法[8]、酸法[9]、亚熔盐法[10]、烧结法[11-14]等。烧结法作为传统的氧化铝生产方法,与其他方法相比具有回收率高、碱耗低的优点,因此,更适于处理钠硅渣等低铝硅比矿物。但是,烧结法同时存在着能耗高,配钙量大,高温燃煤烟气中硫硝难治理的缺点[15-16],限制了该工艺的推广应用,为克服以上技术缺陷,降低烧结温度与配料量,需要对烧结过程中的反应机理与产物形态进行深入的分析。
烧结法处理低铝硅比物料机理研究较少,通常认为其宏观过程为钠硅渣与氧化钙反应生成原硅酸钙和铝酸钠,如方程(1)所示[7]。但对烧结过程中各微观组
元的反应次序尚不明确。可以借鉴的是,前苏联学者在研究高岭石-石灰石-碳酸钠三元组分烧结过程机理时指出,高岭石脱水后首先与碳酸钠反应生成霞石,而霞石与石灰的反应过程分为两个步骤:首先霞石与氧化钙反应生成铝硅酸钠和原硅酸钙(方程(2)),而后生成的铝硅酸钠再与氧化钙反应生成铝酸钠和原硅酸钙(方程(3))。而THOMPSON等[17-18]指出在NaAlO2- NaAlSiO4体系中存在x为0、0.05、0.25、0.35、0.45、0.55、0.85的Na2-xAl2-xSixO4复杂铝硅酸盐化合物,其结构受硅系数x影响较大,这意味着钠硅渣在烧结法处理过程中的反应可能更为复杂。
Na2O·Al2O3·1.7SiO2·2H2O+3.4CaO=1.7(2CaO·SiO2)+Na2O·Al2O3+2H2O (1)
Na2O·Al2O3·2SiO2+2CaO=Na2O·Al2O3·SiO2+2CaO·SiO2 (2)
Na2O·Al2O3·SiO2+2CaO=Na2O·Al2O3+2CaO·SiO2 (3)
因此,本文作者在热力学计算的基础上,分别采用人工合成矿物和钠硅渣,对石灰烧结制备氧化铝熟料过程中的物相变化、反应机理及焙烧产物的溶出性能进行深入的分析,以期为实现低温、低钙比的烧结法工艺提供理论依据。
1 热力学分析
在烧结法过程中,钠硅渣首先脱水形成NaAlSiO4,并可能与石灰发生如下反应(方程(4)~ (10))。为了便于比较,将反应物NaAlSiO4的系数定为1。根据组成类似的复杂化合物的热力学数据[19]与其组成存在的线性关系[20]对不同硅系数x为0、0.05、0.25、0.35、0.45、0.55、0.85的Na2-xAl2-xSixO4基础热力学数据进行了估算,如表1所示。
NaAlSiO4+0.6/1.15CaO=1/1.15Na1.15Al1.15Si0.85O4+0.3/1.15Ca2SiO4 (4)
NaAlSiO4+1.8/1.45CaO=1/1.45Na1.45Al1.45Si0.55O4+0.9/1.45Ca2SiO4 (5)
NaAlSiO4+2.2/1.55CaO=1/1.55Na1.55Al1.55Si0.45O4+1.1/1.55Ca2SiO4 (6)
NaAlSiO4+2.6/1.65CaO=1/1.65Na1.65Al1.65Si0.35O4+1.3/1.65Ca2SiO4 (7)
