J. Cent. South Univ. Technol. (2011) 18: 303-309
DOI: 10.1007/s11771-011-0695-5
Influence of substituting Ni with Co on hydriding and dehydriding kinetics of melt spun nanocrystalline and amorphous Mg2Ni-type alloys
ZHANG Yang-huan(张羊换)1, 2, ZHAO Dong-liang(赵栋梁)1, LI Bao-wei(李保卫)2,
MA Zhi-hong(马志鸿)1, 3, GUO Shi-hai(郭世海)1, WANG Xin-lin(王新林)1
1. Department of Functional Material Research, Central Iron and Steel Research Institute, Beijing 100081, China;
2. School of Material and Metallurgy, Inner Mongolia University of Science and Technology, Baotou 014010, China;
3. Baotou Research Institute of Rare Earths, Baotou 014010, China
? Central South University Press and Springer-Verlag Berlin Heidelberg 2011
Abstract: In order to improve the hydriding and dehydriding kinetics of the Mg2Ni-type alloys, Ni in the alloy is substituted by element Co. The nanocrystalline and amorphous Mg2Ni-type Mg2Ni1-xCox (x=0, 0.1, 0.2, 0.3, 0.4) alloys were synthesized by melt-spinning technique. The structures of the as-cast and spun alloys were studied with an X-ray diffractometer (XRD) and a high resolution transmission electronic microscope (HRTEM). An investigation on the thermal stability of the as-spun alloys was carried out with a differential scanning calorimeter (DSC). The hydrogen absorption and desorption kinetics of the alloys were measured with an automatically controlled Sieverts apparatus. The results demonstrate that the substitution of Co for Ni does not alter the major phase of Mg2Ni but results in the formation of secondary phase MgCo2. No amorphous phase is detected in the as-spun Co-free alloy, but a certain amount of amorphous phase is clearly found in the as-spun Co-containing alloys. The substitution of Co for Ni exerts a slight influence on the hydriding kinetics of the as-spun alloy. However, it dramatically enhances the dehydriding kinetics of the as-cast and spun alloys. As Co content (x) increases from 0 to 0.4, the hydrogen desorption capacity increases from 0.19% to 1.39% (mass fraction) in 20 min for the as-cast alloy, and from 0.89% to 2.18% (mass fraction) for the as-spun alloy (30 m/s).
Key words: Mg2Ni-type alloy; melt-spinning; substituting; Ni; Co; structure; hydriding; dehydriding; kinetics
1 Introduction
Mg and Mg-based metallic hydrides are considered to be the most promising hydrogen storage materials owing to their large hydrogen capacity and low cost. However, the poor absorption/desorption kinetics and high thermodynamic stability of these hydrides make them inappropriate for any practical applications. Therefore, exploring ways to improve the hydriding and dehydriding kinetics of Mg-based alloys has remained one of the main challenges faced by the researchers in this area. Various efforts, such as mechanical alloying (MA) [1], surface modification [2], and alloying with other elements [3] have been undertaken to ameliorate the hydriding and dehydriding properties.
YU et al [4] have acquired the maximum hydrogen capacity of 5.5% (mass fraction) H2 at 200 °C in 60 s under 2.0 MPa hydrogen pressure for Mg-based alloy prepared by mechanical alloying (MA). JANOT et al [5] have improved the hydrogen desorption kinetics of Mg2Ni alloy with surface modification by mechanical grinding (MG). KOHNO and KANDA [6] have employed the surface modification with Ni powder by ball milling to yield a large discharge capacity of 750 mA?h/g at a current density of 20 mA/g for modified Mg2Ni alloys.
High energy ball-milling, undoubtedly, is a quite powerful method for the fabrication of nanocrystalline and amorphous Mg and Mg-based alloys. However, MA Mg-based alloys exhibit extremely poor electrochemical cycle stability on account of the evanishment of the metastable structures formed by ball milling during the multiple electrochemical charging and discharging cycles [7], which has been an insurmountabe barrier for its practical applications. Alternatively, the melt-spinning technique is an impactful method to yield a nanocrystalline structure and has been regarded to be the most appropriate method for the mass-production of the nanocrystalline Mg-based alloys.
