
Effects of process parameters on numerical control bending process for
large diameter thin-walled aluminum alloy tubes
LI Cheng(李 成)1, YANG He(杨 合)1, ZHAN Mei(詹 梅)1, XU Xu-dong(许旭东)2, LI Guang-jun(李光俊)1
1. State Key Laboratory of Solidification Processing, School of Materials Science and Engineering,
Northwestern Polytechnical University, Xi’an 710072, China;
2. Chengdu Aircraft Industry (Group) Corporation Ltd, Chengdu 610092, China
Received 23 May 2008; accepted 16 October 2008
Abstract: Numerical control(NC) bending experiments with different process parameters were carried out for 5052O aluminum alloy tubes with outer diameter of 70 mm, wall thickness of 1.5 mm, and centerline bending radius of 105 mm. And the effects of process parameters on tube wall thinning and cross section distortion were investigated. Meanwhile, acceptable bending of the 5052O aluminum tubes was accomplished based on the above experiments. The results show that the effects of process parameters on bending process for large diameter thin-walled aluminum alloy tubes are similar to those for small diameter thin-walled tubes, but the forming quality of the large diameter thin-walled aluminum alloy tubes is much more sensitive to the process parameters and thus it is more difficult to form.
Key words: large diameter thin-walled aluminum alloy tubes; small bending radius; numerical control bending process
1 Introduction
The research and development of numerical control (NC) bending processes for large diameter thin-walled aluminum alloy tubes with small bending radii is not only one of the demands urgently to be solved in the manufacturing advanced airplanes, but also one of the frontiers in advanced plastic forming fields. However, NC bending processes of thin-walled tubes are very complex tri-nonlinear physical processes with multi-factor coupling interactive effects under multi-die[1-2]. Thus, if there is any deviation of process parameters, it is possible for the tubes to produce over-thinning, section distortion or even wrinkling, and these phenomena occur more easily for large diameter thin-walled aluminum alloy tubes with small bending radii. The key to realize stable and precise bending forming is to select sound process parameters in order to control the stress and strain states, and thus the degrees of ovalization and thinning of the bending tubes can be controlled to some acceptable extent under free wrinkling. And thus, it is necessary to study forming laws in NC bending processes for large diameter thin-walled aluminum alloy tubes with small bending radii, particularly, effects of process parameters. Much research work, using FEM and experiments, has been carried out on the thin-walled tube bending processes, and the stress and strain distribution, tube wall thinning, cross section ovalization and other defects in the NC bending have been studied[3-16]. However, there have not been sufficient studies in the literature on NC bending processes for large diameter thin-walled aluminum alloy tubes with small bending radii.
In this work, the experiments were carried out to investigate the effects of process parameters on tube wall thinning and cross section distortion during NC bending processes for large diameter thin-walled aluminum alloy tubes with small bending radii.
2 Experimental
2.1 Experiment equipment
In this work, experiments were carried out using the NC hydraulic tube bender W27YPC-159, which was equipped with push assistant and booster, as shown in Fig.1. Its bending capacity was up to d159 mm (outer diameter)×12 mm (wall thickness). The largest and the smallest centerline bending radii were 450 mm and 105 mm, respectively. The rotational velocity of the bending die (bending velocity) ranged from 0 r/min to 0.8 r/min.
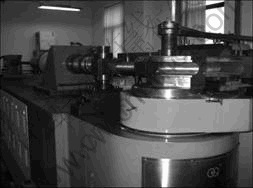
Fig.1 NC hydraulic tube bender W27YPC-159
2.2 Materials and experimental parameters
The 5052O aluminum tubes (d70 mm×1.5 mm) studied in this work are widely used in aerospace, since their strength can be improved by cold-work hardening. The basic mechanical properties (Table 1) of the tubes were obtained using uniaxial tensile test, in which the specimans were intercepted along the tube axes.