NaAlSiO4+3/1.75CaO=1/1.75Na1.75Al1.75Si0.25O4+1.5/1.75Ca2SiO4 (8)
NaAlSiO4+3.8/1.95CaO=1/1.95Na1.95Al1.95Si0.05O4+1.9/1.95Ca2SiO4 (9)
NaAlSiO4+2CaO=NaAlO2+Ca2SiO4 (10)
为了研究反应(4)~(10)在烧结条件的可行性,计算了不同温度下其反应吉布斯自由能的变化,如图1所示。反应(4)~(10)的吉布斯自由能均随温度升高而下降,在计算的温度范围内,其值均为负,这意味着不同硅系数x为0、0.05、0.25、0.35、0.45、0.55、0.85的Na2-xAl2-xSixO4均可以通过钠硅渣与石灰的反应得到,其相应硅系数随配钙比增大而降低。同时,随配钙比的逐步增大,相同温度下反应的吉布斯自由能呈降低趋势,说明硅系数较高时,反应得到的Na2-xAl2-xSixO4可以与CaO继续反应,向硅系数低的产物进行,最终反应生成铝酸钠和硅酸二钙。上述分析揭示了钠硅渣在氧化铝熟料烧结过程中,极有可能存在着复杂的逐级转化过程,且这一过程受温度与配钙比的影响。
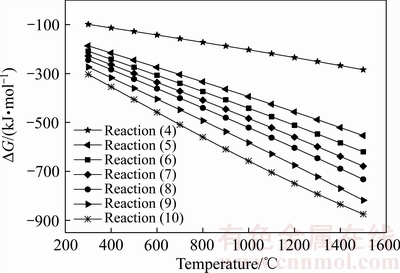
图1 反应(4)~(10)吉布斯自由能随温度变化规律
Fig. 1 Gibbs free energies of reactions (4)-(10) at different temperatures
2 实验
2.1 实验原料
钠硅渣由高岭土矿物与铝酸钠溶液(ρ(Na2Ok)= 230 g/L,ρ(Na2Ok)为苛性氧化钠浓度;αk=2, αk为溶液中苛性氧化钠与氧化铝的分子比)在260 ℃下反应90 min制得(L/S=5),试样用纯水经洗涤后在50 ℃烘干。经化学计量分析,钠硅渣的主要组成为23.52% Na2O、30.29% Al2O3、28.15% SiO2、灼减为14.07%,其XRD谱如图2所示,合成的钠硅渣主要以苏打石形态存在,少量以钙霞石形态存在。反应所用的铝酸钠溶液由分析纯氢氧化铝,分析纯氢氧化钠和纯水配置得到。纯物质烧成实验用碳酸钙、碳酸钠、氢氧化铝与硅酸钠为分析纯。
表1 Na2-xAl2-xSixO4的热力学数据
Table 1 Estimated thermodynamic data of Na2-xAl2-xSixO4
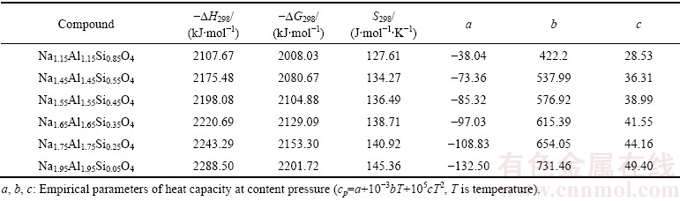
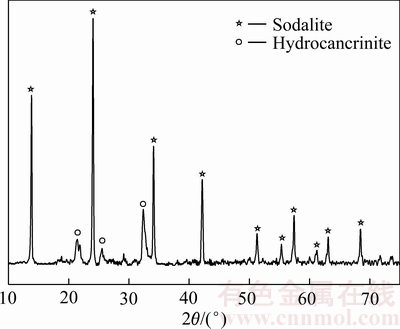
图2 钠硅渣的XRD谱(260 ℃, 1.5 h)
Fig. 2 XRD pattern of sodium hydrate alumino-silicate (260 ℃, 1.5 h)
2.2 实验方法
2.2.1 钠硅渣石灰烧结