Furthermore, the amorphous alloys produced by melt-spinning can exhibit excellent hydriding characteristics even at room temperature, similar to the alloys produced by the MA process. HUANG et al [8] have used the melt spinning technique to fabricate the amorphous and nanocrystalline Mg-based alloy (Mg60Ni25)90Nd10 possessing the maximum hydrogen capacity of 4.2% (mass fraction). TANAKA et al [9] have investigated the amorphization and nano- crystallization of Mg-Ni and Mg-Ni-RE (RE=La, Nd) alloys by melt-spinning. The resultant nanocrystalline alloys, particularly Mg-Ni-RE systems, have been observed to exhibit an excellent hydrogen absorbing kinetics. SPASSOV and K?STER [10] have prepared Mg2(Ni,Y) hydrogen storage alloy with the composition of Mg63Ni30Y7 by rapid solidification process to yield a maximum hydrogen absorption capacity of about 3.0% (mass fraction).
It has been testified that an amorphous phase can be obtained in melt-spun Mg-Ni-based alloy by the addition of third element such as Pd, La and Ca [11]. Therefore, cobalt was chosen as the third element to acquire an amorphous phase in Mg2Ni-type alloy by the melt-spinning technique. The objective of this work is to fabricate the Mg-Ni-based ternary nanocrystalline and amorphous alloys by melt spinning and to examine their thermal stability and hydriding/dehydriding kinetics.
2 Experimental
The nominal composition of the experimental alloy was Mg2Ni1-xCox (x=0, 0.1, 0.2, 0.3, 0.4). For convenience, the alloys were denoted according to Co contents as Co0, Co0.1, Co0.2, Co0.3 and Co0.4. The alloy ingots were prepared using a vacuum induction furnace in a helium atmosphere at a pressure of 0.04 MPa. A part of the as-cast alloy was re-melted and spun by melt-spinning with a rotating copper roller. The spinning rate was approximately expressed by the linear velocity of the copper roller because it was too difficult to measure a real spinning rate, i.e. cooling rate of the sample during spinning. The spinning rates used in the experiment were 15, 20, 25 and 30 m/s.
The phase structures and compositions of the as-cast and spun alloys were determined with an XRD diffracto- meter (D/max/2400). The experimental parameters used for the diffraction were 160 mA, 40 kV and 10 (°)/min. The XRD was performed with Cu Kα1 radiation filtered by graphite. The thin film samples of the as-spun alloys were prepared by ion etching method in order to observe the morphology with high resolution transmission electronic microscope (HRTEM) (JEM-2100F, operated at 200 kV) and also to determine the crystalline state of the samples with electron diffraction (ED).
The thermal stability and crystallization of the as-spun alloys were studied with a DSC instrument (STA449C). The temperature limit was 600 °C with a heating rate of 10 °C/min.
The hydrogen absorption and desorption kinetics of the as-cast and spun alloys were measured by an automatically controlled Sieverts apparatus. The hydrogen absorption was conducted at 1.5 MPa and the hydrogen desorption was performed in vacuum (1×10-4 MPa) at 200 °C.
3 Results and discussion
3.1 Microstructure characteristics
The XRD patterns of the as-spun alloys are shown in Fig.1. It is indicated that the substitution of Co for Ni leads to the formation of secondary phase MgCo2 instead of changing the major phase of Mg2Ni in the alloy. It is evidently visible that the amount of MgCo2 phase grows with an increase in Co content. Fig.1 displays that no amorphous phase is detectable in the as-spun Co0 alloy, but the as-spun Co0.4 alloy obviously shows the presence of an amorphous phase. Thus, it can be concluded that the substitution of Co for Ni intensifies the glass forming ability of the Mg2Ni-type alloy. Two possible reasons are mainly responsible for the enhancement of the glass forming ability of Mg-Ni alloy caused by the Co substitution. First, the addition of third element to Mg-Ni or Mg-Cu alloys can significantly facilitate the glass formation [12]. Second, the atomic radius of Co is larger than that of Ni, leading to the fact that the glass forming ability of the alloy is improved with an increase in the difference of the atom radius of the alloy [13]. Table 1 lists the lattice parameters, cell volume as well as the full width at half maximum (FWHM) values of the main diffraction peaks of the as-spun (15 m/s and 30 m/s) alloys, which are calculated by the software of Jade 6.0. It can be derived from Table 1 that the FWHM values of the main diffraction peaks of alloys significantly increase with an increase of Co content. The substitution of Co for Ni leads to the enlargement of the lattice parameters and the cell volume of alloys, which is attributed to the fact that the radius of Co atom is larger than that of Ni atom. It is also clear in Table 1 that the melt spinning yields the broadened diffusion peaks, indicating the refinement of the average grain size and stored stress in the grains.