Table 1 Mechanical properties of 5052O aluminum tube
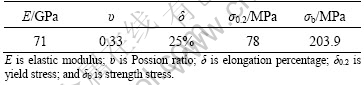
The experimental parameters were as follows: the bending velocity ranged from 1.0 (?)/s to 3.2 (?)/s; the push assistant velocity of the pressure die ranged from 3.50 mm/s to 6.10 mm/s; the mandrel extension length ranged from 10 mm to 20 mm; and the mandrel had 2 or 3 balls.
In addition, these experiments were carried out at room temperature. Draw oil S980B diluted with coal oil was used as antifriction material between the mandrel and the inwall of tube. The wiper die was lubricated with a little thinned oil. Dies were set properly to reduce the risk of wrinkling and the cross-section distortion degree.
2.3 Measurement methods
In this work, an ultrasonic thickness meter PX-7DL was used to measure the thickness of the bent tube wall. The performance parameters were as follows: the resolution factor was up to 0.01 mm; the sonic speed ranged from 1.25 km/s to 10 km/s; the measurable thickness ranged from 0.15 mm to 25.40 mm; and the sound wave ranged from 10 MHz to 22 MHz. Due to the high precision degree, the error was only about 1%. Therefore, the ultrasonic thickness meter PX-7DL satisfies the requirement to the experiment precision.
Cross section distortion can be calculated by the equation:
(1)
where Dmin is the minimum diameter of the formed tube, and Dmax is the maximum diameter of the formed tube. The larger the T, the more serious the cross section distortion.
3 Results and discussion
3.1 Forming quality of tubes
In this work, acceptable bending of the 5052O aluminum tubes with size d70 mm (outer diameter)×1.5 mm (wall thickness)×R105 mm (centerline bending radius) has been accomplished on the basis of correctly setting tooling (Fig.2). The bent tubes have good out-surface quality without wrinkling, cracking or hump. The measurement results show that the maximum wall thinning of the tubes with different bending angles is less than 25%, and the maximum cross section distortion is less than 5%.
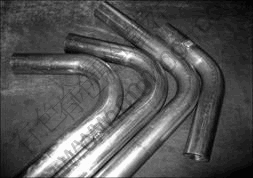
Fig.2 Formed thin-walled aluminum alloy tubes with different bending angles
3.2 Effects of push assistant on tube wall thinning
Push assistant applies an axial pushing force on the tube outside to reduce the tension stress in the bending processes, so that the tube wall thinning can be reduced and acceptable bending is obtained. Thus, the push assistant parameters have influence on the forming quality. In this work, two important parameters were experimentally investigated, namely, the push assistant velocity and the friction between the pressure die and the out-surface of tube.
The results show that the push assistant velocity has a neglectable influence on the tube wall thinning. Fig.3 indicates that the maximum wall thinning is less than 24% in every experiment and the differences between two experiments are all less than 3%, which satisfies the requirement of the aerial standard. Consequently, it is comparatively easy to set the push assistant velocity to obtain acceptable bending in either experiments or actual production.
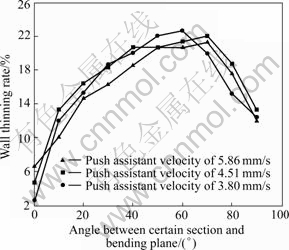
Fig.3 Wall thinning rate with different push assistant velocities
However, it is found that the friction between the pressure die and the out-surface of tube has a significant influence on the tube wall thinning (Fig.4). It can be seen that 1) larger friction can increase the pushing force of the push assistant and improve the wall thinning, while it can also increase the inside wall thickening, and accordingly wrinkling may occur; 2) smaller friction can reduce the pushing force and the inside wall thickening to lessen the risk of wrinkling, while it can also aggravate the outside wall thinning. So, the key to obtaining acceptable bending is to select suitable friction according to the requirement of actual manufacturing.
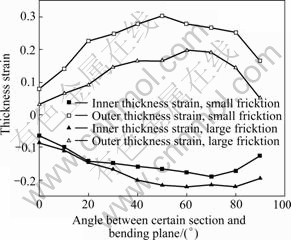
Fig.4 Thickness strain with different pressure friction
These experimental results are similar to those of the aluminum alloy tubes with size d50 mm×1 mm× R100 mm[8]. However, the effects of the friction on the wall thinning are more remarkable in this work.