按不同的配钙比,称取一定质量的钠硅渣、碳酸钙放入混料瓶中,并在对辊式多功能矿物混料机(长沙索拓科学仪器设备有限公司)上将其混合均匀制备成生料;称取混匀后的生料放入刚玉坩埚内,盖上坩埚盖,置于已预热至烧结温度的高温箱式电阻炉(SX-6-16型,长沙科鑫炉业有限公司)内反应2 h,然后将熟料转移至600 ℃的马弗炉内放置30 min,取出自然冷却至室温。冷却后将熟料磨细,混匀并置于磨口瓶中备用。
2.2.2 熟料溶出
模拟熟料工业溶出条件对熟料溶出性能进行了研究:移取50 mL调整液(ρ(Na2Ok)=80 g/L,ρ(Na2OC)=10 g/L,ρ(Na2OC)为以碳酸钠存在的Na2O浓度, αk=1.8)加入到低压反应群釜的钢弹(容积150 mL)中,然后称取磨至粒径≤0.3 mm的熟料10 g,加入到钢弹中,再加入2个直径为15 mm的钢球以加强搅拌,将钢弹加盖拧紧密封后放入低压反应群釜中,于75 ℃下溶出反应30 min。溶出浆液真空抽滤,滤饼用热水(约90 ℃)洗涤,洗涤后的滤饼在100 ℃的烘箱中烘干后,采用容量法分析其化学成分。根据容量法分析得到的熟料和赤泥的化学成分,计算氧化铝和氧化钠的溶出率。
熟料与溶出渣中的物相组成采用Rigaku-TTRⅢ型X-射线衍射仪(日本株式会社,铜靶)进行分析。
3 结果与讨论
3.1 火法合成Na2-xAl2-xSixO4及其溶出性能
热力学计算表明,由钠硅渣制备氧化铝熟料的石灰烧结过程中可能生成一系列的Na2-xAl2-xSixO4化合物,组成复杂且x值受反应条件影响较大,因此,本研究中首先在纯物质体系下对Na2-xAl2-xSixO4的高温稳定性和溶出性能进行了研究,以明确其组成结构与性质间存在的差异。将分析纯Na2CO3、Al(OH)3和Na2SiO4按n(Na2O):n(Al2O3):n(SiO2) (N:A:S)摩尔比值分别为1:1:1、1:1:0.5、1:1:0.25配制生料,于1000 ℃下烧结反应2h后获得了人工矿物Na2-xAl2-xSixO4,并进行溶出,所得熟料及溶出渣物相分析结果如图3和表2所示。
结合图3和表2中物相分析结果可以看出,在Na2O-Al2O3-SiO2烧成体系中,熟料的物相组成与生料中硅矿物配比密切相关,在实验生料配比条件下,除未完全反应的Na2CO3和Al2O3外,熟料中可分别检测出x为0.05、0.25、0.35、0.45、1的Na2-xAl2-xSixO4的物相(XRD标准卡片序号分别为49-003、49-004、49-005、49-006、33-1200),不同配比烧成熟料的主要物相实际分子比与配料分子比较为接近,且随着生料中硅配比的降低,钠硅渣中x值同步下降,这验证了前文热力学分析结果,不同x值的Na2-xAl2-xSixO4物相均可在烧结条件下生成,并可能作为石灰烧结过程中各级反应的微观组元。