The TEM micrographs of the as-spun (30 m/s) Co0,
Co0.1, Co0.3 and Co0.4 alloys are presented in Fig.2. It is quite visible that the as-spun Co0 and Co0.1 alloys display a nanocrystalline structure with a grain size of about
20 nm along with the exhibition of their electron diffraction (ED) patterns as sharp multi-haloes. The morphology of the as-spun Co0.3 alloy presents a nanocrystalline feature, and a small amount of amorphous phase can be found at its grain boundaries. The Co0.4 alloy also exhibits a feature of the nanocrystalline with a grain size of about 20 nm embedded in the amorphous matrix. However, its (Co0.4 alloy) electron diffraction pattern consists of broad and dull halo, confirming the presence of an amorphous structure. This result is quite in conformity with the XRD observation shown in Fig.1.
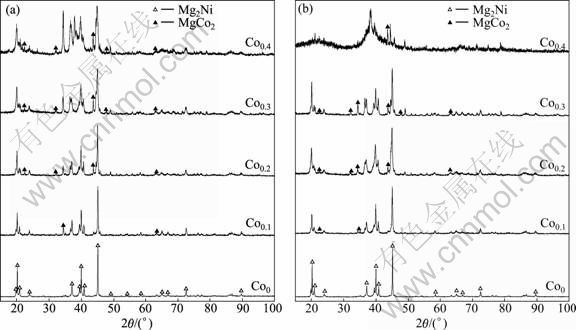
Fig.1 XRD patterns of as-spun alloys with different spinning rates: (a) 15 m/s; (b) 30 m/s
Table 1 Lattice parameters, cell volume and FWHM values of major diffraction peaks of alloys
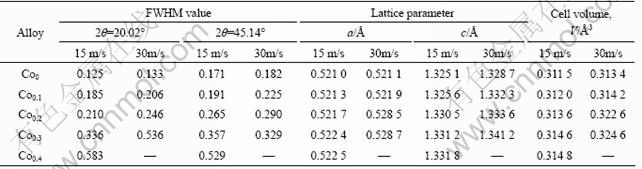
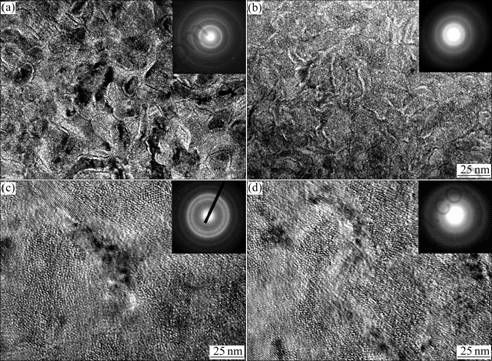
Fig.2 TEM images and electron diffraction patterns of as-spun (30 m/s) alloys: (a) Co0; (b) Co0.1; (c) Co0.3; (d) Co0.4
3.2 Thermal stability and crystallization
In order to examine the thermal stability and crystallization of the as-spun amorphous and nanocrystalline alloys, DSC analysis has been conducted. The resulting profiles of the as-spun (30 m/s) alloys depicted in Fig.3 reveal that the crystallization of the as-spun alloys completes during the heating process, and furthermore, the crystallization process consists of two steps. The first crystallization reaction is associated with a sharp exothermic DSC peak followed by a smaller and wider peak corresponding to a second crystallization reaction. It is also testified that the first sharper peak corresponds to the crystallization (ordering) of the amorphous into nanocrystalline Mg2Ni [14]. The crystallization temperature of the amorphous phase in the as-spun alloys first increases and then decreases with increasing the Co content.