3.3 Effects of bending velocity on bending quality
The bending velocity has a significant influence on the forming quality of the bent tubes. In order to study the influence, experiments were carried out at different bending velocities. The other experimental conditions were as follows: the push assistant velocity of the pressure die was 3.86 mm/s; the mandrel extension length was 14.5 mm; the centerline bending radius was R105 mm (1.5D); and the friction between the pressure die and the out-surface of tube was dry friction.
It is found that the 5052O aluminum tubes are extremely sensitive to the bending velocity, and they may easily crack when the velocity is larger than 3.9 (?)/s (Fig.5), since the hardening value of aluminum alloy is small. Furthermore, the hydraulic tube bender may operate astatically after long-time working, which causes fast heightening of the oil temperature and instability of the hydraulic and electric systems. Experimental results show that the bending velocity of 1.9 (?)/s selected in this work is reasonable, at which the risk of cracking can be reduced and the forming quality is fine.
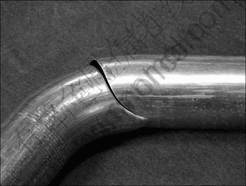
Fig.5 Tube crack shape at high bending velocity
3.4 Effects of mandrel extension length on tube wall thinning
The mandrel extension length is an important parameter in the tube bending processes. Wrinkling may occur when the length is too small, and otherwise the outside of tube may fracture with over large length. In this work, bending processes were investigated with the mandrel extension lengths of 10 mm, 15 mm and 19 mm, respectively, when 2 mandrel balls are used. It is found that no wrinkling or cracking occurs in these cases.
Fig.6 shows the tube wall thinning rate with different mandrel extension lengths. It is found that the larger the mandrel extension length, the more serious the wall thinning. When the length is 10 mm, the maximum wall thinning is 22.7%; when the length is 15 mm, the maximum wall thinning is 23.5%; and when the length is 19 mm, the maximum wall thinning is 25.7%. The reason for this is that larger mandrel extension length increases the friction between the front-end and the tube inwall to baffle the flowing of the material, then larger tangent strain and tube wall thinning are caused. Over large length may cause hump or even cracking.
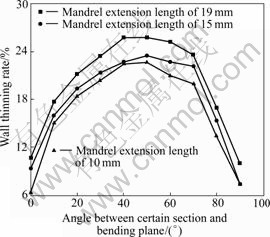
Fig.6 Wall thinning rate with different mandrel extension lengths
These results are similar to those of the stainless steel tubes with size d50 mm×1 mm×R75 mm[6] and the aluminum alloy tubes with size d50 mm×1 mm× R100 mm[8], while the effects of the mandrel extension length on the tube wall thinning are more obvious in this work.
To avoid over-thinning, proper mandrel extension length should be selected in bending processes. An equation to calculate the maximum mandrel extension length is put forward[7]:
(2)
where D is the outer diameter of the tube; d is the mandrel diameter; r is the round radius of the mandrel; t is the tube wall thickness; and R is the centerline bending radius.
In particular, for the tubes with extremely low elongation percentage, test bending after calculating mandrel extension length by the equation is needed, otherwise cracking may easily occur. In this work, the maximum mandrel extension length calculated is 21.8 mm, which is in agreement with the experimental results.
3.5 Effects of ball numbers on bending quality
Mandrel balls used in this work are detachable, thus it is convenient to change the number of balls according to the requirements of experiments or actual manufacturing. To investigate the effects of ball numbers on the bending quality, experiments were carried out with 2 and 3 balls, respectively, when the mandrel extension length was 14.5 mm. The results are shown in Fig.7 and Fig.8.