进一步结合溶出渣的物相结果可以发现,Na2-xAl2-xSixO4在铝酸钠调整液中的稳定性也随其x值的不同而存在差异:生料配比N:A:S=1:1:1时,熟料与溶出渣中物相保持一致,说明x为0.45和1时的Na2-xAl2-xSixO4不能溶解于铝酸钠溶液;而生料配比为N:A:S=1:1:0.5和N:A:S=1:1:0.25时,溶出渣相中物相组成发生明显变化,Na1.55Al1.55Si0.45O4和Na1.65Al1.65Si0.35O4的特征衍射峰没有变化,而Na1.75Al1.75Si0.25O4和Na1.95Al1.95Si0.05O4的特征衍射峰消失。结合NaAlO2在碱液中的可溶解性质,可以认为只有当硅系数x≤0.25时,Na2-xAl2-xSixO4在铝酸钠溶液中才具有良好的低温溶解性能,这一新发现对于烧结熟料物相设计和溶出过程反应行为具有重要的指导意义。
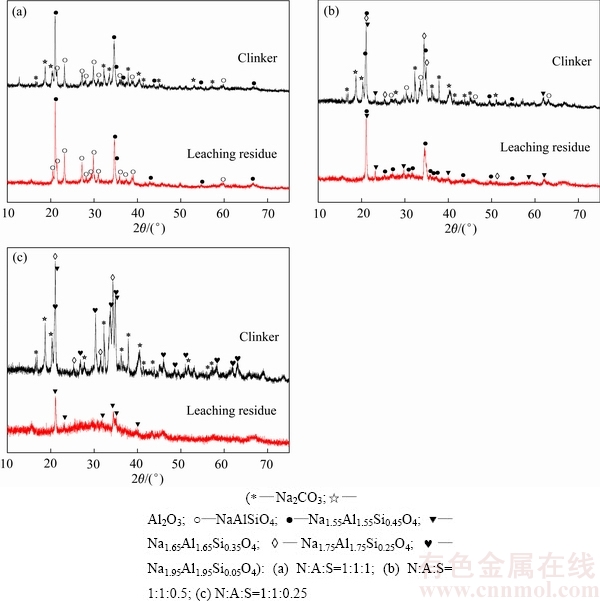
图3 纯物质体系下熟料和溶出渣的XRD谱
Fig. 3 XRD patterns of synthesized sintering clinker and leaching residues
表2 纯物质烧结熟料及溶后渣的物相组成
Table 2 Composition of synthesized sintering clinkers and leaching residues
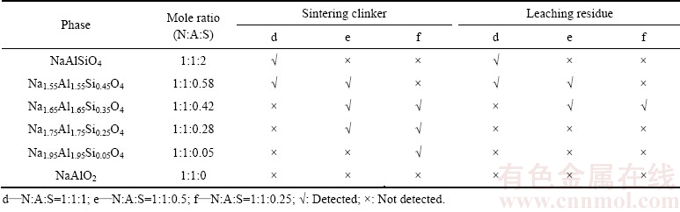
3.2 钠硅渣石灰烧结
3.2.1 烧结温度的影响
采用传统烧结法处理铝土矿或赤泥提取氧化铝时,为满足铝酸钠与原硅酸钙的生成反应及适当的烧成带液相量,烧结温度通常控制在1100~1200 ℃之间,而热力学计算表明,钠硅渣石灰烧结的反应可在较低的温度进行,且相同温度下不同组成的Na2-xAl2-xSixO4生成趋势不同,因此需要明确反应温度与烧成熟料组成的关系。实验考察了750~1200 ℃温度条件下钠硅渣与碳酸钙二组分烧结的反应行为,配钙比为2,反应时间2h,不同温度下烧成熟料的X射线衍射光谱如图4所示(图中配钙比为2.0,烧结时间2 h)。
由图4可知,相同配比的生料在不同温度条件下烧结得到的熟料物相组成具有明显的区别,随烧结温度由750 ℃升高至1200 ℃,熟料中Na2-xAl2-xSixO4 的主要存在形态由最初的NaAlSiO4,逐渐转化为Na1.15Al1.15Si0.85O4(750 ℃),Na1.45Al1.45Si0.55O4(800 ℃),Na1.65Al1.65Si0.35O4(850 ℃),Na1.75Al1.75Si0.25O4(900 ℃,1000 ℃),Na1.95Al1.95Si0.05O4(1000 ℃),和NaAlO2 (1200 ℃),而熟料中硅钙矿物均以原硅酸钙Ca2SiO4形态存在,且其特征衍射峰的强度随烧结温度升高而逐渐增强。因此说明,在钠硅渣石灰烧结过程,Na2-xAl2-xSixO4与CaCO3或CaO之间存在着逐步替代的多级反应,反应温度越高,替代程度越大,也就是说,通过调控钠硅渣石灰烧结温度,可以控制Na2-xAl2-xSixO4的形态,结合3.1中不同x值Na2-xAl2-xSixO4的溶出性能差异研究,反应产物逐步替代至Na1.75Al1.75Si0.25O4,Na1.95Al1.95Si0.05O4,和NaAlO2时,可以实现铝钠元素的溶出,即只需将烧结温度控制在900 ℃以上。