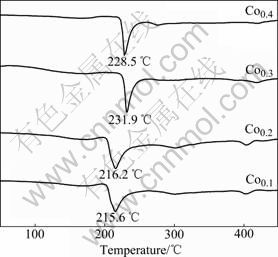
Fig.3 DSC profiles of as-spun (30 m/s) alloys
3.3 Hydriding and dehydriding kinetics
The hydriding process was carried out under 1.5 MPa hydrogen pressure (the pressure is the initial pressure of hydriding process) at 200 °C, and dehydriding process was carried out in vacuum (1×10-4 MPa) also at 200 °C.
The hydrogen absorption kinetic curves of the as-spun alloys are plotted in Fig.4. It is visible that all the as-spun alloys demonstrate very fast hydrogen absorption rates and nearly reach their saturation capacities in 10 min. The high hydrogen absorption capacities and fast hydrogen absorption rates of the Co0.2 and Co0.3 alloys (Fig.4) may be associated with the increased cell volume resulting from the Co substitution. The Co0.4 alloy displays a low hydrogen absorption capacity, which may be ascribed to the increased amount of the MgCo2 phase due to the fact that the hydrogen absorption capacity of the MgCo2 phase is very low. The enhancement in the hydrogenation characteristics can be associated with the enhanced hydrogen diffusivity in the amorphous and nanocrystalline microstructures because the amorphous phase around the nanocrystalline leads to an easier access of hydrogen to the nanograins, thus avoiding the long-range diffusion of hydrogen through an already formed hydride, which is often regarded as the slowest stage of absorption. According to the results reported by ORIMO and FUJII [15], the distribution of the maximum hydrogen concentrations in three nanometer-scale regions, i.e. grain region, grain boundary region as well as amorphous region, have been experimentally determined to be 0.3% H in the grain region of Mg2Ni, 4.0% H at the grain boundary and 2.2% H in the amorphous region. This indicates that the hydrides mainly exist in the grain-boundary region and the amorphous phase region.
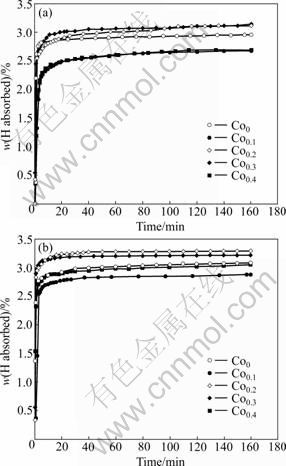
Fig.4 Hydrogen absorption kinetic curves of as-spun alloys: (a) 15 m/s; (b) 30 m/s
The hydrogen absorption kinetic curves of the as-cast and spun Co0.1 and Co0.4 alloys are plotted in Fig.5. The results indicate that the hydrogen absorption property of the alloys is significantly enhanced by melt spinning. As the spinning rate grows from 0 to 30 m/s, the hydrogen absorption capacity in 10 min rises from 2.35% to 2.88% for Co0.1 alloy, and from 1.91% to 2.96% for Co0.4 alloy. These observations indicate that the hydrogenation kinetics and storage capacity of all as-spun nano-crystalline and amorphous Mg2Ni-type alloys under investigation are superior to those of the conventional polycrystalline materials with similar compositions. SPASSOV and K?STER [16] have also confirmed that melt spinning can significantly improve the hydrogen absorption performance of Mg-based alloy, and the maximum hydrogen capacity of 4.0% H (mass fraction) for the as-quenched Mg75Ni20Mm5 (Mm=Ce, La-rich mischmetal) alloy can be obtained.