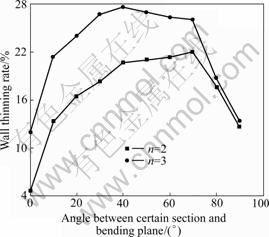
Fig.7 Influence of ball numbers (n) on wall thinning rate
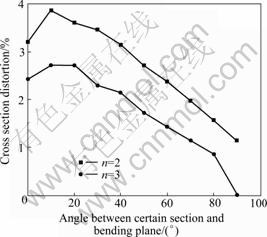
Fig.8 Influence of ball numbers (n) on cross section distortion
Fig.7 shows the tube wall thinning rate with various ball numbers. It can be seen that the maximum wall thinning with 2 balls is 21.3%, while the maximum wall thinning with 3 balls is 26.9%. Consequently, the tube wall thinning is more serious with increasing ball numbers. It can be proved that more balls can increase the friction between the balls and the tube inwall, which baffles the flowing of material, and accordingly causes larger tangent strain and more serious tube wall thinning.
Fig.8 shows that the maximum cross section distortion is 3.86% with 2 balls, while the maximum cross section distortion is 2.71% with 3 balls. It can be seen that more mandrel balls improve the cross section distortion efficiently, because more mandrel balls can support a wider range of curved surface.
These results are similar to those of the stainless steel tubes with size d38 mm×1 mm×R57 mm[6], while the effects of ball numbers on bending quality are more remarkable in this work.
3.6 Effects of ball diameters on bending quality
The mandrel ball diameter is a significant dimension parameter since it greatly influences the bending quality. In this work, bending processes were investigated with the mandrel ball diameters of 65.2 mm and 66.5 mm, respectively, when 2 mandrel balls were used. The results are shown in Fig.9 and Fig.10.
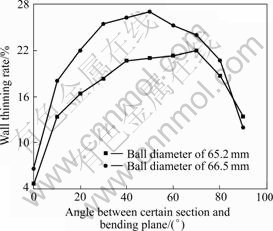
Fig.9 Influence of ball diameters on wall thinning rate
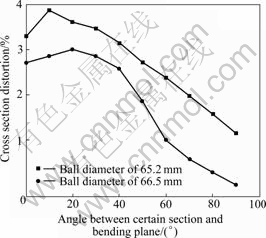
Fig.10 Influence of ball diameters on cross section distortion
Fig.9 shows that the maximum wall thinning with mandrel ball diameter of 65.2 mm is 21.3%; and the maximum wall thinning with diameter of 66.5 mm is 27.1%. Although the difference between the two diameters is only 1.3 mm, the difference of the cross section distortions is up to 5.8%. The increase of the diameter obviously aggravates the wall thinning. This is because larger mandrel ball diameter increases the friction between the balls and the tube inwall, and accordingly causes larger tangent strain and more serious tube wall thinning.
From Fig.10, it is found that the larger the mandrel ball diameter, the smaller the cross section distortion. The maximum cross section distortion with mandrel ball diameter of 65.2 mm is more than 3.8%; however, the maximum cross section distortion with diameter of 66.5 mm is only 3%. It can be concluded that larger mandrel ball diameter can support the inwall of the tube more effectively to improve cross section distortion.
4 Conclusions
1) It is found that the effects of process parameters on bending processes for large diameter thin-walled aluminum alloy tubes are similar to those for small diameter thin-walled tubes, but the forming quality of the large diameter thin-walled aluminum alloy tubes is much more sensitive to the process parameters and thus it is more difficult to form.
2) In NC bending processes of large diameter thin-walled aluminum alloy tubes, the friction between the pressure die and the out-surface of tube has a significant influence on tube wall thinning, while the push assistant velocity affects tube wall thinning slightly. Larger friction can improve the outside tube wall thinning, while it can also increase the inside tube wall thickening, which is possible to produce wrinkling.
3) The mandrel parameters have more obvious influence on the bending quality for the large diameter thin-walled aluminum alloy tubes than for the small diameter thin-walled tubes. Larger mandrel extension length aggravates tube wall thinning, even causes cracking. More mandrel balls or larger mandrel ball diameter can improve cross section distortion, and aggravate tube wall thinning.
4) Acceptable bending of the 5052O aluminum tubes (d70 mm×1.5 mm×R105 mm) is accomplished successfully, showing that though the NC bending of large diameter thin-walled tubes with smaller bending radii is difficult to realize, and qualified bent tube can be obtained when proper process parameters are selected and adopted.