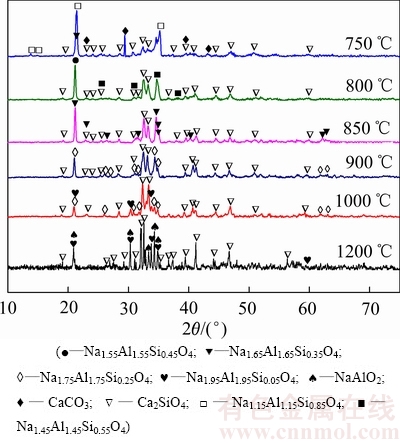
图4 不同温度下烧结熟料的XRD谱
Fig. 4 XRD patterns of sintering clinker at different temperatures
模拟工业溶出条件对不同温度下烧成熟料的溶出性能进行了研究,相应溶出渣的物相和熟料中氧化铝溶出率分析结果分别如图5和图6所示。观察可知,当烧结温度为750~850 ℃时,溶出渣中Na2-xAl2-xSixO4仍分别以Na1.15Al1.15Si0.85O4、Na1.45Al1.45Si0.55O4及Na1.65Al1.65Si0.45O4形态存在,与熟料保持一致;烧结温度为900~1200 ℃时,溶出渣中Na1.75Al1.75Si0.25O4,Na1.95Al1.95Si0.05O4和NaAlO2的特征衍射峰完全消失。上述结果说明了钠硅渣与石灰烧结过程反应得到的Na2-xAl2-xSixO4性质与通过纯物质火法合成的Na2-xAl2-xSixO4一致,当x≤0.25时,其溶解性能发生变化,使得900 ℃温度以上制备的熟料可以良好的溶解于铝酸钠调整液中。此外,除750 ℃熟料溶出渣中存在的CaCO3衍射峰是由于烧成过程未完全分解外,800~900 ℃熟料溶出渣中重新出现的CaCO3物相应为分解后的游离CaO与铝酸钠溶液中的碳酸根作用所致。图6所示为不同温度烧结温度熟料的溶出数据,当烧结温度为750~850 ℃时,熟料氧化铝溶出率仅为33.6%~41.5%,而当温度提高至900~1200 ℃后,氧化铝溶出率可快速提升至82.8%~90%,而熟料中氧化钠溶出与氧化铝溶出率趋势一致,焙烧温度为900 ℃以上时,氧化钠溶出率可达84.5%~92.8%,这再次验证了上述关于Na2-xAl2-xSixO4结构与性能差异的讨论。

图5 不同烧结温度熟料溶出渣的XRD谱
Fig. 5 XRD patterns of leaching residues obtained from clinkers sintered at different temperatures
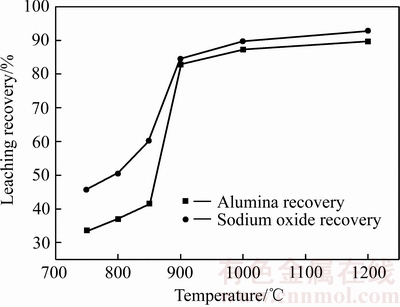
图6 烧结温度对氧化铝和氧化钠溶出率的影响
Fig. 6 Effect of sintering temperatures on alumina and sodium oxide leaching recovery
3.2.2 配钙比的影响
烧结法生料配置过程中主要指标为钙比与碱比,通常情况下,配钙比和碱比直接影响焙烧熟料中物相组成与氧化铝溶出率,考虑到钠硅渣与铝酸钠的碱比一致,烧结过程中无需另配入碱,那么生料配钙比成为首要考察的指标。实验将不同配钙比(1.0~2.5)的生料在900 ℃焙烧2 h,相应熟料的X射线衍射分析结果如图7所示(图中烧结温度900 ℃,烧结时间2 h)。

图7 不同配钙比的烧结熟料的XRD谱