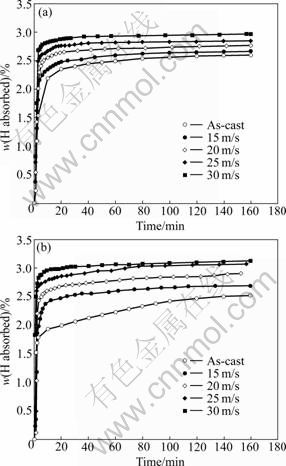
Fig.5 Hydrogen absorption curves of as-cast and spun alloys: (a) Co0.1 alloy; (b) Co0.4 alloy
Fig.6 depicts the hydrogen desorption kinetic curves of the as-spun alloys with spinning rates of 15 m/s and 30 m/s. it is quite visible that the Co substitution significantly ameliorates the hydrogen desorption capacity and kinetics of the as-spun alloys. As Co content (x) increases from 0 to 0.4, the hydrogen desorption capacity of the as-spun (15 m/s) alloy in 20 min rises from 0.51% to 1.72%, and from 0.89% to 2.15% for the as-spun (30 m/s) alloy. It is interesting to note that the hydrogen absorption capacity (Fig.4) of the as-spun Co0 alloy is similar to that of the Co0.4 alloy, but its hydrogen desorption capability is much lower than that of the Co0.4 alloy. Therefore, it can be deduced that the substitution of Co for Ni improves the dehydriding performance of the Mg2Ni-type alloy. The enhanced hydrogenation characteristics may be ascribed to two reasons. First, the Co substitution significantly intensifies the glass forming ability of Mg2Ni-type alloy and the amorphous Mg2Ni exhibits an excellent hydrogen desorption capability [17]. On the other hand, the substitution of Co for Ni in Mg2Ni compound lowers the stability of hydride and also facilitates the desorption reaction [1, 18].
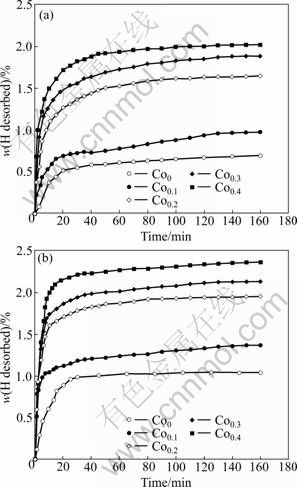
Fig.6 Hydrogen desorption curves of as-spun alloys with different spinning rates: (a) 15 m/s; (b) 30 m/s
Fig.7 shows the hydrogen desorption kinetic curves of the Co0.1 and Co0.4 alloys with different spinning rates. The results clearly demonstrate that the dehydriding capability of the alloys increases with an increase of the spinning rate. As the spinning rate grows from 0 to 30 m/s, the hydrogen desorption capacity of the Co1 alloy in 20 min increases from 0.39% to 1.13%, and from 1.39% to 2.15% for the Co0.4 alloy. In addition, it is clear that the as-cast and spun Co0.1 alloy possesses inferior hydrogen desorption capacity and poorer dehydrogenation kinetics to that of the Co0.4 alloy. This behavior may be ascribed to the high stability of the crystal Mg-based hydride due to the fact that the melt spinning is unable to change the crystal state of the Co0.1 alloy. Hence, the as-spun Co0.4 alloy reveals high hydrogen desorption capacity and very fast dehydriding rate.
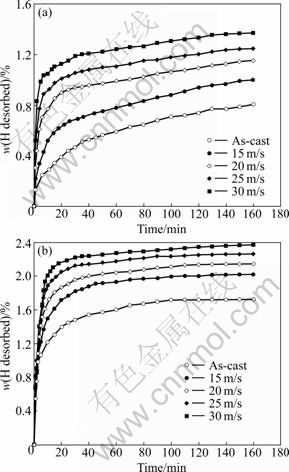
Fig.7 Hydrogen desorption curves of as-cast and spun alloys: (a) Co0.1 alloy; (b) Co0.4 alloy
It can be deduced from the aforementioned results that the substitution of Co for Ni significantly ameliorates the hydrogen absorption and desorption capacities and kinetics of the M2Ni-type alloy. A similar result has already been reported by KHRUSSANOVA et al [19]. The magnesium composites containing 10% and 15% (mass fraction) Mg2Ni1-xCox (x=0.1 and 0.3) have been prepared by mechanical alloying and it has been found that an intermetallic addition exerts an evident catalytic effect on the hydriding of magnesium. Furthermore, it has been confirmed that the formation of Mg2Ni0.8Co0.2 results in a much stronger catalytic action on the hydrogen absorption kinetics of magnesium than Mg2Ni alone does [20]. The catalytic effect of the Mg2Ni1-xCox additive may be ascribed to the inhomogeneity of the alloys containing a MgNi2 phase along with cobalt and nickel clusters. This inhomogeneity is directly associated with the chemisorption of hydrogen and hence facilitates the hydriding reaction. The catalytic effect of Co has been well elaborated by BOBET et al [21]. Ni is a largely known catalyst, which is utilized for the hydriding reactions. In