References
[1] YANG He, LIN Yan, SUN Zhi-chao. Review of advanced plastic processing technology and tube forming facing 21st century [C]// Symposium of 2nd China Science Association annual Conference. Beijing: Press of Science and Technology, 2000: 745-746. (in Chinese)
[2] YANG He, ZHAN Mei, LIU Yu-li. Some advanced plastic processing technologies and their numerical simulation [J]. Journal of Materials Processing Technology, 2004, 151(1/3): 63-69.
[3] GOODARZI M, KUBOKI T, MURATA M. Deformation analysis for the shear bending process of circular tubes [J]. Journal of Materials Processing Technology, 2005, 162/163: 492-497.
[4] TANG N C. Plastic-deformation analysis in tube bending [J]. International Journal of Pressure Vessels and Piping, 2000, 77(12): 751-759.
[5] AL-QURESHI H A. Elastic-plastic analysis of tube bending [J]. International Journal of Machine Tools & Manufacture, 1999, 39(1): 87-104.
[6] SHEN Shi-jun, YANG He, LI Heng, ZHAN Mei. Experimental study on role of mandrel in thin-walled tube NC bending process with small bending radius [J]. Journal of Plasticity Engineering, 2007, 8(4): 29-34. (in Chinese)
[7] WANG Guang-xiang, YANG He, LI Heng, ZHAN Mei, GU Rui-jie. Experimental study of the influence of processing parameters on forming quality of thin-walled NC bending tube [J]. Mechanical Science and Technology, 2005, 24(8): 995-998. (in Chinese)
[8] KOU Yong-le. Experimental research on NC bending with small bending radius of aluminum alloy thin-walled tube [D]. Xi’an: Northwestern Polytechnical University, 2007: 59-73. (in Chinese)
[9] LEE H, VAN TYNE C J, FIELD D. Finite element bending analysis of oval tubes using rotary draw bender for hydroforming applications [J]. Journal of Materials Processing Technology, 2005, 168(2): 327-335.
[10] LI Heng. Study on wrinkling behaviors under multi-die constraints in thin-walled tube NC bending [D]. Xi’an: Northwestern Polytechnical University, 2008: 115-123. (in Chinese)
[11] GANTNER P, BAUER H, HARRISON D K, de SILVA A K M. Free-bending—A new bending technique in the hydroforming process chain [J]. Journal of Materials Processing Technology, 2005, 167(2/3): 302-308.
[12] WANG J, AGARWAL R. Tube bending under axial force and internal pressure [J]. Journal of Manufacturing Science and Engineering, Transactions of the ASME, 2006, 128(2): 598-605.
[13] OLIVEIRA D A, WORSWICK M J, GRANTAB R. Effect of lubricant in mandrel-rotary draw tube bending of steel and aluminum [J]. Canadian Metallurgical Quarterly, 2005, 44(1): 71-78.
[14] AL-QURESHI H A, RUSSO A. Spring-back and residual stresses in bending of thin-walled aluminium tubes [J]. Materials & Design, 2002, 23(2): 217-222.
[15] PAN K, STELSON K A. On the plastic deforming of a tube during bending [J]. Journal of Engineering for Industry, Transactions of NAMRI/SME, 1995, 117: 494-500.
[16] PAULSEN F, WELO T. Application of numerical simulation in the bending of aluminum alloy profiles [J]. Journal of Materials Processing Technology, 1996, 58(2/3): 274-285.
Foundation item: Project(50225518) supported by the National Science Foundation of China for Distinguished Young Scholars; Project(59975076, 50175092) supported by the National Natural Science Foundation of China; Project(04H53057) supported by the Aviation Science Foundation of China
Corresponding author: YANG He, Tel: +86-29-88495632; Fax: +86-29-88495632; E-mail: yanghe@nwpu.edu.cn
DOI: 10.1016/S1003-6326(08)60331-3
(Edited by YANG Hua)