Fig. 7 XRD patterns of sintering clinkers with different calcium ratios
由图7可知,在不同配钙比条件下,钠硅渣石灰烧结熟料中的硅钙化合物均为原硅酸钙(Ca2SiO4),随着配钙比(C/S)从1.0增大至1.9,铝硅酸盐的物相形式依次为:Na1.55Al1.55Si0.45O4(C/S=1.0),Na1.65Al1.65Si0.35O4 (C/S为1.3~1.6),Na1.75Al1.75Si0.25O4(C/S为1.9~2.2),Na1.95Al1.95Si0.05O4(C/S为1.9),当配钙比继续增大至2.2和2.5时,物相中出现NaAlO2和12CaO·7Al2O3的特征衍射峰。这说明了在相同的焙烧温度和焙烧时间条件下,钙比对焙烧产物的物相组成也起到了至关重要的作用,当钙比调整至1.9以上时,熟料中Na2-xAl2-xSixO4物相的x均不大于0.25,这表明在900 ℃的低温焙烧条件下,可以通过调整钙比控制得到溶出性能良好的熟料。图8所示为不同配钙比烧结熟料在模拟工业溶出条件下得到的溶出结果,与熟料中物相分析结果一致,当配钙比为1.0~1.6时,熟料氧化铝溶出率仅为39.6%~47.6%,氧化钠溶出率为45.5%~ 57.7%;当配钙比为1.9~2.5时,氧化铝和氧化钠溶出率可分别提升至82.3~88.4%与83.1%~91.6%。
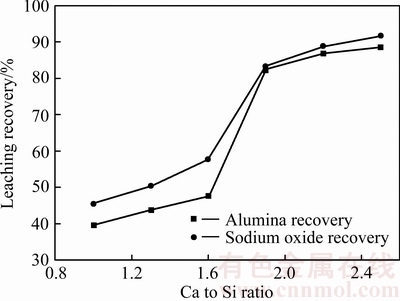
图8 配钙比对氧化铝和氧化钠溶出率的影响
Fig. 8 Effect of Ca to Si ratio on alumina and sodium oxide leaching recovery
4 结论
1) 反应热力学计算表明硅系数x为0、0.05、0.25、0.35、0.45、0.55、0.85的Na2-xAl2-xSixO4化合物均可以在烧结条件下通过钠硅渣与石灰的反应得到,并通过纯矿物实验进行了验证,发现了当x≤0.25时,Na2-xAl2-xSixO4易溶解于铝酸钠调整液。
2) 钠硅渣石灰烧结产物Na2-xAl2-xSixO4的x值同时受反应温度与配钙比影响,提高反应温度和配钙比均促使x由高向低进行转变,将烧结温度900 ℃,钙比为1.9,反应时间2 h,条件下得到的熟料磨细后于70 ℃温度下用铝酸钠调整液((ρ(Na2Ok)=80 g/L,ρ(Na2OC)=10 g/L,αk=1.8)溶出30 min,熟料中氧化铝溶出率可达85%以上,研究结果有助于低温低配钙比的烧结法技术开发与应用。
REFERENCES
[1] XUE S, KONG X, ZHU F, HARTLEY W, LI X, LI Y. Proposal for management and alkalinity transformation of bauxite residue in China[J]. Environmental Science and Pollution Research, 2016, 23(13): 12822-12834.