this work, the catalytic effect of Co substitution on the hydrogen absorption kinetics of the as-spun Mg2Ni alloy is ascribed to the enhanced glass forming ability caused by Co substitution. LEE et al [22] have made efforts to improve the hydrogen sorption properties of Mg by mechanical grinding under H2 (reactive grinding) with Co, finding that the addition of smaller particles of Co (0.5-1.5 μm) exerts a significant impact on the hydrogen sorption properties of Mg. It has been reckoned that Co with smaller particle sizes may act as a grain refiner for the magnesium. In addition, the expansion and contraction of the particles of Mg during the hydriding/dehydriding cycling also make them finer. Therefore, the addition of Co with smaller particle sizes as well as the hydriding/dehydriding cycling will aid the particles of magnesium to exhibit the higher hydrogen sorption rates. Based on the above mentioned discussion, it can be concluded that the substitution of Co for Ni produces a significant catalytic effect on the hydrogen absorption and desorption capacity and kinetics of Mg and Mg-based alloy. However, it must be pointed out that the action mechanism of Co additive is directly associated with the preparation technology of the alloy.
4 Conclusions
1) The investigation on the structures of the as-cast and spun Mg2Ni1-xCox (x=0, 0.1, 0.2, 0.3, 0.4) alloys reveals that there is no amorphous phase in the as-spun Co0 alloy, and the as-spun Co0.4 alloy demonstrates the nanocrystalline structure embedded in the amorphous matrix, testifying that the substitution of Co for Ni significantly enhances the glass forming ability of the Mg2Ni-type alloys. The substitution of Co for Ni leads to the formation of the secondary phase MgCo2 instead of changing the major phase of Mg2Ni in the alloy.
2) The substitution of Co for Ni significantly enhances the hydrogen desorption capacity and rate of as-cast and spun alloys, which is attributed to the decreased stability of the hydride resulting from the Co substitution.
3) Melt spinning significantly improves the hydriding and dehydriding properties of the Mg2Ni-type alloys. Both the hydriding and dehydriding capacity and rate of the alloy markedly rise with the increase in the spinning rate, which is mainly ascribed to the formation of the nanocrystalline and amorphous structure produced by the melt spinning.
References
[1] WOO J H, LEE K S. Electrode characteristics of nanostructured Mg2Ni-type alloys prepared by mechanical alloying [J]. Journal of The Electrochemical Society, 1999, 146(3): 819-823.
[2] LIU F J, SUDA S. A method for improving the long-term storability of hydriding alloys by air water exposure [J]. Journal of Alloys and Compounds, 1995, 231: 742-750.
[3] LIU Y N, ZHANG X J. Effect of lanthanum additions on electrode properties of Mg2Ni [J]. Journal of Alloys and Compounds, 1998, 276: 231-234.
[4] YU Z X, LIU Z Y, WANG E D. Hydrogen storage properties of nanocomposite Mg-Ni-Cu-CrCl3 prepared by mechanical alloying [J]. Materials Science and Engineering: A, 2002, 335: 43-48.
[5] JANOT R, DAROK X, ROUGIER A, AYMARD L, NAZRI G A, TARASCON J M. Hydrogen sorption properties for surface treated MgH2 and Mg2Ni alloys [J]. Journal of Alloys and Compounds, 2005, 404/405/406: 293-296.
[6] KOHNO T, KANDA M. Effect of partial substitution on hydrogen storage properties of Mg2Ni alloy [J]. Journal of the Electrochemical Society, 1997, 144: 2384-2388.
[7] NOHARA S, FUJITA N, ZHANG S G, INOUE H, IWAKURA C. Electrochemical characteristics of a homogeneous amorphous alloy prepared by ball milling Mg2Ni with Ni [J]. Journal of Alloys and Compounds, 1998, 267: 76-78.