[2] XUE S, ZHU F, KONG X, WU C, HUANG L, HUANG N, HARTLEY W. A review of the characterization and revegetation of bauxite residues (Red mud)[J]. Environmental Science and Pollution Research, 2016, 23(2): 1120-1132.
[3] HAYNES B E H J. Bauxite processing residue: A critical review of its formation, properties, storage, and revegetation[J]. Critical Reviews in Environmental Science and Technology, 2011, 41(3):271-31.
[4] 刘桂华, 范旷生, 李小斌. 氧化铝生产中的钠硅渣[J]. 轻金属, 2006(2): 13-17.
LIU Gui-hua, FAN Guang-sheng, LI Xiao-bin. Sodium aluminosilicate hydrate inalumina production[J]. Light Metals, 2006(2): 13-17.
[5] LI Xiao-bin, ZHAO Zhuo, LIU Gui-hua, ZHOU Qiu-sheng, PENG Zhi-hong. Behavior of calcium silicate hydrate in aluminate solution[J].Transactions of Nonferrous Metals Society of China,2005, 15(5): 1145-1149.
[6] SMITH P. The processing of high silica bauxites-Review of existing and potential processes[J]. Hydrometallurgy, 2009, 98(1/2): 162-176.
[7] 杨重愚. 氧化铝生产工艺学[M]. 北京: 冶金工业出版社, 1993: 281-296.
YANG Chong-yu. Alumina processing technology[M]. Beijing: Metallurgical Industry Press, 1993: 281-296.
[8] 张亚莉. 钠硅渣湿法处理工艺与理论研究[D]. 长沙: 中南大学, 2003: 2-16.
ZHANG Ya-li. Research on hydro-treatment technology and theory of sodium hydrate alumino-silicate[D].Changsha: Central South University, 2003: 2-16.
[9] 杨会宾, 张淑珍. 钠硅渣综合利用途径[J]. 轻金属, 2008(11): 16-19.
YANG Hui-bin, ZHANG Shu-zhen. The way to utilize sodium alumino-silicate[J]. Light Metals, 2008(11): 16-19.
[10] ZHONG L, ZHANG Y, ZHANG Y. Extraction of alumina and sodium oxide from red mud by a mild hydro-chemical process[J]. Journal of Hazardous Materials, 2009, 172 (2): 1629-1634.
[11] MISHRA B, STALEY A, KIRKPATRICK D. Recovery and utilization of iron from red mud[C]// Light Metals. TMS Annual Meeting. Warrendale Pennsylvania: Mineral, Metals and Materials Society, 2001: 149-156.
[12] LIU W, YANG J, XIAO B. Application of Bayer red mud for iron recovery and building material production from alumosilicate residues[J]. Journal of Hazardous Materials, 2009, 161(1): 474-478.
[13] KUMAR R, SRIVASTAVA J, PREMCHAND. Utilization of iron values of red mud for metallurgical applications[M]. Jamshedpur, India: Environmental and Waste Management, 1998: 108-119.
[14]
E, APAK R. Furnace smelting and extractive metallurgy of red mud: Recovery of TiO2, Al2O3 and pig iron[J]. Journal of Chemical Technology and Biotechnology, 1997, 70(3): 241-246.
[15] 杨会宾, 涂赣峰, 于海燕, 潘晓林. 钠硅渣石灰烧结法工艺探索研究[J]. 有色金属(冶炼部分), 2015(7): 30-33.
YANG Hui-bin, TU Gan-feng, YU Hai-yan, PAN Xiao-lin. Exploratory study of lime sinter process for sodium aluminosilicate clinker[J]. Nonferrous Metals (Extractive Metallurgy), 2015(7): 30-33.
[16] 朱金伟, 张 凡, 王洪昌, 王 凡, 苏 韫. 高温燃煤烟气脱硫脱硝技术的发展趋势[J]. 环境工程技术学报, 2015(5): 200-204.
ZHU Jin-wei, ZHANG Fan, WANG Hong-chang, WANG Fan, SHU Yun. Analysis on development trend of desulfurization and denitration technologies for coal-fired flue gas[J]. Journal of Environmental Engineering Technology, 2015(5): 200-204.
[17] WITHERS R L, THOMPSON J G, MELNITCHENKO A, PALETHORPE S R. Cristobalite-related phases in the NaAlO2-NaAlSiO4 system. II. A commensurately modulated cubic structure[J]. Acta Crystallographica, 1998, 54(5): 547-557.
[18] THOMPSON J G, WITHERS R L, MELNITCHENKO A, PALETHORPE S R. Cristobalite-related phases in the NaAlO2-NaAlSiO4 system. Ⅰ. Two tetragonal and two orthorhombic structures[J]. Acta Crystallographica, 1998, 54(5): 531-546.
[19] 胡建华, 叶大伦. 实用无机热力学数据手册[M]. 2版. 北京: 冶金工业出版社, 2002: 3-24.
HU Jian-hua, YE Da-lun. Thermodynamics data directory of inorganic matter[M]. 2nd ed. Beijing: Metallurgical Industry Press, 2002: 3-24.
[20] 刘桂华, 李小斌, 李永芳, 彭志宏. 复杂无机化合物组成与热力学数据间的线性关系及其初步应用[J]. 科学通报, 2000, 45(13): 1386-1392.
LIU Gui-hua, LI Xiao-bin, LI Yong-fang, PENG Zhi-hong. Linear relationship between the composition of complex inorganic compounds and thermodynamic data and its preliminary application[J]. Chinese Science Bulletin, 2000, 45(13): 1386-1392.
Phase transformation of sodium hydrate alumino-silicate in alumina sintering process
LI Xiao-bin1, LIU Jing-hui1, WANG Yi-lin1, ZENG Lu2, PENG Zhi-hong1, LIU Gui-hua1, ZHOU Qiu-sheng1, QI Tian-gui1
(1. School of Metallurgy and Environment, Central South University, Changsha 410083, China;
2. The China ENFI Engineering Co., Ltd., Beijing 100038, China)
Abstract: According to the thermodynamic calculation, the multistage reaction and the product composition of sodium hydrate alumino-silicate were proposed in alumina sintering process. The presence of Na2-xAl2-xSixO4 and the differences of dissolution performance were confirmed by the reactions of sodium hydrate alumino-silicate under different conditions. The results show that all the Na2-xAl2-xSixO4 (x=0, 0.05, 0.25, 0.35, 0.45, 0.55, 0.85) can be formed in the alumina sintering process. And the composition of sintering products were influenced by sintering temperature and raw material proportioning. The silicon coefficient (x) of Na2-xAl2-xSixO4 can reduce from 0.85 to 0 gradually with the sintering temperature ranging from 750 ℃ to 1200 ℃ (mole ratio of CaO to SiO2 is 2), or the mole ratio of CaO to SiO2 increasing from 1 to 2.5 (sintering temperature 900 ℃). The dissolution performance of Na2-xAl2-xSixO4 was determined by the silicon coefficient (x), and the Na2-xAl2-xSixO4 can be dissolved in sodium aluminate solution with x≤0.25.
Key words: sintering; sodium hydrate alumino-silicate; lime; silicon coefficient
Foundation item: Project(51374239) supported by the National Natural Science Foundation of China
Received date: 2017-03-20; Accepted date: 2017-06-01
Corresponding author: LI Xiao-bin; Tel: +86-731-88877830; E-mail: x.b.li@csu.edu.cn
(编辑 李艳红)
基金项目:国家自然科学基金项目资助(51374239)
收稿日期:2017-03-20;修订日期:2017-06-10
通信作者:李小斌,教授,博士;电话0731-88877830;E-mail: x.b.li@csu.edu.cn