[8] HUANG L J, LIANG G Y, SUN Z B, WU D C. Electrode properties of melt-spun Mg-Ni-Nd amorphous alloys [J]. Journal of Power Sources, 2006, 160: 684-687.
[9] TANAKA K, KANDA Y, FURUHASHI M, SAITO K, KURODA K, SAKA H. Improvement of hydrogen storage properties of melt-spun Mg-Ni-RE alloys by nanocrystallization [J]. Journal of Alloys and Compounds, 1999, 293/294/295: 521-525.
[10] SPASSOV T, K?STER U. Thermal stability and hydriding properties of nanocrystalline melt-spun Mg63Ni30Y7 alloy [J]. Journal of Alloys and Compounds, 1998, 279: 279-286.
[11] YAMAURA S I, KIM H Y, KIMURA H, INOUE A, ARATA Y. Thermal stabilities and discharge capacities of melt-spun Mg-Ni-based amorphous alloys [J]. Journal of Alloys and Compounds, 2002, 339: 230-235.
[12] INOUE A, MASUMOTO T. Mg-based amorphous alloys [J]. Materials Science and Engineering: A, 1993, 173: 1-8.
[13] CHEN H S. Thermodynamic considerations on the formation and stability of metallic glasses [J]. Acta Materialia, 1974, 22(12): 1505-1511.
[14] SPASSOV T, SPLSONA P, SURI?ACH S, BAR? M D. Optimization of the ball-milling and heat treatment parameters for synthesis of amorphous and nanocrystalline Mg2Ni-based alloys [J]. Journal of Alloys and Compounds, 2003, 349: 242-254.
[15] ORIMO S, FUJII H. Materials science of Mg-Ni-based new hydrides [J]. Applied Physics A, 2001, 72: 167-186.
[16] SPASSOV T, K?STER U. Hydrogenation of amorphous and nanocrystalline Mg-based alloys [J]. Journal of Alloys and Compounds, 1999, 287: 243-250.
[17] GOO N H, JEONG W T, LEE K S. The hydrogen storage properties of new Mg2Ni alloy [J]. Journal of Power Sources, 2000, 87: 118-124.
[18] TAKAHASHI Y, YUKAWA H, MORINAGA M. Alloying effects on the electronic structure of Mg2Ni intermetallic hydride [J]. Journal of Alloys and Compounds, 1996, 242: 98-107.
[19] KHRUSSANOVA M, GRIGOROVA E, BOBET J L, KHRISTOV M, PESHEV P. Hydrogen sorption properties of the nanocomposites Mg-Mg2Ni1-xCox obtained by mechanical alloying [J]. Journal of Alloys and Compounds, 2004, 365: 308-313.
[20] KHRUSSANOVA M, MANDZHUKOVA T, GRIGOROVA E, KHRISTOV M, PESHEV P. Hydriding properties of the nano- composite 85wt.%Mg-15wt.%Mg2Ni0.8Co0.2 obtained by ball milling [J]. Journal of Material Science, 2007, 42: 3338-3342.
[21] BOBET J L, CHEVALIER B, DARRIET B. Effect of reactive mechanical grinding on chemical and hydrogen sorption properties of the Mg+10wt.%Co mixture [J]. Journal of Alloys and Compounds, 2002, 330/331/332: 738-742.
[22] LEE D S, KWON I H, BOBET J L, SONG M Y. Effects on the H2-sorption properties of Mg of Co (with various sizes) and CoO addition by reactive grinding [J]. Journal of Alloys and Compounds, 2004, 366: 279-288.
(Edited by YAGN Bing)
Foundation item: Project(2006AA05Z132) supported by the National High-tech Research and Development Program of China; Projects(50871050, 50961009) supported by the National Natural Science Foundation of China; Project(2010ZD05) supported by the Natural Science Foundation of Inner Mongolia, China; Project(NJzy08071) supported by the High Education Science Research Program of Inner Mongolia, China
Received date: 2010-03-10; Accepted date: 2010-09-02
Corresponding author: ZHANG Yang-huan, Professor, PhD; Tel: +86-10-62187570; E-mail: zyh59@yahoo.com.cn